高速线材生产的质量控制.docx
《高速线材生产的质量控制.docx》由会员分享,可在线阅读,更多相关《高速线材生产的质量控制.docx(35页珍藏版)》请在冰豆网上搜索。
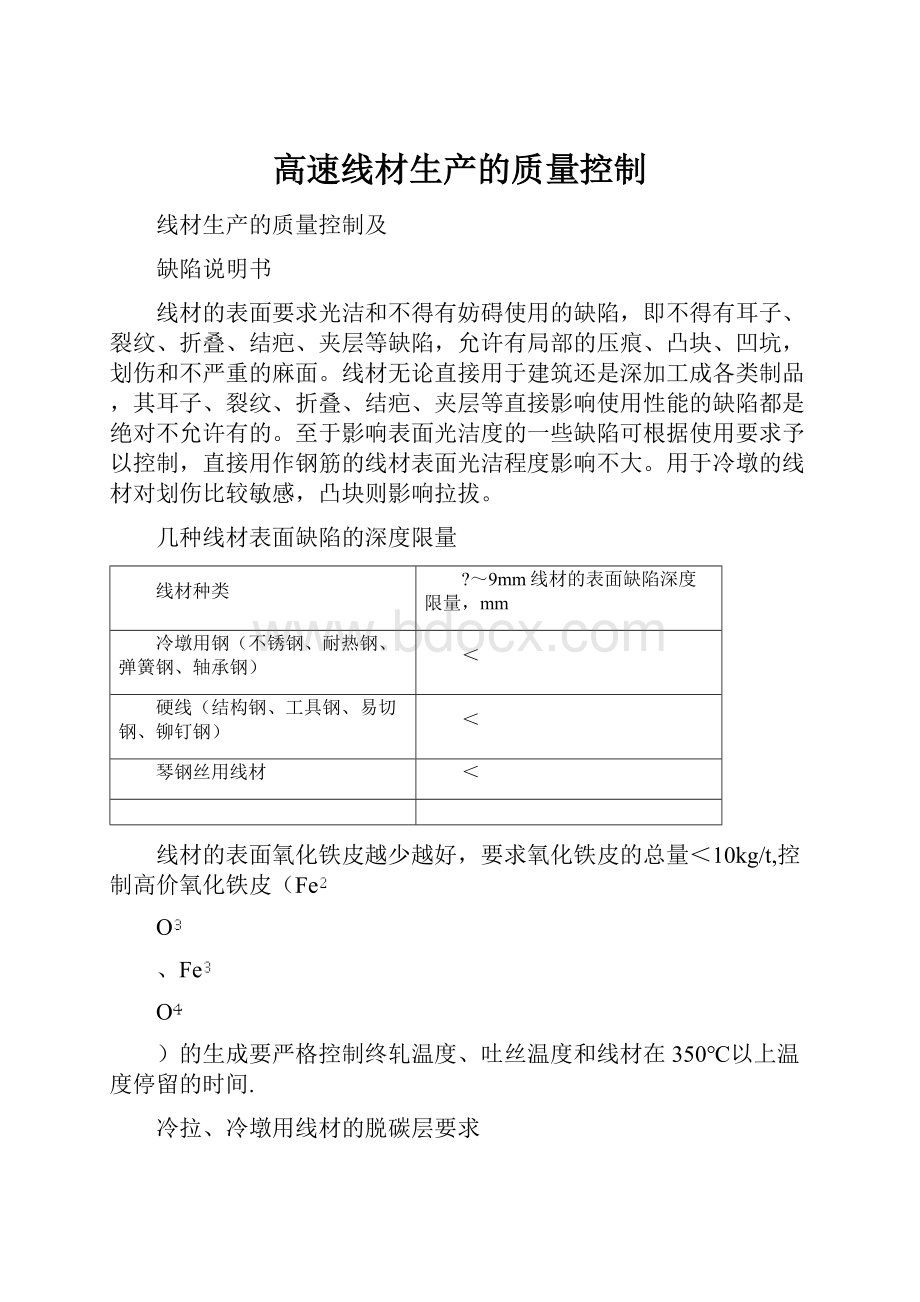
高速线材生产的质量控制
线材生产的质量控制及
缺陷说明书
线材的表面要求光洁和不得有妨碍使用的缺陷,即不得有耳子、裂纹、折叠、结疤、夹层等缺陷,允许有局部的压痕、凸块、凹坑,划伤和不严重的麻面。
线材无论直接用于建筑还是深加工成各类制品,其耳子、裂纹、折叠、结疤、夹层等直接影响使用性能的缺陷都是绝对不允许有的。
至于影响表面光洁度的一些缺陷可根据使用要求予以控制,直接用作钢筋的线材表面光洁程度影响不大。
用于冷墩的线材对划伤比较敏感,凸块则影响拉拔。
几种线材表面缺陷的深度限量
线材种类
?
