套筒类课程设计.docx
《套筒类课程设计.docx》由会员分享,可在线阅读,更多相关《套筒类课程设计.docx(41页珍藏版)》请在冰豆网上搜索。
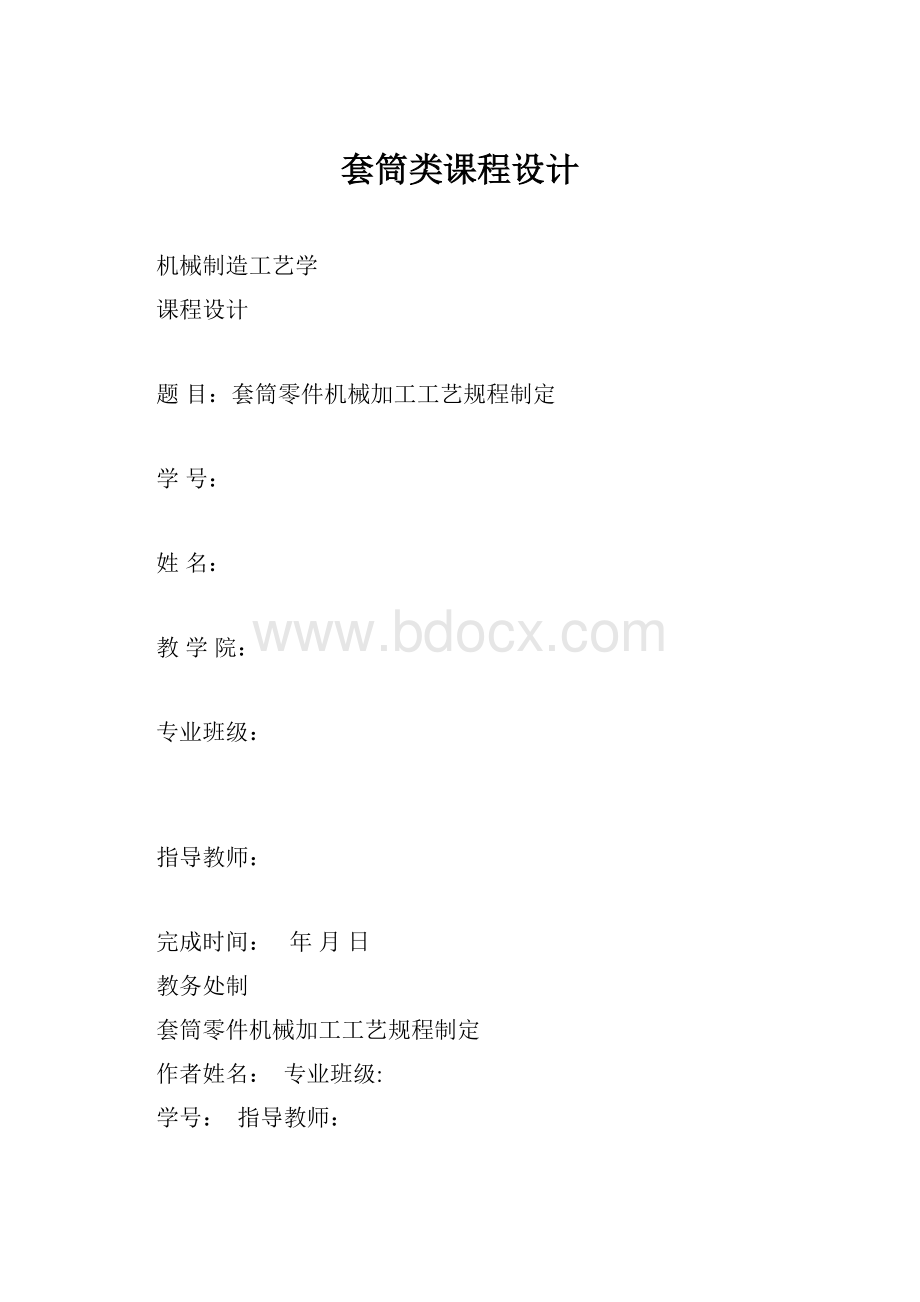
套筒类课程设计
机械制造工艺学
课程设计
题目:
套筒零件机械加工工艺规程制定
学号:
姓名:
教学院:
专业班级:
指导教师:
完成时间:
年月日
教务处制
套筒零件机械加工工艺规程制定
作者姓名:
专业班级:
学号:
指导教师:
摘要:
本文主要讲述套筒零件的加工工艺,通过开篇对零件图纸进行工艺分析,然后设计出毛坯,制定出机械加工工艺路线,分析工序尺寸与确定公差,选择加工设备,再到夹具、刀具、量具的设计,最终编制出零件的加工工艺规程,最后依照工艺规程,完成该零件的所有工序,得到合格的零件。
关键词:
套筒;工序;工艺设计;工艺路线
前言
工艺学是研究机械加工工艺技术和夹具设计为主的技术学科,具有很强的实践性,要求学习过程中应紧密联系生产实践,并具有很强的综合性。
所以开展工艺学课程设计,要求我们全面地综合运用本课程及有关课程的理论和实践知识,进行零件加工工艺规程设计和机床夹具的设计。
本次课程设计研究的题目是套筒零件机械加工工艺规程制定。
所谓套筒零件是指机械加工中经常碰到的一种零件,它的应用范围很广。
例如:
支承旋转轴的各种形式的轴承、夹具上的导向套、内燃机的气缸套以及液压系统中的油缸等。
而机械加工工艺规程,是指产品或零部件机械加工工艺过程和操作方法等的工艺文件。
工艺水平的高低以及解决各种工艺问题的方法和手段都要通过机械加工工艺规程来体现,因此机械加工工艺规程的设计至关重要。
希望能通过这次课程设计对机械制造工艺设计进行一次适应性训练,从中锻炼自己分析问题、解决问题的能力,为今后参加工作打下一个良好的基础。
由于能力有限,设计尚有许多不足之处,恳请老师给予指导与教正。
一、零件的工艺分析
1.零件图样分析
如图1-1所示为套筒零件图,下面就该零件图对其进行工艺分析、夹具设计、刀具设计等。
图1-1套筒零件图
1.1零件技术条件分析
套筒零件是机械加工中常见的一种零件,在各类机械中应用很广,主要起支承或导向作用。
如支承旋转轴的各种形式的滑动轴承、夹具上引导刀具的导向套、内燃机气缸套、液压系统中的液压缸及一般用途的套筒,由于其功用不同,套筒类零件的结构尺寸有着很大的差异,其结构的共同点是:
零件的主要表面为同轴度要求较高的内外圆表面、零件壁的厚度较薄且易变形、零件长度一般大于直径等。
1.2零件加工要求分析
