多工位级进模毕业设计概要.docx
《多工位级进模毕业设计概要.docx》由会员分享,可在线阅读,更多相关《多工位级进模毕业设计概要.docx(34页珍藏版)》请在冰豆网上搜索。
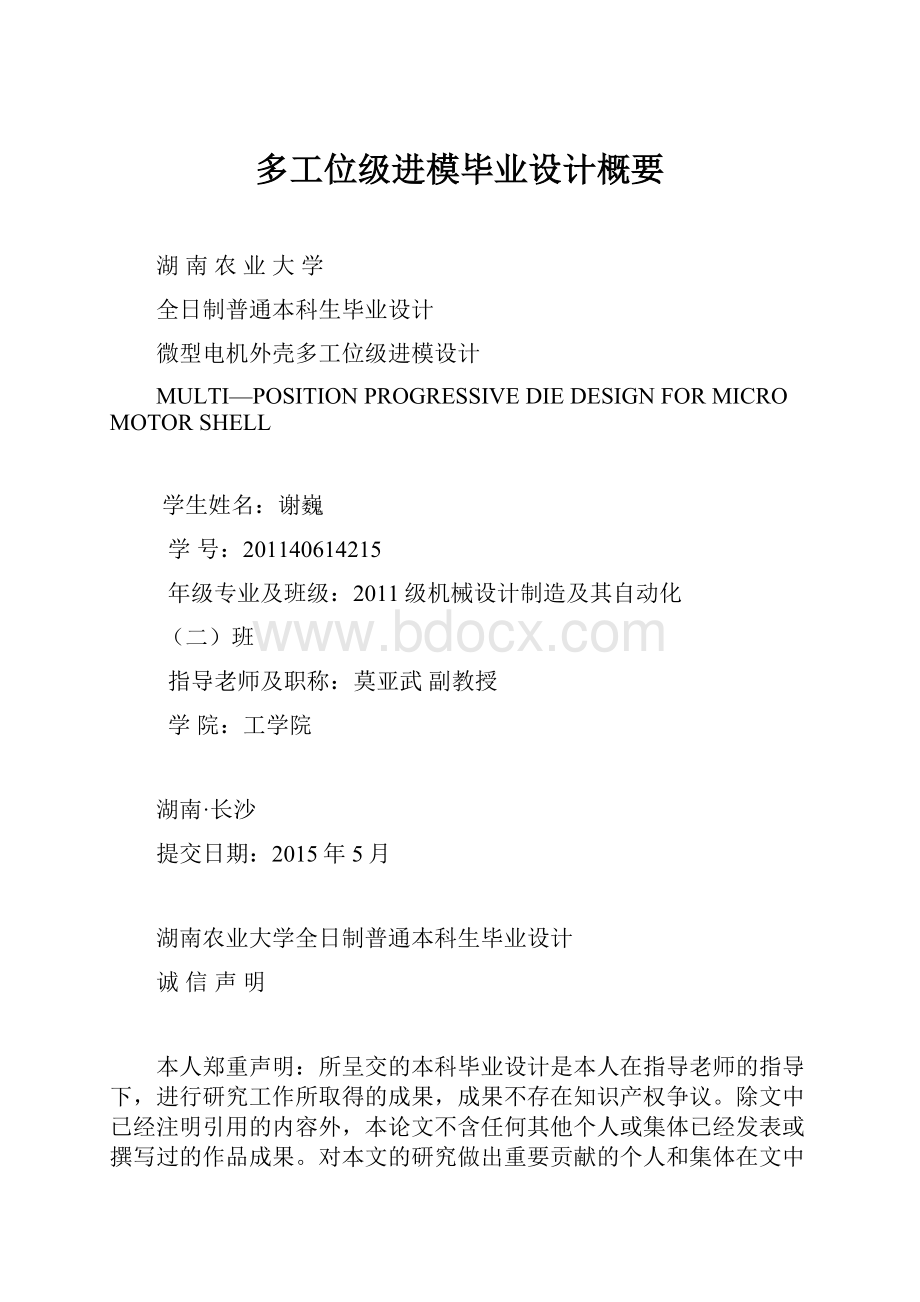
多工位级进模毕业设计概要
湖南农业大学
全日制普通本科生毕业设计
微型电机外壳多工位级进模设计
MULTI—POSITIONPROGRESSIVEDIEDESIGNFORMICROMOTORSHELL
学生姓名:
谢巍
学号:
201140614215
年级专业及班级:
2011级机械设计制造及其自动化
(二)班
指导老师及职称:
莫亚武副教授
学院:
工学院
湖南·长沙
提交日期:
2015年5月
湖南农业大学全日制普通本科生毕业设计
诚信声明
本人郑重声明:
所呈交的本科毕业设计是本人在指导老师的指导下,进行研究工作所取得的成果,成果不存在知识产权争议。
除文中已经注明引用的内容外,本论文不含任何其他个人或集体已经发表或撰写过的作品成果。
对本文的研究做出重要贡献的个人和集体在文中均作了明确的说明并表示了谢意。
本人完全意识到本声明的法律结果由本人承担。
毕业设计作者签名:
年月日
微型电机外壳多工位级进模设计
学生:
谢巍
指导老师:
莫亚武
(湖南农业大学工学院,长沙410128)
摘要:
对微型电机外壳进行了冲压工艺性分析,采用多工位级进模冲压生产。
介绍了制件工步排样设计、模具结构设计及模具工作零件设计。
模具采用自动送料机构作粗定位、导正销精定位,保证了送料精度。
凸、凹模镶块材料选用DC53,提高了模具寿命和减少加工序。
模具设计采用UG软件完成实体建模后导出dwg文件,并通过AutoCAD软件处理,完成平面图设计。
目前,模具运行情况良好,产品质量稳定,达到了预期效果。
关键词:
微型电机外壳;冲压工艺;排样设计;级进模;零件的冲压工艺性分析
Multi—PositionProgressiveDieDesignforMicroMotorShell
Student:
XieWei
Tutor:
YawuMo
(CollegeofEngineering,HunanAgriculturalUniversity,Changsha410128,China)
Abstract:
Basedonprocessanalysisofthemicromotorshell,multi·positionprogressiVediewasusedinproduction.Striplayoutdesign,diestructuredesignanddieworkingpartsdesignwereintroduced.Withtheautomaticfeedingmechanismtocoarselypositionandthepilotpintoaccuratelyposition,thefeedingaccuracywasguaranteed.DC53wasusedforinsertblockofbothconVexandconcaVedietoimproVedielifeandreducemachiningoperations.UGwasusedformodeldesign,andthendwgfileexportfromthemodelwasprocesseditbyAutocadtogetthe2Ddesign.Atpresent,thedieisrunningweUwithstableproductquality,whichmeetsthedesiredeffects.
