浇口的设计.docx
《浇口的设计.docx》由会员分享,可在线阅读,更多相关《浇口的设计.docx(25页珍藏版)》请在冰豆网上搜索。
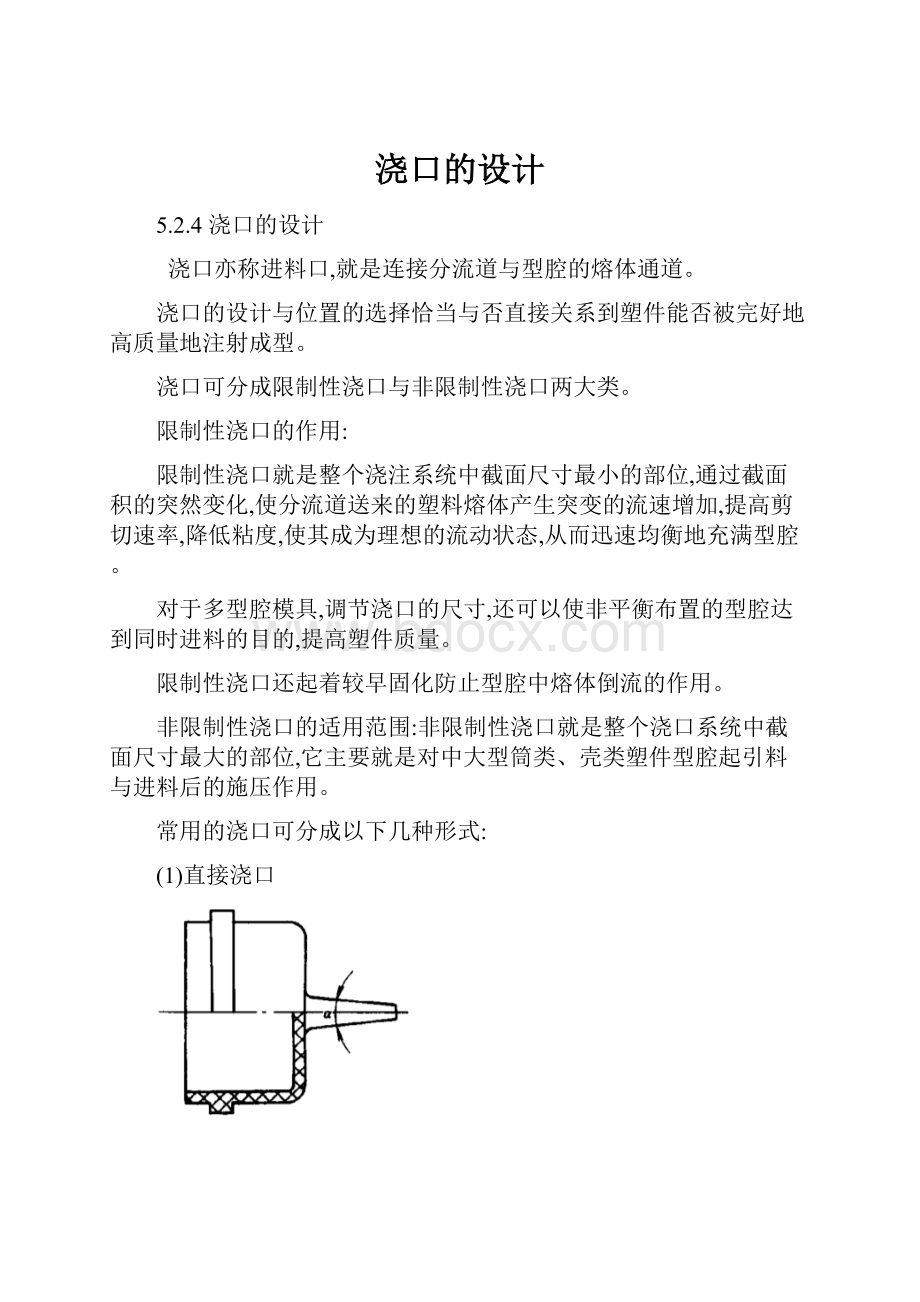
浇口的设计
5.2.4浇口的设计
浇口亦称进料口,就是连接分流道与型腔的熔体通道。
浇口的设计与位置的选择恰当与否直接关系到塑件能否被完好地高质量地注射成型。
浇口可分成限制性浇口与非限制性浇口两大类。
限制性浇口的作用:
限制性浇口就是整个浇注系统中截面尺寸最小的部位,通过截面积的突然变化,使分流道送来的塑料熔体产生突变的流速增加,提高剪切速率,降低粘度,使其成为理想的流动状态,从而迅速均衡地充满型腔。
对于多型腔模具,调节浇口的尺寸,还可以使非平衡布置的型腔达到同时进料的目的,提高塑件质量。
限制性浇口还起着较早固化防止型腔中熔体倒流的作用。
非限制性浇口的适用范围:
非限制性浇口就是整个浇口系统中截面尺寸最大的部位,它主要就是对中大型筒类、壳类塑件型腔起引料与进料后的施压作用。
常用的浇口可分成以下几种形式:
(1)直接浇口
直接浇口又称主流道型浇口,它属于非限制性型浇口,如图5、18所示。
塑料熔体由主流道的大端直接进入型腔,因而具有流动阻力小、流动路程短及补缩时间长等特点。
由于注射压力直接作用在塑件上,故容易在进料处产生较大的残余应力而导致塑件翘曲变形。
这种形式的浇口截面大,去除浇口较困难,去除后会留有较大的浇口痕迹,影响塑件的美观。
这类浇口大多用于注射成型大、中型长流程深型腔筒形或壳形塑件,尤其适合于如聚碳酸脂、聚砜等高粘度塑料。
另外,这种形式的浇口只适于单型腔模具。
在设计直接浇口时,为了减小与塑件接触处的浇口面积,防止该处产生缩孔、变形等缺陷,一方面应尽量选用较小锥度的主流道锥角α(α=2°~4°),另一方面尽量减小定模板与定模座板的厚度。
直接浇口的浇注系统有着良好的熔体流动状态,塑料熔体从型腔底面中心部位流向分型面,有利于消除深型腔处气体不易排出的缺点,使排气通畅。
这样的浇口形式,使塑件与浇注系统在分型面上的投影面积最小,模具结构紧凑,注射机受力均匀。
(2)中心浇口
当筒类或壳类塑件的底部中心或接近于中心部位有通孔时,内浇口就开设在该孔口处,同时中心设置分流锥,这种类型的浇口称中心浇口,如图5、19所示。
中心浇口实际上就是直接浇口的一种特殊形式,它具有直接浇口的一系列的优点,而克服了直接浇口易产生的缩孔、变形等缺陷。
中心浇口其实也就是端面进料的环形浇口(下面介绍)。
图5、19中心浇口的形式
在设计时,环形的厚度一般不小于0、5mm。
当进料口环形的面积大于主流道小端面积时,浇口为非限制性型浇口;反之,则浇口为限制性型浇口。
(3)侧浇口
侧浇口国外称为标准浇口,如图5、20所示。
侧浇口一般开设在分型面上,塑料熔体从内侧或外侧充填模具型腔,其截面形状多为矩形(扁槽),改变浇口的宽度与厚度可以调节熔体的剪切速率及浇口的冻结时间。