~9mm线材的表面缺陷深度限量,mm
冷墩用钢(不锈钢、耐热钢、弹簧钢、轴承钢)
<
硬线(结构钢、工具钢、易切钢、铆钉钢)
<
琴钢丝用线材
<
线材的表面氧化铁皮越少越好,要求氧化铁皮的总量<10kg/t,控制高价氧化铁皮(Fe
O
、Fe
O
)的生成要严格控制终轧温度、吐丝温度和线材在350℃以上温度停留的时间.
冷拉、冷墩用线材的脱碳层要求
钢种
线材直径范围,mm
铁素体脱碳层深度,mm
全脱碳层深度,mm
碳素钢
<
<
<
~
<
<
~
<
<
低合金钢
<
<
~
<
<
~
<
<
~
<
<
>
<
<
缩孔、夹杂、分层、过烧等都是不允许存在的缺陷。
热轧盘条的质量控制
高速线材轧机生产的热轧盘条的质量通常包括两个方面的内容:
一是盘条的尺寸外形,即尺寸精度及外表形貌;二是盘条的内在质量,即化学成分、微观组织和各种性能。
前者主要由盘条轧制技术控制,后者除去轧制技术之外,还严重受上游工序的影响。
任何质量控制都要靠严格的完整的质量保证体系,靠工厂工序的保证能力,靠质量控制系统的科学、准确、及时的测量、分析和反馈。
高速线材轧机是高度自动化的现代轧钢设备,其质量控制概念也必须着眼于全系统的各个质量环节。
为了准确的判断和控制缺陷,首先要把缺陷产生的原因分析清楚,并设法将它控制消灭在最初工序。
缺陷的清理或钢材的判废越早,损失越少。
(一)外形尺寸
高速线材轧机精轧机组的精度很高,轧辊质量很好,当速度控制系统灵敏,孔型轧制制度合理,并且调整技术熟练时,它生产的盘条精度可以大大超过老式盘条的精度。
热轧盘条尺寸精度允许的偏差(GB/T14981)
直径,mm
允许偏差,mm
不圆度,mm
A级精度
B级精度
C级精度
A级精度
B级精度
C级精度
~
±
±
±
≤
≤
≤
~
±
±
±
≤
≤
≤
~
±
±
±
≤
≤
≤
(二)表面质量
现将高速线材生产过程中,易出现的产品缺陷得特征、产生原因及危害、预防及消除方法及检查判断的依据等进行介绍,有些缺陷因条件不具备未能配备图,在以后的实习及生产过程中再进行补充。
1、耳子
(1).缺陷特征
线材表面平行于延轧制方向的条状凸起叫耳子,呈连续或断续分布。
在线材一侧的叫单边耳子;在线材两侧的叫双边耳子;线材上下两个半圆错开的叫错边耳子。
主要是轧槽过充满造成的。
在高速线材轧机连轧生产中,最终产品的头尾两端很难避免耳子的产生。
(2).产生原因及危害
产生原因:
①钢坯温度偏低,导致轧件宽展大,延伸小;
②孔型设计不合理;
③导卫设计不合理、加工不良或导卫安装不正确;
④轧机装配不良、烧轴承未及时发现等造成轴窜;
⑤料型调整不当,成品前架来料偏大或堆钢,造成成品孔过充满。
⑥坯料的缺陷,如缩孔、偏析、分层等外来夹杂物影响轧件的正常变形,也是耳子形成的原因。
⑦孔型错动。
危害:
带有耳子的线材机械性能不均匀,当用于深加工时,产生不均匀变形,降低拉拔性能,且对模子产生不均匀磨损。
(3).预防及消除方法
①确保钢坯加热质量,避免轧辊冷却水直接浇到轧件表面;
②孔型设计要合理;
③导卫设计要合理,导卫加工和安装要符合工艺要求;
