水性双组份聚氨酯清漆.docx
《水性双组份聚氨酯清漆.docx》由会员分享,可在线阅读,更多相关《水性双组份聚氨酯清漆.docx(14页珍藏版)》请在冰豆网上搜索。
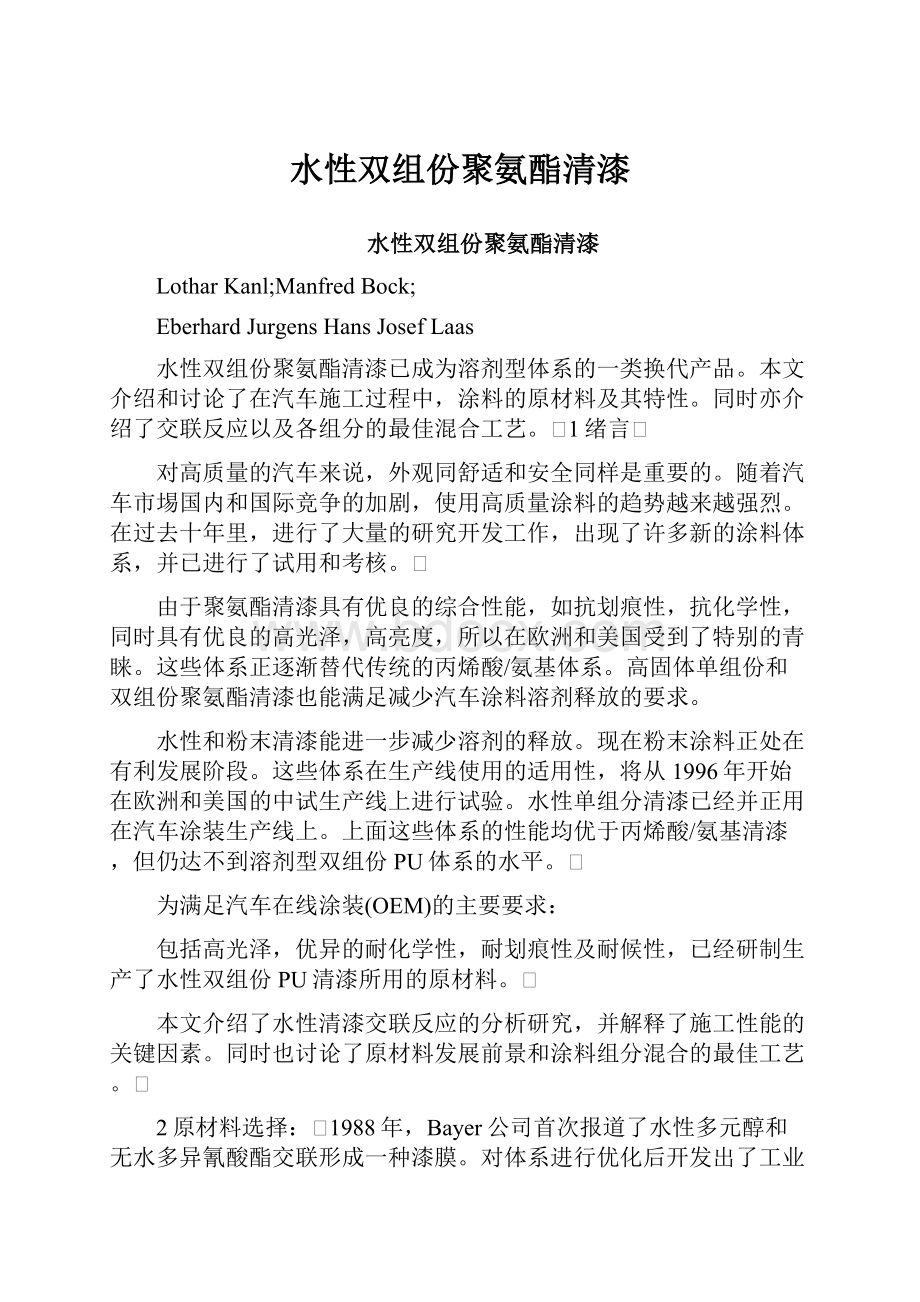
水性双组份聚氨酯清漆
水性双组份聚氨酯清漆
LotharKanl;ManfredBock;
EberhardJurgensHansJosefLaas
水性双组份聚氨酯清漆已成为溶剂型体系的一类换代产品。
本文介绍和讨论了在汽车施工过程中,涂料的原材料及其特性。
同时亦介绍了交联反应以及各组分的最佳混合工艺。
1绪言
对高质量的汽车来说,外观同舒适和安全同样是重要的。
随着汽车市埸国内和国际竞争的加剧,使用高质量涂料的趋势越来越强烈。
在过去十年里,进行了大量的研究开发工作,出现了许多新的涂料体系,并已进行了试用和考核。
由于聚氨酯清漆具有优良的综合性能,如抗划痕性,抗化学性,同时具有优良的高光泽,高亮度,所以在欧洲和美国受到了特别的青睐。
这些体系正逐渐替代传统的丙烯酸/氨基体系。
高固体单组份和双组份聚氨酯清漆也能满足减少汽车涂料溶剂释放的要求。
水性和粉末清漆能进一步减少溶剂的释放。
现在粉末涂料正处在有利发展阶段。
这些体系在生产线使用的适用性,将从1996年开始在欧洲和美国的中试生产线上进行试验。
水性单组分清漆已经并正用在汽车涂装生产线上。
上面这些体系的性能均优于丙烯酸/氨基清漆,但仍达不到溶剂型双组份PU体系的水平。
为满足汽车在线涂装(OEM)的主要要求:
包括高光泽,优异的耐化学性,耐划痕性及耐候性,已经研制生产了水性双组份PU清漆所用的原材料。
本文介绍了水性清漆交联反应的分析研究,并解释了施工性能的关键因素。
同时也讨论了原材料发展前景和涂料组分混合的最佳工艺。
2原材料选择:
1988年,Bayer公司首次报道了水性多元醇和无水多异氰酸酯交联形成一种漆膜。
对体系进行优化后开发出了工业化产品,可用于工业涂装、木材涂装、塑料涂装、和汽车维修。
在汽车OEM使用中同样也存在原材料匹配问题,这将通过进一步与涂料工业加强合作而进行开发。
用于汽车OEM涂装的水性双组分PU清漆是用脂肪族和脂环族多异氰酸酯与水性聚丙烯酸酯及聚氨酯多元醇配制而制得。
疏水多异氰酸酯与溶剂型双组分PU清漆中的固化剂是完全一样的。
水性双组分PU清漆的固化剂可用少量有机助溶剂稀释,达到合适的施工粘度。
水性多元醇是用有机酸来进行亲水性改性,再用胺中和。
多元醇组分中,除水之外还含有特殊的添加剂和少量的有机助溶剂,以提高流平性和施工性能。
不同原材料影响漆膜性能如下:
*HDI多异氰酸酯-耐划痕性
*IPDI多异氰酸酯-耐化学性
*聚氨酯xx-流平性(湿润性)
-耐划痕性
*聚丙烯酸酯多元醇-耐化学品性,耐候性
聚氨基甲酸酯/聚丙烯酸酯混合物是这些水性体系最适用的组份。
根据耐划痕性和耐化学品性的需要,也可使用纯HDI/IPDI混合多异氰酸酯。
