PLC对X62W卧式万能铣床电气控制线路的改造.docx
《PLC对X62W卧式万能铣床电气控制线路的改造.docx》由会员分享,可在线阅读,更多相关《PLC对X62W卧式万能铣床电气控制线路的改造.docx(19页珍藏版)》请在冰豆网上搜索。
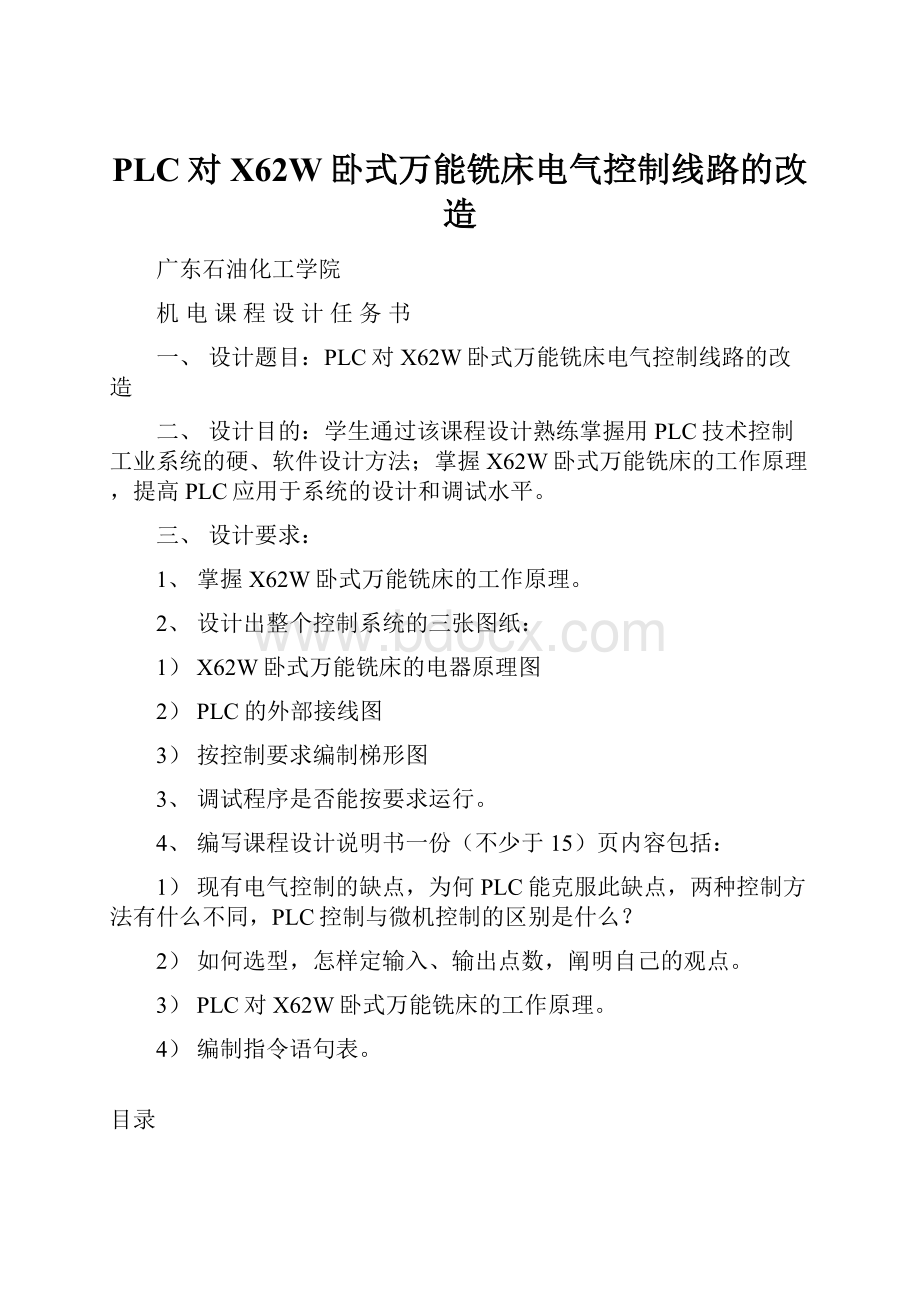
PLC对X62W卧式万能铣床电气控制线路的改造
广东石油化工学院
机电课程设计任务书
一、设计题目:
PLC对X62W卧式万能铣床电气控制线路的改造
二、设计目的:
学生通过该课程设计熟练掌握用PLC技术控制工业系统的硬、软件设计方法;掌握X62W卧式万能铣床的工作原理,提高PLC应用于系统的设计和调试水平。
三、设计要求:
1、掌握X62W卧式万能铣床的工作原理。
2、设计出整个控制系统的三张图纸:
1)X62W卧式万能铣床的电器原理图
2)PLC的外部接线图
3)按控制要求编制梯形图
3、调试程序是否能按要求运行。
4、编写课程设计说明书一份(不少于15)页内容包括:
1)现有电气控制的缺点,为何PLC能克服此缺点,两种控制方法有什么不同,PLC控制与微机控制的区别是什么?
