油气润滑系统.docx
《油气润滑系统.docx》由会员分享,可在线阅读,更多相关《油气润滑系统.docx(17页珍藏版)》请在冰豆网上搜索。
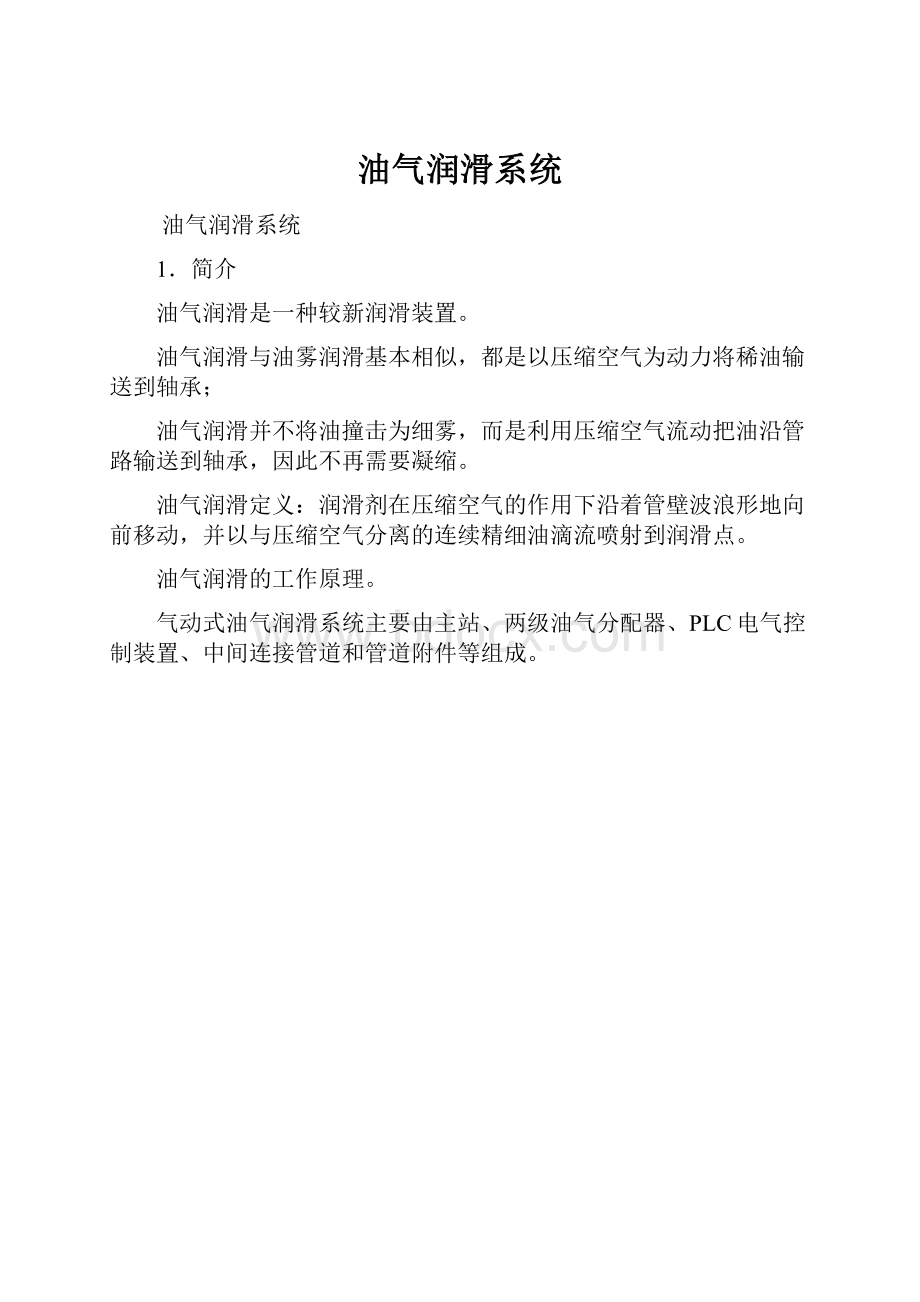
油气润滑系统
油气润滑系统
1.简介
油气润滑是一种较新润滑装置。
油气润滑与油雾润滑基本相似,都是以压缩空气为动力将稀油输送到轴承;
油气润滑并不将油撞击为细雾,而是利用压缩空气流动把油沿管路输送到轴承,因此不再需要凝缩。
油气润滑定义:
润滑剂在压缩空气的作用下沿着管壁波浪形地向前移动,并以与压缩空气分离的连续精细油滴流喷射到润滑点。
油气润滑的工作原理。
气动式油气润滑系统主要由主站、两级油气分配器、PLC电气控制装置、中间连接管道和管道附件等组成。
主站是润滑油供给和分配,压缩空气处理、油气混合和油气流输出以及PLC电气控制的总成。
根据受润滑设备的需油量和事先设定的工作程序接通气动泵。
压缩空气经过压缩空气处理装置进行处理。
润滑油经递进式分配器分配后被输送到与压缩空气网络相连接的油气混合块中,并在油气混合块中与压缩空气混合形成油气流从油气出口输出进入油气管道。
在油气管道中,由于压缩空气的作用,使润滑油沿着管道内壁波浪形地向前移动,并逐渐形成一层薄薄的连续油膜。
经油气混合块混合而形成的油气流通过油气分配器的分配,最后以一股极其精细的连续油滴流喷射到润滑点。
油气分配器可实现油气流的多级分配。
由于进入了轴承内部的压缩空气的作用,即使润滑部位得到了冷却,又由于润滑部位保持着一定的正压,使外界的脏物和水不能侵入,起到了良好的密封作用。
2.目前的应用情况
德国克虏伯钢厂的一套四机架冷带钢连轧机,1—3机架采用正弯辊,第4机架采用正弯辊,轧制速度约1350m/min,弯辊力正弯40t,负弯35t。
工作辊轴承采用四列圆锥轴,用脂润滑,轴承寿命平均约1200h。
改为油气润滑,使用一般极压齿轮油(DIN51502),黏度为220mm2/s,每轴承耗油量每1h为0.02L,总耗油量仅为耗脂量的十分之一。
工作辊轴承寿命提高3倍多,平均达到4000h。
前苏联新利比兹克钢厂的一套五机架冷带钢轧机,其设计参数与我国宝钢的冷轧机同,轧制压力约3000t,设计轧速1800m/min,弯辊力约52t,由于热轧板形等原因,实轧制速度限制在1200m/min。
工作辊轴承采用四列圆锥轴承用脂润滑时,轴承寿命平为800h。
将工作辊轴承改为油气润滑,采用西德的油气润滑装置,轴承寿命大幅提高。
其他如德国、比利时、卢森堡等国轧机轴承都已改造为油气润滑,现在德国设计制的轧机轴承已经不再使用脂润滑了,都采用新式的油气润滑装置。
