毕业设计实习报告.docx
《毕业设计实习报告.docx》由会员分享,可在线阅读,更多相关《毕业设计实习报告.docx(28页珍藏版)》请在冰豆网上搜索。
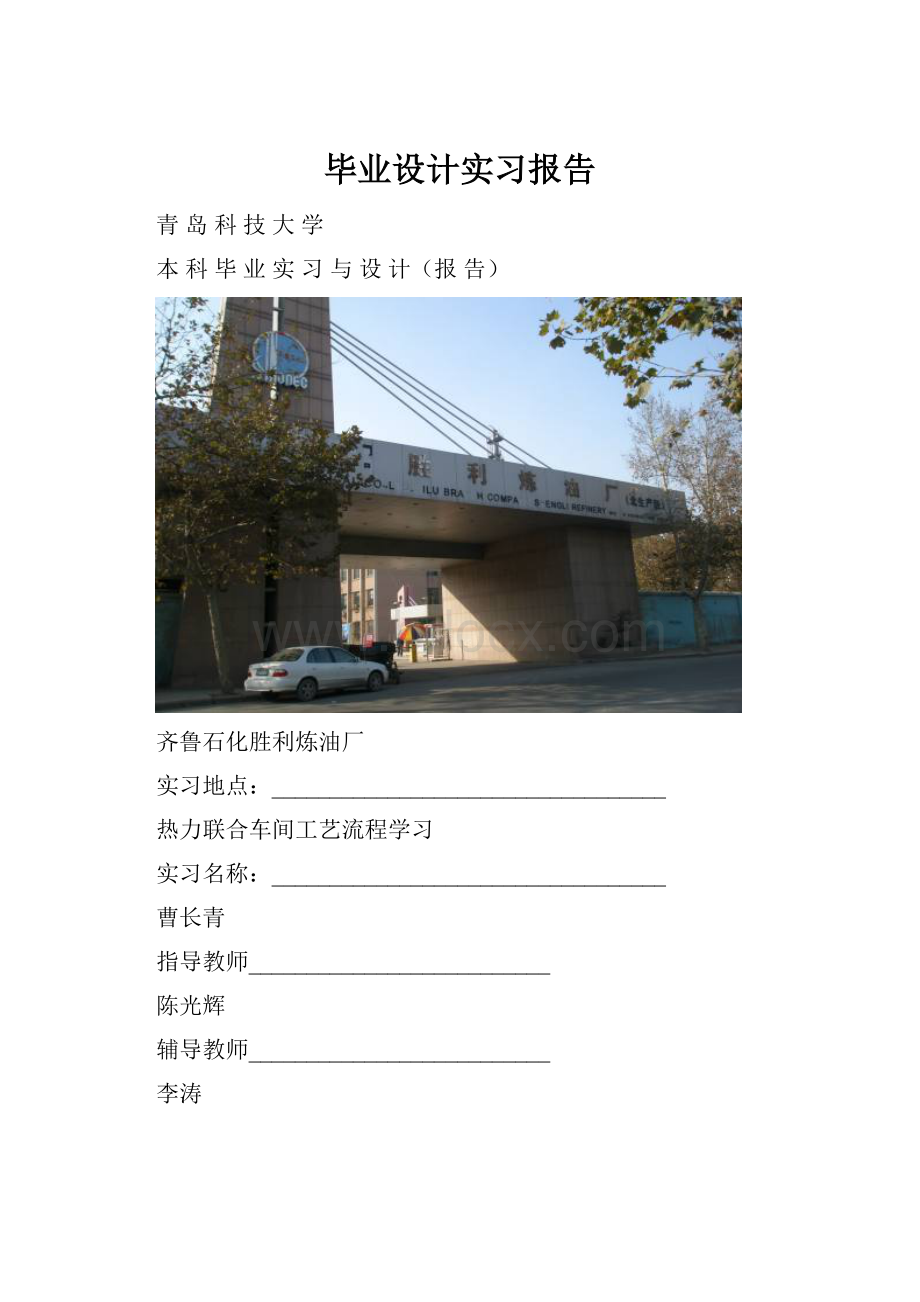
毕业设计实习报告
青岛科技大学
本科毕业实习与设计(报告)
齐鲁石化胜利炼油厂
实习地点:
__________________________________
热力联合车间工艺流程学习
实习名称:
__________________________________
曹长青
指导教师__________________________
陈光辉
辅导教师__________________________
李涛
学生姓名__________________________
0801011315
学生学号_______________________
081
化学工程与工艺
化工学院
_______________________________院(部)____________________________专业________________班
2011
11
20
______年___月___日
学生
李涛
指导教师
陈光辉
实习名称
齐鲁石化炼油厂一热电车间
实习时间
2011.10.25-2011.10.30
实习地点
齐鲁石化炼油厂
实习目的
1、巩固与运用所学各门课程的知识,理论联系实际,培养工程与工艺观点,训练观察分析和解决工程实际问题的独立工作能力。
2、通过对生产工艺过程的现场实习,掌握该产品生产的实际知识和技能,学习操作控制等有关知识。
3、收集各项资料和数据,为毕业设计或论文打下一定的基础。
4.毕业实习是培养化工类本科专业的高级工程设计技术人员的重要实践环节,通过实习使学生能够理论联系实际,进一步巩固和掌握所学理论知识,获得实践知识和技能,提高独立工作能力和组织管理能力,化工产品的技术经济分析能力,化工企业的环境保护意识等,同时还是培养本科生尊重体力劳动,尊重工人师傅的良好机会,使之养成良好的思想作风和工作作风。
5.学完本专业教学计划规定的理论教学课程之后,有针对性地到与本专业相关的工厂或研究单位,把所学的理论知识综合运用到生产和科研实践中,进一步加深、巩固知识。
齐鲁石化简介
齐鲁石化热电厂汽机车间是一个拥有四台60MW上汽机组,两台65-70MW的俄罗斯机组两台,两台哈汽65机组运检一体的综合车间,担负着齐鲁石化公司的发电任务,以娴熟的技术力量,有力的保障了公司的安全生产任务,整个车间团结实干是一个和谐的生产小基层.
中国石化集团齐鲁石化公司胜利炼油厂是全国颇具规模的炼油企业之一,于1966年4月动工建设,1967年10月投入生产,现已成为加工能力10500kt/a,占地面积587公顷的现代化石油加工企业。
该厂拥有生产装置和辅助生产装置60余套,拥有相应配套的科学研究、开发设计、计算机应用、环境保护等设施,是全国最具影响力的含硫原油加工以及沥青、硫磺生产和加氢工艺技术应用基地之一,生产的39种石油产品畅销全国27个省市,部分产品已进入国际市场。
本设计是齐鲁石化热电车间蒸汽发电装置,热力联合车间是炼油厂的一套“心脏”装置,两台循环流化床锅炉(CFB锅炉)为全厂生产装置提供蒸汽并兼顾发电。