Keywords:
Micromotorshell;Punchingtechnology;Layoutdesign;Progressivedie
1前言
现代制造业的发展,尤其是电子,电器,仪表,汽车等产品的发展,几乎都离不开模具。
能否向社会提供更多的优质模具,会直接影响到工业产品的质量,生产成本
和更新换代的速度。
合理的模具结构可有效的实现冲模的功能,达到成本低,制造周期短和操作安全性,并能保证产品零件的各项技术要求,正确选择适用的模具结构是模具设计师提高技术素质的体现。
随着国民经济总量和工业产品技术的不断发展,各行各业对模具的需求量越来越大,技术要求也有越来越高。
业内专家认为,虽然模具种类繁多,但在十一五期间其发展重点应该是既能满足大量需求,又有较高技术含量,特别是目前国内尚不能自给,需大量进口模具和能代表发展方面的大型,精密,复杂,长寿模具。
又由于模具标准件的种类,数量,水平,生产集中度等对整个模具行业的发展有重大影响,因此,一些重要的模具标准件也必须重点发展,而且其发展速度应快于模具的发展速度,这样才能不断提高我国的模具标准化水平,从而提高模具质量,缩短模具生产周期及降低成本。
多工位级进模和精冲模代表了冲压模具的发展方向,精度要求和寿命要求极高,主要为电子工业,汽车,仪器仪表,电机电器等配套。
这两种模具,国内已有相当基础,并已引进了国外技术设备,个别企业生产的产品已达到世界水平,但大部分仍有较大差距,总量也供不应求,进口较多,整体水平有待提高。
模具制造的特点:
制造质量要求高,形状复杂,模具生产为单件多品种生产,材料硬度高,生产周期短,成套性生产等。
研究模具制造的过程,就是研究探讨模具制造的可能性和如何制造的问题,进而研究怎样以较低的成本,较短的周期制造质量较高的模具的问题。
成本,周期,和质量是模具制造的主要技术经济指标。
严格的讲,寻求这三个指标的最佳值,但从模具制造的角度考虑是不够的应综合考虑设计,制造和使用者三个环节,三者的协调。
设计出考虑满足使用功能外,还要充分考虑制造的可能性:
制造要满足设计要求,同时也制约设计,并指导用户使用。
2冲压的介绍
2.1冲压的概念和发展
冲压是利用安装在冲压设备,主要是压力机上的模具对材料施加压力,使其产生分离或塑性变形,从而获得所需零件(俗称冲压或冲压件)的一种压力加工方法。
冲压通常是在常温下对材料进行冷变形加工,且主要采用板料加工成所需零件,所以也叫冷冲压或板料冲压。
冲压是材料压力加工或塑性加工的主要方法之一,隶属于材料成型工程术。
冲压所使用的模具称为冲压模具,简称冲模。
冲模是讲材料(金属或非金属)批量加工成所需冲件的专用工具。
冲模在冲压中至关重要,没有符合要求的冲模,批量生产就难以进行;没有先进的冲模,先进的冲压工艺就无法实现。
冲压工艺与模具、冲压设备和冲压材料构成冲压加工的三要素,只有它们相互结合才能得出冲压件。
冲压在现代工业中,尤其是大批量生产中应用十分广泛。
