压力管道元件无损检测通用规程.docx
《压力管道元件无损检测通用规程.docx》由会员分享,可在线阅读,更多相关《压力管道元件无损检测通用规程.docx(48页珍藏版)》请在冰豆网上搜索。
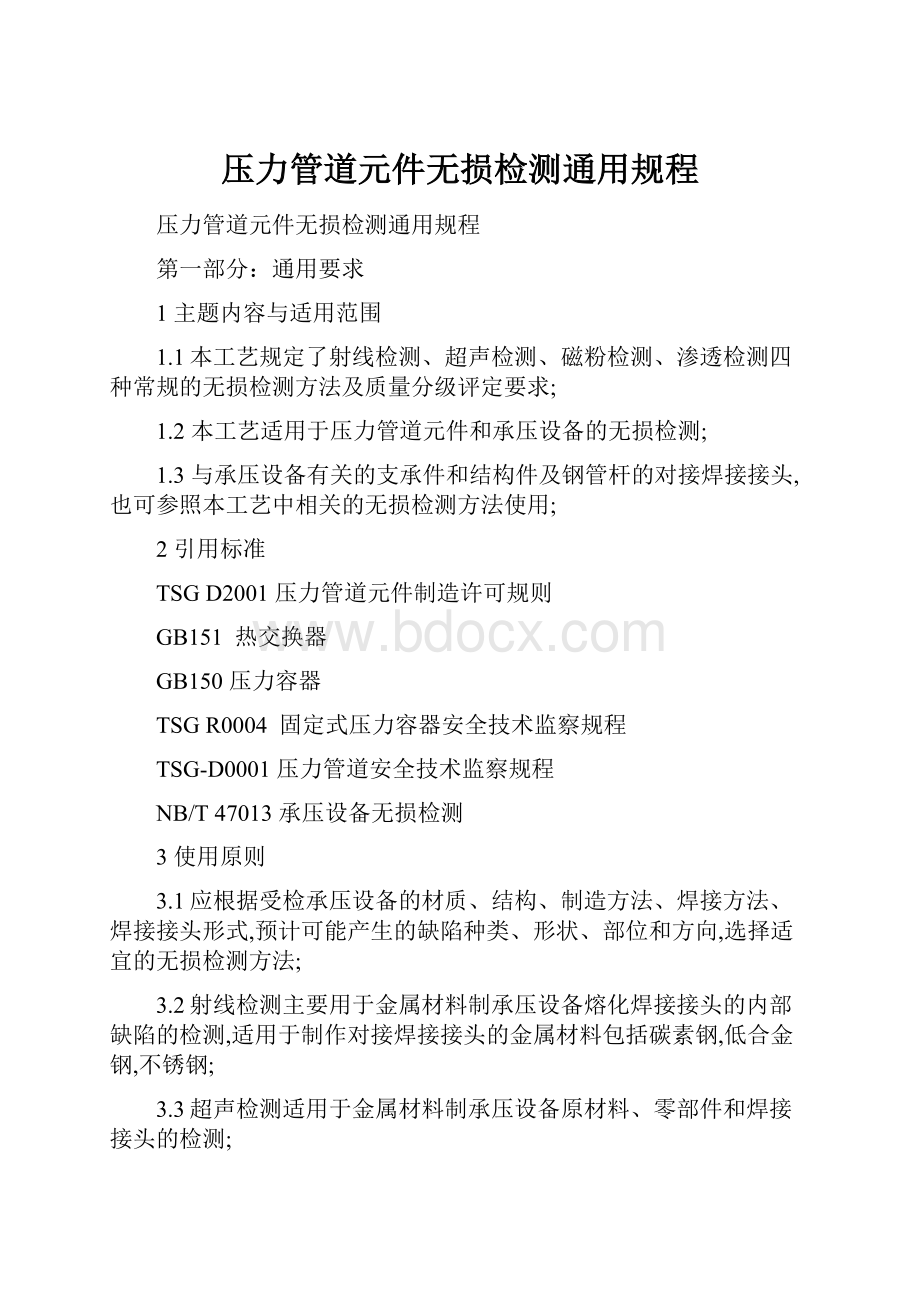
压力管道元件无损检测通用规程
压力管道元件无损检测通用规程
第一部分:
通用要求
1主题内容与适用范围
1.1本工艺规定了射线检测、超声检测、磁粉检测、渗透检测四种常规的无损检测方法及质量分级评定要求;
1.2本工艺适用于压力管道元件和承压设备的无损检测;
1.3与承压设备有关的支承件和结构件及钢管杆的对接焊接接头,也可参照本工艺中相关的无损检测方法使用;
2引用标准
TSGD2001压力管道元件制造许可规则
GB151热交换器
GB150压力容器
TSGR0004固定式压力容器安全技术监察规程
TSG-D0001压力管道安全技术监察规程
NB/T47013承压设备无损检测
3使用原则
3.1应根据受检承压设备的材质、结构、制造方法、焊接方法、焊接接头形式,预计可能产生的缺陷种类、形状、部位和方向,选择适宜的无损检测方法;
3.2射线检测主要用于金属材料制承压设备熔化焊接接头的内部缺陷的检测,适用于制作对接焊接接头的金属材料包括碳素钢,低合金钢,不锈钢;
3.3超声检测适用于金属材料制承压设备原材料、零部件和焊接接头的检测;
3.4磁粉检测适用于铁磁性材料制原材料、零部件和焊接接头表面、近表面缺陷的检测;
3.5渗透检测适用于非多孔性金属材料和非金属材料制承压设备在制造、安装及使用中产生的表面开口缺陷的检测;
4一般要求
4.1无损检测人员
4.1.1从事承压设备的原材料零部件和焊接接头无损检测人员,应按照《特种设备无损检测人员考核与监督管理规则》的要求取得相应无损检测资格;
4.1.2具有无损检测方法资格级别的人员,只能从事与其资格级别相应的无损检测工作,并负相应的技术责任;
4.1.3无损检测人员必须身体健康,并每一年进行一次放射工作人员职业性健康检查,并有记录可查;每年进行一次视力检查,校正视力不得低于1.0;
4.1.4无损检测人员应能熟练操作各种检测仪器,严格按相应的工艺卡中的技术参数进行合理的检测;
4.2对接焊接接头的要求
4.2.1焊缝及热影响区的表面质量(包括焊缝余高)应经外观检查合格,表面的不规则状态在底片上的图像应不掩盖焊缝中的缺陷或与之相混淆,否则应做适当的修整;
4.2.2焊缝两侧应清除焊疤,飞溅等物质,焊缝表面和热影响区表面不允许有裂纹、气孔、弧坑和夹渣等缺陷;
4.3无损检测资料
4.3.1检测记录和报告应准确,完整,并经相应的责任人员签名认可;
4.3.2检测记录和报告等保存期不得少于设计使用年限;达到设计使用年限后可上报企业质管办商订处理方式;
4.3.3检测用仪器和设备的性能应进行定期检定(校准),并有相应记录;
5无损检测标识
经无损检测合格的产品或零部件上应作出永久性标识,标记应清晰,分别采用RTP、UTP、MTP、PTP钢印作为常规检测方法的合格标记;产品上不适合打钢印标记时,可采用详细的检测草图或其它有效的方式,使下道工序或最后检测人员能够辩明;
第二部分:
射线检测通用工艺规程
1.主题内容及适用范围
1.1本工艺规程规定了压力管道元件及承压设备受压元件的熔化焊对接接头的X射线检测方法、底片质量和质量分级的要求;
1.2本工艺规程适用于压力管道元件及承压设备受压元件的对接焊接接头的检测;用于制作焊接接头的金属材料包括碳素钢、低合金钢、不锈钢;
1.3本工艺规程规定射线检测技术为AB级中灵敏度技术;
