模具资料整理.docx
《模具资料整理.docx》由会员分享,可在线阅读,更多相关《模具资料整理.docx(79页珍藏版)》请在冰豆网上搜索。
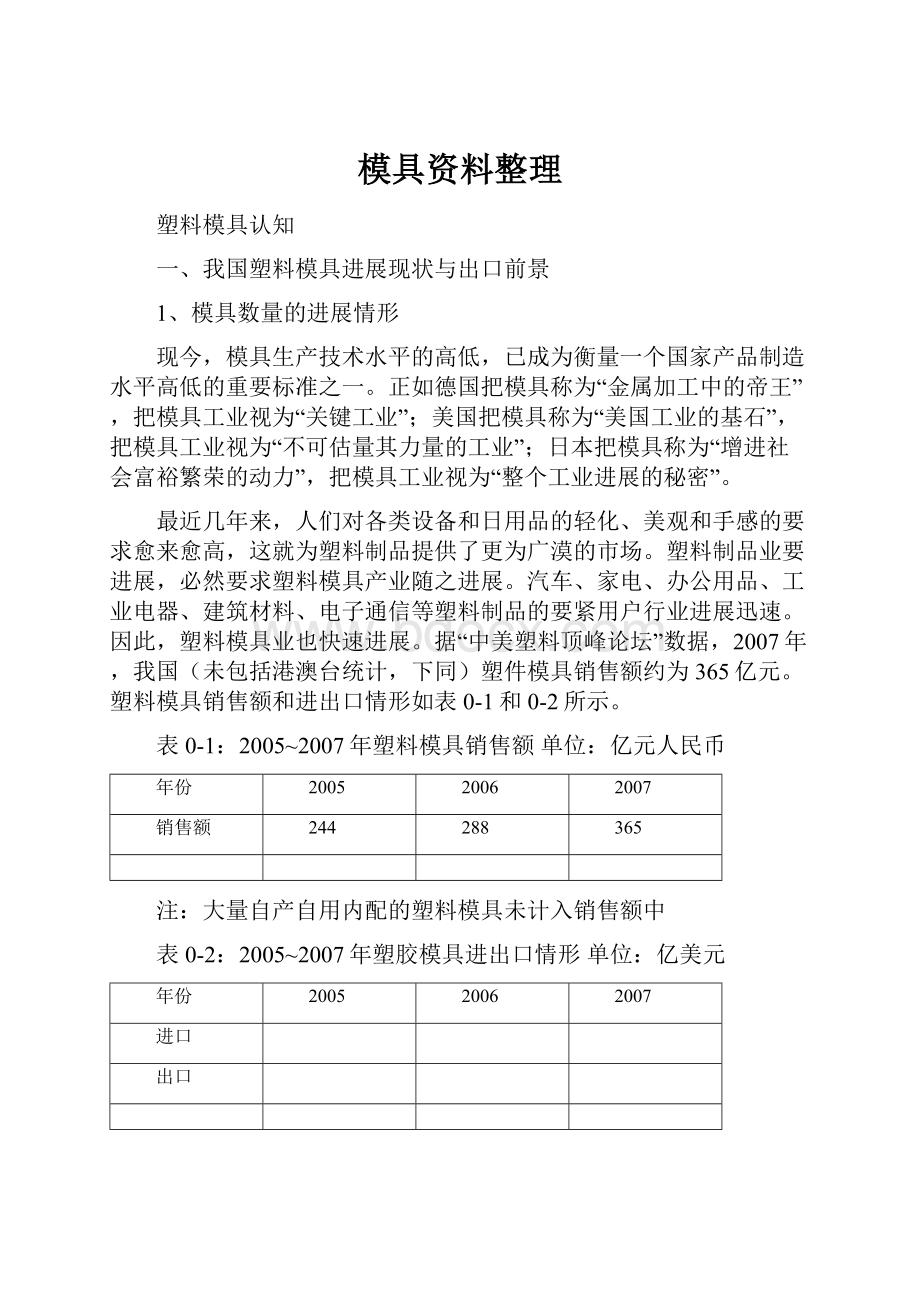
模具资料整理
塑料模具认知
一、我国塑料模具进展现状与出口前景
1、模具数量的进展情形
现今,模具生产技术水平的高低,已成为衡量一个国家产品制造水平高低的重要标准之一。
正如德国把模具称为“金属加工中的帝王”,把模具工业视为“关键工业”;美国把模具称为“美国工业的基石”,把模具工业视为“不可估量其力量的工业”;日本把模具称为“增进社会富裕繁荣的动力”,把模具工业视为“整个工业进展的秘密”。
最近几年来,人们对各类设备和日用品的轻化、美观和手感的要求愈来愈高,这就为塑料制品提供了更为广漠的市场。
塑料制品业要进展,必然要求塑料模具产业随之进展。
汽车、家电、办公用品、工业电器、建筑材料、电子通信等塑料制品的要紧用户行业进展迅速。
因此,塑料模具业也快速进展。
据“中美塑料顶峰论坛”数据,2007年,我国(未包括港澳台统计,下同)塑件模具销售额约为365亿元。
塑料模具销售额和进出口情形如表0-1和0-2所示。
表0-1:
2005~2007年塑料模具销售额单位:
亿元人民币
年份
2005
2006
2007
销售额
244
288
365
注:
大量自产自用内配的塑料模具未计入销售额中
表0-2:
2005~2007年塑胶模具进出口情形单位:
亿美元
年份
2005
2006
2007
进口
出口
注:
在海关统计中,塑料模具和橡胶模具在同一税目中,因此表中数据包括这两类模具,但塑料模具占其中的绝大多数。
从以上两个数据表能够看出,中国塑料模具进展专门快,三年平均进展速度是年均增加的22%,比模具行业整体进展速度高出约3个百分点。
但是,如此快的进展速度仍旧跟不上市场要求,2005年至2007年国产塑料模具在国内市场中的知足率别离只有%、和%。
尽管知足率在逐年提高,可是入口的塑料模具目前仍占我国市场的20%以上。
二、模具水平的进展情形
在生产量高速增加的情形下,中国塑料模具水平也有专门大的提高。
国内目前已能生产单套重量达60吨的大型模具、型腔精度达
的周密模具、一模7800腔的多腔模具及4m/min以上挤出速度的高速模具。
模具寿命也有专门大提高,能够达到100万模次以上。
典型的高水平模具如表0-3所示。
表0-3:
典型模具举例
大型模具
汽车保险杠、整体仪表板、大屏幕彩色电视机、大容量洗衣机等塑件模具
精密模具
光盘、导光板、手机、音像设备、小模数齿轮、车灯等塑件模具
复杂模具
多色注塑、多层注塑、低压注塑、带件注塑、模内转印、蒸汽注塑、热流道注塑、气体辅助注塑等塑件模具
多腔模具
塑料封装模具、塑料包装模具等模具
高速模具
塑料型材挤出模,包括双腔、双色、双材质等共挤模具
3、模具工业的进展趋势
