大气课程设计.docx
《大气课程设计.docx》由会员分享,可在线阅读,更多相关《大气课程设计.docx(18页珍藏版)》请在冰豆网上搜索。
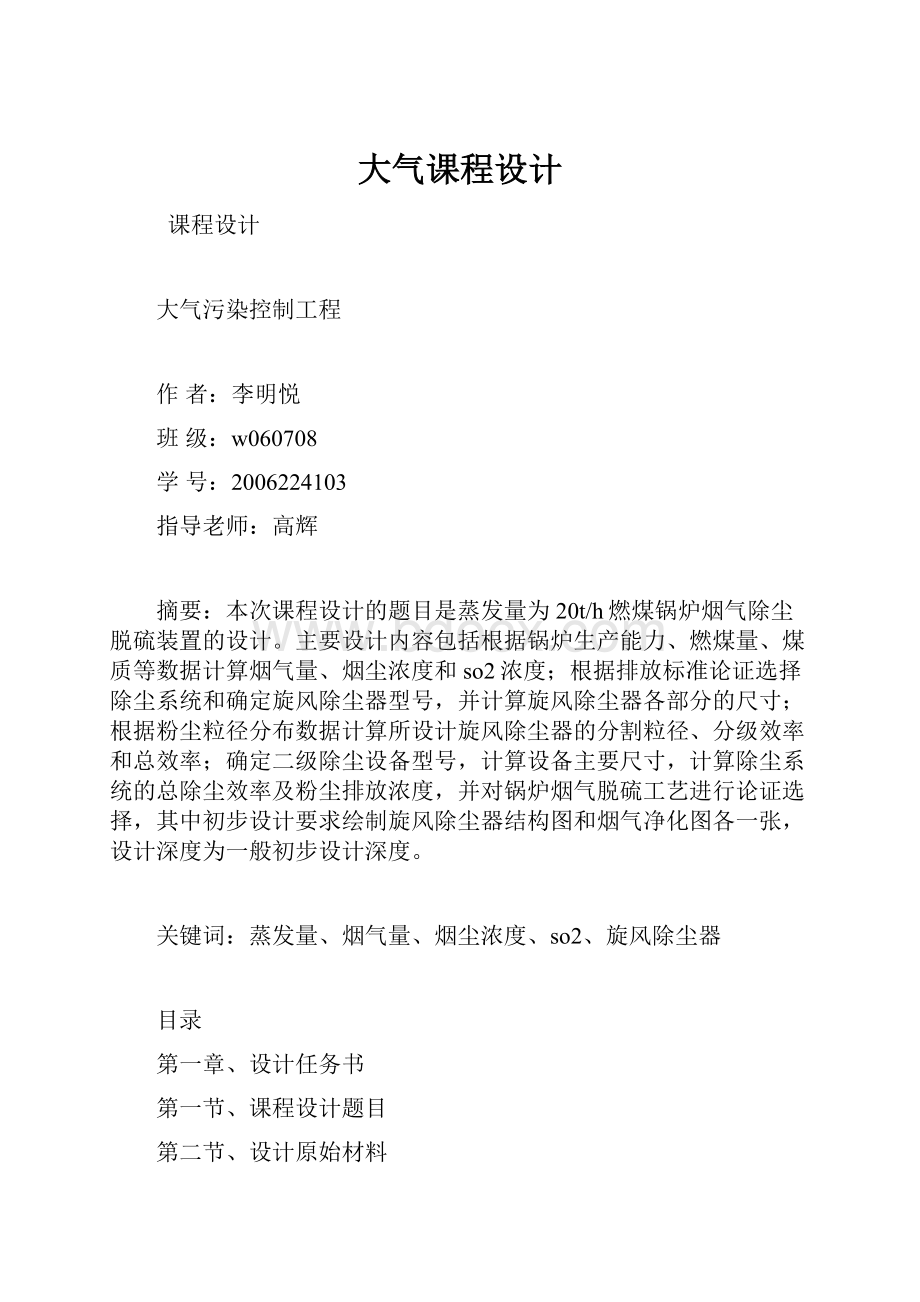
大气课程设计
课程设计
大气污染控制工程
作者:
李明悦
班级:
w060708
学号:
2006224103
指导老师:
高辉
摘要:
本次课程设计的题目是蒸发量为20t/h燃煤锅炉烟气除尘脱硫装置的设计。
主要设计内容包括根据锅炉生产能力、燃煤量、煤质等数据计算烟气量、烟尘浓度和so2浓度;根据排放标准论证选择除尘系统和确定旋风除尘器型号,并计算旋风除尘器各部分的尺寸;根据粉尘粒径分布数据计算所设计旋风除尘器的分割粒径、分级效率和总效率;确定二级除尘设备型号,计算设备主要尺寸,计算除尘系统的总除尘效率及粉尘排放浓度,并对锅炉烟气脱硫工艺进行论证选择,其中初步设计要求绘制旋风除尘器结构图和烟气净化图各一张,设计深度为一般初步设计深度。
关键词:
蒸发量、烟气量、烟尘浓度、so2、旋风除尘器
目录
第一章、设计任务书
第一节、课程设计题目
第二节、设计原始材料
第二章、设计方案的选择确定
第一节、除尘系统的论证选择
第二节、旋风除尘器
第三节、布袋除尘器
第三章、锅炉烟气脱硫装置的论证选择
第一节、脱硫工艺及脱硫吸收器比较选择
第二节、脱硫吸收器比较选择
第三节、脱硫除尘原理
第四节、脱硫除尘工艺设计
第五节、风机和泵的选用及节能设备
第四章、结果综合评价
第一节、方案的优势
第二节、方案的可持性
第一章、设计任务书
第一节、课程设计题目
设计蒸发量为20t/h的燃煤锅炉烟气的除尘脱硫装置
第二节、设计原始材料
1、.煤的工业分析如下表(质量比,含N量不计):
低位发热量(KJ/Kg)
C
H
S
O
灰分
水分
20939
65.7%
3.2%
1.7%
2.3%
18.1%
9.0%
2、锅炉型号:
FG-35/3.82-M型
3、锅炉热效率:
75%
4、空气过剩系数:
1.2
5、水的蒸发热:
2570.8KJ/Kg
6、烟尘的排放因子:
30%
7、烟气温度:
473K
8、烟气密度:
1.18kg/m3
9、烟气粘度:
2.4×106pa·s
10、尘粒密度:
2250kg/m3
11、烟气其他性质按空气计算
12、烟气中烟尘颗粒粒径分布:
平均粒径/μm
0.5
3
7.5
15
25
35
45
55
>60
粒径分布/%
3
20
15
20
16
10
6
3
7
13、按锅炉大气污染物排放标准(GB13217-2001)中二类区标准执行:
标准状态下烟尘浓度排放标准:
≤200mg/m3;
标准状态下SO2排放标准:
≤900mg/m3。
第二章、设计方案的选择确定
第一节、除尘系统的论证选择
(1)锅炉烟气含尘、含硫量计算
利用低位发热量、锅炉热效率、水的蒸发热求需煤量,如下:
蒸发量为20t/h的锅炉所需热量为:
2570.8×20×103=51.4×106KJ/h
需煤量:
(51.4×106)/(20939×75%)=3.3×103(Kg/h)=3.3t/h
