CA6140车床手柄座课程设计报告书.docx
《CA6140车床手柄座课程设计报告书.docx》由会员分享,可在线阅读,更多相关《CA6140车床手柄座课程设计报告书.docx(22页珍藏版)》请在冰豆网上搜索。
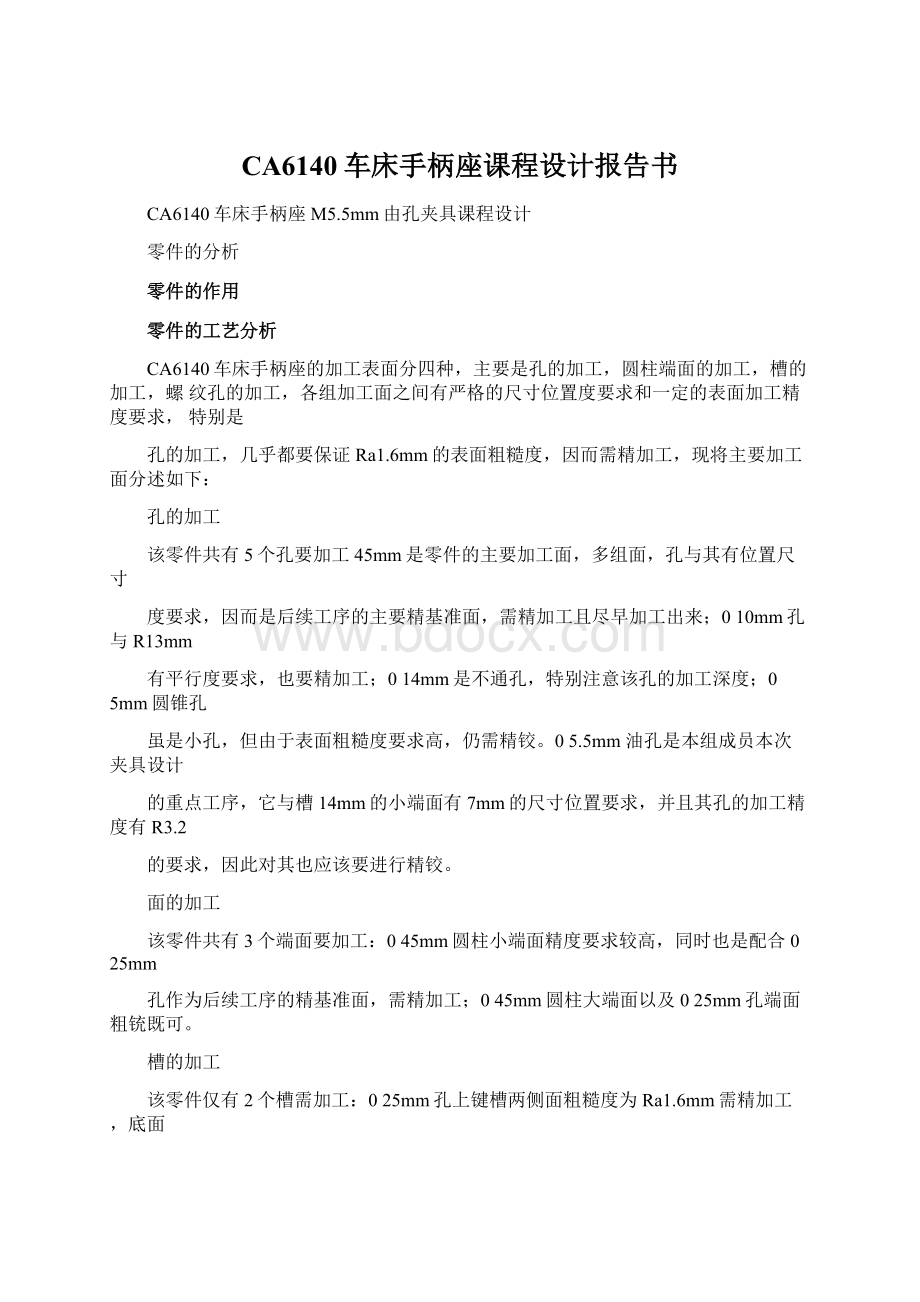
CA6140车床手柄座课程设计报告书
CA6140车床手柄座M5.5mm由孔夹具课程设计
零件的分析
零件的作用
零件的工艺分析
CA6140车床手柄座的加工表面分四种,主要是孔的加工,圆柱端面的加工,槽的加工,螺纹孔的加工,各组加工面之间有严格的尺寸位置度要求和一定的表面加工精度要求,特别是
孔的加工,几乎都要保证Ra1.6mm的表面粗糙度,因而需精加工,现将主要加工面分述如下:
孔的加工
该零件共有5个孔要加工45mm是零件的主要加工面,多组面,孔与其有位置尺寸
度要求,因而是后续工序的主要精基准面,需精加工且尽早加工出来;010mm孔与R13mm
有平行度要求,也要精加工;014mm是不通孔,特别注意该孔的加工深度;05mm圆锥孔
虽是小孔,但由于表面粗糙度要求高,仍需精铰。
05.5mm油孔是本组成员本次夹具设计
的重点工序,它与槽14mm的小端面有7mm的尺寸位置要求,并且其孔的加工精度有R3.2
的要求,因此对其也应该要进行精铰。
面的加工
该零件共有3个端面要加工:
045mm圆柱小端面精度要求较高,同时也是配合025mm
孔作为后续工序的精基准面,需精加工;045mm圆柱大端面以及025mm孔端面粗铳既可。
槽的加工
该零件仅有2个槽需加工:
025mm孔上键槽两侧面粗糙度为Ra1.6mm需精加工,底面
加工精度要求不高,但与R13mn孔上表面有30mm的尺寸要求,而加工键槽时很难以045mm
上表面为定位基准,因而要特别注意尺寸链的推算,保证加工尺寸要求;深槽要注意加工深
度,由于表面粗糙度为Ra6.3mm半精铳即可。
螺纹孔的加工M10mn螺纹孔的加工,它与R13mn孔和025mm孔中心线有30°角度要求,同时中心线与045mm圆柱端面有11mm的尺寸位置要求。
由以上分析可知,该零件的加工应先加工045mm圆柱两端面,再以端面为基准加工作为后
续工序主要精基准的025mm孔,进而以该孔为精基准加工出所有的孔,面,槽,螺纹孔等。
工艺规划设计
毛坯的制造形式
零件材料为HT20Q根据选择毛坯应考虑的因素,该零件体积较小,形状较复杂,外表面采用不去除材料方法获得粗糙度要求,由于零件生产类型为成批,大批生产,而砂型铸造
生产成本低,设备简单,故本零件毛坯采用砂型铸造。
由于零件上孔都较小,且都有严格的表面精度要求,故都不铸出,留待后续机械加工反而经济实用。
基面的选择
基面选择是工艺规划设计中的重要工作之一,基准选择的正确与合理,可以使加工质量
得到保证,生产率得到提高,否则,不但使加工工艺过程中的问题百出,更有甚者,还会造
成零件大批报废,使生产无法正常进行。
粗基准的选择
粗基准选择应为后续加工提供精基准,由于该零件毛坯没有铸孔,故只能以3个主要端