⑴模具产品将向着更大型、更周密、更复杂及更经济快速方向进展;模具生产将朝着信息化、无图化、精细化、自动化方向进展;模具企业将向着技术集成化、设备精巧化、产品品牌化、治理信息化、经营国际化方向进展。
⑵模具CAD/CAE/CAM/PDM正向集成化、三维化、智能化、网络化和信息化方向进展。
快捷高速的信息化时期将率领模具行业进入新时期。
⑶模具的质量、周期、价钱、效劳四要素中,已有愈来愈多的用户将周期放在首位,要求模具尽快交货,因此模具生产周期将继续不断缩短。
⑷大力提高开发能力,将开发工作尽可能往前推,直至介入到模具用户的产品开发中去,乃至在尚无明确的用户对象之前进行开发(这需要在有较大把握和敢冒必然风险的情形下进行),变被动为主动。
和“你给我一个概念,我还你一个产品”的一站式效劳模式都已成为进展趋势。
⑸随着模具企业设计和加工水平的提高,过去以钳工为核心,大量依托技艺的现象已有了专门大转变。
在某种意义上说:
“模具是一种工艺品”的概念正在被“模具是一种高新技术工业产品”所替代,模具“上下模单配成套”的概念正在被 “只装不配"的概念所替代。
模具正从长期以来要紧依托技艺,而变成尔后要紧依托技术。
这不可是一种生产手腕的改变,也是一种生产方式的改变,更是一种观念的改变。
这一趋向使得模具标准化程度不断提高,模具精度愈来愈高,生产周期愈来愈短,钳工比例愈来愈低,最终促使整个模具工业水平不断提高。
⑹高速加工、复合加工、精益生产、敏捷制造及新材料、新工艺、新技术将不断取得进展。
4、模具行业存在的问题
我国塑料模具行业进展水平和国外先进水平相较,要紧存在六个方面的问题。
⑴进展不平稳,产品整体水平较低。
尽管个别企业的产品己达到相当高的水平,个别企业的部份产品已达到或接近国际水平,但整体来看,模具的精度、型腔表面粗糙度、生产周期、寿命等指标与国外先进水平相较尚有较大差距。
包括生产方式和企业治理在内的整体水平与国外工业发达国家相较尚有10年以上的差距。
⑵工艺装备掉队,组织和谐能力差。
尽管部份企业通过近几年的技术改造,工艺装备水平己比较先进,但大部份企业工艺装备仍比较掉队。
更要紧的是咱们的企业组织和谐能力差,难以专门好整合或调动社会资源为我所用,从而就难以承接比较大的项目。
⑶大多数企业开发能力弱。
一方面是技术人员比例低、水平不够高,另一方面是科研开发投入少,更重要的是观念掉队,对开发不够重视。
⑷治理掉队愈甚于技术掉队。
技术掉队往往容易看到,治理掉队有时却难以意识到。
国内外模具企业治理上的差距十分明显,治理的差距所带来的问题往往比技术上的差距更为严峻。
⑸市场需求旺盛,生产进展一时还难以跟上,供需矛盾一时还难以解决,供不该求的局 面还将持续一段时刻,专门是在中高级产品方面矛盾更为突出。
⑹体制和人材问题的解决尚待时日。
在社会主义市场经济中,在经济全世界化的进程中,竞争性行业,专门是像模具如此依托于特殊用户,需单件生产的行业,许多企业目前的体制和经营机制仍旧很难适应多变的市场。