3.水性双组分PU清漆的化学反应:
多异氰酸酯的-NCO基和多元醇的-OH加成形成氨基甲酸酯结构,这是形成网状聚合物的主要反应。
从整个体系看,多异氰酸酯和官能基团之间的副反应可形成如下结构:
与水反应→脲
与中和剂反应→氨基甲酸酯
与羧基反应→酰胺
所有这些反应均能形成交链结构,具有高耐化学性。
与有机酸反应形成酰胺基会极大地破坏体系的亲水性。
其结果是得到具有优良耐水性的涂料。
当多异氰酸酯/多元醇比率超过
1.0时,能形成致密的氨基甲酸酯网络补偿多异氰酸酯网络。
当多异氰酸酯/多元醇的当量比为
1.5时,能满足汽车OEM涂装的要求。
4.烘烤型涂料的反应特性:
主反应和副反应的反应程度主要受固化温度的影响。
汽车修补采用常温干燥的反应过程已被很多人研究,并有不少文献报道。
与汽车修补相反,汽车在线涂装一般采用强制干燥型涂料。
对溶剂型体系,干燥温度在120-140℃范围之内。
由于水与溶剂具有不同的蒸发动力学,水性体系需要较长的闪蒸时间和在70-90℃进行预干燥。
最后在与溶剂型体系一样的条件下进行固化。
下面的水性双组分清漆使用与生产线上相似的干燥条件。
闪蒸:
23℃,8分钟
预干燥:
80℃,5分钟
固化:
130℃,30分钟
4.1NCO基团反应历程
干燥过程中,在给定时间内NCO基的含量由IR光谱(见图1)进行分析。
图1:
OEM条件下,干燥过程中NCO含量的变化
在室温闪蒸期间,NCO含量基本保持不变。
在80℃预干燥时间内,-NCO基团的含量在5分钟内由98%降低到83%。
大部分交联反应是在130℃时发生,经过30分钟后,多异氰酸酯被接到聚氨酯网络上。
大约只有7%的残留-NCO基团能被测出。
在室温下放置三天,-NCO基继续与多元醇及空气中水分反应,残留-NCO降至
0.2%以下。
此时聚氨酯网络完全形成。
4.2水分的挥发
在干燥期间的任一时刻,异氰酸基团的反应能力受该时所有反应组分浓度的控制。
整个挥发过程可由气相色谱分析给出详细的数据(见图2)。
图2:
水性双组份PU清漆的蒸发过程
尽管水的挥发速率较低,但水作为挥发组分的主要组成部分离开漆膜仍相对较快。
在室温闪蒸8分钟和80℃预干燥5分钟后,水的含量已降至
0.5%以下。
130℃固化5分钟后,水的含量已减少到
0.2%左右。
这意味着已没有水可在主交联反应过程中产生副反应了。
二甲基乙醇胺(DMEA)作为中和剂时,起初浓度为
1.7%,经80℃预干燥后检测,以液体清漆计,发现最多只有
0.5%的中和剂。
130℃固化5分钟后已降至
0.1%以下。
由于DMEA有可能与异氰酸酯反应,DMEA含量减少可能由于挥发或由于反应生成氨基甲酸酯所致。
采用不含异氰酸酯固化剂的漆膜对此研究表明,在同样干燥条件下,约有30%的DMEA(绝对含量约
0.4%)挥发掉了。
这就表明在初始的双组份体系中,约有
1.2%的DMEA和异氰酸酯基团反应,生成聚氨酯漆膜了。
