火电厂集控运行专业论文.docx
《火电厂集控运行专业论文.docx》由会员分享,可在线阅读,更多相关《火电厂集控运行专业论文.docx(19页珍藏版)》请在冰豆网上搜索。
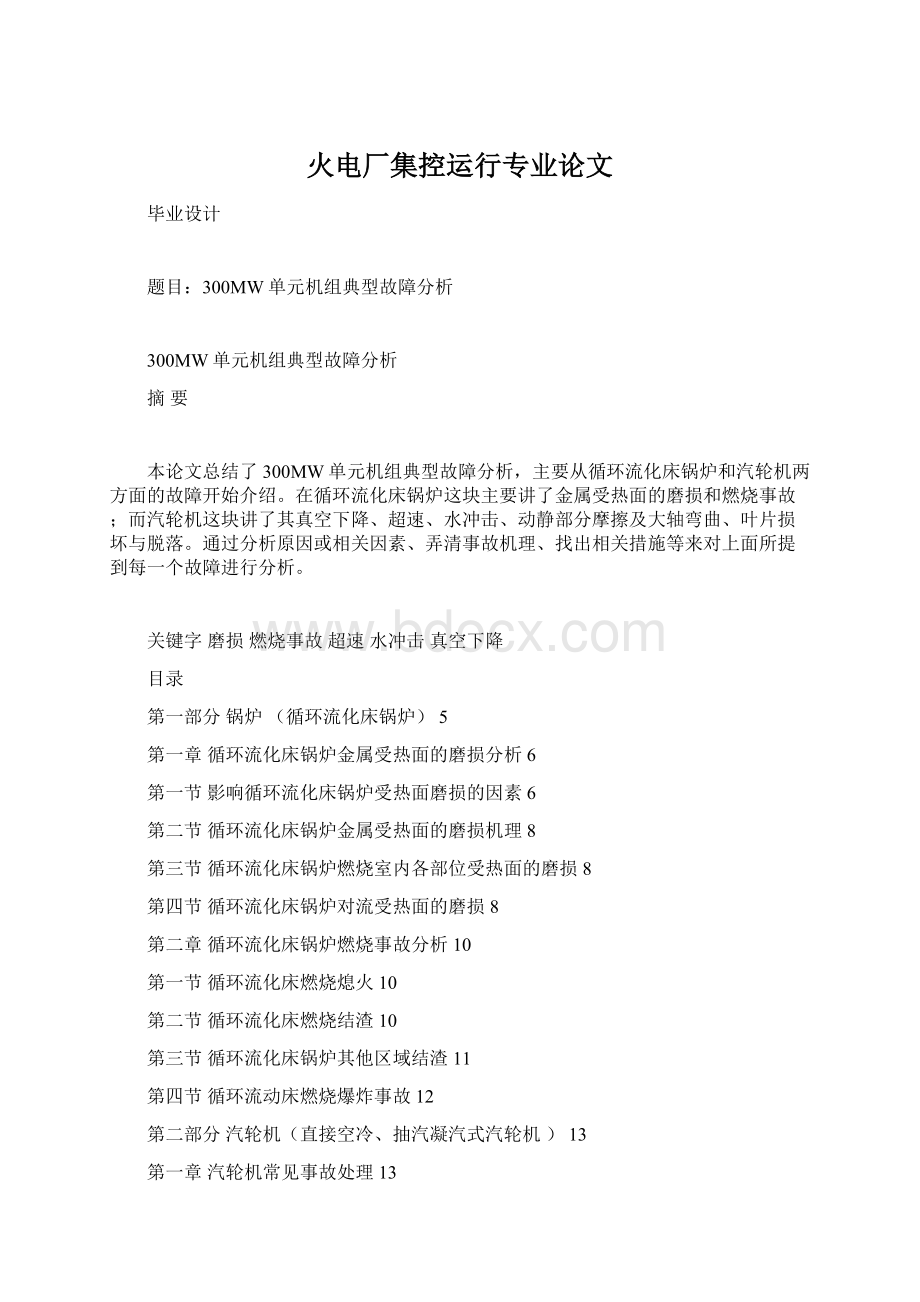
火电厂集控运行专业论文
毕业设计
题目:
300MW单元机组典型故障分析
300MW单元机组典型故障分析
摘要
本论文总结了300MW单元机组典型故障分析,主要从循环流化床锅炉和汽轮机两方面的故障开始介绍。
在循环流化床锅炉这块主要讲了金属受热面的磨损和燃烧事故;而汽轮机这块讲了其真空下降、超速、水冲击、动静部分摩擦及大轴弯曲、叶片损坏与脱落。
通过分析原因或相关因素、弄清事故机理、找出相关措施等来对上面所提到每一个故障进行分析。
关键字磨损燃烧事故超速水冲击真空下降
目录
第一部分锅炉(循环流化床锅炉)5
第一章循环流化床锅炉金属受热面的磨损分析6
第一节影响循环流化床锅炉受热面磨损的因素6
第二节循环流化床锅炉金属受热面的磨损机理8
第三节循环流化床锅炉燃烧室内各部位受热面的磨损8
第四节循环流化床锅炉对流受热面的磨损8
第二章循环流化床锅炉燃烧事故分析10
第一节循环流化床燃烧熄火10
第二节循环流化床燃烧结渣10
第三节循环流化床锅炉其他区域结渣11
第四节循环流动床燃烧爆炸事故12
第二部分汽轮机(直接空冷、抽汽凝汽式汽轮机)13
第一章汽轮机常见事故处理13
第一节汽轮机真空下降13
第二节汽轮机超速14
第三节汽轮机水冲击15
第四节汽轮机动静部分摩擦及大轴弯曲16
第五节汽轮机叶片损坏与脱落17
参考文献19
第一部分锅炉(循环流化床锅炉)
第一章循环流化床锅炉金属受热面的磨损分析
本章主要总结了循环流化床锅炉受热面磨损的因素、金属受热面的磨损机理、燃烧室内各部位受热面的磨损、对流受热面的磨损。
那么什么是磨损呢?
当两个物体接触并有相对运动时,由于力的作用或动量的转移,接触物体产生材料损耗的现象叫磨损。
两种物质接触,由于电化学作用而产生材料的腐蚀称之为材料的腐蚀损耗。
为了说明磨损和腐蚀的程度,工程上一般使用两个特征量来描述。
(1)磨损量。
表示经过一段时间之后磨损的绝对变化。
(2)磨损率。
表示磨损的速率,如锅炉水冷壁管的磨损、腐蚀速率为1mm/1000h。
第一节影响循环流化床锅炉受热面磨损的因素
一、影响循环流化床锅炉受热面磨损的关系式
EunpdpKCτ/2g(1-1)
式中E——磨损量
up——烟气中固体粒子的速度
dp——固体粒子直径
C——烟气中固体粒子的浓度
K——比例常数,表示物料和气体的磨损特性
τ——运行时间;
g——重力加速度。
1,粒子速度的影响
从式(1-1)中看出,磨损量与粒子速度的n次方呈正比。
n值的大小与固体粒子直径、速度有关。
固体粒子速度大约以3次方的关系影响循环流化床锅炉金属受热面的磨损。
