铸造知识概述.docx
《铸造知识概述.docx》由会员分享,可在线阅读,更多相关《铸造知识概述.docx(20页珍藏版)》请在冰豆网上搜索。
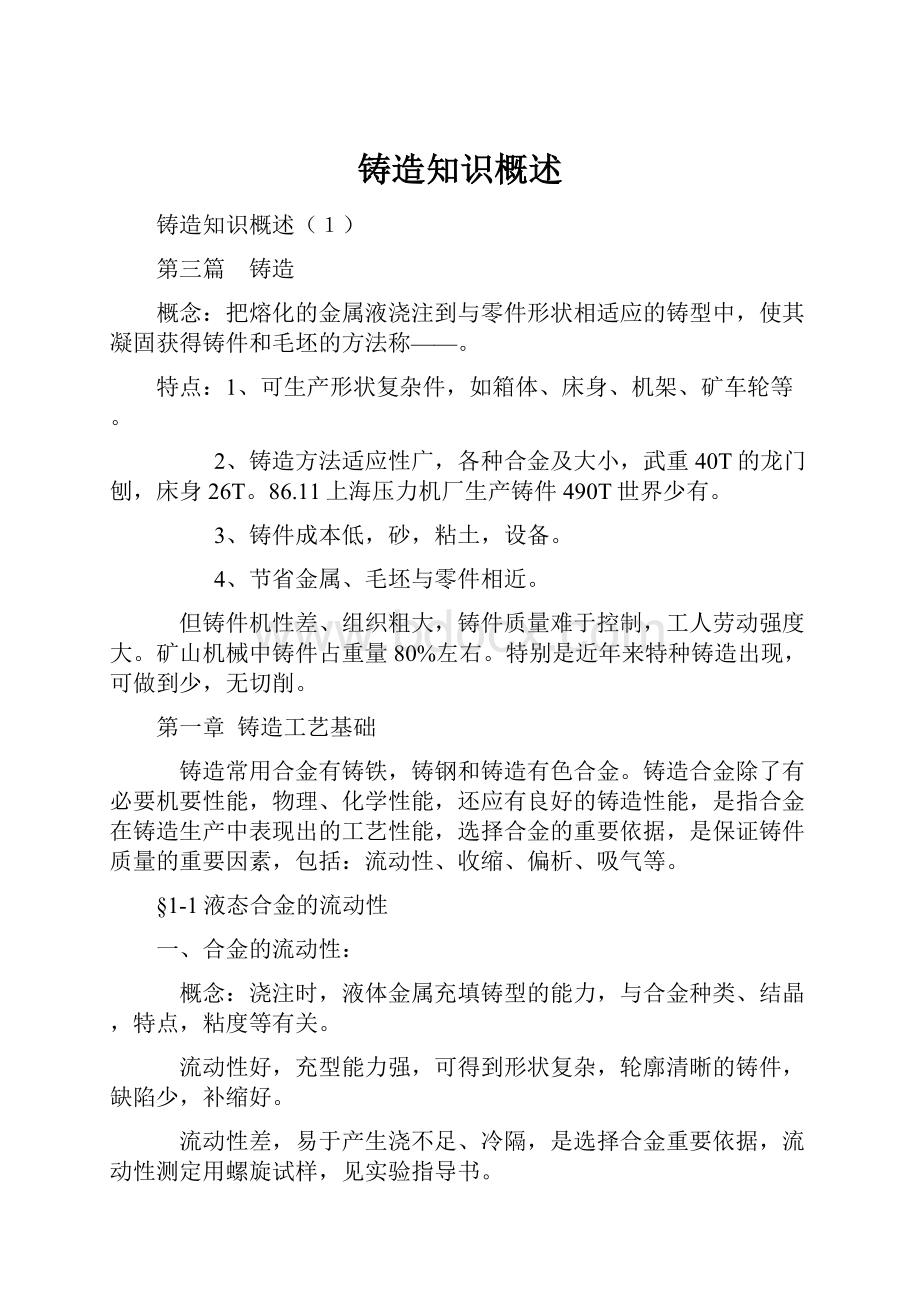
铸造知识概述
铸造知识概述(1)
第三篇 铸造
概念:
把熔化的金属液浇注到与零件形状相适应的铸型中,使其凝固获得铸件和毛坯的方法称——。
特点:
1、可生产形状复杂件,如箱体、床身、机架、矿车轮等。
2、铸造方法适应性广,各种合金及大小,武重40T的龙门刨,床身26T。
86.11上海压力机厂生产铸件490T世界少有。
3、铸件成本低,砂,粘土,设备。
4、节省金属、毛坯与零件相近。
但铸件机性差、组织粗大,铸件质量难于控制,工人劳动强度大。
矿山机械中铸件占重量80%左右。
特别是近年来特种铸造出现,可做到少,无切削。
第一章 铸造工艺基础
铸造常用合金有铸铁,铸钢和铸造有色合金。
铸造合金除了有必要机要性能,物理、化学性能,还应有良好的铸造性能,是指合金在铸造生产中表现出的工艺性能,选择合金的重要依据,是保证铸件质量的重要因素,包括:
流动性、收缩、偏析、吸气等。
§1-1液态合金的流动性
一、合金的流动性:
概念:
浇注时,液体金属充填铸型的能力,与合金种类、结晶,特点,粘度等有关。
流动性好,充型能力强,可得到形状复杂,轮廓清晰的铸件,缺陷少,补缩好。
流动性差,易于产生浇不足、冷隔,是选择合金重要依据,流动性测定用螺旋试样,见实验指导书。
常见合金、黄铜、铸铁最好,铸钢最差。
二、影响合金流动性因素:
影响保持液态时间长短……
1、化学成分:
与合金种类、成分、结晶特点及物理性能有关,结构特点。
见P64图3.1-1。
层状结晶,纯金属、共晶合金流动性好。
见图3.1-2。
P能降低液体粘度和表面张力,提高流动性,明太祖朱元障在南京铸钟……。
2、浇注温度:
T℃高,粘度小,冷却慢,提高流动性
T℃太高,收缩大,吸气严重,氧化严重,粘砂厉害。
3、充型能力:
减小流动阻力,减小冷却速度、均使流动性提高,铸型光滑,流提高,直浇口高,压力大,流动性提高,含水少,透气性好,流动性高,金属型<砂型,干>湿。
§1-2铸造合金的收缩
一、合金的收缩及影响因素:
1、合金的收缩:
合金在凝固和冷却过程中,其体积和尺寸减少的现象。
使铸件产生缩孔,缩松、裂纹、变形、内应力……。
分为三个阶段。
(1)液态收缩:
从浇注温度到开始凝固温度时产生的收缩,产生缩孔原因之一。
(2)凝固收缩:
从凝固开始温度到凝固终了温度的收缩,产生缩孔,缩松的主要原因。
(3)固态收缩:
从凝固终止温度冷却到室温时的收缩,产生应力,变形,裂纹主要原因,P66表3.1-1几种合金收缩率。
2、影响合金收缩的因素:
(1)化学成分:
不同成分收缩不同、钢中碳增加凝固收缩大、固态改缩略小。
铸铁中C增加,G增加收缩小。
硅增加,石墨增加,收缩小,Mn↓。
S↓G↓收缩小。
(2)浇注温度:
T℃提高,收缩大,高温出炉,低温浇注。
(3)铸件结构与铸型:
受阻收缩,芯子阻力,比自由收缩要小。
二、铸件缩孔、缩松的形成及防止:
1、缩孔及缩松的形成
