干法刻蚀技术的应用与发展.docx
《干法刻蚀技术的应用与发展.docx》由会员分享,可在线阅读,更多相关《干法刻蚀技术的应用与发展.docx(16页珍藏版)》请在冰豆网上搜索。
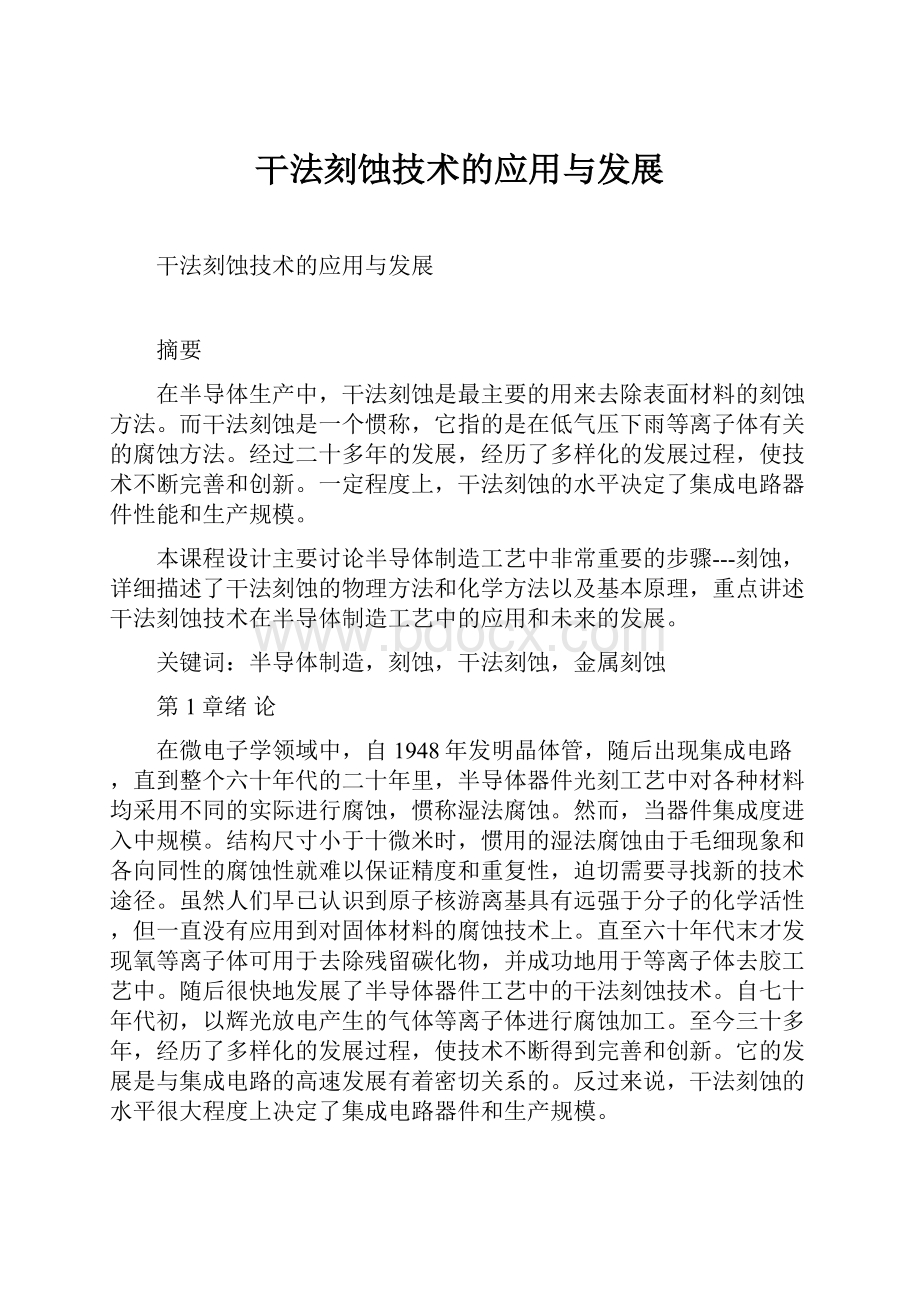
干法刻蚀技术的应用与发展
干法刻蚀技术的应用与发展
摘要
在半导体生产中,干法刻蚀是最主要的用来去除表面材料的刻蚀方法。
而干法刻蚀是一个惯称,它指的是在低气压下雨等离子体有关的腐蚀方法。
经过二十多年的发展,经历了多样化的发展过程,使技术不断完善和创新。
一定程度上,干法刻蚀的水平决定了集成电路器件性能和生产规模。
本课程设计主要讨论半导体制造工艺中非常重要的步骤---刻蚀,详细描述了干法刻蚀的物理方法和化学方法以及基本原理,重点讲述干法刻蚀技术在半导体制造工艺中的应用和未来的发展。
关键词:
半导体制造,刻蚀,干法刻蚀,金属刻蚀
第1章绪论
在微电子学领域中,自1948年发明晶体管,随后出现集成电路,直到整个六十年代的二十年里,半导体器件光刻工艺中对各种材料均采用不同的实际进行腐蚀,惯称湿法腐蚀。
然而,当器件集成度进入中规模。
结构尺寸小于十微米时,惯用的湿法腐蚀由于毛细现象和各向同性的腐蚀性就难以保证精度和重复性,迫切需要寻找新的技术途径。
虽然人们早已认识到原子核游离基具有远强于分子的化学活性,但一直没有应用到对固体材料的腐蚀技术上。
直至六十年代末才发现氧等离子体可用于去除残留碳化物,并成功地用于等离子体去胶工艺中。
随后很快地发展了半导体器件工艺中的干法刻蚀技术。
自七十年代初,以辉光放电产生的气体等离子体进行腐蚀加工。
至今三十多年,经历了多样化的发展过程,使技术不断得到完善和创新。
它的发展是与集成电路的高速发展有着密切关系的。
反过来说,干法刻蚀的水平很大程度上决定了集成电路器件和生产规模。
广义而言,所谓的刻蚀技术,是将显影后所产生的光阻图案忠实地转印到光阻下的材质上,形成由光刻技术定义的图形。
它包含了将材质整面均匀移除及图案选择性部分去除,可分为湿式刻蚀(wetetching)和干式刻蚀(dryetching)两种技术。
湿式刻蚀具有待刻蚀材料与光阻及下层材质良好的刻蚀选择比(selectivity)。
然而,由于化学反应没有方向性,因而湿式刻蚀是各向同性刻蚀。
当刻蚀溶液做纵向刻蚀时,侧向的刻蚀将同时发生,进而造成底切(Undercut)现象,导致图案线宽失真,如下图所示。
图1-1底切现象
自1970年以来,元件制造首先开始采用电浆刻蚀技术(也叫等离子体刻蚀技术),人们对于电浆化学性的了解与认识也就越来越深。
在现今的半导体集成电路或LCD制造过程中,要求精确地控制各种材料尺寸至次微米大小,而且还必须具有极高的再现性,电浆刻蚀是现今技术中唯一能极有效率地将此工作在高良率下完成的技术,因此电浆刻蚀便成为半导体制造以及TFTLCDArray制造中的主要技术之一。
