旋压工艺.docx
《旋压工艺.docx》由会员分享,可在线阅读,更多相关《旋压工艺.docx(68页珍藏版)》请在冰豆网上搜索。
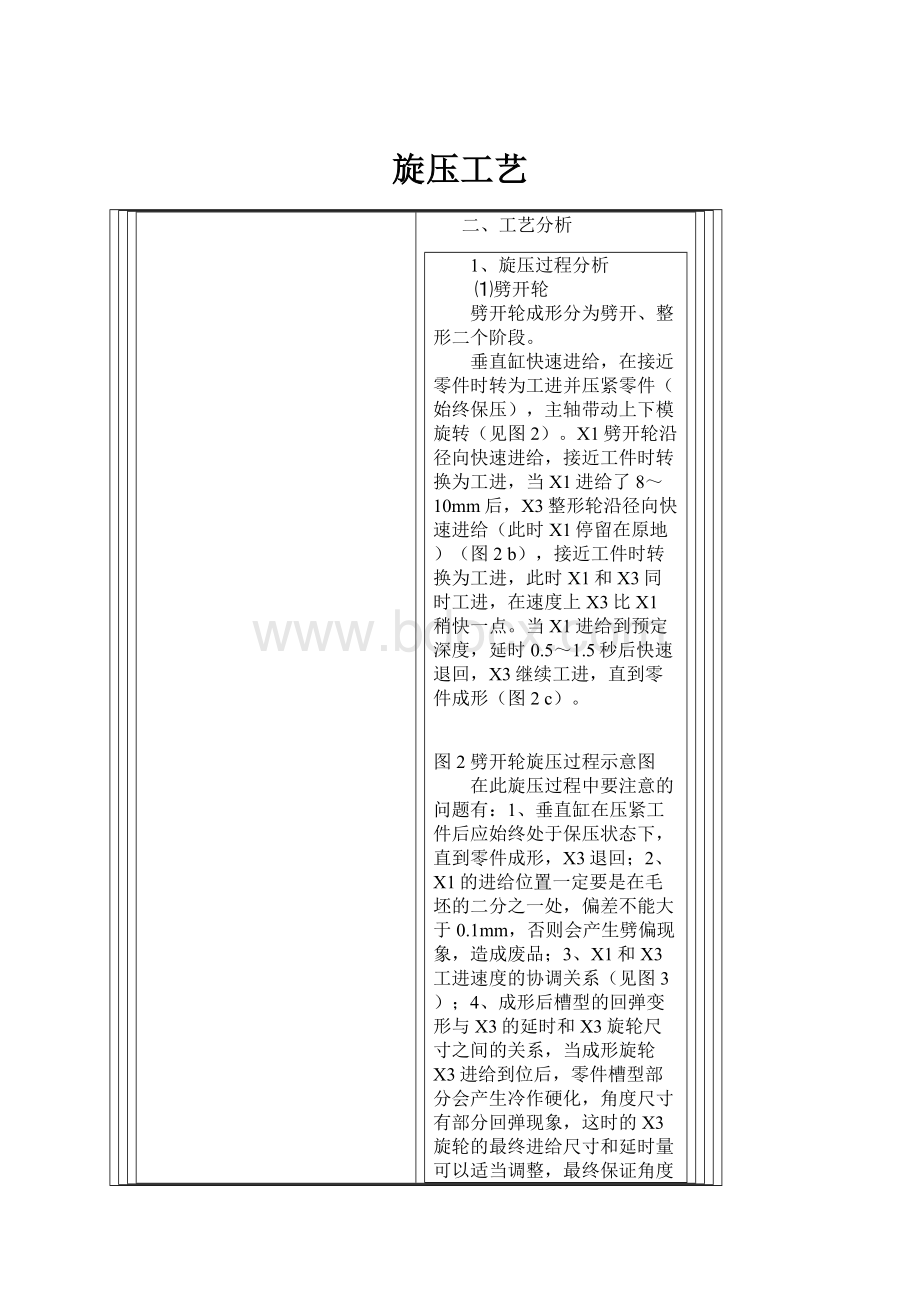
旋压工艺
二、工艺分析
1、旋压过程分析
⑴劈开轮
劈开轮成形分为劈开、整形二个阶段。
垂直缸快速进给,在接近零件时转为工进并压紧零件(始终保压),主轴带动上下模旋转(见图2)。
X1劈开轮沿径向快速进给,接近工件时转换为工进,当X1进给了8~10mm后,X3整形轮沿径向快速进给(此时X1停留在原地)(图2b),接近工件时转换为工进,此时X1和X3同时工进,在速度上X3比X1稍快一点。
当X1进给到预定深度,延时0.5~1.5秒后快速退回,X3继续工进,直到零件成形(图2c)。
图2劈开轮旋压过程示意图
在此旋压过程中要注意的问题有:
1、垂直缸在压紧工件后应始终处于保压状态下,直到零件成形,X3退回;2、X1的进给位置一定要是在毛坯的二分之一处,偏差不能大于0.1mm,否则会产生劈偏现象,造成废品;3、X1和X3工进速度的协调关系(见图3);4、成形后槽型的回弹变形与X3的延时和X3旋轮尺寸之间的关系,当成形旋轮X3进给到位后,零件槽型部分会产生冷作硬化,角度尺寸有部分回弹现象,这时的X3旋轮的最终进给尺寸和延时量可以适当调整,最终保证角度尺寸不会超差。
在设计X3旋轮时也可以将回弹因素考虑进去,X3的旋轮夹角可以在图纸要求的尺寸上增加1°至2°,使之在旋压结束时能补充回弹量。
图3X1与X3工进速度的协调关系
注:
当X1的工进速度比X3快或两者相等,都会产生如图a的效果,这时会发生已经被劈开的材料边缘部分受材料内应力的作用向X1旋轮表面靠拢,最终产生相对摩擦。
这样会在X1旋轮表面留下一圈积削,而这些积削会划伤零件表面,从而影响零件表面质量。
只有当X3的进给速度比X1的进给速度稍快一点(但不能快太多,否则到最后会产生X3成了劈开轮,X1没有起到作用的情况),由X3撑开已经被劈开的材料部分,使被劈开的材料部分不会与X1产生相对摩擦。
从而保证产品质量。
⑵折叠轮
折叠轮成形分为预成形、整形二个阶段。
垂直缸快速进给,在接近零件时转为工进并压紧零件(没有保压)。
主轴带动上下模旋转(见图4)。
X1预成形轮沿径向快速进给,接近工件时转换为工进,同时垂直缸以预成形工进速度对毛坯加压(图4b),当X1进给到位后,垂直缸停止加压,X1快速后退,同时X3沿径向快速进给,接近工件时转换为工进,此时X3和垂直缸同时工进,在速度上以两者同时完成进给为准。
(图4c)。
图4折叠轮旋压过程示意图
在此旋压过程中要注意的问题有:
X1旋轮和垂直缸同时工进时的速度协调性;X3旋轮和垂直缸同时工进时的速度协调性。
X1、X3旋轮在与垂直缸协同进给时各自的进给量均不同,这时需要调整各自的速度来达到时间上的协调(同时完成进给)。
⑶多楔轮
多楔轮成形分为第一次预成形、第二次预成形、整形三个阶段。
