PCB设计规范.docx
《PCB设计规范.docx》由会员分享,可在线阅读,更多相关《PCB设计规范.docx(22页珍藏版)》请在冰豆网上搜索。
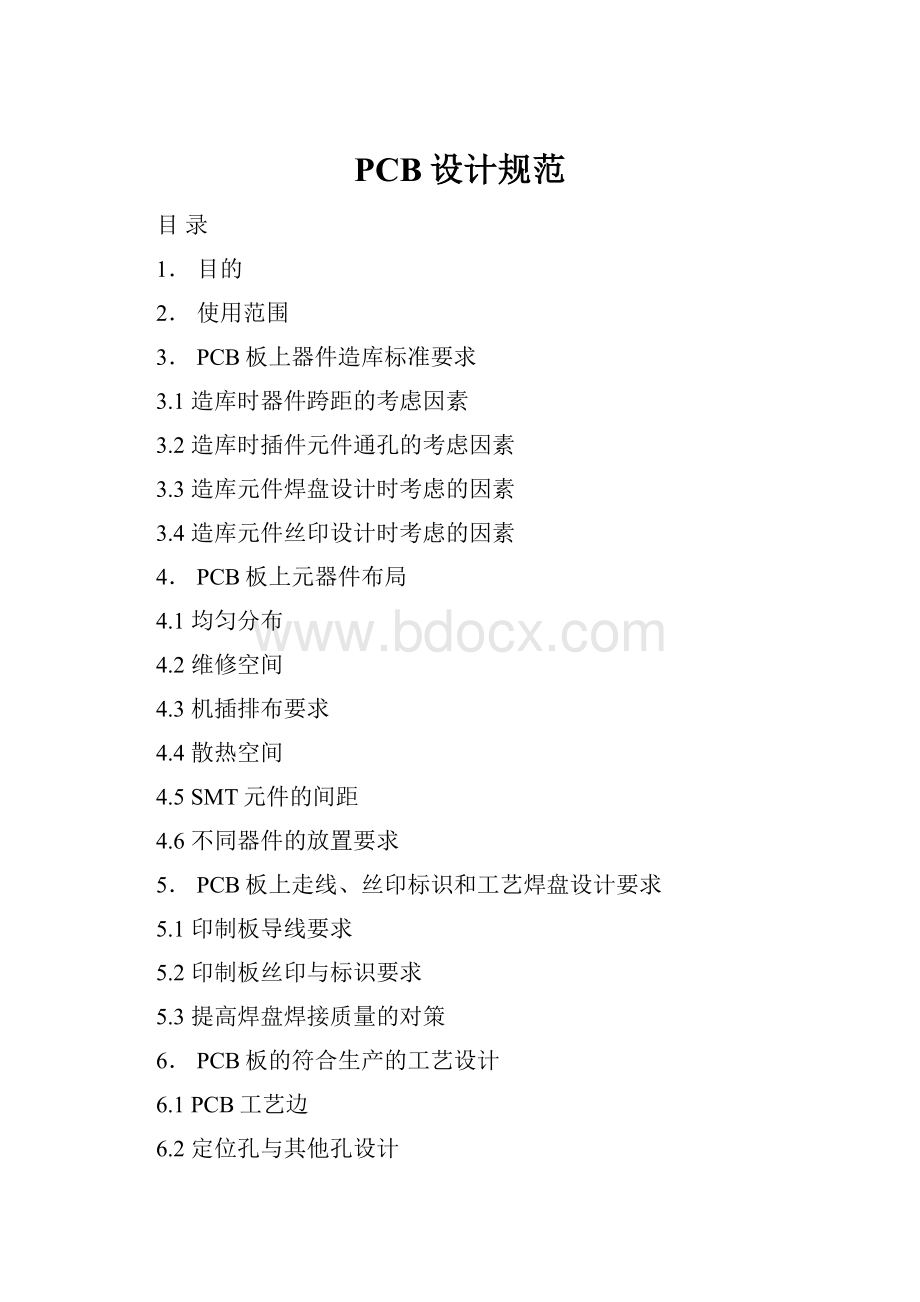
PCB设计规范
目录
1.目的
2.使用范围
3.PCB板上器件造库标准要求
3.1造库时器件跨距的考虑因素
3.2造库时插件元件通孔的考虑因素
3.3造库元件焊盘设计时考虑的因素
3.4造库元件丝印设计时考虑的因素
4.PCB板上元器件布局
4.1均匀分布
4.2维修空间
4.3机插排布要求
4.4散热空间
4.5SMT元件的间距
4.6不同器件的放置要求
5.PCB板上走线、丝印标识和工艺焊盘设计要求
5.1印制板导线要求
5.2印制板丝印与标识要求
5.3提高焊盘焊接质量的对策
6.PCB板的符合生产的工艺设计
6.1PCB工艺边
6.2定位孔与其他孔设计
6.3拼板要求设计
6.4PCB板缺槽
6.5PCB的耐温性能
6.6元器件的耐温要求
6.7印制板的非机插区
7.基准标点(MARK)的制作要求
8.可测性设计的考虑
8.1工艺设计的要求
8.2电气设计的要求
1.目的(返回目录)
针对PCB的设计,为了能够规范化和标准化,以满足生产工艺的要求,特制定本标准。
2.使用范围(返回目录)
本标准适用于和晶公司所有PCB板的设计。
3.PCB板上器件造库标准要求(返回目录)
PCB设计时尽量采用公司设计的标准元器件库中的现成元件库(库中元件均经过批量生产,已经经过验证确认),有利于避免自己设计的元件库因考虑不周导致的失误。
如果元件库中没有现成的元器件,那就需要按照下列具体要求进行设计,并通过部门确认增补进标准元器件库中。
3.1造库时器件跨距的考虑因素:
(返回目录)
卧式器件的跨距必须是2.5mm的整数倍:
5mm、7.5mm、10mm、12.5mm、15mm、17.5mm、20mm、22.5mm等
3.2造库时插件元件通孔的考虑因素:
(返回目录)
⑴未作特别要求时,手插器件引脚的通孔大小规格D按照下式进行设计:
D=d+0.2mm+00.1;
d为元器件脚径,见下图所示
⑵对器件引脚间距≤2.0mm的手插PIN、插座、电容等,引脚的通孔规格为0.8~0.9mm,见下图所示
⑶未作特别要求时,机插器件引脚的通孔大小规格D按照下式进行设计:
D=d+0.4mm+00.1;
d为元器件脚径,见图示3
3.3造库元件焊盘设计时考虑的因素:
(返回目录)
⑴未作特别要求时,通孔安装器件引脚的焊盘大小规格D按照下式进行设计:
D=2d+0.2mm+00.1;
d为通孔孔径大小,见下图所示
⑵对加装铆钉的焊盘,焊盘的直径大小规格D按照下式进行设计:
D=2d+1mm+00.1;
d为通孔孔径大小,见下图所示
⑶对器件引脚间距≤2.0mm的手插PIN、插座、电容等,焊盘的直径大小规格D按照下面分类进行设计:
双面板:
D=d+0.2~0.4mm;
单面板:
D=2d;
d为通孔孔径大小,见下图所示
⑷未作特别要求时,元件孔形状、焊盘与元件脚形状必须匹配,并保证焊盘相对于孔中心的对称性,即方形元件脚配方形元件孔、方形焊盘;圆形元件脚配圆形元件孔、圆形焊盘,窄扁形元件脚配椭圆形(或长方形)孔径与椭圆焊盘,见下图所示
⑸对于需要过波峰焊后才焊的元件,焊盘要开走锡槽,方向与波峰焊走向相反,宽度为0.5~1.0mm(视孔径的大小而定),见下图所示(进行实验)
⑹对于机插器件的焊盘,除满足上述要求外,还需要根据机插元件插入脚打弯勾住印制板的弯脚方向将焊盘加长约1mm,加长焊盘的方式可以是水滴状,也可以如下图。
这样做的好处为:
①防止弯脚碰到旁边铜箔条而短路;②增加弯脚的焊接面积,使焊接可靠。
3.4造库元件丝印设计时考虑的因素:
(返回目录)
⑴器件的丝印应能体现器件的外形大小,保证布局时能确定放置空间大小;方向、电路特征等;
⑵器件的丝印应体现器件的极性,如电解电容、二极管等。
要求在器件放置后便于检验人员识别;
⑶器件的丝印应该明确器件的放置方向,如插座、稳压块、芯片等,要求器件放置后检验人员仍能看到丝印,并根据丝印进行判别器件的摆放方向是否正确;
⑷设计双面板上的器件时针对金属外壳的元件(插件时外壳与印制板接触的),顶层的焊盘不可开,一定要用绿油或丝印油盖住(例如两脚的晶振)。
见下图所示。
⑸器件的焊盘中心距离小于或等于2.54mm的,相邻焊盘周围要用丝印油包裹或隔开,丝印油宽度为0.2~0.5mm(视焊盘之间的宽度而定)
4.PCB板上元器件布局(返回目录)
元器件布局应满足SMT和波峰焊的生产工艺要求,根据不同的工艺要求进行元器件布局设计,正确的设计可以将焊接缺陷降低,在进行元器件布局时要考虑以下几点:
4.1均匀分布:
PCB上元器件分布尽可能的均匀,大体积和大质量的元器件在回流焊时的热容量比较大,布局上过于集中容易造成局部温度过低而导致假焊。
(返回目录)
4.2维修空间:
大型元器件的四周要留有一定的维修空间,不要影响小器件的维修(留出SMD返修设备加热头能够进行操作的尺寸)(返回目录)
4.3机插排布要求:
目前下列卧插器件适用于和晶公司机插设备的机插工艺。
并排的卧插元件(如电阻)间距尽量大于等于2.5mm(注:
原则上还可以小,但要考虑到焊盘不能太窄为好)。
见下图所示。
1跨接线(插入孔间距≥5mm)。
2编带的碳膜电阻。
3编带的小功率金属氧化膜电阻(≤1/2W,注:
较大功率的电阻发热量大,应高架插件,不适宜机插)。
4
编带的二极管(检波、整流或稳压二极管等,注:
某些功率较大的二极管发热量大,应高架插件,不适宜机插)。
5编带的轴向色环电感器。
6编带的轴向电容器。
(返回目录)
4.4散热空间:
(返回目录)
⑴功率器件应均匀的放置在PCB的边缘或整机的通风位置上。
