数控技术基础知识点总结.docx
《数控技术基础知识点总结.docx》由会员分享,可在线阅读,更多相关《数控技术基础知识点总结.docx(8页珍藏版)》请在冰豆网上搜索。
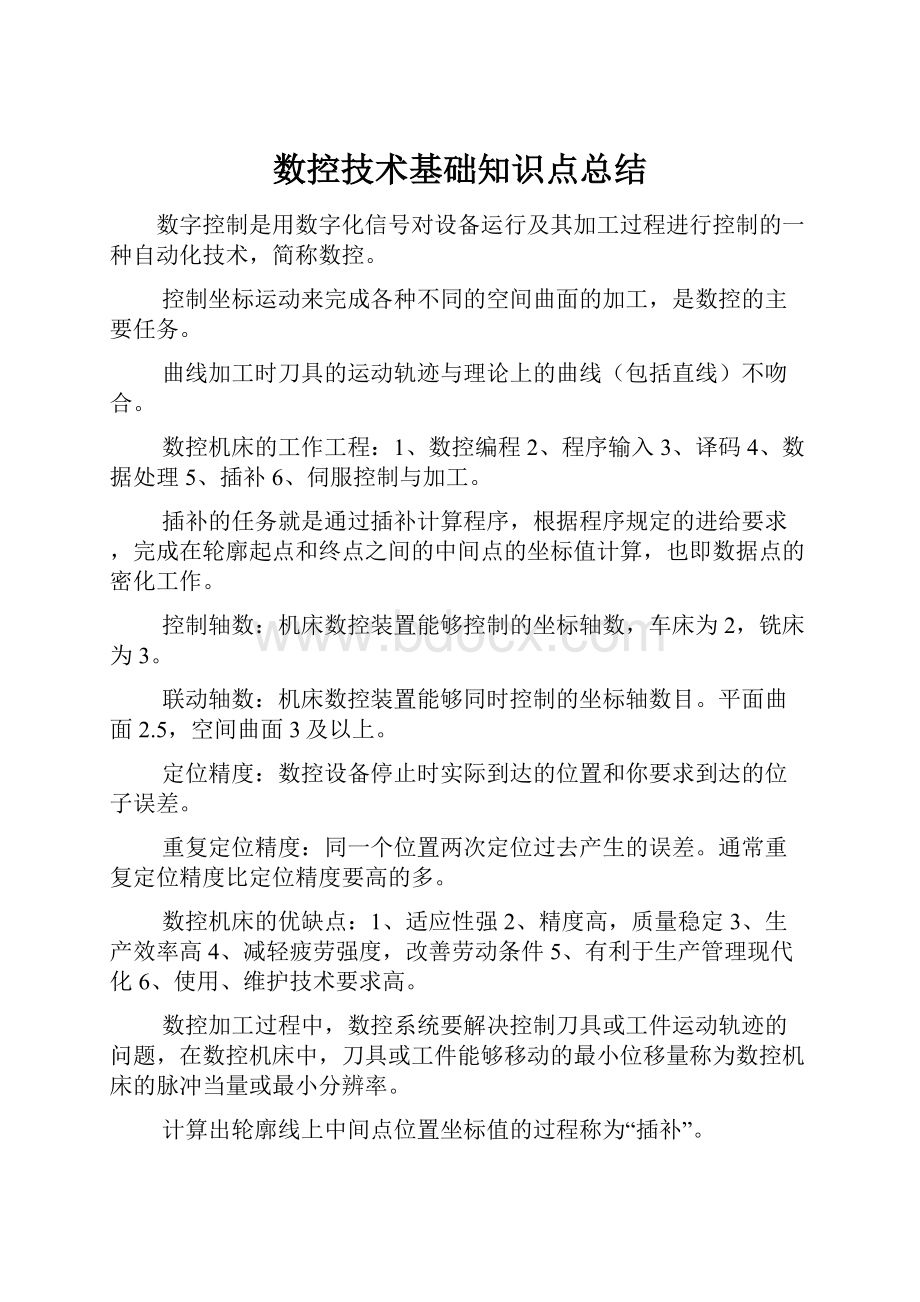
数控技术基础知识点总结
数字控制是用数字化信号对设备运行及其加工过程进行控制的一种自动化技术,简称数控。
控制坐标运动来完成各种不同的空间曲面的加工,是数控的主要任务。
曲线加工时刀具的运动轨迹与理论上的曲线(包括直线)不吻合。
数控机床的工作工程:
1、数控编程2、程序输入3、译码4、数据处理5、插补6、伺服控制与加工。
插补的任务就是通过插补计算程序,根据程序规定的进给要求,完成在轮廓起点和终点之间的中间点的坐标值计算,也即数据点的密化工作。
控制轴数:
机床数控装置能够控制的坐标轴数,车床为2,铣床为3。
联动轴数:
机床数控装置能够同时控制的坐标轴数目。
平面曲面2.5,空间曲面3及以上。
定位精度:
数控设备停止时实际到达的位置和你要求到达的位子误差。
重复定位精度:
同一个位置两次定位过去产生的误差。
通常重复定位精度比定位精度要高的多。
数控机床的优缺点:
1、适应性强2、精度高,质量稳定3、生产效率高4、减轻疲劳强度,改善劳动条件5、有利于生产管理现代化6、使用、维护技术要求高。
数控加工过程中,数控系统要解决控制刀具或工件运动轨迹的问题,在数控机床中,刀具或工件能够移动的最小位移量称为数控机床的脉冲当量或最小分辨率。
计算出轮廓线上中间点位置坐标值的过程称为“插补”。
基准脉冲插补:
每个脉冲使各坐标轴仅产生一个脉冲当量,代表了刀具或工件的最小位移;脉冲的数量代表了刀具或工件移动的位移量;脉冲序列的频率代表了刀具或工件运动的速度。
仅适用于一些由步进电机驱动的中等精度或中等速度要求的开环数控系统。
数据采样插补:
这种插补方法的特点是数控装备产生的不是单个脉冲,而是标准二进制字。
第一步粗插补,采用时间分割思想,把加工一段直线或圆弧的整段时间细分为许多相等的时间间隔,称为插补周期T。
第二步为精插补,一般将粗插补运算称为插补,由软件完成,而精插补可由软件实现,也可由硬件实现。
逼近误差δ与进给速度F、插补周期T的平方成正比,与圆弧半径R成反比。
进给速度F、圆弧半径R一定的条件下,插补周期T越短,逼近误差δ就越小,当δ给定及插补周期T确定之后,可根据圆弧半径R选择进给速度F,以保证逼近误差δ不超过允许值。
弦线逼近:
割线逼近:
当轮廓步长l相等时,内外差分弦的半径误差是内接弦的一半
若令半径误差相等,则内外差分弦的轮廓步长l或角步距是内接弦的√2.
数字积分法又称数字微分分析器法,是利用数字积分的原理,计算刀具沿坐标轴的位移,使刀具沿着所加工的轨迹运动。
积分运算→累加和运算
DDA直线插补的整个过程要经过
次累加才能到达直线的终点。
DDA直线插补的分析可知,判断终点是用累加次数N为条件的,当累加寄存器的位数一旦选定,比如m位,累加次数即为常数
了,而不管加工行程长短都需作N次计算。
这就造成行程长进给速度加快,行程短进给速度变慢,使之各程序段进给速度不均匀,其结果将影响进给表面质量和效率。