相当多的工业部门越来越多地采用冲压法加工产品零件,如汽车、农机、仪器仪表,电子,航空航天,家电及轻工等行业。
在这些工业部门中,冲压件所占的比重都相当大,少则60%以上,多则90%以上。
不少过去用锻造铸造和切削加工方法制造的零件,现在大多数也被质量轻,刚度好的冲压件所代替。
因此可以说,如果生产中不采用冲压工艺,许多工业部门要提高生产效率和产品质量、降低生产成本、快速进行产品更新换代等都是难以实现的。
2.2冲压的基本工序及模具
由于冲压加工的零件种类繁多,各类零件的形状、尺寸和精度要求有各不相同,因而生产中采用的冲压工艺方法也是多种多样的。
概括起来,可分为分离工序和成形工序两大类;分离工序是指使坯料沿一定轮廓线分离而获得一定形状、尺寸和断面质量的冲压工序;成形工序是指使坯料在不破裂的条件下产生塑性变形而获得一定形状和尺寸的冲压件的工序。
上述两类工序,按基本变形方式不同又可分为冲裁、弯曲、拉深和成形四种基本工序,每种基本工序还包含有多种单一工序。
在实际生产中,当冲压件的生产批量较大、尺寸较少而公差要求较小时,若用分散的单一工序来冲压时不经济甚至很难达到要求。
这时在工艺上多采用集中的方案,即把两种或两种以上的单工序集中在一副模具内完成,按组合的方法不同,又可将其分为复合、级进和复合-级进三种组合方式。
复合冲压——在压力机的一次工作行程中,在模具的同一工位同时完成两种或两种以上不同工序的方式。
级进冲压——在压力机的一次工作行程中,按照一定的顺序在同一副模具的不同工位上完成两种或两种以上不同工序的方式。
复合-级进——在一副模具上包含复合和级进两种方式的组合工序。
2.3冲压技术的现状及发展方向
2.3.1冲压成形理论及冲压工艺方面
冲压成形理论的研究是提高冲压技术的基础。
目前,国内外对冲压成形理论的研究非常重视,在材料冲压性能研究,冲压成形过程应力应变分析、板料变形规律研究及坯料与模具之间的相互作用研究等方面取得较大的进展。
特别是随着计算机技术的飞跃发展和塑性变形理论的进一步完善,近年来国内外已开始应用塑性成形过程的计算机模拟技术,即利用有限元等有值分析方法模拟金属的塑性成形过程,根据分析结果,设计人员可预测某一工艺方案成形的可行性分析及可能出现的问题,并通过在计算机上选择修改相关参数,可实现工艺及模具的优化设计。
这样既节省了昂贵的试模费用,也缩短了制模周期。
2.3.2冲模是实现冲压生产的基本条件
在冲模的设计制造上,目前正朝着以下两个方面发展:
一方面,为了适应高速、自动、精密、安全等大批量现代生产的需要,冲模正向高效率、高精度、高寿命及多工位、多功能方向发展,与此相比适应的新型模具材料及其热处理技术,各种高效、精密、数控自动化的模具加工机床和检测设备以及模具CAD/CAM技术也在迅速发展;另一方面,为了适应产品更新换代和试制或小批量生产的需要,锌基合金冲模、聚氨酯橡胶冲模、薄板冲模、钢带冲模、组合冲模等各种简易冲模及其制造技术也得到了迅速发展。
精密、高效的多工位及多工位功能级进模和大型复杂的汽车覆盖件冲模代表了现代冲模的技术水平。
目前,50个工位以上的级进模进距精度可达到2微米,多功能级进模不仅可以完成冲压全过程,还可完成焊接、装配等工序。