按照设计,2006年之所以新建两台CFB锅炉,目的就是消化炼油厂自产的高硫石油焦,因此装置锅炉设计是全烧石油焦,适当可掺烧30%的煤。
热力联合车间2×25MW双抽凝汽汽轮发电机组是齐鲁石油化工公司为替代胜利炼油厂南区和橡胶厂7台燃油锅炉,充分利用胜利炼油厂副产品延迟焦化高硫石油焦,实现资源、区域供电和供热优化的新建工程。
工程由2台220t/h循环流化床锅炉、2台25MW双抽凝汽汽轮机和2台30MW发电机以及循环水、燃料制备输送、空压机等辅助系统组成。
目录
一、CFB锅炉装置概述
1.1装置概况…………………………………………………………………………5
1.2锅炉工艺流程…………………………………………………………………5
1.2.1锅炉启动点火系统………………………………………………………6
1.2.2汽水系统…………………………………………………………………6
1.2.3风烟系统…………………………………………………………………7
1.3主要辅助系统工艺过程简述…………………………………………………8
1.3.1给焦煤系统………………………………………………………………8
1.3.2石灰石粉输送系统………………………………………………………8
1.3.3飞灰再循环系统…………………………………………………………9
1.3.4气力输灰系统工艺流程…………………………………………………9
1.3.5底渣冷却、输送系统工艺流程…………………………………………10
二、汽轮机装置概述
2.1装置概况……………………………………………………………………10
2.2汽机工艺过程简述……………………………………………………………11
2.2.1主蒸汽系统……………………………………………………………11
2.2.2中压蒸汽系统…………………………………………………………11
2.2.3低压蒸汽系统…………………………………………………………11
2.2.4凝结水系统……………………………………………………………12
2.2.5除氧、给水系统…………………………………………………………12
2.2.6油系统…………………………………………………………………12
2.2.7真空系统………………………………………………………………13
2.2.8本体疏水系统…………………………………………………………13
2.2.9轴封抽汽系统…………………………………………………………13
2.2.10高低加汽、水系统……………………………………………………13
2.2.11循环水系统……………………………………………………………14
2.2.12工业水系统……………………………………………………………14
3.3汽轮机调节保安系统…………………………………………………………14
三、综述
3.1炉内脱硫工艺……………………………………………………………18
3.2能量转换…………………………………………………………………18
四、实习体会…………………………………………………………………19
一、CFB锅炉装置概述
1.1装置概况
热力联合车间2×25MW双抽凝汽汽轮发电机组是齐鲁石油化工公司为替代胜利炼油厂南区和橡胶厂7台燃油锅炉,充分利用胜利炼油厂副产品延迟焦化高硫石油焦,实现资源、区域供电和供热优化的新建工程。
