第三章矿井防尘.docx
《第三章矿井防尘.docx》由会员分享,可在线阅读,更多相关《第三章矿井防尘.docx(38页珍藏版)》请在冰豆网上搜索。
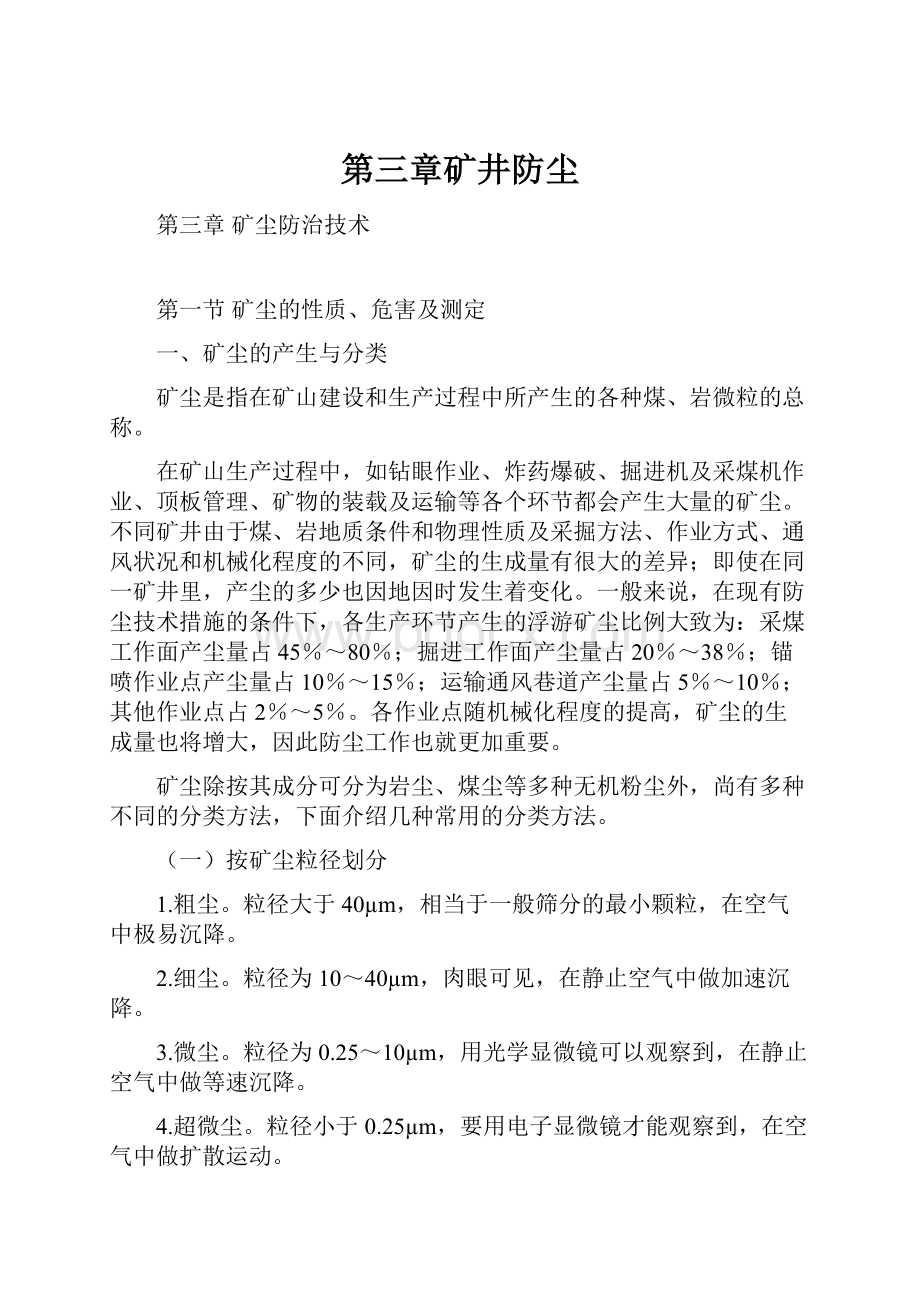
第三章矿井防尘
第三章矿尘防治技术
第一节矿尘的性质、危害及测定
一、矿尘的产生与分类
矿尘是指在矿山建设和生产过程中所产生的各种煤、岩微粒的总称。
在矿山生产过程中,如钻眼作业、炸药爆破、掘进机及采煤机作业、顶板管理、矿物的装载及运输等各个环节都会产生大量的矿尘。
不同矿井由于煤、岩地质条件和物理性质及采掘方法、作业方式、通风状况和机械化程度的不同,矿尘的生成量有很大的差异;即使在同一矿井里,产尘的多少也因地因时发生着变化。
一般来说,在现有防尘技术措施的条件下,各生产环节产生的浮游矿尘比例大致为:
采煤工作面产尘量占45%~80%;掘进工作面产尘量占20%~38%;锚喷作业点产尘量占10%~15%;运输通风巷道产尘量占5%~10%;其他作业点占2%~5%。
各作业点随机械化程度的提高,矿尘的生成量也将增大,因此防尘工作也就更加重要。
矿尘除按其成分可分为岩尘、煤尘等多种无机粉尘外,尚有多种不同的分类方法,下面介绍几种常用的分类方法。
(一)按矿尘粒径划分
1.粗尘。
粒径大于40µm,相当于一般筛分的最小颗粒,在空气中极易沉降。
2.细尘。
粒径为10~40µm,肉眼可见,在静止空气中做加速沉降。
3.微尘。
粒径为0.25~10µm,用光学显微镜可以观察到,在静止空气中做等速沉降。
4.超微尘。
粒径小于0.25µm,要用电子显微镜才能观察到,在空气中做扩散运动。
(二)按矿尘的存在状态划分
1.浮游矿尘。
悬浮于矿内空气中的矿尘,简称浮尘。
2.沉积矿尘。
从矿内空气中沉降下来的矿尘,简称落尘。
浮尘和落尘在不同环境下可以相互转化。
浮尘在空气中飞扬的时间不仅与尘粒的大小、重量、形式等有关,还与空气的湿度、风速等大气参数有关。
(三)按矿尘的粒径组成范围划分
1.全尘(总粉尘)。
各种粒径的矿尘之和。
对于煤尘,常指粒径为1mm以下的尘粒。
2.呼吸性粉尘。
主要指粒径在5µm以下的微细尘粒,它能通过人体上呼吸道进人肺区,可导致尘肺病,对人体危害甚大。
二、矿尘的危害
矿尘具有很大的危害性,表现在以下几个方面:
(一)污染工作场所,危害人体健康,引起职业病。
工人长期吸人矿尘后,轻者会患呼吸道炎症、皮肤病,重者会患尘肺病,而尘肺病引发的矿工致残和死亡人数在国内外十分惊人。
据国内某矿务局统计,尘肺病的死亡人数为工伤事故死亡人数的6倍;德国煤矿死于尘肺病的人数曾比工伤事故死亡人数高10倍。
因此,世界各国都在积极开展预防和治疗尘肺病的工作,并已取得较大进展。
(二)某些矿尘(如煤尘、硫化尘)在一定条件下可以爆炸。
煤尘能够在完全没有瓦斯存在的情况下爆炸,对于瓦斯矿井,煤尘则有可能参与瓦斯同时爆炸。
