产品质量计划压力容器.docx
《产品质量计划压力容器.docx》由会员分享,可在线阅读,更多相关《产品质量计划压力容器.docx(17页珍藏版)》请在冰豆网上搜索。
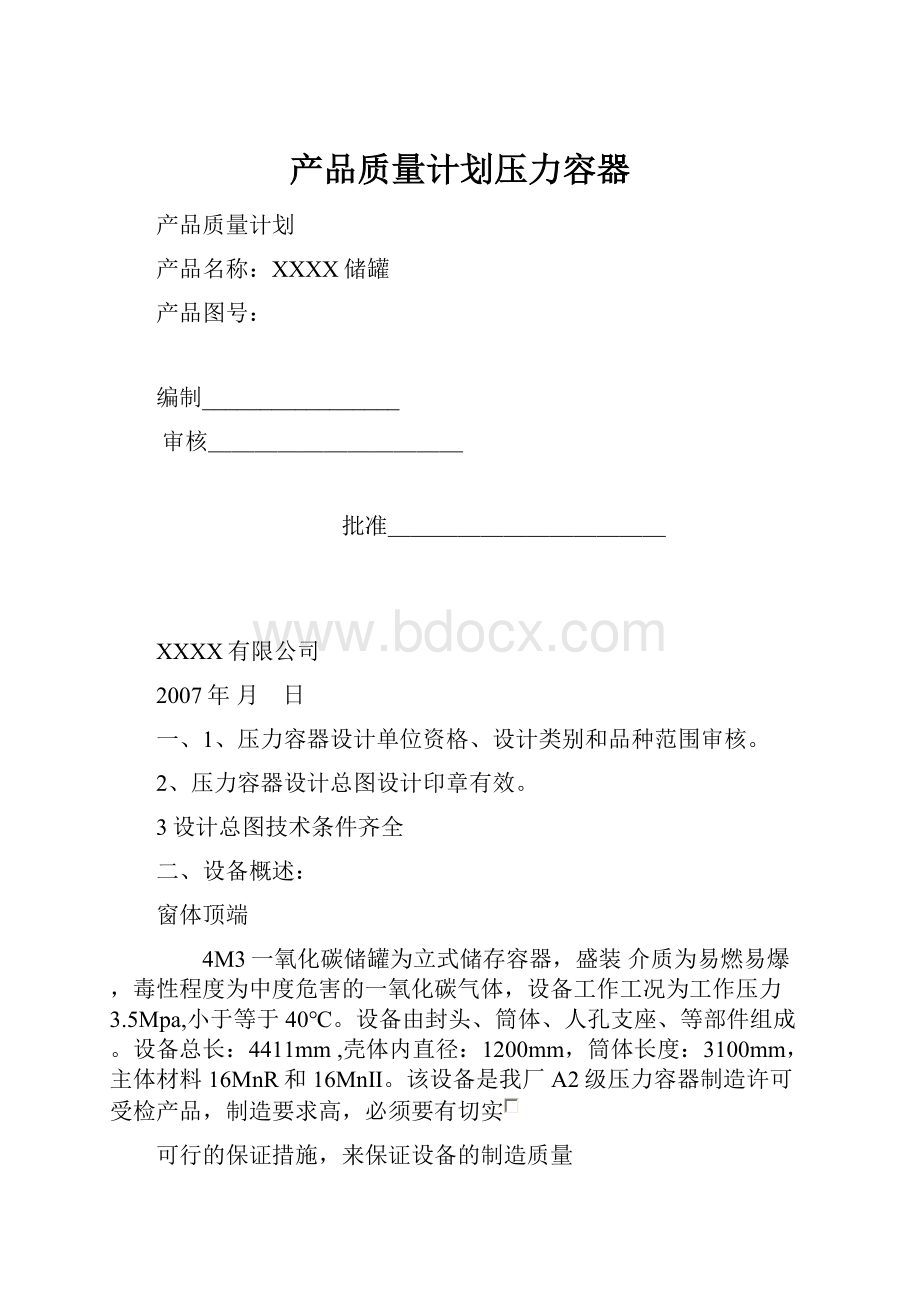
产品质量计划压力容器
产品质量计划
产品名称:
XXXX储罐
产品图号:
编制_________________
审核___________
批准____________
XXXX有限公司
2007年月 日
一、1、压力容器设计单位资格、设计类别和品种范围审核。
2、压力容器设计总图设计印章有效。
3设计总图技术条件齐全
二、设备概述:
窗体顶端
4M3一氧化碳储罐为立式储存容器,盛装介质为易燃易爆,毒性程度为中度危害的一氧化碳气体,设备工作工况为工作压力3.5Mpa,小于等于40℃。
设备由封头、筒体、人孔支座、等部件组成。
设备总长:
4411mm,壳体内直径:
1200mm,筒体长度:
3100mm,主体材料16MnR和16MnⅡ。
该设备是我厂A2级压力容器制造许可受检产品,制造要求高,必须要有切实
可行的保证措施,来保证设备的制造质量
窗体底端
。
1、设备设计条件
设计压力
(Mpa)
设计温度
℃
介质
工作压力
(Mpa)
工作温度
℃
腐蚀裕量水压
水压试验
(Mpa)
3.8
50
co
3.5
≤40
2.0
4.8
设备净重
(Kg)
焊接系数
类别
设备容积
(M3)
筒体壁厚
(mm)
筒体内径
(mm)
无损检测
2420
1.0
三类
4.0
12
DN1200
RT/PT/100%
2、主体材料
零部件名称
材料
执行标准
筒体
16MnRδs=16
GB6654-1996
封头
16MnRδs=18
GB6654-1996
JB/T4746-2002
人孔接管
16MnⅢ
JB4726-2000
人孔法兰
16MnⅢ
JB4726-2000
人孔法兰盖
16MnRδs≥46
GB6654-1996
三、设备制造前准备工作
1、工艺准备
首先进行工艺性审图、并作好审图记录,然后按施工图、规范、标准的要求编制制造工艺过程卡、焊接工艺规程、无损检测工艺卡、专用检验工艺卡、理化试验工艺卡、热处理工艺卡、水压试验工艺卡和气密试验工艺卡及外协事项专有表等文件。
负责人_________
2、材料准备
材料(包括钢板、锻件、焊材)的采购必须在经评审合格的供货单位进行。
订货要求符合相应材料标准(GB6654-1996、JB/T4726-2000、GB/T-5117-1995、GB/T5118-1995、GB/T14957-1994、JB/T4747-2002等),材料入厂应有合格的证明文件,标记齐全、完整、清晰。
用于制造主要受压元件筒体、封头、人孔接管、人孔法兰、及法兰盖的材质应按《容规》第25条第1、3款进行复验。
具体实施要求见附件一。
负责人_____
3、质量控制
按照工厂质量管理文件及设备特点,编写设备质量控制计划,质量计划经各责任人审核、质保工程师批准后,制造过程中严格按照质量计划进行质量控制工作。
负责人______
四、制造过程中主要质量控制环节、控制点