工程由2台220t/h循环流化床锅炉、2台25MW双抽凝汽汽轮机和2台30MW发电机以及循环水、燃料制备输送、空压机等辅助系统组成。
2×25MW机组中的2台220t/h锅炉是由烟台现代冰轮重工有限公司设计并制造的循环流化床锅炉。
其型式为单炉膛、单汽包、无中间再热、自然循环、平衡通风、双高温绝热旋风分离器,全钢架M型露天布置、高温高压循环流化床锅炉。
锅炉由中国石化集团公司第二建设公司下属的山东胜越石化安装公司于2005年5月开始安装,1#、2#炉分别于2006年6月28日和2006年8月19日超水压试验完毕。
过热蒸汽额定压力为9.81MPa(g)、额定温度为540℃。
锅炉由全膜式水冷壁炉膛、水冷布风板、两个高温绝热旋风分离器、非机械式返料U阀和尾部对流受热面等组成。
在炉膛下部密相还原区布置有4个燃料进口(前墙)、2个旋风分离器回料进口(后墙)和27个二次风喷嘴以及4支启动燃烧器和12支BedLance燃烧器接口。
其中,8路石灰石通过前、后墙8个二次风嘴接管进入炉膛;2路飞灰再循环输灰管分别通过炉南北侧墙二次风嘴接管进入炉膛。
在炉膛底部敷焊密抓钉的水冷壁以及水冷布风板上敷设了厚度为80mm和200~207mm的整体浇注耐磨耐火衬里;在炉膛上部,与前墙垂直布置有4片水冷蒸发屏和6片翼屏过热器;在尾部竖井烟道内从上至下布置有高温过热器、低温过热器、钢管非沸腾式省煤器、二次风空气预热器、一次风空气预热器;高温过热器和低温过热器四周及顶棚烟道是由膜式壁围成的包墙过热器;在低温过热器和翼屏过热器及翼屏过热器和高温过热器之间分别布置有Ⅰ级和Ⅱ级文丘利喷水减温器。
Ⅰ级喷水减温器低过至屏过之间左右两根联络管之上各布置1套气动调节的减温调节阀组,屏过至高过之间左右两根联络管之上各布置1套气动调节Ⅱ级的减温调节阀组;正常情况下通过喷水减温器自动调节过热汽温度,控制其在安全和规定的范围之内,保证金属受热面不超温。
锅炉燃料设计采用胜利炼油厂延迟焦化的副产品——高硫组分的石油焦和山东山西混合贫煤;4支床上启动燃烧器和12支BEDLANCE油枪燃用胜利炼油厂0#不合格柴油(冬季为解决长距离输送管线内油品的冻凝问题,燃用的油品会临时改为凝点更低的柴油)。
通过气力输送系统将气固两相流向锅炉炉膛内喷入符合要求的石灰石粉,起到炉内脱硫、降低烟气SO2的作用,达到清洁燃烧的目的。
整个机组采用的是北京国电智深控制技术有限公司的DCS分散控制系统。
DCS能完成模拟量控制(MCS)、锅炉炉膛安全监控(FSSS)、顺序控制(SCS)、数据采集(DAS)等功能,可满足各种运行工况的要求,确保锅炉安全正常运行。
DCS的设计采用合理的冗余和冗错配置和诊断至卡件级的自诊断功能,具有很高的可靠性。
系统内任一组件发生故障,均不影响整个系统的工作。
单台锅炉设有3台DPU(其中DAS/MCS/SCS2台、FSSS1台)、配2个操作员站、1个历史站,2台机组公用1个工程师站。
1.2锅炉及辅助系统工艺过程简述
锅炉工艺过程简述
1.21锅炉启动点火系统
锅炉采用床上点火方式,热二次风为启动燃烧器提供助燃和冷却用风;锅炉用启燃器有两种规格:
其一是锅炉厂原配的每支油枪(工作油压:
0.8~1.5MPa)的出力约为1.3t/h(单支设计最大出力为1.56t/h);其二是北京xx公司设计制造的油枪(工作油压:
0.4~0.8MPa)油枪冷却风采用的是流风机提供的高压风、火检冷却风采用的是空压机提供的净化风、高能点火枪采用的是冷一次风。