面为基准,由于$45mm小端面表面粗糙度为Ra3.2mn,若直接以大端面为粗基准,恐不能一次达到加工精度,故先以$45mm小端面为粗基准,粗铳$45mm大端面,再以$45mm大
端面为基准,精铳小端面,并保证尺寸43mm
精基准的选择
精基准主要考虑如何保证加工精度和装夹方便,前面已多次提过以$25mm孔为第一
精基准,$45mni圆柱小端面作为基准先加工出$25mm孔,然后作为辅助基准面配合$25mm
孔加工后续工序中的孔,面,槽,螺纹等。
工艺路线的拟定
拟定工艺路线的容除选择定位基准外,还要选择各加工表面的加工方法,安排工序的先
后顺序,确定加工设备,工艺装备等。
工艺路线的拟定要考虑使工件的几何形状精度,尺寸精度及位置精度等技术要求得到合理保证,成批生产还应考虑采用组合机床,专用夹具,工
序集中,以提高效率,还应考虑加工的经济性,以便使生产成本尽量下降。
3.3.4工艺方案的确定
I.粗铳$45mm圆柱大端面,以$45mm圆柱小端面为定位基准
n.半精铳$45mm圆柱小端面,以$45mm大端面为定位基准;
川.扩,铰$25H8mn孔,以$45mm圆柱大端面为定位基准;
IV.钻,扩,铰$10H7mm以$25H8mn孔和$45mm圆柱小端面为基准;
V.粗铳$14mm孔端面,利用$45mni圆柱小端面,$25H8mn孔和$10H7mn孔定位,保
证尺寸43mm;
W.钻,扩,铰$14H7mn孔,定位与V工序相同,保证孔深度25mm;
W.钻,攻MIOmrtB纹孔,定位与V工序相同;
忸.钻,铰$5mm圆锥孔,定位与V工序相同;
IX.插键槽,为便于加工,以$45mni圆柱小端面,$10H7mn孔和$14H7mn孔端面定位,
同时要保证尺寸27.3H11mm;
X.铳槽,定位与V工序相同,保证尺寸30mm;
幻.钻,铰$5.5mm孔,定位与V工序相同;
刘.去锐边,毛刺,尤其注意$25H8mn孔表面可能因为钻M10mmi纹孔以及插槽带来的表面鳞次损伤;
xm.终检,入库。
3.4毛坯尺寸及其加工余量的确定
CA6140车床手柄座零件材料为HT200,毛坯重量约为0.73kg,生产类型为大批生产,采
用砂型铸造生产。
毛坯铸造时可以将$25孔直接铸造出来,由于其余孔均有精度要求,且尺寸小,均不
铸出。
故仅确定三个端面的相关尺寸。
查表确定加工余量:
砂型铸造,材料为灰铸铁,机器造型,公差等级为CT8~12,取CT10,加工余量等级E~G,取G.
切削余量:
查表,基本尺寸小于100mm加工余量为1.4mm;
基本尺寸小于63mm加工余量为0.7mm>
铸件公差等级:
查表,基本尺寸小于100mm取3.2mm;
基本尺寸小于63mm取2.8mm>
341$45mm圆柱两端面毛坯尺寸及加工余量计算
根据工序要求,045mm圆柱两端面经过两道工序,先粗铳$45mm圆柱大端面,再粗,
精铳$45mm圆柱小端面,各步余量如下:
粗铳:
由《机械加工工艺手册第一卷》表3.2-23,其余量值规定,对于小端面(<50mm
为1.0~2.0mm,现取1.8mm表3.2-27粗铳平面的厚度偏差(w30mm为一0.250.39mm现取一0.30mm
精铳:
由《加工工艺手册》表3.2-25,其余量规定值为1.0mm。
故铸造毛坯的基本尺寸为43+1.2+1.8+1.0=47mm。
又根据前面铸件尺寸公差标准
值,取尺寸公差为2.8mmo故:
毛坯的名义尺寸:
43+1.2+1.8+1.0=47mm
毛坯的最小尺寸:
47—1.4=45.6mm;
毛坯的最大尺寸:
47+1.4=49.8mm;
粗铳大端面后的最大尺寸:
43+1.0+1.2=45.2mm;
粗铳大端面后的最小尺寸:
45.2—0.30=44.9mm;
粗铳小端面后的最大尺寸:
:
43+1.0=44mm
粗铳小端面后的最小尺寸:
:
44—0.30=43.7mm
精铳后尺寸与零件尺寸相同,但由于设计零件图纸并未给出具体的公差等级,现按《加
工工艺手册》表5.29,粗铳t精铳所能达到的经济精度取IT8,按入体原则取值。
故精铳后
尺寸为mm
3.4.2中心线端面毛坯尺寸及加工余量计算
根据工序要求,$25H8mn孔中心线距离小端面的毛坯基本尺寸为43+1.2=44.2mm,故:
毛坯的名义尺寸:
43+1.2=44.2mm;
毛坯的最大尺寸:
44.2+1.4=45.6mm;
毛坯的最小尺寸:
44.2—1.4=42.8mmo
由于$25H8mn孔有8精度要求,Ra=1.6mm;
根据《加工工艺手册》表3.2-10,加工该孔的工艺为:
因此查《实用机械加工工艺手册》表3-9得其孔的加工余量为2〜5mm我们取为3mm故:
扩孔24.8mm2Z=1.8mm(Z为单边加工余量);
铰孔25H8mm
毛坯$25mm孔的尺寸为:
25-3=22mm
3.4.3$14H7mm孔端面毛坯尺寸及加工余量计算
根据工序要求,014H7mm孔端面仅由粗铳得到,故$14H7mm孔端面距$25H8mm孔中
心线的毛坯基本尺寸为43+1.2=44.2mm,故:
毛坯的名义尺寸:
43+1.2=44.2mm;
毛坯的最大尺寸:
44.2+1.4=45.6vmm;
毛坯的最小尺寸:
44.2—1.4=42.8mmo
粗铳后尺寸应于零件图尺寸相同,但由于零件图纸并未给出具体的公差等级,现按前面
粗铳平面厚度偏差取—0.28mm故粗铳后的尺寸为
mm
其他毛坯尺寸由于零件图纸未做具体的工序尺寸要求,且对后面诸孔,槽的加工影响不
大,仅荒铳即可,故不再一一赘述分析。
3.5其他尺寸极其加工余量的确定
其他工序尺寸包括5个孔,2个槽,1个螺纹孔的基本尺寸,现仅分析主要的5个孔的
加工余量及尺寸偏差。
5个孔均不铸出,机械加工出来,根据《加工工艺手册》,由于5个孔的表面粗糙度要
求均较高,所以都要经过精铰工序,具体工序尺寸和加工余量为:
(1)$10H7mn孔,Ra=1.6mm;
根据《加工工艺手册》表3.2-9,加工该孔的工艺为:
钻-粗铰-精铰
钻孔:
$9.8mm
粗铰:
$9.96mm
精铰:
$10H7mm
(2)014H7mnfL,Ra=1.6mm;
根据《加工工艺手册》表3.2-9,加工该孔的工艺为:
钻-扩-粗铰-精铰
钻孔:
013.0mm
扩孔:
013.85mm
2Z=0.85mm(Z为单边加工余量)
粗铰:
013.95mm
精铰:
014H7mm
(3)
05mm圆锥孔,
Ra=1.6mm;
由于零件图纸未给出具体的公差等级,现也按H7公差等级加工,按表3.2-9,加工该
孔的工艺为:
钻-精铰
钻孔:
04.8mm
精铰5H7mm
(4)05.5mm孔,Ra=3.2mm
由于也未给出公差等级,现同样按05mm圆锥孔加工方式:
钻-精铰
钻孔:
04.8mm
精铰:
05.5H7mm
3.6确定各工序切削用量及基本工时
3.6.1工序I:
粗铳045mm圆柱大端面
机床:
X51立式铳床
刀具:
高速钢端铳刀,直径D=50mm齿数Z=6
根据《加工工艺手册》表2.4-73,取每齿进给量f=0.15mm/Z,根据《切削
工艺手册》表3.9,取铳削速度Vc=20m/min。
贝Ufr=f*vc=127.4r/min。
按机床选取铳刀转数n=160r/min,则实际切削速度Vc=25.12m/min.,
工作台每分钟进给量F=S*Z*Fz=144mm/min,
铳床工作台进给量f=150mm/min,
按《加工工艺手册》表6.2-5,
基本工时t=0.65min。
3.6.2工序n:
半精铳$45mm圆柱小端面
机床:
X51立式铳床
刀具:
高速钢端铳刀,直径D=50mm齿数Z=6
(1)粗铳$45mm小端面
铳削余量Z=1.2mm
同样查表选取确定f=20m/min,fv=0.15mm/Z,贝UVc=127.4r/min,
同样选取vc=160r/min,贝Uf=25.12m/min.,F=S*Z*Fz=144mm/min,取vc=150mm/min
基本工时t=0.43min。
(2)半精铳$45mm小端面
加工余量Z=1.0mm
查表确定f=20m/min,fv=0.15mm/Z,贝UVc==127.4r/min,
选取Vc=160r/min,贝Uf=25.12m/min.,vc=144mm/min,
取vc=100mm/min,
基本工时t=0.65min。
3.6.3工序川:
扩,铰$25H8mm孔
机床:
Z535立式钻床
(1)扩孔$24.8mm
刀具:
高速钢锥柄标准麻花钻,D=24.8mm
双边余量2Z=1.8mm
由《切削工艺手册》表2.10查的扩孔钻扩孔时进给量f=0.7~0.8mm/r,并由《加工工艺手册》表4.2-16取fz=0.72mm/r,扩孔钻扩孔时,根据《切削工艺手册》表2.15查得f=14m/min,故
f=7~4.7m/min,贝V
按机床选取fr=68r/min,贝Uf=5.29m/min.,
基本工时t=1.1min。
(2)铰$25H8mn孔
刀具:
高速钢锥柄机用铰刀,D=25mm
由《切削工艺手册》表2.24查得f=1.0~1.5mm/r,并由《加工工艺手册》
表4.2-16选取fz=1.22mm/r,取切削深度h=0.15~0.25mm,f=4~8m/min,贝Ufr=51~102r/min,
按机床选取fr=68r/min,贝Uf=5.34m/min.,
基本工时t=0.65min。
3.6.4工序W:
钻,铰$10H7孔
机床:
Z535立式钻床
