塑料成型工艺及模具设计.docx
《塑料成型工艺及模具设计.docx》由会员分享,可在线阅读,更多相关《塑料成型工艺及模具设计.docx(19页珍藏版)》请在冰豆网上搜索。
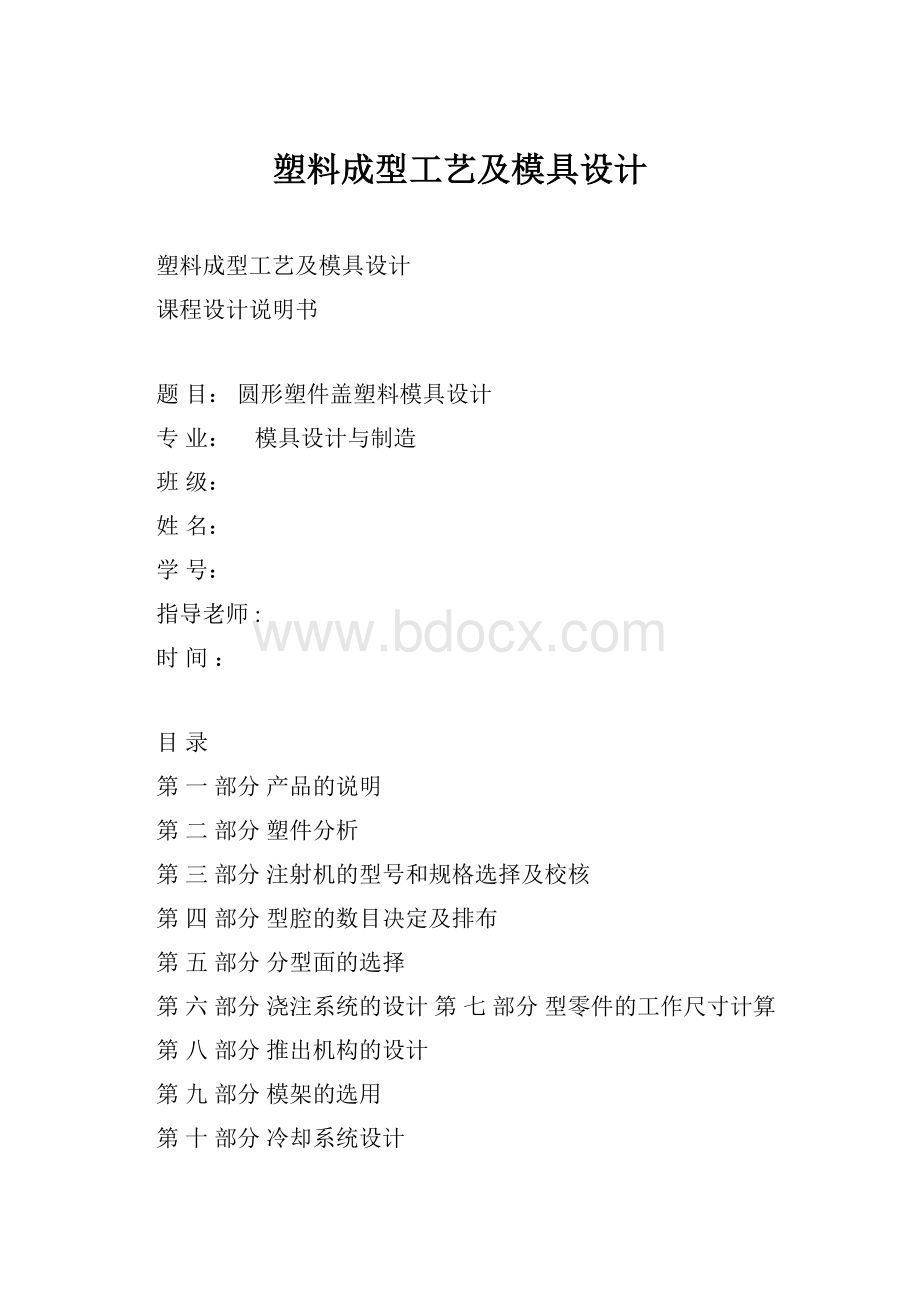
塑料成型工艺及模具设计
塑料成型工艺及模具设计
课程设计说明书
题目:
圆形塑件盖塑料模具设计
专业:
模具设计与制造
班级:
姓名:
学号:
指导老师:
时间:
目录
第一部分产品的说明
第二部分塑件分析
第三部分注射机的型号和规格选择及校核
第四部分型腔的数目决定及排布
第五部分分型面的选择
第六部分浇注系统的设计第七部分型零件的工作尺寸计算
第八部分推出机构的设计
第九部分模架的选用
第十部分冷却系统设计
第十一部分模具的动作过程
第十二部分设计小结
第十三部分参考资料
第一部分产品的说明
本塑件结构简单,壁厚均匀,模架结构较简单。
精度要求较高,为四级精度,材料为ABS成型性能一般,其他并无特殊要求。
图一:
零件实体图
图二:
塑件剖面图
第二部分塑件的分析
ABS塑料
化学名称:
丙烯-丁二烯——苯乙烯共聚物
比重:
1.02克/立方厘米成型收缩率:
0.3-0.8%查表得收缩率为:
0.3%-0.8%。
材料分析:
ABS无毒无味,呈微黄色,成型的塑件有较好的光泽,具有良好的机械强度和一定的耐磨性,耐寒性,耐油性,耐水性,化学稳定性和电器性能,密度为1.02~1.5/cm3
ABS有一定的硬度和尺寸稳定性,易于加工,经过配色可配成任何颜色。
成型特点:
ABS在升温时粘度增高,所以成型压力较高,故塑件上的脱模斜度宜稍大,ABS易吸水,成型加压前应进行干燥处理,ABS易产节痕,模具设计时应注意尽量减少浇注系统对料流的阻力,在正常的成型条件下壁厚,熔料温度对收缩率影响极小,在要求塑件精度高时,模具温度可控制在50~60°c,而
强调塑件光泽和耐热时,模具温度应控制在60~80°c。
塑件注射成型工艺参数的确定:
根据该塑件的结构特点和ABS得成型性能,查相关手册得到ABS塑件的成型工艺参数:
塑件的注射成型工艺参数
工艺参数
内容
工艺参数
内容
预热和干燥
温度80~90℃
成型时间/s
注射时间
3~5
时间2h
保压时间
15~30
料筒温度/℃
后段
180~200
冷却时间
15~30
中段
210~230
总周期
40~70
前段
170~190
螺杆转速/(r/min)
30~60
喷嘴温度/℃
180~190
后处理
方法
红外线灯烘箱
模具温度/℃
60~80
温度/℃
70
注射压力/MPa
70~90
时间/h
2~4
第三部分注射机的型号和规格选择及校核
注射模是安装在注射机上的,因此在设计注射模具时应该对注射机有关技术规范进行必要的了解,以便设计出符合要求的模具,同时选定合适的注射机型号。
从模具设计角度考虑,需要了解注射机的主要技术规范。
