精编机械原理课程设计粉料压片成形机.docx
《精编机械原理课程设计粉料压片成形机.docx》由会员分享,可在线阅读,更多相关《精编机械原理课程设计粉料压片成形机.docx(26页珍藏版)》请在冰豆网上搜索。
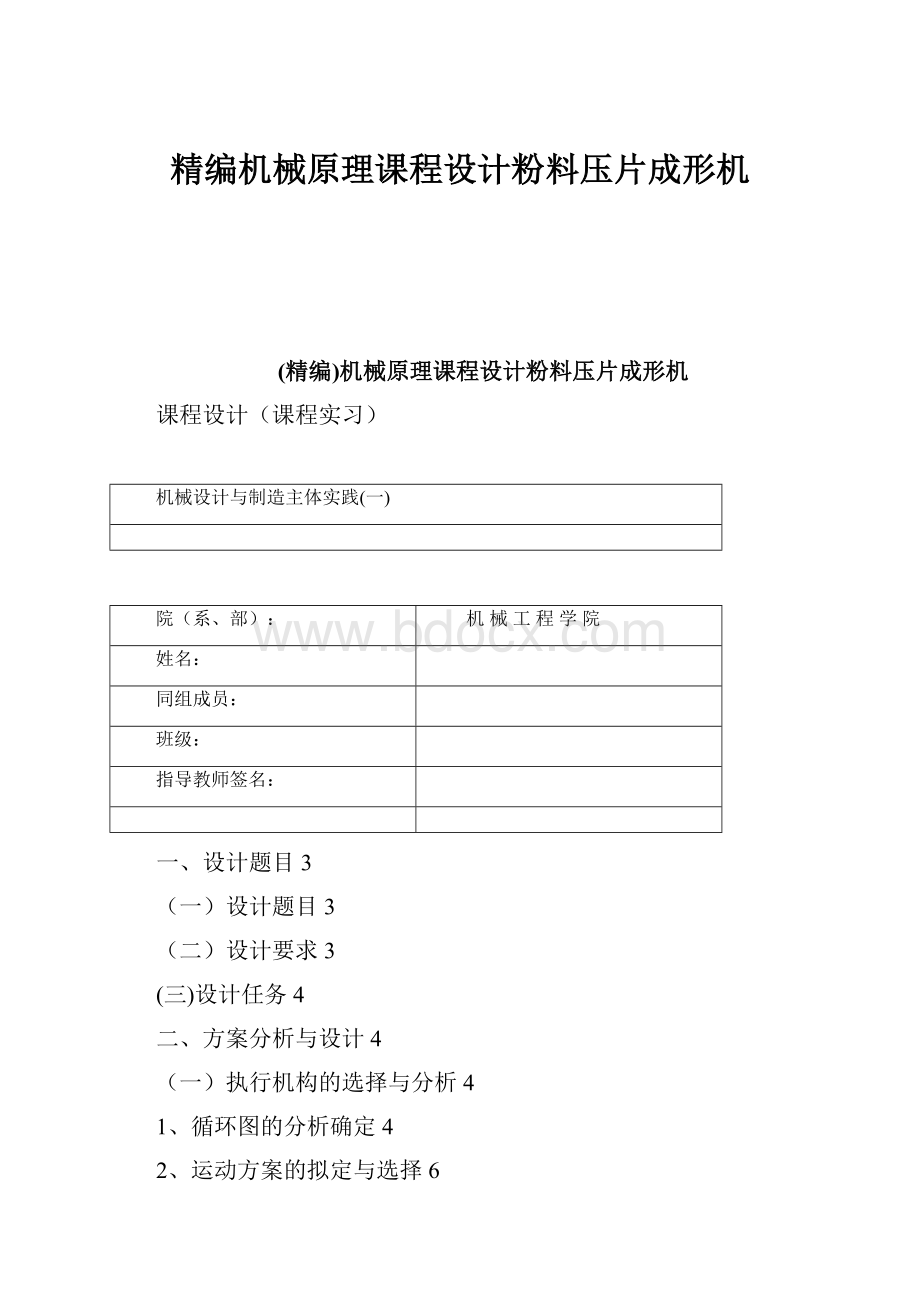
精编机械原理课程设计粉料压片成形机
(精编)机械原理课程设计粉料压片成形机
课程设计(课程实习)
机械设计与制造主体实践
(一)
院(系、部):
机械工程学院
姓名:
同组成员:
班级:
指导教师签名:
一、设计题目3
(一)设计题目3
(二)设计要求3
(三)设计任务4
二、方案分析与设计4
(一)执行机构的选择与分析4
1、循环图的分析确定4
2、运动方案的拟定与选择6
3、机构的运动分析与设计10
(1)上冲头设计10
(2)下冲头设计16
(3)料筛设计19
(二)电动机的选择21
(三)传动机构的选择与减速器的设计22
(四)飞轮的设计23
(五)心得体会25
(六)参考文献26
机械原理课程设计
——粉料压片成形机
一、设计题目
(一)设计题目
1、设计题目及原始数据
设计自动压片成形机,将具有一定湿度的粉状原料(如陶瓷干粉、药粉)定量送入压形位置,经压制成形后脱离该位置。
机器的整个工作过程(送料、压形、脱离)均自动完成。
该机器可以压制陶瓷圆形片坯、药剂(片)等。
数据见表1。
表1压片成形机设计数据
方案号
电动机转速
r/min
生产率片/min
成品尺寸(Φ×d)mm,mm
冲头压力
kN
δ
M冲/kg
M杆/kg
A
1350
60
24×20
60,000
0.10
12
5
B
970
30
60×35
120,000
0.08
24
10
2、压片成形机的工艺动作
(1)干粉料均匀筛入圆筒形型腔(图1a)。
(2)下冲头下沉3mm,预防上冲头进入型腔时粉料扑出(图1b)。
(3)上、下冲头同时加压(图1c),并保持一段时间。
(4)上冲头退出,下冲头随后顶出压好的片坯(图1d)。
(5)料筛推出片坯(图1e)
图1
(二)设计要求
1、上冲头完成往复直移运动(铅垂上下),下移至终点后有短时间的停歇,起保压作用,保压时间为0.4秒左右。
因冲头上升后要留有料筛进入的空间,故冲头行程为90~100mm。
因冲头压力较大,因而加压机构应有增力功能。
2、下冲头先下沉3mm,然后上升8mm,加压后停歇保压,继而上升16mm,将成型片坯顶到与台面平齐后停歇,待料筛将片坯推离冲头后,再下移21mm,到待料位置。
3、料筛在模具型腔上方往复筛料,然后退回。
待批料成型并被推出型腔后,料筛在台面上右移约45~50mm,推卸片坯。
(三)设计任务
1、各执行机构应包括:
实现上冲头运动的主加压机构、实现下冲头运动的辅助加压机构、实现料筛运动的上下料机构。
满足上述运动可采用连杆机构、凸轮机构等。
辅助加压机构可采用凸轮机构
2、设计传动系统并确定其传动比分配,并在图纸上画出传动系统图;
3、画出机器的运动方案简图与运动循环图。
拟定运动循环图时,可执行构件的动作起止位置可根据具体情况重叠安排,但必须满足工艺上各个动作的配合,在时间和空间上不能出现“干涉”;
4、设计机构;
5、对机构进行运动设计,绘出运动线图。
进行机构的动态静力分析,计算飞轮转动惯量;
6、将机构做成三维模型,实现模拟运动;
7、编写设计计算说明书。