煤尘或瓦斯煤尘爆炸,都将给矿山以突然性的袭击,酿成严重灾害。
例如,1906年3月10日法国柯利尔煤矿发生的煤尘爆炸事故,死亡1099人,造成了重大的灾难。
(三)加速机械磨损,缩短精密仪器使用寿命。
随着矿山机械化、电气化、自动化程度的提高,矿尘对设备性能及其使用寿命的影响将会越来越突出,应引起高度的重视。
(四)降低工作场所能见度,增加工伤事故的发生。
在某些综采工作面割煤时,工作面煤尘浓度高达4000~8000mg/m3,有的甚至更高,这种情况下,工作面能见度极低,往往会导致误操作,造成人员的意外伤亡。
三、矿尘的分散度、浓度
(一)矿尘的分散度
分散度是指矿尘整体组成中各种粒级尘粒所占的百分比。
分散度有两种表示方法:
1.重量百分比各粒级尘粒的重量占总重量的百分比称为重量分散度;
2.数量百分比各粒级尘粒的颗粒数占总颗粒数的百分比称为数量分散度。
粒级的划分是根据粒度大小和测试目的确定的,我国工矿企业将矿尘粒级划分为4级;小于2µm、2~5µm、5~10µm和大于10µm。
矿尘分散度是衡量矿尘颗粒大小构成的一个重要指标,是研究矿尘性质与危害的一个重要参数。
矿尘总量中微细颗粒多,所占比例大时,称为高分散度矿尘;反之,如果矿尘中粗大颗粒多,所占比例大,就称作低分散度矿尘。
矿尘的分散度越高,危害性越大,而且越难捕获。
《规程》规定粉尘分散度,每半年测定1次。
(二)矿尘的浓度
单位体积矿内空气中所含浮尘的数量称为矿尘浓度,其表示方法有两种:
1.质量法。
每立方米空气中所含浮尘的毫克数,单位为mg/m3。
2.计数法。
每立方厘米空气中所含浮尘的颗粒数,单位为粒/cm3。
我国规定采用质量法来计量矿尘浓度。
计数法因其测定复杂且不能很好地反映矿尘的危害性,因而在国外使用也越来越少。
矿尘
浓度的大小直接影响着矿尘危害的严重程度,表3—1作业场所空气中粉尘浓度标准
粉尘中游离SiO2含量
(%)
最高允许浓度/(mg/m3)
总粉尘
呼吸性
粉尘
<10
10~<50
50~<80
≥80
10
2
2
2
3.5
1
0.5
0.3
是衡量作业环境的劳动卫生状况和评价防尘
技术效果的重要指标。
因此《规程》对作业
场所空气中粉尘(总粉尘、呼吸性粉尘)浓度
标准做了明确规定,见表3—1。
四、矿尘的测定
《煤矿安全规程》第七百四十条规定,
煤矿企业必须按国家规定对生产性粉尘进行
监测,并遵守下列规定:
总粉尘:
作业场所的粉尘浓度,井下每
月测定两次,地面及露天煤矿每月测定一次;
粉尘分散度,每6个月测定一次。
呼吸性粉尘:
工班个体呼吸性粉尘监测,采、掘(剥)工作面每3个月测定1次,其他工作面或作业场所每6个月测定1次。
每个采样工种分2个班次连续采样,1个班次内至少采集2个有效样品,先后采集的有效样品不得少于4个;定点呼吸性粉尘监测每月测定1次。
粉尘中游离SiO2含量,每6个月测定1次,在变更工作面时也必须测定1次;各接尘作业场所每次测定的有效样品数不得少于3个。
