普通车工一体化教学课程标准.docx
《普通车工一体化教学课程标准.docx》由会员分享,可在线阅读,更多相关《普通车工一体化教学课程标准.docx(12页珍藏版)》请在冰豆网上搜索。
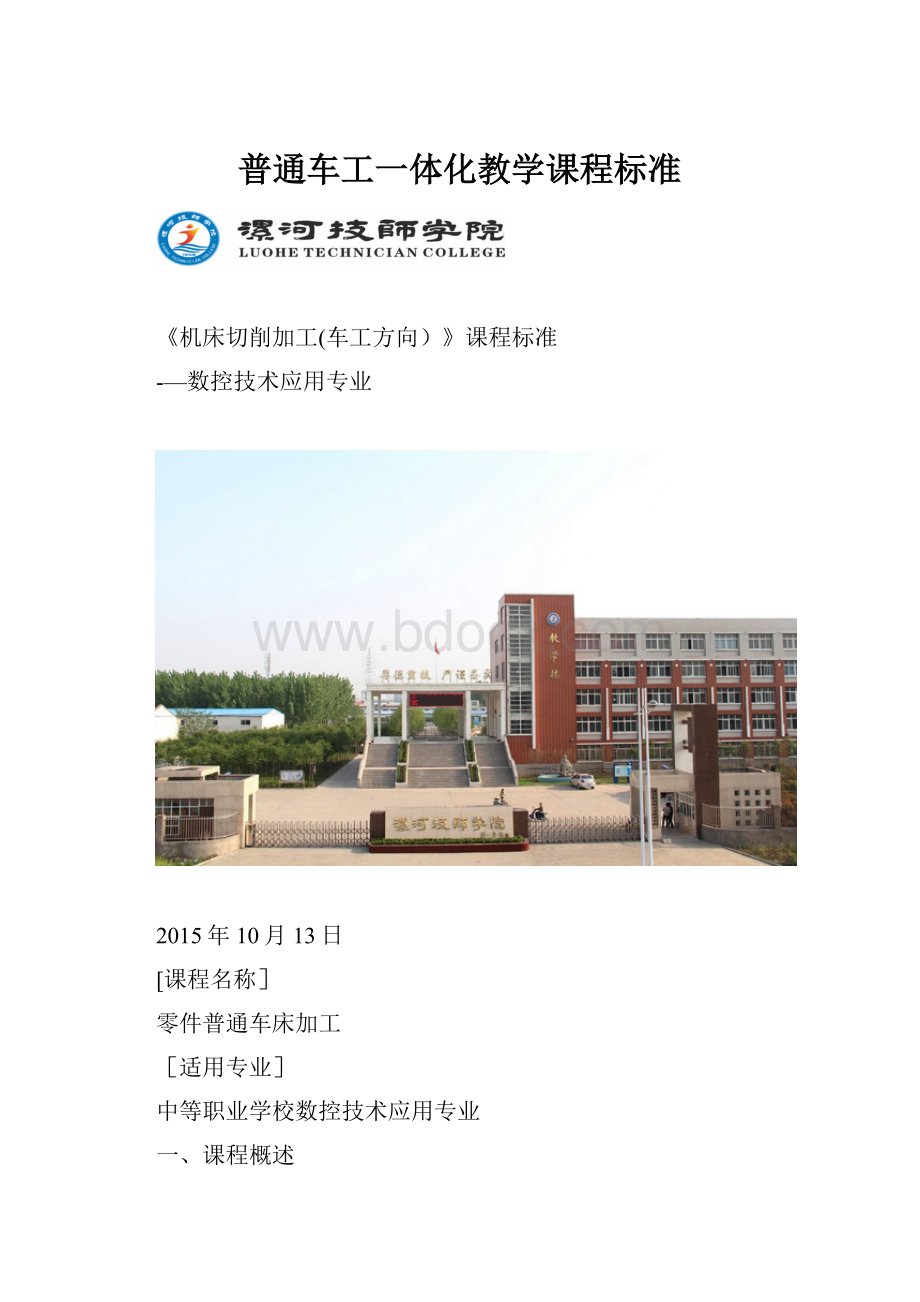
普通车工一体化教学课程标准
《机床切削加工(车工方向)》课程标准
-—数控技术应用专业
2015年10月13日
[课程名称]
零件普通车床加工
[适用专业]
中等职业学校数控技术应用专业
一、课程概述
(一)课程定位
本课程是数控技术专业的核心课程。
通过学习学生应掌握CA6140型车床的基本操作知识,刀具知识和切削用量的正确选择,工艺的合理安排,机床的切削加工等基本知识。
培养普通机床的操作和加工能力,适应机械制造企业机床操作工人员工作岗位的基本要求。
本课程在整个专业课程体系中处于综合应用的地位,在学习“机械制图”、“机械常识”、“公差配合”、“热处理”等课程的同时,学生具备工程图样分析、基本机加工能力的基础上通过本课程的学习,使学生初步具有普通车床中高级工零件的操作水平,加工能力等
(二)设计思路
凸显课程教学内容与实际工作任务的一致性。
与国内大型企业合作,在广泛调研的基础上,共设计3个工作任务,将课程教学内容与就业岗位具体工作任务联系在一起,体现课程内容的职业性和针对性.