(1)孔的技术要求:
孔是套筒类零件与回转轴颈、刀具或移动活塞相配合的,是起支承或导向作用的。
孔的直径尺寸公差等级为IT7,精密轴套为IT6。
形状公差在尺寸公差内,精密轴套控制在(1/2~1/3)T。
表面粗糙度值为Ra=1.6μm。
(2)外圆的技术要求:
外圆一般以过盈或过渡配合与机座或箱体上的孔相连接,它是套筒零件的支承表面。
外圆的尺寸公差等级一般为IT7~IT6,形状公差控制在外径公差范围内,表面粗糙度值为Ra=1.6μm。
(3)几何形状精度要求:
孔与外圆的同轴度当孔的终加工是在套筒装入机座后进行的,要求较低;最终加工是在装配前完成的,一般同轴度为φ0.01~φ0.05mm。
(3)位置精度要求:
端面(包括凸缘端面)若在工作中受轴向载荷或作为定位基准(基配基准),垂直度要求为0.01~0.05mm。
1.3零件的结构工艺性分析
套筒类零件的结构随其用途不同而异,本设计中的套筒零件主要由内外圆柱面、沉孔、螺纹孔等结构组成;其外圆与内孔之间的壁很薄,属于薄壁零件,在加工时容易产生变形,特别是在加工2-M12螺纹时,要更加注意避免变形。
由工艺学所学知识可知各加工位置加工方法
1)Φ160外圆、Φ96外圆:
外圆精度等级IT7~IT6,表面粗糙度值为Ra=1.6μm。
选用加方法:
粗车→半精车→精车
2)Φ780+0.02内孔、Φ650+0.03内孔:
:
公差等级为IT7,表面粗糙度值为Ra=1.6μm
选用加工方法:
粗镗→半精镗→精镗
3)2-Φ10、2-Φ13圆孔:
选用加工方法:
粗钻→扩孔→精铰
4)2-M12×1.75:
底孔Φ10.2
粗钻→攻螺纹→修研
2.确定毛坯
2.1毛坯的制造类型
零件选用材料为HT15-32,由国标GB976-1967可知其中HT表示灰铸铁,15表示抗拉强度,32表示抗弯强度。
铸件壁厚最小2.5mm,最厚为50mm。
可用于制造承受中等弯曲应力、摩擦面间压强高于500KPa的铸件。
考虑到套筒易变形,且属于薄壁零件,查《工艺手册》综合考虑,采用模锻的毛坯制造工艺。
保证材料满足零件工艺要求。
2.2毛坯的余量的确定
在保证加工质量的前提下,加工余量越小越好。
结合本设计,生产纲领为中批量生产,查《工艺手册》表2.2-4,选取加工余量值2.8mm。
长度方向选取加工余量取1.5mm,即毛坯尺寸为Φ165.6×253mm。
2.3毛坯图
3.选择定位基准
3.1粗基准的选择
粗基准选择原则:
(1)如果必须首先保证工件上加工表面与不加工表面之间的位置要求,应以不加工表面作为粗基准。