干式刻蚀通常指利用辉光放电(glowdischarge)方式,产生包含离子、电子等带电粒子以及具有高度化学活性的中性原子、分子及自由基的电浆,来进行图案转印(patterntransfer)的刻蚀技术。
干法刻蚀是亚微米尺寸下刻蚀器件的最主要方法,广泛应用于半导体或LCD前段制程。
和其他一些技术。
比如气相腐蚀、激光诱导腐蚀,以及无掩膜的聚焦离子束腐蚀等,虽然亦有别于“湿法”,但已自成体系,一般不列入干法刻蚀之中。
经过二十多年的发展,出现多种干法刻蚀结构形式,她们具有各自的时代背景,也有各自的特点。
第2章干法刻蚀的机制和原理
2.1刻蚀工艺
在半导体制造中有两种基本的刻蚀工艺:
干法刻蚀和湿法腐蚀。
干法刻蚀是把硅片表面曝露与其他中产生的等离子体,等离子体通过光刻胶中开除的残空,与硅片发生物理或者化学反应(或这两种反应),从而去掉曝露的表面材料。
干法刻蚀是亚微米尺寸下刻蚀器件的最主要方方法。
而湿法腐蚀一般只用于尺寸较大的情况下(大于3微米)。
湿法腐蚀仍然用来腐蚀硅片上的某些层或用来去除干法刻蚀后的残留物。
干法刻蚀也可以根据被刻蚀的材料类型来分类。
按材料分,刻蚀主要分成三种:
金属刻蚀、介质刻蚀和硅刻蚀。
介质刻蚀是用于介质材料的刻蚀,如二氧化硅。
接触空和通孔结构制作需要刻蚀介质,从而在ILD中刻蚀出窗口,而具有高深度宽比(窗口的深于宽的比值)的窗口刻蚀具有一定的挑战性。
硅刻蚀(包括多晶硅)应用于需要去除硅的场合,如刻蚀多晶硅晶体管栅和硅槽电容。
金属刻蚀主要是在金属层上去掉铝合金复合层,制作出互联线。
刻蚀也可以分成有图形刻蚀和无图形刻蚀。
有图形的刻蚀采用掩蔽层(有图形的光刻胶)来定义要刻蚀掉的表面材料区域,只有硅片上被选择的这一部分在刻蚀过程中刻掉,有图形刻蚀可用来在硅片上制作多种不同的特征图形,包括栅、金属互联线、通孔、接触孔和沟槽。
无图形刻蚀、反过来或剥离是在整个硅片没有掩膜的情况下进行的,这种刻蚀工艺用于剥离掩蔽层(如STI氮化硅剥离和用于制备近体馆注入侧墙的硅化物工艺后钛的剥离)。
反刻是在想要把某一层膜的总的厚度减小时采用的(如当平坦化硅片表面是需要见效形貌特征)。
光刻胶是另一个剥离的例子。
总的来说。
有图形刻蚀和无图形刻蚀工艺能够采用干法刻蚀或湿法腐蚀技术来实现。
2.2刻蚀作用
干法刻蚀系统中,刻蚀作用是通过化学作用或物理作用,或者是化学和物理的共同作用来实现的。
在纯化学机理中,等离子体产生的反应元素(自由基和反应原子)与硅片表面的物质发生反应。
为了获得高的选择比(即为了与光刻胶或下层材料的化学反应最小),进入腔体的气体(一般含氯或氟)都经过了慎重选择。
等离子体化学刻蚀由于它是各向同性的,因而线宽控制差。
反应中产生的挥发性生成物被真空泵抽走。