④提高轧辊加工和装配质量;
⑤加强料型调整,合理分配各道次压下量。
⑥注意坯料的质量检查,减少坯料质量带来的缺陷。
⑦经常检查孔型,预防孔型发生错动。
(4).检查判断
肉眼检查;整盘有耳子则判废,头尾耳子应切净。
2结疤
图2结疤
(1)缺陷特征:
在线材表面上与本体粘合一头或完全不粘合的金属层叫结疤。
一般呈舌状,厚薄不均,大小不一,有的生根,有的不生根,在线材全长上,呈有规律或无规律分布。
产生原因及危害
(2)产生原因:
①原料本身存在耳子、折叠或结疤(与盘条本体部分结合);
②轧件表面氧化铁皮未清除干净,压入轧件表面形成结疤(形成完全未结合的金属片层);
③折叠进一步轧制后,折叠层被拉裂形成结疤;
④由于外界金属物落在轧件表面上,同时被带入轧槽,经轧制后,被压附在轧件表面而产生结疤。
这种结疤不生根,分布是无规律的;
⑤轧制过程中轧件划伤严重;
⑥导卫表面粘有铁屑;
⑦非成品孔轧槽上有较大的凹坑,在轧制时压成凸块,再轧后形成周期性的结疤。
危害:
影响线材表面质量等级,在深加工时,易起毛刺,严重时还易发生断裂,降低拉拔性能。
(3)预防及消除方法
①加强原料验收,杜绝表面有质量缺陷的钢坯进入下一道工序;
②合理控制加热工艺,避免钢坯表面氧化层过厚;
③严格料型控制,防止过充满及摆料;
④仔细检查导卫内表面的情况,对粘有氧化铁皮的部位要及时清除;
⑤合理调整机架间的秒流量,避免对轧件严重划伤;
⑥加强轧槽表面质量检查。
(4)检查判断
用肉眼检查;用于深加工线材不允许有结疤缺陷存在。
3折叠
(1).缺陷特征
线材表面沿轧制方向呈直线状或锯齿状的未焊合缝隙,在横断面上呈现折角的缺陷叫折叠,一般是延轧制方向呈连续或断续分布。
折叠的两侧常伴有脱碳层或部分脱碳层,折缝中间氧化铁夹杂。
(2).产生原因及危害
产生原因:
①原料本身存在折叠;
②钢坯表面清理不当,有尖锐棱角,或清理深宽比不符合要求,轧制时形成折叠;
③非成品孔轧件产生明显耳子(单边耳子、双边耳子、错边耳子等),当轧件翻转90o进入下一孔型时,耳子被压倒而形成折叠;
④线材表面划伤较深,再轧制后形成折叠。
⑤连铸坯上的缺陷处理不当留下的深沟,轧制时形成折叠。
图3折叠
危害:
带有折叠的线材在深加工时,极易起毛刺或断裂。
(3).预防及消除方法
①加强原料检查,严禁使用表面质量不合格的原料轧制线材;
②保证轧制温度正常;
③加强料型调整,规范操作,避免成品前某道次出现耳子;
④定期检查轧制情况,防止轧件刮伤。
(4)检查判断
用肉眼检查,或通过镦粗、扭转或金相检查;
按相关标准进行判定。
4裂纹
图4裂纹
(1).缺陷特征
线材表面有不同形状的破裂称裂纹,分为纵向裂纹和横向裂纹两种。
一般纵向裂纹在线材表面呈连续或断续分布;而横向裂纹呈不连续分布。
有的裂纹内有夹杂物,两侧也有脱碳的现象。
(2).产生原因及危害
产生原因:
①线材用钢坯上存在未消除的裂纹(无论纵向还是横向),皮下气泡及非金属夹杂都会在盘条上产生裂纹缺陷;连铸坯上的针孔如不清除,经轧制被延伸、氧化、熔接就会造成成品的线状发纹。
