塑艺成型.docx
《塑艺成型.docx》由会员分享,可在线阅读,更多相关《塑艺成型.docx(27页珍藏版)》请在冰豆网上搜索。
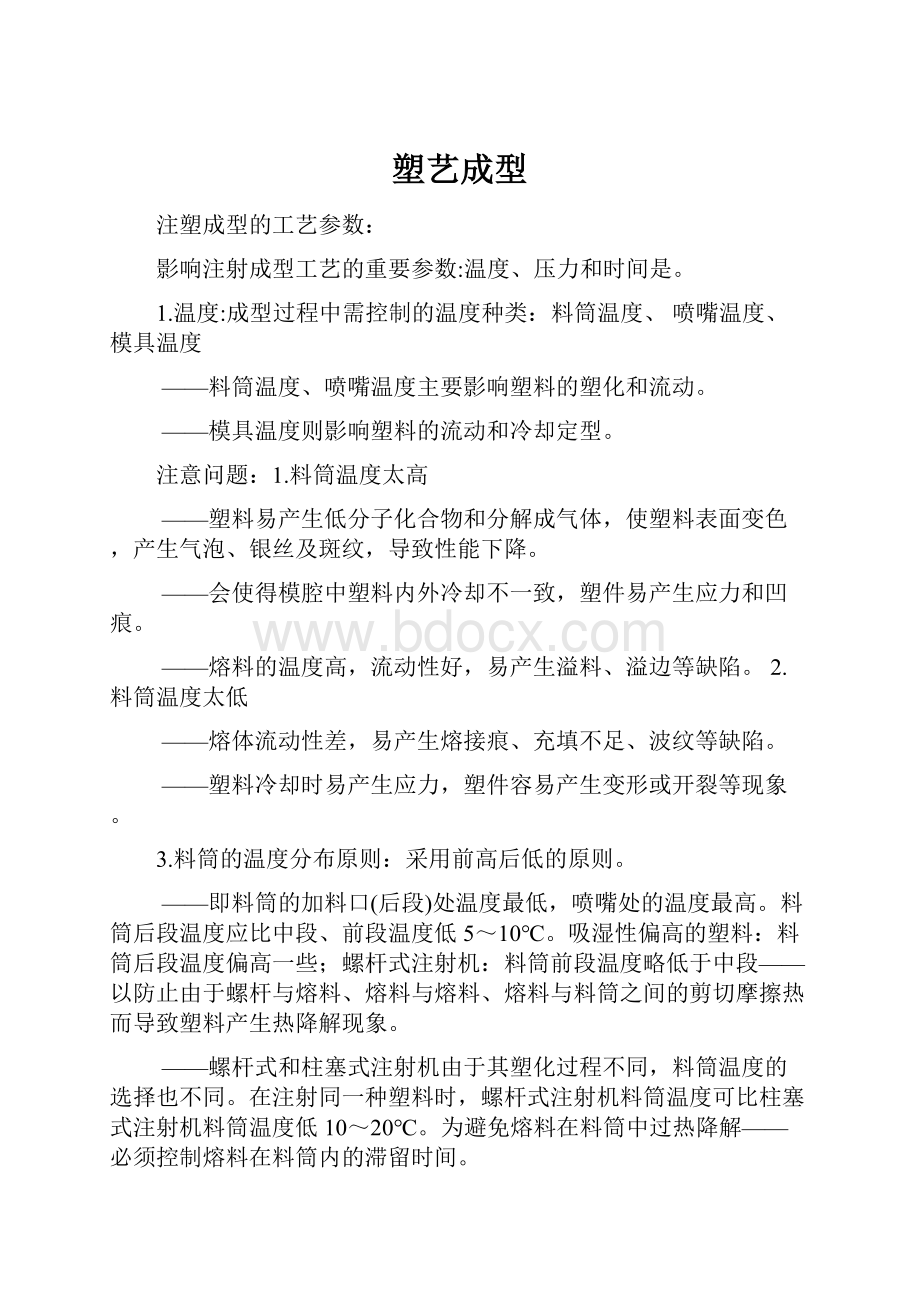
塑艺成型
注塑成型的工艺参数:
影响注射成型工艺的重要参数:
温度、压力和时间是。
1.温度:
成型过程中需控制的温度种类:
料筒温度、喷嘴温度、模具温度
——料筒温度、喷嘴温度主要影响塑料的塑化和流动。
——模具温度则影响塑料的流动和冷却定型。
注意问题:
1.料筒温度太高
——塑料易产生低分子化合物和分解成气体,使塑料表面变色,产生气泡、银丝及斑纹,导致性能下降。
——会使得模腔中塑料内外冷却不一致,塑件易产生应力和凹痕。
——熔料的温度高,流动性好,易产生溢料、溢边等缺陷。
2.料筒温度太低
——熔体流动性差,易产生熔接痕、充填不足、波纹等缺陷。
——塑料冷却时易产生应力,塑件容易产生变形或开裂等现象。
3.料筒的温度分布原则:
采用前高后低的原则。
——即料筒的加料口(后段)处温度最低,喷嘴处的温度最高。
料筒后段温度应比中段、前段温度低5~10℃。
吸湿性偏高的塑料:
料筒后段温度偏高一些;螺杆式注射机:
料筒前段温度略低于中段——以防止由于螺杆与熔料、熔料与熔料、熔料与料筒之间的剪切摩擦热而导致塑料产生热降解现象。
——螺杆式和柱塞式注射机由于其塑化过程不同,料筒温度的选择也不同。
在注射同一种塑料时,螺杆式注射机料筒温度可比柱塞式注射机料筒温度低10~20℃。
为避免熔料在料筒中过热降解——必须控制熔料在料筒内的滞留时间。
(2)喷嘴温度:
喷嘴温度一般略低于料筒的最高温度。
喷嘴温度太高:
熔料在喷嘴处产生流涎现象,塑料易产生热分解现象。
喷嘴温度太低:
易产生冷块或僵块,使熔体产生早凝,其结果是凝料堵塞喷嘴,或是将冷料注入模具型腔,导致成品缺陷。
(3)模具温度模具温度的影响:
对熔体的充模流动能力塑件的冷却速度成型后的塑件性能
模具温度选择原则:
根据塑料的分子结构特点、塑件的结构及性能要求和其他成型工艺条件(熔体温度、注射速度、注射压力和模塑周期等)。
提高模具温度的优点:
改善熔体在模具型腔内的流动性增加塑件的密度和结晶度减小充模压力和塑件中的应力提高模具温度的缺点:
冷却时间会延长,冷却速度慢,产生粘模现象收缩率大和脱模后塑件的翘曲变形会增加降低生产率降低模具温度的优点:
能缩短冷却时间,提高生产率。
降低模具温度的缺点:
过低时,熔体在模具型腔内的流动性能会变差,使塑件产生较大的应力和明显的熔接痕等缺陷。
模具温度较低:
对降低塑件的表面粗糙度值、提高塑件的表面质量有利。
降低模具温度的措施:
采用定温的冷却介质或制冷装置来控制;提高模具温度的措施:
用加热装置对模具加热来保持模具的温度。
——对塑料熔体,注射过程都是冷却过程。
为了使塑料成型和顺利脱模,模具的温度应低于塑料的玻璃化温度θg或工业上常用的热变形温度。