在设计模具时,最好查阅注射机生产厂家提供的有关“注射机使用说明书”上标明的技术规范,。
因为即使同一规格的注射机,生产厂家不同,其技术规格也略有差异。
1、注射机的选用
选用注射机时,通常是以某塑件(或模具)实际需要的注射量和注射压力初选某一公称注射量的注射机型号,然后依次对该机型的公称锁模力、模板行程以及模具安装部分的尺寸一一进行校核。
为了保证正常的注射成型,模具每次需要的实际注射量应该小于某注射机的公称注射量,即:
式子中,
—实际塑件(包括浇注系统凝料)的总体积(
)。
由proe分析/体测量,可得塑料盒的体积为50cm3,考虑到设计为2腔,加上浇注系统的冷凝料,
=1.6x2xVs=192
为了保证注射成型,注射机的注射压力要大于注射时需要的压力。
查表得ABS的注射压力为70-90Mpa取80Mpa
查阅塑料模设计手册的国产注射机技术规范及特性,可以选择SZY—300
SZY-300型注射机的主要参数如下表所示
主要技术参数项目
参数数值
主要技术参数项目
参数数值
最大注射量/cm3
320
最大模具厚度/mm
355
螺杆直径/mm
45
动、定模固定板尺寸/mm
520x620
注射压力/Mpa
125
最小模具厚度/mm
130
注射行程/mm
130
定位圈直径/mm
125
注射方式
螺杆式
最大开模行程/mm
340
锁模力/KN
1400
喷嘴孔直径/mm
4
2、锁模力的校核
锁模力是指注射机的锁模机构对模具所施加的最大夹紧力,当高压的塑料熔体充填模腔时,会沿锁模方向产生一个很大的胀型力。
为此,注射机的额定锁模力必须大于该胀型力,即:
F锁
F胀=KP
F胀=
=241.2kN
F锁=1400KN
F锁—注射机的额定锁模力(N);
P
分—模具型腔内塑料熔体平均压力(MPa);一般为注射压力的0.3~0.65倍。
我们这里选P型=40MPa。
K压力损害系数,查表取1.2
3、开模行程校核
开模行程是指从模具中取出塑料所需要的最小开合距离,用H表示,它必须小于注射机移动模板的最大行程S。
对双分型面注射模,所需开模行程为:
S机
H=H1+H2+a+(5~10)=35+50+45+10=140mm
式中,a—中间板与定模的分开距离(mm)。
S机=340mm所以符合要求
4,安装尺寸的校核
有后面计算查表选用模架为DB2335-70X35X90GB/T12555-2006系列
故模具外形尺寸为300X350<注射机安装尺寸520X620
模具闭合高度=35+80+25+35+35+90+25=325<最大模具厚度355
安装尺寸符合要求
第四部分 分型面的选择
分型面是指分开模具取出塑件和浇注系统凝料的可分离的接触表面。
一副模具根据需要可能有一个或两个以上的分型面,分型面可以是垂直于合模方向,也可以与合模方向平行或倾斜。
1、分型面的形式:
分型面的形式与塑件几何形状、脱模方法、模具类型及排气条件、浇口形式等有关,我们常见的形式有如下五种:
水平分型面、垂直分型面、斜分型面、阶梯分型面、曲线分型面。
2、分型面的选择原则:
a)、便于塑件脱模:
Ⅰ、在开模时尽量使塑件留在动模内
Ⅱ、应有利于侧面分型和抽芯
Ⅲ、应合理安排塑件在型腔中的方位;
b)、考虑和保证塑件的外观不遭损坏
c)、尽力保证塑件尺寸的精度要求(如同心度等)
d)、有利于排气
e)、尽量使模具加工方便
图二分型面(图中蓝色显示)
第五部分型腔数目的决定及排布
1、型腔数目的确定:
对于高精度制品,由于型腔模具难以使各型腔的成型条件均匀,故通常推荐型腔数目不超过4个,塑料件的精度为4级左右,以及模具制造成本、制造难度和生产效率的综合考虑,型腔数目初定为2腔,排布形式为矩形的平衡布局(详细的布局参见零件布局图)。
图三型腔布局图
第六部分浇注系统的设计
1、浇注系统的组成
图四浇注系统的组成
所谓注射模的浇注系统是指从主流道的始端到型腔之间的熔体流动通道。
其作用是使塑件熔体平稳而有序地充填到型腔中,以获得组织致密、外形轮廓清晰的塑件。
因此,浇注系统十分重要。
而浇注系统一般可分为普通浇注系统和无流道浇注系统两类。
我们在这里选用普通浇注系统,它一般是由主流道、分流道、浇口和冷料穴四部分组成,如图四所示:
2、浇注系统各部件设计
A、主流道设计:
主流道是连接注射机喷嘴与分流道的一段通道,通常和注射机喷嘴在同一轴线上,断面为圆形,带有一定的锥度,其主要设计点为:
⑴主流道圆锥角α=2o~6o,对流动性差的塑件可取3o~6o,取锥角为3o。
内壁粗糙度为Ra0.63μm。
⑵主流道大端呈圆角,半径r=1~3mm,取r=2以减小料流转向过渡时的阻力。
⑶查注塑机得喷嘴前端孔径d1=4,喷嘴前端球面半径SR1=12
SR=SR1+(1~2)d=d1=(0.5~1)
得主流道球面半径SR=13,前端孔径d=4.5,计算的大端直径D=8.4
⑷对小型模具可将主流道衬套与定位圈设计成整体式。
但在大多数情况下是将主流道衬套与定位圈设计成两个零件,然后配合固定在模板上。
主流道衬套与定模座板采用H7/m6过渡配合,与定位圈的配合采用
间隙配合。
⑸主流道衬套一般选用T8、T10制造,热处理强度为52~56HRC。
图五.主流道衬套
C、分流道的设计
分流道就是主流道与浇口之间的通道,一般开设在分型面上,起分流和转向的作用。
多型腔模具必定设计分流道,单型腔大型腔塑件在使用多个点浇口时也要设置分流道。
①分流道的截面形状:
通常分流道的断面形状有圆形、矩形、梯形、U形和六角形等。
为了减少流道内的压力损失和传热损失,提高效率,加工难度等综合考虑我们这里就选用U形分流道。
图六分流道尺寸
②分流道的尺寸:
因为各种塑料的流动性有差异,所以可以根据塑料的品种来粗略地估计分流道的直径,常用塑料的分流道直径推荐值如下表一。
但对于壁厚小于3mm,质量在200g以下的塑料,可用此经验公式确定其流道直径:
5
H=2/3b
3.3
式中,m—流经分流道的塑料量(g);L—分流道长度(mm).