武钢冷轧厂五机架连轧机工作辊轴承是四列圆锥轴承,使用脂润滑时,平均寿命较自己改为德国REBS公司设计制造的油气润滑装置,收到良好效果。
后来的HC轧机轧辊轴也是采用油气润滑。
3.工作原理
利用压缩空气在管道内的流动,带动润滑油沿管道内壁不断地流动,把油气混合叫输送到润滑点。
4.油气润滑系统组成
油气润滑系统分为三大部分:
供油部分、供气部分、油气混合部分。
(1)供油部分
这部分有油箱,油泵、步进式给油器等主要元件,都是根据系统的供油量选定的。
步进式给油器排出的油一个一个的输送到油气混合器去,
(2)供气部分
供给的压缩空气应该是清洁而干燥的,必须先经过油水分离及过滤。
(3)油气混合部分
油和气在混合器中要使油能很好的雾化成油滴,均匀地分散在管道内表面,
5.油气润滑的优点
1)有利于环境保护。
没有油雾,周围环境不受污染。
2)精密计量。
油和空气两个成分都可分别准确计量,按照不同的需要输送到每一个润滑点,这是一个非常经济的系统。
3)与油的黏度无关。
凡是能流动的油都可以输送。
它不存在高黏度雾化困难的问题,因为它不需要雾化。
4)可以监控。
系统的工作状况很容易实现电子监控。
5)特别适用于滚动轴承,尤其是重负荷的轧机辊颈轴承,气冷效果好,可降低轴承的运行温度,从而延长轴承的使用寿命。
6)耗油量微小。
仅为耗脂量的1/10~1/20。
6使用实例
油气润滑在冷轧机中应用探讨
前言
目前在冷轧机组中,如冷轧普通钢板带轧机、冷轧铝板轧机、铝箔轧机和其它有色金属板带轧机以及板带的平整机和光整机等,轧机轴承通常采用串列轴承,主要装设在工作辊、中间辊和支承辊上。
轴承的润滑方式主要有干油润滑、稀油润滑和油雾润滑等。
轧机轴承的工况条件有如下几个突出特点:
一轴承负荷大,轴承座内装配有四列圆锥滚子轴承或四列圆柱滚子轴承,整个轴承的直径和宽度相对较大;
二润滑部位点多面广,润滑困难。
由于是串列轴承,存在多个摩擦副,辊颈处的密封也需要润滑,在供给润滑时应采取快速和渗透性强的方式并在轴承座内对润滑进行二次分配,既要求润滑剂能够快速地渗透到各个摩擦副,同时还要考虑以不同的润滑量分别供给轴承和辊颈密封;
三由于采用了工艺轧制液(乳化液等),轴承座受到乳化液的冲刷,乳化液不可避免地侵入到轴承座危害轴承;
四由于工艺的需要,轧辊在每轧制2~3班后就必须更换。
因此轧机轴承由于润滑不良而频繁损毁,严重时甚至使轴承座和轧辊报废,不仅导致很大的设备和停机损失,废品率提高,而且备件和维修费用也不堪重负,并长期污染环境。
另外,由于润滑系统的干油或稀油的外泄对乳化液及乳化液系统等构成严重影响甚至缩短了乳化液的更换周期,并影响带钢表面质量等,这给冷轧生产带来了诸多困难和挑战。