——高粘度塑料:
流动性差和充模能力弱,为了获得致密的组
织结构,必须采用较高的模具温度;
——对于粘度较小、流动性好的塑料:
可采用较低的模具温度,这样可缩短冷却时
间,提高生产效率。
——对于壁厚大的制件:
充模和冷却时间较长,温度过低,易使塑件内部产生真空泡和较大的应力,不宜采用较低的模具温度。
在生产过程中,模具温度的确定原则:
需要根据塑料品种和塑件的复杂程度确定。
满足注射过程要求的温度下,采用尽可能低的模具温度,以加快冷却速度,缩短冷却时间;模具温度保持在比热变形温度稍低的状态下,使塑件在比较高的温度下脱模,然后自然冷却,可以缩短塑件在模内的冷却时间。
ABS塑料成型中小型塑件的温度参数选择:
预热干燥温度:
80~85℃;料筒温度:
后段150~170℃;中段165~180℃;前段180~200℃;喷嘴温度:
170~180℃;模具温度:
50~80℃;
后处理温度:
70℃。
2.压力注射成型过程中压力的种类:
塑化压力;注射压力;保压压力
——它们直接影响塑料的塑化和塑件质量。
(1)塑化压力塑化压力(螺杆背压):
它是指采用螺杆式注射机注射时,螺杆头部熔料在螺杆转动时所受到的压力。
——压力大小可通过液压系统中的溢流阀调整注射中,影响塑化压力大小的因素:
螺杆的设计塑件质量的要求塑料的种类增加塑化压力的优点:
——三个因素和螺杆的转速都不变。
增加塑化压力会提高熔体的温度,并使熔体的温度均匀、色料混合均匀并排除熔体中的气体。
增加塑化压力的缺点:
降低塑化速率,延长成型周期,甚至可能导致塑料的降解。
生产中塑化压力的选择原则:
保证塑件质量的前提下,塑化压力应越低越好,其具体数值随所用塑料的品种而定。
一般为6~20MPa。
1)注射聚甲醛:
较高的塑化压力会使塑件的表面质量提高;但可能使塑料变色、塑化速率降低和流动性下降。
2)注射聚酰胺:
塑化压力必须降低,否则塑化速率将很快降低。
——因为螺杆中逆流和漏流增加的缘故。
——如需增加料温,则应采用提高料筒温度的方法。
3)聚乙烯:
热稳定性较高,提高塑化压力不会有降解的危险,这有利于混料和混色,不过塑化速率会随之降低。
2)注射压力
注射压力:
是指柱塞或螺杆轴向移动时其头部对塑料熔体所施加的压力。
——注射机压力表指示出注射压力的大小,一般在40~130MPa之间,压力的大小可通过注射机的控制系统来调整。
注射压力的作用:
是克服塑料熔体从料筒流向型腔的流动阻力,
给予熔体一定的充型速率以便充满模具型腔。
影响注射压力的大小的因素:
注射机的类型、塑料的品种、模具浇注系统的结构、尺寸与表面粗糙度、模具温度、塑件的壁厚、流程的大小
——目前难以作出具有定量关系的结论。
——在相同条件下,柱塞式注射机的注射压力应比螺杆式注射机的注射压力大。
影响塑料流动阻力的因素:
1.注射压力的大小。
2.塑料与模具浇注系统及型腔之间的摩擦系数和塑料自身的熔融粘度。
