打火机底壳模具设计学位论文.docx
《打火机底壳模具设计学位论文.docx》由会员分享,可在线阅读,更多相关《打火机底壳模具设计学位论文.docx(16页珍藏版)》请在冰豆网上搜索。
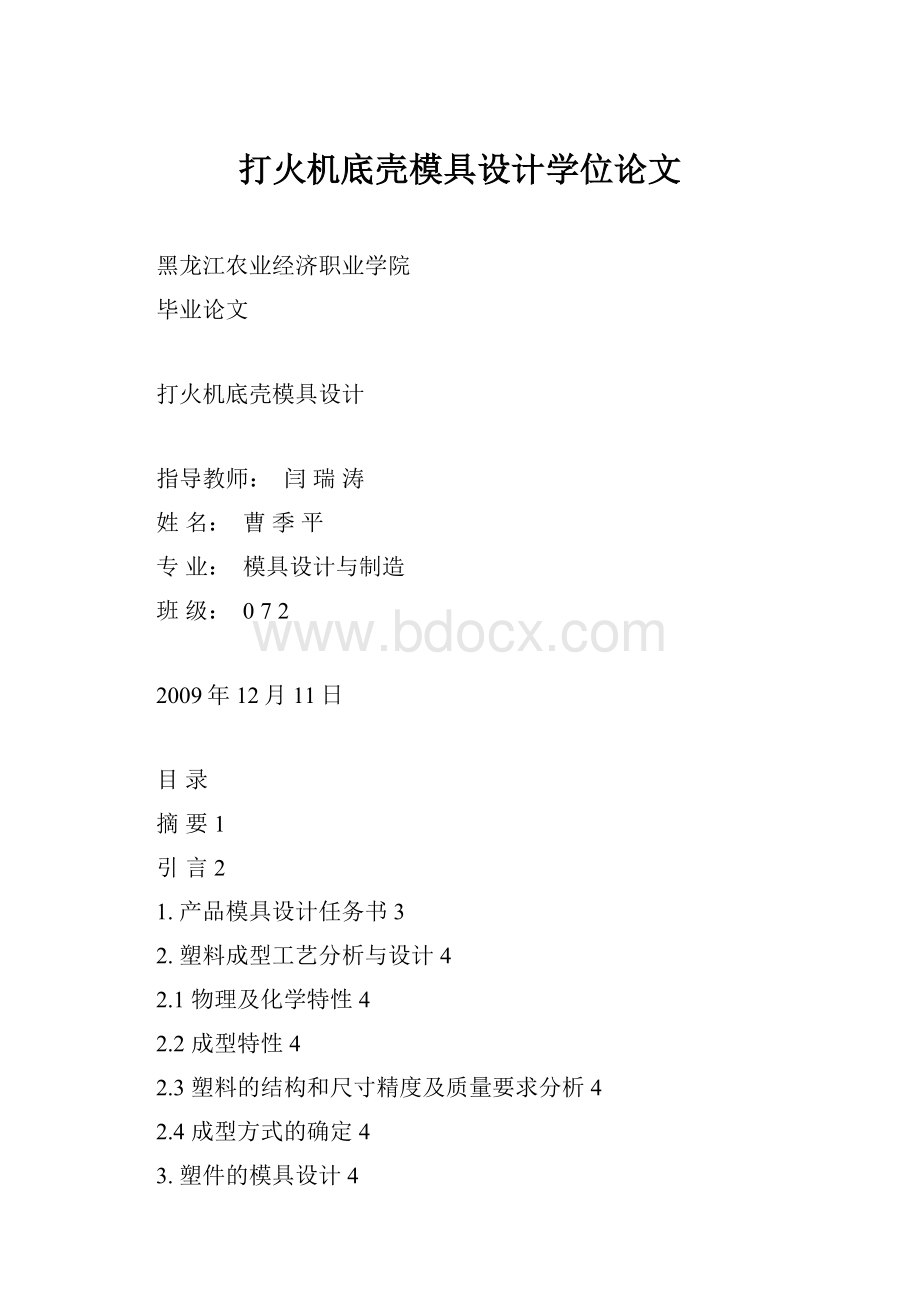
打火机底壳模具设计学位论文
黑龙江农业经济职业学院
毕业论文
打火机底壳模具设计
指导教师:
闫瑞涛
姓名:
曹季平
专业:
模具设计与制造
班级:
072
2009年12月11日
目录
摘要1
引言2
1.产品模具设计任务书3
2.塑料成型工艺分析与设计4
2.1物理及化学特性4
2.2成型特性4
2.3塑料的结构和尺寸精度及质量要求分析4
2.4成型方式的确定4
3.塑件的模具设计4
3.1型腔的数量和布置4
3.2选择注塑机型号和参数4
3.3分型面和排气方式的选择6
3.4浇注系统选择和设计6
3.5推出机构的设计7
3.6冷却系统的设计7
3.7模架尺寸的确定7
3.8校核模具设计的主要参数9
3.9模具设计总装简图8
4.塑件成型工卡11
结论12
参考文献13
谢辞14
打火机底壳模具设计
摘要:
本套塑料模具采用传统且具有代表性的的设计思路,综合模具行业的发展方向充分考虑到其经济价值和使用性能,是简单结构塑料制品的模具的典范设计。
关键词:
成型特性;公称注射量;锁模力;分型面。
引言
模具是现代工业生产的重要工艺设备,随着工业技术的迅速发展,模具技术在国民经济中的地位和作用日趋重要。
世界上一些工业发达国家其模具工业总产值已超过了机床工业,其发展速度也超过了机床、汽车、电子等工业。
美国工业界称“模具工业是美国工业的基石”,日本模具协会称“模具是促进社会富裕的动力”。
模具的价值不仅是其本身的价值,还在于它的应用为社会创造了巨大的经济效益和社会效益。
模具技术特别是制造精密、复杂长寿
命模具技术,已成为衡量一个国家机械制造水平的重要标志之一。
在我国随着生产和科学技术的发展特别是20世纪80年代以来,由于产品品种增多,更新加快,市场竞争激烈,因此对模具的要求是交货期短、精度高及成本低,塑料成型模具正朝着高效率、高精度及高寿命方向发展。
因为塑料具有质量轻、强度高、耐腐蚀、绝缘性好、易着色、制件可加工成任意形状,而且具有生产率高、价格低廉等特点,所以应用日趋广泛,年增长居四大工业材料之首,已经深入到国民经济的各个部门,且在促进现代科技发展、加速国防现代化建设、推进农业现代化、改善和提高人们生活方面,发挥着越来越重要的作用。
由此可见,塑料模具设计,对于产品质量与产量的重要性是不言而喻的。
目前世界模具市场供不应求,模具的主要出口国是美国、日本、法国、瑞士等国家。
中国模具出口数量极少,但中国模具钳工技术水平高,劳动成本低,只要配备一些先进的数控制模设备,提高模具加工质量,缩短生产周期,沟通外贸渠道,模具出口将会有很大发展。