③分流道的布置:
分流道的布置取决于型腔的布局,两者相互影响。
分流道的布置形式分平衡式与非平衡式两类,这里我们选用的是平衡式的布置方法。
④分流道与浇口的连接:
分流道与浇口的连接处应加工成斜面,并用圆弧过渡,有利于塑料熔体的流动及充填。
D、浇口的设计:
浇口是连接分流道与型腔之间的一段细短通道,它是浇注系统的关键部分。
浇口的形状、位置和尺寸对塑件的质量影响很大。
浇口的理想尺寸很难用理论公式计算,通常根
据经验确定,取其下限,然后在试模过程中逐步加以修正。
一般浇口的截面积为分流道截面积的3%~9%,计算得点浇口截面积为一,截面形状常为矩形,浇口长度为0.5~2mm,取1mm。
表面粗糙度Ra不低于0.4μm。
浇口的结构形式很多,按照浇口的形状可以分为点浇口、扇形浇口、盘形浇口、环形浇口、及薄片式浇口。
而我们这里选用的是点浇口。
简图如图七
图七点浇口
浇口位置的选择直接影响到制品的质量问题,所以我们在开设浇口时应注意以下几点:
①浇口应开在能使型腔各个角落同时充满的位置。
②浇口应设在制品壁厚较厚的部位,以利于补缩。
③浇口的位置选择应有利于型腔中气体的排除。
④浇口的位置应选择在能避免制品产生熔合纹的部位。
⑤对于带细长型芯的模具,宜采用中心顶部进料方式,以避免型芯受冲击变形。
⑥浇口应设在不影响制品外观的部位。
⑦不要在制品承受弯曲载荷或冲击的部位设置浇口。
第七部分成型零件的工作尺寸计算
A、型腔型芯的尺寸设计
该塑件的成型零件尺寸计算时均采用平均尺寸,平均收缩率,平均制造公差和平均磨损量来进行计算。
查有关模具设计手册得ABS的收缩率为s=0.3%~0.8%,故平均收缩率为
。
根据塑件尺寸公差要求,模具的制造公差取
。
型腔和型芯工作尺寸计算如下:
类别
塑件尺寸
计算公式
型腔或型芯工作尺寸
型腔计算
D
=[D+DScp-
]
79.87
59.76
45
44.795
5
4.775
型芯计算
50.78
45
45.20
B、型腔壁厚和底板厚度计算
在注射成型过程中,型腔主要承受塑料熔体的压力,因此模具型腔应该具有足够的强度和刚度。
如果型腔壁厚和底板的厚度不够,当型腔中产生的内应力超过型腔材料本身的许用应力时,型腔将导致塑性变形,甚至开裂。
与此同时,若刚度不足将导致过大的弹性变形,从而产生型腔向外膨胀或溢料间隙。
因此,有必要对型腔进行强度和刚度的计算,尤其是对大型塑件。
型腔材料预选为硬化塑料模具钢。
模具钢弹性模量E=2.2
许用应力
Mp
模具许用变形量
=0.03
一,型腔侧壁厚度计算:
1,按刚度条件计算
S刚>=
2,按强度计算
S强=>
=19mm
二,型腔地板厚度计算:
1,刚度条件计算
T刚>=
2,按强度计算:
T强>=
e
图八型腔尺寸
第八部分推出机构的设计
本模具采用推件板推出,推杆选用d=8标准推杆
推出距离d=45+5=50mm
第九部分模架的选用
以模具型腔的大小和进料方式,本模具选用点浇口DB型模架
系列为DB2335-70X35X90GB/T12555-2006