(1)缩孔:
温度降低后,外壳冷却快,形成封闭壳,补充壳凝固、收缩,金属下降一层,又一层形成缩孔。
纯金属和共晶合金属于层状凝固。
(2)缩松:
缩松是分散最后凝固部位细小缩孔,结晶区间宽的合金,先析出枝晶把液体分开,在最后凝固部位形成缩松。
2、缩孔、缩松的防止:
(1)安放冒口补充凝固收缩,使缩孔移出件外,P67,图3.1-66。
冒口还可排气、集渣,ZG件比较大,冒口占件1/3-1/2,铸钢体收缩10-14%。
(2)安放冷铁调整冷速,使铸件同时凝固或顺序凝固,图3.1-6C
§1-3铸造内应力、铸件的变形与裂纹
铸件在凝固后,冷却过程中要产生固态收缩,当受阻时,就会产生内应力,甚至变形与裂纹
一、铸造内应力的形成与控制:
分为热应力与机械应力。
1、热应力、由于铸件厚薄不均,冷速不同,收缩不同(同一时刻)而引起的应力为……。
以铸造应力框来分析热应力形成过程,图3.1-7
(1)当杆Ⅰ、Ⅱ均处于塑性状态时,两杆因冷速不同而收缩不一致,产生内应力被塑变而消除,图3.1-7(a)。
(2)当杆Ⅰ处塑性,杆Ⅱ细处于弹性收缩大,杆Ⅰ受压,处于高塑性状态,发生塑性变形,内应力消失。
图3.1-7(b)。
(3)当Ⅰ、Ⅱ均处于弹性状态:
杆Ⅰ温度较高,杆Ⅱ温度较低,收缩很小,而Ⅰ收缩大,杆Ⅰ收缩受杆Ⅱ阻碍,Ⅰ受拉应力,Ⅱ受压应力,当其强度超过会发生变形和裂纹。
2、机械应力:
铸件固态收缩受阻(铸型、型芯)图3.1-9所示,落砂后会消失,但机械、热应力共同作用会产生熟裂纹。
二、铸件的变形及防止:
壁厚不同收缩时会产生内应力,产生变形,图3.1-10厚受拉应力,薄受压应力。
(1)铸件壁厚要尽量均匀,对称,图3.1-11
(2)尽量同时凝固,加冒口、冷铁。
(3)反变形法。
(4)时效处理、人工时效、自然时效。
三、铸件裂纹及防止:
当内应力超过时,产生裂纹,铸件报废。
(1)热裂:
铸件凝固未期高温下产生裂纹,强度,塑性低,收缩受阻会产生裂纹,特点是裂纹短、缝宽、形状曲折,呈氧化色。
与合金结晶特点、成分有关,合理设计,减少型砂阻力。
(2)冷裂:
低温下形成裂纹,特征是裂纹细小、直线形、无氧化色、减少内应力、脆性增加、↓P含量<0.3%。
第二章 常用铸造合金
常用铸造合金有铸铁、铸钢、铸造有色合金等。
§2-1铸铁件生产
一、概述:
1、铸铁的特点及种类:
是生产中应用最广泛的材料。
铸造性能好,切削加工性好,生产工艺简单,成本低,但塑性差,可焊性差。
常用来制造机架、床身、箱体、曲轴……。
按着碳的存在形态和石墨的形状不同分为:
(1)白口铸铁:
C除极少数溶入铁素体外、其余都以Fe3C形态有在、断口呈银白色、又硬、又脆、不易机加工。
可用来做可铁毛坯,也用于耐磨件,如轧辊、锤头、磨球、犁桦等见P73图3.2-1(a)
(2)灰口铸铁:
碳除微量溶于铁素体,大部全部以片状不石墨形式存在,断口呈灰色。
应用最广泛的铸铁,图3.2-1(b)。
(3)球墨铸铁:
碳大部全部以球状石墨形式存在,用于高性能件,如曲轴……。
(4)可锻铸铁:
碳大中或全部以团絮状石墨形式存在,用于较高强度、韧性件,如后桥等。
二、灰铸铁:
占铸铁总数80%以上,组织由基体+G片
1、灰铸铁化学成分、组织和性能:
(1)灰铁化学成分与组织:
成分:
2.6-3.6%C、1.2-3.0%S、0.4-1.2%Mn、S<0.15%、P<0.3%。
按着基体组织不同分为:
①铁素体灰铁:
F+G粗片大,HB低,切削加工性好,用于要求不高零件。
②铁素体珠光体灰铁:
F+P+G片,较差,铸造性能、切削加工性好,应用较广。
③珠光体灰铁:
P+G细片,、HB高、重要机械零件。
(2)灰铸铁的性能:
钢的基体上嵌入大量G片(孔洞)
①机械性能:
由于G的20mpa,δ、ψ=0,HB=3,相当孔洞,使性能↓,=120-250Mpa,δ、ψ=0,极低,抗压与钢相近。
②工艺性能:
共晶成分,铸造性能好,切削加工性好,不能压力加工,焊接性能差。
③减震性:
大量G片,阻碍震动传播、吸震。
床身、锻锤机座。
④耐磨性:
G干润滑剂,G坑储存油,导轨。
⑤缺口敏感性低:
G存在大量缺口,对外来缺口不敏感了。
2、灰铸铁的孕育处理:
性能决定基体和石墨形态,为了提高性能用碳、硅低的铁水,C=2.7-3.2,Si1=2%,Mn=1%,S<0.12%,p<0.3%,直接浇注白口,麻口。
在铁水包中加入Si-Fe(Si=75%)加入量0.2-0.5%,块度3-10mm,使其得到细小片状石墨,σb、塑性无变化,耐磨性提高特别是厚大截面性能均匀,P75图3.2-2。
常用于齿轮、床身、泵体……。
3、灰铸铁的牌号和应用:
灰铁和性能取决成分和冷却速度,常用机械性能表示,HT200为灰铁,=200Mpa见表3.2-1与老牌号HT20-40相同。
三、球墨铸铁
1、球铁的牌号、组织和性能
QT450-10为球铁,,表3.2–2P76
组织:
铁素体球铁:
F+G球
铁素体珠光体球铁,F+P+G球
珠光体球铁,P+G球
球状石墨对机体割裂作用少,应力集中小,性能大大提高,成本降低,以铁代钢,东风4000,曲轴锻钢一万,球铁三千元。
1、球墨铸铁的生产
(1)化学成分:
3.4-4%C,2-2.6%Si,S<0.07%,P<0.1%。
(2)球化剂与孕育剂:
Mg-稀土合金,脱S,去气,提高铸性,石墨球化,成本低。
加入量1-1.6%。
孕育剂Si-Fe为0.5-1.0%,细化石墨球。
(3)球化处理工艺:
包底冲入法图3.2-3,加入1/3-1/2铁水。
(4)球铁的热处理:
改变基体来提高性能,退火,正火,淬火,回火。
四、可锻铸铁:
成分:
2.4-2.8%C,0.4-1.4%Si,浇注成白口铁,经长时间(40-70h)高温(900℃以上)退火,使Fe3c→Fe+G(团)形成团絮状,耗能大,成本高,重要件,汽车后桥。
KTH300-06墨心可铁(F),。
常见铁素体,珠光体基体,表3.2-3
五、其他铸铁:
1、蠕墨铸铁,介于球铁,灰铁之间……
2、合金铸铁:
耐磨、耐热、耐腐蚀……
§2-2铸钢件生产
一、概述
在煤矿机械中,要求强度高,塑性好,韧性好,常用铸钢件
(1)综合性能高于铸铁,如矿车轮,高压阀门……
(2)焊接性能好,低中碳钢,液压支架
(3)性能稳定,质量较易控制
(4)便于制造具有耐磨,耐蚀,耐热铸件。