研究和发展模具技术,提高模具技术水平,对于促进国民经济的发展有着特别重要的意义。
1.产品的模具设计任务书
根据厂家给定的产品三维组装图及所需设计的零件三维图绘制二维工程图。
表1
塑件名称
打火机底壳
材料
ABS
厚度
1
工件精度
7
(图1装配后分解图)
(图1零件3D图)
设计内容:
1.编制模塑成型工艺规卡
2.绘制产品零件图,塑件注射模总装图(A3图纸各1张)
3.编写完善模具设计说明书(按A4打印纸装订)
2.塑料成型工艺分析与设计
2.1物理及化学特性
ABS是结晶聚合物,不透明.无色无味及微黄的热塑性树脂.可燃。
密度1.02-1.2g/cm3,具有突出的力学性能和良好的综合性能.坚固坚韧坚硬是重要的塑料。
用途广泛如电视机.录音机.冰箱.洗衣机.电话.电风扇及洗尘器等用品的壳体、内衬和部件,还可用于制作玩具、包装容器、家具、安全帽及办公设备等。
除了以上性能和用途外,由于ABS树脂原料来源广泛价格低廉,性能优异,是目前产量和应用最大最广的一种工程塑料。
2.2成型特性
(1)可用注塑、挤出、压延、吹塑、等成型方法。
(2)收缩率小,可制得精密件。
(3)吸湿性较大,流动性中等,溢边值0.04mm,熔体黏度强烈依赖于剪切速度。
模具设计常采用点浇口。
2.3塑件的结构和尺寸精度及质量要求分析
(1)结构分析:
塑件尺寸较小,为壳体,壁厚较均匀。
(2)尺寸精度分析:
塑件精度要求不高,按7级精度加工。
(3)质量要求分析:
该塑件要求表面无缺陷,无毛刺,设计时最好自然成型倒角。
2.4成型方式的确定
通过结构和用途分析决定采用直浇浇注方式。
其结构简单,加工方便并且能够满足成型产品的使用要求。
3.塑件的模具设计
3.1型腔的数量和布局
成型塑料件的尺寸较小,结构简单,精度不高而且产量要求大,因此采用一模八腔的侧浇口浇注。
为保证零件成型后装配的统一和一致性,布局采用平衡式。
尺寸如:
图表(1-5)
3.2选择注塑机的型号和参数
(1)计算注射量:
通过PRO/E软件对单个塑料件进行分析测得体积为566.5mm
,密度按1.1g/cm3,算得重量为0.623g,浇注凝料和飞边体积未知可按塑件体积一倍计算。
所以V=NV
+V
+V
=8
0.5565+8
0.5565
=8.904
公式中
V——表示塑件的总体积(包括浇注系统凝料及飞边在内)
N——型腔数目;
V
——为一个塑件的体积(cm3);
V
——为浇注系统的体积(cm3);
V
——为飞边的体积(cm3);
因塑料的溶积与其压缩率有关,故所需塑料的体积V
为:
V
=K
V
=2
8.904
=17.808
公式中
K
——塑料的压缩率(查的ABS压缩率为1.8-2.0取值2.0);
V——塑件的体积(包括浇注系统凝料及飞边在内);
注射机的最大注射容积V
应等于或小于成型塑件所需塑料的容积V
即:
K
V