1、封头、筒体下料前进行表面、标记检查,并按JB/T4730超声检测4.1.5.3在坡口预定线两侧各50mm内100%扫查,成型前彻底清除影响封头和筒体成型质量的毛刺、氧化熔渣等。
封头成型方式为热压,成型后应保证与钢板的热处理状态一致,成型封头回厂后检验人员按JB/T4746-2002标准检查验收。
封头基本工艺流程:
板材→表面检查→划线→坡口超声检测→标记移植→下料→成型→测厚→切割直边余量→坡口砂磨→检验。
筒体成型、组对
筒体成型前彻底清除影响筒体成型质量的卷板机表面、钢板表面的毛刺、氧化熔渣等,筒体展开长度按封头实测周长配
作。
坡口加工采用半自动切割机切割后砂磨。
筒节园度是本控制环节的重点控制点,筒体组对按GB150-1998规定控制错边量和棱角度。
具体要求见附件二。
基本工艺流程:
板材→表面检查→划线→坡口超声检测→标记移植→下料→筒节成型→组焊→校园→检验→筒体组对→检验
2、产品焊接试板
产品试板焊接采用与筒体、同牌号、同材质、同规格、同热处理状态的钢板制作,必须组对在筒体纵缝延长线上,用相同的焊接方法,相同的焊接材料由同一焊工与筒体纵缝一同施焊。
焊接试板与筒体一同按图样要求进行无损检测后用氧乙炔火熖割下。
待产品完工后,随炉热处理后按JB/T4744-2000标准规定制作试样,进行力学性能和弯曲性能试验。
试板制作工艺详见附件三:
产品试板制作工艺卡。
基本工艺流程:
板材→表面检查→划线→标记移植→下料→刨削坡口→组焊→检验(包括无损检测)→随炉热处理→理化试验
责任人_____
3、设备装配
总装时应注意控制筒体与封头对接的错边量和棱角度众。
不允许强力组对 且不得锤击、划伤、电弧擦伤设备表面,装配质量控制要求详见附件四:
设备组装技术要求。
基本工艺流程:
组焊封头和筒体→检验(射线检测)→组焊人孔→检验(射线检测)→组焊各接管→检验(表面检测)→组焊支座→检验→热处理→压力试验→除锈、油漆、包装
4、标记移植
从设备 下料制作开始,检验员须按本厂公司质量保证手册规定,监督检查材料标记,焊工钢印、无损检测标记、产品制造编号的移植,以便对产品制造质量进行追踪。
主要受压元件材料见附件四:
主要受压元件材料标记及焊工钢印分布图。
责任人_____
5、无损检测
该容器为三类压力容器,筒体A、B类焊缝100%RT,≤250mm接管B类焊缝和C、D类焊缝100%表面检测。
无损检测责任人应按本厂公司质量保证手册规定,负责审核无损检测工艺卡,检查设备,按JB/T4730-2005标准进行检测,按容规要求填写报告。
无损检测工艺卡详见附件五。
责任人_____
6、理化试验
(1)钢板应按GB6654-1996标准进行复验
序号
检验项目
取样数量
取样方法
试验方法
1
化学分析
1(毎炉罐号)
GB222
GB223
2
拉伸
1
GB2975
GB228
3 、
冷弯
1
GB232
4
0℃冲击
3
GB4159
(2)锻件应按JB4726-2000标准进行化学成分、力学性能复验。
超声检测级别按JB4726-2000标准,方法和评级标准按JB/T4730标准进行。
7、热处理
热处理工艺编写按照《容规》、JB/T4709-2000内容编写,由热处理责任人审核。
并下达热处理工艺卡。
产品试板与试制产品同炉热处理。