——摩擦系数和熔融粘度越大,注射压力应越高。
——同一种塑料流动时其与模具的摩擦系数和熔融粘度是随料筒温度和模具温度而变动的。
3.是否加有润滑剂有关。
注射压力太高:
塑料的流动性提高,易产生溢料、溢边,塑料
在高压下强迫冷凝,易产生应力,塑件易粘模,脱模困难,塑件容易变形,但不易产生气泡。
注射压力太低:
塑料的流动性下降,成型不足,产生熔接痕迹,不利于气体从熔料中溢出,易产生气泡,冷却中补缩差,会产生凹痕和波纹等缺陷。
(3)保压压力:
型腔充满后,继续对模内熔料施加的压力。
保压压力的作用:
是使熔料在压力下固化,并在收缩时进行补缩,从而获得健全的塑件。
保压压力等于或小于注射时注射压力的原因:
1)注射和压实时的压力相等,则往往可以使塑件的收缩率减小,并且它们的尺寸稳定性较好。
缺点是会造成脱模时的残余压力过大和成型周期过长。
但对结晶性塑料来说,使用这种方法成型周期不一定增长,因为压实压力大时可以提高塑料的
熔点。
——如聚甲醛,如果压力加大到50MPa,则其熔点可提高90℃,脱模可以提前。
2)保压大小也会对成型过程产生影响,保压压力太高,易产生溢料、溢边,增加塑件的应力;保压压力太低,会造成成型不足。
3.时间(成型周期)成型周期:
完成一次注射成型过程所需的时间。
成型周期的组成:
合模时间、注射时间、保压时间、模内冷却时间、其他时间
(1)合模时间:
是指注射之前模具闭合的时间。
——合模时间太长,则模具温度过低,熔料在料筒中停留时间过长;
——合模时间太短,模具温度相对较高。
(2)注射时间是指注射开始到充满模具型腔的时间(柱塞或
螺杆前进时间)。
——小型塑件注射时间一般为3~5s;
——大型塑件注射时间可达几十秒;
——注射时间中的充模时间与充模速度成反比;注射时间缩短、充模速度提高,取向下降、剪切速率增加,绝大多数塑料的表观粘度均下降。
——对剪切速率敏感的塑料尤其这样。
(3)保压时间:
是指型腔充满后继续施加压力的时间(柱塞或螺杆停留在前进位置的时间),一般为20—25s,特厚塑件可高达5~10min。
保压时间过短:
塑件不紧密,易产生凹痕,塑件尺寸不稳定;保压时间过长:
加大塑件的应力,产生变形、开裂,脱模困难。
保压时间的长短不仅与塑件的结构尺寸有关,而且与料温、模温以及主流道和浇口的大小有关。
(4)模内冷却时间模内冷却时间是指塑件保压结束至开模以前所需的时间(柱塞后撤或螺杆转动后退的时间均在其中)。
冷却时间主要决定于塑件的厚度、塑料的热性能、结晶性能以及模具温度等。
冷却时间的长短应以脱模时塑件不引起变形为原则,冷却时间一般在30~120s之间。
冷却时间过长,不仅延长生产周期,降低生产效率,对复杂塑件还将造成脱模困难、易变形、结晶度高等;冷却时间过短,塑件易产生变形等缺陷。
(5)其他时间其他时间是指开模、脱模、喷涂脱模剂、安放嵌件等时间。