V
公式中
V
——注射机最大注射量(公称容积,cm³);
V
——塑件所需塑料的体积(包括浇注系统凝料及飞边在内);
K
——注射机最大注射量利用系数,一般取K
=0.8。
计算得所需注射机最大注射
量V
最小为22.26cm³;
(2)计算锁模力:
F
P
A
公式中
F——注塑机的公称锁模力;
A——塑件及浇注系统在分型面上的投影面积之和(m³);
P
——型腔内熔体压力(MPa),ABS取P
=35MPa;
通过计算单个塑件在分型面上投影面积为0.208cm²,浇注系统凝料及飞边的投影面积按塑件的一倍计算,得出锁模力F不应小于72.8KN。
根据计算最大注射量和锁模力所得出的结论,采用U102T型号注塑机完全可以满足设及生产要求,XS-ZY-250型注塑机参数如下表:
(表2注塑机参数)
公称注射量/cm³
125
模板的最大厚度/mm
300
螺杆直径/mm
42
模板的最小厚度/mm
200
合模力/KN
900
模板空间
428×450
注射压力/MPa
119
拉杆空间/mm
260×290
注射行程/mm
115
合模方式
液压-机械
模板最大行程/mm
300
液压顶出行程/mm
80
喷嘴球半径/mm
SR12
喷嘴孔直径/mm
4.0
注射方式
螺杆式
最大成型面积/
320
(3)校核注塑机有关参数
注射量的校核:
计算得所需注射机最大注射量V
最小为22.26cm³,其值小于注塑机公称注塑量220cm³的80%,大于其20%,满足要求。
锁模力的校核:
计算得出锁模力F不应小于72.8KN,其值小于注塑机额定锁模力1200KM,满足要求。
3.3分型面和排气方式的选择
在塑件最大截面处分型,可利用分型面及推杆和小型芯镶块的间隙进行排气。
3.4浇注系统的选择和设计
主浇道的设计:
主浇道的小端口直径d=喷嘴口直径4.0mm–0.5mm=3.5mm;
主浇道球径D=12.0mm+1.0mm=13.0mm;
主浇道锥角
=4
主浇口衬套具体尺寸如(图3):
(图3浇口衬套)
分浇道及浇口的设计:
由于采用平衡式布局,为使加工方便,且易脱模达到理想的塑料填充件,浇注系统分浇道及浇口形状尺寸如(图4);ABS流动性一般,分浇道表面粗糙度按1.6加工,定模侧定位环外径
100mm,为注塑机配合为H7/m6。
(图4浇注系统)
3.5推出机构的设计
零件为壳体,有圆锥型结构,采用结构简单的推杆式,一模八腔共16个推杆,其具体位置尺寸如图5所示,并设计
8mm推料杆一根,推板导柱两根。
(图5推出机构)
3.6冷却系统的设计
ABS塑料注塑时需设计冷却系统,采用水冷却动模板和定模板上分别开设冷却水空,孔直径为12mm,水流速不低于1.2m/s,具体尺寸和布局参看(工程图)。
3.7模架尺寸的确定
根据前面的设计采用futaba-fg系列200
200标准模架,尺寸如(图6):
.