⑵电解电容不可触及发热器件,如大功率电阻、热敏电阻、变压器、散热器等,布局时尽量将电解电容远离以上器件,要求最小间隔为10mm,以免把电解液烤干,影响使用寿命。
⑶其他器件与散热器的间隔距离最小为2.0mm。
4.5SMT元件的间距:
需过波峰焊的贴片元件的焊盘之间的距离如右图所示,防止阴影效应导致零件未焊。
(返回目录)
4.6不同器件的放置要求:
1.贵重元器件不要放置在印制板的角、边缘、安装孔、开槽、拼板的切口和拐角处,以上这些位置是印制板的高受力区,容易造成焊点和元器件的开裂和裂纹。
(返回目录)
2.较重的器件(如变压器)不要远离定位孔,以免影响印制板的强度和变形度。
布局时,应该选择较重的器件放置在PCB的下方(也是最后进入波峰焊的一方)。
(返回目录)
3.会辐射能量的器件如变压器和继电器等要远离放大器、单片机、晶振、复位电路等容易受干扰的器件和电路,以免影响到工作时的可靠性。
4.较轻的器件如二极管和1/4W的电阻等,布局时应尽量相互平行,而且使其轴线和波峰焊方向垂直。
见下图所示(返回目录)
5.多个引脚在同一直线上的器件,如连接器、DIP封装器件、TO220封装器件,布局时应使其轴线和波峰焊方向平行。
见示(返回目录)
波峰焊方向
6.所有极性表面贴装元器件和插件器件在可能的时候都要以相同的方向放置。
7.对于QFP封装的IC(需要使用波峰焊接工艺),必须以45℃方向摆放。
并且加上出锡焊盘。
见右图所示
(返回目录)
8.对于多引脚的元器件(如SOIC、QFP等)引脚焊盘之间的短接处不允许直通,应由焊盘加引出互连线之后再短接,以避免产生侨接。
另外还应该避免在其焊盘之间穿互连线(特别是细间距的引脚元器件)。
凡穿越相邻焊盘之间的互连线,必须用阻焊漆对其加以避隔(返回目录)
9.需要过波峰焊的贴片元件,安放在底面(焊接面)的元件高度必须≤5mm,防止过波峰焊时元件被喷口碰到。
(返回目录)
5.PCB板上走线、丝印标识和工艺焊盘设计要求
5.1印制板导线要求(返回目录)
⑴铜箔的最小线宽:
单面板0.4mm;双面板0.3mm,边缘铜箔最小线宽为0.5mm。
⑵铜箔的最小线间距:
单面板0.4mm;双面板0.3mm,边缘铜箔与板边最小间距为0.5mm(如果PCB边缘是V形割槽,则间距要求0.75mm以上)。
⑶印制板导线应避免呈一定的角度与焊盘相连,只要可能印制板导线应从焊盘的长边中心处与之相连
⑷印制板若有大面积的铜箔走线,应将铜箔走线设计成斜方格形,以降低PCB在过回流焊或波峰焊时遇到高温后的变形度。
方格大小待定
⑸爬电距离与电气间隙为满足安全设计要求,对强弱电间距要求≥6mm;强电线之间距离的要求1mm/100V,因此220V火线零线间距≥3mm。
若空间有限也可以缩小到2.5mm。
⑹铜箔宽度决定能通过电流的能力,基本以1A/mm的比例计算是否满足通载能力,如果不能达到要求的,要增加裸铜面积,经过波峰焊接后能提高通载能力。
增加裸铜的方式以后再详细确定。
