支撑块说明书.docx
《支撑块说明书.docx》由会员分享,可在线阅读,更多相关《支撑块说明书.docx(21页珍藏版)》请在冰豆网上搜索。
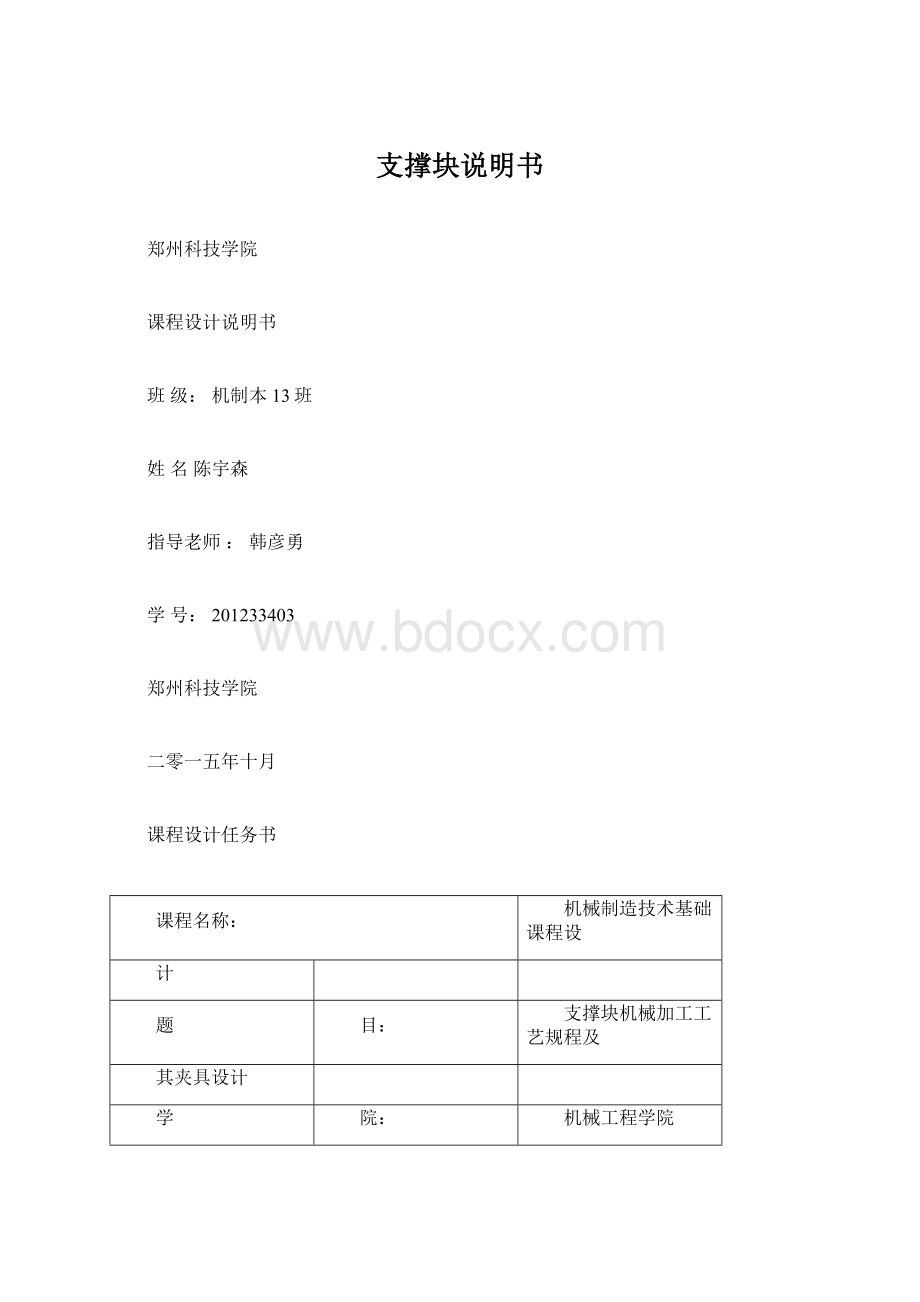
支撑块说明书
郑州科技学院
课程设计说明书
班级:
机制本13班
姓名陈宇森
指导老师:
韩彦勇
学号:
201233403
郑州科技学院
二零一五年十月
课程设计任务书
课程名称:
机械制造技术基础课程设
计
题
目:
支撑块机械加工工艺规程及
其夹具设计
学
院:
机械工程学院
专
业:
机械设计制造及其自动化
班
级:
十三班
学
号:
201233403
姓
名:
陈宇森
起讫日期:
指导教师:
韩彦勇
1.
