完整word版盘式制动器设计说明书docx.docx
《完整word版盘式制动器设计说明书docx.docx》由会员分享,可在线阅读,更多相关《完整word版盘式制动器设计说明书docx.docx(31页珍藏版)》请在冰豆网上搜索。
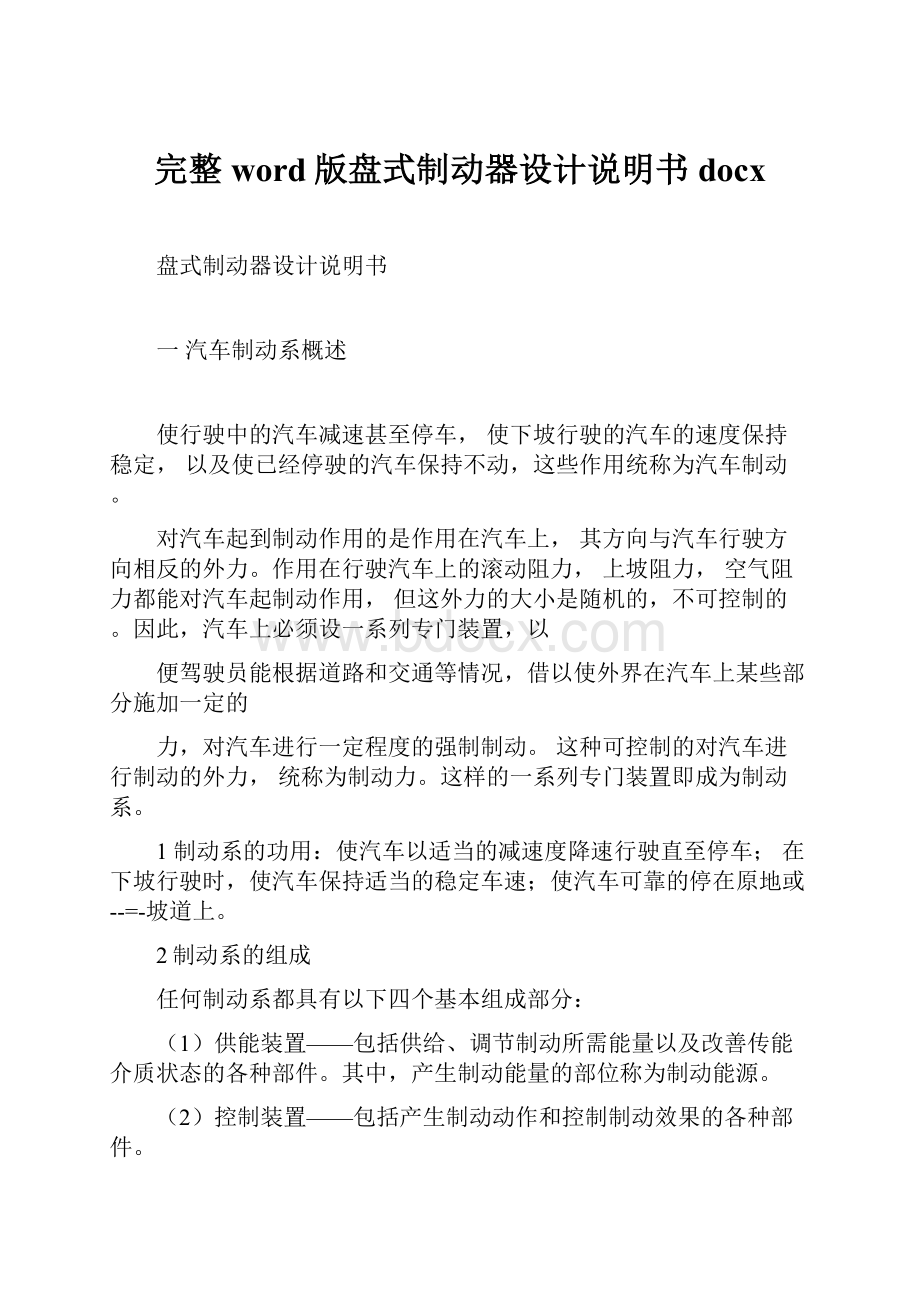
完整word版盘式制动器设计说明书docx
盘式制动器设计说明书
一汽车制动系概述
使行驶中的汽车减速甚至停车,使下坡行驶的汽车的速度保持稳定,以及使已经停驶的汽车保持不动,这些作用统称为汽车制动。
对汽车起到制动作用的是作用在汽车上,其方向与汽车行驶方向相反的外力。
作用在行驶汽车上的滚动阻力,上坡阻力,空气阻力都能对汽车起制动作用,但这外力的大小是随机的,不可控制的。
因此,汽车上必须设一系列专门装置,以
便驾驶员能根据道路和交通等情况,借以使外界在汽车上某些部分施加一定的
力,对汽车进行一定程度的强制制动。
这种可控制的对汽车进行制动的外力,统称为制动力。
这样的一系列专门装置即成为制动系。
1制动系的功用:
使汽车以适当的减速度降速行驶直至停车;在下坡行驶时,使汽车保持适当的稳定车速;使汽车可靠的停在原地或--=-坡道上。
2制动系的组成
任何制动系都具有以下四个基本组成部分:
(1)供能装置——包括供给、调节制动所需能量以及改善传能介质状态的各种部件。
其中,产生制动能量的部位称为制动能源。
(2)控制装置——包括产生制动动作和控制制动效果的各种部件。
(3)传动装置——包括将制动能量传输到制动器的各个部件。
(4)制动器——产生阻碍车辆的运动或运动趋势的力的部件,其中也包括辅助制动系中的缓速装置。
较为完善的制动系还具有制动力调节装置以及报警装置、压力保护装置等附加装置。
3制动系的类型
(1)按制动系的功用分类
1)行车制动系——使行使中的汽车减低速度甚至停车的一套专门装置。
2)驻车制动系——是以停止的汽车驻留在原地不动的一套装置。
3)第二制动系——在行车制动系失效的情况下,保证汽车仍能实现减速或停车的一套装置。
在许多国家的制动法规中规定,第二制动系是汽车必须具备的。
4)辅助制动系——在汽车长下坡时用以稳定车速的一套装置。
(2)按制动系的制动能源分类
1)人力制动系——以驾驶员的肢体作为唯一的制动能源的制动系。
2)动力制动系——完全靠由发动机的动力转化而成的气压或液压形式的势能进行制动的制动系。
3)伺服制动系——兼用人力和发动机动力进行制动的制动系。
按照制动能量的传输方式,制动系又可分为机械式、液压式、气压式和电磁等。
同时采用两种以上传能方式的制动系,可称为组合式制动系。
4设计制动系时应满足如下主要要求:
1)具有足够的制动效能。
行车制动能力是用一定制动初速度下的制动减速度和制动距离两相指标来评定的;驻坡能力是以汽车在良好路面上能可靠的停驻
的最大坡度来评定的。
详见GB/T7258-2004
制动距离:
是指机动车在规定的初速度下急踩制动时,从脚接触制动踏板(或手触动制动手柄)时起至机动车停住时止机动车驶过的距离。
制动减速度:
是指机动车制动时车速对时间的导数。
制动稳定性要求:
是指制动过程中机动车的任何部位(不计入车宽的部位除外)
