加氢装置事故汇编.docx
《加氢装置事故汇编.docx》由会员分享,可在线阅读,更多相关《加氢装置事故汇编.docx(66页珍藏版)》请在冰豆网上搜索。
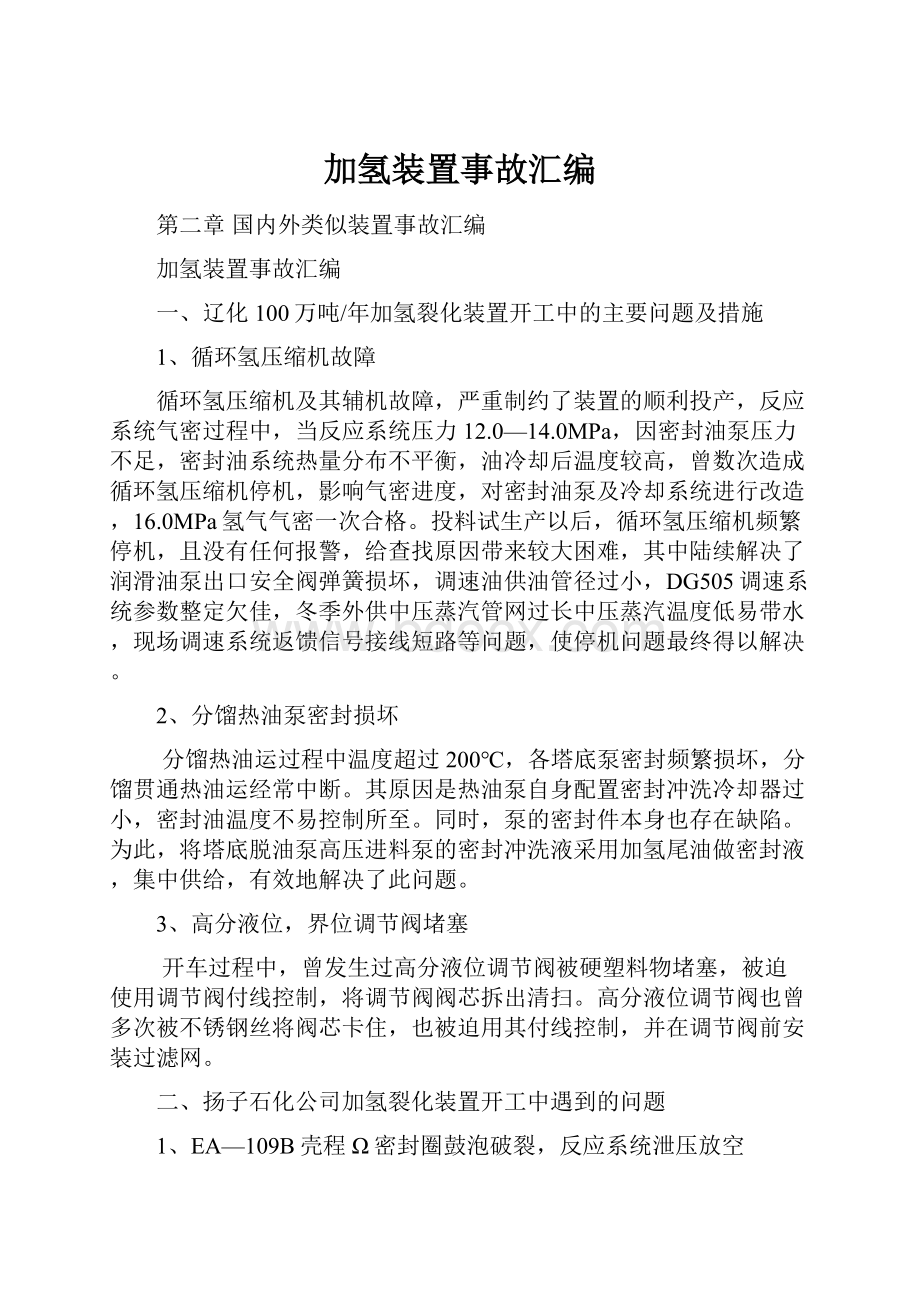
加氢装置事故汇编
第二章国内外类似装置事故汇编
加氢装置事故汇编
一、辽化100万吨/年加氢裂化装置开工中的主要问题及措施
1、循环氢压缩机故障
循环氢压缩机及其辅机故障,严重制约了装置的顺利投产,反应系统气密过程中,当反应系统压力12.0—14.0MPa,因密封油泵压力不足,密封油系统热量分布不平衡,油冷却后温度较高,曾数次造成循环氢压缩机停机,影响气密进度,对密封油泵及冷却系统进行改造,16.0MPa氢气气密一次合格。
投料试生产以后,循环氢压缩机频繁停机,且没有任何报警,给查找原因带来较大困难,其中陆续解决了润滑油泵出口安全阀弹簧损坏,调速油供油管径过小,DG505调速系统参数整定欠佳,冬季外供中压蒸汽管网过长中压蒸汽温度低易带水,现场调速系统返馈信号接线短路等问题,使停机问题最终得以解决。
2、分馏热油泵密封损坏
分馏热油运过程中温度超过200℃,各塔底泵密封频繁损坏,分馏贯通热油运经常中断。
其原因是热油泵自身配置密封冲洗冷却器过小,密封油温度不易控制所至。
同时,泵的密封件本身也存在缺陷。
为此,将塔底脱油泵高压进料泵的密封冲洗液采用加氢尾油做密封液,集中供给,有效地解决了此问题。
3、高分液位,界位调节阀堵塞
开车过程中,曾发生过高分液位调节阀被硬塑料物堵塞,被迫使用调节阀付线控制,将调节阀阀芯拆出清扫。
高分液位调节阀也曾多次被不锈钢丝将阀芯卡住,也被迫用其付线控制,并在调节阀前安装过滤网。
二、扬子石化公司加氢裂化装置开工中遇到的问题
1、EA—109B壳程Ω密封圈鼓泡破裂,反应系统泄压放空
在催化剂硫化结束,反应器降温过程中,高压换热器EA109B壳程法兰处泄漏氢气并着火,由于火势较大,先后启动0.7MPa/min和2.1MPa/min紧急泄压设施,保证了设备和装置安全。
灭火后检查发现壳程法兰Ω密封圈鼓泡(2×3cm)破裂。
2、新鲜原料进料泵联锁造成进料中断
由于气温较低,原料油泵出口流量孔板(F1007)引压管凝堵,使新鲜原料进料泵低流量联锁停泵两次,操作人员发现及时,在5分钟内重新启动进料泵,恢复进料反应器床层温度并未发生大的波动。
三、齐鲁石化缓和加氢裂化开工中出现的问题及处理方法
90年1月3日凌晨循环氢压缩机突然停机,精制反应器入口温度失控超温,压力超高。
紧急泄压重新开工后,精制反应器床层压差由停机前的0.25MPa升至0.3MPa。
15日又进一步升至0.49MPa,25日又突然降回到0.24MPa,与此同时精制油氮含量节节升高,虽不断提高精制床层温度,但氮含量仍升高到143ppm,在这段时间内裂化床层的温度也相应提高,2月2日温度已升到380℃方能维持>350℃馏分的转化率在35%左右。
2月1日发现精制反应器一床层中上部外壁出现过热点,过热区不断扩大,2月9日超温区中心壁温已达320℃,故停工检查处理。
经过开盖检查和再生卸出催化剂后的观测,发现一床层上部到预分配器塔盘均已被焦堵塞,并且在贴近器壁处有一深1.2m以上的洞穴直通超温中心部,内保温表面有一主裂纹和多条小裂纹汇集在超温中心部,另外再生后一床层催化剂大约粉碎了25%,床层水平断面的中心部位粉化的更为严重,这也是压差增大的一个原因。
