刹车片基本知识汇总.docx
《刹车片基本知识汇总.docx》由会员分享,可在线阅读,更多相关《刹车片基本知识汇总.docx(14页珍藏版)》请在冰豆网上搜索。
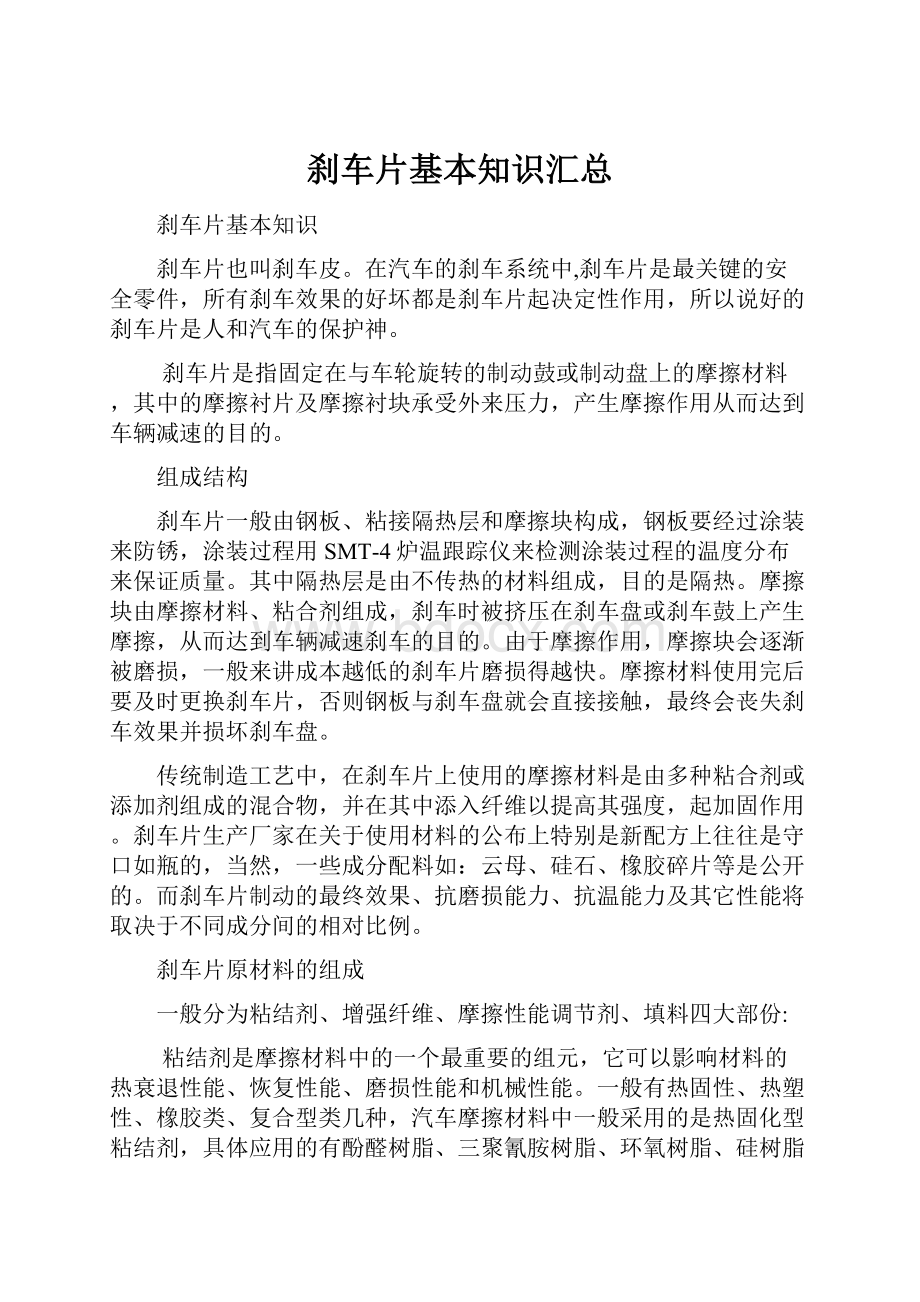
刹车片基本知识汇总
刹车片基本知识
刹车片也叫刹车皮。
在汽车的刹车系统中,刹车片是最关键的安全零件,所有刹车效果的好坏都是刹车片起决定性作用,所以说好的刹车片是人和汽车的保护神。
刹车片是指固定在与车轮旋转的制动鼓或制动盘上的摩擦材料,其中的摩擦衬片及摩擦衬块承受外来压力,产生摩擦作用从而达到车辆减速的目的。
组成结构
刹车片一般由钢板、粘接隔热层和摩擦块构成,钢板要经过涂装来防锈,涂装过程用SMT-4炉温跟踪仪来检测涂装过程的温度分布来保证质量。
其中隔热层是由不传热的材料组成,目的是隔热。
摩擦块由摩擦材料、粘合剂组成,刹车时被挤压在刹车盘或刹车鼓上产生摩擦,从而达到车辆减速刹车的目的。
由于摩擦作用,摩擦块会逐渐被磨损,一般来讲成本越低的刹车片磨损得越快。
摩擦材料使用完后要及时更换刹车片,否则钢板与刹车盘就会直接接触,最终会丧失刹车效果并损坏刹车盘。
传统制造工艺中,在刹车片上使用的摩擦材料是由多种粘合剂或添加剂组成的混合物,并在其中添入纤维以提高其强度,起加固作用。
刹车片生产厂家在关于使用材料的公布上特别是新配方上往往是守口如瓶的,当然,一些成分配料如:
云母、硅石、橡胶碎片等是公开的。
而刹车片制动的最终效果、抗磨损能力、抗温能力及其它性能将取决于不同成分间的相对比例。
刹车片原材料的组成
一般分为粘结剂、增强纤维、摩擦性能调节剂、填料四大部份:
粘结剂是摩擦材料中的一个最重要的组元,它可以影响材料的热衰退性能、恢复性能、磨损性能和机械性能。
一般有热固性、热塑性、橡胶类、复合型类几种,汽车摩擦材料中一般采用的是热固化型粘结剂,具体应用的有酚醛树脂、三聚氰胺树脂、环氧树脂、硅树脂、聚酰胺树脂等。