因此,在冷轧带钢生产中,传统的轧机轴承润滑方式如干油润滑、稀油润滑或油雾润滑已难以满足现代生产的需要,采用一种新型的润滑技术代替原有的润滑方式势在必行,目前油气润滑以它独有的优势在冷轧机组中逐渐得以推广。
例如油气润滑在攀钢冷轧、本钢冷轧的改造项目以及在宝钢、武钢、首钢等大型钢厂新建的冷轧项目中,轧机的工作辊和中间辊轴承润滑多采用了油气润滑技术,使用效果较好。
1油气润滑系统的原理分析
将单独供送的润滑剂和压缩空气进行混合,并形成紊流状的油气混合流后再供送到润滑点,这个过程就是油气润滑。
油气润滑系统的作用是形成油气并对油气进行输送和分配,由以下几个部分组成:
供油及油量分配部分;供气部分;油气混合部分;.油气输送、分配及监控部分;电控装置。
在油气润滑系统工作时,根据受润滑设备的需油量和事先设定的工作程序接通气动泵。
压缩空气经过处理装置进行净化。
润滑油经递进式分配器分配后被输送到与压缩空气网络相连接的油气混合块中,并在油气混合块中与压缩空气混合形成油气流从油气出口输出进入油气管道。
在油气管道中,由于压缩空气的作用,使润滑油沿着管道内壁波浪形地向前移动,并逐渐形成一层薄薄的连续油膜。
经油气混合块混合而形成的油气流通过油气分配器的分配,最后以一股极其精细的连续.油气流喷射到润滑点上。
油气分配器可实现油气流的多级分配。
进入轴承内部的压缩空气,既使润滑部位得到了冷却,又由于润滑部位保持着一定的正压,使外界的脏物和水不能侵入,起到了良好的密封作用。
2..油气润滑与传统润滑方式的比较分析
油气润滑被称为气液两相流体冷却润滑技术,是一种新型的润滑技术。
它与传统的单相流体润滑技术相比,由于其成功地解决了干油润滑、稀油润滑和油雾润滑所无法克服的难题,因此它具有其他润滑方式无可比拟的优越性。
油气润滑与传统润滑方式的技术特性比较见表1。
润滑三种方式的主要比较分析如下:
1)润滑剂的利用率:
干油润滑的大部分润滑剂会从轴承座的密封处排出,仅仅起填充及密封作用,并不能真正起润滑作用,浪费严重,其耗油量是油气润滑的20~100倍。
稀油润滑的部分润滑剂从轴承座的密封处排出,真正起润滑作用的润滑剂不到2%,大部分润滑剂用于冷却作用,所有油品使用一段时间之后必须全部更换;由于漏损及使用一段时间之后油品须全部更换,因此实际耗油量是油气润滑的10~30倍。
油雾润滑虽然仅有少量的润滑剂从轴承座排出,但因润滑剂粘度大小的不同而雾化率不同,对润滑剂的利用率也只有约60%或更低;其耗油量是油气润滑的10~12倍。
而油气润滑由于耗油量极小,只有微量的润滑剂从轴承座排出,如果做成循环型系统,可实现零排放,其润滑剂100%被利用,其耗油量是干油润滑的1/20~1/100;是稀油润滑的1/10~1/30;是油雾润滑的1/10~1/12。
