年产120万吨炼铁车间设计毕业设计 精品.docx
《年产120万吨炼铁车间设计毕业设计 精品.docx》由会员分享,可在线阅读,更多相关《年产120万吨炼铁车间设计毕业设计 精品.docx(64页珍藏版)》请在冰豆网上搜索。
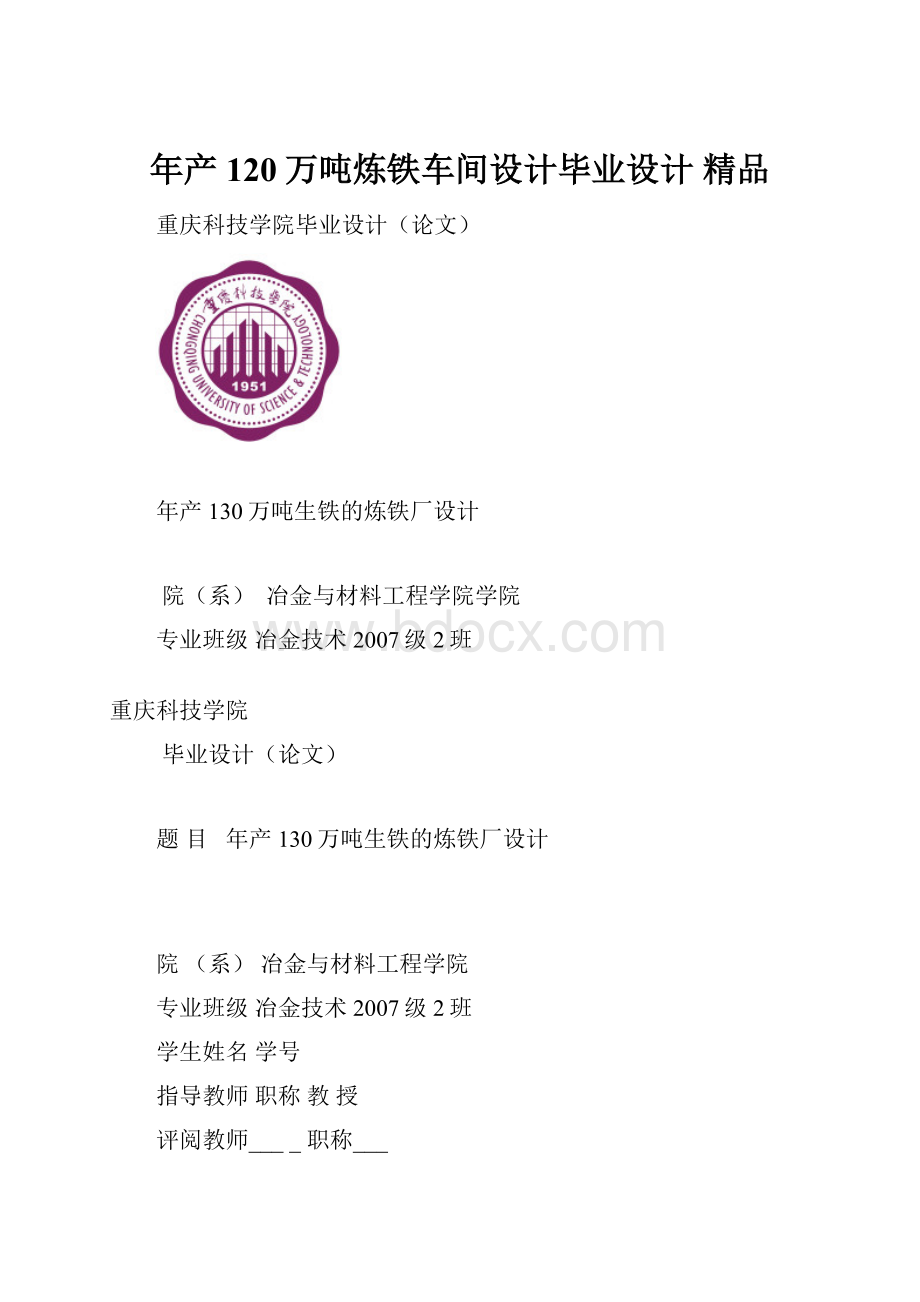
年产120万吨炼铁车间设计毕业设计精品
重庆科技学院毕业设计(论文)
年产130万吨生铁的炼铁厂设计
院(系)冶金与材料工程学院学院
专业班级冶金技术2007级2班
重庆科技学院
毕业设计(论文)
题目年产130万吨生铁的炼铁厂设计
院(系)冶金与材料工程学院
专业班级冶金技术2007级2班
学生姓名学号
指导教师职称教授
评阅教师____职称___
2010年6月10日
行距偏小
一个标题下只有一个问题就不必再分。
如6.1
中文摘要
高炉炼铁是获得生铁的主要手段,也是钢铁冶金过程中最重要的环节之一,在国民经济建设中起着举足轻重的作用。
本着优质、高产、低耗和对环境污染小的方针,设计建造年产量为130万吨的炼铁车间。
车间共有1498m³高炉一座,高炉采用了全冷却壁、砖壁合一薄壁炉衬、铜冷却壁、炭砖—陶瓷杯复合炉底、全软水密闭循环冷却系统、PW串罐无料钟炉顶、内燃燃式热风炉、全干式布袋除尘等一系列先进实用技术。
同时,本设计还结合了国内外相似高炉的一些先进的生产经验和相关数据,力争使该设计的高炉做到合理、长寿、实用,以期达到最佳的生产效益。
设计的主要内容包括炼铁工艺计算(包括配料计算、物料平衡和热平衡)、高炉炉型设计、高炉各部位炉衬的选择、炉体冷却设备的选择、风口及出铁场的设计、原料系统、送风系统、炉顶设备、煤气处理系统、渣铁处理系统、高炉喷吹系统和炼铁车间的布置等。
关键词:
炼铁炼铁工艺计算高炉炉体设计无料钟炉顶内燃式热风炉布袋除尘
Abstract
Pigironismainfromblastfurnace,furnaceironmakingisalsoaimportantprocessinironandsteelmaking,andit‘splayanimportantroleintheconstructionofnationaleconomy.basedonthetargetofhighproductivity,highquality,lowconsumption,longcampaignandenvironmentprotection.thedesignisaimatdesignafurnacewhichproduce1300thousandspigironperyear,theplanthasa1498m³furnacewhichseriesofadvancedandapplicabletechnologieswereadopted,suchasfullcoolingstave,thininnerliningofintegratedbrickingandstaves,carbonbrickscombinedfurnacebottomwithceramiccup,closedloopsoftwatercirculationandcoolingsystem,bell-lesstopwithcentralcharginghopper,innercombustionburnertypehotairstove,drybaggasdedustingetc.