不允许超出规定宽度的试验通道的边缘线。
制动距离和制动稳定性要求
制动初速
满载检验制
空载检验制动
试验通道
机动车类型
度
动距离要求
距离要求m
宽度m
km/h
m
三轮汽车
20
≤5.0
2.5
乘用车
50
≤20.0
≤19.0
2.5
总质量不大于3500kg
的低速货
≤9.0
≤8.0
2.5
车
30
其它总质量不大于
3500kg的汽
≤22.0
≤21.0
2.5
车
50
其它汽车、汽车列车
30
≤10.0
≤9.0
3.0
两轮摩托车
30
≤7.0
——
边三轮摩托车
30
≤8.0
2.5
正三轮摩托车
30
≤7.5
2.3
轻便摩托车
20
≤4.0
——
轮式拖拉机运输机组
20
≤6.5
≤6.0
3.0
手扶变型运输机
20
≤6.5
2.3
制动减速度和制动稳定性要求
制动初速
满载检验充分
空载检验充分发
试验通道宽度
机动车类型
发出的平均减
出的平均减速度
度km/h
m
速度m/s2
m/s2
三轮汽车
20
≥3.8
2.5
乘用车
50
≥5.9
≥6.2
2.5
总质量不大于
3500kg的低速货车
≥5.2
≥5.6
2.5
30
其它总质量不大于3500kg
的汽车
≥5.4
≥5.8
2.5
50
其它汽车、汽车列车30≥5.0≥5.43.0
2)工作可靠。
行车制动装置至少有两套独立的驱动制动器的管路,当其中一套管路失效时,另一套完好的管路应保证汽车制动能力不低于没有失效时规定值的30%。
行车和驻车制动装置可以有共同的制动器,而驱动机构则各自独立。
3)在任何速度下制动时,汽车都不应丧失操纵性和方向稳定性。
4)防止水和泥进入制动器工作表面。
5)制动能力的热稳定性良好。
6)操作轻便,并具有良好的随动性。
7)制动时,制动系产生的噪声应尽可能小,同时力求减少散发出对人体有害的石棉纤维等物质,以减少公害。
8)作用滞后性应尽可能好。
作用滞后性是指制动反应时间,以制动踏板开始动作至达到给定的制动效能所需的时间来评价。
9)摩擦片应有足够的使用寿命。
10)摩擦副磨损后,应有能消除因磨损而产生间隙的机构,且调整间隙工作容易,最好设置自动调整间隙机构。
11)当制动驱动装置的任何元件发生故障并使其基本供能遭到破坏时,汽车制动系应有音响或光信号等报警装置。
防止制动时车轮被抱死有利于提高汽车在制动过程中的转向操纵性和方向稳
定性,缩短制动距离,所以近年来防抱死制动系统(ABS)在汽车上得到了很快
的发展和应用。
此外,由于含有石棉的摩擦材料在石棉有致癌公害问题已被淘汰,
取而代之的各种无石棉型材料相继研制成功。
二汽车主要参数
名称
单位
数值
轴距
Mm
2947
空载质量
Kg
2050
空载质心高度
Mm
1000
空载前轴载荷
Kg
1025
满载质量
Kg
2800
满载质心高度
Mm
1050
满载前轴载荷
Kg
1400
三制动器形式的选择
制动器主要有摩擦式、液力式和电磁式等几种形式。
电磁式制动器虽有作
用滞后性好、易于连接而且接头可靠等优点,但因成本高,只在一部分总质量较大的商用车上用作车轮制动器或缓速器;液力式制动器一般只作缓速器。
目前广泛使用的仍为摩擦式制动器。
摩擦式制动器按摩擦副结构形式不同,可分为鼓式,盘式和带式三种。
带