四、茂名石化加氢裂化装置操作故障及主要经验教训
1、紧急放空的使用问题
1988年5月20日和11月19日,装置曾两次因变电所供电逆变器故障引起大面积停电,此时,低压电、高压电和普通机泵用电均自停,首先是C101(循环氢压缩机)透平在主汽门关闭后自停,0.7MPa/min自起动放空,联锁到反应炉熄灭,及高压原料油泵,高压循环油泵,新氢压缩机自保停运。
在5月20日停电事故处理中,0.7MPa/min自降压到15MPa(高分压力)时,因及时启动C101,当时原料油高压换热器曾内漏较小,经热紧急处理后对生产没造成什么影响。
但在11月19日,停电事故的处理中,因当班班长经验不足,到0.7MPa/min自放空联锁到循环油泵运行,R102A(裂化反应器)入口温度约升高5~8℃时,在0.7MPa/min放空的基础上又起动2.1MPa/min放空,有关人员在高分压力降到9MPa后重新启动C101失败,致使C101调速阀损坏,高压换热器严重内漏。
重新开工后发现了这些问题,但被迫在这种情况下维持生产10多天,造成能耗增大,产品液态烃和轻石脑油质量不合格,产品液收率很低的效果,因而不得不提前检修。
2、反应器R102温升过快
时间:
1990年2月1日零点班
经过:
当班在硫化后的新催化剂用VGO(减压蜡油)切换出低氮油后,控制VGO流量为49.8t/h,循环油流量为30t/h。
至4时,供氢量严重不足。
按49.8t/h的VGO的加工量计算,新氢的供应量(标)最少应为15000m3/h;可实际上只有11492m3/h。
由此,高分压力下降到13.1Mpa;反应炉循环氢呈下降趋势,F101为3700m3/h。
F102为69896m3/h。
由于催化剂处于硫化后换油结束阶段,残存的低氮油较多,很易裂解以致在2时至4时这两个小时内,R101(精制反应器)入口温升速度为10.3℃/h,大大高于现场方案小于6℃/h的规定,由于供氢不足,到4时40分时,各反应器床层温度迅猛上升。
其中,R101冷氢量为9300m3/h,R102冷氢量60000m3/h。
在这种情况下,不得不采取紧急停炉并处理量由49.8t/h降至40t/h的措施以控制住温度。
经验教训:
①应严格按方案执行。
②协调指挥不力,没有及时联系制氢配合开工,供氢不足又盲目地升温。
3、调节循环氢换热旁路阀(T210)过快致使炉F102(第二循环氢加热炉)进料孔板法兰泄漏。
时间:
1990年2月22日白班
经过:
当日零点班,制氢因仪表发生故障一直无法保证供氢,装置被迫在7时停工。
按上级布置,白天班应使装置在14时之前达到重新开工的条件。
当时反应器R101入口温度291℃,R102入口温度289℃,炉F101点燃7个火嘴,炉F102点燃8个火嘴(第一、二循环氢加热炉)。
为提高炉子负荷,使反应器在进料后通过换热器冷旁路调节入口温度,13时50分,当班班长手动调节T210,阀位由30%瞬时开至95%。
约4秒钟后即从炉子处听到法兰泄漏的声响。
经岗位操作工提醒,随即将T210调回至原开度。
之后,泄漏响声消失。
当阀位变化时,TRC-210温度记录由220℃瞬时降至75℃,反应器R101入口和R102A入口各发生有15~25℃的温度波动,由此使开工进油推迟了1个半小时。
事后恢复到进油条件,R101入口295℃,R102A入口293℃,检测该法兰仍有微泄漏。