与式(1-1)
中其他影响因素相比,粒子的速度是影响受热面磨损的决定性的、最重要的因素,循环流化床锅炉中各部分受热面的磨损原因多数是由于粒子速度太高。
n值与床料粒子的直径有关。
当床料粒径50~200μm时,床料粒子直径越大,n值越小,n值在3.78~3.15之间变化。
当床料粒子速度在8~40m/s之间变化时,n值在3.0~4.3之间变化。
也就是说固体粒子速度增加,n值变大。
不同的循环流化床锅炉炉型,流化速度是有区别的,因此不同的循环流化床锅炉炉型的防磨性能是不同的;同一台流化床锅炉
不同部位的气流速度是不同的,那么不同部位的金属受热面的抗磨蚀性能性能是有区别的。
锅炉的设计决定了流化床锅炉各部位的气流速度,从而决定了锅炉受热面金属的防磨性能。
2.粒子浓度的影响
由式(1-1)知,金属受热面的磨损量与粒子浓度呈正比。
在燃烧室内,粒子浓度与飞灰循环倍率有关,循环倍率高,燃烧室内床料浓度高,粒子对燃烧受热面磨损严重。
对流受热面的磨损与分离器布置的位置有关,与分离器分离效率有关。
如果分离器布置在燃烧室出口,后部对流受热面因粒子浓度小而磨损轻;如果分离器布置在对流受热面之间的某一个位置,如布置在水平烟道和尾部竖井烟道之间的换热室,则水平烟道内过热器受热面区的粒子浓度高,磨损较严重。
这就要求过热器区的烟气流速取低一些。
分离器的分离效率低,则布置在分离器之后的受热面区的粒子浓度高一些。
为了受热面磨损,其其流速宜取低一些。
当然,烟气流中的粒子浓度也燃煤中的灰分有关,灰分高,烟气流中的粒子浓度高,带来的磨损大。
3.粒子直径的影响
从式(1-1)中知,受热面的磨损量与床料粒子直径成正比。
随着床料粒径的增大,磨损量增加。
但当床料粒径加大到某一临界值后,受热面的磨损量随着床料直径的增加的变化十分缓慢,如图(1-1)所示。
4.床料颗粒密度,灰的成分和床料形状对受热面磨损的影响
一般来说,颗粒的密度越大,粒子撞击受热面的动量越大,磨损量越大。
粒子形状带棱角的多,尽收受热面的磨损量大。
灰渣化学成分中铝、硅含量高,对受热面磨损严重,钙的含量高,磨损交情。
对一定的床料有一定的K值。
K值通过实验确定。
图(1-1)冲蚀磨损时磨损量与颗粒直径的关系
二、床料温度对受热面磨损的影响
床料温度一般比床温高100~200℃,达到900~1150℃。
在这个范围内,床料粒子的硬度不会发生很大的变化。
因此,床料粒子温度的变化不会对金属受热面的磨损带来很大的变化。
但是,床料温度的变化将使金属受热面外表面温度变化,从而对金属表面产生不同的氧化反应,生成不同的化学生成物。
不同的化学生成物的硬度是不同,也就是说,其抗磨性能是不同的。
管壁温度在130~400℃之间,烟气中的过剩氧与金属壁发生氧化反应,生成a-Fe2O3的氧化膜。
而Fe2O3氧化膜的年硬度比远管材的硬度要大得多(Fe2O3的硬度为11450MPa,管材的硬度为1400MPa)。