2)如何选型,怎样定输入、输出点数,阐明自己的观点。
3)PLC对X62W卧式万能铣床的工作原理。
4)编制指令语句表。
目录
一、X62W型万能铣床简介……………………………………………………3
二、PLC对X62W型万能铣床的工作原理…………………………………4
2.1X62W型万能铣床电气控制电路概述……………………………4
2.2X62W型万能铣床的PLC控制……………………………………6
2.2.1X62W型万能铣床PLC控制输入输出点分配………………6
2.2.2X62W型万能铣床PLC控制接线图………………………7
2.2.3X62W万能铣床PLC控制梯形图…………………………8
2.2.4X62W型万能铣床PLC控制指令语句表…………………10
三、电气控制系统与PLC控制系统的区别……………………………………11
四、PLC控制与微机控制的区别……………………………………………12
五、PLC的选型以及输入、输出点数的确定…………………………………13
六、总结………………………………………………………………………19
一、X62W万能铣床的主要结构及运动形式
X62W万能铣床是一种通用的多用途机床,它可以进行平面、斜面、螺旋面及成型表面的加工,是一种较为精密的加工设备,它采用继电接触器电路实现电气控制。
其操作是通过手柄同时操作电气与机械,以达到机电紧密配合完成预定的操作,是机械与电气结构联合动作的典型控制,是自动化程度较高的组合机床。
X62W型万能铣床的外形结构如左图所示,它主要由床身、主轴、刀杆、悬梁、工作台、回转盘、横溜板、升降台、底座等几部分组成。
在床身的前面有垂直导轨,升降台可沿着它上下移动。
在升降台上面的水平导轨上,装有可在平行主轴轴线方向移动(前后移动)的溜板。
溜板上部有可转动的回转盘,工作台就在溜板上部回转盘上的导轨上作垂直于主轴轴线方向移动(左右移动)。
工作台上有T形槽用来固定工件。
这样,安装在工作台上的工件就可以在三个坐标上的六个方向调整位置或进给。
铣床主轴带动铣刀的旋转运动是主运动;铣床工作台的前后(横向)、左右(纵向)和上下(垂直)6个方向的运动是进给运动;铣床其他的运动,如工作台的旋转运动则属于辅助运动。
在电气控制系统中,故障的查找与排除是非常困难的,特别是在继电器接触式控制系统,由于电气控制线路触点多,线路复杂,故障率高,检修周期长。
而PLC却能克服这些困难。
PLC显著的特点之一就是可靠性高,抗干扰能力强。
将X62W万能铣床电气控制线路改造为可编程控制器控制,可以提高整个电气控制系统的工作性能,减少维护、维修的工作量。
二、PLC对X62W型万能铣床的工作原理
2.1.X62W型万能铣床电气控制电路概述
由电气控制原理图可知,X62W型万能铣床由三台电动机拖动,主轴电动机M1、进给电动机M2和冷却泵电动机M3。
其中,主轴电动机M1由接触器KM1和限位型转换开关QC控制,将QC扳至不同地档位即可控制主轴电动机M1的正、反转。
进给电动机M2由接触器KM3和KM4控制其正、反转。
冷却泵电动机M3由转换开关QS控制。
主轴电动机M1拖动主轴带动铣刀进行铣削加工,通过组合开关SA3来实现正反转;进给电动机M2通过操纵手柄和机械离合器的配合拖动工作台前后、左右、上下6个方向的进给运动和快速移动,其正反转由接触器KM3、KM4来实现;冷却泵电动机M3供应切削液,且当M1启动后,用手动开关QS2控制;3台电动机共用熔断器FU1作短路保护,3台电动机分别用热继电器FR1、FR2、FR3作过载保护。