事实上,到干燥过程结束时,所有非反应性的有机助溶剂均已从漆膜中挥发出了。
残余的一些助溶剂在以后的几天中也会全部挥发掉。
4.3交联反应产物:
水性双组份OEM体系在室温干燥期间所得产物与水性双组分修补漆干燥后所得产物非常类似。
因为水过量,因此约有三分之二的异氰酸基团反应生成脲。
虽不能定量分析出羧酸与异氰酸酯形成酰胺的准确含量,但可借助光谱分析测定酰胺含量大致在3mol%以下。
大多数羧酸基团已反应掉,从而提高了体系的耐水性。
如果固化温度升至130℃,脲的含量将降至约6mol%。
这是由于水分的迅速挥发,130℃烘5分钟后残留的水含量只有
0.2%左右(见表1)。
一旦烘烤结束后,脲是由残余的-NCO基团与大气中水分反应而成。
这一事实在较高温度,较长时间干燥试验中得以证实。
事实上,所有异氰酸酯基团都与多元醇(OH或COOH基团)或中和剂(-OH基团)反应,脲含量降至1mol%以下。
表1:
在水性双组份PU清漆中异氰酸酯的反应产物
干燥条件异
氰酸酯反应产物[mol%]
氨基甲酸酯脲酰胺
1.室温约51约46〈3
2.室温,8分钟
+80℃5分钟
+130℃30分钟
+室温7xx91约6〈3
3.室温,8分钟
+80℃5分钟
+130℃30分钟
+60℃16小时约96〈1〈3
4.4清漆固化过程:
综合上述这些试验结果,可得出水性双组份聚氨酯体系在汽车OEM涂装条件下的固化过程。
在闪蒸期间,多异氰酸酯,多元醇与中和剂之间并没有明显的反应。
在80℃烘5分钟,所有的水全部挥发,多异氰酸酯与多元醇及中和剂首先发生反应。
在130℃,大部分交联反应完成,30分钟后,-NCO含量降至初始量的10%以下。
固化之后,残留的NCO基团与大气中水分反应生成脲。
结果是得到含有氨基甲酸酯、脲及少量酰胺的完全固化涂膜。
5.双组份涂料混合后的稳定性:
既然双组份体系正常施工条件下是经济的,并有利于环境保护,那末两组份在混合后必须具有足够的稳定性。
以使在出现生产线停止或停顿故障时,无需冲洗管道,便能立即恢复涂装。
而对于烘烤型涂料,在生产线中断之前和较长的闪蒸时间之后仍能得到好的结果这是可能的。
下述章节介绍水性双组份PU清漆在开始混合到施工(适用期)及从施工之后到烘烤(延长闪蒸时间)之前,其性能与时间的关系。
5.1适用期
表征适用期特性的主要指标有下述几点:
*湿涂料中的NCO含量
*湿涂料的粘度变化
*流挂极限和针孔形成
*漆膜性能
5.1.1湿涂料中的NCO含量
多异氰酸酯与多元醇混合后,起初三小时内以每小时
0.15%的恒定速率下降(见图3)。
在所研究的体系内,这意味着-NCO含量从
3.8%降至
3.4%。
最近正在研究如何测定NCO基团与多元醇,中和剂,水之间反应引起NCO含量减少到什么程度。
图3:
湿涂料xxNCO含量的减少
5.1.2湿涂料的粘度变化
为确保稳定的施工性能,关键在于涂料在适用期内有一个稳定的粘度。
至今所进行的研究表明,绝对粘度和粘度变化受增稠剂和选用的有机助溶剂的影响。
