涂装前处理生产线工艺设计注意事项.docx
《涂装前处理生产线工艺设计注意事项.docx》由会员分享,可在线阅读,更多相关《涂装前处理生产线工艺设计注意事项.docx(13页珍藏版)》请在冰豆网上搜索。
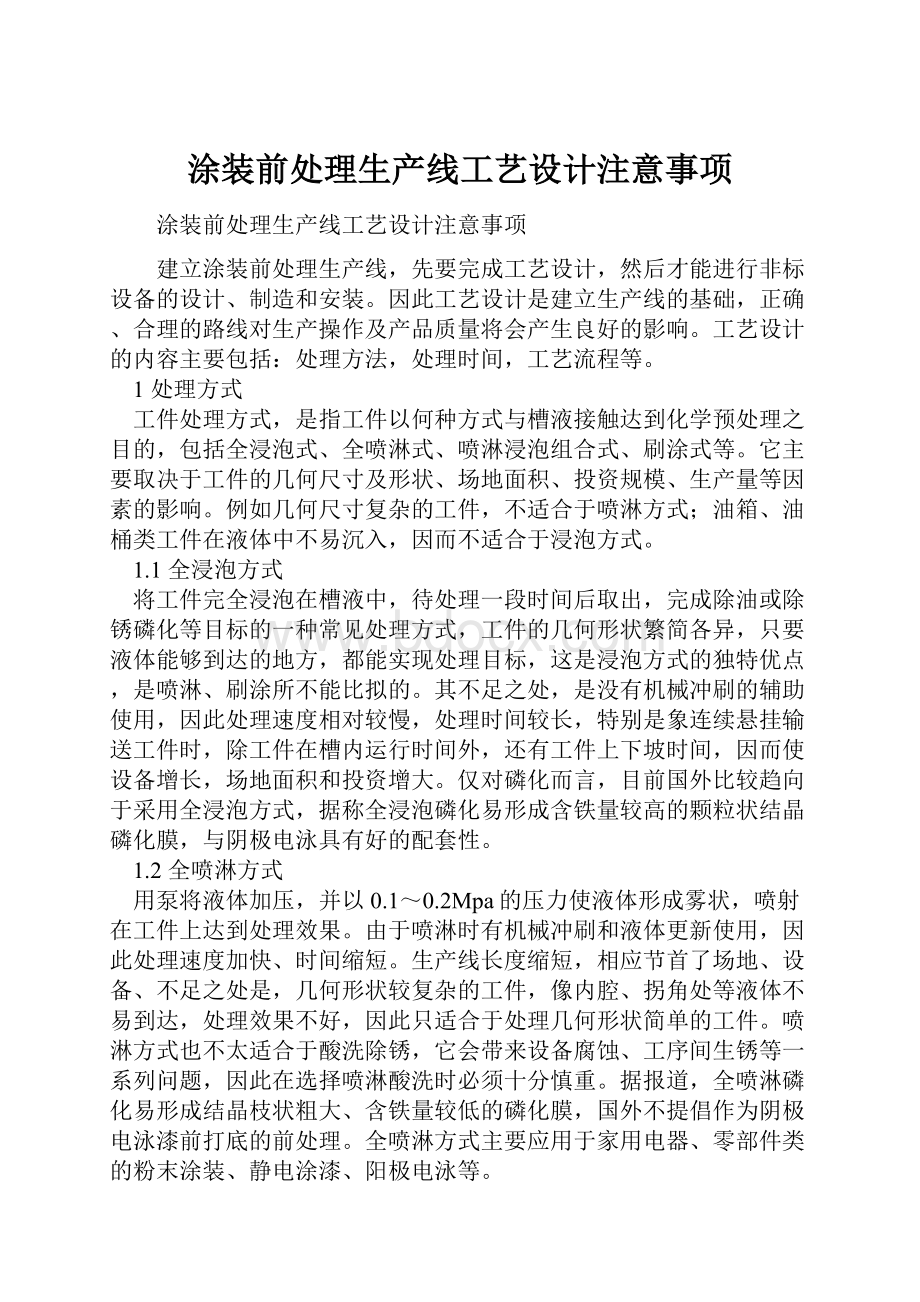
涂装前处理生产线工艺设计注意事项
涂装前处理生产线工艺设计注意事项
建立涂装前处理生产线,先要完成工艺设计,然后才能进行非标设备的设计、制造和安装。
因此工艺设计是建立生产线的基础,正确、合理的路线对生产操作及产品质量将会产生良好的影响。
工艺设计的内容主要包括:
处理方法,处理时间,工艺流程等。
1处理方式
工件处理方式,是指工件以何种方式与槽液接触达到化学预处理之目的,包括全浸泡式、全喷淋式、喷淋浸泡组合式、刷涂式等。
它主要取决于工件的几何尺寸及形状、场地面积、投资规模、生产量等因素的影响。
例如几何尺寸复杂的工件,不适合于喷淋方式;油箱、油桶类工件在液体中不易沉入,因而不适合于浸泡方式。
1.1全浸泡方式
将工件完全浸泡在槽液中,待处理一段时间后取出,完成除油或除锈磷化等目标的一种常见处理方式,工件的几何形状繁简各异,只要液体能够到达的地方,都能实现处理目标,这是浸泡方式的独特优点,是喷淋、刷涂所不能比拟的。
其不足之处,是没有机械冲刷的辅助使用,因此处理速度相对较慢,处理时间较长,特别是象连续悬挂输送工件时,除工件在槽内运行时间外,还有工件上下坡时间,因而使设备增长,场地面积和投资增大。
仅对磷化而言,目前国外比较趋向于采用全浸泡方式,据称全浸泡磷化易形成含铁量较高的颗粒状结晶磷化膜,与阴极电泳具有好的配套性。
1.2全喷淋方式
用泵将液体加压,并以0.1~0.2Mpa的压力使液体形成雾状,喷射在工件上达到处理效果。
由于喷淋时有机械冲刷和液体更新使用,因此处理速度加快、时间缩短。
生产线长度缩短,相应节首了场地、设备、不足之处是,几何形状较复杂的工件,像内腔、拐角处等液体不易到达,处理效果不好,因此只适合于处理几何形状简单的工件。
喷淋方式也不太适合于酸洗除锈,它会带来设备腐蚀、工序间生锈等一系列问题,因此在选择喷淋酸洗时必须十分慎重。
据报道,全喷淋磷化易形成结晶枝状粗大、含铁量较低的磷化膜,国外不提倡作为阴极电泳漆前打底的前处理。
全喷淋方式主要应用于家用电器、零部件类的粉末涂装、静电涂漆、阳极电泳等。
1.3喷淋-浸泡结合式
喷淋-浸泡结合式,一般是在某道工序时,工件先是喷淋,然后入槽浸泡,出槽后再喷淋,所有的喷淋、浸泡均是同一槽液。