我国已能自行设计制造出达到国际水平的精度大2-5微米,进距精度2-3微米,总寿命达1亿万次。
我国主要汽车模具企业,已能生产成套轿车覆盖件模具,在设计制造方法、手段方面已基本达到了国际水平,但在制造方法手段方面已基本达到了国际水平,模具结构、功能方面也已接近国际水平,但在制造质量、精度、制造周期和成本方面与国外相比还存在一定差距。
2.3.3冲压设和冲压生产自动化方面
性能良好的冲压设备是提高冲压生产技术水平的基本条件,高精度、高寿命、高效率的冲模需要高精度、高自动化的冲压设备相匹配。
为了满足大批量高速生产的需要,目前冲压设备也有单工位、单功能、低速压力机朝着多工位、多功能、高速和数控方面发展,加之机械乃至机器人的大量使用,使冲压生产效率得到大幅度提高,各式各样的冲压自动线和高速自动压力机纷纷投入使用,如在数控四边折弯机中送入板料毛坯后,在计算机程序控制下便可依次完成四边弯曲,从而大幅度提高精度和生产率
2.3.4冲压标准化及专业生产方面
模具的标准化及专业化生产,已得到模具行业的广泛重视。
因为冲模属单件小批量生产,冲模零件既具有一定的复杂性和精密性,又具有一定的结构典型性。
因此,只有实现了冲模的标准化,才能使冲模和冲模零件的生产实现专业化、商品化,从而降低模具的成本,提高模具的质量和缩短制造周期。
目前,国外先进工业国家模具标准化成产程度已达70%,模具厂只需设计制造工作零件,大部分模具零件均从标准件厂购买,使生产率大幅度提高。
模具制造厂专业化程度越不定期越高,分工越来越细,如目前有模架厂、顶杆厂、热处理厂等,甚至某些模具厂仅专业化制造某类产品的冲裁模或弯曲模,这样更有利于制造水平的提高和制造周期的缩短。
3零件的冲压工艺性分析
图1微型电动机外壳
FiglMicromotorshell
图1所示为微型电机外壳,用厚度为t=0.6mm的马口铁冲压而成。
马口铁又叫镀锡铁,是电镀锡薄钢板的俗称,英文缩写为SPTE,是指两面镀有商业纯锡的冷轧低碳薄钢板或钢带。
锡主要起防止腐蚀与生锈的作用,并将钢的强度和成形性与锡的耐蚀性、锡焊性和美观的外表结合于一种材料之中,具有耐腐蚀、无毒、强度高和延展性好的特性。
从图1中可以看出,微型电机外壳结构较简单,属筒形拉深件,但成形质量要求较高。
外径(Ф11.9±0.05)mm和底部孔(Ф8±0.05)mm均有IT11级公差要求,高度尺寸(8±0.03)mm为ITl0级公差,筒壁圆度误差要求不大于0.05mm,筒壁相对于底部的垂直度误差要求不大于0.05mm,内外不允许有划伤,筒壁底部圆角处不允许有过度拉薄现象。
4工艺方案的确定
产品零件为大批量生产,要求生产率高,产品质量稳定,模具寿命50万冲次以上,因此采用级进模通过连续拉深的生产方式比较经济和合理,在压力机滑块每次行程中,在同一副模具的不同位置,同时完成二道或二道以上的工序就叫级进模,使用级进模可以把两道或更多的工序合并在同一副模具中完成,所以用级进模生产可以减少模具和设备的数量,提高生产率并容易实现自动化。
但比制造单工序模复杂,成本也高。
用级进模冲压,必须解决条料的准确定位问题,才有可能保证工件的质量。
本零件成型的的方案为先连续拉深,然后再冲底部孔,最后挤压切边。
5工艺设计计算
5.1毛坯尺寸的确定
对于不变薄拉深,虽然在拉深过程中板料的厚度有增厚也有变薄,但实践证明,拉深件的平均厚度与坯料厚度相差不大。
