液压实验指导书2.docx
《液压实验指导书2.docx》由会员分享,可在线阅读,更多相关《液压实验指导书2.docx(22页珍藏版)》请在冰豆网上搜索。
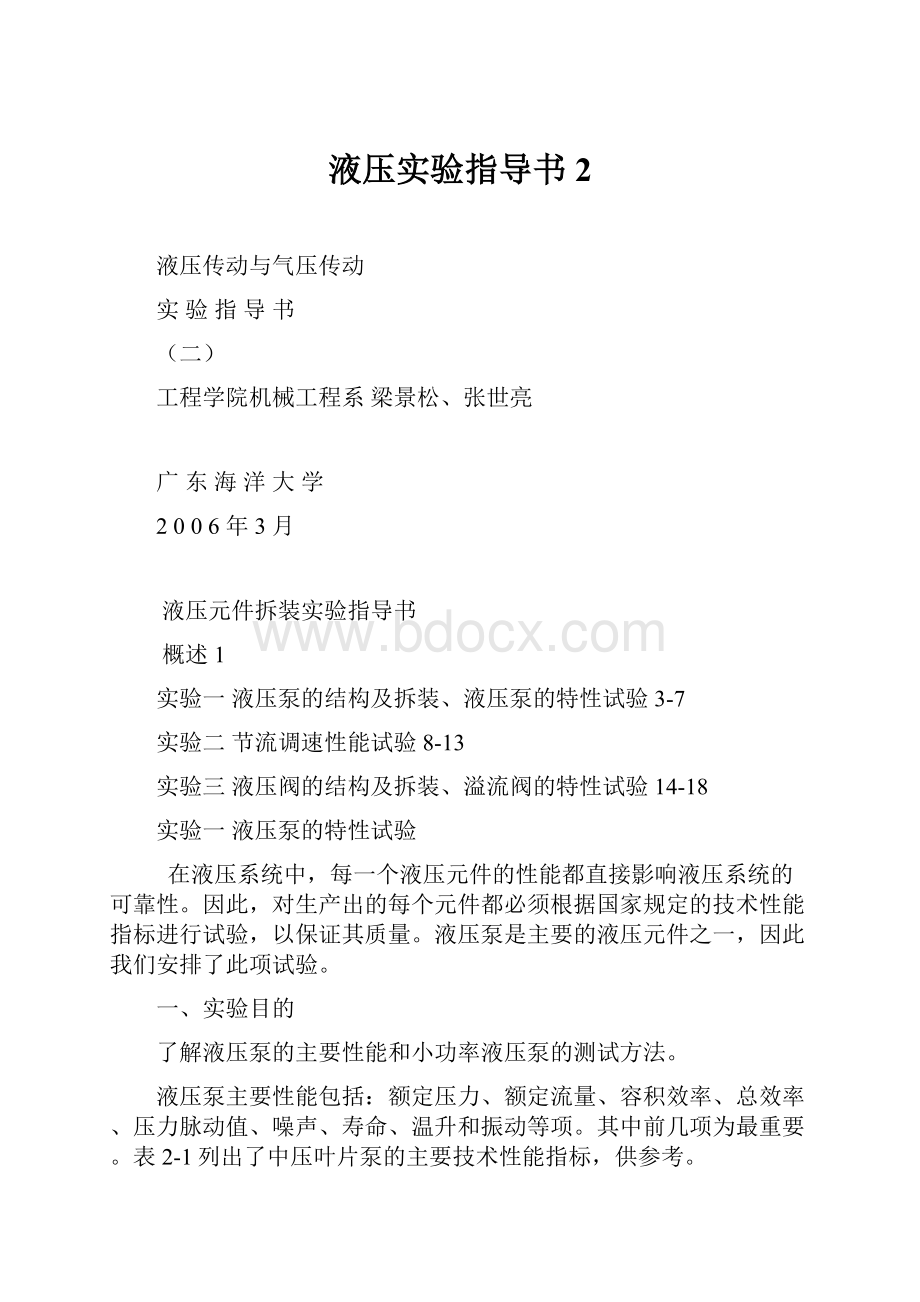
液压实验指导书2
液压传动与气压传动
实验指导书
(二)
工程学院机械工程系梁景松、张世亮
广东海洋大学
2006年3月
液压元件拆装实验指导书
概述1
实验一液压泵的结构及拆装、液压泵的特性试验3-7
实验二节流调速性能试验8-13
实验三液压阀的结构及拆装、溢流阀的特性试验14-18
实验一液压泵的特性试验
在液压系统中,每一个液压元件的性能都直接影响液压系统的可靠性。
因此,对生产出的每个元件都必须根据国家规定的技术性能指标进行试验,以保证其质量。
液压泵是主要的液压元件之一,因此我们安排了此项试验。
一、实验目的
了解液压泵的主要性能和小功率液压泵的测试方法。
液压泵主要性能包括:
额定压力、额定流量、容积效率、总效率、压力脉动值、噪声、寿命、温升和振动等项。
其中前几项为最重要。
表2-1列出了中压叶片泵的主要技术性能指标,供参考。
表2-1
项目
名称
额定压力
MPa
公称排量
ml/r
容积效率
%
总效率
%
压力脉动值
MPa
单级定量
叶片泵
6.3
≤10
≥80
≥65
±0.2
16
≥88
≥78
25~32
≥90
≥80
40~125
≥92
≥81
表中技术性能指标是在油液粘度为17~23CSt时测得,相当于采用20号液压油,温度为50℃时的粘度。
因此用上述油液做实验时,油温要控制在50℃±5℃的范围内才准确。
二、实验内容
1液压泵的压力脉动值;2液压泵的流量—压力特性;
3液压泵容积效率—压力特性;4液压泵的总效率—压力特性;
图2-11
8-定量液压泵9-溢流阀10-节流阀19-功率表20-流量计22-滤油器
三、实验方法
图2-11为QCS003B型液压实验台测试液压泵的液压系统原理图。
图中8为被试泵,它的进油口装有线隙式滤油器22,出油口并联有溢流阀9和压力表P6。
被试泵输出的油液经过节流阀10和椭圆齿轮流量计20流回油箱。
用节流阀10对被试泵加载。
1液压泵的压力脉动值
把被试泵的压力调到额定压力,观察记录脉动值,看是否超过规定值。
(<0.2MPa)测时压力表P6不能加接阻尼器。
2液压泵的流量—压力特性
通过测定被试泵在不同工作压力下的实际流量,得出它的流量—压力特性曲线q=f(p)。