这种结合方式即保留了喷淋的高效率,提高处理速度,又具有浸泡过程,使工件所有部位均可得到有效处理。
因此喷淋-浸泡结合式前处理即能在较短时间内完成处理工序,设备占用场地也相对较少,同时又可获得满意的处理效果。
目前在国内外,对于前处理要求较高的汽车行业,一般都趋向于采取喷淋-浸泡结合方式。
1.4刷涂方式
直接将处理液通过手工刷涂到工件表面,来达到化学处理的目的,这种方式一般不易获得很好的处理效果,在工厂应用较少。
对于某些大型、形状较简单的工件,可以考虑用这种方式。
2处理温度
从节省能源、改善劳动环境、降低生产成本、化学反应速度、处理时间和生产速度要求出发,在生产应用中普遍采用的是低温或中温前处理工艺。
工件除有液态油污外,还有少量固态油脂,在低温下,固态油脂很难去除,因此脱脂温度不管是浸泡还是喷淋均应选择中温范围。
如果只有液态油脂,选用低温脱脂完全可以达到要求。
对一般锈蚀及氧化皮工件,应选择中温酸洗,方可保证在10min内彻底除掉锈蚀物及氧化皮。
除非有足够的理由,一般不选择低温或不加温酸洗除锈,低温酸洗仅限于如:
工件锈蚀很少、无氧化皮;除锈时间不受限制;允许采用盐酸酸洗等情况。
表面调整工序,通常不需加温,一般就是常温处理。
低温或中温磷化,磷化速度都没有明显的差别,都可在较短的时间内快速形成磷化膜。
磷化后的工件,如果要求有较长的工序间存放时间,变应该选择中温磷化,才会有较好的防锈效果。
整个前处理过程,都可采用常温不加温洗方式,如果最后一道水洗是热水烫干,其水温应在80℃以上。
3处理时间
处理方式、处理温度一旦选定,处理时间应根据工件的油污、锈蚀程度来定。
一般可参考前处理药剂使用说明书的处理时间要求。
4工艺流程
根据工件油污、锈蚀程度以及底漆要求,分为不同的工艺流程。
4.1完全无锈工件
预脱脂--脱脂--水清洗--表调--磷化--水清洗--烘干(电泳底漆时可不干燥,直接进入电泳槽)。
这是标准的四工位流程,应用面广,适合于各类冷轧板及机加工的无锈工件前处理,还可将表调剂加到脱脂槽内,减少一道表调工序。
4.2一般油污、锈蚀、氧化皮混合工件
脱脂除锈“二合一”--水清洗--中和--表调--磷化--水清洗--烘干(或直接电泳)。
这套工艺是国内应用最为广泛的流程,适合各类工件(重油污除外)的前处理;如果采用中温磷化,还可省掉表调工序,简单的板型工件,也可省掉中和工序,成为标准带锈件的四工位工艺。
4.3重油污、锈蚀、氧化皮类工件
