工业金属管道工程质量检验评定标准.docx
《工业金属管道工程质量检验评定标准.docx》由会员分享,可在线阅读,更多相关《工业金属管道工程质量检验评定标准.docx(27页珍藏版)》请在冰豆网上搜索。
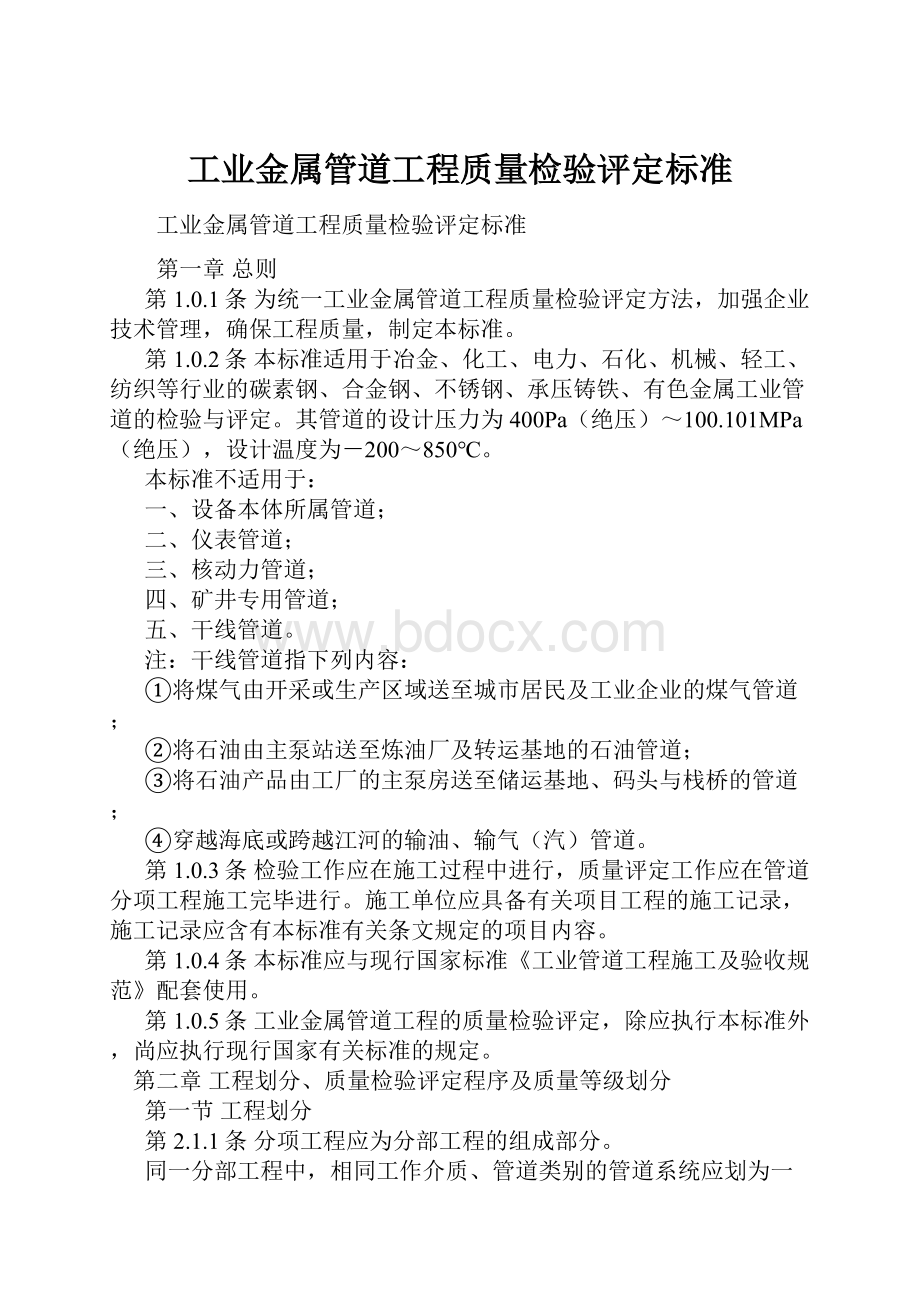
工业金属管道工程质量检验评定标准
工业金属管道工程质量检验评定标准
第一章总则
第1.0.1条为统一工业金属管道工程质量检验评定方法,加强企业技术管理,确保工程质量,制定本标准。
第1.0.2条本标准适用于冶金、化工、电力、石化、机械、轻工、纺织等行业的碳素钢、合金钢、不锈钢、承压铸铁、有色金属工业管道的检验与评定。
其管道的设计压力为400Pa(绝压)~100.101MPa(绝压),设计温度为-200~850℃。
本标准不适用于:
一、设备本体所属管道;
二、仪表管道;
三、核动力管道;
四、矿井专用管道;
五、干线管道。
注:
干线管道指下列内容:
①将煤气由开采或生产区域送至城市居民及工业企业的煤气管道;
②将石油由主泵站送至炼油厂及转运基地的石油管道;
③将石油产品由工厂的主泵房送至储运基地、码头与栈桥的管道;
④穿越海底或跨越江河的输油、输气(汽)管道。
第1.0.3条检验工作应在施工过程中进行,质量评定工作应在管道分项工程施工完毕进行。
施工单位应具备有关项目工程的施工记录,施工记录应含有本标准有关条文规定的项目内容。
第1.0.4条本标准应与现行国家标准《工业管道工程施工及验收规范》配套使用。
第1.0.5条工业金属管道工程的质量检验评定,除应执行本标准外,尚应执行现行国家有关标准的规定。
第二章工程划分、质量检验评定程序及质量等级划分
第一节工程划分
第2.1.1条分项工程应为分部工程的组成部分。
同一分部工程中,相同工作介质、管道类别的管道系统应划为一个分项工程。
该管道系统应根据设计、生产工艺的具体情况划分。
在分部工程中,对工程质量起决定作用的分项工程应划为主要分项工程。
Ⅰ、Ⅱ类管道及有毒、甲、乙类火灾危险介质的管道均应为主要分项工程。
Ⅰ、Ⅱ类管道及有毒、甲、乙类火灾危险介质的管道分类应符合现行国家标准《工业管道工程施工及验收规范》的规定。
第2.1.2条分部工程应为单位工程的组成部分,应按单位工程中的专业进行划分,同一单位工程中的管道工程,应为一个分部工程。
第2.1.3条一个单位工程中,当仅有管道分部工程时,该分部工程应为单位工程。
第二节质量检验评定程序
第2.2.1条质量检验评定工作应按分项工程、分部工程、单位工程的顺序逐级进行。
第2.2.2条分项工程的质量评定工作应在其质量检验工作完毕后进行。
当有一个分项工程的质量评定结果为不合格时,不得进行分部工程的质量评定。
第2.2.3条分部工程、单位工程的质量评定工作应在分项工程质量评定完毕后依次进行。