⑺大型元器件(如变压器、直径15mm以上的电解电容、大电流插座、IC、三极管等)脚的焊盘要加大铜箔及上锡面积,如图示,阴影部分的面积最小要与焊盘面积相等。
这样做是为了增强焊盘强度与元器件脚的吃锡高度。
⑹铜箔入圆焊盘的宽度较圆焊盘的直径小时,则需加泪滴或用敷铜包围焊盘,增强焊盘强度,避免过波峰焊时将焊盘拉脱,见下图所示。
5.2印制板丝印与标识要求:
(返回目录)
⑴在所有的元器件要有位号丝印(按照标准进行标识),并且能够清晰的表明安装方向与脚位(所有的IC必须要标识第一脚的位置)。
为了方便调试维修。
接插件除有脚位标识之外最好要标注每个脚的对应定义代号。
按键增加功能定义代码标注。
⑵PCB板表面的丝印颜色统一要求,丝印字符统一为水平或90度摆放。
⑶在PCB板的元件插装面必须用实心箭头标出波峰焊时的走向,见图示。
⑷PCB上的保险丝、压敏电阻、变压器初级、交流电输入等高压元件要有高压警示符号,并在相应位置标识该器件的标称值。
印制板的电源输入端应将L和N按照要求进行标识。
⑸在空间许可的情况下,增加电源与接地的测试标注,便于维修与测试。
见右图所示
⑹在所有的PCB板上应醒目标识hodgen字体、公司印制板料号、工程过程检测标记,及客户要求的产品专用号。
⑺所有的上锡位置不能丝印任何阻焊油。
焊盘内不允许印有字符和图形标记,标志符合离焊盘边缘距离应大于0.5mm。
5.3提高焊盘焊接质量的对策(仅做参考):
(返回目录)
⑴焊盘直径≥5mm(方形焊盘长边≥5mm)时,焊盘周边必须增加阻焊漆,阻焊漆宽度0.2~0.5mm。
见下图所示。
⑵焊盘DIP后方有裸铜时,焊盘周边必须加阻焊漆,阻焊漆宽度0.2~0.5mm。
防止焊盘的锡被裸露的铜箔拖走,导致焊点锡薄或锡洞。
见下图所示。
(返回目录)
波峰焊方向
⑶需波峰焊的贴片IC要设计为纵向过锡炉,各脚焊盘之间要加阻焊漆;在最后一脚要设计窃锡焊盘,如受布板尺寸限制无法设计窃锡焊盘时,应将DIP后方与焊盘临近或相连的线路绿漆开发为裸铜,作为窃锡焊盘用。
见下图所示(返回目录)
为保证过波峰焊时不短路
⑷过波峰焊的板,若元件面有贴板安装的器件,其底下不能有过孔或者过孔要盖阻焊漆,否则过波峰焊时焊锡会从过孔冒出导致IC脚短路。
见图示。
⑸焊盘与较大面积的导电区如地、电源等平面相连时,应通过一细颈线(宽度为0.25mm)进行热隔离。
细颈线最小长度为0.5mm。
见下图所示。
(返回目录)
贴片焊盘
通孔焊盘
⑹过波峰焊的插件元件焊盘边缘间距应尽可能大于1.0mm,包括元件本身引脚的焊盘边缘间距,见图示11(返回目录)
⑺相邻焊盘边缘距离≤1mm时,焊盘之间要增加阻焊漆。
见下图所示(返回目录)
相邻焊盘边缘距离≥3mm时,焊盘按照标准焊盘设计,不加拖尾。
见下图所示(返回目录)
⑻同一线路中的相邻零件脚或不同PIN间距的兼容器件,要有单独的焊盘孔,特别是封装兼容的继电器的各兼容焊盘之间要连线,如因线路板布局无法设置单独的焊盘孔,则两焊盘周边必须用阻焊漆围住。