由于塑性变形前后体积不变,因此可以按坯料面积等于拉深件表面积的雨泽确定坯料的尺寸。
由于金属板料具有板平面方向性和受模具几何形状等因素的影响,成形后的拉深件口部一般不整齐,因此多数情况下还需采取加大工序件高度或凸缘宽度的方法,拉深后再经过切边工序来保证零件质量。
由h=7.7mm,d=11.3mm,h/d=0.68,查圆筒形拉深件的切边余量表得△=1mm,故总拉深高度H=h+Δ=8.7mm,r=0.5mm,零件毛坯直径可以按公式确定,制件按中线尺寸计算,由公式
D=
(1)计算得D=22.6mm,实际毛坯直径取23mm。
5.2拉深工艺计算
5.2.1计算拉深系数
圆筒形件拉深的变形程度用拉深系数来表示,故拉深系数是拉深工艺的基本参数。
拉深系数是指每次拉深后圆筒形零件的直径与毛坯或前道工序件的直径之比。
用m表示,而且m值越小,拉深时变形程度越大,拉深系数是重要的工艺参数,可以用于计算各个工序的尺寸和毛坯尺寸,一种材料在一定拉深条件下允许的拉深变形程度是一定的,把材料既能拉深成形又不被拉断时的最小拉深系数称为极限拉深系数。
由t/D×100=2.60,总拉深系数m=d/D=0.49。
通过查筒形件的极限拉深系数表,得第一次极限拉深系数[
]=0.48~0.50。
虽然m=d/D=0.49稍大于[
]的极限值0.48,为了保证拉深质量,还是分2次拉深比较合适。
5.2.2各次拉深直径和高度
确定了圆筒形件的拉深次数后,各工序直径可由各工序的拉深系数和前道工序的直径求得,d1=23*0.61=14.4mm,d2=14.4*0.78=11.3mm,由公式
=0.25(D*k
-d)+0.43r
/d
(d
+0.32r
)
(2)
计算得
=6.7mm,取7mm。
D毛坯直径;
d
第一次拉深的工序件直径;
r
第一次拉深的工序件底部圆角半径;
h
第一次拉深的工序件高度;
同理h
=8.7mm。
各工序为:
一次拉深尺寸为Ф15mm×7mm,D=23mm,第一次拉深的中间直径15mm—0.6mm=14.4mm(0.6mm为材料厚度),
=0.61;一次拉深尺寸为Ф11.3mm×8.7mm,d=11.3mm,
=O.78。
5.2.3确定是否采用工艺切口
冲压材料采用厚度o.6mm的马口铁带卷料,采用自动送料装置。
由于该工件是在带料上多次连续拉深,为防止带料在拉深过程中产生变形,避免拉深时相邻工序件之间因材料相互牵连的影响,需在首次拉深前冲出工艺切口,为保证带料导向的可靠性,采用对称的人字形工艺切口。
5.2.4各次拉深凸凹模圆角半径
凹模圆角半径越大,材料越容易进入凹模,但过大材料易起皱。
因此,在材料不起皱的前提下,凹模圆角半径宜取大一些。
计算所得的凹模圆角半径均应符合r大于等于2t,对于带凸缘的筒形件,最后一次拉深的凹模圆角半径还应与零件的凸缘圆角半径相等。
凸模圆角半径过小,会使材料在此受到过大的玩去变形,导致危险断面材料严重变薄甚至拉裂,但过大会使悬空部分增大,容易产生内起皱现象。
最后一次拉深时,凸模圆角半径应与拉深件底部圆角半径相等,但当拉深件底部圆角半径小于拉深工艺性要求时,则凸模圆角半径应按工艺性要求确定,然后通过增加整形工序得到拉深件所要求的圆角半径。