在管壁温度大于300℃以后,氧与铁反应生成氧化膜有三层,第一层为a-Fe2O3,第二层为r-Fe2O3,第三层为Fe2O3。
这些氧化膜的硬度都比原管材`的硬度要大得多。
受热面壁温对磨损的影响如下图(1-2)所示。
当壁温为80℃时,由于氧化膜的生成,磨损速率开始急剧下降。
当壁温超过400图(1-2)受热面温度对磨损的影响℃之后,由于热应力的产生以及高温腐蚀的影响,磨损速率有所增加。
三、床料硬度对金属受热面的磨损
床料由燃煤的成分组成。
烧多灰分的煤、劣质煤、洗干形成的床料,其硬度和粒度均比较大,度受热面的磨损较严重。
燃烧优质燃料形成的床料,其硬度和粒径均比较小,对受热面的磨损较轻。
如图(1—3)所示,当床料硬度接图(1-3)颗粒硬度对磨损的影响近金属受热面硬度时,磨损率变化十分剧烈;当床料硬度比金属受热面硬度小许多或大许多时,磨损速率变化较小。
20号锅炉钢管的硬度为1400Mpa。
四、受热面材料硬度对磨损的影响
受热面的磨损不仅与床料硬度Hp有关,而且与受热面本身的硬度Hm于Hp之间的比值有关。
当Hm|Hp在1附近,磨损较严重;当Hm|Hp远小于或远大于1时,磨损较轻。
五、管束结构和布置间距对磨损的影响
金属受热面对流管束有顺排和错排布置两种形式。
一般来说,错排管束的磨损比顺排管束的严重。
管束排列的结构参数横向节距S1对管束的磨损性能有较大影响。
横向节距S1增大,能降低管束下部第一、二排管的磨损;纵向节距S2的变化一般对管束的磨损影响不打。
第二节循环流化床锅炉金属受热面的磨损机理
一、冲击磨损
当气固两相流中固体粒子沿垂直方向冲击受热面的管子时,使管子表面出现塑性变形或产生显微裂纹。
经过固体粒子的反复冲击,变形层脱落,导致严重磨损。
固体粒子的反复冲击使管子表面产生疲劳磨损破坏,导致爆管。
二、切削磨损
当气固两相流中固体粒子以一定的速度冲刷受热面时,特别是平行、高速冲刷时,对管子表面产生一种刨削作用,导致管壁磨损而爆管。
三、接触疲劳磨损
当气固两相在流动过程中遇到金属受热面管子阻挡时,在管子背风面形成涡流,导致固体粒子涡流对管子背风面的磨损,叫接触疲劳磨损。
四、综合磨损
当气固两相流中固体粒子以一定的角度反复冲刷管子受热面时,对受热面表面同时有冲击磨损、切削磨损、接触疲劳磨损,这种磨损叫综合磨损,如循环流化床锅炉燃烧室内耐火防磨材料与膜式壁的交界台阶处的管子磨损就属于综合磨损。
第三节循环流化床锅炉燃烧室内各部位受热面的磨损
循环流化床锅炉燃烧室内各部位受热面的磨损包括以下几个方面:
a.燃烧室下部耐火防磨层与膜式壁交界处以上一段管壁的磨损。
b.燃烧室上部膜式水冷壁的磨损。
c.燃烧室四角膜式水冷壁的磨损。
d.门孔让管引起的磨损。
e.燃烧室附加受热面的磨损。
f.二次风布置不当引起的磨损。