人材的数量和素养水平也跟不上行业的快速进展。
尽管各地都在尽力解决这两个问题,但要取得较好解决尚待时日。
展望以后,由于国际、国内宏观环境整体良好,国内塑料模具各要紧用户行业仍将持续以较快速度进展,塑料模具也必将持续高速进展。
目前存在的要紧问题通过国内外交流与合作,通过全行业的一起尽力,通过各方面的一起支持,一定会慢慢取得较好的解决。
五、模具出口前景分析
中国是进展中国家,具有生产进展水平较低,劳动力资源丰硕,生产本钱低廉及市场前景广漠等一样进展中国家一样的一些特点,但中国人均GDP己超过2000美元,同时还具有相当雄厚的技术和工业基础,人们聪慧、勤劳、灵巧和改革开放良好环境等一些特殊的特点。
这些特点很适合进展模具工业,因其中国模具工业尽管起步较晚,但进展十分迅速。
从国际来看,一是由于许多外资在中国投资设厂的愈来愈多,二是工业发达国家模具生产本钱愈来愈高,因此世界上许多工业发达国家将模具慢慢转移到中国的趋向十分明显。
由于中国的模具技术提高快,在价钱方面又有较大的优势,模具性价比高,因此很多工业发达国家到中国采购模具的趋向也十分明显。
还有一个方面是有些进展中国家由于技术和工业基础薄弱,模具生产进展一时还跟不上经济进展所需,因此模具供不该求需要入口的现象也较为普遍。
他们入口工业发达国家的模具尽管质量水平高,但价钱昂贵,而中国模具在一样能知足要求的前提下,价钱比较适中,因此也有很多市场。
从近几年中国模具的出口市场来看,除欧、美、日本等工业发达国家是中国出口模具的最要紧市场之外,印度、泰国、马来西亚、越南等国家也有相当大的市场,我国香港和台湾的转口贸易也占了相当大的市场。
中国模具工业协会每一年都组织模具企业到欧、美参加有关的国际展览会,对进展国际交流与合作起到了专门好的增进作用。
近三年来中美模具贸易情形如表0-4所示。
表0-4:
2005~2007中美模具贸易情形单位:
亿美元
年份
2005
2006
2007
中国出口美国
美国出口中国
进入2 1世纪,2000~2007年,中国模具出口额从亿美元增加到亿美元,七年年均增加率为%,这充分说明了以往的出口业绩。
从上述中国的特点、国际市场状况和以往业绩和竞争力等多方面情形进行分析,能够看出中国的塑料模具出口前景将继续看好。
二、塑料成型工艺
一、注射成型工艺
注射成型原理及特点
注射成型又称注射模塑,是热塑性塑料制件的一种要紧成型方式。
除氟塑料外,几乎所有的热塑性塑料都可用此方式成型。
最近几年来,注射成型已成功地用来成型某些热固性塑料制件。
注射成型的原理是将颗粒状态或粉状塑料从注射机的料斗送进加热的料筒中,通过加热熔融塑化成为黏流态熔体,在注射机柱塞或螺杆的高压推动下,以很高的流速通过喷嘴,注入模具型腔,经一按时刻的保压冷却定型后可维持模具型腔所给予的形状,然后开模分型取得成型塑件。
如此就完成了一次注射工作循环,如图0-1所示。