调节节流阀10即得到被试泵的不同压力,可通过压力表P6观测。
不同压力下的流量用椭圆齿轮流量计和秒表确定。
压力调节范围从零开始(此时对应的的流量为空载流量)到被试泵额定压力的1.1倍为宜。
3液压泵的容积效率—压力特性
容积效率=实际输出功率/理论输出功率=实际流量/理论流量
在实际生产中,泵的理论流量一般不用液压泵设计时的几何和运动参数计算,通常以空载流量代替理论流量。
容积效率=实际输出功率/理论输出功率=实际流量/理论流量
4液压泵总效率—压力特性
总效率=泵的实际输出功率/泵的实际输入功率
泵的实际输出功率=实际流量×出口压差
液压泵的输入功率用电功率表19测量出。
功率表指示的数值N表为电动机的输入功率。
再根据电动机的效率曲线,查出电动机效率η电,N入=N表×η电
四、实验步骤
参照图2-1、图2-3和图2-11进行实验。
1将电磁阀12控制旋钮置于“O”位,使电磁阀12处于中位,电磁阀11的控制旋钮置于“O”位,阀11处于下位。
全部打开节流阀10和溢流阀9,接通电源,让被试泵8空载运行几分钟,排除系统内的空气。
2关闭节流阀10,慢慢关小溢流阀9,将压力P调至7MPa,然后用锁紧螺母将溢流阀9锁住。
3逐渐开大节流阀10的通流截面积,使系统压力P降低至额定压力6.3MPa,观测被试泵的压力脉动值。
4全部打开节流阀10,使被试泵的压力为零(或接近零),测出此时的流量,此即为空载流量。
再逐渐关小节流阀10的通流截面积,作为泵的不同负载,对应测出压力P、流量q和电动机的输入功率N表(由功率表测出)。
注意,节流阀每次调节后,须运行一至两分钟后,再测量有关数据。
压力P—从压力表P6上直接读数。
流量q—用秒表测量椭圆齿轮流量计指针旋转一定体积△V所需时间,根据公式q=△V/t求出流量q。
电动机的输入功率N表—从功率表19上直接读数再乘电动机效率η电,N表0.7KW以下η电=70%,0.7KW以上η电=78%。
将上述所测数据记入试验记录表(见表2-2)。
五、实验记录与要求
1填写液压泵技术性能指标;
泵型号规格:
__额定压力:
__排量:
__理论流量:
__
电动机型号:
__额定功率:
__转速:
__油液牌号:
__
2填写试验记录表(见表2-2);
3绘制液压泵工作特性曲线;
绘制q—P、ηv—P和η—P三条曲线。
4分析实验结果;
六、思考题
1液压泵的工作压力大于额定压力时能否使用?