预脱脂--水清洗--脱脂除锈“二合一”--水清洗--中和--表调--磷化--水清洗--烘干(或直接进入电泳槽)。
对于重油污的工件,首先应进行预脱脂,除去大部分的油脂,以保证在下一步脱脂除锈“二合一”处理后,得到完全洁净的金属表面。
5几点注意事项
在工艺设计中有些小地方应该十分注意,即使有些是与设备设计有关的,如果考虑不周,将会对生产线的运行及工人操作产生很多不利的影响,如工序间隔时间,溢流水洗,磷化除渣,工件的工艺孔,槽体及加热管材料等。
5.1工序间隔时间
各个工序间的间隔时间如果太长,会造成工件在运行过程中二次生锈,特别是有酸洗工艺时,酸洗后工件极易在空气中氧化生锈泛绿,最好设有工序间水膜保护,可减少生锈。
生锈泛黄泛绿的工件,严重影响磷化效果,造成工件挂灰、泛黄,不能形成完整的磷化膜,所以应尽量缩短工序间的间隔时间。
工序间的间隔时间若太短,工件存水处的水,不能完全有效的沥干,产生串槽现象,特别在喷淋方式时,会产生相互喷射飞溅串槽,使槽液成分不易控制,甚至槽液遭到破坏。
因此在考虑工序间隔时,应根据工件几何尺寸、形状选择一个恰当的工序间隔时间。
5.2溢流水清洗
提倡溢流水洗,以保证工件充分清洗干净,减少串槽现象。
溢流时应该从底部进水,对角线上部开溢流孔溢流。
5.3工件工艺孔
对于某些管形件或易形成死角存水的工件,必须选择适当的位置钻好工艺孔,保证水能在较短的时间内充分流尽。
否则会造成串槽或者要在空中长时间沥干,产生二次生锈,影响磷化效果。
5.4磷化除渣
对于任何一种磷化液都会或多或少产生沉渣(轻铁系彩色磷化沉渣很少),应在工艺予设计时注明设有磷化除渣装置,特别是喷淋磷化时,除渣装置必不可少,典型的除渣装置有:
斜板沉淀器、高位沉淀塔、离心除渣器、纸布袋滤渣等都可供选择。
5.5槽体及加热管材料
虽然对于槽体加热管材料的选择不是工艺设计的内容,如果在工艺设计时不予提醒,可能会造成设备设计人员的疏忽,而影响整个生产线的运行。
对于硫酸、盐酸酸洗时,其槽体材料只能选用玻璃钢、花岗岩、塑料,加热管只能选用铅锑合金管、陶瓷管,而不能选用不锈钢材料。
如果是采用磷酸酸洗,其槽体及加热管材料均可选用不锈钢材料,当然玻璃钢、塑料、花岗岩均可。
[摘 要] 论述了涂装前处理的在脱脂、除锈、表面调整、磷化等方面的概况及发展。
[关键词] 涂装;前处理;磷化
0 前言
各种金属材料及其制品经机械加工、热处理以及在贮存和运输过程中,在其表面总会有氧化皮、油污等,这些表面污物会严重影响到表面处理过程如涂镀层的致密性及与基体的结合强度。