垂直缸快速进给,在接近零件时转为工进并压紧零件(始终保压),主轴带动上下模旋转(见图5)。
图5多楔轮旋压过程示意图
1─上模2─压料杆3─毛坯
4─下模5─退料板6─定位销
X1预成形轮沿径向快速进给,接近工件时转换为工进,X1进给到位后延时1秒至3秒不等(视零件直径尺寸而定)(图5b),X1快退的同时X2预成形轮快进,接近工件时转换为工进,X2进给到位后延时并快退(图5c),同时X3快进,接近工件时转换为工进,完成成形进给(图5d)。
毛坯在经第一次预成形时,毛坯的直段部分被旋压成了凹形环状,变形后基本保持了材料厚度不变,仅起到将材料填充到所需部位的作用,旋压成形属于金属塑性变形的一种,遵从"体积不变"的原则,旋压前该直段部分材料的体积等于旋压后凹形环状的体积。
多楔轮的旋压过程,材料变形情况比较复杂,不能只用一个成形旋轮就加工出零件,必须分部成形。
第二次预成形是使用齿形角度为50°~60°的预成形轮,旋压凹形环状部位,当槽型填充满后,再用齿形角度为最终角度的旋轮进行整形旋压,最终旋出槽型。
在设计和调试产品时应注意以下几个主要问题:
a、当X1预成形轮加工完后,内侧折叠区域有间隙,并且两侧有一定的圆角,未能填充满(见图6)。
图6
1─下模2─毛坯3─上模
这些间隙和未填满的地方会给以后齿形能否成形造成了影响,因为当X2、X3进行旋压时,有一部分材料就会填充这些间隙和未填满的区域,这样就会产生局部齿形完好成形,而有个别(基本上是两侧的齿形)齿顶出现未成形的情况(见图7)。
要解决这个问题,首先要明确"体积不变"的原则,要保证毛坯件的直线段长度计算准确;其次在设计上、下模时要避免在该地方出现直角,应在图纸允许的情况下以圆角和一定斜角适当过度(见图8)。
图7
1─下模2─毛坯3─上模
图8
1─下模2─毛坯3─上模
另外可以在设计X1旋轮时采用大圆角齿形设计(见图9)(注:
此设计只在一种齿数少的产品中使用过,效果不错,但未经过较广泛的试验,仅供参考。
)。
在编制程序时,也可对X1旋轮的延时进行调整,让X1旋轮进给到位后还有充分的时间进行填充变形。
图9X1旋轮(仅供参考)
b、在旋压过程中,经常会有带状的细铁屑从旋轮和工件之间飞出,一般这些铁屑会被冷却油冲掉,但有的会留在零件槽型中,被旋轮反复的碾压,造成了零件表面质量的损伤。
飞屑问题主要是由于X2旋轮加工完成后,X3旋轮的槽型没有调到和X2旋轮已经加工出的槽型相吻合,由X3切下的细小铁屑;另一种原因是由于X1旋轮的宽度尺寸不够,X1的宽度小于X2的宽度,由X2切下的细小铁屑。
因此在设计时要注意这些情况,尽量避免在旋压时出现此类问题。
c、多楔轮旋压成形体积转移示意图(图10)。
图10体积转移示意图
1─旋压前材料的位置2─旋压后材料的位置
2、毛坯直径计算
我们以多楔轮的毛坯计算举例,使用的是AutoCADR14绘图软件。
⑴首先打开AutoCADR14,新建一张图纸,选择Metric(公制单位),按OK开始。
见图11。
图11选择公制单位
⑵按照图纸实际尺寸绘出零件侧视图,绘图过程在此不作介绍。