二、方案分析与设计
(一)执行机构的选择与分析
1、循环图的分析确定
根据压片机的工艺动作可得各个机构的动作如下:
上冲头:
往复运动。
下降压紧药片,保压0.4s,上升。
下冲头:
复杂的往复运动。
首先下降3mm,接着上升8mm,保压0.4s,上升16mm,间歇一段时间后,下降21mm。
再间歇一段时间。
料筛:
将料送出,筛料,返回,间歇一段时间后重复动作。
由各个机构的动作可画出其运动循环图如图2所示:
图2
则其运动关系如表2所示:
表2
上冲头
进
休
退
下冲头
休
退
进
休
进
休
退
料筛
退
休
进
筛
可将其运动表示为树状功能图:
图3
2、运动方案的拟定与选择
根据循环图及树状图,可得三个机构都做往复运动,且都有间歇运动。
上冲头是主加压机构,故可选曲柄滑块机构,或六杆机构来实现增力。
下冲头运动和筛料机构可用凸轮机构来实现其运动。
筛料机构做往复运动,故可以使用曲柄滑块机构,也可用凸轮机构实现其运动。
设计各个部分的机构如表3所示
表3
方案
上冲头
下冲头
料筛
1
曲柄滑块机构
平底凸轮机构
曲柄滑块机构
2
六杆机构
滚子凸轮机构
滚子凸轮机构
上冲头方案:
方案一:
曲柄滑块机构
方案二:
六杆机构
选择:
选择方案二。
理由:
六杆机构将曲柄滑块的急回特性进一步扩大,同时使行程得到扩大,效率高。
六杆机构接近死点位置所具有的传力特征来实现增力,比曲柄滑块的增力效果好,能够更好的实现加压。
故选择六杆机构作为上冲头的加压机构。
下冲头方案:
方案一:
平底凸轮机构
方案二:
滚子凸轮机构
选择:
选择方案二。
理由:
选择凸轮机构易实现下冲头复杂的运动。
首先我们想到的是方案一,因为方案一的压力角为零,传力效果好,但当画出凸轮轮廓线时,有曲率半径小于零的地方,故方案一不可行,选择滚子凸轮机构。
料筛方案:
方案一:
方案二:
选择:
选择方案二。
理由:
曲柄滑块机构能够实现料筛的往复运动,但不易实现料筛的间歇运动及筛料的过程。
凸轮机构能够很好的实现料筛的间歇运动,且能够实现筛料的过程。
故选用凸轮来控制料筛。
总方案:
根据以上分析可得最终方案如图4所示(六杆机构的曲柄与齿轮结合,由不完全齿轮实现机构的间歇)
图4
3、机构的运动分析与设计
1.上冲头设计
六杆机构的计算
设计数据:
六杆机构已知的数据如表4,六杆机构的中心距x,构件3的上下极限位置角ψ,ψ1,滑块5的行程H,曲柄的转速n,则要求的为各杆的长度,以及y的长度。
表4
X
(mm)
K
ψ
()
ψ1
()
H
(mm)
DE/CD
n
(r/min)
80
1.4
30
90
91
1.6
60
数值计算
第一步分析:
曲柄滑块机构
(1)尺寸计算
图5
将杆3,杆4,滑块5拆下来分析,将图顺时针旋转90°,如图5,以便于分析。
并以C点为原点,滑块5的道路方向为x轴方向,垂直方向为y轴方向。
对CDE分析:
由以上各式可求得:
对CDE分析:
由以上两式可求得:
且
由
联立求得:
(2)运动分析
对于图中所示的曲柄滑块机构已知曲柄的转速n1=60r/min,各从动构件的运动可由表5中所列公式求出。
计算结果见附件一,结果画出的滑块的速度、加速度曲线如图6所示。
此曲柄滑块机构为对心曲柄滑块机构,故无急回特性。
当曲柄不是匀速转动的时候便有了急回特性。
此时最大压力角为38°,小于40°,符合要求。