此外还有塑化时间,它是指螺杆开始转动至预塑结束所需的时间。
不过,塑化是在保压结束后就开始的,已经包含在模内冷却时间内,因此不能重复计算在成型周期内。
(4)模内冷却时间:
是指塑件保压结束至开模以前所需的时间(柱塞后撤或螺杆转动后退的时间均在其中)。
影响冷却时间的因素:
塑件的厚度、塑料的热性能、结晶性能、模具温度。
冷却时间的长短:
应以脱模时塑件不引起变形为原则,冷却时间一般在30~120s之间。
冷却时间过长:
不仅延长生产周期,降低生产效率,对复杂塑件还将造成脱模困难、易变形、结晶度高等;冷却时间过短:
塑件易产生变形等缺陷。
(5)其他时间:
是指开模、脱模、喷涂脱模剂、安放嵌件等时
间。
塑化时间:
是指螺杆开始转动至预塑结束所需的时间。
——塑化是在保压结束后就开始的,已经包含在模内冷却时间内,因此不能重复计算在成型周期内。
——螺杆转速快,剪切热加大,塑化时间缩短;
——螺杆转速慢,剪切热减少,塑化时间增长。
模具的成型周期的影响:
直接影响到生产率和注射机使用率,因此,生产中在保证质量的前提下应尽量缩短成型周期中各个阶段的有关时间。
整个成型周期中,以注射时间和冷却时间最重要,他们对塑件的质量均有决定性影响。
注塑工艺要考虑的7个因素:
一、收缩率
热塑性塑料成型收缩的形式及计算如前所述,影响热塑性塑料成型收缩的因素如下:
1.1塑料品种热塑性塑料成型过程中由于还存在结晶化形起的体积变化,内应力强,冻结在塑件内的残余应力大,分子取向性强等因素,因此与热固性塑料相比则收缩率较大,收缩率范围宽、方向性明显,另外成型后的收缩、退火或调湿处理后的收缩率一般也都比热固性塑料大。
1.2塑件特性成型时熔融料与型腔表面接触外层立即冷却形成低密度的固态外壳。
由于塑料的导热性差,使塑件内层缓慢冷却而形成收缩大的高密度固态层。
所以壁厚、冷却慢、高密度层厚的则收缩大。
另外,有无嵌件及嵌件布局形成收缩大的高密度固态层。
所以壁厚、冷却慢、高密度层厚的则收缩大。
另外,有无嵌件及嵌件布局、数量都直接影响料流方向,密度分布及收缩阻力大小等,所以塑件的特性对收缩大小、方向性影响较大。
1.3进料口形式、尺寸、分布这些因素直接影响料流方向、密度分布、保压补缩作用及成型时间。
直接进料口、进料口截面大(尤其截面较厚的)则收缩小但方向性大,进料口宽及长度短的则方向性小。
距进料口近的或与料流方向平行的则收缩大。
1.4成型条件模具温度高,熔融料冷却慢、密度高、收缩大,尤其对结晶料则因结晶度高,体积变化大,故收缩更大。
模温分布与塑件内外冷却及密度均匀性也有关,直接影 响到各部分收缩量大小及方向性。
另外,保持压力及时间对收缩也影响较大,压力大、时间长的则收缩小但方向性大。
注塑压力高,熔融料粘度差小,层间剪切应力小,脱模后弹性 回跳大,故收缩也可适量的减小,料温高、收缩大,但方向性小。
因此在成型时调整模温、压力、注塑速度及冷却时间等诸因素也可适当改变塑件收缩情况。