Thedesignprogramconsistofabstract、foreword、technologicalcalculate(containblast-furnaceburden、materialbalancecalculateandthermalequilibriumcalculate),thechooseoffurnaceliningandcoolingplant,thedesignoffurnacelines,tuyereandcastinghouse,materialsystem,blastsystemfurnaceroofsystem,gasdisposesystem,ironandslagdisposesystem,fuelinjectionsystemandthedispositionofplant.Besides,thedesignalsoconsultsomeadvancedproduceexperienceanddatafromhomeandabroadsimilarfurnacetomakethedesignachievebest.
Keywords:
ironmaking;Ironmakingcalculation;blastfurnacedesign;bell-lesstop;drybaggasdedusting;innercombustionburnertypehotairstove
1绪论
1.1我国高炉炼铁技术的进步
近10年来,中国高炉大型化、高效化、现代化、长寿化、清洁化发展进程加快,炼铁不仅表现在技术经济指标的显著提高,也表现在工艺技术装备水平迅速提升,其中有些已经进入了世界先进行列。
1.1.1高炉炉体结构技术的进步
高炉炉体结构中,两方面的进步是显著的。
一是软水或纯水闭路循环冷却得到了大面积的推广,其避免结垢、节水降耗的效果十分明显。
同时,我国的铜冷却避及传统的球磨铸铁冷却壁都具有世界先进水平。
二是国内的耐火材料技术已经达到或接近世界先进水平,这包括热风炉使用的硅砖和高炉炉缸使用的刚玉莫来石砖、复合棕榈刚玉砖、微孔刚玉砖以及炉身使用的SiC砖、铝碳砖等
1.1.2高炉无料钟炉顶设备技术创新
采用无料钟炉顶装料设备是现代化高炉的重要技术特征。
首钢自主设计研制的无料钟炉顶设备经历了20多年的创新发展历程,结合大型高炉生产技术的进步,在已有技术的基础上不断优化创新,攻克了大型高炉无料钟炉顶布料装置、齿轮箱冷却、设备工作可靠性及设备使用寿命等关键性技术难题,成为中国自主设计制造全部实现国产化并具有核心竞争力的关键技术装备。
1.1.3高炉煤气全干式布袋除尘技术
高炉煤气干式布袋除尘技术已有30多年的发展历程。
2007年1月,中国自主开发的高炉煤气全干式低压脉冲布袋除尘技术在迁钢2号高炉(2650m³)获得成功,完全取消了备用的煤气湿式除尘系统,研究开发了煤气温度控制、除尘灰浓相气力输送、管道系统防腐等核心技术,使中国在大、中型高炉煤气全干式布袋除尘技术达到国际先进水平。
1.1.4研究开发助燃空气高温预热技术
近年来我国高炉风温水平有了提高,多数在1100~1150℃左右,日本、欧洲及中国宝钢的高炉风温达到1250℃。
由于中国钢铁企业高热值煤气匮乏,大多数热风炉只能使用低热值的高炉煤气,为了实现高风温,开发了助燃空气高温预热技术。
其原理是:
设置两座助燃空气高温预热炉,通过燃烧低热值的高炉煤气将预热炉加热后,再用来预热热风炉使用的助燃空气。
预热炉燃烧温度在1000℃以上,助燃空气可以被预热到600℃以上,同时利用热风炉烟气余热预热高炉煤气到200℃。
由于提高了助燃空气、煤气的物理热,使热风炉拱顶温度也相应提高,从而可以有效地提高送风温度。
1.2我国高炉炼铁技术的发展趋势
1.2.1高炉炉容、技术装备大型化