实施“任务驱动”课程教学模式。
分析本课程特色与特点,总结出“教师布置工作任务、讲授基本知识,并演示基本技能、组织任务实施、进行考核评价、自主练习与任务巩固”五步法,按照这五个步骤完成车削加工操作的工作任务。
第一步任务导入,教师布置工作任务,学生分析工作任务;通过任务驱动的形式引入图纸设计的相关知识点,学生们分组制订加工工艺方案;在课堂上讨论工艺的优略性,在教师指导下按照最佳决策方案,在机床上实施具体的加工,在加工过程中,学生通过对实际问题的分析和解决,对问题的反思,达到每次课的训练目的。
二、课程目标
(一)专业目标
面向企业生产一线,培养熟悉企业岗位的工作流程,能按照作业规范熟练操作普通车床,完成中等复杂程度零件的加工与质量检测、设备的日常保养与维护等工作任务,具有良好的责任心和质量意识,具有职业生涯发展基础的技能人才。
(二)能力目标
1、具有较好的学习新知识和技能的能力;
2、具有较强的组织和团队协作能力;
3、具有较强的敬业精神和良好的职业道德。
4、具有较好的分析问题和解决问题的能力;
5、具备查找相关技术资料的能力。
三、教学内容与学时分配
(一)零件普通车床加工一体化课程标准
一体化课程1
零件普通车床加工
基准学时
240学时
典型任务描述
生产主管根据零件特性、加工要求以及现有工艺设备,综合考虑加工成本、稳定性等因素,确定该零件部分或全部加工部位需要使用车床加工。
该类零件的加工特性主要包括外圆、端面、沟槽、孔等,精度一般为IT8—IT10,表面粗糙度为Ra1.6—3。
2um。
。
操作者从生产主管处接受任务书签字确认,根据工艺规程文件和交接班记录,制定本岗位加工计划。
准备材料、工量夹具及机床、按机床安全操作规程、装夹刀具和工件、合理选择切削用量、切削液,按工艺和图样要求切削工件。
加工过程中要适时检测确保质量,加工完毕后规范存放零件,送检并签字确认,按照现场管理规范清理场地,归置物品、保养设备并填写保养记录,设备保养时要按照国家环保要求和企业要求处理费油液。
下班前填写交接班记录。
工作内容分析
工作与学习对象:
1.领取任务书,签字确认
2.阅读工作任务书,明确
工作任务
3.识读图样、工艺卡和检验卡,明确加工技术要求
4.确定加工工艺及切削用量
5.准备工具、量具、夹具、刃具、辅件及切削液
6.毛坯准备
7.加工前的机床准备
8.工件找正与装夹
9.对刀
10.切削工件
11.测量精度填写检验卡
12.放置零件
13.交付检验、签字确认
14.整理现场,保养机床,填写保养记录
15.填写交接班记录
设备:
普通车床
资料:
生产任务单、图样、工艺卡、安全操作规程、企业生产和管理规程、交接班记录表、切削手册等
工作方法:
1.刀具的选择方法
2.刀具的刃磨方法
3.工件装夹和找正方法
4.机床规范操作方法
5.各类零件切削方法
6.精度测量方法
7.机床的保养方法
劳动组织方式:
1.独立工作
2.从生产主管处领取任务书
3.从仓库领取工具、量具、夹具、刃具及毛坯等材料
4.向同班学生咨询
5.向老师请教
6.加工完成后,交付质检人员检测
工作要求:
1.能按企业规定穿戴劳保用品,执行劳动保护规定
2.能按工作任务书和工艺规程文件的要求,完成工件的加工
3.在工作过程中,具有一定的质量和成本意识,并遵守企业的各种规章制度
4.能阅读工作任务书,明确工时、加工数量等要求
5.能识读图样,工艺卡和检验卡、查阅相关资料并计算、明确加工技术要求
6.能根据加工工艺确定加工工步及切削用量
7.能根据加工技术要求,合理选择工具、量具、夹具、刃具、辅具及切削液
8.能规范刃磨车刀及钻头
9.能根据加工技术要求,确认毛坯