开采深度大于200米的露天煤矿,在气压较低的季节应适当增加测定次数。
定期测定井下空气中的矿尘浓度和分散度,是掌握工作场所矿尘状况,检查防尘效果的重要手段。
(一)矿尘浓度测定
矿尘浓度测定分质量法和计数法两类,我国主要用质量法。
目前煤矿普遍采用滤膜测尘法,它的原理是用抽气装置将含尘空气通过装有滤膜的采样器,将矿尘过滤截留,再根据滤膜的增重和通过的空气量,计算矿尘的浓度。
1.主要装置
1)滤膜
滤膜是用超细合成纤维制成的网状薄膜,表面呈细绒状,不易脆裂,有明显的荷电性和憎水性。
具有阻尘率高(可达99%)、阻力小、不易吸湿、重量轻、性能稳定等优点。
滤膜有直径40mm及75mm两种规格,前者适用于矿尘浓度低于200mg/m3的地点采样;后者多用于矿尘浓度超过200mg/m3的地点采样。
2)采样器
它由采样漏斗和滤膜夹两部分组成,如图3—1所示。
下井测定前,将称量后的滤膜装入滤膜夹,放入滤膜盒内。
采样时取出滤膜夹安放于采样漏斗中。
图3—1
a-采样漏斗;b-滤摸夹
1-漏斗顶盖;2-漏斗;3-锥形环;4-固定盖;5-底座
3)流量计
流量计用来测定通过滤料的含尘空气量(L/min)。
井下常用转子流量计。
它由有一定锥度的有机玻璃管和转子构成,当测尘空气从下而上通过锥形管时,转子和锥形管壁之间的间隙逐渐增加,直到转子的重力和空气的上升力相等时,即平衡在一定高度。
此时可从转子顶部所在锥形管的刻度,得出单位时间的流量值。
4)抽气装置
有电动抽气泵和压气引射器两类。
在有沼气、煤尘爆炸危险的矿井,普通电动抽气泵不能使用。
2.测定工作
1)准备滤膜
首先应将滤膜放在干燥皿内干燥,然后用镊子将滤膜两面的衬纸取下,用万分之一天平或扭力天平称量,记下初量,将之装在滤膜夹上,放入滤膜盒内备用。
直径40mm的滤膜平铺夹牢,直径75mm的折成漏斗形夹牢。
2)采样
应在作业人员经常活动的范围内进行,距地面的高度约1.5m(相当于人的呼吸带高),并需避开风动工具和风流涡流的影响。
采样器入口应迎向风流。
每个试样的采尘量应大于1mg,小于20mg。
一般情况下,采样流量为10~30L/min,时间为20min。
为了保证测尘精度,应在同一地点,在相同条件下同时采取两个试样。
图3-2为压气引射器为动力时的采样布置。
图3-2 利用压气采取尘样
1-采样头;2-采样头固定架;3-喷射器;
4-流量计; 5-压气管
3.称量和计算
称量前,将滤膜放在干燥皿内干燥.如果采样地点水雾较大,滤膜表面有水珠,应在干燥箱内干燥,每隔30min称量一次,直到前后两次的称量差小于0.2mg为止.称量时应将受尘面向上、向内对折2~3次。
称量后按下式计算矿尘浓度:
(3—1)
式中
—矿尘浓度,mg/m3;
—滤膜的增量,mg;
—采样流量,L/min;
—采样时间,min。