设1kg燃煤燃烧为基础,则:
如下表:
燃料成分名称
可燃成分含量(﹪)
可燃成分的量(﹪)
理论需氧量/mol
废气中组分/mol
C
H
S
O
水
灰分
65.7
3.2
1.7
2.3
9.0
18.1
54.75
16
0.53
——
——
——
54.75
8
0.53
-0.75
——
——
54.75CO2
16H2O
0.53SO2
——
5H2O
——
合计
62.56
理论烟气量:
62.56+62.56×0.79/0.21=297.9(mol/kg)
在标准状态下的体积为:
297.9×22.4×10-3=6.67(m3/kg)
理论废气量:
62.56×0.79/0.21+54075+16+0.53+5+311.62mol/kg
在标准状态下理论废气体积:
311.62×22.4×10-3=6.98(m3)
在标准状态下实际烟气体积:
6.98+6.67×(1.2-1)=8.31(m3)
SO2的浓度:
C=4082mg/m3
烟尘的浓度:
C=6534mg/m3
在473T时实际烟气量:
Q=47951m3/h
(2)烟尘的除尘效率计算
按锅炉大气污染物排放标准(GB13217-2001),可
计算出:
烟尘的除尘效率要达到:
≧97﹪
(3)SO2的脱硫效率计算
按锅炉大气污染物排放标准(GB13217-2001)计
出SO2的脱硫效率要达到:
≧78﹪
(4)方案初步设计
先用二级除尘系统除尘(一级预除尘用旋风除尘、
二级用袋式除尘器),再用旋流板塔氧化镁法脱硫。
注:
考虑到压损过大对除尘器的不利影响和对操作
要求高,作为一级预除尘除尘要求不高,因此,确
旋风除尘器型号时要求阻力不大于900Pa。
第二节、旋风除尘器
(1)旋风除尘器的工作原理、应用及特点
A.旋风除尘器是利用旋转气流所产生的离心力将尘粒从合尘气流中分离出来的除尘装置。
它具有结构简单,体积较小,不需特殊的附属设备,造价较低.阻力中等,器内无运动部件,操作维修方便等优点。
旋风除尘器一般用于捕集5-15微米以上的颗粒.除尘效率可达80%以上,近年来经改进后的特制旋风除尘器.其除尘效率可达95%以上。
旋风除尘器的缺点是捕集微粒小于5微米的效率不高.
B.旋风除尘器内气流与尘粒的运动概况:
旋转气流的绝大部分沿器壁自圆简体,呈螺旋状由上向下向圆锥体底部运动,形成下降的外旋含尘气流,在强烈旋转过程中所产生的离心力将密度远远大于气体的尘粒甩向器壁,尘粒一旦与器壁接触,便失去惯性力而靠入口速度的动量和自身的重力沿壁面下落进入集灰斗。
旋转下降的气流在到达圆锥体底部后.沿除尘器的轴心部位转而向上.形成上升的内旋气流,并由除尘器的排气管排出。
自进气口流人的另一小部分气流,则向旋风除尘器顶盖处流动,然后沿排气管外侧向下流动,当达到排气管下端时,即反转向上随上升的中心气流一同从诽气管排出,分散在其中的尘粒也随同被带走。
(2)旋风除尘器的结构设计及选用
1、尺寸计算
A.烟气处理量:
Q=47951(m3/h)
B.初步选用XLP/B型旋风除尘器,处理烟气量大,将选用10个并联,取ξ=5.8