(1)钻$10mm孔
刀具:
高速钢锥柄麻花钻,D=9.8mm
由《切削工艺手册》表2.7查得fz=0.17mm/r,由表2.15取vc=23m/min,
贝Vfr=747.4r/min
按机床选取n=960r/min,贝Uvc=29.54m/min.,
基本工时t=0.31min。
(2)粗铰$9.96mm孔
刀具:
高速钢锥柄机用铰刀,D=9.96mm
由《切削工艺手册》表2.24查得fz=0.17mm/r,根据表2.15取f=6m/min,
则fr=191.85r/min
按机床选取fr=195r/min,贝Uf=6.1m/min.,
基本工时t=0.19min。
(3)精铰$10H7孔
刀具:
高速钢锥柄机用铰刀,D=10mm
由《切削工艺手册》表2.24查得fz=0.8mm/r,根据表2.15取f=6m/min,
按机床选取fr=195r/min,贝Uf=6.1m/min.,
基本工时t=0.31min。
3.6.5工序V:
粗铳$14mm孔端面
机床:
X51立式铳床
刀具:
高速钢端铳刀,D=30mm,Z=6
根据《加工工艺手册》表2.4-73,取asp=0.15mm/Z,根据《切削工艺手册》
表3.9,取f=20m/min,贝Ufr=212.3r/min
按机床选取fr=220r/min,贝Uf=20.72m/min.,vc=198mm/min,
取vc=150mm/min,
基本工时t=0.33min。
3.6.6工序W:
钻,铰$14H7mm孔
机床:
Z535立式钻床
(1)钻孔$13mm
刀具:
高速钢锥柄麻花钻,D=13mm
由《切削工艺手册》表2.7查得fz=0.36mm/r,由表2.15取f=14m/min,
则fr=343r/min,
按机床选取fr=272r/min,贝Uf=11.10m/min.,
基本工时t=0.36min。
(2)粗铰$13.95mm孔
刀具:
高速钢锥柄机用铰刀,D=13.95mm
由《切削工艺手册》表2.24查得f=0.5~1.0mm/r,并由《加工工艺手册》表4.2-16
取fz=0.81mm/r,=4~8m/min,贝U
fr=91~182r/min,
按机床选取fr=140r/min,贝Uf=6.13m/min.,
基本工时t=0.31min。
(3)精铳$14H7mm孔
刀具:
高速钢锥柄机用铰刀
由《切削工艺手册》表2.24查得f=0.5~1.0mm/r,并由《加工工艺手册》表4.2-16
取=0.62mm/r,
=4~8m/min,贝Vf=91~182r/min,
按机床选取fr=140r/min,贝Uf=6.15m/min.,
基本工时t=0.40min。
3.6.7工序四:
钻,攻M10mr螺纹孔
机床:
Z525立式钻床
(1)钻$8.5mm孔
刀具:
高速钢锥柄麻花钻,D=8.5mm
由《切削工艺手册》表2.7查得fz=0.28mm/r,由表2.15取f=16m/min,
则fr=600r/min,
按机床选取=545r/min,则
=14.55m/min.,
基本工时t=0.10min。
(2)攻螺纹M10mm
刀具:
高速钢锥柄机用丝锥
等于工件螺纹螺距p,即
fz=1.25mm/r,由《切削工艺手册》取f=7.5m/min,贝Ufr=298r/min,
按机床选取fr=272r/min,贝Uf=6.8m/min.,
基本工时t=0.05min。
3.6.8工序忸:
钻,铰$5mm®锥孔
机床:
Z525立式钻床
(1)钻$4.8mm圆锥孔
刀具:
高速钢麻花钻,D=5mm
由《切削工艺手册》表2.7查得fz=O.1Omm/r,由表2.15取f=20m/min,
按机床选取fr=1360r/min,贝Uf=20.5m/min.,
基本工时t=0.096min。
(2)铰$5mm孔
刀具:
高速钢锥柄机用机用铰刀,D=5mm
由《切削工艺手册》表2.24查得fz=0.6mm/r,根据表2.15取f=6m/min,则fr=382.17r/min,
按机床选取fr=392r/min,贝Uf=6.15m/min.,
基本工时t=0.055min。
3.6.9工序X:
铳槽
机床:
X63卧式铳床
刀具:
高速钢圆柱形铳刀,D=13mmZ=6
(1)第一次走刀
根据《加工工艺手册》表2.4-73,取fz=0.2mm/Z,根据《切削工艺手册》
表3.9,
铳削速度vc=15m/min。
贝Ufr=367.5r/min。
按机床选取fr=375r/min,贝Uf=15.31m/min.,vc=56.25mm/min,
基本工时t=0.94min
(1)第二次走刀
切削用量与第一次走刀完全相同,fz=0.2mm/Z,
f=15.31m/min,vc=56.25mm/min
基本工时t=0.94min。
3.6.10工序区
机床:
Z525立式钻床
(1)钻$4.8mm孔
刀具:
高速钢锥柄麻花钻,D=4.8mm
由《切削工艺手册》表2.7查得:
选择4.8mm的高速钢锥柄麻花钻
0.10mm/r
20m/min
1000Vc查1000卫1326(r/min)
按机床选取
4.8
0.6mm/r
四、专用夹具设计
保证加工质量,故
由于生产类型为成批,大批生产,要考虑生产效率,降低劳动强度,需设计专用夹具。
4.1定位方案的确定
4.1.1工序要求
本次设计选择设计的是工序X的夹具,主要是针对钻,铰$5.5mm孔的夹具;,它将用于
Z525立式钻床。
该工序要求05.5mm油孔中心线与14mm槽端面(往小端面走的那个面)有7mnm勺位置
要求,因此可以得出该孔在14mm槽的正中心,并且还要求其孔深刚好钻通到键槽位置为止,
不能钻到025的下一端面。
由于小端面经过精铳,精度比较高,因而工序基准为045mm
小端面,同时为了便于立式钻床加工,零件应倒转180°定位,因而也可以采用025H8mm
和010H7mn两孔为定位基准,保证其加工要求。
夹具设计应首先满足这些要求,在保证较高的生产效率的前提下,还应考虑夹具体制造工艺性和生产经济性。
加工过程中夹具的操作
应方便,定位夹紧稳定可靠,并且夹具体应具有较好的刚性。
4.1.2定位方案设计分析
左图为图2攻
05.5mm油孔工序简图如图2所示,为了加工05.5螺纹孔,必须使其完全定位。