分包单位应严格按照热处理工艺卡进行热处理,并按照《容规》格式填写报告。
热处理完成后,热处理责任人应审核报告和热处理曲线,并在报告上签字确认。
热处理工艺和热处理工艺卡见附件六。
责任人_____
8、水压试验
按《容规》及技术条件要求进行水压试验,试验压力为
XXXMPa,操作人应事先进行检查。
水压试验工艺卡由责任人审核。
具体要求见附件七。
责任人_____
9、气密试验
按《容规》及技术条件要求进行气密试验,试验压力为
XXXMPa,操作人应事先进行检查。
气密试验工艺卡由责任人审核。
具体要求见附件八
责任人_____
10、焊接方案
(1)该设备选用的焊接工艺评定编号:
XXXX、XXXX、XXXX、XXXX具体要求见附件九:
焊接工艺规程。
(2)设备焊接选用焊工项目:
焊缝编号
焊工项目
A1、A2
SAW-1G(K)-07/09
B1、B2、B3
SAW-1G(K)-07/09
SMAW-II-1G-12-F3J
B4
SMAW-II-1G-12-F3J
B5~B10
GTAW-2G-3/18-02
D1~D6
SMAW-II-2FG-12/25-F3J
C1~C4
SMAW-II-2FG-12/25-F3J
(3)焊前清除坡口两侧50mm范围内的油、水、锈及污物等有害杂质。
(4)双面焊时采用碳弧气刨清根,刨林槽必须砂磨光洁经检查合格后用压缩空气吹净坡口内灰尘方可施焊。
(5)组装时的点固定位焊,焊接要求与焊缝相同,焊接过程中清除定位焊缝金属。
(6)各类焊缝余高按图样及GB150-1998第10.3.3条规定:
A、B类e1≤2.4mm、e≤1.5mm,C、D类焊脚取焊件中较薄母材厚度。
责任人_____
10、设备制造验收:
按《容规》、GB150-1998的规定执行,产品质量安全技术档案资料必须齐全、完整,向用户提供的随机资料包括设备竣工图、强度计算书、产品质量证明书及铭牌拓印件、压力容产品安全质量监督检验证书。
责任人______
五、竣工资料和产品质量证明文件:
产品竣工资料包括:
材料质量证明书、工艺流转卡、工艺文件、竣工图、产品质量证明书、产品铭牌、压力容产品安全质量监督检验证书、强度计算书。
产品质量证明书的内容按《容规》附件三。
责任人_____
六、主要制造、检验设备
检验设备
超声波测厚仪USTM-600
射线探伤机 XXH2505、XXQ3005
磁粉探伤机 HG-AFO
超声探伤仪 CTS-22
万能试验机 (600KN)
冲击试验机 (300J)
电动试压泵 SY-600B
空气压缩机
制造设备
半自动切割机
卷板机
埋弧自动焊机
焊机变位装置(自制)
手工电弧焊机ZX7-500B
氩弧焊机WSM-315IGBT
车床C630-B
摇臂钻床Z3040*16
牛头刨床B665-650
工件变位机ZT-30
铣床X5020A
桥式行车QD-20/5
七、说明:
质量计划编制依据为施工图、相关标准、规范。
质量计划由正文和附件两部份组成。
质量计划的修改按工厂技术标准规定程序执行。
相关责任人员会签:
(附件一)
一氧化碳储罐(三类)主要受压元件材料
复验技术要求
根据《容规》规定,该设备筒体、封头、人孔筒节、人孔法兰、人孔法兰盖使用的钢板、锻件应按相关标准进行复验。
一、钢板:
材质为16MNnR,厚度=16mm其复验内容:
1、检查钢板的表面质量和材料标志;
2、按炉复验钢板的化学成分:
3、按批复验钢板的力学性能、弯曲性能;
4、钢板质量证明书上已提供超声检测,在此不作钢板的超声检测复验。
5、试样制备:
(1)根据GB6654-1996标准要求,力学性能取一个拉伸、三个冲击试样、弯曲性能取一个试样、化学分析取一个试样 。
(2)、力学性能及弯曲性能取样:
根据GB/T2975-1998要求进行,分别在钢板1/4处切取拉伸、弯曲和冲击试样。
(3)化学成分分析取样:
考虑到GB222取样方法,化学成分分析取样不再单独取样,待拉伸试验数据完整齐全后,在拉伸试样夹头处钻φ12孔钻取铁屑,然后将等量样屑均匀混合即可。
二、锻件:
材质为16MnⅢ(人孔筒节和人孔法兰),复验内容如下:
(1)逐件检查锻件外观质量;
(2)按批复验锻件的力学性能和化学成分;
按照JB4726-2000标准要求,采购锻件时要求厂家提供同炉同批、同锻造工艺、同锻造比且同炉热处理的试样坯,并要求在质量证明书中注明该试样坯的规格。
用该试样坯进行复验锻件的力学性能和化学成分。
(3)逐件进行超声检测;
按照JB4726-2000标准要求验收,按照JB4730-2005标准进行超声检测。
三、人孔法兰盖:
材质为16MnR,厚度为55mm,按照GB150的要求热处理状态必须为正火状态。
下料时选用T=60mm的钢板加工,其复验内容和验收标准参照钢板执行。
附件二、工艺流程(包括焊接工艺)
附件三、产品试板
附件四、标记移植
附件五、无损检测工艺卡
附件六、热处理工艺
附件七、水压试验工艺卡
附件八、气密试验工艺卡
附件九、试制产品的焊接工艺规程和引用的焊接工艺评定
压力试验工艺卡
□水压□气压□气密性
产品名称 制造工令号
产品编号
试验日期
工艺卡编号
试压部位
介质温度℃
环境温度℃
压力表精度
等级
压力量程
试验介质
氯离子含量
mg/L
压力表表盘直径
(mm)
压力表检定日期
年 月 日
设计要求
压力试验
曲线
1
清除筒体内杂物,安装密封圈、压力表及阀门(压力表至少采用两个量程相同经检定合格,并应安装在被试验容器的顶
部便于观察的位置)未使用的管法兰应用盲孔法兰螺栓密封。
2
容器的开口补强圈应在压力试验前通入0.4-0.5Mpa的压缩空气,检查焊接接头的质量。
3
试验时容器顶部应设排气口,充液时应将容器内的空气排尽,试验过程中应保持容器表面的干燥,以便于
于观察。
4
按“压力试验工艺规程”和曲线试压,试验时压力应缓慢上升,达到规定的试验压力后,保压时间一般不少于30min,
然后将压力降至规定的试验压力80%,并保持足够长的时间以对所有焊接接头和连接的部位进行检查。
如有渗漏,修补
后应重新试验。
容器试验过程中应无渗漏,无可见的变形,无异常的响声。
试压合格后及时将液体排尽,清理容器内部
5
压力试验完毕后,操作者填写试验报告,检验员确认,责任工程师审核,监检单位代表签字确认。
整个试验过程中应将
安全生产放在第一位,如发现问题,立即停止加压,疏散人员,并向有关部门汇报。
编制人 年 月 日 审核人 年 月 日
磁粉检测工艺卡
委托单位
检测单位
工件名称
容器类别
三类
工件材质
工件规格