见下图所示。
(返回目录)
⑼接插件、DIP封装的IC或与排件相类似的焊盘,焊盘形状为棱形,在最后过锡脚的焊盘需外后拖尾,拖尾长度为中心孔外外4mm,拖尾的方向根据实际情况决定。
(返回目录)
波峰焊方向
6.PCB板的符合生产的工艺设计
6.1PCB工艺边:
(返回目录)
在SMT、插件过波峰焊的过程中,PCB应留出一定的边缘便于设备夹持。
这个夹持的范围应≥5.00mm,在此范围内不允许放置元器件。
焊盘与板边的最小距离为4.00mm。
如果PCB没有此空间,要设计多板拼装。
6.2定位孔与其他孔设计:
(返回目录)
⑴为了能够保证PCB板准确地进行SMT贴装、ICT检测,需要设置2~4个定位孔,定位孔的大小为4+0.5mm。
在定位孔周围2.5mm的范围内不允许有任何元器件。
⑵安装孔的铜箔面周围2mm内不可有走线(除非是接地用),以免安装过程走线被螺丝或者外壳摩擦损坏,元件面周围3mm内不能有卧式器件,5mm内不能有电解电容、继电器等较高器件,以防止客户装配过程被气批(或电批)碰撞到器件而将其损坏。
⑶对板上有插装元件(如散热器、变压器等)的周围和本体下方其板上不可开散热孔或其他孔,防止过波峰焊时波峰上的锡沾到元件体下或元件脚上,在后工程中不易清理。
但如果PCB不需要进行波峰焊,则表面贴装器件QFP封装的IC底部要增加一个直径为2~3mm的圆形透气孔在板上,这样可以避免SMT贴片过程中的偏位。
⑷对于印制板上的钻孔孔径种类数量应控制在10以内,因为数控钻床安装钻头的数量也只能是10个。
如果设计时超过10个种类的孔径,那印制板厂家就不能严格按照设计的孔径进行加工,而是根据他们的需求调整孔径,这样就会导致印制板孔径与设计文件的钻孔图对应不上,使得印制板检验不合格。
⑸对于印制板上的机插定位孔要求:
1印制板的下边两角应设置机插定位孔。
2(铜箔面朝下时)左下角为主定位孔,该孔孔径为Φ4,孔中心距板左边及下边各为5mm,不能变。
(铜箔面朝下时)右下角为副定位孔,孔径为Φ4×5,孔中心距板下边为5mm,距板右边的距离原则上也为5mm,但必要时可稍作调整。
主副两定位孔的中心距L的优选系列为:
290mm、235mm、350mm。
6.3拼板要求设计:
(返回目录)
拼板的尺寸不可以太大,也不可以太小,以生产、测试、装配工程中便于生产设备的加工和不产生较大变形为宜。
目前公司的生产设备能适用的宽度尺寸为50mm~300mm,宽度为200mm以内较为合理。
拼板上要有单板编号顺序,拼板应以偶数拼合,有利于工程分组管理。
拼板方式可采用邮票孔技术或双面对刻V形槽的分割技术。
在采用邮票孔时,应注意搭边均匀分布在每块拼板的连接处,以避免焊接时由于PCB板受力不均匀而导致变形。
邮票孔的位置应靠近PCB板内侧,防止拼板分离后邮票孔处残留的毛刺影响客户的整机装配。
采用双面V形槽时,V形槽的深度应控制在1/3左右(两边槽之和),要求刻槽尺寸精确,深度均匀。