每个烟气处理量:
47951/10=4795.1(m3/h)
在这里取u=16.2m/s、△P=876﹤900
进口面积A=Q/3600u1=4795.1/(16.2×3600)=0.0822m2
根据XLP/B型旋风除尘器尺寸比例
入口高度h=(2×A)0.5=0.045m
入口宽度b=(A/2)0.5=0.202m
筒体直径D=3.33b=0.673m=673mm
参考XLP/B型旋风除尘器产品系列①,取D=700mm,
de=0.6D=0.6×700=420mm
L=1.7D=1.7×700=1190mm
H=2.3D=2.3×700=1610mm
d1=0.43D=0.43×700=301mm
XLP/B型旋风除尘器外形尺寸
C.选型论证
a×b=0.0882m2
u=Q/A=15.1m/s
△P=ξu2ρ/2=780.2
因为采用的是并联,所以要乘一个压力系数变化:
780.2×1.1=859Pa﹤900Pa符合要求。
(3)XLP/B型旋风除尘器的分割粒径、分级效率和总效率的计算:
bc50=0.27(μD/3.14(ρp-ρ)u=6(μm)
平均粒径/μm
0.5
3
7.5
15
25
35
45
55
>60
粒径分布/%
3
20
15
20
16
10
6
3
7
分级效率/%
13.3
35.9
54.9
70.9
81.9
87.9
91.6
94
100
总效率/%
67.2
经过预除尘后(一级处理),烟尘浓度是:
6534×(1-67.2﹪)=2144mg/m3
二级除尘的效率将要达到:
(2144-200)/2144=90.67%
(4)二级除尘设备的论证选择
在选择除尘技术时,应充分考虑经济性、可靠性、适用性和社会性等方面的影响。
除尘技术的确定受到当地条件、现场条件、燃烧煤种特性、排放标准和需要达到的除尘效率等多种因素的影响。
针对目前环保要求、污染物排放费用的征收情况以及静电除尘器和布袋除尘器在性能上的差异和在各行各业应用的实际情况,对两种除尘器在实际应用中的基本性能做一个简单客观的对比:
1)除尘效率
布袋除尘器:
对人体有严重影响的重金属粒子及亚微米级尘粒的捕集更为有效。
通常除尘效率可达99.99%以上,排放烟尘浓度能稳定低于50mg/Nm3,甚至可达10mg/Nm3以下,几乎实现零排放。
从目前电力行业燃煤锅炉应用的情况来看,布袋除尘器的排放能保证在30mg/Nm3以下。
呼和浩特电厂两台200MW机组的锅炉烟气净化采用了布袋除尘器,从CEMS系统长期自动监测的结果和权威检测单位的测试人员人工采样测试的结果来看,排放浓度均低于27mg/Nm3。
电除尘器:
随着国家环保标准的进一步提高和越来越多的电厂燃用低硫煤(或者经过了高效脱硫),比电阻大,即使达标也变得越来越困难。
而布袋除尘器的过滤机理决定了它不受燃烧煤种物化性能变化的影响,具有稳定的除尘效率。
针对目前国家环保的排放标准和排放费用的征收办法,布袋除尘器所带来的经济效益是显而易见的。
2)系统变化对除尘器的影响