针孔是连铸坯常见的重要缺陷之一,不显露时很难检查出来,应当特别予以注意。
②钢坯加热时过烧,对于高碳钢盘条或合金含量高的钢坯加热工艺不当(预热速度过快,加热温度过高等);
③在轧制过程中严重的温度不均或变形不均(还很可能出现横向裂纹);
④轧件冷却过快或局部骤冷,轧后控冷不当形成的裂纹无脱碳现象伴生,纹缝中一般无氧化铁皮。
危害:
有裂纹的线材极易断裂,造成报废。
(3).预防及消除办法
①加强钢坯质量检查,杜绝轧制不合格钢坯;
②合理控制钢坯加热温度,严禁钢坯过烧;
③合理控制线材的轧制温度和变形制度;
④合理控制冷却工艺制度。
(4).检查判断
用肉眼检查,可通过镦粗、扭转或金相判断;
有裂纹缺陷的部位必须切除或判废。
5压痕
图5压痕
(1).缺陷特征
在线材表面沿轧制方向连续或断续出现的压伤痕迹称压痕。
(2).产生原因及危害
产生原因:
①压辊孔槽加工不良;
②压辊及导卫装配质量差;
③压辊对轧件的夹持力过大。
危害:
影响线材的断面尺寸精度和表面质量等级,严重时影响使用。
(3).预防及消除方法
①提高压辊孔槽加工质量,且上机前用样板仔细检查压辊孔槽质量;
②压辊及导卫装配质量符合工艺要求;
③合理调整压辊夹持力,既保证压辊对盘条的夹持,又不能过大。
(4).检查判断
用肉眼检查;按相关标准进行判定。
6凹坑
图6凹坑
(1).缺陷特征
在线材表面呈规律性或无规律性分布、其大小及深浅不一的局部金属缺损叫凹坑。
(2).产生原因及危害
产生原因:
①在轧制过程中,细小的硬杂物嵌到轧件上,轧制后,嵌入物脱落;
②成品辊表面粘有异物。
危害:
用于深加工时,凹坑处易成为裂纹源,造成线材在拉拔过程中断裂。
(3).预防及消除方法
①加强轧制过程中轧槽、导卫检查,发现异物及时清除;
②加强成品轧辊表面质量检查,并及时清除表面粘有的异物。
(4).检查判断
用肉眼检查;根据相关标准判定。
7不圆度
图7不圆度
(1).缺陷特征
线材的圆形断面失圆,断面的最尺寸与最小尺寸之差超过标准要求称不圆度。
(2).产生原因及危害
产生原因:
①轧件温度不均,造成断面形状不良或堆拉值过大;
②孔型设计不合理或孔槽磨损严重未及时更换;
③料型调整不当;
④轧辊加工质量不符合工艺要求;
⑤轧辊装配不良。
危害:
不圆度过大的线材,用于深加工时,不均匀变形大,模具磨损加剧。
(3).预防及消除方法
①提高钢坯加热质量及轧制工艺稳定性;
②孔型设计要合理,轧槽要及时更换;
③合理进行料型调整,且相邻机架间的拉钢要适当;
④提高轧辊加工质量,加强轧辊加工质量检查,杜绝不合格轧辊上轧机使用;
⑤提高轧机装配精度。
(4).检查判断
用肉眼检查,游标卡尺测量;按相关标准判定。
8划痕
图8划痕
(1).缺陷特征
在线材表面沿轧制方向出现肉眼能看到沟底且呈连续或断续分布的沟槽状擦伤叫划痕。
(2).产生原因及危害
产生原因:
①穿水冷输线管内表面粗糙或粘有氧化铁皮;
②吐丝管内表面粗糙或内表面磨损严重未及时更换。
③夹送辊、散卷输送线、集卷器、打捆机等有缺陷的设备造成。
危害:
用于拉丝及其他深加工时,易起毛刺,降低钢丝表面质量等级。
(3).预防及消除方法
①提高输线管内表面质量,并加强输线管使用状况检查;
②提高吐丝管内表面的光洁度,并及时更换磨损严重的吐丝管。
③对夹送辊、散卷输送线、集卷器、打捆机等设备使用状况进行检查,及时更换有缺陷的设备。
(4).检查判断
用肉眼检查;
按相关标准判定,超过标准的切除或判废。
9凸起及压痕(辊印)
图9凸起及压痕(辊印)
(1).缺陷特征
线材表面呈周期性的凸起或凹陷部份称辊印,其形状不规则。
(2).产生原因及危害
产生原因:
成品孔或成品前孔轧槽碰伤或剥落掉块或局部凸起。
危害:
用于深加工时,辊印处易成为裂纹源,造成拉拔时断裂。
(3).预防及消除方法
加强轧槽检查,发现轧槽碰伤或剥落掉块,必须换槽或换辊。
(4).检查判断
用肉眼检查;按相关标准判定。
10麻点(麻面)
图10麻面
(1).缺陷特征
线材表面上有许多细小凹凸点组成的小颗粒状缺陷称麻面。
它在线材全长上呈周期性或连续性分布。
(2).产生原因及危害
产生原因:
①压辊车削后发生严重锈蚀或孔槽表面不良;
②轧槽长时间不换,使得成品孔型中最易磨损的上下槽底很粗糙;
③轧槽表面粘附有较多的氧化铁皮,轧制时将它压入线材表面,在成品上造成麻面;
④冷却水质量差。
⑤吐丝温度过高,冷却速度过慢盘条表面受到严重的氧化造成
⑥有时盘条存放在潮湿及腐蚀的气氛中。
危害:
影响线材表面质量等级。
(3).预防及消除方法
①严禁表面锈蚀严重或孔槽表面不良的压辊上机使用;
②换辊换槽须严格按技术操作规程进行;
③加强轧槽检查,及时清除表面粘有的氧化铁皮;
④冷却水质量符合工艺要求。
⑤严格控制吐丝温度及冷却速度。
⑥注意应当选择干燥无腐蚀的环境进行存放。
(4).检查判断
用肉眼检查;按相关标准判定。
11毛刺
图11毛刺
(1).缺陷特征
线材深加工时,从线材基体上伸出的长短不一的金属细丝称毛刺。
(2).产生的原因及危害
产生原因:
原料原因:
①线材存在皮下夹杂;
②盘条折叠。
深加工原因:
③深加工模具润滑不良;
④拉丝机拉力不合理。
危害:
影响深加工产品的表面质量,给用户使用造成困难。
(3).预防及消除方法
①提高钢质纯净度,避免存在皮下夹杂;
②在线材轧制时严禁出现折叠;
③深加工模具润滑要良好;
④拉丝机拉力要合理。
(4).检查判断:
用肉眼检查;
按相关标准判定。
12夹杂
图3-1-1夹杂
(1)缺陷特征
暴露在方圆钢表面上的非金属物质称为表面夹杂(一般幼眼可见的非金属夹杂物质)。
一般呈点状、块状或条状分布,其大小、深浅无规律,颜色有暗红、淡黄、灰白等。
(2)产生原因及危害
产生原因:
(1)钢坯表面或近表面有夹杂,多为铸钢时耐火材料附在钢坯表面,钢坯入炉时漏检所致;
(2)钢坯粘有非金属物质(如炉渣、耐火材料等),在加热、轧制过程中,粘附在方圆钢表面上。
危害:
影响外观质量,严重时导致产品判废。
(3)预防消除方法
(1)不使用带有夹杂的钢坯;
(2)轧件经过的地方要干净,避免粘附非金属夹杂。
(4)检查判断
用肉眼检查,必要时可用锤击;