式制动器只用作中央制动器;鼓式和盘式制动器的结构形式有多种,如下所示:
盘式制动器的制动盘有两个主要部分:
轮毂和制动表面。
轮毂是安装车轮的部位,内装有轴承。
制动表面是制动盘两侧的加工表面。
它被加工得很仔细,为制动摩擦块提供摩擦接触面。
整个制动盘一般由铸铁铸成。
铸铁能提供优良的摩擦面。
制动盘装车轮的一侧称为外侧,另一侧朝向车轮中心,称为内侧。
制动盘制动表面的大小由盘的直径决定。
大型车需要较多制动功能,它的制动直径达12in或者更大些。
较小较轻的车车用较小的制动盘。
通常,制造商在保持有效的制动性能的情况下,尽可能将零件做的小些,轻些。
按轮毂结构分类,制动盘有两种常用型式。
带毂的制动盘有个整体式毂。
在这种结构中,轮毂与制动盘的其余部分铸成单体件。
另一种型式轮毂与盘侧制成两个独立件。
轮毂用轴承装到车轴上。
车论凸耳
螺栓通过轮毂,再通过制动盘毂法兰配装。
这种型式制动盘称为无毂制动盘。
这种型式的优点是制动盘便宜些。
制动面磨损超过加工极限时能很容易更换。
制动盘可能是整体式的或者通风的。
通风的制动盘在两个制动表面之间铸有
冷却叶片。
这种结构使制动盘铸件显著的增加了冷却面积。
车轮转动时,盘内扇形叶片的旋转增加了空气循环,有效的冷却制动。
盘式制动器具有散热快,重量轻,构造简单,调整方便等优点。
特别是高负
载时耐高温性能好,制动效果稳定,而且不怕泥水侵袭,在冬季和恶劣路况下行
车,盘式制动比鼓式制动更容易在较短的时间内令车停下。
虽然盘式制动器的制
动盘与空气接触的面积很大,但很多时候其散热效果还是不能让人满意,于是有
的制动盘上又被开了许多小孔,加速通风散热以提高制动效率,这就是通风盘式
制动器。
一般来说,尺寸大的制动盘要比尺寸小的制动盘散热效率高,而通风盘
则要比实体盘的散热效率高。
四轮轿车在制动过程中,一般前轮的制动力要比后
轮大,后轮起辅助制动作用。
因此,一般情况下,汽车前轮制动盘的尺寸要比后
轮大,且前轮多采用通风盘,后轮多采用实体盘或通风盘。
根据制动盘固定元件的结构形式,盘式制动器可分为钳盘式制动器和全盘式制动器两类。
钳盘式制动器
钳盘式制动器的固定摩擦元件是制动块,装在与车轴连接且不能绕车轴线旋转的制动钳中。
制动衬块与制动盘接触面积很小,在盘上所占的中心角一般仅
30o~50o,故盘式制动器又被称为点盘式制动器。
全盘式制动器
全盘式制动器摩擦副的固定元件和旋转都是圆盘形的,分别称为固定盘和旋转盘。
其结构原理和摩擦离合器相似。
多片全盘式制动器的各盘都封闭在壳体中,散热条件较差。
因此,有些国家正在研制一种强制液冷多片全盘式制动器。
这种制动器完全封闭,内腔充满冷却油液。
冷却在制动器内受热升温后,被液压泵吸出,而后被压送入发动机水冷系中的热交换器,在此受发动机冷却水的冷却后再流回制动器。
钳盘式制动器按制动钳的结构不同,分为以下几种。
1.固定钳式
制动钳固定安装在车桥上,既不能旋转,也不能沿制动盘轴线方向移动,因而其中必须在制动盘两侧装设制动块促动装置,以便分别将两侧的制动块压向制动盘。
这种形式也成为对置活塞式或浮动活塞式。
固定钳式制动器存在着以下缺点:
1)液压缸较多,使制动钳结构复杂。
2)液压缸分置于制动盘两侧,必须用跨越制动的钳内油道或外部油管来连通。