(1)轴电动机M1的控制
主轴电动机M1的两地控制由启动停止按钮SB1、SB2与SB5、SB6完成。
KM1是主轴电动机启动接触器,YC1是主轴制动用的电磁离合器,SQ1是主轴变速时瞬时点动的位置开关。
①按下按钮SB1或SB2,接触器KM1通电闭合,主轴电动机M1启动运转,按下按钮SB5或SB6,主轴电动机M1制动停止。
2主轴变速盘瞬时压合行程开关ST1,接触器KM1瞬时通电闭合,主轴电动机M1瞬时启动运转,对主轴变速齿轮进行冲动。
3将换刀制动转换开关SA1扳至“换刀”位置,常开触点SA1—1接通制动电磁铁YC1电源,主轴被制动,操作人员可进行换刀操作。
(2)进给电动机M2的控制
工作台的进给运动在主轴启动后方可进行。
工作台的进给可在3个坐标的6个方向运动,进给运动是通过两个操作手柄和机械联动机构控制相应的位置开关使进给电动机M2正转或反转来实现的,并且6个方向的运动是联锁的,不能同时接通。
1将工作台纵向操作手柄扳至“向左”或“向右”位置,行程开关ST5或ST6压合,接触器KM3或KM4通电闭合,进给电动机M2启动正转或启动反转,通过机械装置带动工作台向左或向右运动。
2将工作台横向和垂直手柄扳至“向下”或“向上”位置,行程开关ST3或ST4
被压合,接触器KM3或KM4通电闭合,进给电动机M2启动正传或启动反转,通过机械装置带动工作台向下或向上运动。
3将工作台横向或垂直手柄扳至“向前”或“向后”位置,行程开关ST3或ST4
被压合,接触器KM3或KM4通电闭合,进给电动机M2启动正转或启动反转,通过机械装置带动工作台向前或向后运动。
④当进给变速盘瞬时压合行程开关ST2时,接触器KM3瞬时通电闭合,进给电动机M2瞬时启动运转,对进给变速齿轮进行冲动。
(3)按下按钮SB3或SB4,接触器KM2通电闭合,电磁铁YC2失电,YC3通电,工作台向六个进给方向快速移动。
(4)将圆工作台开关SA2扳至“接通”位置,SA2—1、SA2—3断开,SA2—2闭合,接触器KM3通电闭合,带动圆工作台工作。
(5)当需要圆形工作台旋转时,将开关SA2扳到接通位置,这时触头SA2-1和SA2-3断开,触头SA2-2闭合,电流经10—13—14—15—20—19—17—18路径,使接触器KM3得电,电动机M2启动,通过一根专用轴带动圆形工作台作旋转运动。
转换开关SA2扳到断开位置,这时触头SA2-1和SA2-3闭合,触头SA2-2断开,以保证工作台在6个方向的进给运动,因为圆形工作台的旋转运动和6个方向的进给运动也是联锁的。
2.2.X62W型万能铣床的PLC控制
2.2.1X62W型万能铣床PLC控制输入输出点分配表见下表。
X62W型万能铣床PLC控制输入输出点分配表
序号
输入器件
输入地址
序号
输出器件
输出地址
1
SB1、SB2主轴启动
X0
1
EL照明
Y0
2
SB3、SB4快速进给
X1
2
KM1主轴启动
Y1
3
SB5-1、SB6-1制动
X2
3
KM2主轴启动
Y2
4
SB5-2、SB6-2制动
X3
4
KM3M2正转
Y3
5
SA1换刀开关
X4
5
KM4M2反转
Y4
6
SA2圆工作台开关
X5
6
YC1主轴制动
Y5
7
SA4照明开关
X6
7
YC3快速进给
Y6
8
SQ1主轴冲动
X7
9
SQ2进给冲动
X10
10
SQ3-1、SQ5-1
X11
11
SQ3-2、SQ4-2
X12
12
SQ4-1、SQ6-1
X13
13
SQ5-2、SQ6-2左右进给
X14
14
FR1热保护触点
X15
15
FR2热保护触点