为此要进行速度均化处理。
直线插补的进给速度均化:
直线的斜率不变,故对加工没有影响。
均化处理后,行程短的程序段,累加次数N减少得多,则进给速度提高得多;而行程长的程序段,累加次数N减少得少,则进给速度提高得较少。
数控系统的刀具补偿(简称刀补)即垂直于刀具轨迹的位移,用来修正刀具实际半径或直径与其程序规定的值之差。
在轮廓加工过程中,由于刀具总是有一定的半径(如铣刀半径),刀具中心的运动轨迹与工件轮廓是不一致的。
取消刀具补偿时用G40表示;左刀具补偿用G41表示;右刀具补偿用G42表示。
B刀具半径补偿为基本的刀具半径补偿。
轮廓尖角铣成小圆角造成误差,读一段算一段走一段没有预测。
C刀具半径补偿随着前后两段编程轨迹的连接方式不同,相应刀具中心的加工轨迹也会产生不同的转接形式,主要有以下几种:
直线与直线;直线与圆弧;圆弧与圆弧。
根据两段程序轨迹的矢量夹角α和刀具补偿方向的不同,又有伸长型、缩短型和插入型几种转接过渡方式。
区别:
1直线插补时,被积函数寄存器的数值为常用Xe和Ye,而圆弧插补时,被积函数寄存器的数值Xi和Yi
2圆弧插补开始时,X坐标被积函数寄存器存入的是y坐标的初值。
y坐标被积函数寄存器存入的是x坐标的初值
3在圆弧插补过程中,y方向发出的脉冲时,x方向被积函数寄存器内容加“1”,x方向发出的脉冲时,y方向被积函数寄存器内容减“1”
4每当积分函数累加器有溢出时,需要及时修正被积函数寄存器x,y值。
因此被积函数寄存器存入的是瞬时值。
伺服系统是数控装置和机床的联系环节,是数控系统的重要组成。
功能:
接受来自数控装置的指令来控制驱动机床的个运动部件,从而准确控制它们的速度和位置,达到加工出所需工件外形和尺寸。
由伺服电路、伺服驱动装置、机械传动机构及伺服进给运动执行部件组成。
伺服系统与一般机床的进给系统有本质上差别,它能根据指令信号精确地控制执行部件的运动速度与位置。
对伺服系统的基本要求:
1、精度高2、快速响应3、调速范围看4、低速大转矩5、惯量匹配6、过载能力强、负载特性硬。
步进电动机的结构和工作原理
步进电动机的分类及基本结构。
按力矩产生的原理,分为反应式和励磁式。
(1)、反应式步进电动机的转子中无绕组,由定子磁场对转子产生的感应电磁力矩实现步进运动。
(2)、励磁式步进电动机的定子和转子均有励磁绕组,由它们之间的电磁力矩实现步进运动。
有的励磁式电动机转子无励磁绕组,是由永久磁铁制成的,转子有永久磁场。
通常也把这种步进电动机称为混合式步进电动机。
混合式步进电动机具有步距角小、有较高的启动和运行频率、消耗功小、效率高、不通电时有定位转矩、不能自由转动等特点。
步进电动机的工作原理:
错齿角越小,所产生的步距角越小,步进精度越高。
对一相绕组一次通电的操作称为一拍,转一齿所需的拍数为工作拍数。
设步进电动机的转子齿数为N,则它的齿距角为
由于步进电机运行K拍可使转子转动一个齿距角,所以每一拍的步距角
可以表示为:
K——步进电机的工作拍数;
N——转子的齿数。
对于转子有40齿并且采用三拍工作的步进电动机,其步距角为:
步进电动机的工作方式分为单拍、双拍和多拍工作方式。
1、三相步进电动机单三拍工作方式。