因此初步的设计方案如下,首先必须明确其加工时应如图2所示,这样垂直竖立放置,便于立式钻床加工。
那么要使其完全定位,可以采用:
(1)一面两销定位,以025H8mr和010H7nn两孔为定位基
准就可以满足其要求
⑵一面加圆柱销和半“V’形块定位,以025H8mn为定位
基准,再在R13外圆表面用“V’形块定位。
4.1.2确定最佳
定位方式
如左图所示,比
较以上两个方案,明显第一个要好得多,因©25H8mr和©10H7mr两孔的中心线在同一直线上,所以只要将其两销定在同一平面同一直线上,就可以很快的将其定位(如图垂直放置);而第二个方案和第一个方案不同点在于用的是“V’型快定位,要使零件很快垂直放置定位很
难,并且需要量具对其精确测量,增加了工时。
因此,选择一面两销定位最佳!
如上图所示,一面限制的自由度有3个,一个销钉限制一个自由度,两个一起再
限制一个自由度;为使定位可靠,加工稳定,我所设计的定位方案如附图A1图纸一一手柄座夹具体装配图所示,总共限制了工件的全部6个自由度,属于完全定位。
在该定位方案中,©45mm圆柱小端面被夹具体上的一个支撑面顶住,限制了x轴的移
动,y轴的旋转,z轴的旋转三个移动自由度。
©25H8mm孔插入短销,限制了y轴的移动,z轴的移动,©10H7mm孔中插入削边销,限制了x轴的旋转,这样6个自由度全部被限制。
定位面板如附图A1图纸一一手柄座夹具体装配图所示。
4.1.3定位误差分析
定位误差是指由于定位不准确引起的某一工序的尺寸或位置精度要求方面的加工误差。
对于夹具设计中采用的定位方案,,只要可能产生的定位误差小于工件相应尺寸或位置公差
的1/3—1/2,即可认为定位方案符合加工要求。
对于本次设计的夹具,需要保证的尺寸要求:
保证油孔轴线距©45mm圆柱小端面
17+7=24mm保证螺纹孔轴线与©25H8mn和©10H7mn两孔的中心线成50mm
对于24mm的要求,由于定位基准也是©45mni圆柱小端面,故基准不重和误差为0,且
由于©45mm圆柱小端面经过半精铳,表面粗糙度达到Ra3.2mm故可认为©45mm圆柱小端
面的平面度误差为0,即不存在基准位置度误差,综上所述,只要支撑面的标准尺寸得到保证,是不存在定位误差的。
对于本工序要求,定位基准与工序基准同为两孔中心线,故基准不重合误差为0。
基准
位置误差则取决于两孔直径尺寸公差以及圆度误差,由于两孔的表面精度都达到Ra1.6mm
都经过精铰,故基准位置误差也可以忽略,只要两销的标准尺寸以及相对位置关系得到保证,定位误差也是很小的。
综上所述,该定位方案是符合加工要求的。
4.1.4定位元件的型号,尺寸和安装方式4.141支撑面
在定位板面上做的一个突起4mmt勺一个支撑面,经过精铳得到精度较高的平面。
其相关尺寸见右图:
4.1.4.2短销
本设计方案选用固定式定位销,查《课
GB2205-1999标准,其相关尺寸见下图3:
程设计指导教程》,确定削边销为
图3削边销尺寸
它和定位面板上的$1Omm销孔呈H7/r6mm过盈配合,并用螺母固定,防止钻孔时松动,影响加工。
4.1.4.3圆柱销
本设