(a)塑化时期
(b)注射时期
(c)塑件脱模
图0-1螺杆式注射机注射成型原理
1—料斗;2—螺杆转动传动装置;3—注射液压缸;4—螺杆;5—加热器;6—喷嘴;7—模具
注射成型的特点是:
成型周期短,能一次成型外形复杂、尺寸周密、带有嵌件的塑料制
件;对各类塑料的适应性强;生产效率高,产品质量稳固,易于实现自动化生产。
因此,注射成型普遍地用于塑料制件的生产中,但注射成型的设备及模具制造费用较高,不适合单件及批量较小的塑料制件的生产。
注射成型工艺进程
注射成型工艺进程包括:
成型前的预备、注射成型进程和塑件的后处置三个时期。
成型前的预备
为使注射进程能顺利进行并保证塑料制件的质量,在成型前应进行一系列必要的预备工作。
⑴原料外观的查验和工艺性能的测定
查验内容包括对色泽、粒度及均匀性、流动性(熔体指数、黏度)、热稳固性及收缩率的查验。
⑵物料的预热和干燥
关于吸水性强的塑料,在成型前必需进行干燥处置,除去物料中过量的水分和挥发物,以避免成型后塑件表面显现斑纹和气泡等缺点,乃至发生降解,严峻阻碍塑料制件的外观和内在质量。
各类物料干燥的方式应依照塑料的性能和生产批量等条件进行选择。
小批量生产用塑料大多数采纳热风循环烘箱或红外线加热烘箱进行干燥;大量量生产用塑料宜采纳沸腾干燥或真空干燥,其效率较高。
⑶嵌件的预热
在成型带金属嵌件,专门是带较大嵌件的塑件时,嵌件放入模具之前必需预热,以减少物料和嵌件的温度差,降低嵌件周围塑料的收缩应力,保证塑件质量。
⑷料筒的清洗
当改变产品、改换原料及颜色时均需清洗料筒。
通常,柱塞式料筒可拆卸清洗,而螺杆式料筒可采纳对空注射法清洗。
⑸脱模剂的选用
塑料制件的脱模,要紧依托于合理的工艺条件和正确的模具设计。
在生产上为顺利脱模,
通常利用脱模剂。
经常使用的脱模剂有硬脂酸锌(除聚酰胺外,各类塑料都可利用)、液态石蜡(白油)(适用于聚酰胺)和硅油(润滑成效好,但价钱较贵,利用也较麻烦)等。
注射成型进程
完整的注射成型进程包括加料、加热塑化、加压注射、保压、冷却定型、脱模等工序。
但从实质上讲主若是塑化、注射充模和冷却定型等大体进程。
⑴塑化
塑化是指粉状或粒状的物料,在料筒内加热熔融呈黏流态并具有良好的可塑性的全进程。
对塑化的要求是:
塑料在进入模腔之前,既要达到规定的成型温度,又要使熔体各点温度均匀一致,并能在规按时刻内提供上述质量的足够熔融塑料以保证生产持续顺利地进行。
⑵注射充模与冷却定型
在那个进程中塑料熔料的温度将不断下降,而压力的转变那么如图0-2所示。
图0-2注射成型进程中塑料压力的转变
①充模
塑化好的塑料熔体在注射机柱塞或螺杆的推动作用下,以必然的压力和速度通过喷嘴和模具的浇注系统进入并充满模具型腔,这一时期称为充模。
这一时期的时刻从开始充模到t1,压力转变为:
熔体未注入模具型腔前模腔内没有压力;待型腔充满时压力达到最大值p0。
②保压补缩(t1~t2)