2引用标准
TSGD2001压力管道元件制造许可规则
GB151热交换器
GB150压力容器
TSGR0004固定式压力容器安全技术监察规程
TSG-D0001压力管道安全技术监察规程
NB/T47013承压设备无损检测
3.射线检测人员要求
3.1从事射线检测的人员应按照《特种设备无损检测人员考核与监督管理规则》的要求取得射线检测资格证书,评片人员必须持有Ⅱ级或Ⅲ级资格证书;
3.2从事射线检测人员上岗前应进行辐射安全知识的培训,并取得放射工作人员证;
3.3射线检测人员必须身体健康,经体检合格,评片人员视力应每年检查一次;未经矫正或经矫正的近(距)视力和远(距)视力应不低于5.0(小数记录值为1.0);
3.4射线检测人员应能熟练操作射线机,正确选用透照工艺,合理使用暗室处理方法,并应熟悉焊接工艺、金属材料等知识,应了解压力管道元件制造工艺,熟悉有关压力管道元件的法规、标准和技术条件;
3.5对接接头的表面质量要求应符合通用部分有关要求;
4.射线检测和验收标准
4.1范围:
必须符合《固定式压力管道元件安全技术监察规程》,GB150和设计文件的要求;
4.2凡要求进行100%射线检测的容器,对其A类和B类焊接接头应不低于JB/T4730.2-2005标准中质量等级Ⅱ级的要求;凡局部射线检测的容器,对其A类和B类焊接接头应不低于JB/T4730.2-2005标准中质量等级Ⅲ级的要求,对低温容器检测长度不得少于各焊接接头长度的50%;对非低温容器检测长度不得少于各焊接接头长度的20%,且均不得小于250mm;
4.3局部射线检测的容器对其所有的T型连接部位,以及拼接封头(管板)的对接接头,必须进行射线检测;
4.4局部射线检测的容器,如在焊接接头上开孔,则以开孔中心为圆心,1.5倍开孔直径为半径的圆中所包容的焊接接头,被补强圈、支座、垫片、内件等所覆盖的焊接接头必须进行射线检测;
4.5如封头采用拼接焊缝,则在压制之后进行100%射线检测;公称直径大于250mm的接管对接接头应进行射线检测;
4.6对局部射线检测的焊接接头,若在检测部位发现超标缺陷时,则应在该缺陷两端的延伸部位,增加不少于该焊缝长度的10%进行,若仍有不允许的缺陷时,则对该条焊接接头做100%的射线检测;
5.检验程序:
5.1经焊接检验员检查合格的焊接接头,应有焊接检验员填写无损检测委托单交无损检测室;
5.2无损检测室接到委托单后,方可安排射线检测;
5.3焊缝及热影响区若不符3.5的要求时,无损检测室应将委托单反馈焊接检验员;
5.4对有延迟裂纹倾向的材料射线检测,应当至少在焊接完成24小时后方可进行;有再热裂纹倾向的材料应当在热处理后增加一次无损检测;
5.5检测人员必须按本工艺做好一切准备工作,并编制射线透照检测工艺卡,按本工艺程序进行操作、暗室处理和底片评定;
6.布片(划线)规定:
6.1焊缝射线检测编号的规定;
6.1.1产品试板的编号,按该试板所代表的产品编号为检测编号;并且应有试板的编号AS,工艺评定试板的工艺评定号为检测编号,片号以S1、S2…表示之;
6.1.2整台产品以产品编号作为检测编号,其表示方法:
A1209/3
该批台数
批次顺序号
制造年份号
产品类别代号
例:
A1209/3其表示内容为2012年压力管道元件第9批共3台;
6.1.3整台产品的焊缝编号以焊接工艺卡节点图上的编号为依据,纵缝以“A”表示,第一条纵缝为1A、第二条纵缝为2A;纵缝第1张为A1、纵缝第2张为A2;如第1条纵缝第二张片即以1A2表示之;环缝以“B”表示,第一条环缝为1B、第二条环缝为2B;环缝第1张为B1、环缝第2张为B2;如第1条环缝第二张片即以1B2表示之;
