专业技术实习报告加热炉串级控制系统设计.docx
《专业技术实习报告加热炉串级控制系统设计.docx》由会员分享,可在线阅读,更多相关《专业技术实习报告加热炉串级控制系统设计.docx(17页珍藏版)》请在冰豆网上搜索。
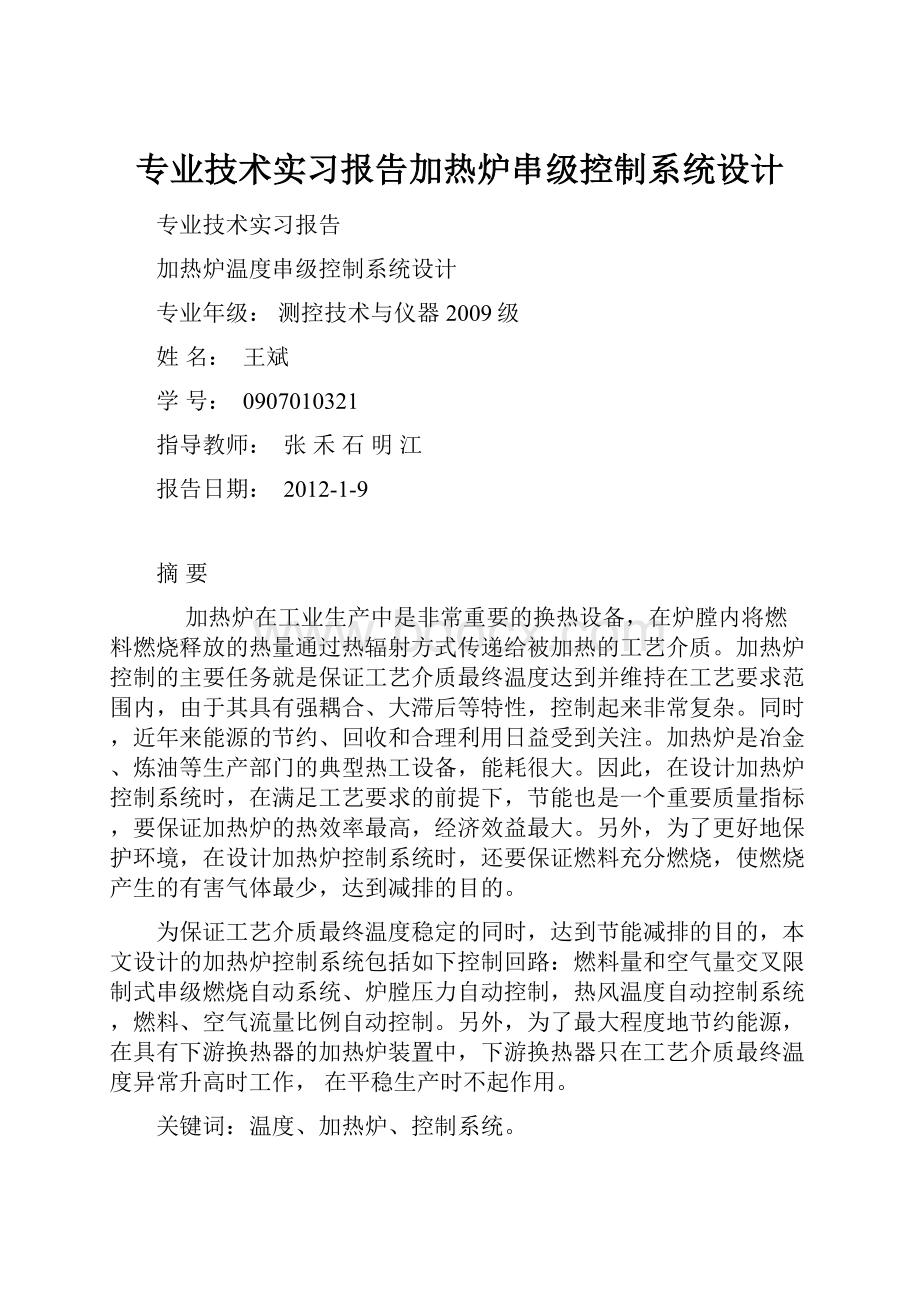
专业技术实习报告加热炉串级控制系统设计
专业技术实习报告
加热炉温度串级控制系统设计
专业年级:
测控技术与仪器2009级
姓名:
王斌
学号:
0907010321
指导教师:
张禾石明江
报告日期:
2012-1-9
摘要
加热炉在工业生产中是非常重要的换热设备,在炉膛内将燃料燃烧释放的热量通过热辐射方式传递给被加热的工艺介质。
加热炉控制的主要任务就是保证工艺介质最终温度达到并维持在工艺要求范围内,由于其具有强耦合、大滞后等特性,控制起来非常复杂。
同时,近年来能源的节约、回收和合理利用日益受到关注。
加热炉是冶金、炼油等生产部门的典型热工设备,能耗很大。
因此,在设计加热炉控制系统时,在满足工艺要求的前提下,节能也是一个重要质量指标,要保证加热炉的热效率最高,经济效益最大。
另外,为了更好地保护环境,在设计加热炉控制系统时,还要保证燃料充分燃烧,使燃烧产生的有害气体最少,达到减排的目的。
为保证工艺介质最终温度稳定的同时,达到节能减排的目的,本文设计的加热炉控制系统包括如下控制回路:
燃料量和空气量交叉限制式串级燃烧自动系统、炉膛压力自动控制,热风温度自动控制系统,燃料、空气流量比例自动控制。
另外,为了最大程度地节约能源,在具有下游换热器的加热炉装置中,下游换热器只在工艺介质最终温度异常升高时工作,在平稳生产时不起作用。
关键词:
温度、加热炉、控制系统。
第一章绪论
1.1引言
近年来,轧钢生产中所涌现的新技术、新工艺主要是围绕节约能源、降低成本、提高产品质量、开发新产品所进行的。
在节能降耗上,主要技术是:
连铸坯热送热装技术、薄板坯连铸连轧技术、先进的节能加热炉等;在提高产品性能、质量上,主要技术是:
TMCP技术、高精度轧制技术、先进的板形、板厚控制技术、计算机生产管理技术等;在技术装备上,主要是大型化、连续化、自动化,即热轧带钢、冷轧带钢的连续化,实现无头轧制、酸轧联合机组、连续退火及板带涂层技术等。
这些技术的应用可极大地提高产品的竞争能力。
以节能降耗为目标的新技术。
加热炉炉温的控制直接影响到生产质量和能耗的多少。
所以加热炉控制系统的优化控制方案有待解决!
第2章控制系统设计
2.1生产工艺及加热炉简介