见图12。
图12绘制零件侧视图
按零件实际尺寸绘制零件侧视图。
⑶点击Draw(绘图),选择BoundaryCreation(面域),出现如图13对话框,点击PickPoints,这时光标变成十字形,将光标移到零件图中空处,点击选择面域,回车后生成一个面域。
(注:
如果在绘图过程中,线段之间没有完全连接,即有短开处,将不能生成面域。
)
图13生成面域
当面域生成后,再选取零件图中线段时,图中所有线段将会以整体被选取。
如图14。
⑷点击Draw(绘图),移动到Solids(实体),选择Revolve(旋转),然后选取已经生成的面域,回车后再选取旋转轴,回车生成一个皮带轮的实体模型。
如图15。
图15生成实体模型
此时可以使用3D工具对图形进行操作,也可调出快捷工具栏,如:
视图工具栏(可看零件各向视图)
渲染工具栏(对零件可进行着色渲染)
⑸点击Tools(工具),移动到Inquiry(查询),选择MassProperties(质量特性),然后选择3D实体模型,回车后将出现特性查询文本框,见图16。
文本框中Volume为体积特性。
这时我们就能计算出毛坯的直径了。
以图中的数字为例,毛坯的直径为:
加入材料拉深放量,粗计为5%,实际毛坯直径为D=246.96·1.05=259.308≈260mm。
图16查询质量特性
3、计算机辅助设计
除了用计算机辅助计算毛坯直径外,在设计模具和加工工艺时,也可以借助计算机辅助设计来发现和更正设计中的缺陷。
例如在设计旋压模具时需要考虑旋轮架在进给时会不会与上下旋压模具发生干涉,旋轮会不会与旋压模具发生干涉等。
此时可以用绘图软件(如:
CAXA、AutoCAD、SolidWorks等)在电脑中绘出实际尺寸的图形并保证各零件的相对位置,然后模拟各工位的移动情况,来发现其中的设计缺陷。
也可以借此来确定各零件的加工尺寸范围,例如旋轮的最大直径、最小直径(旋轮类似于刀具,在生产过程中有正常磨损,当磨损后不能保证产品质量时需要对旋轮进行修整,以延长旋轮的使用寿命。
)。
利用计算机辅助设计能方便、快捷的完成我们的工作,此时,熟练掌握运用电脑就成了关键。
4、工艺流程
图17是折叠轮的整个工艺流程,也是大部分旋压产品的通用流程。
区别仅在于零件的复杂程度与工序的多少。
图17工艺流程图
拉伸工序可视零件外形尺寸来确定拉伸次数,图18为工艺流程的简图示意。
图18工艺流程示意图
当然,也有一部分结构复杂的零件需要利用锻造或铸造来制作旋压毛坯,来满足特定尺寸和要求。
设计人员应该根据不同的零件制订相应的工艺流程,以适应产品要求的需要。
三、模具设计
在模具设计章节中,主要介绍旋压模具,并针对旋压模具设计中影响产品质量的因素进行分析,供设计人员参考。
冲压和拉伸模具由设计人员自行参考相关设计手册进行设计,在此不作介绍。
1.旋压方式
以折叠轮为例,有两种旋压方式能使零件成形,见图19。
正压式旋压和反压式旋压。
图19正反旋压方式