经验教训:
(1)业务技术水平低,盲目操作。
(2)工作上没有统筹安排,急于求成。
4、第1分馏塔液面超高(即:
产品分馏塔)
时间:
1990年2月27日四点班
经过:
当日白班12时该塔进料自90t/h交班时提量到98t/h,这段时间内由于转化率不高,9时和13时柴油的终馏点都高于350℃,而交班前,T103(产品分馏塔)液面实际上已漫顶了(仪表指示在90%就不动了)。
四点班继续提量,18时已达100t/h。
从16时到18时这段时间里,第一分馏塔各侧线的抽出量又趋下降,轻石脑油由17.5t/h降至13.7t/h,重石脑油由15.1t/h降至13.7t/h,航煤由37.2t/h降至29.5t/h。
按当时的物料平衡,该塔在12时至18时之间已存油94899kg。
17时航煤的98%馏出温度高于350℃,说明在这时该塔油已漫至抽出口,只是分析站不及时报送结果,至21时30分才报结果,而不被注意。
后经调整,操作正常,但中间罐航煤约600吨已受污染。
经验教训:
①提量时对产品收率和物料平衡计算不准。
②交接班不清。
③没有严格执行质量负责制,当分析不合格时,应及时通知生产调度。
5、供汽压力波动导致C101(循环氢压缩机)和P102AB(循环油泵)损坏
时间:
1990年9月20日四点班
经过:
16时10分,接班后不久,随着加氢锅炉巨大的放空声,操作人员发现中压蒸汽压力指示值急剧下降。
班长随即询问,调度回答:
"可能锅炉有了问题"。
看到压力继续下降并报警,C101岗位操作工意识到这会影响透平泵转速已降到达2000r/min,泵出口压力约10Mpa。
针对这一情况,岗位操作工马上启动封油备用泵,然后去关封油透平的进汽手阀。
可最后两扣很紧,这时设备员赶到现场,扳动跳闸机构把透平停下。
停后盘车,刚盘车时有紧的现象,但盘动后就松了。
当蒸汽压力恢复到期3.0Mpa时,经请示,按开泵步骤重新启动透平。
逐渐关闭透平泵出口副线阀,将压力憋起,在憋过程中,发现泵出口压力和转速随之下降,泵发出异常声响,未及停车,透平已自停。
停下后盘车不动,情况紧急(封油压力下降至0.56Mpa,危及C101停车),设备员跑回操作室通知当班操作工做停工准备。
经验教训:
①当中压蒸汽压力下降至2.8Mpa以下时,要立即停下封油透平泵,切换备用泵;透平泵停后要经解体检查,确认无问题后方能重新启动。
②无论是透平泵还是电泵,入口负压值不应小于0.01Mpa,当达到或小于此值时,要停泵清扫入口过滤网。
③为防止大透平(CT101)损坏,当蒸汽压力下降,大透平转速小于或等于7200r/min时,要作紧急停机处理。
④为防止泵磨损所产生的铁末污染罐内的油,建议在泵出口返回储罐的油管道上增设过滤网。
6、泵P102(循环油泵)抽空操作导致止推轴承和转子磨损。
时间:
1990年2月20日
经过:
当日白天班,在装置开工新催化剂钝化过程中,由于注氨泵北缸气阻,上量不好,推迟了换油时间。
反应分馏系统在较高温度下(260~280℃)循环产生了裂化反应,各塔器出现了低液面。
9时多,当发现P102由于D107(循环油罐)液面超低抽空时就通知泵工去停泵,抽空时间约5分钟,停泵时未发现有不正常现象。
11时许,D107液面恢复正常,泵按开泵程序启运,发现电流表指针打上去较长时间才回到140安(额定为135安)就再也不下来了,且噪声较大,如此约有5分钟。