燃煤电厂的煤种相对稳定,但也不能避免遇到煤种或煤质发生变化的时候;锅炉系统是一个经常变动和调节的系统,因此从锅炉中出来的烟气物化性能、烟尘浓度、温度等参数也不能保证不发生变化。
这一系列的变化,针对不同的除尘器会引起明显不同的变化。
下面从主要的几个方面进行对比:
(1)送、引风机风量不变,锅炉出口烟尘浓度变化
A.除尘器:
烟尘浓度的变化只引起布袋除尘器滤袋负荷的变化,从而导致清灰频率改变(自动调节)。
烟尘浓度高滤袋上的积灰速度快,相应的清灰频率高,反之清灰频率低,而对排放浓度不会引起变化。
B.对静电除尘器:
烟尘浓度的变化直接影响粉尘的荷电量,因此也直接影响了静电除尘器的除尘效率,最终反映在排放浓度的变化上。
通常烟尘浓度增加除尘效率提高,排放浓度会相应增加;烟尘浓度减小除尘效率降低,排放浓度会相应降低。
(2)锅炉烟尘量不变,送、引风机风量变化
A.对布袋除尘器:
由于风量的变化直接引起过滤风速的变化,从而引起设备阻力的变化,而对除尘效率基本没有影响。
风量加大设备阻力加大,引风机出力增加;反之引风机出力减小。
B.对静电除尘器:
风量的变化对设备没有什么太大影响,但是静电除尘器的除尘效率随风量的变化非常明显。
若风量增大,静电除尘器电场风速提高,粉尘在电场中的停留时间缩短,虽然电场中风扰动增强了荷电粉尘的有效驱进速度,但是这不足以抵偿高风速引起的粉尘在电场中驻留时间缩短和二次扬尘加剧所带来的负面影响,因此除尘效率降低非常明显;反之,除尘效率有所增加,但增加幅度不大。
(3)温度的变化
A.对布袋除尘器:
烟气温度太低,结露可能会引起“糊袋”和壳体腐蚀,烟气温度太高超过滤料允许温度易“烧袋”而损坏滤袋。
但是如果温度的变化是在滤料的承受温度范围内,就不会影响除尘效率。
引起不良后果的温度是在极端温度(事故/不正常状态)下,因此对于布袋除尘器就必须设有对极限温度控制的有效保护措施。
B.对静电除尘器:
烟气温度太低,结露就会引起壳体腐蚀或高压爬电,但是对除尘效率是有好处的;烟气温度升高,粉尘比电阻升高不利于除尘。
因此烟气温度直接影响除尘效率,且影响较为明显。
第三节、布袋除尘器
1、袋式除尘器的工作原理、应用及特点
常用袋式除尘器有简易袋除尘器、机械振打袋式除尘器、脉冲喷吹袋式除尘器和气环式袋式除尘器。
(1)机械振打袋式除尘器
是利用机械装置使滤袋产生振动而清灰的袋式除尘器。
此类除尘器的特点是施加于粉尘层的动能较少而次数较多,因此要求滤料薄而光滑,质地柔软,有利于传递振动,在过滤面上生成足够的振动力。
结构及工作原理中部振打袋式除尘器,又称ZX型袋式除尘器。
基本部件由滤袋、箱体、灰斗、振打清灰装置、进出风管及螺旋输送机等部分组成。
含尘气体由灰斗上部进入,然后向上进入滤袋,粉尘积于滤袋内表面,净气经滤料由阀箱向外排出。
箱体由隔板分成相等滤袋数目的多个仓,袋底开口,并固定于底板的短管上,袋顶由帽盖封闭,并悬吊在振打机构的吊架上。
箱体的顶盖上装有阀箱及振打机构。
特点:
具有较高、稳定的除尘效率和较低的阻力,构造简单,滤袋装卸方便,维护容易,应用范围较广,适用于常温气体的过滤。
(2)脉冲袋式除尘器
脉冲袋式除尘器有侧喷脉冲、顺喷脉冲、对喷