模具设计时根据各种塑料的收缩范围,塑件壁厚、形状,进料口形式尺寸及分布情况,按经验确定塑件各部位的收缩率,再来计算型腔尺寸。
对高精度塑件及难以掌握收缩率时,一般宜用如下方法设计模具:
①对塑件外径取较小收缩率,内径取较大收缩率,以留有试模后修正的余地。
②试模确定浇注系统形式、尺寸及成型条件。
③按实际收缩情况修正模具。
④要后处理的塑件经后处理确定尺寸变化情况(测量时必须在脱模后24小时以后)。
⑤再试模并可适当地改变工艺条件略微修正收缩值以满足塑件要求。
二、流动性
2.1热塑性塑料流动性大小,一般可从分子量大小、熔融指数、阿基米德螺旋线流动长度、表现粘度及流动比(流程长度/塑件壁厚)等一系列指数进行分析。
分子量小,分子量分布宽,分子结构规整性差,熔融指数高、螺流动长度长、表现粘度小,流动比大的则流动性就好,对同一品名的塑料必须检查其说明书判断其流动性是否适用于注塑成型。
按模具设计要求大致可将常用塑料的流动性分为三类:
①流动性好 PA、PE、PS、PP、CA、聚(4)甲基戍烯;
②流动性中等 聚苯乙烯系列树脂(如ABS、AS)、PMMA、POM、聚苯醚;
③流动性差 PC、硬PVC、聚苯醚、聚砜、聚芳砜、氟塑料。
2.2各种塑料的流动性也因各成型因素而变,主要影响的因素有如下几点:
①温度料温高则流动性增大,但不同塑料也各有差异,PS(尤其耐冲击型及MFR值较高的)、PP、PA、PMMA、改性聚苯乙烯(如ABS、AS)、PC、CA等塑料的流动性随温度变化较大。
对PE、POM、则温度增减对其流动性影响较小。
所以前者在成型时宜调节温度来控制流动性。
②压力注塑压力增大则熔融料受剪切作用大,流动性也增大,特别是PE、POM较为敏感,所以成型时宜调节注塑压力来控制流动性。
③模具结构浇注系统的形式,尺寸,布置,冷却系统设计,熔融料流动阻力(如型面光洁度,料道截面厚度,型腔形状,排气系统)等因素都直接影响到熔融料在型腔内的实际流动性,凡促使熔融料降低温度,增加流动性阻力的则流动性就降低。
模具设计时应根据所用塑料的流动性,选用合理的结构。
成型时则也可控制料温,模温及注塑压力、注塑速度等因素来适当地调节填充情况以满足成型需要。
三、结晶性
热塑性塑料按其冷凝时无出现结晶现象可划分为结晶型塑料与非结晶型(又称无定形)塑料两大类。
所谓结晶现象即为塑料由熔融状态到冷凝时,分子由独立移动,完全处于无次序状态,变成分子停止自由运动,按略微固定的位置,并有一个使分子排列成为正规模型的倾向的一种现象。
作为判别这两类塑料的外观标准可视塑料的厚壁塑件的透明性而定,一般结晶性料为不透明或半透明(如POM等),无定形料为透明(如PMMA等)。
但也有例外情况,如聚(4)甲基戍烯为结晶型塑料却有高透明性,ABS为无定形料但却并不透明。
在模具设计及选择注塑机时应注意对结晶型塑料有下列要求及注意事项:
①料温上升到成型温度所需的热量多,要用塑化能力大的设备。