这一时期是从熔体充满型腔时起至柱塞或螺杆退回时为止。
在注射机柱塞或螺杆推动下,熔体仍然维持压力进行补料,使料筒中的熔料继续进入型腔,以补充型腔中塑料的收缩需要。
在这段时刻内,模腔内熔体压力仍为最大值。
保压补缩时期关于提高塑件密度,减少塑件的收缩,克服塑件表面缺点均具有重要阻碍。
③倒流时期(t2~t3)
这一时期是从柱塞或螺杆开始后退时起至浇口处熔体冻结时为止。
这时模腔中的熔料压力比浇口前方的高,因此就会发生型腔中熔体通过浇口流向浇注系统的倒流现象,从而使模腔内压力迅速下降。
倒流将一直进行到浇口处熔料冻结时为止,p1为浇口冻结时的压力。
若是柱塞或螺杆后退时浇口处的熔料已经冻结,或在喷嘴中装有止逆阀,那么倒流时期不存在,就可不能显现t2~t3压力下降的曲线,而是图0-2中所示的虚线。
④浇口冻结后的冷却(t3~t4)
这一时期是从浇口处塑料完全冻结起到制件脱模掏出时为止。
这时,倒流再也不继续进行,模腔内的塑料继续冷却并凝固定型。
脱模时,塑件应具有足够的刚度,不致产生翘曲或变形。
在冷却时期中,随着温度的迅速下降,模腔内的塑料体积收缩,压力也慢慢下降。
开模时,模腔内的压力不必然等于外界大气压。
模腔内压力与外界压力之差称为残余压力(即图0-2中p2)。
当残余压力为正值时,脱模比较困难,塑件容易被刮伤乃至破裂;当残余压力为负值时,塑件表面显现凹陷或内部产生真空泡;当残余压力接近零时,塑件不仅脱模方便,而且质量较好。
应该指出的是,假设冷却速度过快或模温不均,那么塑件会由于冷却不均匀而致使各部份收缩不一致,使塑件产生内应力,因此冷却速度必需适当。
塑件的后处置
由于塑化不均匀或由于塑料在型腔内的结晶、取向和冷却不均匀,或由于金属嵌件的阻碍或由于塑件的二次加工不妥等缘故,塑件内部不可幸免地存在一些内应力,从而致使塑件在利用进程中产生变形或开裂,因此应该设法排除之。
依照塑件的特性和利用要求,可对塑件进行适当的后处置,其要紧方式是退火和调湿处置。
⑴退火处置
退火热处置是将塑件在定温的加热液体介质(如热水、热的矿物油、甘油、乙二醇和液体石蜡等)或热空气循环烘箱中静置一段时刻,然后缓慢冷却至室温,从而排除塑件的内应力,提高塑件的性能。
退火的温度应操纵在塑件利用温度10℃~20℃以上,或塑料的热变形温度以下10℃~20℃。
退火处置的时刻取决于塑料品种、加热介质温度、塑件的形状和成型条件。
退火处置后冷却速度不能太快,以幸免从头产生内应力。
退火处置排除塑件的内应力,稳固了尺寸,关于结晶型塑料还能提高结晶度、稳固结晶结构,从而提高其弹性模量和硬度,但却降低了断裂伸长率。
⑵调湿处置
调湿处置是将刚脱模的塑件放入热水中,以隔间空气,避免对塑料制件的氧化,加速吸湿平稳速度的后处置方式。
其目的是使制件颜色、性能和尺寸维持稳固,避免塑件利用中尺寸转变,制品尽快达到吸湿平稳。
调湿处置要紧用于吸湿性强的聚酰胺等塑件。
注射成型工艺参数