涂装前处理是涂装前的重要步骤,是提高涂装漆膜附着力、耐蚀性能和装饰性能的必要工作。
目前钢铁件的涂装前处理过程主要包括脱脂,除锈,表面调整及磷化等。
1 脱脂
目前常见的除油方法大致有碱性水基清洗除油、高温碱性化学除油、有机溶剂除油、电化学除油、超声波清洗除油等。
高温碱性除油能耗大,污染大,容易腐蚀金属等缺点,有机溶剂易挥发,易燃,成本高。
对于涂装前脱脂普遍使用碱性水基清洗除油,尤其对自动化大规模生产。
目前水基清洗技术应用广泛,我国的水基清洗剂研制起步较晚,但最近十几年发展较快。
水基清洗剂中最主要的有效成份是表面活性剂,它可促进乳化、分散作用,通过润湿、增溶作用,加快除油过程。
由于非离子型表面活性剂在很多性能方面超过离子型表面活性剂,非离子表面活性剂现在越来越受到欢迎。
脱脂的效果直接影响磷化产品的质量,脱脂技术的发展主要体现在以下几个方面:
①由于镀锌板及铝材的大量使用,采用低碱性脱脂可减少复合材质的浸蚀。
由于流水线脱脂一般要求在2~3分钟完成,因此喷淋处理是必要的,而且多采用中温脱脂,对油污较轻的可采用低温脱脂。
②为保证清洗质量,汽车,家电业广泛采用二次脱脂处理或[1]采用脱脂前选用热水预喷湿及多级脱脂处理,减轻脱脂负担,提高后脱脂的效果[2]。
③脱脂处理中磷酸盐排放水的“肥化”生物耗氧问题,表面活性剂的化学耗氧问题都是严重的污染。
为此国外开发了无磷或低磷脱脂剂,使用生物可降解的表面活性剂[3]。
④液体双组分脱脂剂大量使用,尤其是对于粉尘要求较严格的汽车涂装生产线。
金属清洗剂检验指标:
1.清洗能力(重量法)
金属清洗剂的清洗能力是清洗剂的重要性能,目前检验金属清洗剂的清洗能力的方法有很多钟,包括定性的检测有验油试纸法GB/T13312-91钢铁件涂装前除油程度检验方法(验油试纸法),脱脂棉擦试法,水膜法等。
定量检测法包括重量法,荧光法,其中重量法是最方便,简单的方法。
试片经打磨,和有机溶剂清洗干净,干燥后,称重P1,浸入到约80℃人工油污(20#机油2份,工业白凡士林1份,石油磺酸钡(杭州炼油厂)1份)5分钟以上,用提升器以1m/s速度提起,沥干20分钟,刮去底部的油滴并称重P2,将浸油并称重的试片在清洗剂中静渍3分钟摆洗3分钟,摆洗频率为30±1次/分钟.(往返为一次),距离为50±2mm,提出试片并在蒸馏水中摆洗10次,取出在70±2℃温度烘干30~40min,冷却称重P3,则洗油能力为(P2-P3)/(P2-P1)χ100%.