设计任务............................................
1
1.1
设计题目.......................................
1
1.2
设计内容......................................
1
2.
零件分析............................................
1
2.1
零件的作用....................................
1
2.2
零件的尺寸及技术要求..........................
2
3.
确定毛坯的制造方法、初步确定毛坯形状................
4
3.1
选择毛坯的制造方式.............................
4
3.2
毛坯尺寸确定...................................
3
3.3
绘制毛坯图.....................................
4
4.
工艺规程设计........................................
6
4.1
定位基准的选择.................................
6
4.2
工件表面加工方法的选择.........................
5
4.3
制定加工工艺路线...............................
7
4.4
确定加工余量、工序尺寸及公差...................
8
4.5
选择机床及对应夹具、量具、刃具................
11
4.6确定切削用量、基本工时(机动时间).12
5.夹具设计.16
5.1设计要求.16
5.2夹具设计的有关计算.16
5.3夹具结构设计及操作简要说明.17
主要参考资料.20
1.设计任务
1.1设计题目
设计年产量为5000件的支撑块的机械加工工艺规程及典型夹具。
1.2设计内容
(1)
零件图
1张
(2)
毛坯图
1张
(3)
机械加工工艺过程卡
1份
(4)
机械加工工序卡
1份
(5)
夹具设计装配图
1张
(6)
夹具体零件图
1张
(7)
课程设计说明书
1份
1
2.零件分析
2.1零件的作用
对工作零件起支撑、定位作用。
图2-1零件图
如图2-1支承块阶梯孔、60mm表面、50mm表面是重
要加工表面。
根据零件的尺寸、形位要求,60mm表面有平行
度要求,50mm表面对阶梯孔37的中心线有垂直度要求。
零
件材料:
支承块的工作性能要求选择45号钢,45号钢为优质
碳素结构钢,硬度不高,易切削加工,但要进行热处理。
调制
处理后45号钢零件具有良好的机械性能,广泛应用于各种重要
的结构零件,特别是一些在交变荷载下工作的连杆、螺栓、齿
轮、及轴类等。
但表面硬度低,不耐磨。
可用调制+表面淬火提
2
高零件表面硬度。
2.2
零件的尺寸及技术要求
如表2-2
粗糙
尺寸
尺寸
形位公差
面度
精度
公差
阶梯孔
1.6
IT7
37-00.011.014
与上表面有垂
直度要求0.02
阶梯孔阶梯端面
3.2
左右表面AB
1.6
IT8
AB表面有对称
60-00..0105
度要求0.02
上下表面CD
3.2
40外圆
3.2
螺纹底孔3-M5深12
6.3
螺纹底孔M16X1.5
6.3
3
3.确定毛坯的制造方法、初步确定毛坯形状
3.1选择毛坯的制造方式
根据生产纲领的要求,本零件是中批、大批大量生产,还