g.管壁上焊接引起的磨损。
h.燃烧室内热电偶一起的磨损。
i.燃烧室内埋管受热面的磨损。
第四节循环流化床锅炉对流受热面的磨损
循环流化床锅炉对流受热面的磨损主要指过热器和省煤器金属受热面的磨损。
一、影响循环流化床锅炉对流受热面的磨损因素分析
1.分离器的布置位置
分离器的布置位置对对流受热面的磨损影响很大。
循环流化床锅炉有两类,一类是分离器布置在燃烧室的出口,对流受热面布置在气流中粉尘浓度较低的分离器之后;另一类是分离器布置在过热器受热面之后,省煤器之前,如中温下排气旋风分离器循环流化床锅炉,此时,过热器区眼气流中的粉尘浓度较高,而磨损与烟气中粉尘浓度成正比。
2.分离器的分离效率
分离器分离效率越高,分离器后面区域中的粉尘浓度越低、粒度越小。
而磨损是与粉尘浓度和粒度密切相关的:
粉尘浓度大、粒度大,磨损严重;反之则磨损轻。
3.煤的成灰的特性
煤在燃烧过程中的成灰特性决定了循环流化床锅炉床料的特性————粒度的大小、粉尘浓度大小和硬度数值。
对流金属受热面的磨损是与粉尘浓度、粒度、硬度成正比的。
4.气流速度
气流速度是影响对流金属受热面磨损最重要的、决定性的因素。
气流速度高,磨损急剧加快;气流速度过低,发生受热面积灰。
对流受热面区气流速度的正确选择,使之即不产生积灰,有不发生磨损,对循环流化床锅炉的安全、经济运行及其重要的。
二、高低温过热器的防磨措施
1.烟气流速的正确选定。
对流金属受热面的磨损与气流速度的3~4次方成正比。
因此,为了减轻磨损,正确选定气流速度是至关重要的。
对布置在分离器前面的高低温过热器,气流速度一般取6~7m/s,烧灰分高的煤取低值,烧灰分低的煤取高值。
对布置在分离器后面的高低温过热器,气流速度一般取8~10m/s,同样,烧灰分低的煤取高值,烧灰分高的煤取低值。
2.在高低温过热器前面第1~3排的过热器管的迎风面加防磨罩。
3.为了消除烟气走廊的磨损作用,在过热器下部弯头加防磨罩。
4.低温过热器的后部第1~3排管子的背风面由于气流的漩涡作用产生磨损。
对此局部磨损采用防磨罩解决。
二、省煤器的磨损因素及防磨措施
1.影响省煤器磨损的因素
包括气流的速度、分离器布置的位置、分离器的收集效率、煤的成灰特性和省煤器的形式。
2.省煤器的防磨措施
(1)省煤器区气流速度的选择。
省煤器金属受热面的磨损与气流速度的3~4次方成正比。
对分离器的布置在省煤器前面的下排气旋风分离器循环流化床锅炉和分离器布置在省煤器之间的二级分离器循环流化床锅炉,考虑到粒子浓度的变化,对气流速度的选择有所不同。
对下排气分离器循环流化床锅炉,省煤器区的气流中粒子浓度较低,但考虑到排气的残余漩转,气流速度一般选定5.5~6.5m/s。
对二级分离器循环流化床锅炉,分离器布置在二级省煤器之间,省煤器区的气流速度宜取上述数值中的低值;对高温上排气旋风分离器布置在燃烧室出口的循环流化床锅炉,省煤器区气流中的粒子浓度较低,气流速度可取高些,一般选择8~10m/s。