1─上模2─定位销3─毛坯4─退料板5─下模6─退料杆7─定位销
8─压料杆9─上模10─毛坯11─退料板12─下模13─退料杆
正压式旋压的主要特点是旋压模具结构简单,顶出行程短,工件容易取出,单件加工周期短。
缺点是由于是用上模定位,所以受毛坯的质量影响比较大,当毛坯冲压时中心孔的跳动比较大时,容易发生上模在下压时定位销与毛坯中心孔不重合,导致压坏毛坯的现象;其次受工艺参数和液压系统压力影响较大,当工艺参数或液压系统压力发生了变化,上模与旋轮的相对位置会发生相应变化。
导致定位面到槽型中心的定位尺寸发生变化,影响产品的最终质量。
反压式旋压的主要特点是利用下模定位,定位准确,旋轮和工件定位面的相对位置不发生变化,受工艺参数和系统压力影响较小。
不足之处是模具结构较复杂,工件不容易取出,单件加工周期比正压式旋压略长。
在保证产品的成品率的前提下,提倡使用反压式旋压。
目前的大多数折叠轮和多楔轮都能使用反压式旋压。
2.模具结构
旋压模具主要由上、下模和旋轮组成,见图20。
图20
1─上模座2─上模3─压料杆4─退料板5─下模6─退料杆7─下模座
8─顶出杆9─垫板10─定位销11─毛坯12─垫板13─聚氨脂14─垫板
上模座和下模座是和上下同步轴上的齿轮相连接,属于通用零件。
在设计时尽量考虑它的通用性和实用性。
虽然零件尺寸和外形特征的不同,但上、下模的结构基本相同,只是局部有着差异。
由于聚氨脂的弹力要远大于相同直径的橡胶和弹簧,所以在上退料上选用聚氨脂比较合适。
在选用聚氨脂时需要考虑零件的总压缩量,聚氨脂与橡胶、弹簧不同,压缩量只有总高度的三分之一,和橡胶、弹簧一样,在达到压缩极限时容易发生失效和破裂,因此需要考虑留一定的压缩余量。
由于上模座和下模座为通用件,因此在设计上模和下模时首先要协调零件旋压时的工作位置与旋轮中心的位置关系。
让旋轮的工作位置处在最佳受力位置,同时也给工艺调试预留了调整空间。
详细请参考随机附图中的《工装协调图》,图中给出了旋轮座与上下同步齿轮之间的位置关系,设计人员可以参考协调图来合理设计模具尺寸。
上模和下模设计重点在于压紧零件并起到成形作用的型面部分。
型面的尺寸基本上与零件吻合,只是要注意模具在旋压过程中不能和旋轮发生干涉。
这需要设计人员在计算机中反复的试验,模具尺寸尽可能的留有修改的空间。
也需要上机调试人员必须认真仔细调试产品。
3.模具材料与加工工艺
上下模和旋轮为旋压模具中最主要的部件,一套上下模的正常寿命为2万件左右,而旋轮的寿命大概为5000~12000件。
因此对材料就要求有较高的耐磨性和较高的硬度。
目前普遍用于加工上下模和旋轮的材料有Cr12MoV、CrWMn、40Cr等。
在加工上目前受条件所限,有着各不相同的方法,但我们的要求基本是上下模的曲面部分在淬火处理后用陶瓷(立方碳化硼)车刀进行精加工,并抛光。
这样能提高模具的使用寿命和提高零件的表面质量。
旋轮的加工比较复杂,需要进行粗加工后进行热处理,然后进行精加工并抛光,如果有条件的话,希望能用螺纹磨床对齿形进行磨削加工,以提高旋轮的表面光洁度(针对多楔轮的旋轮而言)。