如果在工件上有很多不需加工的表面,则应以其中与加工面的位置精度要求较高的表面作粗基准。
(2)如果必须首先保证工件某重要表面的加工余量均匀,应选择该表面作粗基准。
(3)如满保证各加工表面都有足够的加工余量,应选加工余量较小的表面作粗基准。
(4)选作粗基准的表面应平整,没有浇口、冒口、飞边等缺陷,以便定位可靠。
(5)粗基准一般只能使用一次,特别是主要定位基准,以免产生较大的位置误差。
综上所述,在本零件的加工中,粗车时以左右端面为粗基准面,以保证加工尺寸和满足定位要求。
3.2精基准的选择
精基准的选择原则:
(1)用设计基准作为定位基准,实现“基准重合”,以免产生基准不重合误差。
(2)当工件以某一组精基准定位可以较方便地加工很多表面时,应尽可能采用此组精基准定位,实现“基准统一”,以免产生基准转换误差。
(3)当精加工或光整加工工序要求加工余量尽量小面均匀时,应选择加工表面本身作为精基准,即遵循“自为基准”原则。
该加工表面与其他表面间的位置精度要求由先行工序保证。
(4)为获得均匀的加工余量或较高的位置精度,可遵循“互为基准”、反复加工的原则。
(5)有多种方案可供选择时应选择定位准确、稳定、夹紧可靠,可使夹具结构简单的表面作为精基准。
综上所述,在本零件加工过程中,以粗车后的端面为基准面,以保证遵循精基准选用原则和加工精度。
4.拟定工艺路线
4.1拟定加工路线
制定工艺路线的出发点,应当是使零件的几何形状、尺寸精度以及位置精度等技术要求能得到合理的保证。
在生产纲领为中批量生产的条件下,应采用通用机床配合专用夹具,并使工序集中来提高生产率,还应适当考虑经济效果。
综合考虑各因素下,现制定两条加工加工路线如下:
方案一:
I.制造毛坯
II.热处理正火
III.车夹紧右端毛坯外圆,粗车左端面,左端外圆
IV.车夹紧左端毛坯外圆,粗车右端外圆、端面
V.镗夹左端外圆,粗镗右端内孔
VI.镗撑右端内孔,粗镗左端内孔
VII.车撑右端内孔,半精车后精车左端端面、Φ160外圆
VIII.车撑左端内孔,半精车后精车右端端面、Φ96外圆
IX.镗撑左端内孔半精镗右端内孔,精镗右端内孔
X.镗撑右端内孔半精镗左端内孔,精镗左端内孔
XI.钳在Φ160外圆上划4个圆周孔的中心,并钻中心孔
XII.钻钻2-Φ13、2-Φ10孔,锪2-Φ20沉孔
XIII.钻钻2-M12螺纹底孔(底孔Φ10.2mm)
XIV.攻攻2-M12螺纹
XV.钳去毛刺
XVI.检检验
XVII.入库
方案二:
I.制造毛坯
II.热处理正火