第十部分冷却系统的设计
1、冷却系统设计
塑料在成型过程中,模具温度会直接影响到塑料的充模、定型、成型周期和塑件质量。
所以,我们在模具上需要设置温度调节系统以到达理想的温度要求。
一般注射模内的塑料熔体温度为200℃左右,而塑件从模具型腔中取出时其温度在60℃以下。
所以热塑性塑料在注射成型后,必须对模具进行有效的冷却,以便使塑件可靠冷却定型并迅速脱模,提高塑件定型质量和生产效率。
对于熔融黏度低、流动性比较好的塑料,如聚丙烯、有机玻璃等等,当塑件是小型薄壁时,如我们的塑件,则模具可简单进行冷却或者可利用自然冷却不设冷却系统;当塑件是大型的制品时,则需要对模具进行人工冷却,以
3、冷却系统设计原则
①、尽量保证塑件收缩均匀,维持模具的热平衡
②、冷却水孔的数量越多,孔径越大,则对塑件的冷却效果越均匀。
③、尽可能使冷却水孔至型腔表面的距离相等。
④、浇口处加强冷却。
⑤、应降低进水与出水的温差。
⑥、合理选择冷却水道的形式。
⑦、合理确定冷却水管接头位置。
⑧、冷却系统的水道尽量避免与模具上其他机构发生干涉现象。
⑨、冷却水管进出接头应埋入模板内,以免模具在搬运过程中造成损坏。
4、冷却系统的结构形式
根据塑料制品形状及其所需的冷却效果,冷却回路可分为直通式、圆周式、多级式、螺旋线式、喷射式、隔板式等,同时还可以互相配合,构成各种冷却回路。
其基本形式有六种,我们这里选用的是简单流道式。
简单流道式即通过在模具上直接打孔,并通过以冷却水而进行冷却,是生产中最常用的一种形式。
其结构如图十三:
图九冷却系统
第十一部分模具动作过程
图十模架机构
随着保压的时间结束,锁模机构卸载,在弹簧力的作用下A板和定模板分开待流到废料被拉出后在限位杆的作用下A板停止运动,动模继续后撤,废料和塑件在点浇口出断开,废料再自重下脱落,废料再抱紧力的作用下随型芯后移,在注塑机顶棍的作用下推出机构工作,塑件被推出型芯,脱落。
在注塑机的合模运动中,模架各个部分复位,准备下一次的注塑成型。
第十二部分设计小结
塑料工业是当今世界上最快的工业门类之一,对于我国而言,它在整个国民经济的各个部门中发挥了越来越大的作用。
我们大学生对于塑料工业的认识还是很肤浅的,但是通过这次塑料模具课程设计,让我们更多的了解有关塑料模具设计的基本知识,更进一步掌握了一些关于塑料模具设计的步骤和方法,对塑料模有了一个更高的认识。
这对我们在今后的生产实践工作中无疑是个很好的帮助,也间接性的为今后的工作经验有了一定的积累。
塑料制品成型及模具的设计还是个很专业性、实践性很强的技术,而它的主要内容都是在今后的生产实践中逐步积累和丰富起来的。
因此,我们要学好这项技术光靠书本上的点点知识还是不够的,我们更多的还应该将理论与实际结合起来,这还需要我们到工厂里去实践。
我相信在未来的我一定能走到最前头。
第十三部分参考资料
[1]高汉华何冰强主编,塑料成型工艺与模具设计,大连理工大学出版社,2007
[2]高汉华何冰强主编,塑料模具设计指导与资料汇编,机械工业出版社,2007