东莞精益生产方式计划.docx
《东莞精益生产方式计划.docx》由会员分享,可在线阅读,更多相关《东莞精益生产方式计划.docx(33页珍藏版)》请在冰豆网上搜索。
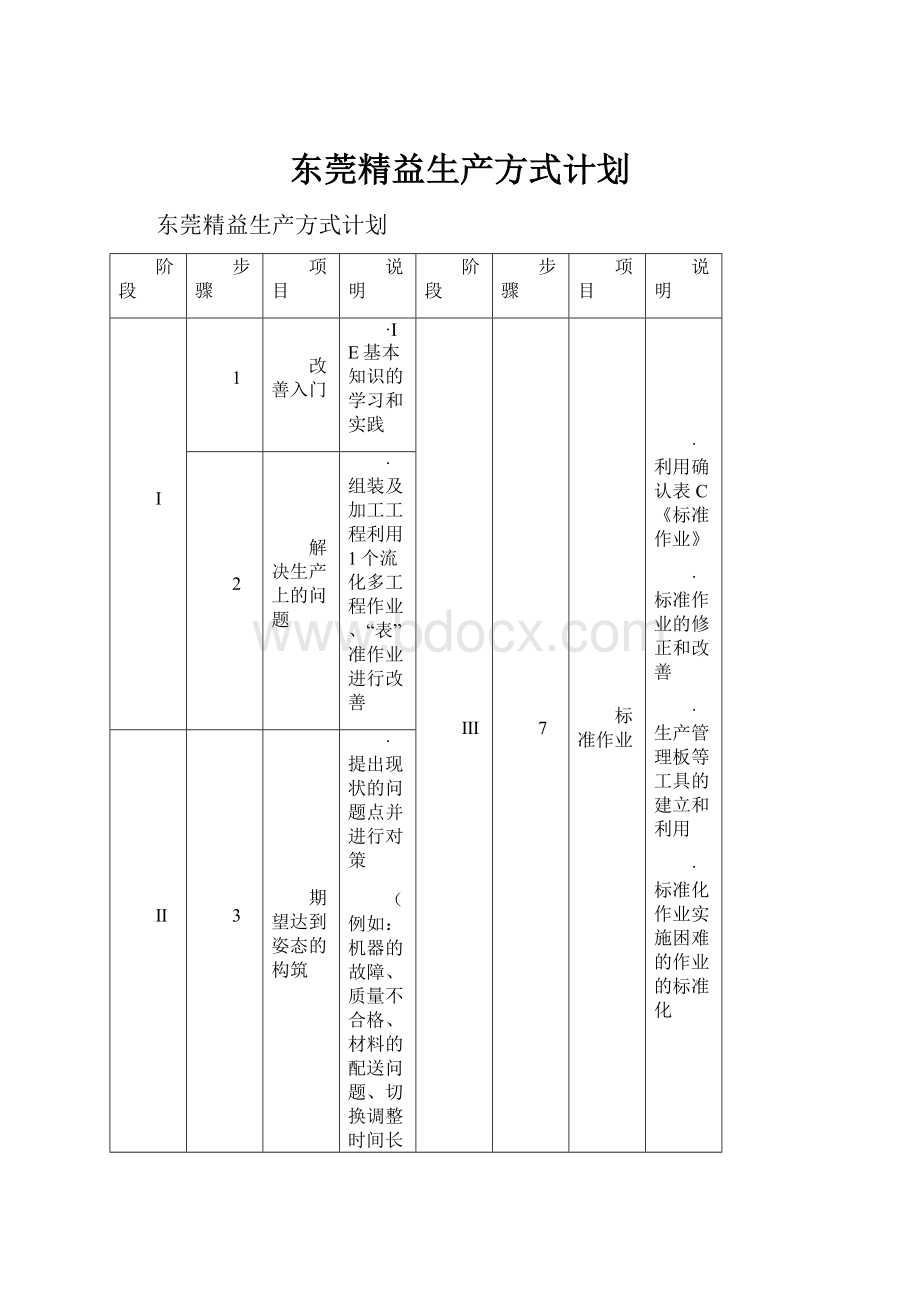
东莞精益生产方式计划
东莞精益生产方式计划
阶段
步骤
项目
说明
阶段
步骤
项目
说明
Ⅰ
1
改善入门
·IE基本知识的学习和实践
Ⅲ
7
标准作业
·利用确认表C《标准作业》
·标准作业的修正和改善
·生产管理板等工具的建立和利用
·标准化作业实施困难的作业的标准化
2
解决生产上的问题
·组装及加工工程利用1个流化多工程作业、“表”准作业进行改善
Ⅱ
3
期望达到姿态的构筑
·提出现状的问题点并进行对策
(例如:
机器的故障、质量不合格、材料的配送问题、切换调整时间长等问题)
4
整流化
·最有效率的生产状态的描述
·整流化的构想和样板生产线的设定
8
消除浪费
·利用确认表D-J
·7大浪费的彻底消除
·详细参照确认表
Ⅲ
5
建成流动化工程
·利用确认表A《流动化》
·建立流动化的工程
·形成后工程拉引生产(看板生产)
6
目视化管理
·利用确认表B《目视管理》
·建立对异常进行管理的方法,防止异常的再次发生
·对物的放置场所、放置方法进行整理(5S)
·看板运用的整备
·目视管理用具的整备
Ⅳ
9
进一步提高水平
·全工程采用流动化生产
·再次利用确认表A-J
10
完成化
·生产接近期望达到的状态
·再次利用确认表A-J
改善的目标及改善的必要项目数数
确认表
全项目数
必要项目数
记号
改善目标
改善主题
阶段Ⅲ
阶段Ⅳ
步骤9
阶段Ⅳ
步骤10
A
建立流动生产的型
流动化
16
12
15
16
B
组成流动化的生产
目视管理
42
32
38
42
C
组成流动化的作业
标准作业
30
23
27
30
D
在需要的时间制造需要的东西
制造过剩的浪费
16
12
15
16
E
制造需要的东西