6.1.4平板封头焊缝检测以“FA”表示,第一条FA1表示,第一张片为FA1-1表示,成型封头焊缝以所配的产品编号及焊卡上的编号为准;
6.1.5焊缝返修标记,一次返修在片号后加“R1”,二次返修在片号后加“R2”表示,增拍片在片号前加”G”表示,旋压(折边)后复拍在片号加“+”表示;
如:
1A1R1表示第一条纵缝第一张片第一次返修;1B1R2表示第一条环焊缝第一张片第二次返修;G1B3表示第一条环缝第三张片,该片为增拍片;
6.2焊缝检测一次透照长度L3和透照次数N的确定;
6.2.1纵缝(包括试板纵缝)的L3规定一般为300mm;特殊情况下L3可增大和缩小,但应满足透照厚度比K≤1.03(A级、AB级)要求;旋边(折边)部分应单独按K值要求进行划线布片;
6.2.2环缝使用定向曝光则根据NB/T47031.2-2005标准取K≤1.1(A级、AB级),首先先计算或查图表,确定整圈环缝透照透照次数N,再以下式计算L3;L3′=πD/N并根据L3′取整数确定L3,其通常规格的容器环缝一次透照长度及透照次数见表1、表2;
表1:
单壁外透法透照次数一览表
内径φ
N
L3(内)
T
L3外
4
5
6
8
10
12
14
400
10
126
128
129
129
130
132
133
135
450
10
141
144
144
145
146
147
149
150
500
10/11
157/143
159
160
161
162
N=11/148
N=11/149
N=11/148
550
11
157
159
160
160
162
163
164
165
600
11
171
173
174
175
176
177
178
179
700
11/12
200/183
202
203
203
204
206
N=12/189
N=12/190
800
12
209
211
212
213
214
215
216
217
900
12/13
235/217
238
238
239
240
N=13/222
N=13/223
N=13/224
1000
13
241
244
244
245
246
247
248
1100
13/14
266/247
268
269
N=14/250
N=14/251
N=14/252
N=14/253
1200
14
269
271
272
273
274
275
276
1300
14/15
292/272
294
294
295
296
297
N=15/278
1400
15
293
295
296
297
297
298
299
1500
16
294
296
297
298
298
299
300
1600
17
296
297
298
298
299
300
301
1700
18
297
298
299
299
300
301
302
1750
18
305
307
307
308
309
310
310
1800
19
297
299
299
300
301
301
302
1900
20
298
300
300
301
301
302
303
注:
1)为保证相邻边界标记能重叠,防止漏检,标记带上的搭接标记可适当扩展;
2)透照长度应控制在300mm以内;公称厚度较厚时,透照长度应控制在290mm以内;
1)焦距为700mm;
表2:
双壁单透法透照次数一览表
φ
F
N
L3
T
L3
6
8
10
12
219
400
6
115
273
500
6
143
325
550
6
170
377
600
5