应用最广泛的是酚醛树脂及其改性树脂。
改性的目的是改善树脂的高温性能。
为了更大的提高粘结剂的高温性能,现在先进的汽车摩擦材料已经有些采用聚酰亚胺树脂,但目前这种树脂成本太高,普及不容易。
增强纤维是摩擦材料也是主要的摩擦组元起增强基的作用,传统材料用的是石棉等矿物纤维,半金属汽车摩擦材料中使用的是钢纤维,同时加入少量铜纤维及其少量矿物纤维。
近年来,增强纤维的种类也越来越多,其中最引人注目的是芳纶(Kevlar)的应用。
有机纤维的加入,可以降低材料的密度、减小其磨损量,但同时也会降低材料的摩擦系数。
为了提高摩擦材料在各温度段的稳定性及其纤维和粘结剂的亲和性能,在实际应用中往往采用多种纤维混合使用。
摩擦性能调节剂可以分为2类:
(1)减摩材料:
莫氏硬度一般小于2,它的加入可提高材料的耐摩性,减小噪音及降低摩擦系数。
这类材料主要有:
石墨、二硫化钼、铅、铜等。
(2)摩阻材料:
莫氏硬度一般大于4,它的加入可以增加材料的摩擦系数。
大部分无机填料和部分金属及其氧化物属这一类。
摩擦性能调节剂的加入主要是调节材料的热稳定性能以及其工作稳定性。
填料主要以粉末的形式加入。
填料的作用很多,比如说加入铜粉,它的作用是可以在摩擦材料和对偶间形成转移膜,既能提高摩擦力矩和稳定摩擦系数,有能减小对对偶件的损伤,提高整个摩擦副的耐摩性能。
加入硫酸钡,可以提高材料的密度。
刹车片的主要性能:
一般,对刹车片的基本要求主要有耐磨损、摩擦系数大、优良的隔热性能。
1、高性能:
摩擦系数高(金麒麟陶瓷刹车片摩擦系数达0.45,属于高摩擦系数刹车片),耐高温,高速行驶和高温行驶过程中表现突出,驾驶过程中高速高温情况下制动效果和制动舒适性良好。
2、安全性:
热衰退低,恢复性能良好,山区道路和高温、高速状态下制动性能不降低。
最大限度的提高了车辆的安全性。
非常适合与山路地区,高速以其他各种路况的使用!