有零件的材料要求(45号钢)及加工表面与非加工表面的技术
要求,我们选择毛坯的制造方式为锻造。
根据《机械制造工艺
设计简明手册》(机械工业出版出版社、哈尔滨工业大学李益民
主编)零件材料为45钢,采用模锻,精度可达到IT11-15,因
此毛坯的加工余量一般。
3.2毛坯尺寸确定
(1)锻件质量Mf0.12kg
(2)锻件的形状复杂系数
Mf
1
1
S
MN
2
2
194864.6
0.684
95x50x60
0.63s1所以为S1级(简单)。
(3)分模线形状:
平直对称
(4)锻件的材质系数:
45号钢含碳量0.42~0.5%,所以材质系数为M1级。
根据上述数据参照《模锻件机械加工余量与公差标准》(JB3834-1985)执行。
锻件的公差范围为普通级。
查表的尺寸及公差如下:
阶梯孔30-00..48,左右表面AB63-01..40,外圆43,上下表
4
面CD53,GH面98,EF面偏离零件设计面1.5mm。
3.3绘制毛坯图
5
4.工艺规程设计
4.1定位基准的选择
(1)精基准的选择:
根据该零件的技术要求,选择37
的孔为精基准。
零件上的很多表面都可以用它们作为基准进行
加工,即遵循了“基准统一原则”。
为了保证50mm表面与其中
心线垂直和保证60mm表面和零件的对称面平行,须先将37
的孔加工出来,再用它定位满足其他尺寸要求。
(2)粗基准的选择:
作为粗基准的表面应平整,没有飞边、
毛刺或其他表面缺陷。
对于本零件而言,选择50mm表面作为
粗基准。
该表面毛坯质量好,余量均匀。
4.2工件表面加工方法的选择
(1)阶梯孔加工方法:
粗镗、半精镗、精镗
(2)50mm面CD:
粗铣、精铣
(3)60mm面AB:
粗铣、半精铣、精铣
(4)直径40mm外圆表面:
粗车、精车
(5)95mm面GH:
粗铣
(6)EF面:
粗铣
(7)螺纹孔M16X1.5:
钻孔、攻螺纹
(8)螺纹孔3-M5:
钻孔、攻螺纹
(9)半圆孔4-R3:
插齿
6
4.3制定加工工艺路线
加工工艺方案分析:
遵循“先基准后其他”原则,应先加工37的孔。
按照“先粗后精”的原则,先安排粗加工工艺,后安排精加工工艺。
遵循“先主后次”的原则,先加工主要表面直径37的孔级台阶孔端面,50mm表面,60mm表面,40mm外圆;后加工次要表面M16X1.5螺纹孔和3个M5深12的螺纹孔。
遵循“先面后孔”原则,先加工支承块四个表面、外圆表面,在加
工3个孔。
由于生产类型为成批生产,故采用通用机床配专用夹具,并尽量使工序集中来提高生产率。
除此之外,还应降低成本。
因此确定加工路线如下:
工序10:
粗铣上下面CD
工序20:
粗镗、半精镗、精镗Φ37阶梯孔。
粗镗至尺寸Φ31
和Φ
34.5
0.25
、半精镗至尺寸Φ
0.10
、
精镗至尺寸Φ
0.014
0
36.50
37
-0.011
工序30:
精铣上下面CD
工序40:
粗车、精车Φ40外圆并倒角
工序50:
精车Φ37阶梯孔的阶梯端面
工序60:
粗铣、半精铣、精铣左右面
AB;
工序70:
粗铣G、H面
工序80:
粗铣E、F面
工序90:
钻螺纹孔、攻螺纹;
工序100:
钻螺纹孔、攻螺纹;
工序110:
插齿
工序120:
清洗、检验入库
7
4.4确定加工余量、工序尺寸及公差
阶梯孔孔径Φ37-00..011014,表面粗糙度为1.6,加工方案为粗
镗、半精镗、精镗,阶梯孔端面表面粗糙度为3.2而且有尺寸
要求400-0.1,加工方案为精车,下面求解各道工序尺寸及公差。