②冷却回化时放出热量大,要充分冷却。
③熔融态与固态的比重差大,成型收缩大,易发生缩孔、气孔。
④冷却快,结晶度低,收缩小,透明度高。
结晶度与塑件壁厚有关,壁厚则冷却慢,结晶度高,收缩大,物性好。
所以结晶性料应按要求必须控制模温。
⑤各向异性显著,内应力大。
脱模后未结晶化的分子有继续结晶化倾向,处于能量不平衡状态,易发生变形、翘曲。
⑥结晶化温度范围窄,易发生未熔料末注入模具或堵塞进料口。
四、热敏性塑料及易水解塑料
4.1热敏性系指某些塑料对热较为敏感,在高温下受热时间较长或进料口截面过小,剪切作用大时,料温增高易发生变色、降解,分解的倾向,具有这种特性的塑料称为热敏性塑料。
如硬PVC、聚偏氯乙烯、醋酸乙烯共聚物,POM,聚三氟氯乙烯等。
热敏性塑料在分解时产生单体、气体、固体等副产物,特别是有的分解气体对人体、设备、模具都有刺激、腐蚀作用或毒性。
因此,模具设计、选择注塑机及成型时都应注意,应选用螺杆式注塑机,浇注系统截面宜大,模具和料筒应镀铬,不得有*角滞料,必须严格控制成型温度、塑料中加入稳定剂,减弱其热敏性能。
4.2有的塑料(如PC)即使含有少量水分,但在高温、高压下也会发生分解,这种性能称为易水解性,对此必须预先加热干燥。
五、应力开裂及熔体破裂
5.1有的塑料对应力敏感,成型时易产生内应力并质脆易裂,塑件在外力作用下或在溶剂作用下即发生开裂现象。
为此,除了在原料内加入添加剂提高开抗裂性外,对原料应注意干燥,合理的选择成型条件,以减少内应力和增加抗裂性。
并应选择合理的塑件形状,不宜设置嵌件等措施来尽量减少应力集中。
模具设计时应增大脱模斜度,选用合理的进料口及顶出机构,成型时应适当的调节料温、模温、注塑压力及冷却时间,尽量避免塑件过于冷脆时脱模,成型后塑件还宜进行后处理提高抗开裂性,消除内应力并禁止与溶剂接触。
5.2当一定融熔体流动速率的聚合物熔体,在恒温下通过喷嘴孔时其流速超过某值后,熔体表面发生明显横向裂纹称为熔体破裂,有损塑件外观及物性。
故在选用熔体流动速率高的聚合物等,应增大喷嘴、浇道、进料口截面,减少注塑速度,提高料温。
六、热性能及冷却速度
6.1各种塑料有不同比热、热传导率、热变形温度等热性能。
比热高的塑化时需要热量大,应选用塑化能力大的注塑机。
热变形温度高塑料的冷却时间可短,脱模早,但脱模后要防止冷却变形。
热传导率低的塑料冷却速度慢(如离子聚合物等冷却速度极慢),故必须充分冷却,要加强模具冷却效果。
热浇道模具适用于比热低,热传导率高的塑料。
比热大、热传 导率低,热变形温度低、冷却速度慢的塑料则不利于高速成型,必须选用适当的注塑机及加强模具冷却。
6.2各种塑料按其种类特性及塑件形状,要求必须保持适当的冷却速度。
所以模具必须按成型要求设置加热和冷却系统,以保持一定模温。
当料温使模温升高时应予冷却,以防止塑件脱模后变形,缩短成型周期,降低结晶度。