启动燃烧器和床枪用燃用炼油厂0#不合格柴油,由详图一不合格柴油线经DN50(CFB界区内变径为DN80)输送至100m3的日用油罐,温度为常温。
2台流量11m3/h、出口压力4.0MPa的卧式三螺杆点火供油泵,将罐内0#柴油打入DN65的供油母管,回油气动调节门调节供油母管压力(0.8~1.8MPa),控制启动燃烧器进油量;回油调节阀后接于炉前回油母线,将回油输送至100m3油罐。
启动燃烧器雾化蒸汽来自于1.0MPa自用蒸汽母管,温度200~230℃,压力0.9~1.1MPa。
启动燃烧器的配风来自二次风空预器出口的热二次风,每支启动燃烧器通过总调节风门调节配风量。
1.2.2汽水系统
锅炉给水通过Φ219×16材质为20#钢的连接管引至省煤器,这一管路上布置有主给水调节阀组。
主给水调节阀组由主给水气动调节门、30%容量的旁路气动调节门组成和Φ194手动大旁路门、Φ32手动小旁路门。
给水经省煤器换热后通过2根Φ159×12、材质为20G的给水管路将给水引至汽包的筒体左右两侧后上部进入汽包下部,经汽包内给水管分配后,由汽包底部左右2根Φ529×36材质为A-106B的集中下降管通过18根Φ159×12材质为20G的分配管送到前、后、左、右四墙水冷壁的4个下联箱;在19160mm和19610mm标高处左右2根集中下降管各引出2根Φ159×12材质为20G分配管至4个水冷蒸发屏。
省煤器再循环(DN50)从左侧下降管引出接至省煤器入口联箱前。
炉膛前、后、左、右四墙水冷壁下联箱分别向对应的水冷壁供水,炉底的水冷布风板与前、后墙水冷壁下联箱相连。
整个炉膛四壁由364根Φ60×5.5材质为20G水冷壁管组成。
其中炉膛前、后墙水冷壁各122根,两个侧墙水冷壁管数量均为60根。
炉膛顶棚由后墙122根水冷壁管向前上弯曲而成,炉底是水冷布风板由60根60×5.5材质为20G的管子和管间材质Q235-A厚度5mm的鳍片焊接而成,水冷布风板前低后高具有一定的倾斜度(后墙水冷壁下联箱比前墙下联箱标高高77mm),整个水冷布风板上布置1059个Φ42×7、材质为312-TP310的耐磨型风帽。
前、后墙水冷壁管引至前墙上联箱,通过12根Φ159×12材质为20G的上升管引至汽包;两个侧墙上联箱分别通过4根159×12材质为20G的上升管引至汽包,4个水冷蒸发屏通过4根159×12材质为20G的上升管引至汽包。
给水通过上述5个回路,在炉膛内加热成汽水混合物,送至各自的上联箱,并通过共24根上升管引至汽包。
汽水混合物在汽包进行汽水分离,被分离出来的水被重新送入汽包水空间进行再循环,被分离出来的饱和蒸汽从汽包顶部4根饱和汽引出管引出
1.23风烟系统
锅炉炉膛内床料流化和燃烧用风以及返料器物料松动、流化主要由1台一次风机,1台二次风机和2台50%容量的高压流化风机供给。
◆一次风
一次风经一次风机升压后送至暖风器(2号炉已拆除)和3级一次风管式空预器加热后,主要分3路。
第1、2路至炉膛底部一次风室,通过布置在布风板上的1059只风帽使床料流化,从而在炉膛内外形成固体物料循环,并为燃料提供初始燃烧用风。
第3路送至布风板上方下一次风环管,12根支风管连接其上,每一支风管均设有手动调风门。
为12支BedLance燃烧器提供燃烧和油枪冷却用风。