二、铸钢的分类、性能和应用:
按着化学成分分为铸造碳钢和铸造合金钢。
1、铸造碳钢:
常分为低碳钢,中碳钢和高碳钢C<0.25%,C=0.25-0.45%,C=0.5-0.6%。
牌号:
ZG200-400,,原牌号ZG15。
见表3.2-4应用。
2、铸造合金钢:
为了提高钢的机械性能,使其具有耐磨、耐热、耐蚀及特殊物理化学性能,加进一些合金元素。
低合金铸钢,Re<3.5%,ZG35Mn
高合金铸钢,Re>10%,ZGMn13,表3.2-4
三、铸钢工艺特点:
1、流动性差,δ>8mm,结晶宽。
2、收缩大:
体10-14%,线1.8~2.5%易于产生缩孔、缩松加冒口补缩。
3、熔点高:
1500℃左右,易氧化粘砂,SiO2>95%
四、铸钢件的热处理:
铸钢件晶粒粗大,过热组织、偏析、残余应力,使机性下降,为此要采用退火和正火。
五、铸钢的熔炼:
常见的有电弧炉炼钢和感应电炉炼钢。
§2-3常用有色合金
1、纯铝:
熔点660℃,d=2.7,导电、导热性好。
常用L1、L2、L3……L8
2、变形铝合金:
①热处理不能强化铝合金,防锈铝合金,表3.2-5
②热处理能强化铝合金,硬铝含金,超硬铝合金、锻铝合金。
3、铸造铝合金
①铝硅合金ZL101……表3.2-6 P84,应用
②铝铜合金ZL201……
③铝镁合金ZL301……
④铝锌合金ZL401……
二、铜合金
1、纯铜:
熔点1083℃,d=8.98/cm3导电、导热、抗腐蚀、塑性高。
常用T1,T2,T3,T4号大,纯度差。
2、黄铜:
Cu+Zn合金
H62,黄铜,Cu=62%,Zn=38%,铆钉,散热片,表3.2-7。
ZH80,铸造黄铜,机性好耐腐蚀,价便宜,用途广。
特殊黄铜HPb59-1,Cu=59,Pb=1,Zn=40。
3、青铜:
除Zn以外铜合金
锡青铜:
QSn6.5-0.1,Sn=6.5,P=0.1,Cu=93.6,表3.2-8。
铝青铜:
ZQAl9-4,铸铝青铜,Al=9%,Fe=4%,Cu=87%。
第三章 特种铸造
砂型铸造有很多优点,适应性广,成本低,应用普遍,但表面光洁度差,工艺复杂,生产率低,劳动条件差,为此常采用金属型铸造,压力铸造,低压铸造,熔模铸造,离心铸造,陶瓷型铸造,挤压铸造,壳型,磁丸,连续,实型铸造。
§3-1金属型铸造
把液体金属浇入到金属制成的铸型里获得铸件……。
1、金属型构造及工艺:
金属型分为水平分型、垂直分型、复合型P88 3.3-1。
铸造工艺特点:
①合适的型温,250-350℃。
②喷刷涂料。
③开型时间、温度合适。
二、金属型特点及应用
1、生产率高、永久型。
2、铸件精度高、余量小,IT14-12,Ra=12.5-6.3
3、机械性能好,Al的σb提高20%
4、成本高、不适于薄件
适用于大批量生产中小有色金属件,活塞、气缸盖,铜瓦……。
§3-2压力铸造
用高压(5~150mpa)高速(5~100m/s)把液态、半液态合金压入金属型中,并在压力下结晶……。
一、压力铸造工艺过程:
在压铸机上完成的,压型是金属型,压铸机按其压室分为冷室、热室,P90,3.3-3,3.3-4。