对于旋轮而言,热处理是很重要的一个环节,如果热处理不过关,将会在旋轮的内部产生应力集中,如果严重的话,在热处理完后旋轮就会开裂,不严重的情况下旋轮的开裂也会发生在旋压加工的过程中,这样会大大降低旋轮的使用寿命。
如果选用淬透性比较好的Cr12MoV作为加工旋轮的材料,旋轮在加工到一定数量的零件后,即对旋轮进行修整,这样可以尽量的延长旋轮的使用寿命。
4.旋轮设计
由于旋轮的尺寸和零件尺寸有着紧密的联系,在此无法具体举例,因此只介绍旋轮设计中的几个需要注意的地方。
注:
旋轮的结构参考附图中的《旋轮装配图》。
⑴、劈开轮
加工劈开轮的旋轮主要有两个:
一个是劈开轮(俗称劈刀),一个是整形轮。
劈开轮的使用部分见图21。
劈开轮的刀尖部为60°夹角,主要起到从材料的二分之一处将材料劈开并撑开已经被劈开的材料部分,使被劈开的材料向两侧分流。
X的取值一般为1.5~2,在加工过程中需要注意的是60°夹角的对称性以及两侧的X值误差。
如果角度和X值误差偏大,容易引起加工过程中劈偏的现象发生。
从而造成废品和次品。
图21
整形轮的形状和尺寸主要取决于零件的形状和尺寸,在此不作介绍。
⑵、折叠轮
加工折叠轮的旋轮主要有两个:
一个是预成形轮,一个是整形轮。
预成形轮的使用部分见图22。
由于折叠轮的材料厚度不同,为了在旋压过程中保证材料不变薄,预成形轮的圆角半径应适当取值,原则上材料越薄,圆角半径越大,R的取值范围为8~12mm,α值取值同圆角半径一样,材料越薄,α值越大,α的取值范围为40°~52°。
旋轮厚度B则随着R和α值的变化而变化,范围在20~40mm之间。
在加工过程中圆角半径和α夹角之间应圆滑过度,表面应经抛光处理。
图22
整形轮的形状和尺寸主要取决于零件的形状和尺寸,在此不作介绍。
⑶多楔轮
加工折叠轮的旋轮主要有三个:
两个是预成形轮,一个是整形轮。
图23是三个旋轮的基本形状,第一预成形轮在调试过程中也可根据实际需要进行修整。
图23
预成形轮的设计主要依据零件的成形尺寸,见图24。
图24
第一预成形轮(X1)的曲面设计关键是确定轮型的宽度,依据体积不变的原则,使图24中的1和2、3和4的体积相等,即能确定轮型的宽度了。
第一预成形轮旋压到等体积线,表现在零件内壁与模具完全贴合。
第二预成形轮(X2)的齿间夹角为50°~60°,最两侧的半齿为18°~20°,与X3的夹角相同。
第二预成形轮旋压到位时表现在零件齿形基本填充圆满。
整形轮(X3)的齿间夹角为最终齿形角度,整形轮旋压到位时表现在零件齿形基本填充圆满。
四、工艺调试
1、旋轮及模具安装注意事项
⑴旋轮安装注意事项
旋轮架的结构简图见图25。
旋轮架结构为固定轮架结构,旋轮在轮轴上无法轴向移动,因此在旋轮内安装了一对圆锥滚子轴承,用压盖将轴承固定。
在安装旋轮时,如果安装方法不正确,会使旋轮相对与轮轴产生跳动,在实践中产生过由于安装不当使跳动达0.3mm之多。
因此在安装好旋轮后,最好使用百分表测量一下旋轮的跳动。