第2.2.4条当单位工程由几个分包单位施工时,其总承包单位应对工程质量全面负责;各分包单位应按本标准的规定对其承建的分项、分部工程质量进行检验评定,并应将有关资料及评定结果交总承包单位。
第三章管子、管件及阀门的检验
第一节一般规定
(1)保证项目
第3.1.1条管子、管件、阀门及支、吊架弹簧的材质、规格、型号应符合设计要求和规范规定。
检验方法:
检查合格证、质量证明书或复(校)验记录。
检查数量:
应各抽查10%,且不得少于3份。
(Ⅱ)基本项目
第3.1.2条管子、管件、阀门及支、吊架弹簧的表面质量应符合下列规定:
合格:
无裂纹、缩孔、夹渣、折迭、重皮、砂眼、针孔和超过壁厚允许偏差的局部凹坑、碰伤;铸铁管应有制造厂标记;黄铜管无绿锈和严重脱锌,不锈钢管无划痕、锈斑。
优良:
在合格的基础上,表面光洁,合金钢及铸铁管的标记明显、清晰,黄铜管无脱锌,弹簧表面无锈蚀。
检验方法:
观察检查,用小锤敲击,用放大镜、卡钳和测厚仪检查。
检查数量:
应按类型各抽查5%,且不得少于1件。
第二节钢管检验
(Ⅰ)保证项目
第3.2.1条当运到现场的高压钢管钢号、炉罐号与证明书不符或无钢号、炉罐号时,必须进行校验检查,其检查数量、方法、项目、标准等必须符合现行国家标准和《工业管道工程施工及验收规范》GBJ235-82第二章第二节的有关规定。
检验方法:
检查高压钢管校验报告。
检查数量:
应抽查10%。
第3.2.2条高压钢管无制造厂探伤合格证或虽有探伤合格证,但经外观检查发现缺陷时,必须进行无损探伤,其检验结果必须符合设计要求和规范规定。
检验方法:
检查无损探伤报告。
检查数量:
应抽查10%。
第3.2.3条合金钢管子必须有光谱分析或其它复验报告,有耐腐蚀要求的不锈钢管子的耐腐蚀性能试验结果必须符合设计要求和规范规定。
检验方法:
检查光谱分析或其它复验报告、耐腐蚀性能试验结果(报告)。
检查数量:
应各抽查10%,且不得少于3份。
(Ⅱ)基本项目
第3.2.4条高压钢管除去缺陷后的实际壁厚应符合下列规定:
合格:
不小于公称壁厚的90%,且不小于设计计算壁厚。
缺陷修磨处过渡圆滑。
优良:
在合格的基础上,表面光洁。
检验方法:
用测厚仪检查或按规定计算;观察检查。
检查数量:
应抽查10%,且不得少于3处。
第三节承压铸铁管及管件检验
(Ⅰ)保证项目
第3.3.1条承压铸铁管及管件的水压试验结果必须符合设计要求和规范规定。
检验方法:
检查产品质量证明书或水压试验复验报告。
检查数量:
应抽查10%。
(Ⅱ)基本项目
第3.3.2条铸铁管及管件外形尺寸偏差值应符合下列规定:
合格:
符合现行国家标准的规定。
检验方法:
检查合格证及质量证明书。
检查数量:
应抽查10%。
第五节阀门检验
(Ⅰ)保证项目
第3.5.1条阀门的强度和严密性试验结果应符合设计要求和规范规定。