(1)用查表法确定各道工序的加工余量及毛坯总余量如下
(见课程设计手册表)
精镗加工余量=0.5mm
半精镗加工余量=2mm
粗镗加工余量=4.5mm
毛坯总余量=各工序余量之和=(0.5+2+4.5)mm=7mm
精车加工余量=0.2mm
(2)计算各工序尺寸的基本尺寸
精镗后孔径应达到图样规定尺寸,因此磨削工序尺寸即图样上
0.014
的尺寸D3
=37-0.011mm(设计尺寸)。
其他各道工序基本尺寸
依次为
半精镗D2
=(37-0.5)mm=36.5mm
粗镗D1=(36.5-2)mm=34.5mm
毛坯D0=(34.5-4.5)mm=30mm
(3)确定各道工序尺寸的公差及其偏差。
工序尺寸的公差按各加工方法所能达到的经济精度确定,
查阅相关“机械制造技术基础”教材中各种加工方法的经济加工
8
精度表或参阅机械制造技术基础课程设计图2-9进行选择。
精镗前半精镗取IT10级,查表得T2=0.10mm(机械制造技术
基础课程设计表3-4)
粗镗取IT12级,查表得T1=0.25mm(机械制造技术基础课程设
计表3-4)
毛坯公差取自毛坯图,这里查阅《机械零件工艺性手册》(GB/T
6414-1999),取T0=0.7mm。
(4)工序尺寸偏差按“入体原则”标注
1.014
精镗:
37-0.011mm
半精镗:
36.50
0.10mm
粗镗:
34.50
0.25mm
毛坯孔:
30-00.4.8mm
为了清楚起见,把上述结果汇于表
5-1中。
表5-1孔的工序尺寸及公差的计算
工序名称
工序间双边余量
工序达到的公差
精镗
0.5
IT7
半精镗
2
IT10
粗镗
3.5
IT12
毛坯孔
-
0.8
-0.4mm
mm
工序尺寸及公差
0.014
37-0.011(H7)
36.500.10
34.500.25
30-0.40.8
镗孔深度40-0.2=39.8mm
上下面C、D经过了粗铣和精铣,用查表法确定各道工序
9
的加工余量
计算各工序尺寸的基本尺寸。
粗铣(单边)余量=1.0mm表面粗糙度6.3精铣(单边)余量=0.5mm表面粗糙度3.2
外圆表面经过了粗车、精车两道工步
用查表法确定各道工序的加工余量及毛坯总余量如下粗车加工余量=2.8mm(见课程设计手册表)精车加工余量=0.2mm(见课程设计手册表)
毛坯总余量=各工序余量之和=(2.8+0.2)mm=3mm用查表法确定各道工序的加工余量及毛坯总余量
工序尺寸的公差按各加工方法所能达到的经济精度确定,查阅相关“机械制造技术基础”教材中各种加工方法的经济加工精度表或参阅机械制造技术基础课程设计图2-9进行选择。
精铣前半精铣取IT11级,查表得T2=0.22mm(机械制造技术
基础课程设计表)
粗镗取IT12级,查表得T1=0.35mm(机械制造技术基础课程
设计表)
为了清楚起见,把上述结果汇于表中。
AB表面的工序尺寸及公差的计算
mm
工序名称
工序间双边余量
工序达到的公差
工序尺寸及公差
精铣
0.5
IT8
0.05
60-0.01
半铣镗
1
IT11
60.5-00.035
10
粗铣
1.5
IT12
61.50
0.25
毛坯孔
-
1.0
63
1.0
mm
-0.4
-0.4
由于G、H、E、F表面只要粗铣就可以达到加工要求所以
它们工序的加工余量均为1.5。
五、选择机床及对应夹具、量具、
刃具
4.5选择机床及对应夹具、量具、刃具
(1)工序10、30、60、70、80是铣削加工,各工序的工步数不多,成批生产不要求很高的生产率,根据工件尺寸选用
X5020A立式铣床。
(机械制造技术基础课程设计表5-5)