一、加热炉简介
1、加热炉分类
在冶金工业中,加热炉习惯上是指把金属加热到轧制成锻造温度的工业炉,包括有连续加热炉和室式加热炉等。
金属热处理用的加热炉另称为热处理炉。
初轧前加热钢锭或使钢锭内部温度均匀的炉子称为均热炉。
广义而言,加热炉也包括均热炉和热处理炉。
连续加热炉包括推钢式炉、步进式炉、转底式炉、分室式炉等连续加热炉,但习惯上常指推钢式炉。
连续加热炉多数用于轧制前加热金属料坯,少数用于锻造和热处理。
主要特点是:
料坯在炉内依轧制的节奏连续运动,炉气在炉内也连续流动;一般情况,在炉料的断面尺寸、品种和产量不变的情况下,炉子各部分的温度和炉中金属料的温度基本上不随时间变化而仅沿炉子长度变化。
2、加热炉的结构
按炉温分布,炉膛沿长度方向分为预热段、加热段和均热段;进料端炉温较低为预热段,其作用在于利用炉气热量,以提高炉子的热效率。
加热段为主要供热段,炉气温度较高,以利于实现快速加热。
均热段位于出料端,炉气温度与金属料温度差别很小,保证出炉料坯的断面温度均匀。
用于加热小断面料坯的炉子只有预热段和加热段。
习惯上还按炉内安装烧嘴的供热带划分炉段,依供热带的数目把炉子称为一段式、二段式,以至五段式、六段式等。
50~60年代,由于轧机能力加大,而推钢式炉的长度受到推钢长度的限制不能太长,所以开始在进料端增加供热带,取消不供热的预热段,以提高单位炉底面积的生产率。
用这种炉子加热板坯,炉底的单位面积产量达900~1000公斤/(米2·时),热耗约为(0.5~0.65)×106千卡/吨。
70年代以来,由于节能需要,又由于新兴的步进式炉允许增加炉子长度,所以又增设不供热的预热段,最佳的炉底单位面积产量在600~650公斤/(米2·时),热耗约为(0.3~0.5)×106千卡/吨。
3、加热炉工作方式
在锻造和轧制生产中,钢坯一般在完全燃烧火焰的氧化气氛中加热。
采用不完全燃烧的还原性火焰(即“自身保护气氛”)来直接加热金属,可以达到无氧化或少氧化的目的。
这种加热方式称为明火式或敞焰式无氧化加热,成功地应用于转底式加热炉和室式加热炉。
4、加热炉节能方式
加热炉对钢锭进行加热时的温度高,烟气带走了大量的高温热量,造成白白浪费,热利用率较低,如果使用蜂窝陶瓷蓄热体可以达到余热回收的目的,但一次性投入大,切换机构多,维修成本高;另外在切换过程中也带走了相当多被烧嘴吹出但未燃烧的燃气,造成能源严重流失。
而使用换热器则可弥补蜂窝陶瓷这方面的不足,且投资少、无切换机构、免维修。