我国炼铁产业集中度低,高炉平均炉容偏小,尚有7500万吨/年落后的小高炉没有淘汰。
我国现有870多家钢铁企业,拥有1300多座高炉。
但是>1000m³以上容积的高炉只有167多座,平均炉容只有570m³左右。
另外我国烧结机、焦炉、高炉的装备容积偏小且数量太多,产品质量不稳定和能耗高,企业效益受到影响。
1.2.2高风、温低燃料比
国际领先水平的热风温度为1300℃,国际先进水平为1250℃左右。
我国与国际先进水平的热风温度差距在100℃左右,是我国炼铁技术指标中与国际差距最大的地方。
我国炼铁工作者首先应当努力缩小这个差距。
热风温度是廉价的能源,这是用45%高炉煤气换来的,是降低炼铁燃料比的工作重点。
炼铁系统能耗占钢铁企业总能耗78.87%,污染物排放占2/3。
所以说,炼铁工序要承担联合企业的节能降耗、降成本、实现环境友好的重任。
特别是高炉炼铁工序占总能耗的59.26%,是钢铁企业节能工作的主攻方向,重点工作是降低炼铁的燃料比。
1.2.3精料技术的提高
高炉炼铁应当以精料为基础,精料技术水平对高炉炼铁的影响率占70%,高炉操作占10%,设备影响占10%,管理水平占5%,外界因素(包括上下工序,运输和动力)占5%。
近年来,一些钢铁企业对精料将方针重视不够,没有善待高炉,使高炉生产处于被劫状态,造成多方面损失。
1.2.4开发非高炉炼铁技术装备,促进炼铁技术的发展
目前非高炉炼铁技术有了较大的发展,但是仍然竞争不过高炉炼铁,是炼铁技术的发展方向,应以予以高度重视,有条件的钢铁企业可进行研究、试验。
2高炉配料计算
冶炼1t生铁,需要一定数量的矿石、熔刑和燃料(焦炭及喷吹燃料)。
对于炼铁设计的工艺计算,燃料的用量是预先确定的,是已知的量,配料计算的主要任务,就是求出在满足炉渣碱度要求条件下,冶炼规定成分生铁所需要的矿石、熔剂数量。
对于生产高炉的工艺计算,各种原料的用量都是已知的,从整体上说不存在配料计算的问题,但有时需通过配料计算求解矿石的理论出铁量、理论渣量等,有时因冶炼条件变化需要作变料计算[1]。
2.1配料计算的目的
配料计算的目的,在于根据已知的原料条件和冶炼要求来决定矿石和熔剂的用量,以配制合适的炉渣成分和获得合格的生铁。
2.2配料计算时需要确定的已知条件
2.2.1原始资料的收集整理
生产中原始资料分析常常不完全,或元素分析和化合物分析不相吻合,加之分析方法不同存在分析误差,以致各种化学组成之和不等于100%。
因此,应该先确定元素在原料存在的形态,然后进行核算,使总和为100%。
换算为100%方法,可以均衡地扩大或缩小各成分的百分比,调整为100%,或者按照分析误差允许的范围,人为的调整为100%。
调整幅度不大时,以调整Al2O3或MgO为宜。
在各种原料中化合物存在的形态和有关换算,按照下述方法处理。
烧结矿分析的S,P,Mn分别以FeS,P2O5,MnO形态存在。
它们的换算为:
S──FeSω(FeS)=ω(S)×
%
P──P2O5ω(P2O5)=ω(P)×
%
Mn──MnOω(MnO)=ω(Mn)×
%
式中的S,P,Mn等元素皆为分析值(百分含量),当要计算Fe2O3时,需要从生铁(TFe)中扣除FeO和FeS中的Fe,再进行换算。
ω(Fe2O3)=(
ω(Fe)-ω(FeO)×
-ω(FeS)×
)%
式中的Fe,FeO为分析所得烧结矿的全铁和氧化亚铁的百分含量,FeS为换算所得的硫化亚铁量。
天然矿石中的S以FeS2形态存在,换算式如下:
ω(FeS2)=ω(S)×
%,式中S为分析所得的百分含量。
2.2.2选配矿石
在使用多种矿石冶炼时,应根据矿石供应量及炉渣成分适当配比选取。