2)系统给油的准确性及调节能力:
干油润滑和稀油润滑能实现定时定量给油,可以在一定范围内对给油量进行调节。
油雾润滑的加热温度、环境温度以及气压的变化和波动均会使给油量受到影响,不能实现定时定量给油,对给油量的调节能力极其有限。
而油气润滑不仅可实现定时定量给油,而且可在极宽的范围内对给油量进行调节。
3)在恶劣工况下的适用性:
干油润滑的轴承座内没有正压,外界脏物、水或有化学危害性的流体会侵入轴承座并危害轴承;不适用于对高速(或极低速)、重载、高温和轴承座易受外界侵蚀的场合。
稀油润滑的轴承座内基本没有正压,外界脏物、水或有化学危害性的流体会侵入轴承座并危害轴承;虽可用于高速(或极低速)、重载场合,但对高温环境的适应性差,不适用于轴承座易受外界侵蚀的场合。
油雾润滑的轴承座内的正压较小,在0.02bar以下,不足以阻止外界脏物、水或有化学危害性的流体侵入轴承座并危害轴承;在高速、高温和轴承座易受外界侵蚀的场合适用性差;不适用于重载场合。
而油气润滑的轴承座内的正压较大,约0.3bar~0.8bar,可有效防止外界侵蚀;适用于高速(或极低速)、重载、高温和轴承座易受外界侵蚀的场合。
4)系统监控性能:
干油润滑、稀油润滑和油雾润滑的监控性能较弱或一般;而油气润滑所有动作元件和流体均能实现自动监控。
5)轴承使用寿命和投资收益:
在轧机轴承润滑中,干油润滑和稀油润滑的轴承使用寿命较短或一般;投资收益一般,消耗大,成本高。
油雾润滑的轴承使用寿命适中;投资效益较好。
而油气润滑的轴承使用寿命很长;投资效益最优。
6)系统的环保性:
干油润滑大量的油脂从轴承座中溢出并污染环境或其它介质(水、乳化液等),使用过的干油处理困难且须花费一定费用,每次更换轴承时都要对轴承上粘附的厚厚的油脂进行清洗。
稀油润滑的部分稀油从轴承座中溢出并污染环境或其它介质(水、乳化液等)。
油雾润滑在雾化时有20%~50%的润滑剂通过排气进入外界空气中成为可吸入油雾,对人体有害并污染环境。
而油气润滑的润滑油不会被雾化,也不和空气真正融合,油品利用率高,对外界污染极小。
如果做成循环型系统,可实现零排放。
3..结论
综上所述,油气润滑.技术比传统的干油润滑、稀油润滑和油雾润滑技术具有明显的优越性,同时一些冷轧厂的生产实践也证明了油气润滑技术在冷轧生产上的采用是成熟可靠、经济环保的,值得推广。
由于采用油气润滑,不仅提高了轧辊轴承的使用寿命,降低了轴承的消耗和维修费用,而且提高了轧机设备的作业率。
同时,润滑剂的消耗大幅度降低,既节约了成本,又减少了污染,还降低了水处理的费用。
油气润滑作为新一代的高效节能润滑方式已经在世界范围内获得了越来越广泛的应用。