这类浇口可以根据塑件的形状特征选择其位置,加工与修整方便,因此它就是应用较广泛的一种浇口形式,普遍用于中小型塑件的多型腔模具,且对各种塑料的成型适应性均较强。
由于浇口截面小,减少了浇注系统塑料的消耗量,同时去除浇口容易,且不留明显痕迹。
但这种浇口成型的塑件往往有熔接痕存在,且注射压力损失较大,对深型腔塑件排气不利。
图5、20a为分流道、浇口与塑件在分型面同一侧的形式;图5、20b为分流道与浇口与塑件在分型面两侧的形式,浇口搭接在塑件上;图5、20c为分流道与浇口与塑件在分型面两侧的形式,浇口搭接在分流道上。
有搭接形式的侧浇口就是塑件端面进料的侧浇口。
设计时选择侧向进料还就是端面进料,要根据塑件的使用要求而定。
侧浇口尺寸计算的经验公式如下:
(5、8)
t=(0、6—0、9)*δ(5、9)
式中b——侧浇口的宽度,mm;
A——塑件的外侧表面积,mm2;
t——侧浇口的厚度;
δ——浇口处塑件的壁厚,mm。
推荐尺寸:
侧向进料的侧浇口(见图5、20a),对于中小型塑件,一般深度t=0、5~2、0mm(或取塑件壁厚的1/3~2/3),宽度b=1、5~5、0mm,浇口的长度L=0、7~2、0mm;端面进料的搭接式侧浇口(见图5、20b),搭接部分的长度L1=(0、6~0、9)+b/2mm,浇口长度l可适当加长,取L=2、0~3、0mm;侧面进料的搭接式浇口(见图5、20c),其浇口长度选择可参考端面进料的搭接式侧浇口。
侧浇口有两种变异的形式,即为扇形浇口与平缝浇口,下面分别介绍。
1)扇形浇口扇形浇口就是一种沿浇口方向宽度逐渐增加厚度逐渐减小的呈扇形的侧浇口,如图5、21所示,常用于扁平而较薄的塑件,如盖板、标卡与托盘类等。
通常在与型腔接合处形成长L=1~1.3mm厚t=0、25~1.0mm的进料口,进料口的宽度b视塑件大小而定,一般取6mm浇口处型腔宽度的1/4,整个扇形的长度L可取6mm左右,塑料熔体通过它进入型腔。
采用扇形浇口,使塑料熔体在宽度方向上的流动得到更均匀的分配,塑件的内应力因之较小,还可避免流纹及定向效应所带来的不良影响,减少带人空气的可能性,但浇口痕迹较明显。
图5、21扇形浇口的形式图5、22平缝浇口的形式
2)平缝浇口平缝浇口又称薄片浇口,如图5、22所示。
这类浇口宽度很大,厚度很小,几何上成为一条窄缝,与特别开设的平行流道相连。
通过平行流道与窄缝浇口熔体得到均匀分配,以较低的线速度平稳均匀地流入型腔,降低了塑件的内应力,减少了因取向而造成的翘曲变形。
这类浇口的宽度b一般取塑件长度的25%~100%,厚度t=0、2~1.5mm,长度L=1、2~1.5mm。
这类浇口主要用来成型面积较少尺寸较大的扁平塑件,但浇口的去除比扇形浇口更困难,浇口在塑件上的痕迹也更明显。
(4)环形浇口
对型腔充填采用圆环形进料形式的浇口称环形浇口,如图5、23所示。
环形浇口的特点就是进料均匀,圆周上各处流速大致相等,熔体流动状态好,型腔中的空气容易排出,熔接痕可基本避免。