此时,需要注意以下几点:
1)矿石含P量不应该超过生铁允许含P量,因考虑P全部进入生铁,故需要依据矿石含量事先预算,若某种矿石冶炼含P超标,此种情况下,只能搭配含P更低的矿石冶炼。
2)冶炼铸造铁时,应该核算生铁含锰量是否满足要求。
ω[Mn]=ηMn×ω(Mn)矿×m(Fe)铁/ω(Fe)矿
式中:
ω[Mn]──生铁含锰量,%
ω(Mn)矿──混合矿含锰量,%
ηMn──锰的回收率,一般为0.5~0.6
m(Fe)铁──矿石带入的生铁的铁量,kg/t铁
ω(Fe)矿──混合矿含铁量,%
3)冶炼锰铁时,为保证其含锰量,必须检查矿石含铁量是否大于允许范围。
ω(Fe)矿=(100-ω[Mn]-ω[C]-ω[Si]-ω[P])/100×(ω[Mn]/ωMn矿×ηMn)
式中:
ω[Mn],ω[Si],ω[C],ω[P]表示锰铁中该元素含量,%
ω(Mn)矿──锰矿含锰量,%
ω(Fe)矿──锰矿允许含铁量,%
ηMn──锰回收率,通常为0.7~0.82
4)适当控制碱金属[2]。
2.2.3确定需要的冶炼条件
(1)根据原料条件,国家标准和行业标准等确定生铁成分。
C,P元素一般操作不能控制,而Si,Mn,S等元素可以改变操作条件加以控制。
(2)各种元素在铁,渣和煤气中的分配比例。
按照经验和实际生产数据选取。
(3)炉渣碱度选择碱,主要是取决于炉渣脱硫的要求,此外若冶炼低硅生铁钒钛磁铁时,还应该考虑炉渣抑制硅钛还原和利于矾的回收能力,在正常炉钢温度下,要保证流动性和稳定性,因此除了考虑二元碱度外,还需要有适宜的MgO含量,若炉料含碱金属还应该兼顾炉渣排碱要求。
(4)燃料比确定。
确定燃料比应该依据冶炼铁种,原料条件,风温水平和生产经验等全面衡定,在有喷吹条件下,力争多喷燃料。
(5)原燃料成分分析,入炉矿石成分见表2.1
表2.1入炉矿石成分(%)
成分
原料
TFe
Mn
P
S
Fe2O3
FeO
MnO
MnO2
CaO
烧结矿
55.63
0.093
0.048
0.033
70.30
8.18
0.12
0
10.10
球团矿
63.54
0.069
0.031
0.007
88.32
0.93
0.09
0
0.95
块矿
58.72
0.165
0.021
0.134
67.94
14.20
0
0.26
1.50
混合矿
57.00
0.094
0.044
0.035
72.86
7.450
0.108
0.016
8.21
不必空这一行,下同
续上表
成分
原料
MgO
SiO2
Al2O3
P2O5
FeS2
FeS
SO2
烧损
合计
烧结矿
2.61
6.20
1.13
0.11
0
0.09
0
1.16
100.00
球团矿
1.07
4.12
0.73
0.07
0
0.02
0
3.70
100.00
块矿
0.65
11.70
2.32
0.05
0.25
0
0
1.13
100.00
混合矿
2.26
6.22
1.146
0.10
0.02
0.07
0
1.54
100.00
焦炭成分分析见表2.2
表2.2焦炭成分(%)
固
灰分11.01
挥发分0.90
定
碳
SiO2
Al2O3
CaO
MgO
FeO
FeS
P2O5
CO2
CO
CH4
H2
N2
86.79
5.12
4.37
0.68
0.11
0.67
0.05
0.01
0.33
0.33
0.03
0.06
0.15
续上表
有机物1.30
∑
全S
游离水
H2
N2
S
100
0.53
4.80
0.40
0.40
0.50
喷吹物成分见表2.3
表2.3喷吹物成分