又可分为卧式、立式,常见有动模、静模、芯子、顶杆……。
(1)合模注入金属
(2)压铸
(3)开型取件
2.压铸的特点及应用:
(1)生产率高80—120件/h,热室400~1000件/h。
(2)精度、质量好,IT13—11,Ra3.2—0.8,薄件、齿轮。
(3)机械性能高,结晶细,。
(4)设备贵,铸件易于气孔、缩孔
适于汽车、飞机、电器的有色合金件。
§3—4熔模铸造
用易熔材料制成蜡模,然后用耐火材料涂挂,硬化后把易熔材料熔失掉,烘干,浇注,获得所需无分型面铸件,例如铸铜主席像。
也称为失蜡铸造。
1909年发明做金牙,保山专利。
二战涡轮发动机,波音飞机。
一、熔模铸造工艺过程:
P93图3.3-6
(1)母模(a)
(2)压型(b)
(3)蜡模压制,组模(c~e)
(4)制壳(f) 4~6次
(5)脱腊(g) 85~95℃水
(6)焙烧 850~900°电阻炉
(7)填砂浇注,清理。
二、熔模铸造特点及应用
(1)铸件精度,光洁度高,IT14-11,Ra12.5—1.6
(2)适于形状复杂,薄壁件,无分型面,1.2mm予热。
(3)适于各种合金,高熔点,难加工。
(4)生产批量不受限制,单件、大批。
(5)工艺复杂周期长,小于25kg件。
§3—5离心铸造
把液态金属浇注入高速旋转(250—1500rpa)铸型中,在离心力作用下,充型和结晶,这种离心铸造。
一、离心铸造的基本方式:
1.立式离心铸造机,P95 3.3-7。
2.卧式离心铸造机。
3.铸造工件离心机 图3.3-8。
二、离心铸造的特点及应用
(1)金属利用率高,省芯、浇注系统,成本低。
(2)结晶致密,气体,夹渣内浮,顺序凝固。
(3)充型能力强,薄件。
(4)适于双金属铸造。
(5)内径尺寸误差大,粗糙,偏析。
适用于铸铁管、气缸套、铜套。
第四章铸造工艺设计
§4-1概述
铸造工艺设计依据铸件的技术要求、结构特点、生产批量及生产条件,确定铸造工艺方案和工艺参数,绘制铸造工艺图,偏制工艺卡等。
工艺设计是生产准备、管理、验收的依据,对保证铸件质量,提高生产率,降低成本有重要意义。
一、铸造工艺设计的依据:
第四章 铸造工艺设计
§4-1 概述
铸造工艺设计依据铸件的技术要求、结构特点、生产批量及生产条件,确定铸造工艺方案和工艺参数,绘制铸造工艺图,偏制工艺卡等。
工艺设计是生产准备、管理、验收的依据,对保证铸件质量,提高生产率,降低成本有重要意义。
一、铸造工艺设计的依据:
1.生产任务和技术要求:
①审查零件图。
②审查零件技术要求。
③生产类型及生产期限。
2.车间生产条件
①设备。
②原材料。
③工人技术水平。
④模具、工装车间能力。
3.设计经济性
二、铸造工艺设计的内容:
1.铸造工艺图,用各种符号在零件上表明铸造工艺方案,如浇注位置,分型面,余量,斜度,收缩率,浇注系统,冒口,冷铁等。
2.铸造工艺卡:
说明造型,造芯,浇注,清理工艺过程及要求文件。
3.合箱图
三、铸造工艺设计的程序
1.审查图纸
2.选择铸造及造型方案
3.确定浇注位置及分型面
4.选用工艺参数
5.设计浇冒口,冷铁
6.设计砂芯
§4-2 铸件结构工艺性