图5、23a所示为内侧进料的环形浇口,浇口设计在型芯上,浇口的厚度t=0、25—1、6mm,长度L=0、8—1、8mm;图5、23b所示为端面进料的搭接式环形浇口,搭接长度L,=0、8—1、2mmm,总长L可取2—3mm;图5、23e为外侧进料的环形浇口,其浇口尺寸可参考内侧进料的环形浇口。
实际上,前述的中心浇口也就是一种端面进料的环形浇口。
环形浇口主要用于成型圆筒形无底塑件,但浇注系统耗料较多,浇口去除较难,浇口痕迹明显。
图5、23环形浇口的形式
(5)轮幅式浇口
轮幅式浇口就是在环形浇口基础上改进而成,由原来的圆周进料改为数小段圆弧进料,浇口尺寸与侧浇口类似,如图5、24所示。
这种形式的浇口耗料比环形浇口少得多,且去除浇口容易。
这类浇口在生产中比环形浇口应用广泛,多用于底部有大孔的圆筒形或壳型塑件。
轮幅浇口的缺点就是增加了熔接痕,这会影响塑件的强度。
图5、24轮幅式浇口的形式
(6)爪形浇口
爪形浇口如图5、25所示,它可在型芯的头部开设流道,如图5、25a所示,也可在主流道下端开设,如图5、25b所示。
爪形浇口加工较困难,通常用电火花成型。
型芯可用作分流锥,其头部与主流道有自动定心的作用(型芯头部有一段与主流道下端大小—致),从而避免了塑件弯曲变形或同轴度差等成型缺陷。
爪形浇口的缺点与轮幅式浇口类似,主要适用于成型内孔较小且同轴度要求较高的细长管状塑件。
图5、25爪形浇口的形式
(7)点浇口
点浇口又称针点浇口或菱形浇口,就是一种截面尺寸很小的浇口,俗称小浇口,如图5、26所示。
这种浇口由于前后两端存在较人的压力差,可较大程度地增大塑料熔体的剪切速率并产生较大的剪切热,从而导致熔体的表观粘度下降,流动性增加,有利于型腔的充填,因而对于薄壁塑件以及诸如聚乙烯、聚丙烯等表观粘度随剪切速率变化敏感的塑料成型有利,但不利于成型流动性差及热敏性塑料,也不利于成型平薄易变形及形状非常复杂的塑件。
点浇口的设计形式有许多种。
图5、26a所示为直接式,直径为d的圆锥形的小端直接与塑件相连。
图5、26b所示为点浇口的另一种形式,圆锥形的小端有一端直径为d,长度为L的浇口与塑件相连,但这种形式的浇口直径d不能太小,浇口长度J不能太长,否则脱模时浇口凝料会断裂而堵塞住浇口,影响注射的正常进行。
上述两种形式点浇口制造方便,但去除浇口时容易损伤塑件,浇口也容易磨损,仅适于批量不大的塑件成型与流动性好的塑料。
图5、26c所示为圆锥形小端带有圆角的形式,其截面积相应增大,塑料冷却减慢,注射过程中型芯受到的冲击力要小些,但加工不如上述两种方便。
图5、26d所示为点浇口底部增加一个小凸台的形式,其作用就是保证脱模时浇口断裂在凸台小端处,使塑件表面不受损伤,但塑件表面遗留有高起的凸台,影响其表面质量,为了防止这种缺陷,可在设计时让小凸台低于塑件的表面。
图5、26e就是适用于一模多件或一个较大塑件多个点浇口的形式。
点浇口的各种尺寸如图5、26所示,d=0、5—1.5mm,最大不超过2mm,L=0、5—2mm,
常取1、0—1、5mm,L0=0、5—1、5mm,L1=1、0—2、5mm,α=6°—15°,β=60°—90°。
点浇口的直径也可以用下面的经验公式计算:
(5、10)