表5曲柄滑块机构运动分析
连杆2
滑块3
转角:
角速度:
角加速度:
其中:
位移:
速度:
加速度:
图6
第二步分析:
曲柄摇杆机构
曲柄滑块机构的曲柄在六杆机构中只做摆动,即曲柄摇杆机构的摇杆。
有上一步分析可得曲柄滑块中曲柄的长度,即曲柄摇杆中摇杆的长度。
由已知数据中的其急回系数为K=1.4,计算可得其极位夹角为,则对曲柄摇杆的设计及为已知摇杆的长度、两个极限位置,以及四杆机构的极位夹角,求各杆的长度,则可用图解法进行分析并求解。
如图7
图7
将图旋转180°,即为六杆机构时的机构,如图8
图8
对此四杆机构进行运动分析,分析数据见附件二,分析的速度、加速度曲线如图9
图9
求得=23,=62,=123,Y=92。
将此四杆机构在软件中计算得最大压力角为37°,符合压力角的要求,故此机构成立。
故可得=23,=62,=123,=196,即六杆机构的各个尺寸已求出,可画出六杆机构的精确结构如图10。
此六杆机构无间歇运动,可让曲柄由不完全齿轮带动,就实现其间歇运动(此齿轮的系数确定见附件三)。
图10
四杆机构的摇杆及曲柄滑块的曲柄,将曲柄滑块的曲柄位置改为四杆机构中摇杆的位置,将曲柄滑块的曲柄的速度改为四杆机构中摇杆的速度,可得出一组滑块的速度,加速度曲线,此速度与加速度曲线则为六杆机构中滑块的速度,加速度曲线,如图11。
由图可得,滑块向下运动的速度小于回来时的速度,即实现了急回特性。
图11
2.下冲头设计
下冲头采用滚子凸轮机构完成其动作。
根据循环图构造凸轮。
若直接使用循环图中的位移曲线,则有较大的刚性冲击,使得运动时有较大的惯性力,从而有震动。
为使凸轮工作时无突变的加速度,故计算时采用3—4—5多项式来计算位移。
计算时所用公式如表6,用excel表格计算,计算数据中有确定其位移、速度、加速度曲线,凸轮的理论廓线、实际廓线,确定基圆半径,计算压力角。
计算数据见附件二。
其位移、速度、加速度曲线,及凸轮理论廓线、实际廓线,如图12所示
表6凸轮计算公式
推程
回程
理论廓线:
实际廓线:
压力角:
图12
3.料筛的设计
料筛机构为滚子凸轮机构。
为使其运动时没有冲击,也是用3-4-5多项式计算位移,筛料的过程中也为3-4-5多项式,计算公式与下冲头相同,见表,计算出的数据表格见附件三,其位移、速度、加速度及凸轮理论廓线、实际廓线如图13
图13
(二)电动机的选择
1、正确选用电动机的基本原则:
1)电动机的机械特性、启动、制动、调速及其它控制性能应满足机械特性和生产工艺过程的要求,电动机工作过程中对电源供电质量的影响(如电压波动、谢波干扰等),应在容许的范围内;
2)按预定的工作制、冷却方法基辅在情况所确定的电动机功率,电动机的温升应在限定的范围内;
3)根据环境条件、运行条件、安装方式、传动方式,选定电动机的结构、安装、防护形式,保证电动机可靠工作;
4)综合考虑一次投资几运行费用,整个驱动系统经济、节能、合理、可靠和安全。
2、常用电动机的结构特征
1)Y系列三相异步电动机
该系列电机能防止水滴、灰尘、铁屑或其他杂物浸入电机内部,它是我国近年来研制成功的新型电动机。
2)电磁调速三相异步电动机
YCD电磁调速三相异步电动机,有组合式和整体式两种机构,这两种调速电动机为防护式,空气自冷,卧式安装,且无碳刷,集电环等滑动接触部件。
3、确定原动机的功率Pn