3、舒适性:
制动舒适,无噪音,无污染,制动平衡。
4、合理的使用寿命:
一般非改装车辆,在正常行驶的情况的下,前制动器的刹车片寿命为3—5万公里,后制动器刹车片的使用寿命为8-10万公里.前刹车盘使用寿命6-10万公里.当然经常在山区行驶的汽车刹车片和盘则寿命要短很多.
5、较低的掉粉率
刹车片的摩擦系数:
是指两表面间的摩擦力和作用在其一表面上的垂直力之比值。
它是和表面的粗糙度有关,而和接触面积的大小无关。
依运动的性质,它可分为动摩擦系数和静摩擦系数。
刹车片最重要的性能指标就是摩擦系数。
国家标准规定的刹车摩擦系数在0.35-0.40之间。
合格的刹车片摩擦系数适中、稳定,如果摩擦系数低于0.35,刹车时就会超过安全制动距离甚至刹车失灵,如果摩擦系数高于0.40,刹车容易突然抱死,出现翻车事故。
国家非金属矿制品质量监督检验中心检验人员:
"国家标准规定,350度摩擦系数应该大于0.20,
刹车片的类型分类:
汽车刹车片从类型上分有:
-用于盘式制动器的刹车片
-用于鼓式制动器的刹车蹄
-用于大卡车的来令片
刹车鼓上装的是刹车蹄,但一般人叫刹车片就统指刹车片和刹车蹄,所以用“盘式刹车片”来特别指明是盘式制动器上装的刹车片。
并不是刹车盘。
从配方技术上分有:
半金属,少金属,石棉,陶瓷,
以下就简单谈一谈几种不同材质的刹车片。
石棉型刹车片
从最初开始石棉就已经被用作刹车片的加固材料,由于石棉纤维具有高强度和耐高温的特性,因此可以满足刹车片及离合器盘和衬垫的要求。
但是除了危害健康方面的因素外,石棉型刹车片还存在着另一个重要问题。
由于石棉是绝热的,其导热能力特别差,通常反复使用制动器会使热量在刹车片中堆积起来,刹车片变热后,它的制动性能就要发生改变,要产生同样的摩擦和制动力会需要更多的踩刹车次数,这种现象被称为“制动萎缩”,如果刹车片达到一定的热度,将导致制动失灵。
当车辆制造商和制动材料供应商决定发展新的更安全的石棉替代品时,新的摩擦材料几乎同时应运而生。
这就是下面要谈到的“半金属”混合物型和无石棉有机物型(NAO)刹车片。
“半金属”混合物型刹车片
“半金属”混合物型刹车片(Semi-met)主要是采用粗糙的钢丝绒作为加固纤维和重要的混合物。
从外观上(细的纤维和微粒)可以很方便地将石棉型和无石棉有机物型刹车片(NAO)区分开来,另外它们还具有一定的磁性。
钢丝绒具有较高的强度和导热性,这使得“半金属”混合物型刹车片同传统的石棉型刹车片有着不同的制动特性。
例如:
“半金属”刹车片内部金属含量较高而强度大,高金属含量同时也改变了刹车片的摩擦特性,通常是指“半金属”刹车片需要更高的制动压力来完成同样的制动效果。
特别是在低温环境中高金属含量同样也就意味着刹车片会引起较大的制动盘或制动鼓的表面磨损,同时会产生更大的噪音。
“半金属”混合物型刹车片(Semi-met)的主要优点在于它的温控能力及较高的制动温度,同石棉型的传热性能差与制动盘、制动鼓的冷却能力差相比它们在刹车时帮助制动盘和制动鼓将热量从其表面上散发出去,热量被传递到制动钳及其组件上。
当然如果这些热量处理不当也会产生问题,刹车液受热后温度会上升,如果温度达到一定水平,将导致制动萎缩和刹车液沸腾。
这种热量同时对制动钳、活塞密封圈及回位弹簧也有一定的影响,会加快这些组件老化,这也是在制动维修时要重新装配制动钳及更换金属件的原因。
无石棉有机物型刹革材料{NAO)
无石棉有机物型刹车材料主要使用玻璃纤维、芳香族聚酷纤维酷或其它纤维(碳、陶瓷等)来作为加固材料,其性能主要取决于纤维的类型及其它添加混合物。
无石棉有机物刹车材料主要是作为石棉的替代晶而研制的,用于制动鼓或制动蹄,但是近期它们也正在开始被尝试用作前盘式刹车片的替代品。
就性能而言,NAO型刹车片更接近石棉刹车片,而不是半金属刹车片。
它不像半金属刹车片那样具有良好的导热性和良好的高温可控性。
新型的NAO原材料与石棉刹车片相比有何不同?