脉冲、气箱脉冲、大型分室脉冲、旁插扁袋脉冲、离线脉冲、回转清灰脉冲袋式除尘器等多种形式。
工作原理:
含尘空气进气口进入除尘箱,因气体突然扩张,流速骤然降低,颗料较粗的粉尘,靠其自重力向下沉降,落入灰斗。
细小粉尘通过各种效应被吸附在滤袋外壁,经滤袋过滤后的净化空气,通过文氏管进入上箱体,从出气口排出,被吸附在滤袋外壁的粉尘,随着时间的增长,越积越厚,除尘器阻力逐渐上升,处理的气体量不断减少,为了使除尘器经常保持有效状态,设备阻力稳定在一定的范围内,就需要清除吸附在滤袋外面的积灰。
消灰过程是由控制仪按规定要求对各个电磁脉冲阀发出指令,依次打开阀门,顺序向各组滤袋内喷吹高压空气。
于是,气包内压缩空气经由喷吹管的孔眼穿过文氏管进入滤袋(称为一次风)。
而当喷吹的高速气流通过文氏管—引射器的一刹那,数位于一次的周围空气被诱导同时进入袋内(称二次风)。
由于这一、二次风形成一股与过滤气流相反的强有力逆向气流射入袋内,使滤袋在一瞬间急剧从收缩—膨胀—收缩,以及气流反向作用,逐将吸附在袋壁外面的粉尘清除下来。
由于清灰时向袋内喷吹高压空气是在几组滤袋间依次进行的,并不切断需要处理的含尘空气。
所以
在清灰过程中,除尘器的压力损失和被处理的含尘气体量都几何不变。
这一点就是脉冲袋式除尘器的先进性之一。
特点:
清灰方式作用强度很大,而且其强度和频率都可以调节,所以清灰效果好。
(3)气环式风袋式除尘器
含尘气体从上部进入顶部的分布室,均匀进入各个滤袋内,净化后的气体经排气管排出。
吸附在滤袋内壁的粉尘和纤维缝中的粉尘,被气环箱喷出的高速空气吹落,吹落的粉尘沉降到集灰斗中,经输送机械送走。
气环箱紧贴滤袋靠机械传动装置作周期性上下移动,每移动一次,即完成一次清灰过程。
气环反吹袋式除尘器的主要特点:
适用于高湿度、高浓度的含尘气体;可采用小型高压鼓风机作为气源,过滤风速大,投资省,由于装在机体外部,所以维修管理方便;不需要高精度的控制仪表,造价较低。
主要缺点:
气环箱上下移动时紧贴滤袋,使滤袋磨损加快,故障率较高。
它的性能如见下表:
除尘种类
概略除尘效率﹪
适用净化程度
经济指标
使用年限
粒径/μm
投资
耗钢量
/kg.m-3
其他(水、电、压缩空气)
﹤1
1~5
5~10
简易袋除尘器
﹤30
﹤80
﹤95
中细净化
较大
较少
少量电能
取决于滤布的性能
机械振打袋式
﹤90
﹤99
﹤99
较大
0.1~0.25
少量电能
脉冲喷吹袋式
﹤90
﹤99
﹤99
中
0.1~0.2
少量电能及压缩空气
气环式袋
﹤90
﹤99
﹤99
中
综合比较,将选用旋风除尘器来设计。
第三章、锅炉烟气脱硫装置的论证选择
目前,世界上烟气脱硫工艺有上百种,但具有实用价值的工艺仅十几种。
根据脱硫反应物和脱硫产物的存在状态可将其分为湿法、干法和半干法3种。
湿法脱硫工艺应用广泛,占世界总量的85.0%,其中氧化镁法技术成熟,尤其对中、小锅炉烟气脱硫来说,具有投资少,占地面积小,运行费用低等优点,非常适合我国的国情。
采用湿法脱硫工艺,要考虑吸收器的性能,其性能的优劣直接影响烟气的脱硫效率、系统的运行费用等。