当发现电流超高,后轴承处甩火花时,泵工当即按停泵按钮,但由于触点不好,按钮失效,后联系电工拉闸,这时,另一泵工按停泵按钮成功。
检查发现泵的止推轴承烧坏,转子和内件受到一定程度的磨损。
经验教训:
①分馏操作工责任心不强,致使D107液面两次超低,是这次事故的主要责任者。
②泵工在第一次停泵,开泵前盘车时没能发现泵已经有了问题,且在起动电流超高时又没能将泵停下,失去了阻止事故发生的机会。
③在重新开泵时,没有发现循环油罐入口温度比泵体积高出20~30℃。
启动后泵体温度突然升高,升温度很可能超过每分钟2℃,这也可能是事故原因之一。
五、上海股份有限公司芳烃厂加氢装置BA-101(循环氢加热炉)炉管爆裂事故。
1989年6月18日1时26分左右,当班副班长发现DC-102(裂化反应器)第1床层出口温度点T-01066高报警,该点温度从正常370℃升高到380℃,DC-102进口温度则从367℃降至360℃,同时发现DC-101(精制反应器)进口温度下跌,BA-101的燃料气的控制阀后压力从正常的0.11Mpa升至0.18Mpa,BA-101的循环氢流量计F-01009的指示达到满刻度,调节阀FV-1009处于全关状态。
另外从中控室的仪表屏上发现燃料气管网压力下降。
此时运转主任提醒:
FV-1009已处于全关状态,无法判断加热炉是否已破裂。
当班副班长即按常规将FV-1009恢复到75%开度。
在1时30分,当班班长在压缩机房处听到两声不连续的爆裂声,同时反应外操报告加热炉烟囱有火,班长立即决定启动2.1Mpa/min泄压;装置紧急停工。
2时35分,加热炉烟囱倒塌,2时45分火势基本得到控制,3时05分,大火熄灭。
事故分析:
这次事故估计是先有一根炉管爆裂引起的。
当时BA-101的循环氢流量控制器FIC-01009处在自控状态,炉管破裂漏出大量氢气使得FV-1009指示大于正常值,因而FV-1009自动关小直到全关。
当发现FV-1009全关时,为防止加热炉空烧炉管,当班人员将FTC-01009改为手控,将FV-1009开至正常开度。
这一过程中,BA-101循环氢已中断过,已有VGO(减压柴油)从炉出口的单向阀倒入BA-101的炉管。
炉子还未降温,FV-1009打开后,大量氢气进入炉膛造成燃爆。
VGO在炉管内结焦,造成炉管局部过热爆裂。
事后发现炉膛里有多根管破裂。
启动2.1Mpa/min泄压系统已是过了一段时间,所以从反应系统倒过来的VGO在炉膛内继续燃烧。
事故原因:
(1)第1根炉管破裂可能是实际炉管壁温超标。
(2)测温点不在第一组炉管最高温度的第8根炉管,而是在第二组炉管上。
(3)主要原因是炉管材质缺陷。
六、扬子石化公司芳烃加氢装置生产中出现的事故
1、DA-102(产品分馏塔)操作控制不住
92年7月13日被迫停工检查,发现塔底严重受损,经分析,原因是DA-102冲塔造成。
开车时此塔液位较高,当时未受重视,另外仪表不准,新增的EA-125(新鲜进料和尾油换热器)使用不当,回流量大,引起塔气相负荷大,压差大造成冲塔。
事故总结:
责任心不强,未及时发现操作参数的变化,对仪表过于信任,未去现场察看,今后加强业务学习,提高操作技能。
2、DC-103(裂化反应器)飞温的经过
91年8月14日14:
45分(进加热炉循环氢控制阀)T-1156阀突然失控关小,副线控制阀又处于手动关的位置,BA-102炉终断了循环氢,造成炉管干烧10分钟,后打开T-1156阀循环氢进入加热炉内,把炉管内的热量顶入DC-103,造成DC-103一、二床层飞温至930℃,紧急打开2.1Mpa/min放空泄压。
事后检查发现炉管有部分弯曲,DC-103一、二床层催化剂失活。
应吸取教训是:
①对仪表、控制阀要详细认真地确认。
②要加强操作技能的训练,加强对事故的演练。
3、仪表故障造成装置停工
93.8.31日13:
00左右,GB-101振动较大,循环氢中断反应温度上升较快,这时紧急启动0.7Mpa/min泄压停车。
事故原因是GB-101仪表盘进水(估计是下雨所至)。
GB-101出口阀误动作关死,造成循环氢中断,后经对仪表盘处理再开车。
4、操作不慎造成人身伤害
EA-903(脱丁烷塔进料换热器)内漏,蒸汽冷凝水带油,从导淋处接了一根胶管向地沟排放,有一操作工在准备关导淋时,导淋桶部胶管突然脱落,高温冷凝水喷泉反弹至这位工人身上,造成烫伤事故,住院治疗。
教训:
接胶管时未用铁丝捆绑,且排放阀开的过大,此人安全防护意识较差,今后应加强学习。
5、氢气泄漏引起着火
90年5月8日14:
25分GB-102B(补充氢压缩机)二段出口压力表引压管根部阀填料大量泄氢气着火,经扑救于14:
45分熄灭,同时启动0.7Mpa/mi泄压停车,14:
45分启动GB-102A,因负荷阀仪表接线烧断,无法将负荷切到100%,被迫作长时间氢循环运转(改小循环)。
晚20:
30分左右保运人员在拆除氢气泄漏阀时,因引压管内余压未排尽,引起瞬时间燃烧,险些烧伤保运人员,后来用N2将火吹灭。
经验教训:
①未及时发现问题,今后要加强巡检。
②责任心不强,未将故障设备处理干净,就交给保运人员,
6、GAT-183齿轮箱轴烧坏
92年7月19日22:
30分启动GAT-183(密封油蒸汽透平泵),准备开循环氢压缩机,在开GAT-183前做好了开泵前的一切准备工作。
开启后发现此泵振动较大,立即向上级有关部门汇报并来人查看未做任何处理,交接班时下个班也未发现任何问题,到1:
30分发现GAT-183齿轮箱轴烧坏。
事后进行事故分析,主要原因是检修不过关造成烧轴,另一方面有可能是润滑油少的原因造成烧轴。
经验教训:
①此泵检修完后未进行认真检查。
②操作人员对事故判断能力较差。
③没有严格按操作规程去作,润滑油位低。
④有关上级部门对此事不够重视,岗位人员应继续向上级汇报。
7、机泵故障造成装置停车
92年10月28日15:
00点,GB-101(循环氢压缩机)因密封油泵停运。
FA-184(密封油高位槽)液位低造成联锁停车,启动0.7Mpa/mi泄压,装置紧急停工。
原因是10月27日,GAT-183A(密封油蒸汽透平泵)故障紧急抢修后,于28日午安装完毕,进行试运,工作泵由GA-183B(电动备泵)代替,下午15:
00正准备提A泵转速时,B泵突然停运,经检查B泵齿轮被卡死,造成电机跳闸,此时A泵出口压力上不去,密封油液位直线下降,引起GB-101联锁停车。
10月30日7:
00装置重新开车,A泵未处理好,仍然开B泵,12:
00B泵再次突停,原因同上,GB-101再次联锁停车,启动0.7Mpa/mi泄压,装置紧急停车。
经验教训:
备用设备要认真检查,发现问题及时联系处理,确保随时能投入正常使用。
七、辽化炼油厂加氢裂化车间在生产上发生的事故