方圆钢表面有夹杂部分进行清理,清理后按缺陷深度进行判定。
13轧疤
图13轧疤
(1)缺陷特征
轧制过程中造成的粘结在方圆钢表面上的金属薄片称为轧疤。
其外形类似结疤,与结疤相区别的主要特征是轧疤缺陷下面常无非金属夹杂或夹渣。
(2)产生原因及危害
产生原因:
1火焰清理操作不当,在钢坯表面造成深宽比不合,再轧后产生轧疤;
2轧件在孔型内打滑,造成金属堆积在变形区,再轧后形成轧疤;
3孔型刻痕不良、有砂眼、掉肉或损伤,使轧件表面产生周期性凸块或凹坑,再轧后形成周期性轧疤;
4轧件被辊道、翻钢机等机械设备卡(刮)伤,再轧后形成轧疤。
有的还伴生月牙形金属破缺现象。
危害:
有严重结疤的方圆钢应判废。
(3)预防消除方法
1加强钢坯检查,不使用清理深宽比不符合标准规定的钢坯;
2钢坯加热温度不宜过高,以免轧件在孔型内打滑;
3换辊前认真检查辊道、翻钢机等机械设备,检查孔型表面,不使用有砂眼或刻痕不良的孔型。
(4)检查判断
用肉眼检查,用深度游标卡尺测量其深度,必要时采用试铲试磨的方式对深度进行测量;
轧疤深度较浅时,可沿轧制方向进行修磨,修磨深度不得超过该部位的尺寸偏差;轧疤深度较深时,缺陷部位必须切除或判废。
14过烧
图14过烧
(1)缺陷特征
钢坯加热温度过高使钢材局部沿晶界断裂,形成表面的横向裂口称为过烧。
多出现在棱角处。
(2)产生原因及危害
产生原因:
当钢坯的加热温度超过AC3临界点,并在此温度下停留时间过长,导致晶粒之间弱化,轧件轧制变形中局部撕裂,主要有:
①加热操作不当,炉温过高;
②因故停轧时,钢坯在高温下停留时间过长;
③当加热炉内有偏烧时,易产生局部过烧。
危害:
导致轧件判废。
(3)预防消除方法
①严格执行钢坯加热操作规程,根据钢的不同成分选择加热温度和加热时间;
②待轧时应按降温制度控制加热炉温度;
③加强操作,注意烧嘴中空气与煤气的配比,防止偏烧现象;
④注意观察加热炉内钢坯棱角部位是否出现模糊不清和白亮,有时氧化铁皮发生熔化或冒火花,操作人员应及时调整炉温。
(4)检查判断
用肉眼检查;
有过烧的方圆钢判废。
15热扭
图15热扭
(1)
缺陷特征
沿长度方向各部分截面绕其纵轴角度不同的现象称扭转。
在台架上,可见一端的一侧翘起,有时另一端亦翘起,与台面成某一角度。
扭转十分严重时,整根钢材甚至成“麻花形”。
(2)产生原因及危害
产生原因:
1轧机安装、调整不当,轧辊中心线不在同一垂直或水平面上,轧辊轴向窜动、轧槽错位;
2导卫板安装不正或磨损严重;
3轧件温度不均或压下量不均,造成各部分延伸不一致。
危害:
扭转严重的方圆钢判废。
(3)预防消除方法
①加强轧钢机和导卫板的安装调整。
不使用磨损严重的导卫板,以消除加在轧件上的扭转力矩;
②钢材在热态下尽量不要在冷床一端进行翻钢,避免端部扭转;
③轧制中造成方圆钢扭转严重时,在矫直过程中较难消除。
因此用肉眼观察出成品孔的轧件不得有明显的扭转。
(4)检查判断
肉眼在水平台架上检查,量具测量;
以钢材一端在台架上翘起缝隙来衡量扭转程度,并按相应标准进行判定。
15热刮伤
图15热刮伤