2.消泡性能
消泡性能试验主要是为了检查水基金属清洗剂溶液的泡沫消除能力。
试液按30g/L或说明书规定配制,并预热至30±2℃,将试液到入比色量筒中使液面距离塞下端面70mm,盖塞,在30±2℃下恒温10min取出,立即上下摇动1min,摇动距离为0.33m,频率为100~100次/min。
摇动完毕后,打开茼塞,在30±2℃温度下静置10min后观察泡沫高度。
3.乳化性能
乳化性测定采用比色量筒装50ml脱脂剂及规定数量的4#拉延油,温度在55℃,以均匀的速度上下摇晃30次,距离为400mm,记录下工作液的状态如有无分层现象。
4.漂洗性能
漂洗性能试验主要用与检查覆盖在金属表面上的清洗剂残留物被水洗去的性能。
将在清洗剂中清洗后的试片取出呈45º角放置到凉干为止,将凉干的试片全浸在蒸馏水中摆洗10次立即取出用热风机吹干试片。
检查试片表面有无清洗剂的残留物,再在试片上滴一滴无水乙醇,乙醇自然挥发后再检查试片上有无白色残留物。
5.对金属的腐蚀性能
对金属的腐蚀性能试验是将金属试片全浸在一定温度的水基金属清洗剂水溶液中,以金属试片失重和表面颜色的变化评定清洗剂对金属的腐蚀性能。
此外对金属清洗剂的性能检测还有硬水稳定性能,高低温稳定性和单片和叠片防锈性能。
在涂装前处理脱脂去油工序中,工件表面的油脂大多被脱脂液中的表面活性剂乳化与脱脂液中,当它们含量过高就会析出,从而影响脱脂效果。
因此要求脱脂液中含油量不超过4g/L。
在生产中可以采用溢流水除去表面析出的油脂或采用超滤膜法,对乳化液进行破乳使生产线上脱脂含油废水分离得以实现。
超滤透过液中油的含量可由原液的(100~1000)χ10-6下降为10χ10-6。
李政雄。
膜技术在涂装工业中的应用汽车工艺与材料,2004.310~16。
2 除锈
除锈也是磷化前处理的一步重要工序。
对于钢铁件常用的除锈方法有喷沙、抛丸、酸洗等。
钢铁除锈一般用添加缓蚀剂和润湿剂的稀酸洗,对于两性金属Zn、Al,可用弱碱液浸蚀。
对于大型工件还有用高压、超高压水除锈,高压水清理除锈技术具有高效优质成本低和无污染特点[4]。
3 表面活化
目前使用的表面调整剂,大部分主要成分为Jernstedt盐,这种含磷酸钛胶体的表调剂其表调能力良好,一般为粉末状,除了制备方法较复杂外,也有很多更难以克服的缺点。
Jernstedt盐的活性和寿命会受水中钙、镁离子影响很大。
钙、镁离子会与带负电的钛胶体电中和而使其失去在水中的稳定性,大大缩短了Jernstedt盐的使用寿命,但也有研究认为在表调槽中含有一定量的钙、镁离子有助于胶体的稳定。
另外,由于钛胶体在pH超过8.0–9.5和温度超过35℃时会沉聚,因而使用时必须在特定的pH值和温度下,这限制了其使用范围。
表面调整可使金属基体产生数量极多的晶核,使磷化膜均匀细致。
在生产中为保证表调剂效果,应采用去离子水或纯水配制,其电导率不大于200μs/cm。
若表面调整剂中加入了软化剂,可用自来水配制,消除了钙、镁离子的影响,为了防止表面调整剂中所含P2O74-对钢铁表面钝化形成磷酸铁蓝色或白色膜,表面调整剂中可添加Mg2+离子(以MgSO4形式加入),Mg2+与P2O74-摩尔比应保持在0.4~1.1[5]。
对镀锌板磷化前表调可采用添加硼酸盐的胶体磷酸钛盐[6],B2O72-:
PO43-的重量比在2~10:
1,由此得到的表调剂在硬水及自来水中稳定,可使磷化槽液游离酸保持在较宽范围,减少沉渣。
国外开发了现代液态表调剂,表面调整能力强热稳定性好,加热到50℃,其表面调整能力不变,使用寿命长,较粉状经济,且加料方便,分散性好,含钛量较低[7]。
目前,也有将表调剂加入到脱脂剂中,即脱脂表调“二合一”,但效果不够理想,其弊端是
(1)当加热到65℃以上,表面调整剂就会失去作用;
(2)pH值过高,胶体溶液凝聚结块,破坏了钛的稳定性。
表面调整检测指标
1.表调液状态
以0.1%浓度配制表调液,静置,观察表调液有无不溶物,絮状沉淀及分散情况。
2.表调液的磷化膜质量
配制新的表面调整液,试片经脱脂,表调,磷化后,通过扫描电镜观察磷化膜的结晶形貌,晶粒大小。
3.存放后表调液的磷化膜质量
配制的表面调整液,放置一段时间后取上部清液,试片经脱脂,表调,磷化后,通过扫描电镜观察磷化膜的结晶形貌,晶粒大小。
工作液中,一般只要控制工作液的pH值或,或用比色法测定工作液中Ti4+的含量,其方法是:
取25mL准确配置的0.1%的表面调整剂水溶液置于50mL的比色管中,加入98%的浓硫酸5mL,摇匀,再加入5mL,H2O2,摇匀,即显出黄色,以此作为溶液的标准颜色。
按上述方法分别制备15%,0.2%,0.3%等浓度的表面调整剂水溶液的标准颜色。
按上述将工作槽液的颜色与各标准颜色进行比色,以确定其浓度范围。
P79
4 磷化
自从1869年Ross申请第一个磷化专利已来,磷化处理技术已发展了一个多世纪。
为了防止汽车车身钢材的腐蚀,从20世纪70年代开始,镀锌板大量应用于汽车工业。
此前传统的磷化方式不适于镀锌板磷化,而于20世纪80年代开发了含Ni、Mn的三元体系磷化液[8]。
另外从节能方面的考虑,为了减轻车重,出现了铝及铝合金的车身及零部件,开发出了铝及铝合金的磷化液[9]。
从环保方面的考虑,目前磷化技术的进展主要表现为无亚硝酸盐磷化,无镍磷化,无铬钝化,其它则表现在钢、镀锌钢和铝材金属组合件的同时磷化,此外磷化还更加强调对操作人员更安全,无毒害;工艺过程简单化、低温化,磷化快速成膜等。
4.1 多种金属组合件的磷化
为了提高金属件的耐蚀性,镀锌钢板越来越多地作为汽车车身材料,此外为了减轻车体重量,铝材使用也有增加,如铝质的汽车配件——钢圈、散热管等。
金属组合件由于其电偶效应,更易腐蚀,因此其对涂装的要求也较高。
对金属组合件进行磷化处理,由于磷化层的绝缘性和“抛锚效应”——与漆膜的紧密结合,减缓了腐蚀的诱导产生和腐蚀的扩展,提高了抗腐蚀性能[10、11],磷化与不磷化的金属件比较,经过涂漆后,其抗蚀性可提高几倍。
因此,汽车结构材料的发展变化,促进了同时处理钢、镀锌钢、铝材的金属组合件磷化产品的研究。
目前,汽车工业广泛应用含镍、锰的三元锌系磷化,由于镀锌板的使用,在其表面难以形成磷叶石[Zn2Fe(PO4)2·4H2O],为了提高镀锌板的可涂装性和耐碱性,在镀锌板磷化时广泛采用含锌、锰、镍的三元阳离子磷化体系[8]。
镍,锰离子的加入可在镀锌板表面形成类磷叶石的结构,结晶紧密、更细。
所生成的磷化膜有较低的化学活性,与无镍磷化比较,增加了耐碱性和涂层的二次附着力(如图1)。
在镀锌板的磷化中,会出现锌的过度溶解和结块,通过加入氟化物(如氟硅酸,氟硼酸,氟钛酸)来改善这种情况[8]。