1、高压分离罐仪表液位指示失灵,界面板指示不准,造成高分脱水液面过低,16Mpa的气体串到下游脱硫装置,造成酸性水罐发生爆炸。
这次事故的发生虽然是因仪表故障造成,但操作员责任心不强,业务水平低也是一方面原因。
2、在一次加热炉点火过程中,操作人员未按要求去做,先用蒸汽吹扫炉膛,再进行可燃性气体分析,而直接点火,结果造成炉膛爆炸,这是一起严重的违章操作,望大家引以为诫。
3、加氢装置开工期间,装置进行热油运行时,分馏塔液面仪表指示失灵,塔被装满后仪表没有指示和报警,造成安全阀起跳,油串入火炬线将火炬放空罐装满,幸好离心机没有联锁泄放,否则火炬放空罐将发生大爆炸,后果不堪设想。
从以上事故中我们应吸取他们的经验教训,在以后的开工及生产中不应过分相信仪表,尤其是开工初期,室内仪表指示要经常与实际相对照,发现问题及时联系仪表处理。
做为操作人员对操作情况要做到心中有数,操作发生变化时应多思考,做到手勤、腿勤、眼勤,发现问题及时处理,避免类似事故在我们装置发生。
八、金陵石化公司加氢裂化装置生产中出现的故障及处理措施:
1、P101A/B润滑油过滤器破损
1986年4月24日清洗P101A/B(原料油泵)润滑油过滤网时,发现滤芯滤网破裂。
分析:
当时气温较低润滑油温低粘度大,在大流量下形成较大压差,超出滤芯所能承受的强度时滤网被击穿。
正确的做法是过滤器进油前,可以先关小润滑油冷却器上水,以提高润滑油温度,同时控制进入过滤器的油量,监视过滤器差压表,防止超压事情发生。
随着油温的提高而慢慢地加大润滑油量。
2、氮气线窜油
1986年7月6日发现氮气线内有油,经查找发现是从C101(循环氢压缩机)润滑油泵临时氮气线窜入。
事后氮气线全面扫线。
这时又发现油已随氮气进入废热锅炉,造成废热锅炉第二次煮炉。
分析:
氮气线是装置内非常重要的系统管线,连接部位很多,容易造成窜油事故。
一旦窜油便会威胁C101,C102(新氢压缩机)等设备的安全运行,有可能导致重大事故发生。
各用氮点在设计时应作处理,单向阀组正确的用法应将单向阀前后阀关闭,导凝阀打开,杜绝窜油事故发生。
当工艺管线线路压力与氮气线压力相差很大时,应加盲板。
该故障发生在C101试运前,是幸运的。
本次原因是施工人员不熟悉工艺管线在氮气线上接一皮管至润滑油线,造成油窜入氮气线,因此在有外单位人员参加工作时,本装置人员更要注意检查。
3、C101(循环氢压缩机)密封油液位导致机组联锁跳闸
1986年7月9日,C101机组在第一次试运中,8:
05时密封油高位罐液位下降,电泵也无法维持液位。
8:
08时由于高位罐液位低造成联锁跳闸,C101自动停运。
事后发现液位自控回路调节阀处于关闭状态,经检查是该阀定位器供风定值器损坏,仪表风中断造成调节阀自动关闭,使密封油不能进入高位罐。
分析:
调节阀出故障是操作中常见的现象,当运转设备正常而出现断流故障,应立即查看调节阀开度,必要时用旁路阀调节。
4、脱硫岗位液态烃抽提塔T151(即液化气脱硫塔)超压
1986年8月17日,脱硫单元液态烃抽提塔T151进行氮密,充氮时将安全阀前阀关闭,充氮流程是将2.5Mpa氮气线到接脱丁烷塔再进入抽提塔。
当时方案将脱丁烷塔充压到2.5Mpa后再向T151充氮,但操作人员没将T151进料阀关闭,仅在脱丁烷塔底观察压力。
当脱丁烷塔充压到2.5Mpa时,T151已达2.3-2.4Mpa,事后检查T151有两个垫片被撕开,被迫重新换垫。
分析:
这是一起严重的设备超压事故,发生的原因是对流程检查不细,该关阀门没关。
生产中相当多的事故出自流程搞错,阀门开错。
5、1Mpa蒸汽温度减温到180℃
1986年8月21日,C101(循环氢压缩机)正在开机试运中,废热锅炉开除氧系统,(向CT1019循环氢压缩机蒸汽透平)背压蒸汽注减温水,将1Mpa蒸汽控制在250℃,由于除氧器温度升的过高液位波动,造成F106-P01A泵(减温水泵)抽空减温水中断,背压汽温控表TC-713自动将注减温水阀全开,备用泵起动后温控表调节滞后大量减温水注入C101背压汽中,使1Mpa蒸汽温度降到180℃。
故障出现后,紧急将TC-713改手动将温度提回到250℃。
分析:
加氢裂化装置的低压汽是排放到厂管网,1Mpa蒸汽饱和温度为170℃,接近170℃时会造成蒸汽带水事故。
我厂热裂化装置和瓦斯压缩站使用以1Mpa蒸汽为动力的汽轮机,蒸汽带水会造成汽轮机损坏,对蒸汽温度的控制万不可大意。
此外蒸汽带水对加热炉会造成重大影响,使炉火熄灭易产生回火爆燃事故。
6、C102(新氢压缩机)出口向入口倒压
1986年9月1日,准备开C102A升压,此时反应压力为3.0Mpa,C102A各级出口返回线没关,C102A机出口单向阀漏,当机出口阀打开之后,反应器内的氢气倒窜回机入口,造成一级入口安全阀起跳。
分析:
单向阀一般来说是不严密的,因此C102A开机时应将各级出口返回阀关闭,防止倒窜事故发生。
7、C102向制氢返回氢中断
1986年9月2日,C102B机(新氢压缩机)由于一级入口滤网堵需更换到C102A机。
启动C102A机后,由于新氢管路太脏,一级和二级入口滤网立即堵塞,被迫紧急停机,造成制氢返回氢中断,制氢装置被迫切断进料。
分析:
制氢反应炉需要加氢C102提供返回氢作反应配氢,返回氢中断制氢将被迫切断进料,反之又影响加氢,这是一个联系两个装置的重要环节,换机时一定要注意将返氢线打开,此次故障产生于试运阶段,所以影响不大。
正常生产操作则会产生重大波动。
8、C101蓄能器内胆破裂
1986年9月2日发现前天向C101(循环氢压缩机)密封高位罐装的油液位下降,判断是蓄能器内胆破裂。
经检查发现第二组蓄能器顶端脱落,经分析可能是由于以下两种原因造成:
a.施工单位清洗蓄能器时,由于安装不当造成损坏。
b.引油引压时速度太快,造成受力突变,把内胆撕破。
分析:
高位罐油如窜入封油系统会污染密封油腐蚀密封机件损坏设备,更严重的是高位罐建立不起正常液位,势必造成自动C101停车。
9、F106废热炉入口负压超高
1986年9月2日,反应炉F101和F102正在升温,废热锅炉开C104(烟道气引风机)引烟气煮炉。
操作人员在进行烟气切换时,烟道旁路挡板DA-6关得太快,废热锅炉入口负压过高,将F101和F102两炉火抽熄。
分析:
废热锅炉入口负压控制着五台工艺炉负压,它的激烈波动将造成五台工艺炉负压波动,严重时会产生熄火,炉膛爆炸等恶性事故。
锅炉操作人员调整负压时,应与反应和分馏岗位联系,三方人员到现场严密监视各炉负压变化情况,必须缓慢调节。
10、C102B入口憋压
1986年9月11日准备开C102B(新氢压缩机),将氢气引入机入口。
PRC-116B压力升高到1.23MPa,中控室控制表PRC-116B输出到100%压力仍撤不下来,操作人员被迫跑到现场开旁路阀放压。
事后发现C102B的PRC-116B控制三通被人拨到PRC-1