典型的石棉为基础的摩擦材料含有五到七种基础混合物,它们包括加固用石棉纤维、多种添加材料以及粘合剂等,如亚麻仁油、树脂、苯酣醒、树脂。
相比较而言,NAO摩擦材料大约包含十七种不同的棍合物材料,因为去掉石棉不能等同于简单地更换一种替代品,而需要用一大批混合物来保证制动性能,使之持平或超过石棉摩擦块的制动效果。
NAO型刹车片的材料已经历了几次变革,现在的NAO材料在诸多方面已经有效地超过了石棉刹车片的性能,这主要是在抗摩性能及噪音等方面。
当然规范标准首先应确定下来,因为只有这样才能检验任何新的摩擦材料配方。
这些规范中应包括摩擦性能、抗疲劳能力、温度适应性、抗磨损能力以及噪音等。
摩擦材料越好摩擦块在不同的温度及压力下的摩擦性能保持得越好,换句话说,在低温或高温情况下,其性能应变化不大。
摩擦材料越好,反复制动后越不可能出现制动萎缩,这使得“制动踏板感觉”保持良好。
较好的材料同时也会减少磨损,降低噪音。
早先的NAO刹车片只达到了其中一部分的要求,但现在已基本完全达到。
如今的NAO刹车片比石棉刹车片的使用寿命明显延长,同时还有利于延长制动鼓与制动盘的使用寿命。
养护方法
制动蹄片俗称刹车片,属于消耗品在使用中会逐渐磨损,当磨损到极限位置时,必须更换,否则将降低制动的效果,甚至造成安全事故。
制动蹄片关乎生命安全,必须谨慎对待。
1.正常行驶条件下每行驶5000公里对制动蹄片检查一次,不仅要检查剩余的厚度,还要检查蹄片磨损的状态,两边磨损的程度是否一样,回位是否自如等,发现不正常情况必须立即处理。
2.制动蹄片一般由铁衬板和摩擦材料两部分组成,一定不要等摩擦材料部分都磨没了才更换蹄片。
例如捷达(图库论坛)车的前制动蹄片,新片的厚度为14毫米,而更换的极限厚度是7毫米,其中包括3毫米多的铁衬板厚度和近4毫米的摩擦材料厚度。
一些车辆带有制动蹄片报警功能,一旦达到了磨损极限,仪表会报警提示更换蹄片。
达到了使用极限的蹄片必须更换,即使尚能使用一段时间,也会降低制动的效果,影响行车的安全。
3.更换时要换原厂备件提供的刹车片,只有这样,才能使刹车片和刹车盘之间的制动效果最好,磨损最小。
4.更换蹄片时必须使用专用工具将制动分泵顶回。
不能用其他撬棍硬压回,这样易导致制动钳导向螺丝弯曲,使刹车片卡死。
5.更换完后,一定要踩几脚刹车,以消除蹄片与制动盘的间隙,造成第一脚没刹车,易出现事故。
6.制动蹄片更换后,需磨合200公里方能达到最佳的制动效果,刚换的蹄片须谨慎行驶
更换刹车片的原则
更换刹车片时,最好能使用高性能的刹车片,虽然其价格比经济性的刹车片高一些,但其材料要好得多,使用寿命较长,当然安全性也要强得多,因此,一时的高技人肯定会换来更多的回报。
需要提醒车主的是:
更换刹车片时要尽可能使用与旧刹车片具有相同的材质,当然如果能做到新的刹车片材料比原件的材料高一级别就更好。
更换不同材质的刹车片时只有遵循下述两条原则方可保证其安全性。
*尽量不要使用NAO材料的去替换半金属材料的刹车片。
*NAO材料的可替换石棉材料的刹车片。
刹车制动很重要!