随着我国环保标准的日益提高以及清洁能源和节能技术的应用,在冶金行业尤其是在冷轧机和连铸机上,油气润滑的应用越来越普遍,国内已有不少冷轧项目和连铸机上采用了油气润滑技术。
油气润滑技术在冷轧项目上的优势主要表现为:
1)对处于大轧制力、高温状态运行的轴承的降温效果明显,轴承能维持在相对较低的温度下运行,从而使轴承寿命有了明显的提高。
轴承寿命比采用传统润滑方式提高3~6倍,大幅降低了轴承消耗费用和备件费用。
2)润滑油的消耗量很低,每个轴承每小时只需1mL~2mL润滑油即可满足润滑要求,其耗油量仅为其它润滑方式的1/5以下,对润滑油的利用率极高,经济性显著。
3)润滑油在管道中输送时温度较低,不会像干油那样受高温影响结块并堵塞管道进而导致润滑失效;更重要的是系统监控完善,可避免像油雾润滑那样出现轴承无润滑运转的现象。
4)不污染生产环境和轧制乳化液。
油气润滑既不会污染环境,又不会对乳化液系统等构成严重影响甚至缩短乳化液的更换周期,同时由于压缩空气在轴承座内保持正压,也可有效防止外界杂物尤其是乳化液侵入轴承座危害轴承。
高温区域设备油气润滑技术
前言
高速线材生产线的斯太尔摩运输线(以下简称STM)是辊道式运输线,全长110米,安装辊子约420只,采用分段集中驱动方式,滚子链传动。
辊子两端各用一只带座轴承支撑。
根据产品规格的不同、急冷和缓冷等控冷方式的需要,STM辊道运行的速度可以从30m/min~60m/min进行调整。
辊道辊子的轴承原采用干油集中润滑的方式,由于环境温度较高,平均在700C以上,极容易导致干油融化或在管路内干结,造成润滑脂不能到达润滑点。
另外,由于区域环境粉尘大,尤其是细碎的氧化铁皮多,容易导致轴承卡死、辊颈磨损断裂等故障,制约正常生产。
针对问题,我们认真分析和研究,结合油气润滑方式的原理和优点,对其中的一段问题较多的辊道轴承润滑进行改造,将油脂润滑改为油气润滑,取得了良好的效果,不仅提高了零部件使用寿命,减少了轴承润滑不良而卡死的故障,生产效率得到提高,也改善了周围的环境。
1..存在的问题及原因分析
STM辊子轴承润滑原采用油脂润滑,润滑脂采用高温脲基脂,在使用中存在以下问题:
1)油量难以调节。
由于油脂润滑的工作方式的原因,在使用过程中,难以对供油量进行精确调节。
由于现场环境温度较高,且管线较长,如给油量调节过小,给油间隙过长,则容易导致管线内部干油干结堵塞管路现象,从而导致轴承供油不畅,轴承卡死;如油量调节过大,间隙时间过短,则容易导致干油过剩,融化堆积于现场,污染环境,并导致燃烧。
2)多余的堆积干油难以处理,且易引起燃烧,
构成隐患。
为了达到优良的产品性能,我们生产的产品很多需要在盖上STM保温罩,降低辊道运行速度,对线卷进行缓冷!