图4表示,双组份涂料在使用聚氨酯增稠剂和不同助溶剂时所得到的结果。
图4:
使用不同混合助溶剂时粘度变化
混合助溶剂A和C不适合用在适用期长的产品中,要不粘度增长太快,要不在短时间后明显下降。
这两种情况,混合后施工性能均会随时间而有所变化。
相反,含混合助溶剂B的涂料粘度在90分钟内保持稳定,随后明显升高。
为确保最长的适用期,按不同体系选择混合助溶剂。
若使用不同基料,必须重新选择。
5.1.3流挂趋势和针孔形成
涂料的粘度和流挂性有密切的关系。
体系的粘度越低,在垂直表面上就越易流挂。
绝对粘度和粘度随时间的稳定性是确保流挂性的关键因素。
另外,在室温和升温干燥时底材上的涂料的粘度也不能有明显下降。
对含混合助溶剂B的双组份体系(具有优良的粘度稳定性)的施工性进行了详尽的研究。
(见图5)
图5:
混合涂料的贮存时间和施工性能的关系
漆膜在75-90分钟内,流挂性无多大变化,涂膜的流挂极限厚度为40-45μm。
随涂料粘度升高,在垂直面上的耐流挂性也增强。
形成针孔的界限变化却相反。
在开始的75-90min内,约55μm厚时仍保持稳定。
然后,渐渐地降低。
较低的极限可用以下原因解释:
一是-NCO/水反应随时间而增多,二是水和二氧化碳从较高粘度的漆膜中挥发更加困难。
5.1.4漆膜性能
双组份PU清漆的流平性和清晰度主要受液体涂料的流平性和展布性控制。
这种结构状态经干燥后就被固定下。
在混合和施工后,这种水性双组分体系的流动非常类似于溶剂型双组份体系。
当涂料的粘度增加时,由于喷涂施工和溶剂挥发出现的桔皮现象也会加重。
对含混合助溶剂B的水性漆。
经2小时后可看到这种现象。
在这期间,机械性(摆杆硬度和耐划痕性)和抗性没有变化。
涂料混合后不立即离工,耐候性将受到不良影响的说法是不太可能的。
目前正在进行研究以证实这一结论。
5.1.5适用期的设定
如上所述,混合和施工后,湿涂料和漆膜性能对时间的依赖性表明:
适用期主要受施工性能影响。
粘度升高与低限针孔形成和明显桔皮形成使适用期限制在90分钟以内。
这对使用双组份喷涂设备的在线涂装是足够了。
如果涂装线停止超过90分钟,含混合涂料的涂装线的所有部件必须全部清洗。
5.2较长时间闪蒸后涂料的性能
为了模拟在涂装线发生中断时的情况时,已涂装好的汽车经较长时间闪蒸后才烘烤的状况,将试验样板经过24小时闪蒸后,按常规烘干,检测其结果。
施工后,半小时内涂膜中几乎所有的水都蒸发掉,同时吸收周围的湿气,达到约1%的平衡值(以漆膜量计算)。
室温24小时后,异氰酸酯通过与多元醇,中和剂和水反应,其含量降至起始量的30%(见图6)。
经烘烤进一步交联,-NCO含量降至5%左右。
如果涂料经较短闪蒸时间后就烘烤,对NCO含量迅速下降的曲线应从较高值开始。
否则会出现相似的过程。
较长的闪蒸时间对涂料的施工性能有明显的改善。
(见表2)
。
在24小时内均具有较良好的流平性。