制造不良品的浪费
20
15
18
20
F
人的100%利用
等待的浪费
14
11
13
14
G
在需要的时间进行需要的运输
搬运的浪费
24
18
22
24
H
加工时间的缩短
加工的浪费
22
17
20
22
I
作业时间的缩短
动作的浪费
19
15
18
19
J
消除集中各种浪费的在库
在库的浪费
17
13
16
17
合计
220
168
202
220
样板生产线的现状调查
项目
加工工序
单件加工时间(s)
不良率(%)
设备数(台)
月平均产量(个)
人数(人)
平均故障时间(s/月)
切换时间(s)
稼动率(%)
可动率(%)
在库数量(月)
部门:
作成者:
整流化的构想
对象产品:
年月日
项目
记入
1.期待达到状态的形象
2.整流化生产线的概要流程图
3.生产线的生产品种和生产量
生产线名
生产线性格
(专用、混流、特殊)
生产线投入的主要产品品种或产品编号
数量
(日生产量)
T/T
现状
人数
4.平面布置概要
【现状】
【整流化构想】
Page1/2
年月日
部门:
做成:
主要改善成员:
样板生产线设定
(注:
除1、2、8项外,记入现状)
项目
记入
1.样板生产线名称
2.样板生产线的工程流程图
3.现状的平面布置图
4.不同工程能力调查
工程
①理论上生产能力
②切换调整(时间×次数)
③其他富余率
④实际能力
①-②-③
备注
Page2/2
5.生产品种和节拍时间(T/T)
品种
数量
加工时间
标准品换算系数
换算数量
T/T
实T/T
6.生产指示方法或看板周转的方法(图示)
7.问题点或制约条件
8.目标
(现状→目标值)
期限年月日
丰田生产方式建立确认表A(流动化)
判定者
评价者2
评价者1
月日
月日
月日
年月日开始年月日完成
车间
样板线
(工程)
项目
评价
判定
记事
1.全工程、全产品是否都采用了整流化构想?
是否选定了样板生产线?
●
●
●
2.设备是否是按照工程顺序排列的?