近年来美国提出了汽车制造厂家平均燃料基准强制执行方案,促使汽车厂家积极开发轻量化技术,其中最重要的一步是采用铝合金制作车体。
单一的铝材的最佳处理方法是经铬酸-铬酸盐化学处理后经油漆涂装。
也有开发了无铬工艺处理铝材,如氟钛酸/氟锆酸工艺,铈酸盐工艺及有机薄膜处理。
在汽车工业中较多的是钢材,铝材或钢,镀锌钢,铝材组合件,如果组合件涂装不良,则会产生较为严重的双金属电偶腐蚀和丝状腐蚀,丝状腐蚀作为一种特殊的腐蚀形式,发生在涂层下金属基体上,其腐蚀产物呈丝状从金属基体上直接生长出来[12],为了避免这种情况的发生,需要对组合件进行同时磷化处理。
对于铝合金及其组合件的处理的最重要的是磷化优劣受游离氟离子浓度的影响,其磷化时,游离氟离子有一个最佳浓度,当游离氟离子低于这个浓度时,不能得到适当膜重的磷化膜,其耐碱性也明显下降;当高于此浓度时,其二次附着力将变差[9],这是由于Na3AlF6与磷酸锌共同沉积于铝表面,影响了磷化膜的形成。
图2是在加入H2SiF6与不加入H2SiF6时膜重与游离氟含量的关系曲线。
磷酸锌处理液中,溶解下来的Al3+与F-反应生成络合物。
当Al3+累积到数十到数百ppm时,对膜的生成反应会有一定的影响,因此,为获得质量良好的磷化膜,必须除去处理液中过多的Al3+。
其方法是添加氟化钠,氟化钾,使之与Al3+反应生成沉淀,其反应式如下:
Al+3F-—→AlF3
AlF3+3F-+3Na+—→Na3AlF6↓(冰晶石)
磷化液中游离氟宜控制在100—600ppm,游离氟<100ppm,刻蚀不足,难以形成完整的膜,游离氟>600ppm,影响磷化膜的形成。
4.2 无亚硝酸盐磷化
亚硝酸盐作为磷化中的氧化促进剂,是目前使用最方便,最广泛,最有效,最经济的磷化氧化促进剂。
亚硝酸盐有毒,在磷化过程中容易产生氮氧化合物,污染环境,且沉渣多易堵塞喷嘴管道。
亚硝酸盐易分解,需配制成单独组分,磷化时不断补加,给使用和控制都带来不便,基于以上原因,人们正着力开发无亚硝酸盐磷化工艺。
在目前开发出的众多的新型促进剂中,硫酸羟胺(HAS)是较为实用的,其磷化过程中反应如下:
NH3OH++H2→NH4++H2O。
据报道1996年德国就有几条采用HAS的汽车生产线[13]。
HAS可单独作促进剂,HAS也可和其它促进剂相互配合使用,以减少HAS的用量[7]。
无亚硝酸盐磷化工艺中,另一类为双氧水促进,其还原产物为水,不产生任何环境污染,双氧水促进工艺在喷淋线上更显优势,适合镀锌板。
但由于双氧水在酸性溶液中不稳定,故需频繁检测促进剂。
从上是两种无亚硝酸盐磷化,都能完全避免氮氧化合物的产生,但是HAS工艺酸度较不稳定,双氧水工艺控制较麻烦,这是它们在磷化中的不足。
4.3 无镍磷化
70年代为了提高汽车的耐蚀性能镀锌板开始作为汽车车身材料,用量越来越大。
从涂装角度考虑,它与有机膜的结合力远低于钢板,因此涂装前的磷化显的更重要[14],而且通常是在含有较高Mn2+、Ni2+等磷化液中进行,以便得到耐碱性更好的磷化膜。
由于对废水中重金属离子的严格限制,我国目前的排放标准为1mg/L,而德国废水中要求不超过0.5ppm,因此需开发新的无镍磷化工艺。