这必然使得制动钳的尺寸过大,难以安装现代化轿车的轮毂内。
3)热负荷大时,液压缸和跨越制动盘的油管或油道中的制动液容易受热汽化。
4)若要兼用于驻车制动,则必须加装一个机械促动的驻车制动钳。
这些缺点使得固定钳式制动器难以适应现代汽车的使用要求,故70年代以来,逐渐让位于浮钳盘式制动器。
a)固定钳式b)滑动钳式c)摆动钳式
2.浮动钳式
(1)滑动钳式制动钳可以相对于制动盘作轴向滑动,其中只有在制动盘的内
侧置有液压缸,外侧的制动块固定安装在钳体上。
制动时活塞在液压作用下使活动制动压靠到制动盘上,而反作用力则推动制动钳体连同固定制动块压向制动盘的另一侧,直到两制动块受力均等为止。
(2)摆动钳式它也是单侧液压缸结构,制动钳体与固定在车轴上的支座铰接。
为实现制动,钳体不是滑动而是在与制动盘垂直的平面内摆动。
显然,制动块不可能全面而均匀的磨损。
为此,有必要经衬块预先作成楔形。
在使用过程中,衬块逐渐磨损到各处残存厚度均匀后即应更换。
2.浮钳盘式制动器的制动钳一般设计得可以相对制动盘转向滑动。
其中,只在组、制动盘的内侧设置液压缸,而外侧的制动块则附加装在钳体上。
浮动钳式制动器的优点有:
1)仅在盘的内侧有液压缸,故轴向尺寸小,制动器能进一步靠近轮毂;
2)没有跨越制动噢案的油道或油管,加之液压缸冷却条件好,所以制动液汽化的可能性小;
3)成本低
4)浮动钳的制动块可兼用于驻车制动。
与鼓式制动器相比,盘式制动器有如下优点:
1)热稳定性好。
原因是一般无自行增力作用。
衬块摩擦表面压力分布较鼓
式中的衬片更为均匀。
此外,制动鼓在受热膨胀后,工作半径增大,使
其只能与蹄中部接触,从而降低了制动效能,这称为机械衰退。
制动盘
的轴向膨胀极小,径向膨胀根本与性能无关,故无机械衰退问题。
因此,
前轮采用盘式制动器,汽车制动时不易跑偏。
2)水稳定性好。
制动块对盘的单位压力高,易将水挤出,因而浸水后效能降低不多;又由于离心力作用及衬块对盘的擦拭作用,出水后只需经一,二次制动即能恢复正常。
鼓式制动器则需经十余次制动方能恢复。
3)制动力矩与汽车运动方向无关。
4)易于构成双回路制动系,使系统有较高的可靠性和安全性。
5)尺寸小,质量小,散热良好。
6)压力在制动衬块上分布比较均匀,故衬块上磨损也均匀。
7)更换制动块简单容易。
8)衬块与制动盘之间的间隙小(0.05~0.15mm),从而缩短了制动协调
时间。
9)易实现间隙自动调整。
盘式制动器的主要缺点是:
1)难以实现完全防尘和锈蚀(封闭的多片式全盘式制动器除外)。
2)兼作驻车制动器时,所需附加的手驱动机构比较复杂。
3)在制动驱动机构中必须装用助力器。
4)因为衬块工作面积小,所以磨损快,寿命低,需用高材质的衬块。
因此,从结构,散热,技术,成本等多方面考虑,决定采用浮钳盘式制动器(前轮)。
四浮钳盘式制动器主要参数的确定
1.制动盘直径D
制动盘直径D应尽可能取大些。
这时制动盘的有效半径得到增加,可以见效制
动钳的加紧力,降低衬块单位压力和工作温度。
受轮辋直径的限制,制动盘的直径通常选择为轮辋直径的70%-79%。
总质量大于2t的汽车取上限。
轮辋直径为17英寸,又因为M=2050kg,所以D取330mm.