第一次拉深凹模圆角半径可以按一下经验公式计算:
r
=0.8
=2.12mm(3)
式中r
凹模圆角半径;
D坯料直径;
d凹模内径;
t材料厚度;
第一次拉深凸模圆角半径可取r
=(0.7-1.0)r
=1.908mm;
第二次拉深时,凹模圆角半径应逐渐减小,一般可以按经验公式确定:
r
=(0.6-0.9)r
=1.272mm(4)
第二次拉深时,凸模圆角半径应与拉深件底部圆角半径相等r
=0.2mm
5.2.5拉深凸、凹模间隙
拉深凸凹模间隙对拉深力,拉深质量,模具寿命等都有较大的影响。
间隙小时,拉深力大,模具磨损也大,但拉深件回弹小,精度高。
间隙过小,会使拉深件壁部严重变薄甚至拉裂。
间隙过大,拉深件坯料起皱,而且口部的变厚得不到消除,拉深件出现较大的锥度,精度较差。
因此,拉深件凸、凹模间隙应根据坯料厚度及公差、拉深过程中坯料的增厚情况、拉深次数、拉深件的形状及精度等要求确定。
对于有压料装置的拉深模,凸凹模单边间隙可根据材料厚度和拉深次数表确定,按经验公式
Z/2=(0.9-0.95)t(5)
计算得双面间隙Z=1.08mm。
5.2.6拉深凸、凹模工作尺寸及其公差
拉深件的尺寸和公差是由最后一次拉深模保证的,考虑拉深模的磨损和拉深件的弹性回复,最后一次拉深模的凸、凹模工作尺寸及公差按如下确定:
第二次拉深模的凸、凹模工作尺寸及公差按如下确定:
当拉深件标注为外形尺寸,以凹模为基准,则
D
=(D
-0.75Δ)
=11.875
(6)
D
=(D
-0.75Δ-2Z)
=11.855
(7)
对于首次拉深,因工序件尺寸无需严格要求,所以其凸、凹模工作尺寸取相应工序的工作尺寸即可,同样以凹模为基准,则
D
=D
=15
(8)
D
=(D-2Z)
=14.98
(9)
式中D
凹模工作尺寸;
D
凸模工作尺寸;
D
拉深件的最大外形尺寸;
Z凸、凹模单边间隙;
Δ拉深件的公差,为IT11级;
凸、凹模的制造公差,可按IT6-IT9级确定;
D各次拉深工序件的基本尺寸。
5.3冲裁工艺计算
5.3.1冲孔凸、凹模刃口尺寸及其制造公差的确定原则
凸模和凹模的刃口尺寸和公差,直接影响冲裁件的尺寸精度。
模具的合理间隙值也靠凸模、凹模刃口尺寸及其公差来保证。
因此,正确确定凸、凹模刃口尺寸和公差,是冲裁设计中的一项重要工作。
模具刃口尺寸精度是影响冲裁件尺寸精度的首要因素。
模具的合理间隙值也要考模具刃口部分尺寸及其公差来保证。
因此,在确定凸、凹模刃口部分尺寸及其制造公差时,必须考虑到冲裁变形规律、冲裁公差等级、模具磨损和制造工艺等方面。
实践证明,由于存在模具间隙,冲裁件的断面都带有锥度,落料件的大端尺寸接近于凹模刃口尺寸,冲孔件的小端尺寸接近于凸模刃口尺寸。
在冲裁过程中,凸、凹模与冲裁件和废料发生摩擦,凸模和凹模会向入体方向磨损。
因此,确定凸模和凹模刃口尺寸,需遵循下述原则:
确定基准件,设计落料模时,以凹模为基准件,间隙取在凸模上;设计冲孔模时,以凸模为基准件,间隙取在凹模上。
考虑冲模的磨损规律,设计落料模时,凹模公称尺寸应按入体方向接近或等于相应的落料件最小极限尺寸,此时的凸模公称尺寸按凹模相应尺寸沿入体方向减(加)一个最小合理间隙值;设计冲孔模时,凸模公称尺寸按入体方向接近或等于相应的冲孔件最大极限尺寸,此时的凹模公称尺寸按凸模相应尺寸沿入体方向加(减)一个最小合理间隙值。