旋流板塔吸收器具有负荷高、压降低、不易堵、弹性好等优点,可以快速吸收烟尘,具有很高的脱硫效率。
第一节、脱硫工艺及脱硫吸收器比较选择
(1)脱硫除尘工艺比较选择(见下表)
项目
石灰石/石膏湿法脱硫工艺
双碱法脱硫工艺
氧化镁脱硫工艺
喷雾干燥法脱硫工艺
氨法脱硫工艺
循环流化床脱硫工艺
工艺形式
湿法
湿法
湿法
半干法
干法
干法
脱硫剂
石灰石
镁基和钠基石灰
氧化镁
石灰
氨
石灰石
副产物状态
湿态
湿态
湿态
干态
干态
干态
烟煤含硫量
无限制
可适用高硫煤1%左右
无限制
中、低硫煤
高硫煤
中、低硫煤
脱硫率
高
高
高
一般
高
一般
适用范围
大容量
最大装机容量1000MW
大容量
试验中等容量
最大200MW机组
中、小容量
投资
中
中
低
中
低
中
运行费
中
低
低
高
低
中
脱硫工艺
湿法
半干法
干法
石灰石/石膏湿法
钠法
双碱法
氧化镁
氨法
海水法
喷雾干燥法
炉内喷钙
循环流化床
等离子体
脱硫效率﹪
90-98
90-98
90-98
90-98
90-98
70-90
70-85
60-75
60-90
≧90
吸收剂
CaCO3
NaOH
NaCO3
NaOH
Mg(OH)2
CaO
MgO
NH3
海水
CaO
CaO
CaO
NH3
可靠性
高
高
高
高
一般
高
一般
一般
高
高
结垢
易结垢
不结垢
不结垢
不结垢
不结垢
不结垢
易结垢
易结垢
易结垢
不结垢
堵塞
堵塞
不堵塞
不堵塞
不堵塞
不堵塞
不堵塞
堵塞
堵塞
堵塞
不堵塞
占地面积
大
小
中
小
大
中
中
中
中
中
第二节、脱硫吸收器比较选择
脱硫吸收器的选择原则,主要是看其液气接触条件、设备阻力以及吸收液循环量。
脱硫吸收器比较选择下表所示。
吸收器类型
持液量
逆流接触
防堵性能
操作弹性
压降
除尘性能
喷淋塔
低
是
差
好
低
差
筛板塔
高
是
中
中
高
好
填料塔
中
是
差
好
中
差
湍球塔
高
是
差
差
高
好
旋流板塔
高
是
好
好
低
好
吸收设备中:
喷淋塔液气比高,水消耗量大;筛板塔阻力较大,防堵性能差;填料塔防堵性能差,易结垢、黏结、堵塞,阻力也较大;湍球塔气液接触面积虽然较大,但易结垢堵塞,阻力较大。
相比之下,旋流板塔具有负荷高、压降低、不易堵、弹性好等优点,适用于快速吸收过程,且具有很高的脱硫效率。
因此,选用旋流板塔脱硫吸收器。
第三节、脱硫除尘原理
(1)氧化镁法脱硫原理
氧化镁法脱硫的主要原理:
在洗涤中采用含有MgO的浆液作脱硫剂,MgO被转变为亚硫酸镁(MgSO3)和硫酸镁(MgSO4),然后将硫从溶液中脱除。
氧化镁法脱硫工艺有如下特点:
A、氧化镁法脱硫工艺成熟,目前日本、中国台湾应用较多,国内近年有一些项目也开始应用。
B、脱硫效率在90.0%~95.0%之间。
C、脱除等量的SO2,MgO的消耗量仅为CaCO3的40.0%。
D、要达到90.0%的脱硫效率,液气比在3~5L/m3之间,而石灰石-石膏工艺一般要在10~15L/m3之间。
E、我国MgO储量约80亿t,居世界首位,生产量居世界第一。