同时采取两个平行试样时,它们之间的相对差值小于20%方为合格:
(3—2)
式中
—平行样品的相对差值,%
—两个样品的各自测定值,mg/m3。
最后,以两个合格的平行样品的算术平均值作为测定地点的矿尘浓度。
4.除油
工作面空气中常含有很多机械用油的油雾,它能吸附在滤膜上,造成测定的误差。
为了消除这一影响,可将滤膜置于120号汽油中侵润10~15min在称量。
携带式直读测尘仪种类型号很多,目前国内生产的有:
根据
射线通过含尘空气时辐射强度衰减原理而制成的,如WAR型测尘仪;用静电采样器将粉尘采集在石英晶体振荡器的电极表面上,引起它的振荡频率减少的CO—1型测尘仪;利用光通过含尘空气时的吸收、散射原理制成的测尘仪,等等。
这类仪器测定简单、迅速、直观,但是精度不高。
(二)矿尘分散度测定
矿尘的分散度分为质量分散度(各类粒径的质量百分比)和数量分散度(各类粒径的数量百分比)两类。
前者多用沉降法,后者多用显微观察法。
数量分散度的测定,可在滤膜法测定矿尘
浓度后进行。
即利用滤膜可溶于有机溶剂
的特点,将带尘滤膜平脯在载物玻璃片上,
带尘面向上,滴中性加拿大胶一滴,胶内
的二甲苯将滤膜纤维溶解,形成透明的带
尘滤膜,盖上盖玻片以防污染。
或者将带
尘滤膜放在磁坩埚中,加醋酸丁溶剂1~2
ml,待滤膜溶解后,将溶液搅拌均匀,取
一滴置于载物玻璃上,用另一玻片将之推
平。
一分钟后形成带尘滤膜,盖上盖玻片。
图3—3分散度测定示意图
制好的试样玻片放于400~600倍显微镜的载物台上,用目镜测微尺,量尘粒的定向粒径(图3—3)。
尘粒数量少的试样,每一颗尘粒都应测量到。
尘粒数量多时需测200粒以上。
测量的结果按分散度的分级计算它们的百分比。
第二节煤尘爆炸及其预防
煤尘爆炸同瓦斯爆炸一样都属于矿井中的重大灾害事故。
我国历史上最严重的一次煤尘爆炸发生在1942年日本侵略者统治下的本溪煤矿,死亡1549人,残246人,死亡的人员中大多为CO中毒,事故发生前,巷道内沉积了大量煤尘,是由于电火花点燃局部聚积的瓦斯而引起的重大煤尘爆炸事故。
一、煤尘爆炸的机理及特征
(一)煤尘爆炸的机理
煤尘爆炸是在高温或一定点火能的热源作用下,空气中氧气与煤尘急剧氧化的反应过程,是一种非常复杂的链式反应。
一般认为其爆炸机理及过程如下:
1.煤本身是可燃物质,当它以粉末状态存在时,总表面积显著增加,吸氧和被氧化的能力大大增强,一旦遇见火源,氧化过程迅速展开;
2.当温度达到300~400℃时,煤的干馏现象急剧增强,放出大量的可燃性气体;
3.形成的可燃气体与空气混合在高温作用下吸收能量,在尘粒周围形成气体外壳,即活化中心,当活化中心的能量达到一定程度后,链反应过程开始,游离基迅速增加,发生了尘粒的闪燃;
4.闪燃所形成的热量传递给周围的尘粒,并使之参与链反应,导致燃烧过程急剧地循环进行,当燃烧不断加剧使火焰速度达到每秒数百米后,煤尘的燃烧便在一定临界条件下跳跃式地转变为爆炸。