2制动盘的厚度h
制动盘厚度h对制动盘质量和工作时的温升有影响。
为使质量小些,制动盘厚度不宜取的很大;为减小温升,制动盘厚度又不宜取的过小。
制动盘可以做成实心的,或者为了散热通风需要在制动盘中间铸出通风孔道。
这里选用通风式制动盘,h取20mm
3摩擦衬块外半径R2与内半径R1
推荐摩擦衬块外半径R2与内半径R1的比值不大于1.5。
若比值偏大,工作时衬块的外缘与内侧圆周速度相差较多,磨损不均匀,接触面积减少,最终将导致制动力矩变化大。
取外半径R2=135mm,内半径R1=95mm
4制动衬块工作面积A
在确定盘式制动器衬块工作面积A时,根据制动衬块单位面积占有的汽车质量,推荐在1.6-3.5kg/c㎡范围内选用。
汽车满载质量为2800kg,前轮满载时地载荷为1400kg,
1400
c㎡c㎡
3.5
4
1.6
4
所以A取120c㎡
五浮钳盘式制动器的设计计算
1.运用MATLAB的制动系的匹配设计。
2.确定设计目标
2.1车辆类型和整车质量参数
首先要明确设计车辆的类型和相关的整车质量参数,
这些内容由总布置给出。
整车的质量参数如下:
名称
单位
数值
轴距
Mm
2947
空载质量
Kg
2050
空载质心高度
Mm
1000
空载前轴载荷
Kg
1025
满载质量
Kg
2800
满载质心高度
Mm
1050
满载前轴载荷
Kg
1400
明确以上参数之后,计算制动系所用到的质心到前后轴的距离等参数均可推算出来。
输入语句如下:
clc
clear
M1=1;
%属于M1
类车辆填
1,否则填0
N1=0;
%
属于N1
类车辆填
1,否则填0
OTHER=0;
%
属于其它类车辆填
1,否则填0
ma_k=2050;
%
空载质量(kg)
ma_m=2800;
%
满载质量(kg)
g=9.80665;
%
重力加速度(m/s2)
hg_k=1000;
%
空载质心高(mm)
hg_m=1050;
%
满载质心高(mm)
L=2947;
%
轴距(mm)
load_f_k=1025;
%
空载前轴负荷
load_f_m=1400;
%
满载前轴负荷
b_k=load_f_k*L/ma_k;
%
空载质心到后轴的距离(
mm)
b_m=load_f_m*L/ma_m;
%
满载质心到后轴的距离(
mm)
a_k=L-b_k;
%
空载质心到前轴的距离(
mm)
a_m=L-b_m;
%
满载质心到前轴的距离(
mm)
G_k=ma_k*g;
%
空载重力(N)
G_m=ma_m*g;
%
满载重力(N)
2.1.2满足国家法规要求
目前国内关于制动系统方面有两个强制性标准,一个是
GB/T12676-1999《汽车制动系统结构、性能和试验方法》,在汽
车制动系统结构、性能方面的内容在技术上是等效采用ECE
第13号法规。
另一个是GB7258-2004《机动车安全技术条件》
中关于制动系统的部分。
2.1.3制动系统的结构配置
根据整车的市场定位、目标价格及供应商配套资源的情
况,再加上以往开发经验,选定制动系的配置结构和主要参数。
例如:
该车型初选制动系的结构为前盘后鼓、真空助力制动形
式,管路布置为Ⅱ型,制动力调节装置采用感载比例阀。
制动系相关参数输入如下:
f=0.7;
%
路面附着系数
D=20.64;
%
主缸直径(mm)
D1=50.8;
%
前轮缸径(mm)
D2=20.64;
%
后轮缸径(mm)
C1=0.7;
%
前轮制动器因数
C2=2.398;
%
后轮制动器因数
R1=98.5;
%
前轮制动器作用半径(mm)
R2=110;
%
后轮制动器作用半径(mm)
rd=281;
%
车轮有效半径(mm)
p_k=3;
%