10.能按零件加工要求,完成机床准备
11.能使用机床夹具完成工件的找正与装夹
12.能根据工件的加工要求正确对刀
13.能按工艺规程切削工件,适时检测,确保精度
14.能根据切削状态调整切削用量,确保正常切削
15.加工完成后,能正确选择量具,规范测量,正确读取数据,并填写检验卡.当出现不合格品和废品时,能够进行简单的成本分析
16.能按企业规定放置零件
17.能按产品工艺和企业要求,进行产品交接
18.能按企业规定,整理现场,保养机床,填写保养
19.能按企业规定填写交接班记录
20.能按国家环保要求和企业要求处置费油液
21.能与他人进行有效沟通
课程目标
1.按照机械加工车间防护规定,正确穿戴劳保用品,严格执行安全操作规程
2.能描述车床的组成、结构、功能、指出各部件的名称和作用,并能正确规范操作车床
3.能阅读生产任务单,明确工时、加工数量等要求,说出所加工零件的用途、功能和分类
4.能查阅机床使用手册,明确机床精度、加工范围等技术参数,判别加工的可能性
5.能识读图样,明确加工内容及技术要求
6.能识别常用刀具材料,根据零件材料和形状特征,通过查阅切削手册和刀具手册合理选择刀具
7.能综合考虑零件材料、刀具材料、加工性质、机床特性等因素,查阅切削手册,确定切削三要素中的切削速度、进给量和背吃刀量
8.能根据现场条件,确定符合加工技术要求的工、量、夹具及辅件、切削液
9.能正确编制传动轴、轴套、顶尖、螺纹轴等中等复杂程度零件加工工艺,制定加工工步
10.能说明车刀角度参数的含义,表示方法及对切削性能的影响,能在刀具几何角度示意图中用规范的标示符号,标出相应角度,并在实物中判别其位置
11.能根据刀具材料选择合适的砂轮,按照规范的刃磨方法,安全地刃磨车刀及钻头
12.能根据零件图样要求,通过测量或找正、借料等手段,判断毛坯是否满足加工要求
13.能按操纵规程进行机床功能检查、加工前机床润滑、预热等准备工作
14.能根据零件的结构特性,合理选择车床夹具,装夹工件并找正
15.能规范装夹刀具,运用适当对刀方法正确对刀
16.在加工过程中,能严格按照操作规程操作车床,按制定的工艺卡和工步完成零件加工
17.能规范使用量具,在加工过程中和加工后对零件进行检测并判断加工质量
18.能采取有效措施,解决车削加工过程中遇到的积屑瘤等常见问题
19.能按车间现场管理规定,正确放置零件
20.能按产品工艺流程和车间要求,进行产品交接并确认
21.能按车间规定,整理现场,保养机床,填写保养记录
22.能按车间规定填写交接班记录
23.能按国家环保相关规定和车间要求,正确处置费油液等废弃物
24.能主动获取有效信息,展示工作成果,对学习与工作进行总结与反思,能与他人合作,进行有效沟通
学习内容
1.车削加工安全生产要求、规章制度和技术发展趋势
2.机械基础内容
3.高速钢、硬质合金等金属材料知识
4.普通车床安全用电常识
5。
车削加工常用加工工具和设备的认知、使用、保养与调整
6。
常用车刀刃磨
7.车削加工常用量具规格、用途、使用和保养方法
8。
中级工车削类零件的工艺编制
9。
车削类零件装夹顺序及加工顺序制定
10.企业6S管理制度
参考性学习任务
序号
名称
学时
1
CA6140型车床的基本操作
60
2
车削传动轴
108
3
车削轴套
72
教学实施建议
1.2人一台车床
2.可将学生进行分组,分别进行机床操作和工作页的填写
3.教学实施过程中要注重机床操作和工量具使用的规范性
4.教学实施过程中要注重强调安全操作的重要性
5.教学实施过程中要让学生养成注重环保的意识
6.要设计具有实际使用价值的工作任务,激发学生的学习兴趣