如果跳动在0.03mm以上,就需要调整轴承压盖的螺钉,最终将跳动调整到允许范围以内。
另外也可以配磨两轴承中间的垫环,使两轴承外圈加上垫环的总高比旋轮的厚度多0.05~0.1mm,最后靠压盖将两轴承外圈压紧,并与旋轮两端面贴合上,以保证旋轮和轮轴的同轴度。
在拧紧图25中6号螺母时,需要注意松紧程度,该螺母是起到调整轴承间隙用的。
上紧的松紧程度以稍用力能转动旋轮为准,不可过于太紧,如果太紧,可能会产生旋压过程中旋轮不随零件从动旋转的情况。
图25旋轮架装配图
1─轮轴2─压盖3─圆锥滚子轴承4─旋轮5─垫环6─螺母
⑵模具安装注意事项
模具和旋轮在安装前必须经过清洗,保证在安装过程中没有杂质影响装配。
上下模具按照次序装完后,需要在不加载荷情况下测试装配精度,上下模具的相对跳动不能超过0.08mm。
以保证旋压完后的零件质量。
2、程序设计
我们以三个典型的产品来介绍如何编写加工程序。
在编写程序之前请操作人员务必先熟悉《操作说明书》,并能熟练操作机床。
首先介绍一些编程中所需要掌握的名词:
过冲量:
由于系统采用液压驱动,当X轴或Z轴在进给到某一数值时需要由快进转换为工进时,该轴必会沿进给方向冲过一定数值的位移量后才会停下。
所冲过的数值称为过冲量。
因此在设定各轴进给量时需要用所测得的数据减去过冲量,得到的才是所需的数值。
延时:
在某一个工作状态结束后,设定延迟的时间量。
加压:
系统持续对Z轴施加压力。
工进:
X轴和Z轴使用慢速的工作速度做进给运动。
快进:
X轴和Z轴使用快速的工作速度做进给运动或退回。
⑴、劈开轮
零件图纸中需要掌握几个编程所需要的数据,简图见图26。
另外,还需要操作人员实际测绘出三个X轴和Z轴的过冲量。
方法如下:
开机后,依次找到各轴的零点,然后按"F5"进入"程序"状态,按"F3"后输入ceshi.dat以新建一个名为ceshi.dat的程序。
然后编写以下程序:
n 1 0 (第一程序段)
x1 10 2 (x1快进10mm)
x2 10 2 (x2快进10mm)
x3 10 2 (x3快进10mm)
z 20 2 (z快进20mm)
按"F2"存盘后退出。
按"F1"进入"自动"状态,按下"启动"按钮,此时三个X轴和Z轴会同时以快进的速度进给所设定的数值,此时电脑屏幕上显示的数值都要大于所设定的10mm和20mm,记录下四个数值,用各轴的数值分别减去所设定的10mm和20mm,得到的数值即是各轴的过冲量。
按"ESC"退出,然后按"F2"进入"手动"状态,分别选择各轴按"手动退"将四轴退回。
得到各轴的过冲量后,我们还需要各旋轮在距零件1mm处时的尺寸,见图26。
因为我们需要设定X轴由快进转换为工进时的数值。
我们用旋轮距零件1mm处时的尺寸减去过冲量,就得到了快进转工进的数值了。
最后需要确定Z轴压紧零件时的数值,在此假定为E。
在这里我们设定X1、X2、X3旋轮距零件1mm(旋轮快进时防止和零件发生碰撞的安全系数)处时的尺寸分别为:
A、B、C;过冲量分别为Δ1、Δ2、Δ3、Δz。
因为劈开轮只需要使用X1和X3旋轮,不需要X2,因此在开机前不选X2。
程序示例如下:
n
n
0
(第一程序段)
z
E–Δz–2
2
(Z轴快进的数值,其中E减去的2mm为安全系数)
n
2
0
(第二程序段)
z
Δz+2
1
(Z轴工进的数值,工进和快进的数值相加等于E)
n
3
0
(第三程序段)
s
1
0
(主轴旋转)
m
50
1
(Z轴加压)
n
4
0
(第四程序段)
x1
A–Δ1
2
(X1轴快进的数值)
n
5
0
(第五程序段)
x1
Δ1+10
1
(X1轴工进10mm)
n
6
0
(第六程序段)
x3
C–Δ3+Δx
2
(X3轴快进的数值,Δx为X3旋轮进到被X1劈开部分内的距离)
n
7
0
(第七程序段)
x1
13–10+1
1
(X1轴工进的数值)
x3
6
1
(X3轴工进6mm)(注意速度上的搭配,见图3)
n
8
0
(第八程序段)
x1
-20
2
(X1轴快退的20mm)
n
9
0
(第九程序段)
x3
13–6+Δ3–Δx
1
(X3轴继续完成剩余工进值)
n
10
0
(第十程序段)
t
1.5
0
(延时1.5秒)
n
11
0
(第十一程序段)
x3
-5
2
(X3轴快退5mm,让X3旋轮在主轴停转之前退出)
n
12
0
(第十二程序段)
s
0
0
(主轴停止转动)
m
60
0
(Z轴撤压)
n
13
0
(第十三程序段)
x3
-15
2
(X3轴快退的数值)
z
-60
2
(Z轴快退的数值)
编程结束后记住按"F2"存盘。
在计算数值时需要注意的是Z轴向下进给的数值E等于工进和快进的数值相加;X1轴快进和工进总的进给数值应等于A+1+13(见图26);X3轴快进和工进总的进给数值应等于C+1+13(见图26)。
图26
⑵、折叠轮
零件图和毛坯图中需要掌握几个编程所需要的数据,简图见图27。
图27
操作人员使用ceshi.dat程序实际测绘出三个X轴和Z轴的过冲量。
只要各轴快进的速度没有调整,过冲量基本是保持不变的,只是与启动液压泵站时的油温有关,油温的变化会改变过冲量的大小。
因此给每个轴都留有1~2mm的安全系数。
同时也希望操作人员能经常测绘出各轴的过冲量,随时调整程序的数据,以确保安全和优质生产。
因为折叠轮同样只需要使用X1和X3旋轮,不需要X2,因此在开机前不选X2。
得到各轴的过冲量后,我们还需要X1旋轮在距零件1mm处时的尺寸,X3旋轮是在X1旋压完后测量此时距零件1mm处时的尺寸;最后需要确定Z轴压紧零件时的数值,在此假定为E。
在这里我们设定X1、X3旋轮距零件1mm处时的尺寸分别为:
A、C;过冲量分别为Δ1、Δ3、Δz。
由图27能看出,毛坯的原始高度为37mm,旋压成形后为21mm。
其图中的2mm尺寸部分没有参与变形。
此时从毛坯到成形零件的总压缩量为37-21-2=14mm。
旋轮进给深度为14.3mm。
在旋压折叠轮时需要速度协调一致,而且Z轴需要以不同速度分段进给,因此需