正确的注射成型工艺能够保证塑料熔体良好塑化,顺利充模、冷却与定型,从而生产出合格的塑料制件。
温度、压力和时刻是阻碍注射成型工艺的重要参数。
温度
在注射成型中需操纵的温度有料筒温度、喷嘴温度和模具温度等。
前两种温度要紧阻碍塑料的塑化和流动,而后一种温度主若是阻碍塑料的充模和冷却定型。
⑴料筒温度
料筒温度的选择与诸多因素有关,要紧有以下几方面:
①塑料的黏流温度或熔点
不同塑料,其黏流温度或熔点是不同的,关于非结晶型塑料,料筒结尾最高温度应高于黏流温度(Tf);关于结晶型塑料应高于熔点(Tm)。
但不论非结晶型或结晶型塑料,料筒温度均不能超过塑料本身的分解温度(Td)。
也确实是说,料筒温度应操纵在黏流温度(或熔点)与分解温度之间(Tf~Td或Tm~Td)。
除严格操纵最高温度外,还应操纵塑料在加热筒中停留的时刻,因为停留时刻太长(即便在温度不十分高的情形下)塑料也会发生降解。
②注射机类型
在柱塞式注射机中,塑料的加热仅靠料筒壁和分流梭表面传热,而且料层较厚,升温较
慢。
因此,料筒温度应高些,以使塑料内外层受热、塑化均匀。
关于螺杆式注射机,由于螺杆转动的搅动,同时使物料受高剪切作用,物料自身摩擦生热,使传热加速,因此料筒温度能够低于柱塞式10℃~20℃。
③塑件及模具结构特点
关于薄壁制件,其相应的模腔狭小,熔体充模的阻力大,冷却快,为了提高熔体流动性,
使其顺利充模,料筒温度应选择高一些。
相反,注射厚壁制件时,料筒温度可选择低一些。
关于形状复杂或带有嵌件的制件,或熔体充模流程曲折较多、较长的,料筒温度也应选择高一些。
料筒温度的散布,一样从料斗一侧起至喷嘴是慢慢升高的,以利于塑料慢慢均匀塑化。
⑵喷嘴温度
喷嘴温度通常略低于料筒最高温度,这是为了避免熔料在喷嘴处产生流涎现象。
喷嘴低温产生的阻碍可从熔料注射时所产生的摩擦取得必然程度的补偿。
可是,喷嘴温度不能太低,不然熔料在喷嘴处会显现早凝而将喷嘴堵塞,或有早凝料注入模腔而阻碍塑件的质量。
料筒温度和喷嘴温度的最正确值一样通过试模来确信。
⑶模具温度
模具温度对塑料熔体在型腔内的流动和塑料制品的内在性能与表面质量阻碍专门大。
模具温度的高低决定于塑料的特性、塑件尺寸与结构、性能要求及其他工艺条件等。
模具温度由通入定温的冷却介质来操纵,也有的靠熔料注入模具自然升温和自然散热达到平稳而维持必然的模温。
在特殊情形下,可采纳电阻加热圈和加热棒对模具加热而维持定温。
不管是加热或冷却,对塑料熔体来讲进行的都是冷却降温进程,以使塑件成型和脱模。
压力
注射成型进程中的压力包括塑化压力和注射压力,它们关系到塑化和成型的质量。
⑴塑化压力
塑化压力是指采纳螺杆式注射机时,螺杆顶部熔体在螺杆旋转后退时所受的压力,亦称背压,其大小能够通过液压系统中的溢流阀来调整。
塑化压力大小对熔体实际温度、塑化效率及成型周期等均有阻碍。
在其他条件相同的情形下,增加塑化压力,会提高熔体的温度及其均匀性,使色料的混合均匀并排出熔体中的气体。