成分
C
H2
O2
H2O
N2
S
灰分
∑
SiO2
Al2O3
CaO
MgO
FeO
煤粉
77.48
4.35
4.05
0.79
0.42
0.66
7.48
3.42
0.60
0.30
0.45
100
6)确定焦比与煤比
根据目前国内生产经验,选择焦比为360Kg/t,煤比为160Kg/t。
7)元素分配率见表2.4
表2.4各种元素分配率[2]标题上不要引用
铁种
元素
Fe
Mn
P
S
V
生铁
炉渣
煤气
0.997
0.003
--
0.600
0.400
--
1.00
--
--
--
--
0.06
0.800
0.200
--
2.2.4配料计算的内容四级标题是什么?
(1)矿石用量及配比计算;
(2)生铁中铁量计算;
(3)渣量及炉渣成分计算;
(4)炉渣性能校核;
(5)生铁成分校核。
2.3计算方法与过程
2.3.1计算方法
为精确配料,现根据设计的生产要求,先假定生铁成分,然后用理论方法进行配料比计算,然后以配出的矿石为基础对矿石用量、生铁中铁量、渣量及炉渣进行计算,最后炉渣性能、生铁成分进行校核。
2.3.2确定生铁成分
根据设计的生产要求假定的生铁成分,规定Si=0.35,S=0.03,Mn=0.08,P=0.09,R=1.10,由公式[C]=4.3-0.27[Si]-0.32[P]+0.03[Mn],可得C=4.18,Fe=95.27。
2.3.3计算所配矿石比例
根据以上已知条件,先以1t生铁作为计算单位进行计算,确定矿石配比。
在计算时需要列出两个方程:
碱度方程和铁平衡方程,根据生产要求列出方程如下:
(1)铁平衡方程:
(2)碱度平衡方程:
式中CaO1,CaO2,CaO3,CaO焦,CaO煤,分别表示烧结矿、球团、生矿、焦炭、煤粉中的CaO含量。
SiO2
(1),SiO2
(2),SiO2(3),SiO2(焦),SiO2(煤),SiO2(R),分别表示烧结矿、球团、生矿、焦炭、煤粉中的SiO2含量、还原到铁水中的SiO2量(kg),其中SiO2(R)=
以1t生铁作为计算单位进行计算,据以上各表数据可以求得焦炭带入铁量=1.99kg,煤粉带入铁量=0.5775kg,行距不对
假定配烧结矿Xkg,球团矿配Ykg,块矿=100kg,因此有:
铁平衡方程:
碱度平衡方程:
联立解出方程组可得:
烧结矿=1323.83kg(占79%),球团矿=247.03kg(占15%),块矿=110kg(占6%),需要矿石总量为1670.86kg,入炉熟料率=94%。
2.3.4计算冶炼每吨生铁炉料的实际用量
冶炼每吨生铁炉料的实际用量计算见表2.5
表2.5冶炼每吨生铁炉料的实际用量
名称
干料用量kg
机械损失%
水分%
实际用量kg
混合矿
1670.86
0.5
—
1679.21
焦炭
360
0.5
4.8
379.08
煤粉
160
—
—
160
合计
2190.86
2218.29
2.3.5终渣成分及渣量计算
(1)终渣S含量
炉料全部含S量=1670.86×0.0004+360×0.005+160×0.0066=3.53kg
进入生铁的S量=0.3kg
进入煤气的S量=3.53×0.06=0.21
进入炉渣的S量=3.53-0.3-0.21=3.02kg
(2)终渣的FeO量=
=3.69kg
(3)终渣的MnO量=1670.86×0.00094×0.5×
(4)终渣的SiO2量=1670.86×0.0622+360×0.0512+160×0.0748-7.5
=126.83kg
(5)终渣的CaO量=1670.86×0.0821+360×0.0068+160×0.0060