III.车夹紧右端毛坯外圆,粗车、半精车左端面,左端外圆,
IV.车夹紧左端外圆,粗车、半精车右端端面,右端外圆。
V.车夹右端外圆,粗镗、半精镗、精镗左端内孔
VI.车撑左端内孔,粗镗、半精镗、精镗右端内孔
VII.钳在Φ160外圆上划4个圆周孔的中心,并钻中心孔
VIII.钻钻2-Φ13、2-Φ10孔,锪2-Φ20沉孔
IX.钻钻2-M12螺纹底孔(底孔Φ10.2mm)
X.攻攻2-M12螺纹
XI.钳去毛刺
XII.车夹紧右端外圆,精车左端外圆,Φ96外圆左端面。
XIII.车撑内孔,精车右端外圆,Φ160外圆右端面。
XIV.检检验
XV.入库
综合分析:
比较方案一与方案二,方案一中半精加工与精加工同时进行,进行了工序集中处理,但是再精加工后还需要加工圆孔与螺纹。
很有可能破坏工件的形状精度和位置精度,并且整个过程中需要进行多次装夹,较为麻烦。
而方案二中将单边工序放入一道工序中,减少了装夹次数,并安排精加工工序在钻孔与攻螺纹工序之后,保证了工件的形状与位置精度要求。
而方案二的工序数目也比方案一少,对于提高生产效率有很大作用。
综合分析来看,可以选择第二道工序作为工艺路线。
4.2确定工序尺寸和工序余量
a)加工外圆(Φ96、Φ160)
外圆的尺寸公差等级为IT7~IT6之间,参考《工业手册》表2.3-2,粗车后留给半精车余量1.3mm,参考《工业手册》表2.3-3,半精车留给精车余量0.1mm.则粗车尺寸为1.4mm。
b)加工孔(Φ650+0.03、Φ780+0.02)
孔的直径尺寸公差等级为IT7,参考《工业手册》表2.3-8,粗镗余量0.5mm,半精镗余量0.2mm,精镗0.1mm。
c)钻2-Φ10、2-Φ13孔
参考《工业手册》表2.3-9选取加工余量0.2mm。
二、零件的加工
1.拟定工艺路线
I.制造毛坯
II.热处理正火
III.车夹紧右端毛坯外圆,粗车、半精车左端面,左端外圆,
IV.车夹紧左端外圆,粗车、半精车右端端面,右端外圆。
V.车夹右端外圆,粗镗、半精镗、精镗左端内孔
VI.车撑左端内孔,粗镗、半精镗、精镗右端内孔
VII.钳在Φ160外圆上划4个圆周孔的中心,并钻中心孔
VIII.钻钻2-Φ13、2-Φ10孔,锪2-Φ20沉孔
IX.钻钻2-M12螺纹底孔(底孔Φ10.2mm)
X.攻攻2-M12螺纹
XI.钳去毛刺
XII.车夹紧右端外圆,精车左端外圆,Φ96外圆左端面。
XIII.车撑内孔,精车右端外圆,Φ160外圆右端面。
XIV.检检验
XV.入库
2.确定加工尺寸和切削用量
2.1工序III.