为什么?
2从η—P曲线中得到什么启发?
3在液压泵特性试验液压系统中,溢流阀9起什么作用?
4节流阀10为什么能对被试泵加载?
实验一液压泵性能试验记录表表2—2
序号
数据
内容
1
2
3
4
5
6
7
8
1
被试泵压力
(MPa)
2
流量计读△V
(m³)
时间t秒
(S)
泵的流量q
(m³/s)
3
功率表读N表
(KW)
电动机效率
η电(%)
泵的实际输入功率
Pr=N表η电Nm³/s
4
实际输入钮矩
T(N.m)
泵转速n(r/min)
泵的实际输入功率
Pr=2πnT/60
5
容积效率ηv(%)
6
总效率η(%)
注意:
被试泵的压力P可在0~7MPa范围内,间隔1MPa取点。
实验二节流调速性能试验
在各种机械设备的液压系统中,调速回路占有重要的地位,尤其对于运动速度要求较高的机械设备,调速回路往往起着决定性作用。
在调速回路中节流调速回路结构简单,成本低廉,使用维护方便,是液压传动中一种主要的调速方法。
一、实验目的
1分析、比较采用节流阀的进油节流调速回路中,节流阀具有不同通流面积时的速度负载特性;
2分析、比较采用节流阀的进、回、旁路三种调速回路的速度负载特性;
3分析、比较采用节流阀、调速阀的调速性能;
二、实验内容
1测试采用节流阀的进油路节流调速回路的速度负载特性;
2测试采用节流阀的回油路节流调速回路的速度负载特性;
3测试采用节流阀的旁油路节流调速回路的速度负载特性;
4测试采用调速阀的进油节流调速回路的速度负载特性;
节流调速回路由定量泵、流量阀、溢流阀和执行元件等组成。
通过改变流量阀的通流面积,调节流入或流出执行元件的流量,以调节其速度。
节流调速回路按其流量阀的类型或安放位置的不同,组成上述四种调速回路,其调速性能有所不同。
三、实验方法
图2-12为QCS003B型液压实验台节流调速回路性能试验的液压系统原理图。
该液压系统由两个回路组成。
图2-12的左半部是调速回路,右半部则是加载回路。
在加载回路中,当压力油进入加载缸18右腔时,由于加载液压缸活塞杆与调速回路液压缸17(以后简称工作液压缸)的活塞杆都处于同心位置直接对顶,而且它们的缸筒都固定在工作台上,因此工作液压缸的活塞杠受到一个向左的作用力(负载FL),调节溢流阀9可以改变FL的大小。
在调速回路中,工作液压缸17的活塞杆的工作速度V与节流阀的通流面积a、溢流阀调定压力p1(泵的供油压力)及负载FL有关。
而在一次工作过程中,a和p1都预先调定不再变化,此时活塞杆运动速度V与负载FL有关。
V与FL之间的关系,称为节流调速回路的速度负载特性。
A和P1确定之后,改变负载FL的大小,同时测量出相应的工作液压缸活塞杆速度V,就可得到一条速度负载特性曲线。
四、实验步骤
参照图2-3和2-12进行实验
1采用节流阀的进油路节流调速回路的速度负载特性
(1)测试前的调整
加载回路的调整—全部打开节流阀10和溢流阀9的调节手柄,启动液压泵8,全部关闭节流阀10,慢慢拧紧溢流阀9的调节手柄(使回路中压力P6处于0.5MPa)。
转换电磁阀12的控制按钮,使电磁阀12左、右切换,加载液压缸18的活塞往复动作两、三次,以排除回路中的空气。
然后使活塞处于退回位置。
调速回路的调整—全部打开调速阀4及节流阀5、6、7和溢流阀2的调节手柄,启动液压泵1,全部关闭节流阀7和调速阀4,慢慢拧紧溢流阀2的调节手柄(使回路中压力P1处于0.5MPa)。
将电磁阀3的控制旋钮置于“左”位使电磁阀3处于左位工作。
再慢慢调节进油节流阀5的通流面积,使工作液压缸17的活塞运动速度适中(40~60mm/s)。
左右转换电磁阀3的控制旋钮,使活塞往复运动几次,检查回路工作是否正常,并排除回路中空气。
(2)按拟定好的实验方案,调定液压泵1的供油压力P1和本回路流量控制阀(进油节流阀5)的通流面积a,使工作液压缸退回,加载液压缸活塞杆向前伸出,两活塞杆对顶。
(3)逐次用溢流阀9调节加载液压缸18的工作压力P7。
分别测出工作液压缸的活塞运动速度v,负载应加到工作液压缸活塞不运动为止。