式中d——点浇口直径,mm;
δ——塑件在浇口处的壁厚,mm;
A——型腔表面积,mm2。
*采用点浇口进料的浇注系统,在定模部分必须增加一个分形面,
用于取出浇注系统的凝料,因此会增加模具的复杂性。
图5、26点浇口的各种形式
(8)潜伏浇口
潜伏浇口又称减切浇口,由点浇口变异而来。
这种浇口的分流道位于模具的分形面上,而浇口却斜向开设在模具的隐蔽处。
塑料熔体通过型腔的侧面或推杆的端部注入型腔,因而塑件外表面不受损伤,不致因浇口痕迹而影响塑见的表面质量与美观效果。
潜伏浇口的形式如图5、27所示。
图5、27a所示为浇口开设在定模部分的形式;
图5、27b所示为浇口开设在动模部分的形式;
图5、27c所示为潜伏浇口开设在推杆的上部而进料口在推杆上端的形式。
潜伏浇口一般就是圆形截面,其尺寸设计可参考点浇口。
潜伏浇口的锥角B取10°~20°,倾斜角A为42°~45°,推杆上进料口宽度为0、8~2mm,具体数值大小应视塑件大小而定。
由于浇口与型腔相连时有一定角度,形成了能切断浇口的刃口,这一刃口在脱模或分型时形成的剪切力可将浇口自动切断,不过,对于较强韧的塑料则不宜采用。
图5、27潜伏浇口的形式
由上所述,不同的浇口形式对塑料熔体的充填特性、成型质量及塑件的性能会产生不同的影响。
各种塑料因其性能的差异而对不同形式的浇口会有不同的适应性,设计模具时可参考表5、2所列部分塑料所适应的浇口形式。
表5、2常用塑料所适应的浇口形式
浇口形式
塑料种类
直接浇口
侧浇口
平缝浇口
点浇口
潜伏浇口
环形浇口
硬聚氯乙烯(PVC)
0
O
聚乙烯(PE)
0
0
0
聚丙烯(PP)
0
0
O
聚碳酸脂(PC)
0
0
0
聚苯乙烯(PS)
0
O
0
O
橡胶改性苯乙烯
0
聚酰胺(PA)
0
0
0
0
聚甲醛(POM)
0
0
0
0
0
0
丙烯腈—苯乙烯
0
0
0
ABS
0
0
0
O
0
O
丙烯酸酯
0
0
注:
“。
”表示塑料适用的浇口形式。
需要指出的就是,表5、2就是生产经验的总结。
如果针对具体生产实际,能处理好塑料的性能、成型工艺条件及塑件的使用要求,即使采用了表中所列出的不适应的浇口,仍有可能取得注射成型的成功。
5.2.5浇口的位置选择与浇注系统的平衡
5.2.5.1浇口的位置选择
如前所述,浇口的形式很多,但无论采用什么形式的浇口,其开设的位置对塑件的成型性能及成型质量影响都很大,因此,合理选择浇口的开设位置就是提高塑件质量的一个重要设计环节。
另外,浇口位置的不同还会影响模具的结构。
选择浇口位置时,需要根据塑件的结构与工艺特征与成型的质量要求,并分析塑料原材料的工艺特性与塑料熔体在模内的流动状态、成型的工艺条件,综合进行考虑。
(1)尽量缩短流动距离
浇口位置的选择应保证迅速与均匀地充填模具型腔,尽量缩短熔体的流动距离,这对大型塑件更为重要。
(2)避免熔体破裂现象引起塑件的缺陷(避免喷射与蠕动)
小的浇口如果正对着一个宽度与厚度较大的型腔,则熔体经过浇口时,由于受到很高的剪切应力,将产生喷射与蠕动等熔体断裂现象。