是否采用了专门的设备?
●
●
●
3.是否决定了投入的产品?
投入量是否稳定?
●
●
●
4.加工、组装、精密切削工程是一个流吗?
●
●
●
5.装置型设备等批量生产设备是否做到了小批量?
●
●
●
无
6.加工、组装、精密切削工程是否实现同期化了?
(装置型设备是否是只生产必要的数量?
)
●
●
●
7.作业是否是完成了一个工序后马上进入下工序?
(多工程作业的做法)
●
●
●
8.是否建立了流动化的生产?
是否实施“表”准作业化(往返作业化)了?
●
●
●
9.是否有作业员兼任样板生产线以外的作业?
●
●
●
10.为达到多能化,是否对作业员进行训练评价了?
●
●
●
11.是否消除了中间在库和半成品?
●
●
●
12.是否进行了缩短切换调整时间的改善?
●
●
●
13.加工、组装、精密加工工程是按照顺序进行切换调整的吗?
●
●
●
14.样板线的设备是否与其他生产线的设备共用?
●
●
●
15.设备、工程间如果是分离的无法实现同期化,是否依据看板来实现后工程拉动了?
●
●
●
16.样板生产线的表示是否能够判明工程的顺序?
●
●
●
判定项目数
阶段Ⅲ要达到12以上项目数
阶段Ⅳ步骤9要达到15以上项目数
阶段Ⅳ步骤10要达到16个项目数
丰田生产方式建立确认表B(目视化管理)
CHKsheetBPage1/3
判定者
评价者2
评价者1
月日
月日
月日
年月日开始年月日完成
车间
样板线
(工程)
项目
评价
判定
记事
1.是否开展了5S活动?
机械、工具、备品、地面等是否都是干净的?
●
●
●
2.是否确定了平面的位置编号(门牌号)并很容易能够判断?
●
●
●
3.出厂是否适当考虑了方便利用的功能(位置、场所、长、高、样式、表示方法等)?
●
●
●
4.所以物品(材料、中间产品、产品、设备、备品、工具、用具、容器、搬运工具等)的放置场所是否确定了?
●
●
●
5.是否在规定以外的场所有物品放置?
不需要品是否都清除了?
●
●
●
6.材料、辅助材料的供应是否直接送到生产线上?
(是否有中间的临时放置场所?
)
●
●
●
7.材料、产品、辅助材料是否是先进先出了?
●
●
●
8.对物品是否有合适的判断方法?
如果多或少了是否能够一目了然?
●
●
●
9.不良品是否就那么任其发生?
●
●
●
10.切换调整品是否任意放置?
●
●
●
11.机台、生产线的名称、编号是否清楚地表示了?
●
●
●
12.要领书、质量标准、技术标准、指导书、注意书等揭示物,任何时间都是完备的吗?
●
●
●
13.物品是否都必须使用看板进行管理?
●
●
●
14.看板的样式、记载的项目、内容都适当吗?
●
●
●
15.按照顺序向外部发行看板,是否必须按照看板要求制造?
是否实行了按顺序进行生产?
●
●
●
16.即使是批量生产,也是按照生产顺序进行的吗?
每个批量的生产时间是否规定了?
●
●
●
17.看板发行的方法、使用方法的规定是否作成了?
能否顺利进行周转?
●
●
●
18.看板箱是否在必要的场所设置了?
●
●
●
CHKsheetBpage2/3
19.是否切实地对看板进行维护了?
对看板进行管理了吗?
●
●
●
20.涂装、热处理等连续生产工程,产品的位置制定方式是否得到利用了?
●
●
●
21.现在生产是什么产品,在这个设备位置能否判断明白?
●
●
●
22.生产线停止的时候,能否判明停止的理由?
●
●
●
23.下次切换调整时间的预定和将要加工的产品品种是否能够判明?
●
●
●
24.下次生产中需要使用的材料、辅助材料的准备是否能够运用时间表进行判断并应用?
●
●
●
25.特急品、加塞品什么时间生产能迅速判明吗?
●
●
26.生产进度延迟了能迅速判明吗?