但增加塑化压力会降低塑化速度,从而延长成型周期,而且增加了塑料分解的可能性。
因此,塑化压力应在保证塑件质量的前提下越低越好,其具体数值是随所用塑料的品种而异的,通常不超过2MPa。
⑵注射压力
注射机的注射压力指柱塞或螺杆顶部对塑料熔体所施加的压力。
其作用是克服熔体流动充模进程中的流动阻力,使熔体具有必然的充模速度及对熔体进行压实。
注射压力的大小取决于注射机的类型、塑料的品种、模具结构、模具温度、塑件的壁厚及流程的大小等,尤其是浇注系统的结构和尺寸。
关于熔体黏度高的塑料,其注射压力应比黏度低的塑料高;对薄壁、面积大、形状复杂及成型时熔体流程长的塑件,注射压力也应该高;模具结构简单、浇口尺寸较大的,注射压力能够较低;关于柱塞式注射机,因料筒内压力损失较大,故注射压力应比螺杆式注射机的高;料筒温度高、模具温度高的,注射压力也能够较低。
型腔充满后,注射压力的作用在于对模内熔料的压实。
在生产中,压实时的压力等于或小于注射时所用的注射压力。
若是注射时和压实时的压力相等,那么往往能够使塑件的收缩率减小,而且尺寸稳固性及力学性能较好。
缺点是会造成脱模时的残余压力过大、塑件脱模困难和成型周期长。
时刻(成型周期)
完成一次注射成型所需要的时刻,称为成型周期,它是决定注射成型生产率及塑件质量的一个重要因素。
它包括以下几部份:
充模时刻(柱塞或螺杆前进时刻)
注射时刻
注射时刻(保压时刻(柱塞或螺杆停留在前进位置的时刻)
成型周期
闭模冷却时刻(柱塞后退或螺杆转动后退的时刻均包括在这段时刻内)
其他时刻(指开模、脱模涂拭脱模剂、安放嵌件和闭模等时刻)
成型周期直接阻碍生产效率和设备利用率,应在保证产品质量的前提下,尽可能缩短成型周期中各时期的时刻。
在整个成型周期中,注射时刻和冷却时刻是大体组成部份,注射时刻和冷却时刻的长短对塑料制品的质量有决定性阻碍。
注射时刻中的充模时刻不长,一样不超过10s;保压时刻较长,一样为20~120s(特厚塑件可达5~10min)。
通常以塑料制品收缩率最小为保压时刻的最正确值。
冷却时刻要紧决定于塑料制品的壁厚、模具温度、塑料的热性能和结晶性能。
冷却时刻的长短应以保证塑料制品脱模时不引发变形为原那么,一样为30~120min。
另外,在成型进程中应尽可能缩短开模、脱模等其他时刻,以提高生产率。
注射模的分类及典型结构
注射模包括定模和动模两部份。
定模安装在注射机的固定模板上,动模安装在注射机的移动模板上,并可随移动模板的移动实现模具的启闭。
模具闭合后,动模和定模一路组成模具型腔和浇注系统,注射机即可向模具型腔注入熔融塑料,通过冷却,待模具型腔内的塑件定型后动模和定模分离,由推出机构将塑件推出,即完成一个生产周期。
注射模的结构组成
注射模的种类很多,其结构与塑料的品种、塑件的结构和注射机的种类等很多因素有关。
一样情形,注射模是由成型部件、浇注系统、导向部件、推出机构、调温系统、排气系统和支承零部件组成,若是塑件有侧向的孔或凸台,注射模还包括侧向分型与抽芯机构。