大于10m/s之后,对省煤器磨损还是较严重的。
对烧高灰分煤的循环流化床锅炉,设计省煤器区的烟气流速取低值,反之取高值。
(2)消除省煤器区的烟气走廊。
省煤器蛇形管弯头与烟道之间的间隙形成了烟气走廊,对省煤器弯头部产生了严重磨损。
消除烟气走廊方法有二;一在烟气走廊中加隔板,将省煤器弯头部伸入墙内
(3)省煤器上几排管的防磨。
由于粒子动量的影响,省煤器的磨损多发生在上面几排管子的迎风面。
对这种局部磨损,可采用护瓦来防止,也可在省煤器前加2~3排假省煤器管来阻挡磨损,定期更换即可。
(4)省煤器消旋均流板。
对下排气旋风分离器循环流化床锅炉,由于排气管中的气流残余旋转,粒子受离心力的作用,对省煤器上面第1~2排管子的迎风面产生局部磨损。
在省煤器之上放置一个多孔消旋均流板,可较好保护省煤器。
定期检查和更换多孔消旋均流板,即可控制省煤器的磨损。
3.省煤器的形式对磨损的影响
(1)光管省煤器与膜式省煤器相比,光管省煤器磨损严重。
(2)顺排管省煤器与错排管省煤器相比,后者磨损严重。
在省煤器的设计中正确选定气流速度,结构上采取局部的防磨措施,运行中注意不要大风量运行,省煤器的磨损完全能实现磨损的可控运行。
第二章循环流化床锅炉燃烧事故分析
本章将总结循环流化床锅炉最常发生的一些燃烧事故并提出预防和处理措施。
循环流化床锅炉常发生的燃烧事故包括;
1.燃烧熄火
2.床料结渣
3.返料系统(返料器、料腿、返料管)结渣
4.燃烧爆炸事故
第一节循环流化床燃烧熄火
1.断煤是引起循环流化床燃烧熄火的主要原因
2.造成断煤主要原因是煤的水分大于8%,煤在煤仓内搭桥、堵塞、不下煤,而运行人没有发现,未能及时消除。
预防措施;设计较大的干煤棚,控制煤的水分低于8%;加强给煤监视,设计断煤警报器或语言提醒是防止断煤的有效措施。
3.锅炉负荷大幅度变化时,及时调整给煤量,防止高温结渣及低温熄火
一般,当锅炉负荷变大时,要加风、加煤;相反,当锅炉负荷变小的时候,要减风、减煤;如果运行人员没有这样做,在负荷变大的情况下,会造成燃烧室温度不断下降,最终导致熄火。
在负荷变化小的时候,会造成燃烧室温度不断升高,最终导致高温结渣而停炉。
4.返料投入运行时控制不当,造成压灭火事故
对中小容量的循环流化床锅炉,投入返料不当,也可能将燃烧室火压灭。
有的运行人员喜欢在锅炉运行一段时间之后投入返料量,造成大量返料进入燃烧室,将燃烧压灭。
5.煤的发热量发生很大的改变时,调整给煤量,防止低温熄火和高温结渣
一般当燃烧热值变低时,必须加大给煤量。
当燃烧值变高时,减少煤量。
如果不及时调整,在煤热值变低的时候,会发生燃烧室温度越来越低,最终导致熄火。
在煤热值变高的时候,会发生燃烧室温度越来越高,最终导致高温结渣而被迫停炉。
6.排床底渣失控,造成流化床熄火