检验方法:
检查出厂合格证或复验试验记录。
检查数量:
应抽查10%,且不得少于3份。
第3.5.2条合金钢阀门和高压阀门每批取10%,且不少于1个进行解体检查,其质量应符合下列规定:
一、材质正确。
二、阀座与阀体结合牢固。
三、阀芯与阀座接触良好,且无缺陷。
四、阀杆与阀芯联接灵活、可靠。
五、阀杆无弯曲、锈蚀,阀杆与填料压盖配合合适,螺纹无缺陷。
六、阀盖与阀体接合良好。
七、垫片、填料、螺栓等齐全,无缺陷。
检验方法:
检查阀门解体记录。
检查数量:
应全部检查。
第3.5.3条安全阀在安装前应铅封良好,标牌上的技术参数符合规定,且阀门经调试后符合要求。
检验方法:
检查安全阀调整试验记录。
检查数量:
应全部检查。
第3.5.4条合金钢阀门应有光谱分析或其它复验报告。
检验方法:
检查光谱分析或复验报告。
检查数量:
应抽查10%,且不得少于3份。
(Ⅱ)基本项目
第3.5.5条阀门的传动装置应符合下列规定:
合格:
启闭灵活可靠,开度指示器指示正确。
优良:
在合格的基础上,用手扳动无卡涩现象。
检验方法:
观察检查,启闭检查。
检查数量:
低压阀门应抽查5%,且不得少于1个;中、高压、合金钢、安装在有毒、剧毒及甲、乙类火灾危险物质管道上的阀门应抽查10%,且不得少于3个。
第3.5.6条公称压力小于或等于2.5MPa的水用铸铁、铸铜闸阀密封面的允许渗漏量应符合下列规定:
合格:
实际渗漏量符合表3.5.6的规定。
优良:
实际渗漏量小于允许渗漏量的95%。
闸阀密封面允许渗漏量 表3.5.6
检验方法:
检查闸阀严密性试验记录。
检查数量:
应各抽查10%,且不得少于3份。
第六节管件检验
(Ⅰ)保证项目
第3.6.1条高压管件及紧固件、中压焊制管件的化学成分、力学性能,合金钢管件的金相分析结果和高压管件的无损探伤结果必须符合现行国家技术标准的规定。
检验方法:
检查产品质量证明书和验收记录。
检查数量:
应各抽查10%,且不得少于3份。
第3.6.2条法兰密封面必须平整光洁,无毛刺和径向沟槽。
法兰螺纹完整、无损伤。
凸凹面法兰能自然嵌合,凸面的高度不低于凹槽的深度。
检验方法:
观察检查。
检查数量:
应抽查10%,且不得少于3件。
第3.6.3条合金钢管件应有光谱分析或其它复验报告;有耐腐蚀要求的不锈钢管件的耐腐蚀性能试验结果应符合设计要求和规范规定。
检验方法:
检查光谱分析或其它复验报告、耐腐蚀性能试验结果(报告)。
检查数量:
应各抽查10%,且不得少于3份。
(Ⅱ)基本项目
第3.6.4条螺栓及螺母的表面质量应符合下列规定:
合格:
螺纹完整,无伤痕。
螺栓与螺母配合良好,无松动或卡涩现象。
优良:
在合格的基础上,螺纹表面干净、无毛刺。
检验方法:
观察检查。
检查数量:
应抽查1%,且不得少于10套。