7.要加强专项技能训练,反复强化基本技能
8.人均操作机床时间不少于总学时的60%
教学考核
1.以学习任务单位进行考核评价,以学生操作规范性的工作页规范填写为主要考核点,两者结合进行考核
2.要注重基本技能熟练程度的考核
四、实施过程中的评价系统
级
姓名
学号
日期
年月日
评价
指标
评价要素
权重
等级评定
A
B
C
D
信息
检索
能有效利用网络资源、工作手册查找有效信息;能用自己的语言有条理地去解释、表述所学知识;能对查找到的信息有效转换到工作中
10%
感知
工作
是否熟悉你的工作岗位,认同工作价值;在工作中,是否获得满足感
10%
参与
状态
与教师、同学之间是否相互尊重、理解、平等;与教师、同学之间是否能够保持多向、丰富、适宜的信息交流。
10%
探究学习,自主学习不流于形式,处理好合作学习和独立思考的关系,做到有效学习;能提出有意义的问题或能发表个人见解;能按要求正确操作;能够倾听、协作分享
10%
学习
方法
工作计划、操作技能是否符合规范要求;是否获得了进一步发展的能力
10%
工作
过程
遵守管理规程,操作过程符合现场管理要求;平时上课的出勤情况和每天完成工作任务情况;善于多角度思考问题,能主动发现、提出有价值的问题
15%
思维
状态
是否能发现问题、提出问题、分析问题、解决问题、创新问题
10%
自评
反馈
按时按质完成工作任务;较好的掌握了专业知识点;具有较强的信息分析能力和理解能力;具有较为全面严谨的思维能力并能条理明晰表述成文
25%
自评等级
有益
的经
验和
做法
总结
反思
建议
班级
姓名
学号
日期
年月日
评价
指标
评价要素
权重
等级评定
A
B
C
D
他能有效利用网络资源、工作手册查找有效信息
5%
5%
他能对查找到的信息有效转换到工作中
5%
他能用自己的语言有条理地去解释、表述所学知识
他是否熟悉自己的工作岗位,认同工作价值
5%
他在工作中,是否获得满足感
5%
参与
状态
他与教师、同学之间是否相互尊重、理解、平等
5%
他与教师、同学之间是否能够保持多向、丰富、适宜的信息交流
5%
他能处理好合作学习和独立思考的关系,做到有效学习
5%
他能提出有意义的问题或能发表个人见解;能按要求正确操作;能够倾听、协作分享
5%
他积极参与,在产品加工过程中不断学习,综合运用信息技术的能力提高很大
5%
学习
方法
他的工作计划、操作技能是否符合规范要求
5%
他是否获得了进一步发展的能力
5%
工作
过程
他是否遵守管理规程,操作过程符合现场管理要求
5%
他平时上课的出勤情况和每天完成工作任务情况
5%
他是否善于多角度思考问题,能主动发现、提出有价值的问题
5%
思维
状态
他是否能发现问题、提出问题、分析问题、解决问题、创新问题
5%
自评
反馈
他能严肃认真地对待自评,并能独立完成自测试题
10%
互评等级
简要
评述
五、教学实施条件
(一)教师基本要求
从事本课程的教师应具备丰富的机加工理论知识,较强的机床操作能力,较好地课堂组织能力和掌控能力。
(二)实训条件
实训场地包括普车车间,多媒体设备,普通车床,可同时容纳50人进行实训.实训场地应具有企业真实工作氛围,生产性实训比例不低于75%.
(三)教学资源条件
1、教材的编写与使用建议
本学期《零件的普通车床加工》实施一体化教学,通过本课程的一体化学习,85%以上能完全独立的完成一般零件的加工。
2、其他教学资源
一体化教材,学生工作页,配套的课件,题库和电子教案,实际加工视频的录制。
六、建议
(一)普通车床加工操作,属于较危险工作,需强调学生自身的人身安全和设备安全意识。
(二)根据加工特点,建议加强学生的过程监控。