为了获得物理机理的刻蚀,等离子体产生的带能粒子(轰击的正离子)在强电场下朝硅片表面加速,这些离子通过溅射刻蚀作用去除未被保护的硅片表面材料。
一般是用惰性气体,如氩。
这种机械刻蚀的好处在于它有很强的刻蚀方向性,从而可以获得高的各向异性刻蚀剖面,以达到好的线宽控制目的。
这种溅射刻蚀速率高,然而选择比差。
另外一个问题是被溅射作用去除的元素是非挥发性的,可能会从新淀积到硅片表面,带来颗粒和化学污染。
还有一种是物理和化学混合作用机理,其中离子轰击改善化学刻蚀作用。
刻蚀剖面可以通过调节等离子体条件和气体组分从各向同性向异性改变。
这种物理和化学混合作用机理刻蚀能获得好的线宽控制并有不错的选择比,因而在打多少数干法刻蚀工艺中被采用。
干法刻蚀系统可以是各向同性或各向异性的刻蚀机,这取决于RF电场相对于硅片表面的方向。
意思是指正离子溅射的发生是硅片表面还是硅片的边缘。
如果这个电场是垂直于硅片表面,刻蚀作用就是重正离子溅射和一些基本的化学反应,如果这个电场平行于硅片表面,物理的溅射作用就很弱,因此刻蚀作用主要是表面材料和活性元素之间的化学反应。
2.2.1物理刻蚀
纯物理性蚀刻可视为一种物理溅镀(Sputter)方式,它是利用辉光放电,将气体如Ar,解离成带正电的离子,再利用自偏压(selfbias)将离子加速,溅击在被蚀刻物的表面,而将被蚀刻物质原子击出。
此过程乃完全利用物理上能量的转移,故谓之物理性蚀刻。
利用下电极所产生的自偏压会吸引电浆中的正离子轰击基板表面,达到破坏膜层表面的刻蚀目的,这种刻蚀的好处在于它很强的刻蚀方向性,从而可以获得高的各相异性刻蚀剖面,以达到好的线宽控制目的。
其特点有:
图2-1物理溅射(sputter)机理
1、各相异性刻蚀。
2、低刻蚀选择比。
3、并且因轰击效应使得被刻蚀膜层表面产生损伤。
4、反应副产物多为非挥发性,容易累积于腔体部。
2.1.2化学刻蚀
纯化学反应性蚀刻,则是利用各式能量源(RF,DC,microwave等)给予气体能量,产生电浆,进而产生化学活性极强的原(分)子团,原(分)子团扩散至待蚀刻物质的表面,与待蚀刻物质反应产生挥发性之反应生成物,最后挥发性生成物被真空设备抽离反应腔。
因这种反应完全利用化学反应来达成,故谓之化学反应性蚀刻。
这种蚀刻方式相近于湿式蚀刻,只是反应物及产物的状态由液态改变为气态,并利用电浆来促进蚀刻的速率。
因此纯化学反应性蚀刻拥有类似于湿式蚀刻的优点及缺点,特点有:
1、各向同性刻蚀
2、高刻蚀选择比
3、高刻蚀速率
4、低表面损伤
5、反应腔体洁净度较易维持
图2-2化学反应性刻蚀机理
在半导体以及LCD制程中,纯化学反应性蚀刻应用的情况通常为不需做图形转换的步骤,如光阻的去除等。
图2-3基于化学反应机制的理想乾蚀刻过程
如图2-3所示,一个仅基于化学反应机制的理想乾蚀刻过程可分为以下几个步骤:
(1)刻蚀气体进入腔体,在电场作用下产生电浆形态之蚀刻物种,如离子及自由基(Radicals);
(2)蚀刻物种藉由扩散、碰撞或场力移至待蚀刻物表面;(3)蚀刻物种吸附在待蚀刻物表面一段时间;(4)进行化学反应并产生挥发性之生成物;(5)生成物脱离表面;(6)脱离表面之生成物扩散至气体中并排出。
上述步骤中若其中一个停止发生,则整个反应将不再进行。
而其中生成物脱离表面的过程最为重要,大部份的反应物种皆能与待蚀刻物表面产生快速的反应,但除非生成物有合理的气压以致让其脱离表面,否则反应将不会发生。
第3章干法刻蚀的应用
在集成电路制造过程中需要多种类型的干法刻蚀工艺,这些应用涉及在生产线上用到的所有材料。
我们将按被刻蚀材料的种类:
介质、硅和金属,来阐述干法刻蚀。
随着关键尺寸的缩小、较高的深宽比窗口以及新材料砸硅片制造过程的应用对这三类的刻蚀提出了挑战。
优化刻蚀条件是产品开发人员要解决的关键问题。
一般来说,一个成功的干法刻蚀要求:
1、对不需要刻蚀的材料(主要是光刻胶和下层材料)的高选择比。
2、获得可接受的产能的刻蚀速率。
3、好的侧壁剖面控制、
4、好的片均匀性。
5、低的期间损伤。
6、宽的工艺制造窗口。
对于每一种特殊的干法刻蚀应用,关键的刻蚀工艺参数通过工艺优化来确定。
其中一些参数在表(3-1),在许多情况下,优化是通过工艺设备的计算机模拟来实现的。
因为用硅片进行实际的样机测试需要很高的成本。
表3-1干法刻蚀中的关键参数
设备参数
设备设计、电源、电源频率、压力、温度、气流速率、
真空状况、工艺菜单
工艺参数
等离子体-表面相互作用:
表面材料、复合金属的不同层、表面温度、表面电荷、表面形貌;化学和无理要求;
时间
质量指标
刻蚀速率、选择比、均与性、特性曲线、关键尺寸、残留物
其他相关因素
净化间规、操作过程、维护过程、预防维护计划
3.1介质的干法刻蚀
对于200mm硅片,介质的干法刻蚀是最复杂的刻蚀过程;而对于300mm硅片,介质刻蚀将遇到最大的挑战。
氧化物刻蚀的最大困难在于随着特征尺寸缩小,在通互连中用于双层大马士革技术的层间介质的新的沟槽刻蚀工艺以及需要刻蚀低K层间介质所带来的更严格的工艺规。
3.1.1氧化物
刻蚀氧化物通常是为了制作接触孔和通孔。
这些事很关键的应用,要求在氧化物中刻蚀出具有高深宽比的窗口。
对于DRAM应用中的0.18um图形,深宽比希望能达到6:
1,对下层的硅和硅化物、多晶硅的选择比要求大约50:
1。
有一些新的氧化物刻蚀应用,如有新沟槽刻蚀和高深宽比刻蚀要求的双大马士革结构,也有低的深宽比通孔刻蚀,如非关键性的氧化物刻蚀应用。
3.1.1.1下层材料的选择比
氧化物刻蚀的主要困难之一是获得对下层材料(通常是硅、氮化硅或者一层抗反射图层)的高的选择比。