236
426
650
5
268
450
650
5
290
292
295
298
500
700
6
268
270
272
274
600
800
7
269
275
276
278
280
700
900
8
275
281
281
283
285
800
1000
9
279
283
285
286
288
1000
1200
11
289
290
291
293
注:
1)φ450至φ1000为内径尺寸;
6.3布片(划线)方法:
6.3.1全部(100%)和局部≥20%射线透照检测的产品均采用100%布片,对局部检测的产品除本工艺规定必须检测的部位外,由检测人员或焊接检验员自行任意抽查,检测部位由检测人员在摄片定位图中注明;
6.3.2环缝以外径周长尺寸为焊缝全长,以该台产品的N为透照次数,L3为划线长度,以该环缝和筒体交叉部位(T型接头)中心为第一张片,以顺时针方向顺序划线;
6.4射线透照检测部位打钢印规定:
6.4.1纵环缝的起始号(1号片)位置应打焊缝编号,片号中心标记,确保中心标记钢印与标记带上的中心位置重合;
6.4.2其余透照部位应在摄片定位图中注明,所摄片号,并与实物、X光底片相符,保证追溯的准确性和重复性;
6.4.3凡打钢印的部位,钢印应离焊缝边缘10-20mm,深度不宜超过0.5mm;
6.4.4对某种特殊的材料不准打钢印的产品,由检测人员负责绘制详细焊缝检测部位示意图,标注尺寸,并用有色笔在检测部位写上焊缝编号、片号及中心标记;
6.5布片示意图如下:
7.射线透照器材选择要求:
7.1X射线透照
7.1.1当焦距为700mm时,曝光量为:
A级和AB级射线检测技术不小于15mA·min,当焦距改变时按平方反比定律对曝光量推荐值进行换算;
7.1.2选用的射线源至工件表面的距离f应满足如下要求:
……A级射线检测技术:
f≥7.5d·b2/3
……AB级射线检测技术:
f≥10d·b2/3
7.1.3对每台X射线机均应作出经常检测材料的曝光曲线,依据曝光曲线确定曝光参数;对使用中的曝光曲线每年应校验一次;
7.1.4X射线照相时应尽量选用较低的管电压;X光机能量应留有20%余量,以保证仪器使用寿命;
7.2胶片:
选用T3类或更高类别的胶片类型,如:
AgfaD7,天津Ⅲ型,上海GX-A7;其本底灰雾度应不大于0.3;
7.3增感屏:
采用铅箔增感,前屏厚度0.02-0.05mm,后屏厚度大于前屏,一般采用0.03/0.10;增感屏和胶片在透照中应保证紧贴;
7.4暗盒:
一般使用80×360mm和80×250mm,暗盒不得漏光,对初次制定的检测工艺,或使用中工艺条件及环境发生改变时,应进行背散射防护检查,暗盒背面要贴附“B”铅字标记;(其高度为13mm,厚度为1.6mm);
7.5像质计:
7.5.1线型像质计的型号&规格应符合JB/T7902的规定,JB/T7902中未包含的线号、丝径等内容,应符合HB7684的有关规定;
7.5.2像质计的选用应符合下列表格的要求;
表3像质计灵敏度值—单壁透照、像质计置于源侧
应识别丝号
(丝径,mm)
公称厚度(T)范围,mm
A级
AB级
B级
18(0.063)
—
—
≤2.5
17(0.080)
—
≤2.0
>2.5~4.0
16(0.100)
≤2.0
>2.0~3.5
>4~6
15(0.125)
>2.0~3.5
>3.5~5.0
>6~8
14(0.160)
>3.5~5.0
>5.0~7
>8~12
13(0.20)
>5.0~7
>7~10
>12~20
12(0.25)
>7~10
>10~15
>20~30