其中,Pw为工作机要求的功率;η为由电动机到工作机执行机构的总效率。
工作机要求的功率Pw主要为执行构件在单位时间里克服工作阻力所作的功。
在压片机中,主要为在单位时间里冲头冲压时克服工作阻力所作的功。
则
其中,Fr为冲头冲压时的工作阻力,主要发生在冲头下压的后半个行程中,且假定为线性变化,我们选择方案一,故行程结束时达到最大值60000N。
vC为冲头的运动速度,可以通过得曲柄滑块机构的运动分析得到(见附件一)。
由上式可以算得冲头在不同位置时,消耗的功率,列于表7。
可见最大值为15.5千瓦左右。
平均值为10千瓦左右,考虑机构中运动副的摩擦,参照电动机的技术数据选择Y160M-4电机。
输出功率N=11KW,转速n=1350r/min。
表7
Fr
vc
Pw
0
0.2500201
0
6666.667
0.2836218
1890.812
13333.33
0.3087638
4116.851
20000
0.3255634
6511.268
26666.67
0.3341589
8910.904
33333.33
0.3346993
11156.643
40000
0.3273508
13094.032
46666.67
0.3123069
14574.322
53333.33
0.2898106
15456.565
60000
0.2529884
15179.304
(三)传动机构的选择与减速器的设计
1、传动机构的选择
如何合理分配各级传动比,将直接影响传动装置的结构尺寸,重量,运行维护,造价及性能,这是设计过程中一个重要的问题,必须认真对待。
通常,不同类型的传动机构具有不同的传动比合理范围,同一种传动机构用于高速级和低速级时也具有不同的传动比合理范围。
因此,应使各级传动机构的传动比尽量在合理范围内。
各种传动机构的传动比合理范围如表8:
表8
性能指标
传动机构
带传动
链传动
齿轮传动
蜗杆传动
功率P/kW
小(<=20)
中(<=100)
中(最大达50)
小(<=50)
单级传动比:
常用值
最大值
2-4
5
2-5
6
3-5
8
10-40
80
传动效率
中
中
高
较低
许用线速度
<=25
<=40
6级精度直齿轮<=18,非直齿<=36
5级精度可达100
滑动速度
Vs<=50
综合上表,齿轮传动效率高最高,且许用线速度最大,故我们选择齿轮传动
2、减速器的设计
驱动电机的转速为1350r/min,冲压时曲柄的转速为60r/min,则机械传动系统的总传动比为:
采用二级齿轮传动。
齿轮的传动比常用值为3—5,在多级传动中,传动装置的总传动比是各级传动机构传动比的连乘积,即:
i=i1*i2*i3*i4……
根据传动比从小到大的顺序,选择一级传动比为9:
2,二级传动比为5:
1。
一级齿轮:
取Z1=20.Z2=,9/2×20=90
二级齿轮:
Z’2=17.Z3=5×17=85
(四)飞轮的设计
压片时冲头工作阻力的变化(如表7所示),造成机器的速度波动,必须通过加飞轮的方法进行调节。
将飞轮安在一级齿轮的小齿轮上。
轴的转速n=1360r/min,不均匀系数δ=0.1。
1、计算等效阻力矩Mr
粉料压片成形机的能量消耗,主要来自冲头冲压粉料时消耗的能量。
因此,可以忽略其它执行机构,以及各构件惯性力的影响,只考虑冲头的工作阻力Fr。
此时,机器的等效阻力矩为