异氰酸酯/水反应生成二氧化碳逸出不会产生起泡,膜厚在40~50μm时,仍有很好的抗流挂性。
闪蒸时间若24小时时,形成针孔的膜厚极限从55μm增加到120μm以上。
若闪蒸时间延长到2小时,漆膜性能无多大变化。
不过闪蒸24小时后,漆膜硬度和抗溶剂和耐化学试剂性稍有降低。
总之,试验结果表明生产线中断24小时之后,烘干的涂膜质量仍是好的。
图6较长闪蒸时间漆膜NCO含量变化
表2:
不同闪蒸时间和施工性能(模拟生产线中断条件)
干燥条件:
室温,X分钟
+80℃,5分钟
+130℃,30分钟
闪蒸时间X抗流挂性
形成针孔极限流平性
8分钟约45μm〉55μm好
30分钟约50μm〉70μm好
1小时约50μm〉110μm好
2小时约50μm>120μm好
24小时约50μm〉120μm好
6.对施工温湿条件的要求
水性中涂,底色漆和单组份清漆在生产线应用结果表明,这些体系对大气温度和湿度的施工要求比溶剂型体系要严得多。
这意味着漆膜性能,如:
流平性、光泽、流挂性和针孔形成总是和施工期间的气候条件有关。
从原理上讲,水性双组份PU清漆也同样如此。
然而,研究表明:
这些体系施工对温度湿度要求比水性单组份清漆要松得多(见图7)。
漆膜表面状态的光学性能对气候条件的依赖性比同样的水性单组份清漆要小(见图7)。
这可能是液体多异氰酸酯对流平的促进作用。
针孔形成的界限随大气湿度增加而降低。
相对湿度约80%时,它的值达到45~50μm。
同时,由于水分从漆膜中蒸发减慢,使漆的粘度增长缓慢,故流挂极阴从45~50μm降至35~40μm。
7.漆膜特性比较
如果混合的水性双组份体系在适用期内施工,并在OEM条件下固化,可以得到充分交链,并具有高质量的聚氨酯清漆膜。
使用水性双组份PU清漆,挥发物(VOC)的释放要比溶剂型体系低的多。
释放值也比单组份水性漆要低。
根据VOC含量可以直接进行比较。
水性涂料的VOC值定义如下:
VOC[g/L]=挥发物质量[g]-水的质量[g]/
涂料体积[L]-水的体积[L]
各种体系的VOC值比较如下:
双组份水性PU涂料:
约230g/L
单组份PU/氨基水性涂料:
约270g/L
双组份溶剂型PU涂料:
约405g/L
图7:
水性双组份PU清漆对施工温度湿度的要求水性双组份PU体系与单组份相比,它具有较好的流平性,较宽的施工温湿度适应范围和较好的耐性。
表3对下述清漆体系进行比较:
水性单组份PU体系与封闭多异氰酸酯(BL-PIC)和氨基树脂交链。
水性和溶剂型双组份PU体系:
a)与HDI多异氰酸酯交链,具有中等耐化学性能。
b)与HDI/IPDI多异氰酸酯交链,具有优异的耐化学性能。
表3:
水性和溶剂型PU清漆性能比较
单组份PU封闭型聚氨酯/氨
基树脂双组份PU多元醇/HDI多异氰酸酯双组份PU多元醇/HDI-IPDI多异氰酸酯水性溶剂型水
NCO/OH
0.3
1.0
1.5
1.0
1.5
耐化学性能1)
H2SO4(1%)[℃]NaOH(1%)[℃]木松香[℃]水[℃