(二)煤尘爆炸的特征
1.形成高温、高压、冲击波煤尘爆炸火焰温度为1600~1900℃,爆源的温度达到2000℃以上,这是煤尘爆炸得以自动传播的条件之一。
在矿井条件下煤尘爆炸的平均理论压力为736kPa,但爆炸压力随着离开爆源距离的延长而跳跃式增大。
爆炸过程中如遇障碍物,压力将进一步增加,尤其是连续爆炸时,后一次爆炸的理论压力将是前一次的5~7倍。
煤尘爆炸产生的火焰速度可达1120m/s,冲击波速度为2340m/s。
2.煤尘爆炸具有连续性由于煤尘爆炸具有很高的冲击波速,能将巷道中落尘扬起,甚至使煤体破碎形成新的煤尘,导致新的爆炸,有时可如此反复多次,形成连续爆炸,这是煤尘爆炸的重要特征。
3.煤尘爆炸的感应期煤尘爆炸也有一个感应期,即煤尘受热分解产生足够数量的可燃气体形成爆炸所需的时间。
根据试验,煤尘爆炸的感应期主要决定于煤的挥发分含量,一般为40~280ms,挥发分越高,感应期越短。
4.挥发分减少或形成“粘焦”煤尘爆炸时,参与反应的挥发分约占煤尘挥发分含量的40%~70%,致使煤尘挥发分减少,根据这一特征,可以判断煤尘是否参与了井下的爆炸。
对于气煤、肥煤、焦煤等粘结性煤的煤尘,一旦发生爆炸,一部分煤尘会被焦化,粘结在一起,沉积于支架和巷道壁上,形成煤尘爆炸所特有的产物—焦炭皮渣或粘块,统称“粘焦”。
“粘焦”也是判断井下发生爆炸事故时是否有煤尘参与的重要标志。
5.产生大量的CO煤尘爆炸时产生的CO,在灾区气体中的浓度可达2%—3%,甚至高达8%左右。
爆炸事故中受害者的大多数(70%~80%)是由于CO中毒造成的。
二、煤尘爆炸的条件
煤尘爆炸必须同时具备三个条件:
煤尘本身具有爆炸性;煤尘必须悬浮于空气中,并达到一定的浓度;存在能引燃煤尘爆炸的高温热源。
(一)煤尘的爆炸性
煤尘具有爆炸性是煤尘爆炸的必要条件。
煤尘爆炸的危险性必须经过试验确定
(二)悬浮煤尘的浓度
井下空气中只有悬浮的煤尘达到一定浓度时,才可能引起爆炸,单位体积中能够发生煤尘爆炸的最低和最高煤尘量称为下限和上限浓度。
低于下限浓度或高于上限浓度的煤尘都不会发生爆炸。
煤尘爆炸的浓度范围与煤的成分、粒度、引火源的种类和温度及试验条件等有关。
一般说来,煤尘爆炸的下限浓度为30~50g/m3,上限浓度为1000~2000g/m3。
其中爆炸力最强的浓度范围为300~500g/m3。
一般情况下,浮游煤尘达到爆炸下限浓度的情况是不常有的,但是爆破、爆炸和其他震动冲击都能使大量落尘飞扬,在短时间内使浮尘量增加,达到爆炸浓度。
因此,确定煤尘爆炸浓度时,必须考虑落尘这一因素。
(三)引燃煤尘爆炸的高温热源
煤尘的引燃温度变化范围较大,它随着煤尘性质、浓度及试验条件的不同而变化。
我国煤尘爆炸的引燃温度在610~1050℃之间,一般为700~800℃。
煤尘爆炸的最小点火能为4.5~40mJ。