其中,ω为电动机的角速度;vc为冲头往复直线运动的速度,滑块的速度可由六杆机构的运动分析中得到,Fr如表7中所示,则可画出其等效力矩曲线。
等效力矩随等效构件转角的变化曲线如图14所示。
其中横坐标为等效构件的转角,等效构件的转速为曲柄的22.5倍,所以等效力矩相对与等效构件的变化周期为T=50π=157s。
2、计算等效驱动力矩Md
根据能量守恒的原理,驱动力矩在一个周期里所做的功等于阻力矩在一个周期里消耗的功。
等效阻力矩消耗的功为等效阻力矩曲线下的面积,。
由曲线积分可得阻力矩消耗的功为W=1036J,则Md=W/T=1036/2π=165Nm。
图14
3.计算最大盈亏功[W]
其中,ΔWmax,ΔWmin分别为最大的赢功和最小的亏功,用积分的方法可得ΔWmax=256,ΔWmin=-467,可以算得[W]=256-(-256)=723J。
4.计算飞轮的转动惯量JF
5.确定飞轮的尺寸
对于如图15所示的轮形飞轮,其转动惯量可用下式表示
其中,D为飞轮轮缘的平均直径,m为飞轮的质量
其中,ρ为飞轮材质的密度。
取ρ=7800kg/m3
(五)心得体会
通过这次实践,我们将机械原理学的知识运用到实践中,充分的了解到了各个机构的作用以及如何充分并正确的利用机构。
此次实践中,在方案的选择中,我们用到了凸轮机构,曲柄滑块机构,并应用了以前没有接触过的机构——六杆机构。
以前在机械原理课上所学的只是理论的知识,并没有深刻的去了解每一个机构。
而做方案的选择时,需要去查资料了解每一个资料的功能及缺陷,以确定比较好的方案。
在查资料的时候,能够学到许多以前没有接触到的机构,并了解各个机构的突出功能及应用方向。
六杆机构就是在查资料的时候找到的。
虽然在课上没有接触到过,不知道怎么去计算,但我们还是选择去尝试,希望尽量将机构做到最好。
我们的机构共分成三个部分,两个凸轮,一个六杆机构。
在此过程中,我负责算六杆机构。
在一开始接触到六杆机构的时候,比较陌生,不知道从何入手。
同过查阅资料,找到了合适的计算方法。
然而在计算的过程中,出现了好多问题。
首先是我们的六杆机构与资料中的六杆机构略有不同,需要转化以后才能计算;其次,是六杆机构的数据不足,有些数据需要自己去假设,若假设不当,最后设计出的六杆机构会有死点,或者不存在。
在这个过程中,通过对各个数据的多次假设,计算出了最合适的方案。
同组的其他两个成员计算凸轮的时候,遇到了选择计算方式以及怎么转换的问题。
经过我们的讨论,选择了3—4—5多项式来计算。
接下来就是电动机的选择及减速器的设计,这些我们在机械原理中并没相关的内容,这些就需要由资料并参考老师给的模板来计算得到。
飞轮我们已经不再陌生,在机械原理课中,飞轮是重要的一课,但实践与做题有着很大的差别,在做题时,等效阻力矩等等一些数据都是题目给的,而实际的时候这些图以及数据都需要自己算。
将机构设计好以后,用workingmodel做了模拟。
以前的时候对这个软件并没有什么了解,当设计结束的时候,知道了其功能及怎么用。
在整个过程中,我深刻体会到了自学的作用以及学会查资料的重要性。
在整个过程中,查资料占了我们大部分的时间,但在查资料的过程中,我们收获了许多。
同时团体合作也十分重要。
团结是一个小组工作的核心,只有团结合作,合理分工,才能把这个任务做好。
(六)参考文献
[1]毛炳秋.机械设计课程设计[M].北京:
电子工业出版社,2011.