有时塑料熔体直接从型腔的一端喷射到型腔的另一端,造成折叠,在塑件上产生波纹状痕迹或其她表面疵瘢缺陷。
要克服这种现象,可适当地加大浇口的截面尺寸,或采用冲击型浇口(浇口对着大型芯等),避免熔体破裂现象的产生。
(3)浇口应开设在塑件壁厚处
当塑件的壁厚相差较大时,若将浇口开设在壁薄处,这时塑料熔体进入型腔后,不但流动阻力大,而且还易冷却,影响熔体的流动距离,难以保证充填满整个型腔。
从收缩角度考虑,塑件壁厚处往往就是熔体最晚固化的地方,如果浇口开设在薄壁处,那壁厚的地方因液体收缩得不到补缩就会形成表面凹陷或缩孔。
为了保证塑料熔体顺利充填型腔,使注射压力得到有效地传递,而在熔体液态收缩时又能得到充分地补缩,一般浇口的位置应开设在塑件的壁厚处。
(4)应有利于型腔中气体的排除
要避免从容易造成气体滞留的方向开设浇口。
如果这一要求不能充分满足,在塑件上不就是出现缺料、气泡就就是出现焦斑,同时熔体充填时也不顾畅,虽然有时可用排气系统来解决,但在选择浇口位置时应先行加以考虑。
(5)考虑分子定向的影响
塑料熔体在充填模具型腔期间,会在其流动方向上出现聚合物分子与填料的取向。
由于垂直于流向与平行于流向之处的强度与应力开裂倾向就是有差别的,往往垂直于流向的方位强度低,容易产生应力开裂,所以在选择浇口位置时,应充分注意这一点。
图5、28a所示塑件,由于其底部圆周带有一金属环形嵌件,如果浇口开设在A处(直接浇口或点浇口),则此塑件使用不久就会开裂,因为塑料与金属环形嵌件的线收缩系数不同,嵌件周围的塑料层有很大的周向应力。
若浇口开设在B处(侧浇口),由于聚合物分子沿塑件圆周方向定向,应力开裂的机会就会大为减少。
图5、28b所示塑件为一带有铰链的聚丙烯盒体,为了使该铰链达到几千万次弯折而不断裂,就要求在铰链处高度定向,为此,将两点浇口开设在图示位置,有意识地让铰链部位高度定向。
图5、28浇口位置对定向的影响
(6)减少熔接痕,提高熔接强度
由于浇口位置的原因,塑料熔体充填型腔时会造成两股或两股以上的熔体料流的汇合。
在汇合之处,料流前端就是气体且温度最低,所以在塑件上就会形成熔接痕。
熔接痕部位塑件的熔接强度会降低,也会影响塑件外观,在成型玻璃纤维增强塑料制件时这种现象尤其严重。
如无特殊需要最好不要开设一个以上的浇口,以免增加熔接痕,如图5、29所示。
圆环形浇口流动状态好,无熔接痕,而轮幅式浇口有熔接痕,如图5、30所示,而且轮幅越多,熔接痕越多。
图5、29减少熔接痕的数量
图5、30环形浇口与轮幅浇口熔接痕比较
为了提高熔接的强度,可以在料流汇合之处的外侧或内侧设置一冷料穴(溢流槽),将料流前端的冷料引入其中,如图5、31所示。
(7)不在承受弯曲或冲击载荷的部位设置浇口
一般塑件的浇口附近强度最弱。
产生残余应力或残余变形的附近只能承受一般的拉伸力,而无法承受弯曲与冲击力。
(8)浇口位置的选择应注意塑件外观质量
浇口的位置选择除保证成型性能与塑件的使用性能外,还应注意外观质量,即选择在不影响塑件商品价值的部位或容易处理浇口痕迹的部位开设浇口。