当设计双面贴装元器件,不进行波峰焊的PCB板时,可采用双数拼板正反面各半,两面图形按相同的排列方式可提高设备的利用率(在中、小批量生产条件下设备投资可以减半),节约生产设备费用和时间。
6.4PCB板缺槽:
(返回目录)
PCB设计和布局时尽量减少印制板的开槽和开孔,以免影响印制板的强度。
PCB板的一些边缘区域内不能有缺槽,以避免印制板定位或传感器检测时出现错误,具体位置因为不同设备而变化。
6.5PCB的耐温性能(返回目录)
印制板的翘曲度要求:
采用表面安装元件的印制板允许的最大翘曲度与扭曲度为0.75%,其他印制板为1%。
对于以拼板形式的印制板应以拼板的翘曲和扭曲度为准。
6.6元器件的耐温要求(返回目录)
PCB上元器件要求应能承受10个回流焊周期,每个周期是215℃(无铅工艺为235℃)、60秒,并能承受在250℃(无铅工艺为260℃)的熔融焊锡中浸没10秒。
6.7印制板的非机插区(返回目录)
板的上下两边距板边5mm范围内及两个机插定位孔周围不能排机插元件;如果有元件,则这些元件不能机插,只能手工插件。
图1.2-1:
机插定位孔及不能机插的区域
7.基准标点(MARK)的制作要求(返回目录)
公司对需要SMT生产的基板上的MARK点的要求(见联络单050624)为:
MARK点直径大小应为1.5~2mm,在以MARK点中心为圆心,半径为2.5mm的范围内应无元器件和焊盘及走线。
PCB上MARK点数量要求3个。
如果由于器件排布密集,无条件在PCB上设置MARK点,可将MARK点放置在工艺边上,放置MARK点的工艺边要求达到8mm的宽度,且要求3个MARK点的位置为工艺边的中心线上。
对于高精度贴片设计时请参考以下规则:
7.1为了精密的贴装元器件,可根据需要设计用于整块PCB的光学定位的一组图形(全局基准点),用于引脚数较多、引脚间距小的单个元器件的单个器件定位图形(局部基准点)。
若是拼板设计,则需要为每块单板设计基准标记,将每块单板单独看待。
(返回目录)
7.2基准图形标记有正三角形、圆、正方形、十字等,推荐采用标记是实心圆和方形标记,直径(或边长)为1mm。
(返回目录)
7.3基准标记大小:
基准点标记最小直径为0.5mm(0.020”),最大直径为3mm(0.120”)。
基准点标记不应该在同一块印制板上尺寸变化超过25微米(0.001”)(返回目录)
7.4基准点的选择:
基准点可以是裸铜、由清澈的防氧化涂层保护的裸铜、镀镍或镀锡层(热风整平)。
电镀或焊锡涂层的首选厚度为5~10微米(0.0002~0.0004”),焊锡涂层不应该超过25微米(0.001”)。
(返回目录)
7.5平整度要求:
基准点标记的表面平整度应在15微米(0.0006”)之内。
7.6对比度要求:
在基准点的标记周围,应该有一块没有其他电路特征或标记空旷区。
空旷区的尺寸最好等于标记的直径3倍。