(1)缺陷特征
轧件在热态被设备、工具尖棱刮成的沟痕称热刮伤。
其深度不等,可见沟底,一般有尖锐棱角,常呈直线形,也有的呈曲线形。
(2)产生原因及危害
产生原因:
①导卫板加工不良,导卫板磨损严重或粘有异物,将轧件表面刮伤;
②导卫板安装调整不当,对轧件压力过大,将轧件表面刮伤;
③热轧区地板、辊道、移钢、翻钢等设备有尖棱,轧件通过时被刮伤。
危害:
严重的热刮伤,造成产品判废,影响质量等级。
(3)预防消除方法
①导卫装置、地板、辊道等设备要保持光滑平整,不得有尖锐棱角;
②加强对导卫板安装调整,不应偏斜或过紧,避免对轧件压力过大;
③轧制生产中,当某道次轧件被导卫装置刮伤时,可见飞溅火星或刮出铁丝,此时操作人员应及时检查处理。
(4)检查判断
用肉眼检查;
热刮伤按相应标准进行判定。
在保证尺寸的情况下,可采取修磨方式进行消除。
16冷伤
图16冷伤
(1)缺陷特征
冷态的方圆钢在输送、吊运、存放过程中产生的各种大小不一,深浅不同,无规律的伤痕称为冷伤。
伤痕处一般较为光亮。
(2)产生原因及危害
产生原因:
①在输送过程中,方圆钢碰撞地板、挡板等机械设备;
②吊运或堆放不当,方圆钢局部碰伤而造成伤痕;
③在输送台架传送过程中,因移钢小车的划爪不齐,同时拉钢根数太多、速度过快或短钢相夹被碰伤。
危害:
严重的冷伤经热加工易形成疤痕缺陷。
(3)预防消除方法
①垫平地板,排除方圆钢输送过程中的各种机械性障碍,在辊道中运行接近挡板时,应减速,以防碰伤;
②钢材在辊道上停止前进时,辊道应停转,以免磨伤方圆钢;
③冷床拉钢小车的划爪应调整在一条直线上,一次拉钢数量不应太多,速度不应过快,应“勤拉、慢靠”。
台架滑轨接头部分应平齐,轨面应光洁平滑,避免拉伤方圆钢。
(4)检查判断
用肉眼检查;有局部轻微的冷伤可进行修磨,较深的切除或判废。
17错牙
图3-14-1错牙
(1)缺陷特征
钢材截面上、下两部分沿对称轴互相错开一定位置而呈现的金属凸缘叫错牙。
(2)产生原因及危害
产生原因:
成品孔上下孔型未对正,相互错开一定位置。
危害:
影响外观质量,下工序易产生折迭缺陷。
(3)预防消除方法
换辊时注意使上、下孔型对正,并紧固轧机部件,防止轧辊轴向窜动。
(4)检查判断
用肉眼检查,量具测量;
按产品标准规定进行判定。
18分层(还需分析)
(1).缺陷特征
盘条纵向分成两层或更多层的缺陷称为分层。
(2).产生原因及危害
产生原因:
化学成分严重偏析,或轧制钢坯切头不尽。
危害:
有裂纹的线材极易断裂,造成报废。
(3).预防及消除办法
①加强钢坯质量检查,杜绝轧制不合格钢坯;
②合理控制剪切参数,将头部剪切干净;
(4).检查判断
用肉眼检查;
有裂纹缺陷的部位必须切除或判废。
19缩孔
盘条截面的中心部位的疏松或空洞称为缩孔。
缩孔处存在非金属夹杂,同时某些非铁元素富集。
当连铸钢坯的钢液冷缩时,在钢锭中心部位出现空洞。
连铸坯有时出现周期性的缩孔。
缩孔与内裂(由内应力产生坯、材中心部位的裂纹)不同,缩孔伴有严重的非金属夹杂,内裂是由于加工应力或热处理相变应力造成的内部裂纹,两侧及附近没有夹杂无聚集。