导致STM辊道区域环境温度非常高,干油极易融化,融化了的干油不仅污染环境,而且高温经常会引发废油燃烧,尤其在夏季高温时间,燃烧更加频繁,构成了一个比较严重的火险隐患。
但是为了防止因润滑不良造成的轴承卡死、链条断裂等设备故障,我们不得不缩短给油周期,因此,每年消耗大量的高温油脂。
3)由于现场环境氧化铁皮较多,相当多的氧化铁皮微粒漂浮并粘结在轴承表面的干油上,并被带入轴承座内,干油混合进氧化铁皮,形成了具有一定危害的磨削剂,损坏轴承,大大降低了轴承的使用寿命,并会磨损辊子辊颈,导致辊颈断裂,造成故障停机,影响生产。
2..油气润滑的原理及特点
2.1..油气润滑的基本原理
如图1所示,油气润滑是基于润滑剂在管路中的附壁效应!
利用气流将润滑剂输送到润滑点处的技术。
润滑剂是有粘度的,当气流以一定的速度在管路中流动时,润滑油受到压缩空气的吹动,沿管道内壁以螺旋状方式不断地向前流动并逐渐形成精细、连续的油流进入润滑点,润滑剂下层附着在管壁上,上层被气流吹动向前输送,因此,滴状润滑剂就会被吹成线状油流向前输送。
经过一段距离的管路输送后,间断供应的润滑剂就会形成连续的油流进入润滑点,对润滑点形成连续润滑,从油气混合块到润滑点的管路距离最短为0.5米,最长可达100米。
且油气润滑具有气液两相膜液体润滑的强承载性能和减磨作用,气液两相膜的厚度要比单相液体膜厚,承载能力比较高,由于油膜厚度的增加,使润滑膜形成率提高,减少了相对运动的摩擦副之间的直接接触机会,并减轻了摩擦副之间的摩擦,使摩擦副始终保持均匀、连续、稳定的润滑膜,保证摩擦副良好的润滑状态。
图1润滑原理图
2.2油气润滑的特点
1)润滑效率高:
在润滑过程中,润滑油的用量其实并不是越多越好。
以轴承的润滑为例:
如下图所示,润滑效果实际上存在一个临界点,当给油量增大到一定程度时,大量的润滑油带走轴承产生的热量,因此轴承的温度就会呈现下降趋势,这正是传统润滑方式中我们所希望看到的良好的润滑效果。
在这条曲线的中部,温度值是最高的,因为此时给油量还没有达到足以带走轴承产生的热量的地步而润滑剂本身也会发热的缘故。
图2润滑曲线图
而油气润滑系统是利用了上图2中两条曲线的最低点区域,也就是给油量最小的地方,此时的给油量可以满足润滑点的润滑需要,足以在摩擦表面形成润滑油膜;图中可见只要极少量的润滑油就可以使润滑点处于温度和摩擦最小的状态。
因此实现润滑剂的100%被利用,效率极高。
2)油气润滑效果好。
由于油气本身原理上的优势,轴承的工作环境从以下几个方面得到明显改善:
a、由于油气润滑系统给每一个轴承的润滑剂保持在最低水平,因此可以消除润滑剂本身的摩擦发热;
b、油气润滑系统有压缩空气在轴承座内部形成正压,防止周围环境中的灰尘、氧化铁皮、水蒸气等不利于轴承润滑的杂质进入轴承座,保持轴承的清洁,客观上起到气封的作用;
c、压缩空气同时可以将轴承自身摩擦产生的细微金属微粒迅速清理干净;
d、压缩空气的比热小,并且是连续送入轴承座,可以明显降低轴承温度。
3)润滑剂消耗量极少,运行和维护费用低。
如前所述,油气润滑系统由于采用先进的润滑工作机理,因此在可以保证轴承获得正常润滑油膜的前提下,所需要的润滑剂的消耗量是采用传统意义上的润滑系统所无法想象的一个数量。
这个数量仅仅是干油润滑情况下润滑剂消耗量的几十分之一。
在大多数冶金企业的实际应用情况来看,采用一套油气润滑系统的耗油量甚至比采用稀油润滑站的情况下的泄漏量还要少。
并且油气润滑所需要的润滑剂仅需要普通的工业齿轮油即可,无需选用昂贵的特制油品。