(2)工序90、100是钻孔、攻螺纹。
根据工件尺寸可以选
用Z5125A型立式钻床。
(机械制造技术基础课程设计表5-6)
(3)工序20是粗镗、半精镗、精镗孔,根据工件尺寸可
以选用T618型卧式镗床。
(机械制造技术基础课程设计表
5-9)
(4)工序40、50是车削加工。
根据工件尺寸可以选用
CA6140型卧式车床。
(5)工序110是插孔。
根据工件尺寸选用Y54B型插齿机。
为了提高劳动生产率、保证加工质量、降低劳动强度。
可
以设计专用夹具。
本零件属成批生产,一般情况下尽量采用通用量具。
根据
零件表面的精
度要求、尺寸和形状特点,参考本书有关资料,选择如下。
(1)选择加工孔用量具。
37-00..011014mm孔经粗镗、半精镗、
11
精镗三次加工。
粗镗至34.500.25mm,半精镗36.500.10mm。
a.粗镗孔34.500.25mm,公差等级为ITl2,选择测量范
围0mm-60mm的内径千分尺即可。
b.半精镗孔36.500.10mm,公差等级为IT10,选择测量
范围0mm-60mm的内径千分尺即可。
c.精镗孔37-00..011014mm,由于精度要求高,加工时每个工
件都需进行测量,故宜选用极限量规。
根据孔径可选三牙锁紧
式圆柱塞规(GB/T6322-1986)。
(2)Φ15螺纹孔、Φ4螺纹孔,选择测量范围0mm-20mm
的内径千分尺即可。
(3)其他尺寸如:
AB面、CD面、GH面的尺寸可以选
用0mm-100mm游标卡尺。
(1)铣削AB、CD、EF、GH面时,选用镶齿套式硬质合金端
面铣刀,直径D=Φ80mm
(2)镗孔时选用机夹单刃硬质合金镗刀直径D=Φ20mm
(3)车阶梯孔阶梯端面时选用端面车刀。
(4)钻孔15mm时,选用直柄麻花钻,直径15mm。
(5)钻孔4mm时,选用直柄麻花钻,直径4mm。
(6)攻螺纹时用M16、M5的螺纹刀。
(7)插齿时选用6的插刀。
4.6确定切削用量、基本工时(机动时间)
(A)确定切削用量
12
a.确定背吃用量
粗镗时,为提高效率,一般选择镗削背吃刀量等于加工余量,
一个工作行程镗完,所以粗镗大孔时加工余量为4.5mm,选择
背吃刀量ap4.5mm
b.确定进给量和切削速度
1)根据《机械制造技术基础课程设计》表5-83,选择进给
量为0.8mm/r切削速度为0.45m/s.
2)确定镗刀的磨钝标准及耐用度
根据《机械制造技术基础课程设计》表3-7取粗镗时单刃镗刀刀具的耐用度T=50min。
3)确认机床主轴转速
(B)确定时间定额
基本时间
查《机械制造技术基础课程设计》表3-10得:
=40mm,
=3mm,=3mm。
(A)确定切削用量
a确定背吃用量
半精镗时,半精镗时一般为1.5~3mm或更小,所以取背吃刀量
等于其在此工序的加工余量,即=2mm。
0
b确定进给量和切削速度
13
1)根据《机械制造技术基础课程设计》表5-83,选择进给量
为0.6mm/r切削速度为0.45m/s.
2)确定镗刀的磨钝标准及耐用度
根据《机械制造技术基础课程设计》表3-7取半精镗时单刃镗
刀刀具的耐用度T=50min。
3)确认机床主轴转速
10
(B)确定时间定额
基本时间
查《机械制造技术基础课程设计》表3-10得:
=40mm,
=3mm,=3mm。
精镗
(A)确定切削用量
a.确定背吃用量
取背吃刀量等于其在此工序的加工余量,即=0.5mm。
b.确定进给量和切削速度
1)根据《机械制造技术基础课程设计》表5-83,选择进给
量为0.3mm/r切削速度为0.45m/s.