当塑料余热不足以使模具保持一定温度时,则模具应设有加热系统,使模具保持在一定温度,以控制冷却速度,保证流动性,改善填充条件或用以控制塑件使其缓慢冷却,防止厚壁塑件内外冷却不匀及提高结晶度等。
对流动性好,成型面积大、料温不匀的则按塑件成型情况有时需加热或冷却交替使用或局 部加热与冷却并用。
为此模具应设有相应的冷却或加热系统。
七、吸湿性
塑料中因有各种添加剂,使其对水分有不同的亲疏程度,所以塑料大致可分为吸湿、粘附水分及不吸水也不易粘附水分的两种,料中含水量必须控制在允许范围内,不然在高温、高压下水分变成气体或发生水解作用,使树脂起泡、流动性下降、外观及力学性能不良。
所以吸湿性塑料必须按要求采用适当的加热方法及规范进行预热,在使用时防止再吸湿。
塑料:
1.塑料的特性:
塑料具有特殊的物理力学性能和化学稳定性能,以及优良的成型加工性能,在加热和压力下,利用不同的成型方法几乎可将塑料制成任何形状的制品。
分类:
热塑性塑料、热固性塑料两类。
热塑性塑料的特点:
受热后软化或熔融,此时可成型加工,冷却后固化,再加热仍可软化。
热固性塑料的特点:
开始受热时也可以软化或熔融,但一旦固化成型就不再软化。
此时,即使加热到接近分解的温度也无法软化,且也不会溶解在溶剂中。
常用成型方法:
a.热塑性塑料,注射、挤出或吹塑等;b.热固性塑料,压缩或压注,有的也可以采用注射成型。
塑料的性能:
优点a.质量轻b.比强度高c.耐化学腐蚀能力强d.绝缘性能好e.光学性能好f.加工性能好、经济效益显著
缺点:
a.一般塑料的刚性差b.塑料的耐热性差c.散热性差d.若长期受载荷作用,产生“蠕变”现象。
e.易燃烧.f.光和热作用下性能容易变坏,发生老化现象。
2.聚合物熔体在成型过程中的流动状态
Ⅰ塑料聚合物熔体在注射机内的旋转螺杆与料筒之间进行输送、压缩、熔融塑化,并将塑化好的熔体储存在料筒的端部。
Ⅱ储存在料筒端部的熔体受螺杆的向前推压力并通过喷嘴、模具的主流道、分流道和浇口,开始射入模腔内。
Ⅲ塑料熔体经浇口射入模具型腔过程中的流动、相变与固化。
影响聚合物熔体充模流动的因素:
注射工艺参数和模具结构(浇口截面尺寸型腔形状等)
1)浇口和模腔对熔体充模流动的影响:
a.浇口截面高度与模腔深度相差很大,易出现射流,熔体不稳定,表面粗糙,且易破裂,先喷出的熔体降速阻碍后面的熔体流动,造成蛇形流。
b.浇口截面高度与模腔深度相差不太大,在制件厚度不大时,熔体中速进入模腔比较平稳的扩展运动。
c.浇口截面高度与模腔深度接近,在制件厚度很小时,熔体进入模腔后低速平稳的扩展充模
2)扩展流动充模的特点随料流前缘运动特点不同,分为三个阶段:
a.起始阶段,熔体流的开始部分,前锋料头呈辐射状流动;b.圆弧状的中间过度状;c.黏弹性熔膜为前锋料头的均整运动的主阶段。
3)熔体遇到阻碍物时的充模流动熔体遇到阻碍物分流,再会合,形成熔接痕,会在该处降低强度,外观变坏。