(4)调节供油压力P1和通流面积a,再测量工作液压缸的活塞在不同负载下的运动速度v。
即重复
(2)(3)步骤。
工作液压缸的活塞运动速度v=L/t(mm/s);L—工作液压缸的活塞运动行程;t—运动时间
负载F=P7×A1
其中:
P7—负载液压缸18的工作腔压力
A1—负载液压缸无杆腔的有效面积。
将上述所测数据记入实验记录表2-3。
2采用节流阀的回油路节流调速回路的速度负载特性;
(1)测试前调整
加载回路的调整—调节溢流阀9的调节手柄(使回路中压力P6处于0.5MPa)。
转换电磁阀12的控制按钮,使电磁阀12左、右切换,使活塞处于退回位置。
调速回路的调整—将电磁阀3的控制旋钮置于“O”位,使电磁阀3处于中位工作。
全部打开节流阀5、6全部关闭节流阀7、和调速阀4,再使电磁阀3处于左位工作,慢慢调节回油节流阀6的通流面积,使工作液压缸17的活塞运动速度适中(40~60mm/s)。
(2)按拟定好的实验方案,调定液压泵1的供油压力P1和本回路流量控制阀(回油节流阀6)的通流面积a,使工作液压缸退回,加载液压缸活塞杆向前伸出,两活塞杆对顶。
(3)逐次用溢流阀9调节加载液压缸18的工作压力P7。
分别测出工作液压缸的活塞运动速度v,负载应加到工作液压缸活塞不运动为止。
将上述所测数据记入实验记录表2-3。
3采用节流阀的旁油路节流调速回路的速度负载特性;
(1)测试前调整
加载回路的调整—调节溢流阀9的调节手柄(使回路中压力P6处于0.5MPa)。
转换电磁阀12的控制按钮,使电磁阀12左、右切换,使活塞处于退回位置。
调速回路的调整—将电磁阀3的控制旋钮置于“O”位,使电磁阀3处于中位工作。
全部打开节流阀5、6、7全部关闭调速阀4,再使电磁阀3处于左位工作,慢慢调节回油节流阀7的通流面积,使工作液压缸17的活塞运动速度适中(40~60mm/s)。
(2)按拟定好的实验方案,调定液压泵1的供油压力P1和本回路流量控制阀(旁油节流阀7)的通流面积a,使工作液压缸退回,加载液压缸活塞杆向前伸出,两活塞杆对顶。
(3)逐次用溢流阀9调节加载液压缸18的工作压力P7。
分别测出工作液压缸的活塞运动速度v,负载应加到工作液压缸活塞不运动为止。
将上述所测数据记入实验记录表2-3。
4采用调速阀的进油节流调速回路的速度负载特性;
(1)测试前调整
加载回路的调整—调节溢流阀9的调节手柄(使回路中压力P6处于0.5MPa)。
转换电磁阀12的控制按钮,使电磁阀12左、右切换,使活塞处于退回位置。
调速回路的调整—将电磁阀3的控制旋钮置于“O”位,使电磁阀3处于中位工作。
全部打开节流阀6和调速阀4,全部关闭节流阀5、7,再使电磁阀3处于左位工作,慢慢调节进油调速阀4的通流面积,使工作液压缸17的活塞运动速度适中(40~60mm/s)。
(2)按拟定好的实验方案,调定液压泵1的供油压力P1和本回路流量控制阀(进油调速阀4)的通流面积a,使工作液压缸退回,加载液压缸活塞杆向前伸出,两活塞杆对顶。
(3)逐次用溢流阀9调节加载液压缸18的工作压力P7。
分别测出工作液压缸的活塞运动速度v,负载应加到工作液压缸活塞不运动为止。
将上述所测数据记入实验记录表2-3。
为了便于对比上述四种调速回路的试验结果,在调节各参数时,应保持一致。
现列出一些参数的具体数值,供参考。
液压泵1的供油压力P1可拟定在3~4MPa之间;负载压力P7可拟定在0.5~3.5MPa之间(P1要大于P7);流量阀通流面积a的调节可参照工作液压缸17的活塞运动速度V大小进行,也可参照节流阀的刻度进行。
五、实验记录与要求
1实验条件
液压缸无杆腔有效面积A1:
__液压缸有杆腔有效面积A2:
__
液压缸活塞杆行程L:
__油液牌号:
__油液温度:
__
2填写数据表(表2-3和表2-4)
3绘制节调速回路的速度-负载特性曲线。
4分析实验结果。
六、思考题
1采用节流阀的进油路节流调速回路,当节流阀的通流面积变化时,它的速度负载特性如何变化?