X16
16
FR3热保护触点
X17
2.2.2X62W型万能铣床PLC控制接线图如下所示:
2.2.3X62W万能铣床PLC控制梯形图:
2.3PLC程序设计
根据X62W万能铣床的控制要求,设计该电气控制系统的PLC控制梯形图,如图3所示。
该程序共有9条支路,反映了原继电器电路中的各种逻辑内容。
在第1支路中,因SQ1和SB5、SB6都采用常闭触头分别接至输入端子X7、X2,则X7、X2的常开触点闭合,按下启动按钮SB1或SB2时,X0常开触点闭合,Y1、M0线圈得电并自锁,第4支路中Y1常开触点闭合,辅助继电器M1线圈得电,其常开触点闭合,为第5支路以下程序执行做好准备,保证了只有主轴旋转后才有进给运动。
Y1的输出信号使主轴电动机M1启动运转。
当按停止按钮SB5或SB6时,X2常开触点复位,Y1线圈失电,主轴惯性运转,同时X3常开触点闭合,Y5线圈得电接通电磁离合器YC1,主轴制动停转。
第2支路表达了KM2及YC3的工作逻辑,当按下快速移动按钮SB3或SB4时,X1常开触点闭合,则Y2及Y6线圈得电,KM2常闭触头断开,电磁离合器YC2失电,YC3得电,工作台沿选定方向快速移动;松开SB3或SB4则YC2得电,YC3失电,快速移动停止。
第5、6、7、8支路表达了工作台六个方向的进给、进给冲动及圆工作台的工作逻辑关系。
当圆形工作台转换开关SA2动作,5、7支路中X5的常开触点分断,第7支路中X5常闭触头复位,M4及Y3线圈得电,使KM3得电,电动机M2启动,圆形工作台旋转;当SA2复位时,M4、Y3线圈失电,圆形工作台停止旋转。
左右进给时,SQ5或SQ6被压合,X14常开触点复位,第6、7支路被分断,而X11或X13常开触点闭合,M2(其常开触点使Y3线圈得电)或Y4线圈得电,电动机M2正转或反转,拖动工作台向左或向右运动。
同样,工作台上下、前后进给时,SQ3或SQ4被压合,X12常开触点复位,第6、7支路被分断,M2或Y4线圈得电,电动机M2正转或反转,拖动工作台按选定的方向(上、下、前、后中某一方向)作进给运动。
该程序及PLC的硬接线不仅保证了原电路的工作逻辑关系,而且具有各种联锁措施,电气改造的投资少、工作量较小。
2.2.4X62W型万能铣床PLC控制指令语句表如下图所示
0
LD
X0
34
MPS
1
OR
Y1
35
AND
X11
2
AND
X2
36
MPP
3
ANI
X7
37
AND
X13
4
OR
X7
38
ANI
Y3
5
ANI
X4
39
OUT
Y4
6
ANI
X15
40
LD
X5
7
ANI
X16
41
AND
X14
8
OUT
Y1
42
AND
X12
9
LD
X1
43
ANI
X10
10
ANI
X7
44
AND
M1
11
ANI
X4
45
OUT
M3
12
ANI
X15
46
LD
X10
13
ANI
X16
47
AND
X12
14
MPS
48
AND
X14
15
OUT
M0
49
ANI
X5
16
MPP
50
AND
M1
17
ANI
X17
51
OUT
M4
18
MPS
52
LD
M2
19
OUT
Y2
53
OR
M3
20
MPP
Y6
54
OR
M4
21
AND
X7
55
ANI
Y4
22
LD
X3
56
OUT
Y3
23
OR
X4
57
LD
X6
24
OUT
Y5
58
OUT
Y0
25
LD
Y1
59
END
26
OR
Y2
27
AND
M0
28
OUT
M1
29
LD
X10
30
AND