]3945455651425050525036363665484050508065
耐划伤性能2)相对保光性%7380
847676耐候性3)-++++
1)梯度烘箱法:
数值越大表示耐性越好
2)在实验室的洗刷体系来回擦洗10次
3)加速老化和户外耐候
水性双组份PU清漆经固化交链后,其质量明显高于水性单组份体系,和溶剂型双组份体系相差不多。
以HDI为基料的水性双组份体系还具有较高的耐划伤性。
这是因为其中的氨基甲酸酯含量和脲基团的增加,导致了较高的漆膜强度。
在HDI/IPDI体系中,这种效果可用增加硬度和降低柔韧性来补偿。
以高官能度多元醇与HDI/IPDI交链的溶剂型PU清漆具有最好的耐化学性能。
这是由于固化的漆膜具有致密的聚合网络和高玻璃化温度聚合物链的运动性低和较小的自由体积。
水性双组份体系的质量还不能与这些高性能的涂料相比,但确已超过常规的溶剂型涂料。
水性双组份涂料的耐候性试验还没有做完。
但经过一段时间的加速老化和户外耐候试验已显示了它具有很好的耐候性。
在佛罗里达和宾夕法尼亚的工业环境,气候条件下进行的接近使用条件下的试验,证实水性双组份PU涂料具有良好的耐候性。
以HDI/IPDI为基础的聚氨酯涂料具有最好的耐性。
在盛夏,将样板放在大气中曝晒16个星期,然后再检验其化学性。
这种方法同时考虑了气候影响和大气污染两种因素。
1995年得到的最新结果表明,水性双组份PU涂料是耐化学品腐蚀最好的清漆体系之一。
(见图8)
评价标准:
O=无破坏;12=严重破坏
图8:
在佛罗里达和宾夕法尼亚曝晒样板试验结果
德国联邦材料研究检测研究院(BAM)的试验也证实了这个结果。
在实验室采用酸雾(露)试验来检验汽车涂料在UV照射时的耐酸雨性能。
8.水性双组份清漆的混合工艺
以上所介绍的水性双组份清漆是以疏水的多异氰酸酯与亲水的多元醇配合制成的。
其质量非常适合用于在线汽车涂装作业上。
先前的实验工作已建立了漆膜性能,特别是流平性和组分混合质量之间的关系。
分散于水性多元醇中的多异氰酸酯液滴越细小,固化后的漆膜性能和光泽就越高。
由于使用的多异氰酸酯在水中无自乳化性能,因此,固化剂和水性多元醇之间的界面张力较高,需要大量的能量,才能保证各组份充分混合均匀。
使用普通的静态和动态混合器,如凯尼克斯(Kenics)混合器或转子/定子混合器,它们不能提供所须能量。
其结果是一种多异氰酸酯的粗液滴分散在高度分散的多元醇中的乳液。
喷射分散技术有可能获得所需的混合数量。
其原理是从喷咀喷出时压力降低,多异氰酸酯液滴便自然高度分散(见图9)。
操作过程简介:
多异氰酸酯和水性多元醇在一定压力下分别进入预混合器。
多异氰酸酯在约2巴(bar)的压力下通过一个扁平的喷咀喷入多元醇内。
这就得到了直径约5~25μm的多异氰酸酯液滴的预乳化液。
图9:
喷射分散过程
细分散体可在流程下端连接的喷射分散器中收集到。
在通过直径约为
0.2~
0.5mm喷咀时,该分散体压力降为常压,压力转化成分散能。