上述这些原则在应用时常常会产生某些不同程度的相互矛盾,应分清主次因素,以保证成型性能及成型质量,得到优质产品为主,综合分析权衡,从而根据具体情况确定出比较合理的浇口位置。
5.2.5、2浇注系统的平衡
为了提高生产效率,降低成本,小型(包括部分中型)塑件往往采取一模多腔的结构形式。
在这种结构形式中,浇注系统的设计应使所有的型腔能同时得到塑料熔体均匀的充填,也就就是说,应尽量采取从主流道到各个型腔分流道的形状及截面尺寸相同的设计,即型腔平衡式布置的形式。
若根据某种需要浇注系统被设计成型腔非平衡式布置的形式,则需要通过调节浇口尺寸,使各浇口的流量及成型工艺条件达到一致,这就就是浇注系统的平衡,亦称浇口的平衡。
浇口平衡计算的思路就是通过计算多型腔模具各个浇口的BGV(BalancedGateValue)值来判断或计算。
浇口平衡时,BGV值应符合下述要求:
相同塑件的多型腔,各浇口计算出的BGV值必须相等;不同塑件的多型腔,各浇口计算出的BGV值必须与其塑件型腔的充填量成正比。
相同塑件多型腔成型的BGV值可用下式表示:
(5、11)
式中Ag——浇口的截面积;
Lr——从主流道中心至浇口的流动通道的长度;
Lg——浇口的长度。
不同(大小)塑件多型腔成型的BGV值可用下式表示:
(5、12)
式中Wa、Wb——分别为型腔a、b的充填量(熔体质量或体积);
Aga、Agb——分别为型腔a、b的浇口截面积,mm2;
Lra、Lrb——分别为从主流道中心到型腔a、b的流动通道的长度
Lga、Lgb——分别为型腔a、b的浇口长度,mm。
在一般多型腔注射模浇注系统设计中,浇口截面通常采用矩形或圆形点浇口,浇口截面积Ag与分流道截面积Ar的比值应取:
Ag:
Ar=0、07—0、09(5、13)
设:
矩形浇口的截面宽度b为其厚度t的3倍,即b=3t,各浇口的长度为相等。
进行浇口的平衡计算。
[例]图5、32所示为相同塑件10个型腔的模具流道分布简图,各浇口为矩形窄浇口,各段分流道直径相等,分流道dr=6mm,各浇口的长度Lg=1.25mm为保证浇口平衡进料,确定浇口截面的尺寸。
图5、32浇口平衡计算实例
解:
从图5、32的型腔排布可瞧出,A2、B2、A4、94型腔对称布置,流道的长度相同;A3、B3、A5、B5对称相同;A1、B1对称相同。
为了避免两端浇口与中间浇口的截面相差过大,可以A2、B2、A4、B4:
为基准,先求出这两组浇口的截面尺寸,再求另外三组浇口的截面尺寸。
(1)分流道截面积Ar
(2)基准浇口A2、B2、A4、B4这两组浇口截面尺寸(取Ag=0、07Ar);
因为:
b=3t,则,Ag=b×t=3t×t=3t2;
所以:
错
对
(3)其她三组浇口的截面尺寸
根据BGV值相等原则:
(公式5、11)
把上述计算结果列于表5、3中,用以比较。
表5、3平衡后的各浇口尺寸
型腔
浇口尺寸
A1、B1
A2、B2
A3、B3
A4、B4
A5、B5
长度Lg
1、25
1、25
1、25
1、25
1、25
宽度b
1、47
2、43
2、82