当基准点标记和印制板的基质材料出现高度对比时可达到最佳的性能。
见右图所示。
(返回目录)
7.7位置要求:
基准点要距离印制板边缘至少5.0mm(smema的标准传输空隙),并满足最小的基准点空旷要求。
(返回目录)
8.可测性设计的考虑
可测性设计主要是针对目前ICT装备情况,将后期产品制造的测试问题在电路和表面贴片印制板设计时就考虑进去。
提高可测性设计要考虑工艺设计和电气设计两个方面的要求。
8.1工艺设计的要求:
(返回目录)
定位的精度、基板的大小、探针的类型都是影响探测可靠性的因素。
⑴精确的定位孔:
在基板上设定精确的定位孔,定位孔误差在+0.05mm以内,至少设置两个定位孔,且距离越远越好。
采用非金属化的定位孔,以减少焊锡层的增厚而不能达到公差要求。
如基板是整片制造后再分开测试,则定位孔就必须设计在主板及各单独单板上。
⑵测试点的直径不能小于1mm(推荐使用直径2mm的测试点)。
相邻测试点的间距最好在2.54mm以上,不要小于1.27mm。
测试点应选择能明显区别于周围焊点不同的形状,便于QC目检。
⑶最好将测试点放置在元器件周围1.0mm以外,避免探针和元器件撞击损伤。
定位孔环状周围3.2mm以内,不可有元器件或测试点。
⑷测试点不可设置在PCB边缘5mm的范围内,这5mm的空间是用来保证夹具夹持。
⑸所有测试点最好镀锡或选用质地较软、易贯穿、不易氧化的金属传导物,以保证可靠的接触,延长探针的使用寿命。
⑹测试不可被阻焊漆或文字油墨覆盖,否则将会缩小测试的接触面积,降低测试的可靠性。
⑺PCB板开模后测试焊盘不能随意移动,除非不得已,但是必须与工程部进行协商,否则可能导致测试ICT和治具报废。
8.2电气设计的要求(返回目录)
⑴要求尽量将元器件面的SMC/SMD的测试点通过过孔到焊接面,过孔的直径应大于1mm。
这样可以在测试时采用单面针床进行测试,从而降低了在线测试夹具的成本。
⑵每个电气节点都必须有一个测试点,每个IC必须有POWER和GROUND的测试点,且尽量接近此元器件,最好在距离IC的2.54mm范围内。
⑶在电路的走线上设置测试点,可将其宽度放大到1mm左右。
⑷将测试点均匀的分布在印制板上。
如果探针集中在某一区域时,较高的压力会使待测板或针床变形,进一步造成部分探针不能接触到测试点。
⑸电路板上的供电线路应分区域设置测试点,便于电源去耦电容或电路上的其他器件出现对电源短路时查找故障点更为快捷准确。
设计断点时,应考虑恢复测试断点后的功率承受能力。
⑹测试点如右图所示。
通过延伸线在元器件引线附件设置测试焊盘。
测试点尽量不要选在元器件的焊点上,这种测试可能是虚焊节点在探针的压力作用下压到理想位置,造成误判;而且会使虚焊焊点在探针因定位误差引起的偏晃,使探针直径作用于元器件的端点或引脚上而造成元器件损坏。
⑺ICT测试点不得以过孔充当(多层板),因为过孔上锡不良较高,测试时与测试针接触不良则容易产生误判不良。