=140.59kg
(6)终渣的Al2O3量=1670.86×0.01146+360×0.0437+160×0.0342
=40.35kg
(7)终渣的MgO量=1670.86×0.0226+360×0.0011
+160×0.003=38.64kg
终渣成分见表2.6
表2.6终渣成分
成分
SiO2
Al2O3
CaO
MgO
MnO
FeO
S/2①
合计
R
Kg
126.83
40.35
140.59
38.64
1.01
3.69
1.51
352.62
1.10
%
35.96
11.44
39.87
10.96
0.29
1.05
0.43
100
①由于分析所得Ca++都折算成CaO,但其中一部分Ca++却以CaS形式存在,CaS和CaO之质量差为S/2,为了质量平衡,Ga++仍以CaO存在,而S则只算S/2[2]
炉渣碱度R=1.10,符合规定值。
MgO%=10.96%,符合设计要求。
根据炉渣百分组成,校验炉渣物理性质得:
熔化温度1350℃,粘度2Pa·S(1450℃)。
该炉渣适合于炼钢铁生产。
2.3.6生铁成分校核
(1)含P量
(2)含S量
,
(3)含Si量
(4)含Mn量
(5)含Fe量=95.27%
(6)含C量=100-95.27-0.08-0.35-0.03-0.08=4.19%
生铁成分列于表2.7
表2.7生铁成分(%)
Fe
Si
Mn
P
S
C
合计
95.27
0.35
0.08
0.09
0.03
4.18
100
校验结果与生铁成分的误差很小,表明原定生铁成分恰当。
3高炉物料平衡计算
3.1高炉物料平衡计算的意义
通过高炉配料计算确定单位生铁所需要的矿石、焦炭、石灰石和喷吹物等数量,这是制定高炉操作制度和生产经营所不可缺少的参数。
而在此基础上进行的高炉物料平衡计算,则要确定单位生铁的全部物质收入与支出,即计算单位生铁鼓风数量与全部产品的数量,使物质收入与支出平衡。
这种计算为工厂的总体设计、设备容量与运输力的确定及制定生产管理与经营制度提供科学依据,是高炉与各种附属设备的设计及高炉正常运转的各种工作所不可缺少的参数。
3.2高炉物料平衡计算的内容
物料平衡是建立在物质不灭定律的基础上,以配料计算为依据编算的。
计算内容包括:
风量、煤气量,并列出收支平衡表。
物料平衡有助于检验设计的合理性,深入了解冶炼过程的物理化学反应,检查配料计算的正确性。
校验高炉冷风流量,核定煤气成分和煤气数量,并能检查现场炉料称量的准确性,为热平衡及燃料消耗计算打基础。
(1)原料全分析并校正为100%(表2.1;表2.2;表2.3);
(2)生铁全分析;(表2.7)
(3)各种原料消耗量(表2.5);
(4)鼓风湿度,f=1.5%;
(5)本次计算选择直接还原度rd=0.45;
(6)假定焦炭和喷吹物含C总量的1.0%与H2反应生成CH4。
上述1,2,3原条件已经由配料计算给出,本例仅假定其余各项未知条件,分别为鼓风湿度f=1.5%(12g/m3),富氧率2.5%,氧气浓度98%。
3.2.1根据碳平衡计算风量
(1)风口前燃烧的碳量C风根据碳平衡得:
C风=∑C燃-(C)×103-∑C直-CCH4
式中C风──风口前燃烧C量,kg;
(C)──生铁含C量%;
∑C燃,∑C直,CCH4──分别为燃料带入C量,直接还原耗C和生成CH4的C量,㎏[2];
按上式分别进行计算:
燃料带入的C=m(C)J+m(C)M=360×0.8679+160×0.7748=436.41kg
溶于生铁的C=41.8kg
直接还原耗碳=m(C)Mn+m(C)Si+m(