一次风暖风器利用自用1.0MPa蒸汽,预热一次风空预器进风温度不低于68℃,从而保证一次风空预器低温端金属壁温高于烟气硫酸露点,防止低温酸腐蚀对空预器管的破坏。
实际上因我车间炉内脱硫效率高,烟气中的
为解决一次风道振动过大问题,2#炉暖风器在开工初期就已经被拆除。
◆二次风
二次风经二次风机升压后,分为2路。
其中1路直接从风机出口管路引出为冷二次风、另1路经空预器加热为热二次风。
冷二次风:
冷二次风分为3路。
第1路自二次风机出口风道引一DN300的风管至两台旋风分离器返料斜腿上部,此路冷风又分4个支路、通过4个手动调节风门作为2个返料装置的密封用风;第2路自二次风机出口冷风道引一500×500方形风道至炉膛前墙:
①接8个DN200的支路、通过8个手动调节风门至4根落煤管上的风环和斜管,作为给煤机的输送风和播煤风;②从方形冷风道方形风门前,引1根DN300母线分4个DN150支路、通过4个手动调节风门至4台给煤机,作为给煤机密封冷却风。
热二次风:
热二次风分为3路从3个层面(10807mm、9967mm和8457mm)送入炉膛。
其中2路为上二次风和中二次风,其母管上各设1个自动调节风门。
上二次风和中二次风方型环绕炉膛四周的环管共接27个支管并由27个手动风门控制27个热二次风喷嘴,为炉膛内物料的分段燃烧提供空气,起助燃作用;第3路母管上设自动调节风门和电动风门各1个,至炉前分为4路为4支启动燃烧器配风。
2009年通过改造,从炉膛北墙外启燃专用热二次风方形风道上又引出1支路,通过一个手动矩形风门与原供的冷二次风方形方形风门后风道相接,作为的给煤机的输送风和播煤风。
烟气及携带的固体颗粒离开炉膛,从炉膛后墙的两个旋分入口切向进入旋风分离器,粗颗粒通过离心力从烟气中分离出来,落入旋风分离器下面的U阀后,在固体物料自身重力差的作用下,被U阀底部输入的高压风流化了的高温物料颗粒重新被送入炉膛再次参与燃烧,而烟气携带极细颗粒则通过旋风分离器中心管从顶部引出,进入尾部竖井,从上至下流动,分别经高温过热器、低温过热器、省煤器、空预器后进入布袋除尘器,除去飞灰后,经引风机送入烟囱,排至大气。
◆高压风
U阀采用的是高压流化风。
高压风由2台50%容量的高压流化风机提供,高压流化风机型式为罗茨风机。
风压是由自动调节风门调节并通过旁路将富余的空气送入空预器前的冷一次风管路。
高压风由1根DN65和2根DN80的管路进入返料器底部,流经48个12孔风帽和28个6孔风帽流化旋分捕集下来的高温物料颗粒,在重力差的作用下重返炉膛循环参与燃烧。
在每台返料器的侧面尚有7根DN25的管路连接布置于侧面的风嘴,从侧面斜下吹向返料器内物料。
1.3锅炉主要辅助系统工艺过程简述
1.3.1给焦煤系统
每台CFB锅炉配设4台耐压称重式皮带给煤机,布置于15.7m平台。
炉前墙4点给煤,炉墙给煤口距炉底约1.45m。
布置安装于炉前除氧煤仓间的2台钢质方锥型原煤仓,其几何容积208m3、有效容积166.4m3,1台原煤仓的2个方型出口分别对应2台给煤机。
按比例已经于制煤输煤系统混合好的、符合入炉粒径要求的煤、焦宽筛分颗粒通过给煤机入口的电动插板门落入给煤机皮带,给煤机上的称重传感器实时测量给煤量,变频调速电机会接受锅炉主控器的指令,通过调节皮带机转速控制进入炉膛的燃料总量,皮带给煤机将燃料连续送入炉膛内。