这样的温度条件,几乎一切火源均可达到,如爆破火焰、电气火花、机械摩擦火花、瓦斯燃烧或爆炸、井下火灾等。
三.影响煤尘爆炸的因素
(一)煤的挥发分
煤尘爆炸主要是在尘粒分解的可燃气体(挥发分)中进行的,因此煤的挥发分数量和质量是影响煤尘爆炸的最重要因素。
一般说来,煤尘的可燃挥发分含量越高,爆炸性越强,即煤化作用程度低的煤,其煤尘的爆炸性强,随煤化作用程度的增高而爆炸性减弱。
(二)煤的灰分和水分
煤内的灰分是不燃性物质,能吸收能量,阻挡热辐射,破坏链反应,降低煤尘的爆炸性。
煤的灰分对爆炸性的影响还与挥发分含量的多少有关,挥发分小于15%的煤尘,灰分的影响比较显著,大于15%时,天然灰分对煤尘的爆炸几乎没有影响。
水分能降低煤尘的爆炸性,因为水的吸热能力大,能促使细微尘粒聚结为较大的颗粒,减少尘粒的总表面积,同时还能降低落尘的飞扬能力。
煤的天然灰分和水分都很低,降低煤尘爆炸性的作用不显著,只有人为地掺入灰分(撒岩粉)或水分(洒水)才能防止煤尘的爆炸。
(三)煤尘粒度
粒度对爆炸性的影响极大。
粒径1mm以下的煤尘粒子都可能参与爆炸,而且爆炸的危险性随粒度的减小而迅速增加,75µm以下的煤尘特别是30~75µm的煤尘爆炸性最强,因为单位质量煤尘的粒度越小,总表面积及表面能越大,粒径小于10µm后,煤尘爆炸性增强的趋势变得平缓。
煤尘粒度对爆炸压力也有明显的影响。
煤炭科学研究院重庆分院的试验结果表明:
在同一煤种不同粒度条件下,爆炸压力随粒度的减小而增高,爆炸范围也随之扩大,即爆炸性增强。
粒度不同的煤尘引燃温度也不相同。
煤尘粒度越小,所需引燃温度越低,且火焰传播速度也越快。
(四)空气中的瓦斯浓度
瓦斯参与使煤尘爆炸下限降低。
瓦斯浓度低于4%时,煤尘的爆炸下限可用下式计算:
MW=Mk(3—3)
式中MW—空气中有瓦斯时的煤尘爆炸下限,g/m3;
M—煤尘的爆炸下限,g/m3;
K—系数,见表3—2—1。
表3—2瓦斯浓度对煤尘爆炸下限的影响系数
空气中的瓦斯浓度/%
0
0.50
0.75
1.0
1.50
2.0
3.0
4.0
k
1
0.75
0.6
0.5
0.35
0.25
0.1
0.05
随着瓦斯浓度的增高,煤尘爆炸浓度下限急剧下降,这一点在有瓦斯煤尘爆炸危险的矿井应引起高度重视。
一方面,煤尘爆炸往往是由瓦斯爆炸引起的,另一方面,有煤尘参与时小规模的瓦斯爆炸可能演变为大规模的煤尘瓦斯爆炸事故,造成严重的后果。
(五)空气中氧的含量
空气中氧的含量高时,点燃煤尘的温度可以降低,氧的含量低时,点燃煤尘云困难,当氧含量低于17%时,煤尘就不再爆炸。
煤尘的爆炸压力也随空气中含氧的多少而不同。
含氧高,爆炸压力高,含氧低,爆炸压力低。
(六)引爆热源
点燃煤尘云造成煤尘爆炸,就必须有一个达到或超过最低点燃温度和能量的引爆热源。
引爆热源的温度越高,能量越大,越容易点燃煤尘云。
而且煤尘初爆的强度也越大;反之温度越低,能量越小,越难以点燃煤尘云,且即使引起爆炸,初始爆炸的强度也越小。