2在进、回油路节流调速回路中,采用单活塞杆液压缸时,若使用的元件规格相同,问那种回路能使液压缸获得更低的稳定速度?
3采用调速阀的进油路节流调速回路,为什么速度负载特性变硬(速度刚度变大)?
而在最后,速度却下降得很快?
4比较采用节流阀进、旁油路节流调速回路的速度负载特性哪个较硬?
为什么?
5分析并观察各种节流调速回路液压泵出口压力的变化规律,指出那种调速情况下功率较大?
那种经济?
实验二采用节流阀的进油路节流调速回路的速度负载特性试验记录表表2-3
确定参数
测算内容
泵压P1
(MPa)
通流
面积
负载缸工作压力P7
(MPa)
负载FL=P7×A
(N)
活塞杆
行程L
(mm)
时间
t
(s)
活塞杆
速度V
(mm/s)
P2
(MPa)
P4
(MPa)
P5
(MPa)
小
1
2
3
4
5
6
7
8
中
1
2
3
4
5
6
7
8
大
1
2
3
4
5
6
7
8
实验二采用节流阀的回油、旁油路和调速阀进油路的节流调速回路试验记录表
项
目
确定参数
测算内容
泵压
P1
(MPa)
通流
面积
负载缸工作压力P7
(MPa)
负载
FL=P7×A
(N)
活塞杆
行程L
(mm)
时间
t
(s)
活塞杆
速度V
(mm/s)
P2
(MPa)
P4
(MPa)
P5
(MPa)
节
流
阀
回
油
路
调
速
中
1
2
3
4
5
6
7
8
节
流
阀
旁
油
路
调
速
中
1
2
3
4
5
6
7
8
调
速
阀
进
油
路
调
速
中
1
2
3
4
5
6
7
8
实验三、溢流阀性能实验
一、实验目的
1.通过实验,深入了解溢流阀稳定工作状态的主要静态特性(调压范围、压力稳定性、卸荷压力、压力损失、启闭特性等)
2.掌握溢流阀静态特性的测试方法和所用仪器、设备的使用方法,并能根据实验结果对被试阀的主要性能进行分析。
二、实验内容和原理
先导式溢流阀是液压系统中最常用的压力控制元件之一。
其性能的优劣直接影响到系统工作的品质。
本实验采用Y1-10B型先导式溢流阀作为被试阀,标准中规定此类阀出厂试验的技术指标如下表所示。
额定压力(Pn)
6.3MPa
卸荷压力
≤0.2MPa
额定流量(qn)
10L/min
压力损失
≤0.4MPa
调压范围
0.5~6.3MPa
压力振摆
≤0.2MPa
内泄漏
≤40mL/min
压力偏移
≤0.2MPa
启闭特性
开启压力Pk
闭合压力Pb
溢流量
≥5.3MPa
≥5MPa
≤0.1L/min
1.调压范围和压力稳定性
调压范围给定了溢流阀的使用压力范围。
在使用压力范围内压力振摆(在稳定工况下调定压力波动值)和压力偏移(在规定时间内调定压力的偏移量)的大小,是衡量压力稳定性的主要指标。
希望溢流阀在其额定压力范围内的调压范围要大,以满足各种压力工况的要求,而压力振摆和压力偏移却越小越好,以提高系统的平稳性。
2.卸荷压力和压力损失
卸荷压力是指先导式溢流阀在远程控制下卸荷(远程控制口直通油箱)、通过额定流量时阀所引起的压力损失(进、出口压力差),此压力损失将使通过的油液温度升高,它反映了阀在卸荷状态下泵的功率损失,卸荷压力越小越好,其大小主要取决于主阀芯的结构及其开口量的大小(开口量又与主阀弹簧刚度有关)。
压力损失是指调压手轮完全放松使主阀全开、通过额定流量时,阀所引起的压力损失,先导式溢流阀的压力损失一般略大于其卸荷压力,原因是在测试压力损失时,回油在阀内所经油路较长造成阻力较大所致。
3.内泄漏量
内泄漏量是指溢流阀调压手轮完全拧紧使主阀全闭,其进口压力为额定压力时通过阀口的泄漏量,它是作安全阀使用时的重要性指标,其值越小越好。