获得对硅的高选择比的一种方法是通过在化学气体中加入洋气来控制氧化物和硅之间的选择比。
少量洋气能改善氧化物刻蚀和硅刻蚀的速率。
当氧气浓度大至大约20%时,氧化物刻蚀比硅刻蚀要更快,增大了选择比,减少了对下层硅的刻蚀。
另一种提高选择比的方法是在气体混合物中加入氢气,减少硅的刻蚀速率,当氢气浓度达到大约40%是,硅刻蚀的速率几乎为零。
同时,氧化物刻蚀速率在氢气浓度地狱40%的时候几乎不受什么影响。
3.1.1.2光刻胶选择比
为了防止形成倾斜的侧墙,获得高的氧化硅/光刻胶选择比是很重要的。
光刻胶用于定义要刻蚀的图形。
在接触孔和通孔的刻蚀中,数百万的孔被同时刻蚀,每个孔中都需要去除精确数量的表层材料,而孔常常位于不同的深度,一种见效光刻胶选择比的因素是在高密度等离子体重活性氟原子的有效生成。
自由的氟原子会刻蚀掉有机的光刻胶的选择比。
另外,需要刻蚀抗反射涂层,这延长了刻蚀时间,进一步减小了光刻胶的厚度。
3.1.1.3侧壁剖面
在局部(LI)氧化层介质中的接触窗口尺寸通常与具有高深宽比的最小特征尺寸相等。
对于这种类型的应用,需要高度各项异性的垂直侧壁剖面。
一个重要的因素是高密度等离子体重高方向性的离子轰击。
3.1.2氮化物
在硅片制造过程中用到两种基本的氮化硅。
一种是在700~800摄氏度下用LPCVD顶级的,它产生按
组成比的氮化硅膜。
另外一种低密度的氮化硅膜是在低于350摄氏度下用PECVD淀积。
由于它的低密度,PECVD生长的氮化硅膜的刻蚀速率较快。
可用不同的化学气体来刻蚀氮化硅,常用的气体是
并与
和
混合使用。
增加
/
的含量来西施氟基的浓度并降低对下层氧化物的刻蚀速率。
另外可能用于氮化硅刻蚀的主要气体有
、
、
和
。
3.2硅的干法刻蚀
3.2.1多晶硅栅刻蚀
硅的等离子体干法刻蚀是硅片制造中的一项关键工艺技术,用等离子体刻蚀的两个主要硅层是制作MOS栅结构的多晶硅栅和制作器件隔离或DRAM电容结构中的单晶硅槽。
在MOS器件中,掺杂的LPCVD多晶硅是用做栅极的导电材料。
掺杂多晶硅线宽决定了有源器件的栅长,并会影响晶体管的性能。
刻蚀多晶硅(硅)通常是一个三步工艺工程。
这使得在不同的刻蚀步骤中能对各向异性刻蚀和选择比进行优化。
这三个步骤是:
(A)、第一步是预刻蚀,用于去除自然氧化层、硬的掩蔽层和表面污染物来获得均匀的刻蚀。
(B)、接下来的是刻蚀至终点的主刻蚀。
这一步用来刻蚀掉大部分的多晶硅膜,并不损伤栅氧化层和获得理想的各向异性的侧壁剖面。
(C)、最后一步是过刻蚀,用于去除刻蚀残留物和剩余的多晶硅,并保证对栅氧化层的高选择比,这一步应避免在多晶硅周围的栅氧化层形成微槽。
多晶硅栅是难以刻蚀的结构,在刻蚀过程中需要仔细且精密。
具有0.15μm特征尺寸器件的栅氧化层厚度是20~30Å(等6~10个氧化硅原子层的厚度)。