四、煤尘爆炸性鉴定
《规程》规定:
新矿井的地质精查报告中,必须有所有煤层的煤尘爆炸性鉴定材料。
生产矿井每延深一个新水平,应进行一次煤尘爆炸性试验工作。
煤尘爆炸性的鉴定方法有两种:
一种是在大型煤尘爆炸试验巷道中进行,这种方法比较准确可靠,但工作繁重复杂,所以一般作为标准鉴定用,另一种是在实验室内使用大管状煤尘爆炸性鉴定仪进行,方法简便,目前多采用这种方法。
大管状煤尘爆炸性鉴定仪如图3—4所示,它的主要部件有;内径为75~80mm的燃烧管1,长为1400mm的硬质玻璃管,一端经弯管与排尘箱8连接,在另一端距入口400mm处径向对开的两个小孔装入有铂丝加热器2,加热器是长为110mm的中空细瓷管(内径1.5mm,外径3.6mm),铂丝11缠在直径0.3mm的管外;两端由燃烧管的小孔引出,接在变压器T上:
铂铑热电偶10,它的两端接上铜导线构成冷接点置于冷瓶3中,然后连到高温计4以测量火源温度:
铜制试料管5,长100mm,内径9.5mm,通过导管6与电磁气筒7连接,排尘管内装有滤尘板,并和小风机9连接。
试验的程序是;将粉碎后全部通过75µm筛孔的煤样在105℃温度时烘干2h,称量1g尘样放在试料管中,接通加热器电源,调节可变电阻R将加热器的温度升至1100
5℃;按压电磁气筒开关K2,煤尘试样呈雾状喷人燃烧管,同时观察大管内煤尘燃烧状态,最后开动小风机排除烟尘。
煤尘通过燃烧管内的加热器时,可能出现下列现象:
1.只出现稀少的火星或根本没有火星;2.火焰向加热器两侧以连续或不连续的形式在尘雾中缓慢地蔓延;3.火焰极快地蔓延,甚至冲出燃烧管外,有时还会听到爆炸
声。
同一试样应重复进行5次试验,其中只
要有一次出现燃烧火焰,就定为爆炸危险煤
尘。
在5次试验中都没有出现火焰或只出现
稀少火星,必须重做5次试验,如果仍然如
此,定为无爆炸危险煤尘,在重做的试验中,
只要有一次出现燃烧火焰,仍应定为爆炸危
险煤尘。
对有爆炸危险的煤尘,还可进行预防煤
尘爆炸所需岩粉量的测定。
具体做法是将岩
粉按比例和煤尘均匀混合,用上述方法测定
它的爆炸性,直到混合粉尘由出现火焰刚转
图3—4煤尘爆炸性鉴定示意图
1—燃烧管;2—铂丝加热器;3—冷瓶;4—高温计;5—试料管;6—导管;
7—电磁气筒;8—排尘箱;9—小风机;10—铂铑热电偶
入不再出现火焰,此时的岩粉比例,即为最
低岩粉用量的百分比。
矿井中只要有一个煤层的煤尘有爆炸危
险,该矿井就应定为有煤尘爆炸危险的矿井。
根据煤尘爆炸性试验,我国有80%左右的煤
矿属于开采有煤尘爆炸危险煤层的矿井。
五、预防煤尘爆炸的技术措施
预防煤尘爆炸的技术措施主要包括减、降尘措施,防止煤尘引燃措施及隔绝煤尘爆炸措施等三个方面。
(一)减、降尘措施
减、降尘措施是指在煤矿井下生产过程中,通过减少煤尘产生量或降低空气中悬浮煤尘含量以达到从根本上杜绝煤尘爆炸的可能性。