X12
31
OR
X14
32
AND
X5
33
AND
M1
三、:
PLC控制与电气控制的区别
1、PLC控制系统与电气控制系统的不同之处主要在以下几个方面:
1)从控制方法上看,电气控制系统控制逻辑采用硬件接线,利用继电气机械触点的串联或并联等组合成控制逻辑,其连线多且复杂、体积大、功耗大,系统构成后,想再改变或增加功能较为困难。
另外,继电气的触点数量有限,所以电气控制系统的灵活性和可扩展性受到很大限制。
而PLC采用了计算机技术,其控制逻辑是以程序的方式存放在存储器中,要改变控制逻辑只需改变程序,因而很容易改变或增加系统功能。
系统连线少、体积小、功耗小,而且PLC所谓“软继电气”实质上是存储器单元的状态,所以“软继电气”的触点数量是无限的,PLC系统的灵活性和可扩展性好。
2)从工作方式上看,在继电气控制电路中,当电源接通时,电路中所有继电气都处于受制约状态,即该吸合的继电气都同时吸合,不该吸合的继电气受某种条件限制而不能吸合,这种工作方式称为并行工作方式。
而PLC的用户程序是按一定顺序循环执行,所以各软继电气都处于周期性循环扫描接通中,受同一条件制约的各个继电气的动作次序决定于程序扫描顺序,这种工作方式称为串行工作方式。
3)从控制速度上看,继电气控制系统依靠机械触点的动作以实现控制,工作频率低,机械触点还会出现抖动问题。
而PLC通过程序指令控制半导体电路来实现控制的,速度快,程序指令执行时间在微秒级,且不会出现触点抖动问题。
4)从定时和计数控制上看,电气控制系统采用时间继电气的延时动作进行时间控制,时间继电气的延时时间易受环境温度和温度变化的影响,定时精度不高。
而PLC采用半导体集成电路作定时器,时钟脉冲由晶体振荡器产生,精度高,定时范围宽,用户可根据需要在程序中设定定时值,修改方便,不受环境的影响,且PLC具有计数功能,而电气控制系统一般不具备计数功能。
5)从可靠性和可维护性上看,由于电气控制系统使用了大量的机械触点,其存在机械磨损、电弧烧伤等,寿命短,系统的连线多,所以可靠性和可维护性较差。
而PLC大量的开关动作由无触点的半导体电路来完成,其寿命长、可靠性高,PLC还具有自诊断功能,能查出自身的故障,随时显示给操作人员,并能动态地监视控制程序的执行情况,为现场调试和维护提供了方便。
在电气控制系统中,故障的查找与排除是非常困难的,特别是在继电气接触式控制系统,由于电气控制线路触点多、线路复杂、故障率高、检修周期长,给生产与维护带来诸多不便,严重地影响生产。
而PLC控制系统无论是硬件还是软件,控制稳定可靠,具有极高的可靠性与灵活性,更容易维修,更能适应经常变动的工艺条件。
四、PLC与微机的区别
微型计算机是在以往计算机与大规模集成电路的基础上发展起来的,其最大特点是运算速度快,功能强,应用范围广,在科学计算,科学管理和工业控制中都得到广泛应用。
所以说,微机是通用计算机。
而PLC是一种为适应工业控制环境而设计的专用计算机。
但人工业控制的角度来看,PLC又是一种通用机,只要选配对应的模块便可适用于各种工业控制系统,而用户只需改变用户程序即可满足工业控制系统的具体控制要求。
而微机就必须根据实际需要考虑抗干扰问题及硬件软件的设计,以适应设备控制的专门需要。
1、PLC控制与微机控制的主要区别:
(1)PLC抗干扰性能为微机高
(2)PLC编程比微机编程简单
(3)PLC设计调试周期短
(4)PLC的I/0响应速度慢,有较大的滞后现象(MS),而微机的响应速度快(US)。
(5)PLC易于操作,人员培训时间短;而微机则较难人员培训时间长;