氧化硅厚度的损伤不得超过5Å(大约1.5个氧化硅原子层)。
为了防止栅氧化层的穿透,刻蚀的选择比要大于150:
1;为了去除刻蚀残留物和多余的多晶硅,过刻的选择比要大于250:
1。
3.2.2单晶硅的刻蚀
单晶硅刻蚀主要用于制作沟槽,如器件隔离沟槽或高密度。
DRAMIC中的垂直电容的制作。
在集成电路中硅槽的刻蚀要求对每一个沟槽都进行精确地控制。
在微米甚至亚微米构中,每个沟槽都要求一致的光洁度、接近垂直的侧壁、正确的深度和圆滑的沟槽顶角和底角。
3.3金属的干法刻蚀
金属刻蚀的一个主要应用是作为金属互联线的铝合金刻蚀。
金属刻蚀的要求主要有以下几点:
1、 高刻蚀速率(大于1000nm/min)。
2、 对下面层的高选择比,对掩蔽层(大于4:
1)和层间介质层(大于20:
1)。
3、 高的均匀性,且CD控制很好,没有微负载效应(在硅片上的任何位置小8%)。
4、 没有等离子体诱导充电带来的期间损伤。
5、 残留污染少(如铜硅残留物、显影液侵蚀和表面缺陷)。
6、 快速去胶,通常是在一个专用的去胶腔体中进行,不会带来残留物污染。
7、 不会腐蚀金属。
3.3.1铝和金属复合层
通常用氯基气体来刻蚀铝。
为了得到各向异性的刻蚀工艺,必须在刻蚀气体中加入聚合物(如CHF3或从光刻胶中获得的碳)来对侧壁进行钝化。
典型步骤:
1、 取出自然氧化层的预刻蚀。
2、 刻蚀ARC层(可能与上一步结合起来)。
3、 刻铝的主刻蚀。
4、 去除残留物的过刻蚀,它可能是主刻蚀的延续。
5、 阻挡层的刻蚀。
6、 为防止侵蚀残留物的选择性去除。
7、 去除光刻胶。
3.3.2钨
钨是在多层金属结构中常用的一种用于通孔填充的重要金属。
可用氟基或氯基气体来刻蚀钨。
常常在氟基的刻蚀气体中加入
来获得对光刻胶的好的选择比;有时加入
来减少碳的沉积。
氯基气体(如
和
)能用来刻蚀钨并改善各向异性特性和选择比。
第4章干法刻蚀设备的构成和主要性能指标
4.1.干法刻蚀设备的概述
刻蚀是用化学或物理的方法有选择地从基材表面去除不需要的材料的过程,其中干法刻蚀(DryEtching)具有很好的各向异性刻蚀和线宽控制,在微电子技术中得到广泛的应用。
在TFT-LCD制造过程中,Island,Channel和Contact的刻蚀一般使用的是干法刻蚀中RIE模式(ReactiveIonEtchingMode),图4-1是TEL(TokyoElectronLimited)生产的干刻机的简单示意图。
其设备的主体是工艺腔室(ProcessChamber),其他的辅助设备有产生工艺必需的真空之真空泵(Pump),调节极板和腔体的温度之调节器(Chiller),判断刻蚀终点之终点检测器(EPD,End-pointDetector),处理排出废气的尾气处理装置(Scrubber),以及搬运玻璃基板的搬送装置(比如马达,机械手)。