2、双三拍工作方式:
每一相都是连续通电两拍,所以励磁电流比单拍要大,所产生的励磁转矩也较大。
由于同时有两相通电,所以转子齿不能和这两相定子齿对齐,而是处于两定子齿的中间位置。
3、六拍工作方式:
在六拍工作方式中,控制电流切换六次,磁场转一周,转子转动一个齿距角,其步距角
检测装置常用类型
(1)增量式:
测量位移的增量值,测量装置输出的是脉冲,一个脉冲是一个测量单位,任何一个对中点都可作为测量始点,实际位移值靠对脉冲计数取得。
(2)绝对式:
测量位移的绝对值,测量装置的输出能够代表移动件当前的实际位置(坐标值)移动的方向靠当前值和历史记忆取得。
增量式充电编码器又能测位移又能测速度。
给步进电机输入一个脉冲信号,其转子转过的角度称为步距角。
步进电机工作原理:
步进电机有A、B、C三相,每相有两个磁极,转子有四个磁极。
当A相绕组通以直流电时,B相磁极产生磁通,这时转子2、4极与定子B相磁极对齐。
如果按A→B→C→A的通电顺序,转子则沿逆时针方向一步步转动起来,每步转过
,这个角度叫步距角。
数数控机床程序编制的方法有三种:
即手工编程、自动编程、和图形编程。
1、人工完成零件图样分析、工艺处理、数值计算、书写程序清单,直到程序的输入和检验,称为“手工编程”。
2、所谓计算机辅助自动编程,就是使用计算机或编程机,完成零件程序编制的过程。
3、图形交互式自动编程是利用被加工零件的二维和三维图形,有专用软件,以窗口和对话框的方式生产的加工程序,这种编程方式使得复杂曲面的加工更为方便。
规定假定工件是永远静止的,而刀具是相对静止的工作而运动。
机床坐标系中X、Y、Z轴的关系用右手直角笛卡尔法则确定,大拇指的指向为X轴的正方向,食指指向为Y轴的正方向,中指指向为Z轴的正方向。
坐标系分为机床坐标系和工件坐标系。
对刀点是指通过对刀确定刀具与工件相对位置的基准点。
对刀点往往就选择在零件的加工原点。
所谓对刀是指使“刀位点”与“对刀点”重合的操作。
“刀位点”是指刀具的定位基准点。
换刀点是为加工中心、数控车床等采用多刀进行加工的机床而设置的,因为这些机床在加工过程要自动换刀。
数控车床的编程特点:
1、根据图纸标注,可按绝对坐标编程,也可按相对坐标编程,也可混合编程;
2、通常在图纸上和测量时均以直径值表示被加工零件的径向尺寸,通常X在绝对方式编程中以直径直表示,在相对方式编程中以实际位移量的二部表示。
3、由于毛坯常用棒料或铸锻件,加工余量较大,数控车床常具备不同形式的循环功能,可进行多次重复循环切削,简化编程。
4、刀具补偿功能,刀具半径和长度补偿。
恒线速度(G96)取消恒线速度(G97)主轴转速限定(G50)
螺纹切削(G33)螺纹切削循环单一(G92)复合螺纹切削循环重复(G76)比例缩放(G51)刀具返回到初始点所在的平面(G98)刀具返回到R点所在的平面(G99)
子程序调用(M98)子程序结束(M99)
非模态调用(G65)模态调用(G66)
坐标旋转(G68)取消选择(G69)
刀具半径补偿的作用:
1可直接按零件的轮廓不考虑刀具半径值
2刀具磨损后只需要手动输入刀具半径值,不必修改程序
3可以使用同一程序,甚至同一刀具加工