●
●
●
27.是否利用了生产管理板?
●
●
●
28.是否利用图表来表示必要的生产指标(生产量、生产性、稼动率、切换时间、不良品件数、小的异常停止等)的推移状况?
现场是否采取了能突出效果的揭示方法了?
●
●
●
29.问题点对策、改善状况等是否在现场张贴了?
●
●
●
30.看板是否对作为目视管理的工具发挥作用了?
●
●
●
31.针对异常都做了那些规定?
是否明确了正常和异常时的有关做法?
●
●
●
32.对异常是否能够作出判断?
能尽早发现异常吗?
●
●
●
33.出现异常时,设备或生产线能自动停下吗?
34.加工、组装、精密切削等人工作业是,生产线发生异常时能立即停止吗?
35.是否设置了能够告知异常的“表示灯”、“警报”、“呼叫灯”等装置?
36.是否建立了异常发生时尽早进行处理的体制?
●
●
●
37.是否确定了异常的对应方法?
是否禁止作业人员私自进行判断和处置?
●
●
●
38.是否进行了异常记录?
异常再发生防止的对策是否切实地实施了?
●
●
●
39.看板的种类的选择是否适当(通常看板、信号看板、位置制定、特殊看板等)?
●
●
●
CHKsheetBpage3/3
40.投入看板的工程的生产指示全部都是按照看板进行生产的吗?
●
●
●
41.对于特急生产、加塞生产、临时生产(极小批量品、试做品等)在看板工程生产时,是否仔细研究了看板的利用方法?
42.是否利用产品编号、管理编号(缩短了的编号或背番号)来表示产品了?
●
●
●
判定项目数
阶段Ⅲ要达到32以上项目数
阶段Ⅳ步骤9要达到38以上项目数
阶段Ⅳ步骤10要达到42个项目数
38
丰田生产方式建立确认表C(标准作业)
CHKsheetCpage1/2
判定者
评价者2
评价者1
月日
月日
月日
年月日开始年月日完成
车间
样板线
(工程)
项目
评价
判定
记事
1.是否将标准作业运用于以操作者为中心的作业中,以使全体了解作业要求?
(T/T、作业顺序、标准待加工品)
●
●
●
2.生产能够平准化吗?
另外针对平准化是否进行了持续改善和努力?
●
●
●
3.“工程能力表”、“标准作业组合票”、“标准作业票”等成套作业标准是否做好了?
●
●
●
4.标准作业是否揭示在现场容易看见的位置?
●
●
●
5.经常性地对标准作业进行改进了吗?
(禁止按个人想法作业)
●
●
●
6.是否对作业员进行了有关标准作业的教育和培训?
●
●
●
7.作业者无法按标准作业进行作业时,是否将作业停下来呼叫责任者?
●
●
●
8.是否对作业标准进行不断的修正和改善?
(标准作业组合票、标准作业票都经常进行修改吗?
)
●
●
●
9.在不断重复的作业中,不是每回都要进行的作业是否也标准化了?
(例如:
材料更换、抽样检查、刀具更换、捆包等)
●
●
●
10.装置型设备是否也尽可能地采用了不断重复的作业方式?
如果有困难的话,是否也采用呼叫方式?
●
●
●
11.切换调整时,是否事先规定了作业手段和标准时间?
●
●
●
12.外作业、部件供给、搬运等生产线以外的作业是否也标准化了?
●
●
●
13.是否决定了外作业、部件供给、搬运等有谁来做,必要时,是由专任者实施的吗?
●
●
●
14.确定了生产线的责任者的同时,其职责范围是否也明确了?
●
●
●
15.针对极少量品、限定品、特殊样品等非流动品,是否采用其他方式规定使用方法了?
●
●
●
16.是否确定了在作业中间出现不良或问题时的处置方法?
●
●
●
17.是否确定了材料欠缺时的处置方法?
●
●
●
18.缺人时,补充新人或替代作业者的做法是否明确?
●
●
●
19.多工程作业时,各作业者所花费的时间是不同的,针对这样的问题是否进行了彻底的对策?