如果出现拍底渣失控,床料量排除太多,使床料量太少,床层厚度太薄,不能维持一个稳定的燃烧温度,会发生燃烧灭火。
相反,如果底渣不能顺畅排除,造成床料越来越多,床层越来越高,一次风机压头不够,不能将床料吹起来,出现燃烧被压灭。
7.浓相床受热面布置过多,造成点火和运行过程中经常发生低温熄火
8.点火过程中.油枪撤除过早已造成熄火
采取床下预燃室和床上油枪点火时,当燃烧室温度达到850~900℃时,逐渐撤除油枪的同时,逐渐增加给煤量。
确认加入的煤着火、燃烧温度有上升趋势时,撤除最后一根油枪。
撤除油枪时流化介质温度由预燃烟气温度降到比环境温度稍高的温度,这时对燃烧带来较大冲击。
如果油枪全部撤除后,发现燃烧温度下降较快、有熄火危险时,赶快重新油枪助燃。
撤油枪操作处理不当,最易引起熄火事故。
第二节循环流化床燃烧结渣
各种结渣原因是操作温度超过了灰渣的熔点。
灰渣的熔点一般在1250~1350℃之间,具体数值的大小与灰渣特性、灰渣成分和燃烧气氛有关。
如果控制运行温度低于灰熔点200~300℃,保持良好的流化状态和正常的流动,就不会发生床料和灰渣的结渣现象。
燃烧室浓相床内结渣分高温结渣和低温结渣两种:
一、低温结渣常发生与点火启动过程中。
低温结渣的特点是整个浓相床温度较低,只有400~600℃,但在个别局部地方的温度,由于没有流化或流化不好,燃料燃烧释放的热量不能被烟气带走或被受热面吸收,造成热量局部堆积,使局部床料温度超过了灰渣熔点,而发生灰渣熔融结块。
低温结渣的表现:
浓相床内温度显示偏差大;火色差异大;风室压力波动较大。
处理办法:
一旦发现并确认,必须立刻采取果断措施消除结渣。
对小型炉子可打开炉门人工打耙子,打散渣块,继续点火(注意保持炉门负压防止烧伤司炉人员)。
对大型流化床锅炉,赶快加大风量将渣块打散。
(低温结渣的渣块比较疏松)
二、高温结渣
1、高温结渣的特点和处理
高温特点:
全床完全流化和全床燃烧温度超过灰渣熔点,全床发生灰渣的熔融和结块。
运行中的显示是燃烧火焰变成白色,刺眼;床层温度急剧上升,显示超过1050~1150℃;有的床层被吹空,火苗从床层往上直冲;风室压力波动异常。
处理方法:
小型流化床锅炉打开炉门扒出渣块,重新启动。
如果渣块盖满大半个或几乎整个床,只有停炉。
如果及时发现高温结渣,也可全开风机,用大风将炉子吹灭。
燃烧清渣。
2、高温结渣的原因分析
(1)点火过程中爆燃引起高温结渣。
(2)负荷大幅度变化导致高温结渣。
(3)燃煤热值大幅度改变导致高温结渣。
(4)返料器返料发生故障,不返料造成高温结渣。
(5)浓相床受热面布置过少易引起高温结渣。
(6)高温压火时易产生床料高温结渣。
(7)渣块落入浓相床造成床料高温局部结渣。
总的起来说循环流化床锅炉浓相床内的高温结渣原因有许多:
设计方面的原因——床内受热面不知过少;外界条件变化——锅炉负荷突然变小或燃煤热值许多;运行条件的变化——返料器突然停止返料,高温过热器区的大渣块落入床内,或压火过程操作不当。
第三节循环流化床锅炉其他区域结渣
一、高温过热器区结渣
影响高温过热器结渣的主要因素:
煤的种类,燃煤粒径分布,一、二次风分配和飞灰循环倍率。
(1)燃煤种类的影响。
(2)灰熔点低的煤易发生高温过热器结渣。
(3)燃煤小于1mm颗粒的百分数太高,造成燃烧室上部燃烧份额偏大,燃烧室出口温度偏高,产生高温过热器结渣。
(4)煤的灰分高,飞灰循环倍率过大,造成燃烧室出口温度偏高,引起高温过热器结渣。
(5)二次风比率偏高,造成燃烧室出口温度升高,引起高温过热器结渣。
采取措施:
运行人员必须注意监视煤种和煤质的变化及时调整燃煤粒度分布和一、二次风的比率,及飞灰循环倍率的大小,防止燃烧室出口烟温偏高和高温过热器区的二次燃烧。
另外,在高温过热器区不知吹灰器,定期吹灰。
如果发现结渣时就要施行人工打渣(加大风量,保持炉膛负压以免烧伤运行人员)
二、高温分离器结渣
1、影响高温旋风分离器结渣的因素:
(1)煤种的影响(主要是灰熔点的变低)。
(2)烟煤在分离器内燃烧回路份额比无烟煤大,二次燃烧产生的温升高,如果超过灰熔点是就易结渣。
(分离器的作用:
一是其分离作用,二是燃尽作用)
(3)煤的粒度的影响。
(4)燃烧室内流化速度的影响。
流化速度大,吹入分离器的物料的平均粒径大,数量多,造成二次燃烧强度加大,温升大,结渣的机会就大。
(5)二次风入口高度和二次风量大小的影响。
二次风入口里布风板近,二次风量大,风口以上燃烧室内的气流速度和物料浓度加大。
这样吹入分离器内的物料量和平均粒径均加大,两个因素的联合作用将导致分离器的二次燃烧温升变大,控制不好引起结渣。
2、分离器内结渣对燃烧的不利影响
(1)破坏了分离器内的气流场,造成分离效率变低,影响燃烧效率,降低锅炉蒸发量。
(2)渣块在分离器内变大后在合适的情况下堵住料腿,小渣块则落入返料器内破坏正常返料。
3、分离器内发生高温结渣的处理一旦结渣燃烧室出口烟气温度降低,锅炉蒸发量带不足,飞灰含碳量升高,分离器进出口之间的烟气压差加大。
如判断分离器结渣后,立即采取锅炉降低负荷运行,并寻求清渣措施。
否则停炉进行。
三、返料器内高温结渣
1、返料器内高温结渣的原因
(1)设计上的原因。
返料器流化床和移动床面积及送风量都偏大,返料器变成了一个燃烧器,燃烧温度超过灰熔点而结渣。
(2)运行上的原因。
、飞灰含碳量偏高,移动床送风量过大,造成移动床燃烧,燃烧温度超过灰熔点而结渣。
(3)分离器和返料器料腿中的耐磨隔热层脱落,掉入返料器中,破坏了移动床和流化床的流动情况而产生低温结渣
2、返料器结渣的判断
(1)燃烧室下部温度迅速上升。
(2)燃烧室出口温度迅速下降。
(3)锅炉负荷下降。
(4)飞灰含碳量上升。
3、防止返料器结渣的措施