工序包括加工粗车、半精车左端面,左端外圆。
(1)加工条件
工件材料:
材料为HT15-32,正火处理,Rm=100GPa
加工要求:
粗车、半精车Φ160外圆,左端面
机床:
普通车床CA6140
刀具:
刀片材料YT15查询车床说明书中心高205mm,则刀杆尺寸20X30mm,考虑材料特性则kr=90o,γ0=12oα0=8orε=0.5mm
(2)计算切削用量
A.粗车、半精车左端面
已知长度方向加工余量1.5mm,则粗车最大加工余量可按Zmax=1mm,半精车余量0.3mm.
●进给量f0
根据《切削用量简明第3版》(以下简称《切削手册》)中表1-4,当刀杆尺寸为20X30mm,ap≤3,以及工件直径100mm,
f=0.9~1.3mm/r
查询CA6140车床说明书(《切削手册》)中表1-31取
f=0.91mm/r
●计算切削速度
Vc=
kvm/min
其中,Cv=158,xv=0.15,yv=0.40,m=0.2,修正系数kv可由《切削手册》(寿命选T=60min)查的kv=1
则有
Vc=
X1=61.354m/min
●确定机床主轴转速
ns=
=
=122.042r/min
按机床说明书,与该转速相近的机床转速度有125r/min和100r/min,现选取125r/min,则实际切削速度为62.83m/min
●切削工时按《工艺手册》表6-2.1中的公式计算
Tm=1.441min
B.粗车、半精车外圆
粗车余量1.1mm,半精车余量1.3mm
●切削深度粗车1.1mm、半精车1.3mm
●进给量f根据《切削手册》选取f=0.9mm/r
●计算切削速度由《切削手册》可知
Vc=
kvm/min
=
X1=61.63m/min
●主轴转速
ns=
=
=122.61r/min
按机床说明书,与该转速相近的机床转速度有125r/min和100r/min,现选取125r/min,则实际切削速度为62.83m/min
●切削工时按《工艺手册》表6-2.1中的公式计算
Tm=1.441min
2.2工序IV
工序包括粗车、半精车右端端面,右端外圆
(1)粗车、半精车右端端面
已知长度方向加工余量1.5mm,则粗车最大加工余量可按Zmax=1mm,半精车余量0.3mm.
●进给量f0
根据《切削用量简明第3版》(以下简称《切削手册》)中表1-4,当刀杆尺寸为20X30mm,ap≤3,以及工件直径100mm,
f=0.9~1.3mm/r
查询CA6140车床说明书(《切削手册》)中表1-31)取
f=0.91mm/r
●计算切削速度
Vc=
kvm/min
其中,Cv=158,xv=0.15,yv=0.40,m=0.2,修正系数kv可由《切削手册》(寿命选T=60min)查的kv=1
则有
Vc=
X1=61.354m/min
●确定机床主轴转速
ns=
=
=203.4r/min
按机床说明书,与该转速相近的机床转速度有250r/min和200r/min,现选取200r/min,则实际切削速度为60.31m/min
●切削工时按《工艺手册》表6-2.1中的公式计算
Tm=1.386min
2.3工序V
工序包括粗镗、半精镗、精镗左端内孔
镗孔至Φ64.5,单边余量Z=0.5,一次镗完,ap=0.5mm
●进给量
由《切削手册》表2.7,当铸铁的Rm<200HBS,当d=30mm时,进给量f=0.9~1.1mm/r.由于本零件在加工Ф30mm孔时属于低刚度零件,故进给量应乘以系数0.75,则
f=(0.9~1.1)
mm/r=0.675~0.825mm/r