4.启闭特性
启闭特性是溢流阀在调压弹簧调定以后,阀芯开启和闭合过程中流量与压力间的变化关系。
使用中要求溢流阀能在不同溢流量下保持恒定的系统压力,希望其溢流特性如图4-1中的A,即在其进口压力P<PT(PT为调定压力或叫全流压力)时,阀完全不溢流,仅在P=PT时才溢流,且不管溢流量多少,其进口压力始终保持在PT值,实际上这是不可能的。
从溢流阀的工作原理可知,先导式溢流阀工作时必须先开启导阀,只有当导阀开到一定开口量后主阀口才开启使系统溢流,直到全流量溢流。
在溢流量变化的过程中,主阀开口量的变化将使弹簧力和稳态液动力也产生变化,所以实际溢流特性曲线为B,图中PK"为导阀开启压力、PK'为主阀开启压力。
由此可见,溢流阀在其进口压力P未达到调定压力PT时主阀未动作就从导阀口开始溢流,开始溢流时压力显然小于通过额定流量时的调定压力PT。
目前有关实验标准规定:
溢流阀在开启过程中溢流量达到额定流量1%时的进口压力PK(见图4-1中曲线B)称为开启压力,而在闭合过程中溢流量减至额定流量1%时的进口压力Pb(见图4-1中曲线C)称为闭合压力,全流压力PT与开启压力PK之差(PT-PK)称为静态调压偏差。
开启压力PK与全流压力PT之比(PK/PT)称为开启比,溢流阀的静态调压偏差越小(即开启比越大),则开启压力越接近调定压力,它所控制的系统压力便越准确。
有关实验标准还规定:
在额定压力Pn时的开启压力PK不得小于Pn的85%、闭合压力Pb不得小于Pn的80%。
有关参数见表4-1。
同时还规定Pb应小于PK,这是由于在开启与闭合过程中阀芯所受的摩擦力方向不同引起粘滞现象所致。
(开启时阀芯所受摩擦力与其底部所受的液压力反向,闭合时则同向)。
三、实验用设备和仪器
玻璃量筒一个
秒表一个
QCS003B型液压教学实验台。
本实验所采用的液压系统原理图如图所示,进行本实验时,节流阀10应完全关闭,实验中由于阀16和流量计的阻力小至可以忽略,所以被试溢流阀14的出口压力可以认为零。
在进行启闭特性实验过程中,由于溢流量相差很大,所以在测量大流量时用流量计,测量小流量时则改用量筒。
四、实验步骤、方法和注意事项
检查电控箱所有控制旋钮均置于“O”位,将压力表开关转至“P6”和“P8”位,关闭节流阀10,完全松开溢流阀9和14,起动液压泵8使其空转几分钟后才进行以下各实验。
1、调压范围和压力稳定性
将溢流阀9的压力(由P6表显示)调至高于额定压力10-15%(7MPa左右)然后迅速使二位三通阀11通电。
被试阀14的调压手轮从全松()调至额定压力(6.3MPa),再调至全松,观察P8的升降是否平稳、有无突变或滞后现象,反复两次,记下每次平稳变化的最小至最大压力的范围——调压范围。
在阀14的调压范围内设定5个压力点(应包含额定压力点)逐次调节阀14于各压力点分别读出P8的振摆值,并标出其中的最大值。
调节阀14使P8等于额定压力,观测压力表P8在1分钟或3分钟内的压力偏移值。
2、卸荷压力和压力损失
调节阀14使P8等于额定压力,使二位三通电磁阀15通电使阀14的远程控制口接通油箱,此时阀14全开,通过泵的全部流量(小于该阀的额定流量),记下此时阀前后的压力差即为卸荷压力,
反复二次。
使阀15断电并将阀14完全松开,记下此时阀14前后的压力差,即为压力损失,反复二次。
放松溢流阀9和14,使电磁阀11断电。
在测试卸荷压力和压力损失时,通过被试阀14的流量本应是额定流量值,但因实验台所配YB1-6型泵的实际供油量小于阀14的额定流量,故测试数据会有差异。
3、内泄漏量(关闭泄漏量)