第3.6.5条石棉橡胶、橡胶、塑料等非金属垫片的质量应符合下列规定:
合格:
质地柔韧,无老化变质,表面无分层和折损。
优良:
在合格的基础上,表面无皱纹等缺陷。
检验方法:
观察检查。
检查数量:
应抽查10%,且不得少于3件。
第3.6.6条金属垫片的质量应符合下列规定:
合格:
材质符合要求,加工尺寸、精度、粗糙度及硬度符合设计要求,表面无裂纹、毛刺、凹槽、径向划痕等缺陷。
优良:
在合格的基础上,表面光洁,无锈斑。
检验方法:
观察检查,检查合格证。
检查数量:
应抽查10%,且不得少于3份(件)。
第3.6.7条缠绕式垫片的质量应符合下列规定:
合格:
材质符合要求,质地柔韧,缠绕紧密。
优良:
在合格基础上不锈钢带点焊牢固,无脱焊痕迹,两平面上的石棉橡胶带高出钢带,无翘曲现象。
检验方法:
观察检查。
检查数量:
应检查10%,且不得少于3件。
第七节支、吊架弹簧检验
(Ⅰ)允许偏差项目
第3.7.1条支、吊架弹簧的允许偏差、检验方法和检查数量应符合下列规定:
一、支、吊架弹簧的允许偏差和检验方法应符合表3.7.1的规定。
支、吊架弹簧的允许偏差和检验方法
表3.7.1
二、检查数量:
应各抽查10%,且不得少于3件。
第四章管道加工
第一节管子切割
(Ⅰ)保证项目
第4.1.1条高压钢管、不锈钢管和合金钢管切割后必须及时正确标上原有标记,且明显、清晰。
检验方法:
观察检查。
检查数量:
应按钢种各抽查5%,且不得少于1件。
第二节弯管制作
(Ⅰ)保证项目
第4.2.1条 高压钢管弯制后,必须进行无损探伤,如果有缺陷,应予消除,其剩余壁厚严禁小于公称壁厚的90%,且不小于设计计算壁厚。
检验方法:
检查高压弯管加工记录。
检查数量:
应抽查10%,且不得少于3份。
第4.2.2条冷弯后的碳素钢、合金钢弯管和有应力腐蚀的弯管的热处理应符合设计要求和《工业管道工程施工及验收规范》GBJ235—82第3.2.7条的规定。
检验方法:
检查热处理记录。
检查数量:
应抽查10%,且不得少于3份。
第4.2.3条合金钢弯管热处理后的硬度值应符合设计要求和《工业管道工程施工及验收规范》GBJ235-82第3.2.8条的规定。
检验方法:
检查热处理记录。
检查数量:
应抽查10%,且不得少于3份。
(Ⅱ)基本项目
第4.2.4条弯管的表面质量应符合下列规定:
合格:
无裂纹、分层、重皮、过烧等缺陷,且过渡圆滑。
优良:
在合格的基础上,表面光洁。
检验方法:
观察检查。
检查数量:
应抽查5%,且不得少于1件。
第4.2.5条高压弯管的壁厚减薄率和椭圆率应符合下列规定:
合格:
壁厚减薄率不超过10%,且弯管的壁厚不小于设计计算壁厚;椭圆率不超过5%。
检验方法:
检查高压弯管加工记录并用测厚仪及卡尺实测。
检查数量:
高压弯管加工记录应抽查10%,实测5%,且不得少于1件。
第4.2.6条除高压弯管外,其它弯管的壁厚减薄率和椭圆率应符合下列规定:
合格:
一、壁厚减薄率不超过15%,且弯管的壁厚不小于设计计算壁厚。
二、椭圆率为:
中、低压管≤8%
铜、铝管≤9%
铜合金、铝合金管≤8%
铅管≤10%
检验方法:
用测厚仪及卡尺实测。
检查数量:
应实测5%,且不得少于1件。
(Ⅲ)允许偏差项目
第4.2.7条中、低压弯管内侧波浪度的允许偏差、检验方法和检查数量应符合下列规定:
一、中、低压弯管内侧波浪度的允许偏差和检验方法应符合表4.2.7的规定。
弯管内侧波浪度的允许偏差和检验方法(mm)
表4.2.7
二、检查数量:
应按钢管、有色金属管分别抽查10%,且不得少于3处。
第三节卷管加工
(Ⅰ)保证项目
第4.3.1条卷管的材质、规格应符合设计要求。
检验方法:
检查卷管加工合格证或加工记录。
检查数量:
应抽查5%,且不得少于1份。
第4.3.2条卷管所有焊缝的质量必须符合设计要求和《工业管道工程施工及验收规范》GBJ235—82第3.3.10条的规定。
检验方法:
检查卷管加工合格证或加工记录。
检查数量:
应抽查5%,且不得少于1份。
(Ⅱ)基本项目
第4.3.3条卷管管段的两纵缝间距、支管外壁与纵、环向焊缝间距应符合下列规定:
合格:
管段两纵缝间距不应小于100mm,支管外壁与纵、环向焊缝间距不应小于50mm;当间距小于前述规定时,应经无损探伤检查合格。
优良:
管段两纵缝间距应大于100mm,支管外壁与纵、环向焊缝间距应大于50mm。
检验方法:
用卷尺、直尺测量或检查无损探伤报告。
检查数量:
不得少于3处。
(Ⅲ)允许偏差项目
第4.3.4条卷管加工的允许偏差、检验方法和检查数量应符合下列规定:
一、卷管加工的允许偏差和检验方法应符合表4.3.4的规定。
卷管加工允许偏差和检验方法(mm)
表4.3.4
二、检查数量:
应按不同规格各抽查1处。
第四节高压管螺纹及密封面加工
(Ⅰ)保证项目
第4.4.1条螺纹加工质量应符合现行国家标准的规定。
检验方法:
检查螺纹加工记录。
检查数量:
应抽查10%,且不得少于3份。
第4.4.2条管端锥角密封面必须无划痕、刮伤、凹陷、啃刀等缺陷,粗糙度严禁高于1.6,平垫密封的管端密封面粗糙度严禁高于6.3,且端面与管子中心线必须垂直。
检验方法:
检查密封面加工记录。
检查数量:
应抽查10%,且不得少于3份。
(Ⅱ)允许偏差项目
第4.4.3条加工后的高压管段允许偏差、检验方法和检查数量应符合下列规定:
一、加工后的高压管段允许偏差和检验方法应符合表4.4.3的规定。
高压管段允许偏差和检验方法
表4.4.3
二、检查数量:
应各抽查10%,且不得少于3份。
第五节夹套管加工
(Ⅰ)保证项目