为达到这一目的,煤矿上采取了以煤层注水为主的多种防尘手段,本节将重点介绍煤层注水。
1.煤层注水实质
煤层注水是回采工作面最重要的防尘措施之一,在回采之前预先在煤层中打若干钻孔,通过钻孔注入压力水,使其渗入煤体内部,增加煤的水分,从而减少煤层开采过程煤尘的产尘量。
煤层注水的减尘作用主要有以下三个方面:
1)煤体内的裂隙中存在着原生煤尘,水进入后,可将原生煤尘湿润并粘结,使其在破碎时失去飞扬能力,从而有效地消除这一尘源。
2)水进入煤体内部,并使之均匀湿润。
当煤体在开采中受到破碎时,绝大多数破碎面均有水存在,从而消除了细粒煤尘的飞扬,预防了浮尘的产生
3)水进入煤体后使其塑性增强,脆性减弱,改变了煤的物理力学性质,当煤体因开采而破碎时,脆性破碎变为塑性变形,因而减少了煤尘的产生量。
2.影响煤层注水效果的因素
1)煤的裂隙和孔隙的发育程度
对于不同成因及煤岩种类的煤层来说,其裂隙和空隙的发育程度不同,注水效果差异也较大。
煤体的裂隙越发育则越易注水,可采用低压注水(根据煤科院抚顺分院建议:
低压小于2943kPa,中压为2943~9810kPa,高压大于9810kPa),负则需采用高压注水才能取得预期效果,但是当出现一些较大的裂隙(如断层、破裂面等),注水易散失于远处或煤体之外,对预湿煤体不利。
煤体的孔隙发育程度一般用孔隙率表示,系指孔隙的总体积与煤的总体积的百分比。
根据实测资料,当煤层的孔隙率小于4%时,煤层的透水性较差,注水无效果;孔隙率为15%时,煤层的透水性最高,注水效果最佳;而当孔隙率达40%时,煤层成为多孔均质体,天然水分丰富则无需注水,此多属于褐煤。
2)上覆岩层压力及支承压力
地压的集中程度与煤层的埋藏深度有关,煤层埋藏越深则地层压力越大,而裂隙和孔隙变得更小,导致透水性能降低,因而随着矿井深度的增加,要取得良好的煤体湿润效果,需要提高注水压力。
在长壁工作面的超前集中应力带以及其他大面积采空区附近的集中应力带,因承受的压力增高,其煤体的孔隙率与受采动影响的煤体相比,要小60%~70%,减弱了煤的透水性。
3)液体性质的影响
煤是极性小的物质,水是极性大的物质,两者之间极性差越小,越易湿润。
为了降低水的表面张力,减小水的极性,提高对煤的湿润效果,可以在水中添加表面活性剂。
4)煤层内的瓦斯压力
煤层内的瓦斯压力是注水的附加阻力。
水压克服瓦斯压力后才是注水的有效压力,所以在瓦斯压力大的煤层中注水时,往往要提高注水压力,以保证湿润效果。
5)注水参数的影响
煤层注水参数是指注水压力、注水速度、注水量和注水时间。
注水量或煤的水分增量是煤层注水效果的标志,也是决定煤层注水除尘率高低的重要因素,如图3—5,3—6所示。
通常,注水量或煤的水分增量变化在50%到80%之间,注水量和煤的水分增量都和煤层的渗透性、注水压力、注水速度以及注水时间有关。
图3—5除尘率与注水量的关系图图3—6除尘率与煤水分增量的关系
3.煤层注水方