11(0.32)
>10~15
>15~25
>30~35
10(0.40)
>15~25
>25~32
>35~45
9(0.50)
>25~32
>32~40
>45~65
8(0.63)
>32~40
>40~55
>65~120
7(0.80)
>40~55
>55~85
>120~200
6(1.00)
>55~85
>85~150
>200~350
5(1.25)
>85~150
>150~250
>350
4(1.60)
>150~250
>250~350
—
3(2.00)
>250~350
>350
—
2(2.50)
>350
—
—
表4像质计灵敏度值——双壁双影透照、像质计置于源侧
应识别丝号
(丝径,mm)
公称厚度(T)范围,mm
A级
AB级
B级
18(0.063)
—
—
≤2.5
17(0.080)
—
≤2.0
>2.5~4.0
16(0.100)
≤2.0
>2.0~3.0
>4~6
15(0.125)
>2.0~3.0
>3.0~4.5
>6~9
14(0.160)
>3.0~4.5
>4.5~7
>9~15
13(0.20)
>4.5~7
>7~11
>15~22
12(0.25)
>7~11
>11~15
>22~31
11(0.32)
>11~15
>15~22
>31~40
10(0.40)
>15~22
>22~32
>40~48
9(0.50)
>22~32
>32~44
>48~56
8(0.63)
>32~44
>44~54
—
7(0.80)
>44~54
—
—
表5像质计灵敏度值——双壁单影或双壁双影透照、像质计置于胶片侧
应识别丝号
(丝径,mm)
公称厚度(T)范围,mm
A级
AB级
B级
18(0.063)
—
—
≤2.5
17(0.080)
—
≤2.0
>2.5~4.0
16(0.100)
≤2.0
>2.0~3.5
>4~6
15(0.125)
>2.0~3.5
>3.5~5.5
>6~12
14(0.160)
>3.5~5.5
>5.5~11
>12~18
13(0.20)
>5.5~11
>11~17
>18~30
12(0.25)
>11~17
>17~26
>30~42
11(0.32)
>17~26
>26~39
>42~55
10(0.40)
>26~39
>39~51
>55~70
9(0.50)
>39~51
>51~64
>70~100
8(0.63)
>51~64
>64~85
>100~180
7(0.80)
>64~85
>85~125
>180~300
6(1.00)
>85~125
>125~225
>300
5(1.25)
>125~225
>225~375
—
4(1.60)
>225~375
>375
—
3(2.00)
>375
—
—
表6不同焊接型式的透照厚度W
公称厚度
焊缝余高
透照厚度W(mm)
单壁透照
双壁单影或双壁双影透照
T
无
T
T×2
T
单面
T
T×2
T
双面
T
T×2
T
单面(有垫板)
T
T×2
注:
1)T—表示受检工件名义厚度,不考虑材料制造偏差和加工减薄;
2)W—表示射线照射方向上材料的公称厚度;多层透照时,透照厚度为通过的各层材料公称厚度之和;(不考虑垫板厚度及余高)
3)焊缝两侧母材厚度不同时,以薄板公称厚度计算;
7.5.2像质计应放在工件源侧表面焊接接头的一端(被检区长度1/4部位),金属丝应横跨焊缝,细丝置于外侧;
7.5.3单壁透照时像质计应放置在源侧,双壁单影透照时像质计应放置于胶片侧;双壁双影透照时可放置于源侧,也可放置于胶片侧;