方形冷二次风道上引出一DN300的冷风管,作为4台给煤机的密封冷却风母管,母管分4个DN150支路从给煤机末端底侧部进入给煤机壳体内。
落煤管上设有冷二次风作为播煤风和密封风。
密封风主要是防止微正压炉膛内的高温烟气反窜,舔烧损坏给煤机。
在皮带给煤机出口与落煤口之间设有可在5~7秒内迅速关闭的气动快关门。
一旦锅炉MFT,DCS给4台快关门与4台给煤机同时发出速闭和停运指令,切断锅炉的燃料输入,最大限度地保护人身和机组设备的安全。
给煤机头部壳体上方安装1只电接点温度表,一旦给煤机腔体内温度达到设定值(90℃),给煤机即联锁停运并关闭出口速关门,此联锁为给煤机现场控制柜PLC控制。
1.3.2石灰石粉输送系统
为CFB锅炉配供石灰石的齐胜公司脱硫剂车间将破碎达到设计要求粒度的石灰石粉颗粒,通过气力输送至厂区内每炉1台的400m3石灰石日用钢仓。
石灰石粉输送系统将石灰石粉仓的石灰石粉按照锅炉脱硫所需的粉量连续可调地输送至炉膛。
单套石灰石粉输送系统的最大输送量为9.75t/h。
每台锅炉石灰石粉添加口为8个,前后墙各4个,标高为9457mm。
输送距离约120m,提升高度约8m。
通过仓泵的四个过程:
进料过程、加压过程、输送过程、吹扫过程,最终将石灰石粉输送至炉膛8个给料口。
每台粉仓配1套石灰石粉输送系统。
旋转给料阀出口接DN150管路,通过1个一分二和2个一分四管路分配器,压缩空气携带石灰石粉(CaCO3)通过炉膛前后墙的8个中位二次风口进入炉膛。
石灰石粉进入燃烧区在850~900℃适宜的条件下受热分解成CaO(生石灰)和CO2,CaO与炉膛内的SO2以及O2反应生成CaSO4(石膏)完成炉内脱硫过程,实现清洁燃烧。
石灰石粉添加量是通过烟气在线检测的SO2含量,人工远程控制石灰石旋转给料机(或称星形给料机)转速的高低,改变注料泵旋转给料阀的出料量。
1.33飞灰再循环系统
飞灰再循环系统起自灰库。
飞灰再循环输送系统将再循环飞灰按照锅炉所需的飞灰量连续可调地输送至锅炉。
输送系统的调节范围为锅炉燃用设计煤种带20%负荷再循环飞灰消耗量(0.26t/h)至锅炉BMCR工况下燃用校核煤种飞灰再循环灰量(1.6t/h)。
再循环飞灰灰库的卸料口设置一个手动隔离门和一台注料泵。
注料泵由进料圆顶门,收料泵,给料泵和给料调节出料门构成。
再循环飞灰由注料泵通过变频调速电机调节旋转给料阀刮板速度调节再循环飞灰量,通过压缩空气气力经一个一分二的管路分配器,将再循环飞灰喷吹到锅炉炉膛左右侧墙的2个中位二次风入口。
1.3.4气力输灰系统工艺流程
气力输灰系统是由空气压缩系统、下引式仓泵及管道、控制系统、灰库系统四部分组成,其流程见下图:
正压输送工艺流程分为三个阶段:
进灰阶段流化出灰阶段吹扫阶段,这三个阶段循环往复,将布袋除尘器下的6个灰斗和空气预热器下的2个灰斗里的飞灰通过仓泵输送至灰库。
下引式流态化仓泵的流化喷嘴利用0.3~0.7MPa的压缩空气喷射将灰斗里的烟灰流化而形成高浓度低速度的灰气两相流,仓泵及管道内的压力迅速升至稳态值,达到流化输送状态。
仓泵的运行方式:
同时运行:
串联在一起的一组仓泵同时进灰,同时出灰,同时运行。
交替运行:
同一输灰管上的两组仓泵交替运行。
输灰级别:
一根输灰管上的某组仓泵达到高料位时,此仓泵优先输灰。
灰库系统:
在灰库的库顶安装一台脉冲式布袋除尘器,除尘器的过滤面积为54m2,处理风量为2580~6450m3/min。