2)确定镗刀的磨钝标准及耐用度
根据《机械制造技术基础课程设计》表3-7取半精镗时单刃镗
14
刀刀具的耐用度T=50min。
3)确认机床主轴转速
技术基础课程设计》表3-10得:
=40mm,=3mm,=3mm。
15
5.夹具设计
5.1设计要求
根据课程设计的要求,设计一个车40外圆的专用夹具。
加工要求为:
加工外圆,保证同轴度。
因此,必须限制的自由
度为X,Z,X、Z方向的旋转自由度。
夹具的主要结构为:
莫氏
5号锥度轴、过渡盘、2个定位元件、夹紧装置、平衡块、螺母
等。
具体见附图。
5.2夹具设计的有关计算
必要的加工精度分析、计算:
定位形式为两垂直平面定位,
定位误差计算公式为
机床Z方向上误差(Z)(2Hh)tan=2(50-45)
DW
tan=10tan
机床Y方向上误差(Y)(2Hh)tan=2x(63-51.5)
DW
tan=13tan
为两定位元件垂直度误差。
必要的夹紧力的分析、计算:
工件以两个垂直平面定位,侧
向夹紧。
所需的夹紧力为
FSKFXbFYL(N)
afL
16
5.3夹具结构设计及操作简要说明
车床专用夹具设计要点
在车床上加工回转面时,要求工件被加工面的轴线与车床
主轴的旋转轴线重合,夹具上定位装置的结构和布置,必须保
证这一点。
选择50mm表面中的一个表面和60mm表面中的一
个,共两个相互垂直的表面作定位面,如图所示。
在车削过程中,由于工件和夹具随主轴旋转,除工件受切削扭矩的作用外,整个夹具还受到离心力的作用。
此外,工件定位基准的位置相对于切削力和重力的方向是变化的。
因此,夹紧机构必须产生足够的夹紧力,自锁性能要可靠。
对于角铁式夹具,还应注意施力方式,防止引起夹具变形。
选择螺栓与
37的孔配合来做夹紧装置,如图所示。
车床夹具与机床主轴的连接精度对夹具的回转精度有决定
性的影响。
因此,要求夹具的回转轴线与主轴轴线应具有尽可
能高的同轴度。
17
心轴类车床夹具以莫氏锥柄与机床主轴锥孔配合连接,用螺
杆拉紧。
所以选择莫氏5号锥度轴
车床夹具一般是在悬臂的状态下工作,为保证加工的稳定
性,夹具的结构应力求紧凑、轻便,悬伸长度要短,使重心尽
可能靠近主轴。
由于加工时夹具随同主轴旋转,如果夹具的总体结构不平
衡,则在离心力的作用下将造成振动,影响工件的加工精度和
表面粗糙度,加剧机床主轴和轴承的磨损。
因此,车床夹具除
了控制悬伸长度外,结构上还应基本平衡。
因此,设计一个平
衡块,通过调整质量块的位置,使质量中心与回转中心重合,
保证加工过程的平稳。
18
1-螺钉2-定位块3-螺母4-垫圈5-螺栓6-平衡块7-过渡盘
8-莫氏5号锥度轴
19
参考资料
[1]柯建宏.机械制造技术基础课程设计.武汉.华中科技大学出版社,2012
[2]王先逵.机械制造工艺学.北京:
机械工业出版社,2006
[3]陈宏钧.实用.北京:
机械工业出版社,2003
[4]四川大学CAD/CAM研究所.机床夹具设计手册.北京:
机械工业出版社,2001
[5]机械加工工艺手册(软件版)编委会.机械加工工艺手册(软件版).北京:
机械工业出版社,2001
20