(图6模架结构)
3.8校核模具设计的主要参数
(1)模具外形尺寸的校核:
模具外形尺寸为200
200mm,满足注塑机428
450的尺寸要求;
(2)喷嘴球径的校核:
模具浇口衬套球径为13mm大于注塑机喷嘴球径SR=12mm,满足要求;
(3)浇口衬套小端口径的校核:
模具浇口衬套小端口径为
3.5mm小于注塑机喷嘴口径4.0mm,满足要求;
(4)模具闭合高度的校核:
模具闭合后高度245mm,注塑机最大模板厚度为300mm,满足要求;
(5)推出距离的校核:
设计推出距离为30mm,满足塑件推出要求,所选模具最大推出距为33mm,满足要求。
3.9模具设计总装简图
(图7主剖面)
(图8侧剖面)
(图9俯视面)
1.定位环2.浇口衬套3.定模座板4.型腔镶块5.型腔板6.塑件7.推杆8.复位杆9.推板导柱套10.推料杆11.推杆固定板12.推板13.动模座板14.推板导柱15.定位环紧固螺钉16.导柱17.导套18.水道嘴19.螺栓20.垃圾钉
4.塑件成型工艺卡
表3
塑件名称
打火机底壳
根据3D图形所绘成的二维图纸
材料牌号
ABS
单件重量
0.623g
成型设备型号
XS-ZY-250
每模件数
8
成型工艺参数
材料干燥
干燥设备名称
烘箱
温度/℃
70~80
时间/h
1~2
成型过程
料筒温度
后段/℃
200~210
中段/℃
210~230
前段/℃
180~200
喷嘴/℃
180~190
模具温度/℃
50~70
时间
注射/s
3~5
保压/s
50~70
冷却/s
15~30
压力
注射/MPa
70~90
保压/MPa
50~70
后处理
温度/℃
_____
时间/min
_____
编制
日期
审核
日期
曹季平
2009.11.11
闫瑞涛
2009.12.11
结论
本设计首先说明了塑料工业的重要地位和当今注塑模具的现状,随着经济的发展,塑料工业将继续呈现蓬勃发展之势。
其次介绍了注塑件的一般设计原则,对塑件的特征如倒圆角、加强筋等做了说明。
从实际来看,几乎所有的注塑件都遵循这些原则。
在做好注塑成型的准备工作之后,接着介绍了模具设计的内容,冷流道注塑模具无外乎包括四大系统:
浇注系统、温度调节系统、顶出系统和机构系统(其实也可以归为顶出系统,该系统如斜导柱、滑块和开闭器等)。
在浇注系统的设计中根据经验公式取流道横截面形状,确定浇口尺寸,对流道剪切速率进行校核;温度调节系统说明了设计的一般步骤,确定冷却时间,计算体积流量等;顶出系统着重说明了推杆,推管的安装要求,并进行强度校核;该模具属于简单脱模机构,无滑块抽芯机构,也无开模先后顺序的要求,做完这些工作之后,该模具的设计到此结束。
在设计的过程中发现经验公式有不一致的地方,不同公式的计算结果有的相差很大,特别是在温度调节与脱模力的计算这两块。
在完成图纸之后发现塑件的设计有的地方是不合理的,比如说壁厚,虽然有经验可循,但从实际中看显然本设计的塑件壁厚过大;还有就是推管处的设计不合理,按该塑件加工,则标准推管需要再加工;从这里可以知道,注塑件的设计与模具设计关系密切,好的塑件结构可以简化模具结构,降低生产成本。
参考文献
[1]谭雪松林晓新温丽编.新编塑料模具设计手册[M].北京:
人民邮电出版社,2009.
[2]曾正明主编.塑料制品速查手册[M].北京:
机械工业出版社,2009.6.
谢辞
在本次毕业设计过程中,闫瑞涛教授对该论文从选题、构思、资料收集到最后定稿的各个环节给予了细心地指引与教导,使我对模具设计有了深刻的认识和理解,使我得以最终完成毕业设计,在此表示衷心感谢。
同时我还要感谢机电系所有的老师,正是由于他们的传道、授业、解惑,让我学到了专业知识,并从他们身上学到了如何求知治学、如何为人处事。
我也要感谢我的大学,是她提供了良好的学习环境和生活环境,让我的大学生活丰富多姿,为我的人生留下精彩的一笔。
另外,感谢我所有的老师对我的教育和勉励。
师生之情和同窗之情,我将终生难忘!
路漫漫其修远兮,吾将上下而求索。
我愿在未来的学习和研究过程中,以更加丰厚的成果来答谢曾经关心、帮助和支持过我的所有老师、同学和朋友。