镍可被其它离子取代,而无需牺牲磷化的综合性能[8],德国拜尔汽车公司的下属生产厂建立了世界上第一条无镍,无亚硝酸盐的磷化线,废水中镍浓度降低到0.2ppm以下]。
4.4 无铬钝化
钝化处理通过填充磷化膜孔隙有效地提高磷化膜的性能,特别是二次附着力,传统的方法用铬酸或铬酸盐的稀溶液进行封闭,欧美大多数汽车厂都使用钝化工序,而日本、韩国则没有此工序[1]。
由于Cr6+的致癌性和毒性,废水较难处理,成本高,同时对废水的排放标准要求严格Cr6+不超过0.1mg/m3,因此国外正大力开发和应用无铬钝化。
目前,已开发出较为成功,并已实际应用的钝化之一是含有促进剂的氧化锆无机钝化液[15、16、17],盐水暴露实验及油漆附着力实验表明其性能与含铬钝化性能相当。
该种工艺在德国已有上十条生产线使用[4]。
从环保方面考虑,无铬钝化或不用钝化是以后磷化后处理的方向与趋势。
4.5 低温磷化
由于环保和节能的要求,低温处理始终是磷化发展的方向。
高、中温磷化工艺时间长,渣多成本高,不利于自动化生产,为了提高磷化液的质量,减少沉渣,磷化工艺已向低温低渣,低能耗,优质磷化发展,当前低温磷化的技术的研究和开发已得到人们的重视,成为当前磷化研究的主要内容。
开发低温快速磷化工艺,其关键是研究和选择适宜的促进剂,以提高低温条件下的化学反应速度。
低温磷化的特征是反应动力小,腐蚀反应缓慢,因此,低温磷化膜具有均匀细致的特点。
低温磷化,为了保证较好的磷化效果,在工艺上有以下要求:
①选用渗透性强的脱脂剂,必要时应加热处理;②对低温磷化,尤其是室温磷化表面调整是必不可少的,胶体磷酸盐可以消除碱性脱脂或除锈等造成的表面不均匀性,改善工件表面与磷化液的适应性,促进反应效果。
低温反应由于磷化成膜反应平衡常数较低[18],应保持较低的游离酸度及较高的总酸度以增强反应的动力。
磷化首先是铁的腐蚀,为了解决低温下腐蚀作用缓慢,加强刻蚀,应添加0.5~1.5g/L的氟化物,既加强了腐蚀速度,又起到了缓冲剂的作用,增加了酸度的稳定性。
由于低温及酸度低,亚硝酸盐的分解减少,低温下亚硝酸盐的浓度较中、高温磷化高。
磷化性能指标检测
5 结语
涂装前处理中以水基脱脂剂为原料的水剂清洗技术总的发展趋势是向常温、高效、低泡、专用型多样化、节能方向发展。
表面调整则是向低钛含量,高效,能长时间保持活性的液体表调剂发展。
磷化处理已发展了一百多年,近三四十年是磷化技术发展最迅速的时期,工艺配方的改良,大大提高了产品的耐蚀性。
随着人们环保意识的加强和技术的进步,磷化则表现为无亚硝酸盐,无镍磷化,低温低渣快速磷化,磷化工艺的自动控制和检测,磷化工艺的简单化。
[参考文献]
[1]王锡春等.最新汽车涂装技术.机械工业出版社.1997.
[2]唐春华.现代磷化技术问答(Ⅰ).电镀与环保.1998;18
(1):
32~34.
[3]刘娅莉.磷化技术最新进展.电镀与涂饰.1998;17(4):
45~49.
[4]周丹,王庆国.超高压水喷射技术在表面预处理中的应用.化学清洗.2000;16
(1):
34~36.
[5]唐春华.现代磷化技术问答(Ⅱ).电镀与环保.1998;18
(2):
36~38.
[6]谢素玲等.电镀与涂饰.1993;12
(2):
48~50.
[7]杨喜云,陈范才,赵常就.常温磷化促进剂的研究.表面技术.1998;27(4):
18~20