感载比例阀空载拐点液压(MPa)
p_m=7.2;
%
感载比例阀满载拐点液压(MPa)
u=0.25;
%
感载比例阀分配比
ip=4.2;
%
制动踏板杠杆比
is=3.5;
%
助力器助力比
np=0.85;
%
制动踏板和主缸之间的传动效率
Po1=810;
%
最大助力点输入力(N)
Pw=9.31;%真空助力器拐点压力(MPa)
2.2制动理论相关函数曲线的绘制
2.2.1前后轴制动力分配曲线
前、后制动器制动力分配的比例将影响到汽车制动时的方
向稳定性和附着条件利用程度,是设计汽车制动系必须妥善处
理的问题。
为了保证制动时的方向稳定性,防止后轮抱死,实际
的制动力分配曲线(β线)应位于理想制动力分配曲线(I线)
的下方,而为了提高制动效率,β线应尽可能靠近I线。
根据汽车理论,理想制动器制动力分配曲线方程为:
F!
1—前制动器制动力;
F!
2—后制动器制动力;
G—汽车重力;
b—汽车质心至后轴中心线距离;
hg—汽车质心高度。
输入如下语句即可得到空、满载理想制动力分配曲线(I
线)数组:
Fu1=[0:
G_m];%前制动器制动力
Fu2_k=0.5*(G_k/hg_k*(b_k^2+4*hg_k*L*Fu1/G_k).^0.5-(G_k*b_k/hg_k+2*
Fu1));%
空载I
线
Fu2_m=0.5*(G_m/hg_m*(b_m^2+4*hg_m*L*Fu1/G_m
/hg_m+2*Fu1));%满载I
).^0.5-(G_m线、
*b_m
plot(Fu1,Fu2_k);%输出空载I曲线
holdon
plot(Fu1,Fu2_m);%输出满载I曲线
根据制动器因数的定义:
BF=Tf/PR
BF—制动器因数;
Tf—制动器摩擦力矩;
R—制动器作用半径;
P—输入力。
由制动器制动力Tf/rd,输入力与液压的关系
2
P=p*πd/4(rd为车轮有
效半径,p为管路液压,d为轮缸直径)可得到:
2×T
2×BF×P×R
2
F=
=
2×BF×P×!
×d×R
f=
(3)
!
(1/2)
rd
rd
4×rd
则比例阀拐点前的前、后制动器制动力比值(此时管路液压相等)用语句输入为:
k1=D2^2*C2*R2/(D1^2*C1*R1);
比例阀拐点后的前、后制动器制动力比值(此时管路液压分配比为u)用语
句输入为:
k2=k1*u;
求空、满载实际的制动力分配曲线(β线)数组,语句输入
为:
Fwf_k=pi*D1^2/4*p_k*2*C1*(R1/rd);%空载拐点前轮制动力
Fwr_k=k1*Fwf_k;%空载拐点后轮制动力
F1_k_1=[0:
Fwf_k];%空载拐点前的前轮制动力
F2_k_1=k1*F1_k_1;%空载拐点前的β线
F1_k_2=[Fwf_k:
G_m];%空载拐点后的前轮制动力
F2_k_2=k2*F1_k_2+(Fwr_k-k2*Fwf_k);%空载拐点后的β线
Fwf_m=pi*D1^2/4*p_m*2*C1*(R1/rd);%满载拐点前轮制动力
Fwr_m=k1*Fwf_m;%满载拐点后轮制动力
F1_m_1=[0:
Fwf_m];%满载拐点前的前轮制动力
F2_m_1=k1*F1_m_1;%满载拐点前β线
F1_m_2=[Fwf_m:
G_m];%满载拐点后的前轮制动力
F2_m_2=k2*F1_m_2+(Fwr_m-k2*Fwf_m);%满载拐点后的β线空、满载拐点后的β线方程可由线性方程求解得出
plot(F1k1,F2k1);%输出空载β线
holdon
plot(Fwf_k,Fwr_k);
holdon
plot(F1k2,F2k2);
holdon
plot(F1m1,F2m1);%输出满载β线
holdon
pl