根据Z575机床说明书,现取0.70mm/r
●切削速度:
根据《切削手册》表2.15,查得切削速度为V=21m/min,所以
按机床说明书(见《工艺手册》表4.2-15),与
相近的机床转速为251
到354
现取n=251
。
所以实际的切削速度为:
根据表2.29可知钻孔的入切量及超切量
=11mm,
=70mm,所以切削工时
根据表2.29可知钻孔的入切量及超切量
=11mm,
=150mm,因为钻孔深度等于直径的5倍,所以根据《切削手册》表2.7可知进给量要乘以0.9,所以进给量f=0.7
0.9=0.63mm/r
●切削工时
2.4工序VI
工序包括粗镗、半精镗、精镗右端内孔
扩孔Ф60mm,利用Ф60mm的钻头对Ф30mm的孔进行扩孔钻,根据有关手册的规定,扩钻的切削用量可根据钻孔的切削用量选取,根据《切削手册》2.7可选:
f=1.2mm/r
切削速度:
根据《切削手册》表2.15,查得切削速度为V=17m/min,
按机床说明书(见《工艺手册》表4.2-15),现取n=64
。
所以实际的切削速度为:
根据表2.29可知钻孔的入切量及超切量
=21mm,
=70mm,所以切削工时
根据表2.29可知钻孔的入切量及超切量
=21mm,
=150mm,所以切削工时
2.5工序VII
工序包括钻2-Φ13、2-Φ10孔,锪2-Φ20沉孔
采用刀具:
Ф65mm专用扩孔钻
进给量f=2mm/r
机床主轴转速取68r/min,查得切削速度为V=8.23m/min,
采用刀具:
Ф78mm专用扩孔钻
进给量f=2.2mm/r
机床主轴转速取88r/min,
2.5工序IX
工序包括钻2-M12螺纹底孔
2.8工序X.
工序包括攻2-M12螺纹
1钻2-M12螺纹底孔φ10.1
根据《实用切削加工速查手册》中表7-12,可知Vc=21。
根据表7-12,可知f=0.14,所以
3.工序卡片(见附件)
四、结论
通过这段时间的机械设计课程设计进一步巩固、加深和拓宽所学的知识;通过设计实践,树立了正确的设计思想,增强创新意思和竞争意识,熟悉掌握了机械设计的一般规律,也培养了分析和解决问题的能力;通过设计计算、绘图以及对运用技术标准、规范、设计手册等相关设计资料的查阅,对自己进行了一个全面的机械设计基本技能的训练。
在具体做的过程中,从设计到计算,从分析到绘图,让我更进一步的明白了作为一个设计人员要有清晰的头脑和整体的布局,要有严谨的态度和不厌其烦的细心,要有精益求精、追求完美的一种精神。
现在把这个课程做完了才发现自己对以前学的知识点有了更好的理解,知识只有放在实践运用上才能体现他的价值才能更好地被大家接受,所以这门实践课的开设是非常好的,要去认认真真完成的在这个过程中,要谢谢老师对我的教导,让我过这次课程设计对机械制造工艺设计进行一次适应性训练,从中锻炼自己分析问题、解决问题的能力,为今后参加工作打下一个良好的基础。
参考文献
[1]刘华明.金属切削刀具设计简明手册[M].机械工业出版社,1994.陈宏钧.实用金属切削手册[M].机械工业出版社,2005
[2]哈尔滨工业大学,赵家齐.机械制造工艺学课程设计指导书[M].机械工业,1994.
[3]齐世恩.机械制造工艺学[M].哈尔滨工业大学出版社,1989.
[4]王绍俊.机械制造工艺设计手册[M].机械工业出版社,1985.
[5]艾兴,肖诗纲.切削用量简明手册,第3版[M]//切削用量简明手册(第3版).1966.
[6]吴宗泽.机械设计课程设计手册[M].高等教育出版社,2012.
[7]黄靖远,龚剑霞.机械设计学[M].机械工业出版社,1999.