7.5.4单壁透照中,如果像质计无法放置于源侧,也可放置于胶片侧;但应进行对比试验,以保证实际透照的底片灵敏度符合要求;当像质计放置在胶片侧时,应在像质计上适当位置放置铅字“F”作为标记,“F”标记的影像应与像质计的标记同时出现在底片上,且应在检测报告中注明;
7.5.6小径管(外直径D0≤100MM)可选用通用线型像质计或JB/T4730.2-2005附录F规定的专用(等径金属丝)像质计,金属丝应横跨焊缝放置;
7.5.7底片黑度均匀部位(一般是邻近焊缝的母材金属区)能清晰地看到长度不小于10mm的连续金属丝影像时,则认为该丝是可识别的;专用像质计至少应能识别两根金属丝;
7.6标记:
7.6.1被检测的每段焊缝附近(底片上)应有下列铅质的识别标记,产品编号、像质返修标记“R”,需增拍时还应增拍标记“G”,及必要时的“F”标记;其排列示意如下图;
注:
透照日期的放置按惯例排列6位数进行;如120525表示2012年5月25日;
7.6.2各种标记至少离焊缝5mm,各种标记应符合6.1要求,每次摄片在标记带上必须有符合7.5要求的像质计;
8.贴片、对位、屏蔽的要求:
8.1贴片时应保证整个胶片暗盒于被检焊缝紧贴;
8.2定向曝光时,射线束的中心应对准透照区中心,并使强度最大的射线束覆盖透照区焊缝;
8.3摄片时应采用铅光栅、铅遮板、铅衬板等,照射场内不应堆放杂物,以防止散乱射线影响底片质量;为检查散射线的影响程度,当底片上“B”出现较淡的影响时,说明散射线影响较重,应予复照;
9.透照方式和操作顺序;
9.1应根据工件特点上和技术条件的要求选择适宜的透照方式;应优先选用单壁透照法,在单壁透照不能实施时方可采用双壁透照;典型透照方式见下图:
(A)(B)
(A)纵缝透照法(B)环缝外透法
(C)双壁单影法(D)双壁双影法
9.2透照时射线束中心一般应垂直指向透照区中心,需要时也可选用有利发现缺陷的方向透照;
9.3对于100mm<D0≤400mm的环向对接接头(包括曲率相同的曲面焊接接头),A级,AB级允许采用K≤1.2;
9.4小口径管采用双壁透照时,当同时满足T(壁厚)≤8mm;g(焊缝宽度)≤D0/4时应采用倾斜透照方式椭圆成像;椭圆成像时,应控制映象的开口宽度(上下焊缝投影最大间距)在1倍焊缝宽度左右;不满足上述条件时或椭圆成像有困难时可采用垂直透照方式重叠成像;
9.5小径管环向对接焊接接头100%检测透照时;采用倾斜透照椭圆成像时,当T/D0≤0.12时;相隔90°透照2次;T/D0>0.12时,相隔120°或60°透照3次;垂直透照重叠成像时,一般应相隔120°或60°透照3次;
9.6操作顺序:
9.6.1按“X光机安全操作规程”做好开机前检查工作和必要的“训机”;
9.6.2开机后,升高压前预热3-5分钟,再根据曝光规范缓慢升压,再升mA至规定值,在时间到前15秒,应缓慢降mA和KV值至结束;
9.6.3透照结束不能立即切断电源,至少冷却5分钟后方可切断电源;
9.6.4透照人员在透照结束,应做好原始记录和摄片定位图,;并应在原始记录上签名和签署检测日期;
10.暗室处理
10.1显定影液均应与所用胶片厂推荐的配方相符,配制好放置24小时后,方可使用;
10.2显定影液使用温度应严格控制在20℃±2℃范围内;
10.3显影时间为5-8分钟,胶片应在显影液重不断摆动,显影结束应在清水(或停影液)中停显30″后方可进行定影,定影时间不少于15分钟,定影结束应在流水中冲洗不少于30″,水洗结束后进行脱水烘(晾)干处理;
10.4暗室操作人员应严格按暗室处理的有关操作规程进行操作,并要将发现的不符合