至少有两个孔排列在相对称的位置,以使乳化喷出液垂直碰撞,产生附加的剪切力。
松驰压力约△p=20bar(巴),可产生最大粒径为1μm的颗粒。
用这种方法分散的水性双组分清漆涂装的车身,其外观镜面效果和用双组份PU清漆涂装的一样。
如果进一步增大压力,会获得更细小的分散颗粒,但对流动性无明显作用。
表4表示采用混合工艺对水性双组份PU体系的分散程度及对涂膜流平性能的影响波纹扫描测量。
表-4混合工艺对多异氰酸酯的分散性和漆膜流平性的影响
混合工艺粒径大小*波纹扫描**(细波纹)
凯尼克斯混合器15μm6
Dynamic混合器9μm
4.5
喷射分散
5bar6μm
2.3
20bar1μm
0.6
50bar
0.5μm
0.5
*最大粒径
**在玻璃板上水平观察
将新形成的乳液进行冷冻断面电镜分析,可以清晰地看出喷射分散的效果。
在研究开发期间的实验室和中试生产中,喷射分散操作是安全和容易实现的。
操作时,金属或陶瓷喷咀没有磨损。
产生压力所用的喷头,泵及体系的管道能用水,乙二醇丁醚和胺的混合物(比例为90:
9.9:
0.1)清洗干净。
我们与德国设备制造商DurrBehrofBietigheimBissingen一起,打算把水性体系引入到在线涂装应用中。
已讨论了各种替代产品,目前的工作是集中建立一个独立于喷漆柜的中央压力站和分散体站体系。
混合后的涂料通过低压输送软管从混合站被传送到ESTA喷枪上。
另一种方法是涂料进入ESTA喷枪之前进行分散(见图10)。
然而,这需要更复杂的控制系统,并对现有的喷咀工艺进一步改进。
目前正在做这方面的开发工作。
图10:
在喷枪前直接混合的示意图
目前,发展了一种活动的试验性分散设备,其核心部分是一个混合喷头,将组分混合在一起,并通过直径很细的喷咀进行细分散。
这种设备试用后,将对在线汽车涂装用的混合水性双组份PU涂料的喷射分散施工奠定基础。
9.结论
水性双组份PU涂料目前正在成为溶剂型双组份PU体系的一种替代产品。
使用喷射分散可得到组分的最佳混合。
组分混合后适用期可达90分钟。
与水性单组份体系相比,它具有更大的施工温湿度变化适应性,在施工时,对环境要求不那么苛刻。
在汽车(OEM)涂装的烘烤条件下,异氰酸酯与水的反应不是主要的。
多异氰酸酯与水溶性多元醇反应形成致密的氨基甲酸酯和脲的网状结构,其中,氨基甲酸酯含量超过90mol%。
合理选择原料对耐化学性和抗划痕性可以有较宽的适应性。
到目前为止,水性体系和溶剂型体系一样,不太可能同时具有高的耐化学性和抗划痕性。
但在两者之间建立一个可接受的平衡是可能的。
因此,现在汽车工业已拥有了第一代可在线涂装中使用的水性清漆体系,其性能与溶剂型双组份聚氨酯清漆相当。
与粉末清漆相比,水性双组份体系有其优越性,能在现有的湿涂装线上施工。
如果没有建立新涂装线,水性双组份PU清漆在线施工的条件亦已具备。
同时,在保证质量的前提下,可以大量减少溶剂的释放。