下面的容将对其中工艺腔室、真空泵、温度调节器和终点检测器进行介绍,以期对干法刻蚀设备的构成和主要性能指标有一个基本的了解。
图4-1TEL干刻机台的概貌
图4-2玻璃基板在干刻机台中的基本流程
4.2.干法刻蚀工艺流程
玻璃基板的基本流程(图4-2):
玻璃基板(GlassPanel)先存放在S/R中,通过机械手经由A/A传送到L/L,然后到T/C,接着基板被分配到各个P/C中去进行等离子体刻蚀处理。
在刻蚀过程中由EPD装置确定刻蚀的终点,如果达到刻蚀终点,则停止刻蚀,基板经由原来的路径传送到设备外进行下一段工序。
4.3.设备的主要的组成部分
玻璃基板在干刻工序的整个流程中,处于工艺腔(P/C)才是真正进行刻蚀,其他的动作只是基板从设备外大气状态下传送到工艺腔(真空状态)以及刻蚀前后进行的一些辅助程序。
所以整个干法刻蚀设备的核心部分是工艺腔。
基板置于工艺腔后,刻蚀气体由MFC控制供给到工艺腔,利用RF发生器产生等离子体,等离子体中的阳离子和自由基对需要刻蚀的薄膜进行物理和化学的反应,膜的表面被刻蚀,得到所需的图形,挥发性的生成物通过管道由真空系统抽走。
整个刻蚀过程就是这样的(图4-3)。
通过控制压力,RF功率,气体流量,温度等条件使得等离子体刻蚀能顺利进行。
图4-3工艺腔(ProcessChamber)的示意图
MFC:
MassFlowController,质量流量控制器;CM:
CapacitanceManometer,电容式压力计;APC:
AdaptivePressureController,压力调节器;TMP:
TurboMolecularPump,涡轮分子泵
4.4.干法刻蚀设备的主要性能指标
干法刻蚀设备的功能是在薄膜上准确复制特征图形,从生产产品的角度讲可以归于两方面:
产量和良率。
具体到设备上就对其性能指标提出一些要求。
简单的讲,产量,对应的是干法刻蚀设备的刻蚀速率和机台的稼动力;良率,对应的是干法刻蚀的刻蚀均匀性、刻蚀选择性、损伤和污染。
这里只对干法刻蚀设备这些性能指标作一个笼统的介绍。
蚀刻材料
刻蚀速率
a-Si
2000Å/min
n+a-Si
1000Å/min
SiNx
3000Å/min
表4-1刻蚀速率和稼动力
上表给出的是干法刻蚀工艺中需刻蚀的材料及其刻蚀速率。
但这只是单纯的指膜材料刻蚀的速率,并且这个数值可以通过修改工艺参数进行调节。
实际上,刻蚀前的准备(上下物料,抽真空等等)和刻蚀后的处理都要占用时间而影响产量。
所以在工艺过程中,真空设备的抽气时间、吹扫时间,物料的传送等等动作都是需要考量的。
另,TEL机台的刻蚀稼动力为85%。
刻蚀均匀性
面积
保证值
单片
<10%
片对片
<5%
腔对腔
<5%
刻蚀选择比
材料
选择比
a-Si/SiNx
>4
SiNx/Mo
>10
颗粒污染
颗粒物大小
颗粒物含量