常见的汽车制动器解析(组图)
在日常车辆行驶的过程中,最为常用的一项动作就是刹车,为了避免前方的障碍物,或者下坡行驶中为了保持速度问题,都要需用到汽车的制动系统,而实现这一切的动作的核心部件就是制动器。
我们最为常见的两种制动器为鼓式制动器和盘式制动器两种,今天我们就来为大家详细介绍一下这两种制动器。
●鼓式制动器
鼓式制动器的旋转元件是制动鼓,固定元件是制动蹄,制动时制动蹄在促动装置作用下向外旋转,外表面的摩擦片压靠到制动鼓的内圆柱面上,对鼓产生制动摩擦力矩。
凡对蹄端加力使蹄转动的装置统称为制动蹄促动装置,制动蹄促动装置有轮缸、凸轮和楔。
制动器根据动力辅助的方式不同,可以分为以下三种:
以液压制动轮缸作为制动蹄促动装置的制动器称为轮缸式制动器;以凸轮作为促动装置的制动器称为凸轮式制动器;用楔作为促动装置的制动器称为楔式制动器。
其中我们最为常见的制动器就是轮岗式制动器。
下面就来介绍几种轮岗式制动器。
1、领从蹄式
领从蹄式
桑塔纳鼓式制动机
其特点是两个制动蹄各有一个支点,一个蹄在轮缸促动力作用下张开时的旋转方向与制动鼓的旋转方向一致,称为领蹄;另一个蹄张开时的旋转方向与制动鼓的旋转方向相反,称为从蹄。
2、双领蹄和双向双领蹄式
双向双领蹄式制动机
双向双领蹄式
双向双领蹄式
汽车前进时两个制动蹄均为领蹄的制动器称为双领蹄式制动器。
双领蹄式制动器的结构特点是,每一制动蹄都用一个单活塞制动轮缸促动,固定元件的结构布置是中心对称式。
双向双从蹄式制动器使用了两个双活塞轮缸,无论汽车前进还是倒车,都是双领蹄式制动器,故称双向双领蹄式制动器
3、双从蹄式
双从蹄式
汽车前进时两个制动蹄均为从蹄的制动器为双从蹄式制动器。
4、单向和双向自增力式
自增
(1)单向自增力式制动器
其特点是两个制动蹄只有一个单活塞的制动轮缸,第二制动蹄的促动力来自第一制动蹄对顶杆的推力,两个制动蹄在汽车前进时均为领蹄,但倒车时能产生的制动力很小。
(2)双向自增力式制动器
其特点是两个制动蹄的上方有一个双活塞制动轮缸,轮缸的上方还有一个制动蹄支承销,两制动蹄的下方用顶杆相连。
无论汽车前进还是倒车,都与自增力式制动器相当,故称双向自增力式制动器。
点评:
鼓式制动器有内张型和外束型两种,依靠的都是摩擦的原理,由于造价便宜,鼓式制动器的应用非常普遍,但是它有很多的缺点:
制动力稳定性差,不易于掌控;由于散热性能差,在制动过程中会聚集大量的热量;制动块和轮鼓在高温影响下较易发生极为复杂的变形,容易产生制动衰退和振抖现象,引起制动效率下降,等等,而盘式制动器就能改善一部分缺点。
在现实生活中,应用更多更值得信赖的刹车方式是盘式,也就是我们经常听到的“碟刹”,随着盘刹的优势逐渐被认可,因此制动器越来越多的开始采用了盘式刹车。
盘式刹车有什么优势之处呢?
