保证装配精度的四种装配方法.docx
《保证装配精度的四种装配方法.docx》由会员分享,可在线阅读,更多相关《保证装配精度的四种装配方法.docx(7页珍藏版)》请在冰豆网上搜索。
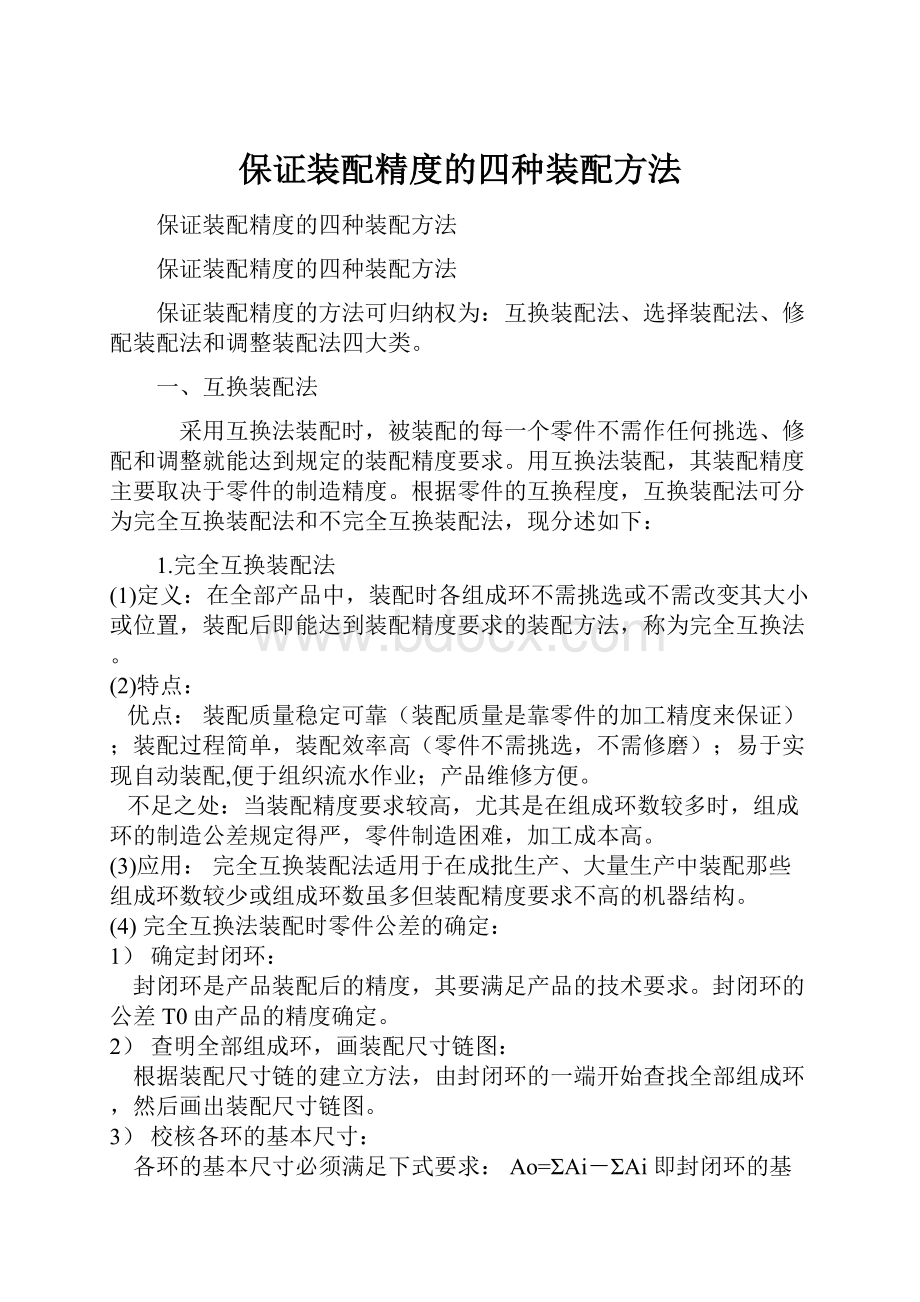
保证装配精度的四种装配方法
保证装配精度的四种装配方法
保证装配精度的四种装配方法
保证装配精度的方法可归纳权为:
互换装配法、选择装配法、修配装配法和调整装配法四大类。
一、互换装配法
采用互换法装配时,被装配的每一个零件不需作任何挑选、修配和调整就能达到规定的装配精度要求。
用互换法装配,其装配精度主要取决于零件的制造精度。
根据零件的互换程度,互换装配法可分为完全互换装配法和不完全互换装配法,现分述如下:
1.完全互换装配法
(1)定义:
在全部产品中,装配时各组成环不需挑选或不需改变其大小或位置,装配后即能达到装配精度要求的装配方法,称为完全互换法。
(2)特点:
优点:
装配质量稳定可靠(装配质量是靠零件的加工精度来保证);装配过程简单,装配效率高(零件不需挑选,不需修磨);易于实现自动装配,便于组织流水作业;产品维修方便。
不足之处:
当装配精度要求较高,尤其是在组成环数较多时,组成环的制造公差规定得严,零件制造困难,加工成本高。
(3)应用:
完全互换装配法适用于在成批生产、大量生产中装配那些组成环数较少或组成环数虽多但装配精度要求不高的机器结构。
(4)完全互换法装配时零件公差的确定:
1)确定封闭环:
封闭环是产品装配后的精度,其要满足产品的技术要求。
封闭环的公差T0由产品的精度确定。
2)查明全部组成环,画装配尺寸链图:
根据装配尺寸链的建立方法,由封闭环的一端开始查找全部组成环,然后画出装配尺寸链图。
3)校核各环的基本尺寸:
各环的基本尺寸必须满足下式要求:
Ao=ΣAi-ΣAi即封闭环的基本尺寸等于所有增环的基本尺寸之和减去所有减环的基本尺寸之和。
4)决定各组成环的公差:
各组成环的公差必须满足下式的要求:
To≥ΣTi即各组成环的公差之和不允许大于封闭环的公差。
各组成环的平均公差Tp可按下式确定:
Tp=To/m式中:
m----为组成环数。
各组成环公差的分配应考虑以下因素:
a)孔比轴难加工,孔的公差应比轴的公差选择大一些;例如:
孔、轴配合H7/h6。
b)尺寸大的零件比尺寸小的零件难加工,大尺寸零件的公差取大一些;
c)组成环是标准件尺寸时,其公差值是确定值,可在相关标准中查询。
5)决定各组成环的极限偏差:
a)先选定一组成环作为协调环:
协调环一般选择易于加工和测量零件尺寸;
b)包容尺寸(如孔)按基孔制确定其极限偏差:
即下偏差为0;
c)被包容尺寸(如轴)按基轴制确定其极限偏差:
即上偏差为0。