●
●
●
20.作业发生延迟进行呼叫,生产线责任者是否立即进行支援了,是否恢复到正常运行了?
●
●
●
21.仅仅是小的作业延迟的话,前后作业员是否合力相助以达到产量?
22.根据标准作业决定的生产量,是否每日都达成了?
●
●
●
23.生产管理板是否很充分地运用了?
●
●
●
24.基础产品是否很灵活地运用了?
25.是采取“一起动”方式了?
作业开始时,是否所有作业员一齐开始生产作业?
(作业开始时,是否各工序都保留了产品?
)
●
●
●
26.是否遵守定位置停止的原则?
27.是否有看不见的“水下作业”?
●
●
●
28.是否有离散小岛式的作业?
●
●
●
29.为使标准作业简单方便,是否进行了紧密型的平面布置
●
●
●
30.装置型设备操作人员的作业程序和标准时间是否也做了规定?
●
●
●
判定项目数
阶段Ⅲ要达到23以上项目数
阶段Ⅳ步骤9要达到27以上项目数
阶段Ⅳ步骤10要达到30个项目数
27
CHKsheetpage2/2
丰田生产方式建立确认表D(制造过剩浪费)
CHKsheetDpage1/2
判定者
评价者2
评价者1
月日
月日
月日
年月日开始年月日完成
车间
样板线
(工程)
项目
评价
判定
记事
1.生产计划的制定方法标准化以后,是否合理?
●
●
●
2.出货数量与生产计划相吻合,日生产量是平准化的吗?
●
●
●
3.是绝对按照只是数量生产不制造多余的产品吗?
●
●
●
4.没有看板是绝对不能进行生产吗?
●
●
●
5.在“只有需要时制造产品”的原则下,是否有不满足这个原则要求的生产计划?
生产中是否存在问题?
●
●
●
6.批量生产的设备是否进行小批量生产?
每次生产的批量都是一定的吗?
●
●
●
7.因为材料更换和切换调整效率低的理由,是否生产了比出货批量大很多的生产批量?
关于这个问题是否认真研究并改善了?
●
●
●
8.看到工程的加工和出厂状况能否判断出数量及生产指示是否适当?
●
●
●
9.规定数量外的中间半成品、完成品是否没有放置位置?
●
●
●
10.加工时间有差异的产品在同一生产线流动的场合,为了吸收这个差异,是否能够容忍差异而不超量进行生产?
这个最大量规定了吗?
●
●
●
11.工件的收容数(一箱、一盒、一台、一卷的数量)是否规定了?
是否规定了尽可能小的数量?
●
●
●
12.为实现小批量化,切换调整的时间是否进行了改善?
(实现单一调整了吗?
)
●
●
●
13.根据标准作业要求作业不能进行,本作业在等待的时候,其他作业还在继续进行吗?
●
●
●
14.对于整体的作业,在等待的时候,作业员是否根据自己对下个作业的判断来帮助进行其他工作了?
●
●
●
15.作业改善中,所有生产线在等待的情况发生时,原则上作业员什么都不做进行等待,以使等待的浪费显现化,针对这样的问题改善是否有效果?
●
●
●
CHKsheetDpage2/2
16.生产量是否足够?
是否有因为害怕制造不足而先行进行生产的情况存在?
●
●
●
判定项目数
阶段Ⅲ要达到12以上项目数
阶段Ⅳ步骤9要达到15以上项目数
阶段Ⅳ步骤10要达到16个项目数
丰田生产方式建立确认表E(生产不良品的浪费)
CHKsheetEpage1/2
判定者
评价者2
评价者1
月日
月日
月日
年月日开始年月日完成
车间
样板线
(工程)
项目
评价
判定
记事
1.针对不良的对策是否彻底?
不良是否极少?
2.不良发生时,是否按照现场、现物、现实的原则,立即动手进行改善?
(没有处理好的运用5个为什么进行改善,达到防止再发)
3.如果出现了不良,生产线是否要停止下来?
4.是否利用防错措施来防止不良的流出?
5.是否利用向前反馈和向后反馈的方法来沟通不良的修正方法?