1.3.5底渣冷却、输送系统工艺流程
锅炉底渣冷却采用的是章丘圣火科技设计制造的滚筒式冷渣器。
炉膛底部布风板上原设计布置有4个DN150的落渣口(2010年11月,2#炉改造为3个落渣口,与炉前墙4个给煤口错列)。
落渣口靠近前墙,距炉膛前后中心线垂直距离483mm。
每个落渣口接一个总长3109.5mm、内管DN200底渣筛分器,筛分器落渣内管在距落渣口623.4mm和953.4mm两处分别设有5个沿圆周水平均布的Φ4小孔,小孔中心线与落渣管内壁夹角为40°。
高压风通过上、下两层10个小孔向管内斜下吹送,提供底渣流化用风,落入管中较轻的灰渣颗粒被吹回炉膛内继续参与燃烧,而较大颗粒的灰渣向下落入底渣筛分器底部,被选择进入冷渣器入口。
通过调节此处的高压风风压,调整落渣颗粒的大小。
在两层吹灰选渣管之间,设有DN50的空气炮,可在发生渣管堵渣时向管内脉冲喷射空气,疏通落渣管路。
落到筛分器底部的灰渣,经过DOME排渣阀,进入滚筒冷渣器。
冷渣器入口与DOME阀之间设有一非金属膨胀节,用以消除锅炉在垂直方向上冷热膨胀带来的位移,保护固定安装于锅炉零米上的冷渣器。
滚筒冷渣器吸热工质为热电车间专线输送而来的40~50℃的冷除盐水,高温热渣从冷渣器进渣口进入旋转的冷渣器内从上斜下沿着六边形渣道流动,与六边形渣道之间的夹套中流动的冷水进行热量交换传递,完成热渣到冷渣的冷却过程。
正常运行时,冷渣器的输渣排渣量是由变速调节驱动电机控制的,转速的增大和降低,直接影响炉膛内床料的数量,床压亦相应变化:
输送速度增大,则床料量减少、床压降低;反之,则床料量增多,床压升高。
冷却后的灰渣通过冷渣器落渣口首先进入1#埋刮板输渣机;1#埋刮板输渣机共有4个进渣口对应4台冷渣器和1个出渣口。
自北向南最远运送23m后冷渣进入东西走向的2#埋刮板输渣机,运送15m后转入斗式提升机,将渣垂直提升22.5m,最终送入位于两炉炉后中间350m3的钢质渣仓内。
二、汽轮机装置概述
2.1装置概况
1、2#汽轮发电机组为哈尔滨汽轮机厂有限责任公司CC25-8.83/4.12/1.15双抽凝汽式汽轮发电机组,由哈尔滨汽轮机厂有限责任公司汽轮机设备配套检修公司于2006年9月开始安装,1、2#机自2006年10月开始调试。
其额定蒸汽汽压力为8.83MPa,温度535℃。
汽轮机采用切换母管制,给水系统也采用切换母管制,除氧器采用一级高压除氧。
外供4.12MPa蒸汽采用中压抽汽为主,中压减温减压器为辅的系统;外供1.15MPa蒸汽采用低压抽汽为主,低压减温减压器为辅的系统,汽轮机备配高、低压加热系统。
循环水场采用闭式循环,循环水水质处理采用外包式经营。
汽轮机采用喷嘴调节,新蒸汽通过主蒸汽阀后,由四根主汽导管分别引入四个调节汽阀,由调节汽阀控制进入汽缸。
汽缸由高、中、低三部分用垂直法兰连接而成。
中压抽汽、低压抽汽分别用双座阀、低压旋转隔板调节。
转子采用整锻加套装的组合式结构。
套装叶轮通过端面径向键与转子相连,末端采用套装的刚性连轴器与发电机相连。
转子共17级,第1~11级采用整锻结构,第12~17级采用套装结构,其中末三级叶片采用扭叶片。
轴系采用弹性支承,汽轮机一阶临界转速区间为1451~1853rpm。
前轴封及隔板汽封均采用高低齿式汽封(现1#机前轴封改为蜂窝