(6)PLC易于维修,微机则较困难
五、PLC的选型,及输入、输出点数的确定
1、PLC如何选型
在PLC系统设计时,首先应确定控制方案,下一步工作就是PLC工程设计选型。
工艺流程的特点和应用要求是设计选型的主要依据。
PLC及有关设备应是集成的、标准的,按照易于与工业控制系统形成一个整体,易于扩充其功能的原则选型所选用PLC应是在相关工业领域有投运业绩、成熟可靠的系统,PLC的系统硬件、软件配置及功能应与装置规模和控制要求相适应。
熟悉可编程序控制器、功能表图及有关的编程语言有利于缩短编程时间,因此,工程设计选型和估算时,应详细分析工艺过程的特点、控制要求,明确控制任务和范围确定所需的操作和动作,然后根据控制要求,估算输入输出点数、所需存储器容量、确定PLC的功能、外部设备特性等,最后选择有较高性能价格比的PLC和设计相应的控制系统。
2、确定输入、输出点数
(一)确定I/O点数
根据控制系统的要求确定所需要的I/O点数时,应再增加 10%~20%的备用量,以便随时增加控制功能。
对于一个控制对象,由于采用的控制方法不同或编程水平不同,I/O点数也应有所不同。
表2列出了典型传动设备及常用电气元件所需的开关量的I/O点数。
(二)开关量I/O
开关量I/O接口可从传感器和开关(如按钮、限位开关等)及控制设备(如指示灯、报警器、电动机起动器等)接收信号。
典型的交流输入/输出信号为24~240V,直流输入/输出信号为5~240V。
尽管输入电路因制造厂家不同而不同,但有些特性是相同的,如用于消除错误信号的抖动电路等。
此外,大多数输入电路在高压电源输入和接口电路的控制逻辑部分之间都设有可选的隔离电路。
在评估离散输出时,应考虑熔丝、瞬时浪涌保护和电源与逻辑电路间的隔离电路。
熔丝电路也许在开始时花费较多,但可能比在外部安装熔丝耗资要少。
(三)模拟量I/O
模拟量输入/输出接口一般用来感知传感器产生的信号。
这些接口可用于测量流量、温度和压力,并可用于控制电压或电流输出设备。
这些接口的典型量程为-10~+10V、0~+11V、4~20mA或10~50mA。
一些制造厂家在PLC上设计有特殊模拟接口,因而可接收低电平信号,如RTD、热电偶等。
一般来说,这类接口模块可用于接收同一模块上不同类型的热电偶或RTD混合信号。
(四)特殊功能I/O
在选择一台PLC时,用户可能会面临一些特殊类型且不能用标准I/O实现的I/O限定(如定位、快速输入、频率等)。
此时用户应当考虑供销厂商是否提供有特殊的有助于最大限度减小控制作用的模块。
有些特殊接口模块自身能处理一部分现场数据,从而使CPU从繁重的任务处理中解脱出来。
(五)智能式I/O
当前,PLC的生产厂家相继推出了一些智能式的I/O模块。
一般智能式I/O模块本身带有处理器,可对输入或输出信号作预先规定的处理,并将处理结果送入CPU或直接输出,这样可提高PLC的处理速度并节省存储器的容量。
3、存储器容量的估算
存储器容量是可编程序控制器本身能提供的硬件存储单元大小,程序容量是存储器中用户应用项目使用的存储单元的大小,因此程序容量小于存储器容量。
设计阶段,由于用户应用程序还未编制,因此,程序容量在设计阶段是未知的,需在程序调试之后才知道。
为了设计选型时能对程序容量有一定估算,通常采用存储器容量的估算来替代。
存储器内存容量的估算没有固定的公式,许多文献资料中给出了不同公式,大体上都是按数字量I/O点数的10~15倍,加上模拟I/O点数的100倍,以此数为内存的总字数(16位为一个字),另外再按此数的25%考虑余量。