>1µm
<300
>3µm
<50
表4-2良率相关的参数
上面三个表给出了干法刻蚀机台的刻蚀均匀性、选择性和污染的性能指标。
刻蚀均匀性的计算是在基板上选取13个点,测量数值,然后由(max-min)/(max+min)*100这个公式得到。
在工艺中,等离子体的刻蚀辐射损伤对器件的影响不是很明显,所以我们没有去考量。
总结与展望
一、总结
本文简单描述了干法刻蚀的机理和原理,了解干法刻蚀的在集成电路制造工艺的一些应用,熟悉了干法刻蚀设备的构成和主要性能指标。
干法技术的出现是由于集成电路制造工艺的需要,其发展也是伴随集成电路的不断微细化和高集成化而完善更新。
目前已成为生产不可缺少的关键技术,而且集成电路的器件性能和生产水平很大程度上取决约干法刻蚀技术,现在干法刻蚀设备的投资,已成为集成电路大规模产业化的重要部分。
干法刻蚀技术经过二十多年,已有很的的发展,并不断向新的方向开拓。
它对微电子学的发展、超大规模集成电路产业的扩大和量子期间的突破性进展起了关键性的作用。
干法刻蚀技术源于微电子器件的制作工艺需要,在光电子学领域的应用中有共同之处,但在工艺要求上各有侧重,因此从技术和设备的发展中已显示出各自的特点。
今后的发展不论在技术的本身或设备的结构上都是多样化的,而且仍然是方兴未艾。
在微细加工技术中,干法刻蚀是当前制作最微细结构的技术之一。
最大的应用领域首推微电子学,其次是光电子学,其他如微机械如超导等方面也有一定的应用。
参考文献
[1]MichaelQuirk,JulianSerda,半导体制作技术[M]..,电子工业,2009.7
[2]PhilipE.Allen,DouglasR.HolbergCMOS集成电路设计[M]..电子工业,2011.1
[3]来新泉,专用集成电路设计基础教程[M],,电子科技大学,2008.10
[4]朱正涌,海洋,朱正红,半导体集成电路[M],,清华大学,2009.04
[5]建中.半导体器件工艺中干法刻蚀的技术进展[J].微细加工技术,1993,(3):
43-50
[6]庆钊.90nm技术节点硅栅的干法刻蚀研究[J].微细加工技术2007.10
[7]任延同.离子刻蚀技术现状与未来发展.[J].《光学精密工程》1998.4
致
这次课程设计让我受益匪浅,首先我对于集成电路制造工艺有了更进一步的理解,深刻理解了干法刻蚀在集成电路制造工艺中的原理、具体应用和干法刻蚀设备的构成和主要性能指标。
通过写作论文提高了自己在专业知识方面的能力。
论文中还有很多不足之处希望老师给予指正和教导。
在论文即将完成之际,我的心情非常激动,从开始进入课题到论文的顺利完成,有很多可敬的老师、同学、朋友给了我无言的帮助,在这里请接受我诚挚的意!
感信息职业技术学院给了我人生中最美好的三年时光让我成长!
最后还要感支持和鼓励我的家人。
你们!