4)熔接痕(熔合缝,其强度是塑料制件的强度)
熔接痕是塑料制品中的一个区域,由彼此分离的塑料熔体相遇后熔合固化而成。
该区域力学性能比周边低,是塑件的薄弱环节。
产生原因:
a.模腔内型信或安放的嵌件;b.同一型腔多个浇口;c.塑件壁厚有变化;d.熔体喷射和蛇形流会引起波状折叠的熔合缝。
3.入口效应:
熔体在入口端出现压力降,在出口端出现膨胀的现象称为端末效应,亦分别称为入口效应。
产生入口效应的原因:
聚合物液体以收敛流动方式进入导管入口时,它必须变形以适应它在新的且有适当压缩性的流道内流动,但聚合物熔体具有弹性,也就是对变形具有抵抗力,因此,就必须消耗适当的能量,即消耗相当的压力降,来完成在这段管内的变形。
熔体各点的速度在进入导管前后是不同的,为调整速度,也要消耗一定的压力降。
入口效应和离模膨胀效应通常对塑料的成型都是不利的,特别是在注射成型、挤出成型和拉丝过程中,可能导致产品变形和扭曲,降低塑件的尺寸稳定性,并可能在塑件内产生内应力,降低塑件物理和力学性能。
增加管子或口模的平直部分长度,适当降低成型时的压力和提高成型温度,并对挤出物加以适当速度的牵引或拉伸等,均有利于减小或消除端末效应带来的不利影响。
4.影响结晶的因素:
(1)熔融温度和熔融时间:
低温快速有利结晶
冷却速度:
缓冷有利结晶,急冷结晶不均而产生内应力,中速冷却结晶组织稳定,结晶应力小。
(2)压力和切应力:
增大压力可使聚合物在高于正常情况下的熔化温度发生结晶;切应力可导致微晶生成,产生均匀的微晶结构。
(3)分子结构:
聚合物分子结构越简单、越规整,结晶越快,结晶度越高,同一种聚合物的最大结晶速率随相对分子质量的增大而减小。
(4)添加剂
5.结晶对塑件性能的影响
(1)密度:
密度随结晶度的增大而提高。
(2)力学性能:
抗拉强度随结晶度的增大而提高;冲击韧性将下降;弹性模量将减小。
(3)热性能:
结晶有助于提高聚合物的软化温度和热变形温度。
(4)翘曲:
结晶程度越高,体积收缩越大,因此结晶态塑件比非结晶态塑件更容易因收缩不均而发生翘曲。
(5)表面粗糙度和透明度:
结晶后,塑件表面粗糙度将降低,而透明度会减小或丧失。
6.成型过程中聚合物的降解
(1)概念:
由于聚合物大分子受热和应力的作用,或由于在高温下受微量水分、酸、碱等杂质及空气中氧的作用,聚合物会发生相对分子量降低或大分子结构改变等化学变化,这种现象叫降解或裂解。
(2)分类:
有热降解、氧化降解、水降解、应力降解等类型
(3)避免降解的措施:
a.严格控制原材料的技术指标和使用合格的原材料
b.使用前对聚合物进行严格的干燥c.确定合理的加工工艺、加工条件,含模具设备状态良好d.使用添加剂
7.塑件设计原则:
①在保证使用要求的前提下尽量选用价格低廉和成型性能较好的塑料。
②力求结构简单、壁厚均匀、成型方便,利于模具分型、排气、补缩和冷却。
③塑件结构应能使其模具的总体结构尽可能简化,避免模具侧抽