检测时机
外检合格
表面状况
良
检测比例
100%
检测部位
灵敏度试片型号
-30/100
仪器型号
HG-AFO
磁化方法
磁轭法
磁粉种类
黒磁膏
磁悬液浓度
18g/L
磁化方向
纵向磁化
磁化电流
/
提升力
≥45N
磁化时间
2S×2
触头(磁轭)间距
75~200mm
检测标准
JB/T4730.4-2005
合格级别
I级
检测工艺编号
检测程序
预处理→磁化→施加磁悬液→检验→复验→退磁→后清洗
检测部位示意图
编制
审核
无损检测专用章
200年月日
200年月日
渗透检测工艺卡
委托单位
检测单位
工件名称
容器类别
三类
工件材质
工件规格
检测时机
表面状况
良
检测比例
100%
检测部位
对比试块
镀铬试块
渗透剂型号
HG-3P
清洗剂型号
HG-3R
显象剂型号
HG-3D
渗透温度
℃
渗透时间
≥10min
显象时间
≥8min
检测方法标准
JB/T4730.5-2005
合格级别
I级
检测工艺编号
检测程序
预处理→渗透→去除多余渗透剂→显象→检验→复验→后清洗
检测部位示意图
编制
审核
无损检测专用章
200年月日
200年月日
锻件、钢板超声检测工艺卡
委托单位
检测单位
钢板(锻件)牌号
钢板(锻件)编号
钢板(锻件)炉批号
检测时机
钢板(锻件)规格
检测部位
表面状态
仪器型号
检测方法
探头型号
扫查方式
试块型号
扫描调节
耦合剂
扫查灵敏度
表面补偿
检测标准
JB/T4730.3-2005
合格级别
级
检测工艺编号
检测规范
底波降低量度(BG/BF)
级
单个缺陷当量直径
级
密集区缺陷占检
测总积百分比%
级
单个缺陷指示长度(mm)
级
单个缺陷指示面积(cm2)
级
在任意一1m×1m检测面积内存在的缺陷面积百分比%
级
检测部位示意图
注:
检测结束前应1.对扫描量程进行复核2.对扫查灵敏度进行复核。
编制
审核
无损检测专用章
200年月日
200年月日
焊缝射线检测工艺卡
委托单位
检测单位
技术等级
AB级
工件名称
容器类别
工件材质
工件规格
检测时机
表面状况
良
检测部位
检测比例
底片黑度
2.0~4.0
设备型号
胶片牌号
胶片规格
增感屏厚度
Pb前屏mm
Pb后屏mm
像质计摆放位置
应识别丝号
(丝径mm)
#
mm
透照方式
射线源至工件距离(f)
mm
管电压
kv
管电流
mA
曝光时间
min
透照次数
次
显影时间
min
定影时间
min
显定影温度
℃
检测标准
JB/T4730.2-2005
合格级别
II级
检测工艺编号
焊缝编号
透照张数
张
检测部位示意图
编制
审核
无损检测专用章
200年月日
200年月日
焊缝超声检测工艺卡
委托单位
检测单位
工件名称
工件材质
容器类别
检测时机
工件规格
坡口型式
表面状况
检测部位
检测比例
仪器型号
探头型号
试块型号
扫查方法
耦合剂
扫描调节
表面补偿
检测标准
JB/T4730.3-2005
技术等级B级
合格级别
I级
检测工艺
编号
检测规范
评定线(EL)
定量线(SL)
判废线(RL)
检测部位示意图
注:
检测结束前应1.对扫描量程进行复核2.对扫查灵敏度进行复核。
编制
审核
无损检测专用章
200年月日
200年月日