2、43
2、82
厚度t
0、49
0、81
0、94
0、81
0、94
在实际的注射模设计与生产中,常采用试模的方法来达到浇口的平衡。
1)首先将各浇口的长度、宽度与厚度加工成对应相等的尺寸。
2)试模后检验每个型腔的塑件质量,特别要检查一下后充满的型腔其塑件就是否产生补缩不足所产生的缺陷。
3)将晚充满塑件有补缩不足缺陷型腔的浇口宽度略微修大。
尽可能不改变浇口厚度,因为浇口厚度改变对压力损失较为敏感,浇口冷却固化的时间也会前后不一致。
4)用同样的工艺方法重复上述步骤直至塑件质量满意为止。
在上述试模的整个过程中,注射压力、熔体温度、模具温度、保压时间等成型工艺应与正式批量生产时的工艺条件相一致。
5.2.6冷料穴与拉料杆的设计
冷料穴就是浇注系统的结构组成之一。
主流道下端的冷料穴与角式注射机用模具的冷料穴分别如图5、10与图5、11所示,多型腔模具冷料穴在分型面的设置形式如图5、33所示。
冷料穴的作用就是容纳浇注系统流道中料流的前锋冷料,以免这些冷料注入型腔。
这些冷料既影响熔体充填的速度,又影响成型塑件的质量。
主流道末端的冷料穴除了上述作用外,还有便于在该处设置主流道拉料杆的功能。
注射结束模具分型时,在拉料杆的作用下,主流凝料从定模浇口套中被拉出,最后推出机构开始工作,将塑件与浇注系统凝料一起推出模外。
这里需要指出的就是,点浇口形式浇注系统的三板式模具,在主流道末端就是不允许设置拉料杆的,否则模具将无法工作。
图5、33多型腔模具分型面上的冷料穴
1一型腔;2一浇口;3、7一冷料穴;
4—三次分流道;5—二次分流道;6—一次分流道
主流道拉料杆有两种基本形式:
Z字形拉料杆、球头型拉料杆
1、Z字形拉料杆
一种就是推杆形式的拉料杆,其固定在推杆固定板上,Z字形拉料杆典型的结构形式如图5、34a所示。
图5、34b与图5、34c所示分别为在动模板上开设的反锥度冷料穴与浅圆环槽冷料穴的形式,它们的后面设置推杆。
Z字形拉料杆就是最常用的一种形式。
工作时依靠Z字形钩将主流道凝料拉出浇口套,推出后由于钩子的方向性而不能自动脱落,需要人工取出。
2—球头型拉料杆
对于图5、34b与图5、34c的形式,在分型时靠动模板上的反锥度穴与浅圆环槽的作用将主流道凝料拉出浇口套,然后靠后面的推杆强制地将其推出。
球头型拉料杆就是仅适于推件板脱模的拉料杆!
其典型的形式就是球字头拉料杆,固定在动模板上,如图5、34d所示。
图5、34e所示为菌形头拉料杆,它就是靠头部凹下去的部分将主流道从浇口套中拉出来,然后在推件板推出时,将主流道凝料从拉料杆的头部强制推出。
图5、34f就是靠塑料的收缩包紧力使主流道凝料包紧在中间拉料杆(带有分流锥的型芯)上以及靠环形浇口与塑件的连接将主流道凝料拉出浇口套,然后靠推件板将塑件与主流道凝料一起推出模外。
图5、34b~f的形式,主流道凝料都能在推出时自动脱落。
图5、34主流道冷抖穴与拉抖杆的形式
并不就是所有多型腔注射模在分型面都要设计冷料穴,对于塑料性能与成型工艺控制较好、对塑件的要求又不高时,可不必设置冷料穴。