[8]吴宗泽.高等机械设计[M].清华大学出版社,1991.
[9]唐保宁,高学满.模具设计与制造简明手册[M].上海科学技术出版社,1985.
[10]张策.机械原理与机械设计[M].机械工业出版社,2004.
[11]李秋娟,张兵.论CAD在机械设计中的应用及机械制造技术的新发展[J].化学工程与装备,2010(3):
140-141.
[12]蔡春源.新编机械设计手册[M].辽宁科学技术出版社,1993.
[13]徐灏.新编机械设计师手册[M].机械工业出版社,1995.
[14]王杰,程明远,李士晓.浅谈机械设计加工中应注意的几个问题[J].科技信息,2011(11):
96-97.
[15]楼鸿棣,邹慧君.高等机械原理[M].高等教育出版社,1990.
[16]姜书金.机械原理与机械零件[M].高等教育出版社,1988.
[17]胡凤兰,姚俊红,齐新丹.互换性与技术测量基础[M].高等教育出版社,2010.
[18]赵阳.机械制造工艺与设备[J].科技经济导刊,2017(17):
82.
[19]吴拓.机械制造工艺与机床夹具[M].机械工业出版社,2006.
[20]胡永生.机械制造工艺原理[M].北京理工大学出版社,1992.
[21]沈建峰.数控车床编程与操作实训[M].国防工业出版社,2005.
[22]陈宏钧,马素敏.车工操作技能手册[M].机械工业出版社,2000.
[23]李玉平.机械加工误差的综合分析及控制研究[J].新余学院学报,2019(3).
[24]上海市汽车运输公司322编.机械加工工艺[M].上海科技情报研究所,1971.
[25]孟华峰.机械加工工艺技术与误差分析[J].煤炭技术,2011,30(8):
18-19.
机械加工工艺过程卡片
产品型号
零件图号
产品名称
零件名称
套筒
共2页
第1页
材料牌号
HT15-32
毛坯种类
铸铁
毛坯外形尺寸
Φ165.6×253mm
每毛坯件数
每台件数
备注
工序
号
工名
序称
工序内容
车
间
工
段
设备
工艺装备
工时
准终
单件
I
铸造
制造毛坯
II
热处理
正火
III
车
夹紧右端毛坯外圆,粗车左端面,左端外圆
普车
三爪卡盘
IV
车
夹紧左端外圆,粗车右端端面,右端外圆
普车
三爪卡盘
V
车
夹右端外圆,粗镗、半精镗、精镗左端内孔
普车
三爪卡盘
VI
车
撑左端内孔,粗镗、半精镗、精镗右端内孔
普车
三爪卡盘
VII
钳
在Φ160外圆上划4个圆周孔的中心,并钻中心孔
VIII
钻
钻2-Φ13、2-Φ10孔,锪2-Φ20沉孔
钻床
组合钻夹具
IX
钻
钻2-M12螺纹底孔(底孔Φ10.2mm)
钻床
专用钻夹具
X
攻
攻2-M12螺纹
攻丝机
设计(日期)
校对(日期)
审核(日期)
标准化(日期)
会签(日期)
标记
处数
更改文件号
签字
日期
标记
处数
更改文件号
签字
日期
机械加工工艺过程卡片
产品型号
零件图号
产品名称
零件名称
套筒
共2页
第1页
材料牌号
HT15-32
毛坯种类
铸铁
毛坯外形尺寸
Φ165.6×253mm
每毛坯件数
每台件数
备注
工序
号
工名
序称
工序内容
车
间
工
段
设备
工艺装备
工时
准终
单件
XI
钳
去毛刺
XII
车
夹紧右端外圆,半精车、精车左端外圆,Φ96外圆左端面
XIII
车
撑内孔,半精车、精车右端外圆,Φ160外圆右端面
XIV
检
检验
XV
入库
设计(日期)
校对(日期)
审核(日期)
标准化(日期)
会签(日期)
标记
处数
更改文件号
签字
日期