(三)化学成分
钢的化学成分是决定成品金相组织的基础条件。
它除了对加工工艺过程有影响(如连铸操作希望钢中Mn:
Si大于3:
1)之外,还对盘条的各项性能有重要影响。
C、Mn(Si)左右着钢的强度,韧性等基本性能。
S、P一般被认为是有害元素,其含量越低越好,往往根据S、P的含量评定钢的等级。
P固熔于铁素体,虽能增加强度,但使之脆化。
S则影响热工工艺,其化合物破坏基体的连续性。
评价既定钢种、钢号“化学成分”质量的着眼点,应是各元素含量允许波动范围和同一熔炼号实物的波动值,还有不可避免的偏析值。
化学成分除与整个生产生产技术水平有关之外,和分析取样方法有关。
应当根据客户的要求,对生产出产品进行化学成分调整。
例如:
生产制绳用的盘条的碳含量(熔炼成分)只允许5个点的波动(%—%);Mn含量允许波动值均匀为20个点。
此外对钢中的残余元素,如对高强度弹簧盘条及制绳钢丝,规定Ni、Gr含量均不得大于%,对高质量用的制绳用钢规定的元素含量的最高限量为:
%、%、%、%、%.
当连铸时残余元素往往造成严重的中心偏析,在拉丝时中心偏析会造成断裂事故。
铜、锡含量高,则在钢坯加热的强氧化气氛中沉积于表面,影响盘条质量。
钢中的氮可提高拔丝的加工硬化速率,更影响时效硬化,对拉丝不利。
因此,应当控制氮含量不得高于%。
YB4027-91和ZBH44002、44004、44005—88结合我国具体情况对盘条的化学成分作了明确的规定。
国际市场用户很重视根据合同在成品上取样,对化学成分进行核验,另外ZBH标准对供求双方发生质量争议时的取样再验,也有极为详细而又严格的规定。
成分分析允许碳含量偏差值表
碳含量范围%
平均值与熔炼成分之差不大于,%
任一试样与熔炼成分之差不大于,%
及以下
至
以上
硅、锰成品分析6个试样平均值必须符合熔炼成分要求,硅的任一试样不得比熔炼成分高出%,锰的6个试样波动范围不得大于%。
硫及磷成品分析6个试样各自的平均值必须在熔炼成分范围内,硫及磷任一元素其任一单独试样的波动值不得超出熔炼成分±%。
(四)高倍低倍检验
需要进行高倍低倍检验的项目有元素偏析、表面脱碳、夹杂、晶粒度及微观组织等。
偏析在盘条的断面上存在着元素不均匀的现象,称为偏析,常见的碳、硫、磷偏析最为严重。
偏析现象主要是钢液在冷却凝固过程中,元素在结晶与余液中分配不一致造成的。
元素的偏析程度与钢种、浇注方法、元素成分含量、浇注工艺操作有关。
钢中的碳偏析和锰偏析,对高碳钢丝来说可能是最重要的问题。
不同的炼钢工艺所产生的偏析位置不同。
连铸坯全长上断续存在着偏析,是低熔点的夹杂物沿钢坯长度不断增大和凝固形成的。
P402图
连轧坯的偏析随其断面的增大而减少。
高碳钢连铸坯的主要问题是碳、硫和锰的偏析峰在控制冷却过程中与输送机边缘局部缓慢冷却部位重合而产生的晶界自由渗碳体和偶然粗大的珠光体晶粒,不能成功地拉拔成钢丝。
特别是生产大直径的线材时,拔丝更为困难。
通过实验,发现有效控制偏析的方法是将铸造温度控制低一些。
把中间包温度控制在固相线以上2