6)协调环的极限偏差的确定:
根据中间偏差的计算公式:
△0=Σ△i-Σ△j
式中:
△0---为封闭环的中间偏差,△0=(ES0+EI0)/2;
Σ△i、Σ△j---分别为所有增环的中间偏差之和、
为外尺寸,按基轴制确定极限偏差:
A1=300-0.06A2=50-0.04A3为内尺寸,按基孔制确定极限偏差:
A3=43+0.070
(6)协调环的极限偏差的确定:
封闭环的中间偏差为:
△0=(0.35+0.1)/2=0.225
各组成环的中间偏差为:
△1=(0-0.06)/2=-0.03
△2=(0-0.04)/2=-0.02
△3=(0.07+0)/2=0.035
△4=(0-0.05)/2=--0.025
由:
△0=△3-(△1+△2+△4+△5)得:
△5=△3-(△1+△2+△4+△0)=0.035-(--0.03-0.02--0.025+0.225)=--0.115
协调环A4的极限偏差为:
ES=△5+T5/2=--0.115+0.03/2=-0.10EI=△5-T5/2=-0.115-0.03/2=-0.13
所以有:
A5=5-0.10-0.13。
2.统计互换装配法(不完全互换装配法)
用完全互换法装配,装配过程虽然简单,但它是根据增环、减环同时出现极值情况来建立封闭环与组成环之间的尺寸关系的,由于组成环分得的制造公差过小常使零件加工产生困难。
完全互换法以提高零件加工精度为代价来换取完全互换装配有时是不经济的。
统计互换装配法又称不完全互换装配法,其实质是将组成环的制造公差适当放大,使零件容易加工,但这会使极少数产品的装配精度超出规定要求,但这种事件是小概率事件,很少发生。
尤其是组成环数目较少,产品批量大量,从总的经济效果分析,仍然是经济可行的。
统计互换装配方法的优点是:
扩大了组成环的制造公差,零件制造成本低;装配过程简单,生产效率高。
不足之处是:
装配后有极少数产品达不到规定的装配精度要求,须采取另外的返修措施。
大数互换装配方法适用于在大批大量生产中装配那些装配精度要求较高且组成环数又多的机器结构。
二、选择装配法
1、选择装配法定义:
是将装配尺寸链中组成环的公差放大到经济可行的程度,然后选择合适的零件进行装配,以保证装配精度要求的装配方法,称为选择装配法。
适用场合:
装配精度要求高,而组成环较少的成批或大批量生产。
2、选择装配法种类
•直接选配法:
(1)定义:
在装配时,工人从许多待装配的零件中,直接选择合适的零件进行装配,以保证装配精度要求的选择装配法,称为直接选配法。
(2)特点:
1)装配精度较高;2)装配时凭经验和判断性测量来选择零件,装配时间不易准确控制;3)装配精度在很大程度上取决于工人的技术水平。
•分组选配法:
(1)定义:
将各组成环的公差相对完全互换法所求数值放大数倍,使其能按经济精度加工,再按实际测量尺寸将零件分组,按对应的组分别进行装配,以达到装配精度要求的选择装配法,称为分组选配法。
(2)应用:
在大批大量生产中,装配那些精度要求特别高同时又不便于采用调整装置的部件,若用互换装配法装配,组成环的制造公差过小,加工很困难或很不经济,此时可以采用分组选配法装配。
(3)分组选配法的一般要求:
1)采用分组法装配最好能使两相配件的尺寸分布曲线具有完全相同的对称分布曲线,如果尺寸分布曲线不相同或不对称,则将造成各组相配零件数不等而不能完全配套,造成浪费。
2)采用分组法装配时,零件的分组数不宜太多,否则会因零件测量、分类、保管、运输工作量的增大而使生产组织工作变得相当复杂。
(4)分组法装配的特点:
主要优点是:
零件的制造精度不高,但却可获得很高的装配精度;组内零件可以互换,装配效率高。
不足之处是:
增加了零件测量、分组、存贮、运输的工作量。
分组装配法适用于在大批大量生产中装配那些组成环数少而装配精度又要求特别高的机器结构。
三、修配装配法
1、定义:
是将装配尺寸链中各组成环按经济加工精度制造,装配时,通过改变尺寸链中某一预先确定的组成环尺寸的方法来保证装配精度的装配法,称为修配装配法。
采用修配法装配时,各组成环均按该生产条件下经济可行的精度等级加工,装配时封闭环所积累的误差,势必会超出规定的装配精度要求;为了达到规定的装配精度,装配时须修配装配尺寸链中某一组成环的尺寸(此组成环称为修配环)。
为减少修配工作量,应选择那些便于进行修配的组成环做修配环。
在采用修配法装配时,要求修配环必须留有足够但又不是太大的修配量。
2、修配装配法的特点:
主要优点是:
组成环均可以加工经济精度制造,但却可获得很高的装配精度。
不足之处是:
增加了修配工作量,生产效率低;对装配工人的技术水平要求高。
3、应用:
修配装配法适用于单件小批生产中装配那些组成环数较多而装配精度又要求较高的机器结构。
四、调整装配法
1、定义:
装配时用改变调整件在机器结构中的相对位置或选用合适的调整件来达到装配精度的装配方法,称为调整装配法。
调整装配法与修配装配法的原理基本相同。
在以装配精度要求为封闭环建立的装配尺寸链中,除调整环外各组成环均以加工经济精度制造,由于扩大组成环制造公差累积造成的封闭环过大的误差,通过调节调整件(或称补偿件)相对位置的方法消除,最后达到装配精度要求。
调节调整件相对位置的方法有可动调整法、固定调整法和误差抵消调整法等三种。
2、调整装配法的特点:
主要优点是:
组成环均可以加工经济精度制造,但却可获得较高的装配精度;装配效率比修配装配法高。
不足之之处是要另外增加一套调整装置。
3、应用:
可动调整法和误差抵消调整法适用于在小批生产中应用,固定调整法则主要适用于大批量生产。