铸件结构设计除了满足使用性能及机械性能外,还要考虑铸造结构工艺性能,将影响铸件质量及成本。
一、铸造工艺对铸件结构的要求:
1.减小分型面,并尽可能为平面,图P10中3.4-1、3.4-2。
2.铸件结构应少用或不用型芯,图3.4-3、3.4-4。
3.铸件结构有利于型芯固定,排气和清理,3.4-5、3.4-6。
3.4-7 空心圆球,工艺孔。
4.铸件形状简单,避免使用活块,3.4-8。
5.铸件上应用结构斜度,3.4-9。
6.铸件的吊装、运输和装夹方便,安全。
二、合金铸造性能对铸件结构的要求:
1.铸件壁厚应合理,δ>最小壁厚,太厚晶粒粗大,组织疏松,易于产生缩孔,不能提高厚度来提高承载能力。
例
抗弯 100% 194% 282%
重量 100% 50% 65%
2.铸件壁厚应尽可能均匀,P103图3.4-10。
3.铸件壁的连接
(1)要用圆角连接,P104 3.4-11、12。
①热量大,②柱状晶杂质集中,③应力集中,④工艺简单
(2)不同壁厚连接,表3.4-2。
(3)避免锐角和交叉连接,图3.4-13 3.4-14。
4.避免铸件收缩受阻,图3.4-15
5.避免过大水平面,图3.4-16水平面金属液上升速变慢。
6.铸件防裂筋的应用,图3.4-17。
三、组合铸件,图3.4-18
§4-3 铸造工艺方案的确定
一、铸型种类及造型方法的选择
铸型:
砂型、金属型、壳型……。
砂型分为湿型、干型、表干型……。
造型方法:
手工造型、机械造型
二、浇注位置的选择:
浇注时铸件在铸型中所处位置。
1.重要面质量要求高面朝下或放于侧面,图3.4-19、3.4-20。
2.铸件的大平面应放在下部,图3.4-21。
3.薄部位置于下部或倾斜、垂直放置,图3.4-22。
4.减少型芯,便于安放、稳固、排气,图3.4-23。
5.易于产生缩孔,厚大部位置于上部、侧面,便于安放冒口,图3.4-24。
三、分型面选择;为取出模型,砂箱间的分界面
1.尽量减少分型面的数目,简化工艺↓成本,图3.4-25。
2.分型面要尽量平直,图3.4-26。
3.尽量使铸件全部或大部置于同一半型中,图3.4-27、图3.4-28。
4.分型面便于下芯、合箱及检查型腔尺寸,图3.4-29。
5.分型面选在最大截面
§4-4 铸造工艺参数选择
工艺方案确定后,还要确定工艺参数
一、机械加工余量:
为进行机加工而放大的尺寸,依合金种类,尺寸生产批量,复杂程度,加工面位置。
P110图3.4-3。
二、收缩率:
由于合金的收缩,使体积减少,要放大收缩量的这个尺寸,工厂称缩尺,合金种类,尺寸,结构而定,HT0.7~1.0%、ZG1.5~20%、有色1.5~1%。
三、拔模斜度:
为了便于取出模型,在垂直于分型面的表面制造模型时留出一定斜度,图3.4-30,砂型15′~3°,内3°~15°。
四、最小铸出孔和槽:
是否要铸出看工艺要求。
灰铁单件φ30~50,成批φ15~30,大量φ12~15mm
五、铸造圆角,相交壁圆角过渡
§4-5 型芯、浇注系统和冒口设计
一、型芯设计:
形成铸件内,腔孔及复杂表面,减少分型面和活块数目。
1.型芯分块:
大尺寸,复杂芯减少芯,图3.4-31、图3.4-32。