凸、凹模刃口尺寸制造公差应合理。
凸、凹模刃口部分尺寸的制造公差要按零件的尺寸要求决定,一般模具的制造精度比冲裁件的精度高2—3级。
若零件未注公差,对于非圆形件,冲模按IT9精度制造;对于圆形件,一般按IT6-7级精度制造。
本设计中冲孔以凸模为基准件,间隙取在凹模上,凸模取IT8级,凹模取IT9级。
尺寸偏差应按入体原则标注。
5.3.2凸、凹模刃口尺寸的计算方法
凸模与凹模刃口尺寸的计算方法按分开加工计算,对于冲孔计算公式如下:
d
=(d+x*Δ)
=8.075
(10)
d
=(d
+Z
)
=8.171
(11)
d
凸模尺寸;
d
凹模尺寸;
Δ制件公差;
X考虑磨损的系数,按零件公差选取,零件精度为IT11级时,取0.75;
分别为凸模和凹模的制造公差;
Z
凸、凹模最小初始双面间隙;
5.3.4冲孔凸、凹模间隙的确定原则
冲裁间隙影响冲裁件质量、冲裁力、模具寿命、断面质量、尺寸精度,是冲裁模设计最重要的工艺参数之一。
考虑到模具制造中的偏差及使用中的磨损,生产中通常选择一个适当的范围作为合理间隙。
在此范围内选用的间隙值可以获得合格的零件。
这个范围的最小值称为最小合理间隙,最大值称为最大合理间隙值。
由于模具在使用过程中的磨损使间隙增大,设计与制造新模具时采用最小合理间隙值。
选择合理间隙值的总的原则是:
在满足冲裁件质量的前提下,间隙值一般取偏大值,这可以降低冲裁理和提高模具寿命。
5.3.5冲孔凸、凹模间隙值的确定方法
确定凸、凹模间隙的方法有理论法和经验法两种。
经验方法也是根据材料的性质和厚度,来确定最小合理间隙值,根据经验法按下列数据确定凸、凹模间隙C=(8%-10%)t=0.08*0.6=0.048mm,双面间隙Z=0.096mm。
实验研究结果与实践经验表明对于尺寸精度、断面垂直度要求高的工件应选用较小间隙值,对于断面垂直度要求不高的工件,以提高模具寿命为主,可采用较大的间隙。
5.4切边凸、凹模刃口尺寸及公差的确定
为保证切边工位的冲制质量,冲裁双边间隙为0.02mm,凸、凹模刃口部分表面粗糙度为Ra0.2~0.4μm,以确保冲裁面粗糙度值符合Ra1.6μm的要求,刃口尺寸公差按IT6级制造。
切边凸模的刃口尺寸为11.9
,切边凹模的刃口尺寸为11.9
。
5.5排样设计
冲裁件在条料或板料上的布置方法叫排样,排样是冲裁模设计中的一项极其重要的工作。
排样方法对材料的利用率、冲裁件的质量、生产率、乬结构和寿命都有重要的影响,合理的排样可以提高材料的利用率。
5.5.1排样原则
对于冲裁来说,由于产量大,冲裁件的生产率高,材料费用占冲压总成本的60%以上。
材料利用率是一项及其重要的经济指标。
要提高材料的材料利用率,就要减少废料。
冲裁过程中产生的废料可分为结构废料和工艺废料两种。
结构废料是由工件形状决定的,而工艺废料是由冲压方式和排样方式决定的。
使人工操作方便、安全、减轻工人的劳动强度,使模具结构简单、模具寿命较高,排样应保证冲裁件的质量。
第一工位安排局部外形冲切和冲导正孔,第二工位设置导正销对条料导正,在以后的工位中,对易发生窜动的工位设置导正销,也可以在以后的工位中没隔2-3个工位设置导正销,本设计中在模具的主要工位分别设置有6对导正销,冲