我们先来了解一下:
制动钳
(1)盘式制动器无摩擦助势作用,制动力矩受摩擦系数的影响较小,即热稳定性好;
(2)盘式制动器浸水后效能降低较少,而且只须经一两次制动即可恢复正常,即基本不存在水衰退问题;
定钳盘式制动器
(3)在输出相同制动力矩的情况下,盘式制动器尺寸和质量一般较小;
(4)制动盘沿厚度方向的热膨胀量极小,不会像制动鼓的热膨胀那样使制动器间隙明显增加而导致制动踏板行程过大;
(5)较容易实现间隙自动调整,其他维修作业也较简便。
盘式制动器主要有钳盘式和全盘式两种,现代汽车上应用最多的就是钳盘式制动器,它的旋转元件是制动盘,固定元件是制动钳。
而根据制动钳的运动方式又可分为定钳盘式制动器、滑动钳盘式制动器和钳盘式制动器,其中滑动钳盘式制动器应用更广。
钳盘式制动器的工作原理就类似于自行车上的刹车,在制动过程中,制动钳将制动块挤压到制动盘上,随着制动盘和衬块之间的摩擦逐渐的将速度降下来。
而滑动钳盘式制动器就是制动钳可以相对制动盘作轴向滑动;只在制动盘的内侧设置油缸,而外侧的制动块则附装在钳体上。
盘式制动器在使用过程中,也会出现故障,其中比较常见的有气阻、制动力不足和制动时有噪声等。
盘式制动器的发热部位集中在很窄的制动衬块上,其单位压力又比鼓式制动器大,制动衬块和钳体的活塞直接接触,因此制动时的热量极易传给制动液。
这样,使盘式制动器容易产生气阻现象。
但是,若采取相应的措施,也可防止气阻现象的发生。
植物油型制动液无法满足盘式制动器的使用要求,因此必须使用高沸点的合成制动液。
但是,合成制动液具有吸水特性。
在某些使用条件中,沸点下降很快。
为防止制动液沸点的明显下降,一般常采用以下一些措施:
1、定期更换制动液。
夏季3个月或行驶5000km;冬季6个月或行驶1000km后,即将制动液更新。
制动盘
2、不同性质的制动液不可互换使用或混用。
3、密闭保存制动液。
盘式制动器制动力不足时,可采用下述方法予以解决:
1、改变制动衬块材料,可换用稍软的制动衬块材料,使摩擦系数相对得到提高,制动力变大。
2、清除制动衬块排屑槽中的异物,如果制动衬块的排屑槽被异物覆盖,制动时将失却排出尘土、刮去水分的作用,使制动力降低。
制动时,若有“嗄吱、嗄吱”的噪声时,可采用下述方法排除:
1、在制动器钳体活塞和制动衬片之间,加一防噪声片,使活塞上形成一倾斜度。
从而保证制动时制动衬块和制动盘柔性接触,使制动衬块在正常磨损状态下无异常噪声出现。
2、选择材质软些、密度小些的制动衬块材料。
3、制动时,制动衬块向一侧移动,可能出现撞击声响。
这是由于制动衬块和钳体之间的间隙过大所致,可用镀覆焊锡的方法消除间隙。
但须注意,应使焊锡镀覆在与行驶方向相反的一侧,防止在制动力的作用下失效。
点评:
今天我们简单的了解了盘式制动器的优势以及工作原理,以及日常制动过程中遇到的问题。
它的优点是显而易见的,但也有一些缺点,例如液压制动是管路压力较高,因此需要伺服装置,而其在驻车制动中还需假装驻车传动装置,因为整体构造会很复杂,因此需要的成本也会增高,因此在一些价格较低的车上,会采取前轮盘刹后轮鼓刹的搭配方式。