2.芯头设计:
作用定位,固定,排气,清砂。
分为水平芯头、垂直芯头,图3.4-33
二、浇注系统设计
1.组成:
由浇口杯、直浇道、横浇道、内浇道。
2.类型:
封闭式、开放式、半封闭式。
F直>F横>F内,F直F横顶浇式、底注式、中间注入式,图3.4-34。
3.尺寸的确定
三、冒口和冷铁设计
1.冒口作用及种类:
作用补缩,调速冷速,排气,集渣。
种类有顶冒口,边冒口,明冒口,大气压力冒口,发热冒口。
P114图3.4–35。
2.冒口设置及计算
3.冷铁:
作用,减少冒口,改善金相组织,控制凝固顺序,增加冒口补缩距离,常见冷铁类型,图3.4-36。
§4-6典型件铸造工艺设计举例
一、铸造工艺图表示方法,P17 表3.4-5。
二、典型件举例图3.4-37、3.4-38、3.4-39。
1.生产任务和技术要求:
①审查零件图。
②审查零件技术要求。
③生产类型及生产期限。
2.车间生产条件
①设备。
②原材料。
③工人技术水平。
④模具、工装车间能力。
3.设计经济性
二、铸造工艺设计的内容:
1.铸造工艺图,用各种符号在零件上表明铸造工艺方案,如浇注位置,分型面,余量,斜度,收缩率,浇注系统,冒口,冷铁等。
2.铸造工艺卡:
说明造型,造芯,浇注,清理工艺过程及要求文件。
3.合箱图
三、铸造工艺设计的程序
1.审查图纸
2.选择铸造及造型方案
3.确定浇注位置及分型面
4.选用工艺参数
5.设计浇冒口,冷铁
6.设计砂芯
§4-2 铸件结构工艺性
铸件结构设计除了满足使用性能及机械性能外,还要考虑铸造结构工艺性能,将影响铸件质量及成本。
一、铸造工艺对铸件结构的要求:
1.减小分型面,并尽可能为平面,图P10中3.4-1、3.4-2。
2.铸件结构应少用或不用型芯,图3.4-3、3.4-4。
3.铸件结构有利于型芯固定,排气和清理,3.4-5、3.4-6。
3.4-7 空心圆球,工艺孔。
4.铸件形状简单,避免使用活块,3.4-8。
5.铸件上应用结构斜度,3.4-9。
6.铸件的吊装、运输和装夹方便,安全。
二、合金铸造性能对铸件结构的要求:
1.铸件壁厚应合理,δ>最小壁厚,太厚晶粒粗大,组织疏松,易于产生缩孔,不能提高厚度来提高承载能力。
例
抗弯 100% 194% 282%
重量 100% 50% 65%
2.铸件壁厚应尽可能均匀,P103图3.4-10。
3.铸件壁的连接
(1)要用圆角连接,P104 3.4-11、12。
①热量大,②柱状晶杂质集中,③应力集中,④工艺简单
(2)不同壁厚连接,表3.4-2。
(3)避免锐角和交叉连接,图3.4-13 3.4-14。
4.避免铸件收缩受阻,图3.4-15
5.避免过大水平面,图3.4-16水平面金属液上升速变慢。
6.铸件防裂筋的应用,图3.4-17。
三、组合铸件,图3.4-18
§4-3 铸造工艺方案的确定
一、铸型种类及造型方法的选择
铸型:
砂型、金属型、壳型……。
砂型分为湿型、干型、表干型……。
造型方法:
手工造型、机械造型
二、浇注位置的选择:
浇注时铸件在铸型中所处位置。
1.重要面质量要求高面朝下或放于侧面,图3.4-19、3.4-20。