[2]邹慧君殷鸿梁.间歇运动机构设计与应用创新[M].北京:
机械工业出版社,2008.
[3]王霄刘会霞.UGNX5.0高级设计实例教程[M].北京:
化学工业出版社,2009.
[4]冯立艳.机械原理[M].北京:
机械工业出版社,2012.
[5]袁祖强.机械设计基础[M].北京:
北京航空航天大学出版社,2011.
[6]安琦.机械设计课程设计[M].上海:
华东理工大学出版社,2012.
附件一
曲柄滑块机构运动分析结果
φ(。
)
Φ2(。
)
ω2(rad/s)
ε2
XC(mm)
vc(mm/s)
ac(mm/s2)
0
0
-3.91096
0
318
1533.097
7737.77
10
-6.20506
-3.87424
-1.63192
314.9983
1510.668
7744.378
20
-12.2918
-3.76133
-3.08254
306.1494
1444.478
7761.322
30
-18.133
-3.56399
-4.15978
291.921
1338.022
7780.606
40
-23.5846
-3.26903
-4.66542
273.0856
1197.971
7791.614
50
-28.4781
-2.85998
-4.43705
250.7039
1036.086
7786.488
60
-32.6194
-2.32168
-3.44976
226.0848
873.3748
7767.256
70
-35.7967
-1.64916
-1.96129
200.7016
746.4426
7747.313
80
-37.8062
-0.85956
-0.57324
176.0425
703.9132
7738.586
90
-38.4952
0
0
153.4014
766.5486
7737.77
100
-37.8062
0.859564
-0.57324
133.6723
898.521
7738.586
110
-35.7967
1.649158
-1.96129
117.2487
1049.725
7747.313
120
-32.6194
2.321681
-3.44976
104.0848
1189.179
7767.256
130
-28.4781
2.859978
-4.43705
93.86372
1304.334
7786.488
140
-23.5846
3.269032
-4.66542
86.17078
1392.98
7791.614
150
-18.133
3.563993
-4.15978
80.61084
1457.259
7780.606
160
-12.2918
3.761326
-3.08254
76.86443
1500.369
7761.322
170
-6.20506
3.874244
-1.63192
74.70517
1525.064
7744.378
180
0
3.910962
0
74
1533.097
7737.77
190
6.205059
3.874244
1.631923
74.70517
1525.064
7744.378
200
12.29177
3.761326
3.082543
76.86443
1500.369
7761.322
210
18.13304
3.563993
4.159778
80.61084
1457.259
7780.606
220
23.58459
3.269032
4.665424
86.17078
1392.98
7791.614
230
28.47815
2.859978
4.437055
93.86372
1304.334
7786.488
240
32.61944
2.321681
3.449756
104.0848
1189.179
7767.256
250
35.79668
1.649158
1.961285
117.2487
1049.725
7747.313
260
37.8062
0.859564
0.573239
133.6723
898.521
7738.586
270
38.49519
0
0
153.4014
766.5486
7737.77
280
37.8062
-0.85956
0.573239
176.0425
703.9132
7738.586
290
35.79668
-1.64916
1.961285
200.7016
746.4426
7747.313
300
32.61944
-2.32168
3.449756
226.0848
873.3748
7767.256
310
28.47815
-2.85998
4.437055
250.7039
1036.086
7786.488
320
23.58459
-3.26903
4.665424
273.0856
1197.971
7791.614
330
18.13304
-3.56399
4.159778
291.921
1338.022
7780.606
340
12.29177
-3.76133
3.082543
306.1494
1444.478
7761.322
350
6.205059
-3.87424
1.631923
314.9983
1510.668
7744.378
360
0
-3.91096
0
318
1533.097
7737.77