第4.5.1条套管内的主管如有焊缝,应进行无损探伤检查,其结果必须符合设计要求和规范规定。
检验方法:
检查夹套管加工记录。
检查数量:
应抽查10%,且不得少于3份。
第4.5.2条主管和套管的试验压力和试验结果应符合设计要求和《工业管道工程施工及验收规范》GBJ235-82第3.6.4条、第3.6.5条的规定。
检验方法:
检查夹套管加工记录。
检查数量:
应全部检查。
(Ⅱ)基本项目
第4.5.3条主管与套管间隙、支承块与弯管起弯点距离以及直管段上支承块间距应符合下列规定:
合格:
主管与套管间隙符合设计要求,支承块与起弯点距离为0.5~1.2m,直管段上支承块间距为3~5m。
优良:
在合格的基础上,主管与套管间隙匀称,支承块间距均匀,定位可靠。
检验方法:
检查夹套管加工记录。
检查数量:
应抽查10%,且不得少于3份。
第六节焊制中、低压管件加工
(Ⅰ)允许偏差项目
第4.6.1条焊制中、低压管件尺寸允许偏差、检验方法和检查数量应符合下列规定:
一、焊制中、低压管件尺寸允许偏差和检验方法应符合表4.6.1的规定。
焊制中、低压管件尺寸允许偏差和检验方法(mm)
表4.6.1
二、检查数量:
每种管件应各抽查3件。
第七节补偿器加工
(Ⅰ)基本项目
第4.7.1条“Π”形和“Ω”形补偿器的壁厚减薄率和椭圆率应按本标准第4.2.5条、第4.2.6条的规定进行检验。
(Ⅱ)允许偏差项目
第4.7.2条“Π”形和“Ω”形补偿器的内侧波浪度应按本标准第4.2.7条的规定进行检验。
第4.7.3条补偿器的允许偏差、检验方法和检查数量应符合下列规定:
一、补偿器的允许偏差和检验方法应符合表4.7.3的规定。
补偿器的允许偏差和检验方法(mm) 表4.7.3
二、检查数量:
应按类别各抽查10%,且不得少于1件。
第八节管道支、吊架制作
(Ⅰ)基本项目
第4.8.1条管道支、吊架应符合下列规定:
合格:
支、吊架的型式、材质、加工尺寸符合设计要求。
优良:
在合格的基础上,外形规整、美观。
检验方法:
检查加工合格证或按施工图核对。
检查数量:
应抽查10%,且不得少于3份。
第4.8.2条管道支、吊架焊接质量应符合下列规定:
合格:
焊接牢固、无漏焊、裂纹等缺陷。
优良:
在合格的基础上,焊缝表面光洁,无飞溅物。
检验方法:
观察检查。
检查数量:
应抽查10%,且不得少于3件。
第五章管道焊接
第一节一般规定
(Ⅰ)保证项目
第5.1.1条焊接材料(焊条、焊丝、焊剂等)的牌号、规格应符合设计要求。
材料代用应有材料代用记录。
检验方法:
检查焊接工作记录和材料代用记录。
检查数量:
应全部检查。
第5.1.2条焊接材料的质量必须符合现行国家标准的规定。
检验方法:
检查产品质量证明书或材料复验报告。
检查数量:
应全部检查。
第5.1.3条焊条、焊剂的烘干应符合产品说明书的规定。
检验方法:
检查烘干记录。
检查数量:
应全部检查。
第5.1.4条首次使用的母材或者当焊接方法、焊接材料的型号、成分改变时,所做焊接工艺评定必须符合设计要求和规范规定。
检验方法:
检查焊接工艺评定记录。
检查数量:
应全部检查。
第5.1.5条焊工必须具有符合施焊位置和施焊材质范围的焊工合格证。
检验方法:
检查焊工合格证。
检查数量:
应全部检查。
第二节预热和热处理
(Ⅰ)保证项目
第5.2.1条管道焊前预热及层间温度应符合焊接工艺要求或《工业管道工程施工及验收规范》GBJ235-82第4.3.2条~第4.3.5条的规定。
检验方法:
检查Ⅰ、Ⅱ类管道焊接工作记录。
检查数量:
应全部检查。
第5.2.2条焊后热处理工艺参数及结果应符合焊接工艺要求或《工业管道工程施工及验收规范》GBJ235-82 第4.3.6条~第4.3.9条的规定。
检验方法:
检查热处理记录。
检查数量:
应全部检查。
第三节焊接接头检验
(Ⅰ)保证项目
第5.3.1条对接焊缝表面严禁有气孔、裂纹、夹渣等缺陷。
检验方法:
观察检查。
检查数量:
应抽查10%,且不得少于3道焊缝。
第5.3.2条Ⅰ、Ⅱ级对接焊缝表面严禁有凹陷,Ⅲ、Ⅳ级对接焊缝表面凹陷的深度与长度必须符合《工业管道工程施工及验收规范》GBJ235-82表4.4.2的规定。
检验方法:
观察检查和用焊接检验尺检查。
检查数量:
应抽查10%,且不得少于3道焊缝。
第5.3.3条焊缝无损探伤应符合设计要求或《工业管道工程施工及验收规范》GBJ235-82第4.4.3条~第4.4.6条的规定。
检验方法:
检查无损探伤报告和焊缝位置单线图。
检查数量:
应全部检查。
(Ⅱ)基本项目
第5.3.4条对接焊缝咬边应符合下列规定:
合格:
焊缝咬边深度不超过0.5mm,每道焊缝咬边长度不超过焊缝全长的10%,且小于100mm。
优良:
Ⅰ、Ⅱ类管道焊缝无咬边,Ⅲ、Ⅳ、Ⅴ类管道焊缝咬边深度不超过0.5mm,咬边长度不超过焊缝全长5%,且不大于50mm。
检验方法:
观察检查和用焊接检验尺测量。
检查数量:
应抽查10%,且不得少于3道焊缝。
第5.3.5条角焊缝外观质量应符合下列规定:
合格:
焊脚高度符合设计规定,表面无裂纹、气孔、夹渣等缺陷,咬边深度不大于0.5mm。
优良:
在合格的基础上,外形平缓过渡。
检验方法:
观察检查和用焊接检验尺测量。
检查数量:
应抽查10%,且不得少于3道焊缝。
(Ⅲ)允许偏差项目
第5.3.6条对接接头的焊缝余高、外壁错边量、接头平直度的允许偏差、检验方法和检查数量应符合下列规定:
一、对接接头的焊缝余高、外壁错边量、接头平直度的允许偏差和检验方法应符合表5.3.6的规定。
焊缝余高、外壁错边量、接头平直度的允许偏差和检验方法(mm)
表5.3.6
注:
b为焊缝宽度。
二、检查数量:
应抽查1