4、控制功能的选择
该选择包括运算功能、控制功能、通信功能、编程功能、诊断功能和处理速度等特性的选择。
(一)运算功能
简单PLC的运算功能包括逻辑运算、计时和计数功能;普通PLC的运算功能还包括数据移位、比较等运算功能;较复杂运算功能有代数运算、数据传送等;大型PLC中还有模拟量的PID运算和其他高级运算功能。
随着开放系统的出现,目前在PLC中都已具有通信功能,有些产品具有与下位机的通信,有些产品具有与同位机或上位机的通信,有些产品还具有与工厂或企业网进行数据通信的功能。
设计选型时应从实际应用的要求出发,合理选用所需的运算功能。
大多数应用场合,只需要逻辑运算和计时计数功能,有些应用需要数据传送和比较,当用于模拟量检测和控制时,才使用代数运算,数值转换和PID运算等。
要显示数据时需要译码和编码等运算。
(二)控制功能
控制功能包括PID控制运算、前馈补偿控制运算、比值控制运算等,应根据控制要求确定。
PLC主要用于顺序逻辑控制,因此,大多数场合常采用单回路或多回路控制器解决模拟量的控制,有时也采用专用的智能输入输出单元完成所需的控制功能,提高PLC的处理速度和节省存储器容量。
例如采用PID控制单元、高速计数器、带速度补偿的模拟单元、ASC码转换单元等。
(三)通信功能
大中型PLC系统应支持多种现场总线和标准通信协议(如TCP/IP),需要时应能与工厂管理网(TCP/IP)相连接。
通信协议应符合ISO/IEEE通信标准,应是开放的通信网络。
PLC系统的通信接口应包括串行和并行通信接口(RS2232C/422A/423/485)、RIO通信口、工业以太网、常用DCS接口等;大中型PLC通信总线(含接口设备和电缆)应1:
1冗余配置,通信总线应符合国际标准,通信距离应满足装置实际要求。
PLC系统的通信网络中,上级的网络通信速率应大于1Mbps,通信负荷不大于60%。
PLC系统的通信网络主要形式有下列几种形式:
1)PC为主站,多台同型号PLC为从站,组成简易PLC网络;2)1台PLC为主站,其他同型号PLC为从站,构成主从式PLC网络;3)PLC网络通过特定网络接口连接到大型DCS中作为DCS的子网;4)专用PLC网络(各厂商的专用PLC通信网络)。
为减轻CPU通信任务,根据网络组成的实际需要,应选择具有不同通信功能的(如点对点、现场总线、工业以太网)通信处理器。
(四)编程功能
离线编程方式:
PLC和编程器公用一个CPU,编程器在编程模式时,CPU只为编程器提供服务,不对现场设备进行控制。
完成编程后,编程器切换到运行模式,CPU对现场设备进行控制,不能进行编程。
离线编程方式可降低系统成本,但使用和调试不方便。
在线编程方式:
CPU和编程器有各自的CPU,主机CPU负责现场控制,并在一个扫描周期内与编程器进行数据交换,编程器把在线编制的程序或数据发送到主机,下一扫描周期,主机就根据新收到的程序运行。
这种方式成本较高,但系统调试和操作方便,在大中型PLC中常采用。
五种标准化编程语言:
顺序功能图(SFC)、梯形图(LD)、功能模块图(FBD)三种图形化语言和语句表(IL)、结构文本(ST)两种文本语言。
选用的编程语言应遵守其标准(IEC6113123),同时,还应支持多种语言编程形式,如C,Basic等,以满足特殊控制场合的控制要求。
(五)诊断功能
PLC的诊断功能包括硬件和软件的诊断。
硬件诊断通过硬件的逻辑判断确定硬件的故障位置,软件诊断分内诊断和外诊断。
通过软件对PLC内部的性能和功能进行诊断是内诊断,通过软件对PLC的