(1)正确选定返料器移动床和流化床的风量和气流速度,防止返料器变成一个燃烧器。
(2)分布装设移动床和流化床送风量计,控制运行中的送风量,防止返料器中发生燃烧。
(3)返料器上设计结渣、打渣孔。
(4)一旦发现返料器结渣,应降低锅炉负荷,边运行、边清渣。
(5)如果边低负荷运行、边清渣不能解决问题,申请压火停炉清渣。
(6)、如果结渣十分严重,短时间内压火清渣不能解决问题,最终采取停炉清渣。
四、返料器料腿中结渣
料腿高度:
返料器料腿中的床料有一定的料柱高度。
料腿之上的床料为希相流动,料腿中床料的流动属移动床流动。
料腿中如果有被脱落的耐火层堵塞,发生床料流动受阻,有可能在受阻处结渣。
五、返料器至燃烧室的连接管(称之为返料管)结渣
第四节循环流动床燃烧爆炸事故
燃烧爆炸多发生在点火启动和燃烧操作、调整过程中,在正常运行过程中很少发生燃烧爆炸事故。
一、燃烧爆炸的基本条件(燃烧爆炸四要素)
(1)有大量的可燃气体,如H2、CO、CxHy等。
(2)有氧气存在。
(3)有明火。
(4)在一个比较密或流通不好的容器内。
四个条件同时具备才会发生燃烧爆炸。
二、点火启动过程中的燃烧爆炸
点火过程中有一个挥发份析出、着火燃烧,接着是焦炭的着火燃烧过程。
在这个过程中氧量是过剩的。
可燃气体燃烧爆炸四要因素中有三个要素存在。
只要第四个爆炸因素一具备,就有发生燃烧爆炸的可能。
三、燃烧调整、操作失误造成的燃烧爆炸事故
调整燃烧和运行操作过程中操作失误造成大量燃料进入燃烧室,产生大量可燃气体,当遇空气,并达到可燃气体与爆炸比时,又有火星存在,爆炸立即发生。
四、预防燃烧爆炸的措施
(1)司炉人员务必了解燃烧爆炸四要素。
(2)锅炉燃烧室上部都要设计防爆门,这样至少可减轻燃烧爆炸对设备的损坏。
(3)风室要布置防爆门。
(4)要有健全的点火操作规程,严格的防爆措施。
(5)操作人员要严格按规程操作。
(6)运行人员要牢记安全第一。
宁可多点火时间长一些,宁可多耗些油,也要防止燃烧爆炸。
(7)正确处理燃烧过程中的事故,如床料多、熄火等事故,防止燃烧爆炸。
(8)点火时床料中引子煤不要加入过多。
达到煤着火温度后,加煤要加加停停,断定加入的煤着火之后,随床温的上升逐渐加大的给煤量,防止点火过程中加煤过多,引起爆燃或爆炸。
第二部分汽轮机(直接空冷、抽汽凝汽式汽轮机)
第一章汽轮机常见事故处理
本章主要总结了汽轮机真空下降、超速、水冲击、动静部分摩擦及大轴弯曲、叶片损坏与脱落的故障原因、事故特征、处理方法等。
第一节汽轮机真空下降
一、汽轮机真空下降的危害及采取的措施
汽轮机运行中,凝汽器真空下降,将导致排汽压力升高,可用焓减小,同时机组出力降低;排汽缸及轴承座受热膨胀,轴承负荷分配发生变化,机组产生振动;凝汽器铜管受热膨胀产生松弛、变形,甚至断裂;若保持负荷不变,将使轴向推力增大以及叶片过负荷,排汽的容积流量减少,末级要产生脱流及