4)有效改善环境,排除火灾隐患.在油气润滑的过程中,可以根据现场的使用情况,适当调节油量,又油气润滑的给油量本来就很小,所以并不会在现场留下过多残留油液,少量油液也会及时蒸发,从而彻底解决了油液残留堆积问题,现场环境较好,更从根本上解决了火灾隐患的问题。
5)系统结构简单,可靠,可实现监控.工作原理简单,配管简洁明了,动作稳定可靠。
主要分配器及油气混合块安装在全封闭的结构中,因此其可以最大限度避免周围恶劣环境中杂质的侵入造成油气混合块的失效。
3设计系统基本原理及构成方案
改造范围为斯太尔摩风冷线第48只辊子至第190只辊子。
此段运输线主要相关技术参数:
a、长度:
37008mm;
b、跨度:
2060mm;
c、距油站安装位置高度:
5m左右;
d、辊子数量:
100只;
e、轴承数量:
200只;
f、轴承型号:
UCP209
3.1..基本原理及构成方案
泵站:
泵站采用双齿轮泵装置,一用一备,泵装置1.0L/MIN,额定工作压力为60BAR。
油箱:
500L。
设置在STM下面。
泵站开始工作时,一个齿轮泵开始工作,2位二通阀得电,润滑油经过单向阀、安全阀、过滤器到出口,系统压力上升;出口处安装数显示压力发讯器;当管路中的压力到达分配器的工作压力30BAR时,压力发讯器发出信号到电控系统,经过保压延时3-10S(视现场情况而定,初始设置为3S),系统进入间歇时间;间歇时间内,二位二通阀失电,系统卸压到5BAR以下。
压力发讯器发讯点可调,初始设置为30BAR。
泵站有温度开关控制油加热器工作,保证润滑油油温在45C左右;
液位传感器自动低液位报警,同时有空气管路压力发讯器低压报警。
润滑油需经过VOE-B油气分配器进行分配,每点油量由分配器上DEB定量块型号决定。
润滑油:
N100或N220工业齿轮油。
油气分配器:
WOERNERVOE-B/6/2-7/7/7/7/7/7/P20只。
以下是油气分配器的工作原理示意图,见图3。
油气分配器负责在油路卸荷阀得电回油管路开通系统卸荷后,把经过混合的油气混合润滑油滴吹喷到各润滑点。
压缩空气系统在气源后面安装了气动三联件和常闭式二位二通阀,压缩空气压力设定值2.5bar;另,油、气压力开关各一套。
图3油气分配器工作原理示意图
3.2..供气量及油耗计算
预想改造的辊子数量为100只(从第2只保温罩至第8只保温罩共100只辊子),系统润滑点数为200点,耗气量及耗油量见表1。
3.3..电气控制
泵站带液位传感器自动低液位报警;同时有空气管路压力发讯器低压报警;低油压报警。
控制采用PLC。
系统设计原理示意图如图4。
图4设计原理图
4..使用效果
对STM辊子轴承进行油气润滑改造后,经过一段时间的使用,基本上解决了原来的润滑方式所存在的问题,取得了很好的实际效果。
1)润滑效果较好,润滑效率较高,在润滑剂较少的情况下起到较好的润滑效果,且压缩空气一定程度上降低了轴承内部的温度,使轴承寿命得到了显著的提高,大大减少了因此而带来的设备维护工作量,由于润滑而产生的故障停机大大减少,提高了生产效率。
2)稀油良好的流动性及压缩空气形成的正压作用防止了氧化铁皮的附着,使轴承及轴径部位相当清洁,润滑良好,无氧化铁皮黏附。
3)与干油润滑比较,油气润滑系统选用油品的粘度范围很广、用油量少,润滑油利用率高;油气润滑系统产生废油少、回收方便,更加清洁环保。
4)现场较干油润滑,更加清洁,无堆积油污,更未发生起火现象。
5)供油量及喷油频率还需在实践中摸索调整,以期达到最好的效果。
5..结语
以往油气润滑技术多应用于高速、高温等场合,本次技术改造的成功,说明了在高温、低转速的工况下采用油气润滑技术方式润滑也是比较合适的选择。
因此,对于油气润滑的应用推广也是一次比较好的实践,积累了经验。