图0-3为最具有代表性的单分型面注射模,表0-5为常见注射模模具的结构组成。
(a)合模状态(b)开模状态
图0-3单分型面注射模的结构
1—动模板;2—定模板;3—冷却水道;4—定模座板;5—定位圈;6—浇口套;7—型芯;
8—导柱;9—导套;10—动模座板;11—支承板;12—支承钉;13—推板;
14—推杆固定板;15—拉料杆;16—推板导柱;17—推板导套;18—推杆;
19—复位杆;20—垫板;21—注射机顶杆
表0-5注射模的结构
结构名称
说明
零件名称(以图0-3为例)
成型部件
是指动、定模部分有关组成型腔的零件
动模板1、定模板2和型芯7
浇注系统
是将熔融的塑料从注射机喷嘴进入模具型腔所经的通道,它包括主流道、分流道、浇口及冷料穴
浇口套6、拉料杆15、动模板1和定模板2
导向部件
在注射模中,用导向部件对模具的动定模导向,以使模具合模时能准确对合
导柱8、导套9
推出机构
是指分型后将塑件从模具中推出的装置
推板13、推杆固定板14、拉料杆15、推板导柱16、推板导套17、推杆18、支承钉12和复位杆19
调温系统
为了满足注射工艺对模具温度的要求,需要有调温系统对模具的温度进行调整。
一般热塑性塑料的注射模主要是设计模具的冷却系统
冷却水道3
排气系统
为了将成型时塑料本身挥发的气体排出模外,常常在分型面上开设排气槽。
对于小塑件的模具,可直接利用分型面或推杆等与模具的间隙排气
支撑零部件
用来安装固定或支承成型零部件及前述的各部分机构的零部件
定模座板4、定位圈5、支承板11、支承钉12、垫板20和动模座板10
侧向分型
与抽芯机构
当有些塑件有侧向的凹凸形状的孔或凸台时,需先把侧向的凹凸形状的瓣合模块或侧向的型芯从塑件上脱开或抽出
常见注射模的分类及典型结构
注射模的分类方式很多,按加工塑料的品种可分为热塑性塑料注射模和热固性塑料注射模;按注射机类型可分为卧式注射机用注射模、立式注射机用注射模和角式注射机用注射模;按型腔数量可分为单型腔注射模和多型腔注射模;按其注射模整体结构特点可分为单分型面注射模、双分型面注射模、斜导柱(弯销、斜导槽、斜滑块、齿轮齿条)侧向分型抽芯注射模、带有活动镶件的注射模、定模带有推出机构的注射模和自动卸螺纹注射模等。
通常是按注射模具整体结构特点来分,所分类型的典型结构如下:
⑴单分型面注射模
如图0-3所示,只有一个分型面,因此称为单分型面注射模,也称两板式注射模。
这是注射模中最简单且用得最多的一种结构形式。
分流道及浇口在分型面上。
合模时在导柱八、导套9的导向定位下,动模和定模闭合。
型腔由定模板2上的凹模与固定在动模板1上的凸模7组成,并由注射机合模系统提供的锁模力锁紧。
以后注射机开始注射,塑料熔体经定模上的浇注系统进入模具型腔,待熔体充满模具型腔并通过保压、补缩和冷却定型后开模。
开模时,注射机合模系统带动