第四节、脱硫除尘工艺设计
(1)主要设计参数
主要设计参数:
处理烟气量47951m3/h;烟气温度150~160℃;脱硫除尘塔入口烟温150~160℃;脱硫除尘塔出口烟温55℃;脱硫塔入口烟气SO2浓度4082mg/m3 (计算值);脱硫效率>83.0%(设计值);脱硫剂氧化镁粉>200目,纯度>90.0%;液气比2~3L/m3;脱硫剂耗量23kg/h(max);脱硫剂浆液浓度10.0%。
除尘效率86%(设计值)。
(2)脱硫除尘工艺设计说明
烟气脱硫除尘工艺可分为脱硫剂配制系统、烟气脱硫除尘系统和循环水系统三大部分。
锅炉烟气从烟道切向进入主塔底部,在塔内螺旋上升中与沿塔下流的脱硫液接触,进行脱硫除尘,经脱水板除雾后,由引风机抽出排空。
脱硫液从旋流板塔上部进入,在旋流板上被气流吹散,进行气液两相的接触,完成脱硫除尘后从塔底流出,通过明渠流到综合循环池。
(3)脱硫剂制备系统工艺流程设计说明
脱硫剂MgO乳液的制备系统主要由螺旋给料机、乳液贮槽、搅拌机、乳液泵等组成。
(4)脱硫除尘工艺设备设计说明
旋流板塔:
脱硫除尘塔(旋流板塔)塔体采用麻石砌筑,主塔平台、支架、梯子等为碳钢,塔内件包括喷头、旋流板、脱水器、检修孔、支架、接管,这些物件均采用316L不锈钢材质,以确保整套装置的使用寿命。
设备外径为2540mm(塔壁厚220mm),高度为17000mm。
(5)烟气排放分析
经湿法脱硫洗涤净化后的冷烟气经脱水器脱水后,温度降至露点以下,通常为50~60℃,所含水蒸气已近饱和,极易结露,对后续烟道腐蚀性较大,采用蒸汽再热器提高烟气扩散温度(≥80℃)后经烟囱排放。
通过对锅炉烟气污染物净化,最终排放烟气中污染物浓度预计为:
SO2≤500mg/m3,烟尘≤100mg/m3。
第五节、风机和泵的选用及节能设备
通风机选用G4-73-11-No11D型(转速(r/min):
730)2个
引风机选用Y4-73-11-No12D型(转速(r/min):
960)1个
水泵5个
乳液水泵1个
热交换器1个
第四章、结果综合评价
第一节、方案的优势
1、最终排放烟气中污染物浓度预计为:
SO2≤500mg/m3,烟尘≤100mg/m3。
不仅低于排放标准,而且在以后10年内排放标准再严格也有适用。
2、经过一级除尘后,除去大部分粗粉尘,对后面的二级除尘起了很大的作用。
除尘效果更好,对二级除尘器的损害,有很好的保护,从而降低对仪器的维修费用,提高仪器的使用寿命。
3、经过二级除尘,设计总除尘效率达到96﹪,降低压损,减少对滤袋、除尘仪器都有不利的影响,降低仪器的操作要求和运行耗能。
为企业创造更多的收益。
4、废气经过二级除尘系统后,除尘效率可以达到97﹪以上,已达到烟尘排放标准(≦200mg/m3),再经过后面的旋流板塔氧化镁湿法脱硫工艺,预计可以达到99﹪,使用本方案烟尘排放不会超标。
第二节、方案的可持性
1.经过二级除尘,设计总除尘效率达到96﹪,降低压损,减少对滤袋、除尘仪器都有不利的影响,降低仪器的操作要求和运行耗能。
同时也为以后的排放标准更为严格留