6.后工程出现不良的信息是否向发生不良的工程进行传达?
7.慢性不良的工程能力调查及SQC的运用是否获得了彻底的改善效果?
8.不良品的修正、再捡、挑选等作业是由制造者来做的吗?
9.是否将不良对策进行记录了?
10.在线检查是否实施了?
是按制造顺序进行了吗?
11.特定情况以外,工程以外是否设置了检查场所,进行批量检查?
12.在标准作业中,检查的要点和程序是否纳入其中了?
13.标准作业中,品质相关的要点上是否纳入了?
14.不良的数据是否恰当地收集了?
在利用进行改善同时是否为达到提高品质意识提高的目的在现场揭示了这些数据?
15.是否设置了红色的不良品箱吗?
16.为提高作业者的品质意识,是否开展了各种各样的活动?
CHKsheetEpage2/2
17.是否建立针对不良的体制了
18.外协工厂供应商的不良对策是否有效?
材料不良是否几乎没有?
19.对作业者是否进行了充实的教育?
有关遵守规定方面的确认是否实施了?
20.生产计划是否估计了不良品数?
判定项目数
阶段Ⅲ要达到15以上项目数
阶段Ⅳ步骤9要达到18以上项目数
阶段Ⅳ步骤10要达到20个项目数
丰田生产方式建立确认表F(等待的浪费)
CHKsheetFpage1/1
判定者
评价者2
评价者1
月日
月日
月日
年月日开始年月日完成
车间
样板线
(工程)
项目
评价
判定
记事
1.反复往返作业的标准作业时间是否没有一点等待的时间?
任何作业等待的时间都能发现吗?
●
●
●
2.根据标准作业进行机械加工时,能否发现在其侧边有站立、观看、等待的现象?
●
●
●
3.对于装置型的工程,是否有在看机器的工作?
●
●
●
4.工程没有改善前是否允许作业员等待工作?
●
●
●
5.作业的空闲时间内作业员是在等待工作吗?
●
●
●
6.依据标准作业进行改善缩短了各作业者的作业时间T/T时,生产线内作业员是否有作业时间不均衡的现象?
(作业者在T/T内满负荷地工作时,最后的一个人因为出现零头而等活)
●
●
●
7.来自前工程等处的工件或材料中断时,作业者是否要等待?
●
●
●
8.后工程发生问题工程不能进展时,本工程的作业员是否要进行等待?
●
●
●
9.装置型工程,作业者在规定作业以外的时间,是否在固定的位置上等待?
●
●
●
10.装置型工程或外围作业的作业者是否到处走动?
●
●
●
11.作业者在发生等待时,监督者、责任者立即进行处置后,是否进一步彻底地进行再发防止了?
●
●
●
12.等待发生时,是否将这个改善简单地进行了记录?
●
●
●
13.按照标准作业时会产生一些短时间的延迟现象,是否划分了区域进行互助,以防止产生等待的时间?
14.是否有离散的小岛或定员制的工程?
●
●
●
判定项目数
阶段Ⅲ要达到11以上项目数
阶段Ⅳ步骤9要达到13以上项目数
阶段Ⅳ步骤10要达到14个项目数
13
丰田生产方式建立确认表G(搬运的浪费)
CHKsheetGpage1/2
判定者
评价者2
评价者1
月日
月日
月日
年月日开始年月日完成
车间
样板线
(工程)
项目
评价
判定
记事
1.搬运的方法是否做成规定了?
(路线、时间、内容、数量、场所、方法、人)
●
●
●
2.是否利用了独自的搬运方式
●
●
●
3.是否按照后工序拉动的原则进行搬运的
●
●
●
4.是在搬运看板的原则下进行搬运的吗?
看板以外的搬运指示是否存在
●
●
●
5.在没有采用看板的工程中,是否规定了搬运的方法(时间、数量)?
●
●
●
6.“物品”是否同看板一起移动
●
●
●
7.搬运是否设立了专门的担当者
●
●
●
8.生产线作业员是否需要离开生产线取物品
●
●
●
9.紧急需要材料时,生产线作业员是否呼