如果使用金属换热器,由于材质的限制,抗氧化能力差,不能在高温下长期使用,余热回收率低。
如烟道温度达到800度以上,金属换热器非常容易被高温损坏,无法达到余热回收的目的。
2.2控制系统的设计思想和总体方案
2.2.1控制系统的设计思想
串级控制系统采用两套检测变送器和两个调节器,前一个调节器的输出作为后一个调节器的设定,后一个调节器的输出送往调节阀。
前一个调节器称为主调节器,它所检测和控制的变量称主变量(主被控参数),即工艺控制指标;后一个调节器称为副调节器,它所检测和控制的变量称副变量(副被控参数),是为了稳定主变量而引入的辅助变量。
整个系统包括两个控制回路,主回路和副回路。
副回路由副变量检测变送、副调节器、调节阀和副过程构成;主回路由主变量检测变送、主调节器、副调节器、调节阀、副过程和主过程构成。
2.2.2控制系统的设计方案
一、加热炉控制系统的基本组成
1、炉膛压力自动控制
炉膛压力直接影响钢坯的加热质量、炉温分布、燃料消耗及炉体寿命。
一般加热炉控制炉膛为微正压状态,以使炉子既不吸入冷空气,炉气也不外溢。
炉膛压力控制是靠控制器升降烟道闸板,即改变烟囱抽力来实现的,系统串入阻尼器以提高其稳定性,又由于炉膛压力数值小,故取压管用较粗的管子,且从取压装直至变送器之间的导压管设置了补偿导管。
有些加热炉在烟道中设置两组调节翻版,其中一组有比值设定器,可根据数值来调节比值,保证烟道内气流均匀。
2、热风温度自动控制系统
采用控制放风量的方法以保持热风温度在以最大限制范围内。
系统还设有废气温度控制系统,他用热电偶测量废气温度,通过控制器动作冷风阀向烟囱里加入冷风以保证废气温度不高于换热器允许温度,和防止烧坏炉子设备。
3、燃料、空气流量比例自动控制
在加热炉操作中,保证燃烧在最佳空燃比条件下进行是必不可少的,空燃比过高使钢坯表面氧化,损失增加,空燃比过低,燃料不完全燃烧,产生黑烟,浪费燃料和污染环境。
燃烧控制有三种方式:
一是并列方式。
即温度变化时,同时改变燃料和空气流量,这种方式能防止温度变化时产生的黑烟;二是燃料先行方式,这种方式当燃料控制回路出现扰动时,空气能随动修正,防止黑烟的产生,但当温度低时,控制的瞬间燃料增加,空气尚代跟上时,这将产生黑烟;三是空气先行方式。
这种方式则刚好相反。
目前使用性能最佳的是交叉限制式串级燃烧控制系统。
其特点是利用最大、最小值选择器,当炉温低于设定值时,使系统为空气先行方式,而炉温高于设定值则为燃料先行方式,他可有效防止黑烟的产生。
二、设计方案
1、燃料控制系统流程
如图2—1所示,以炉内温度为主被控对象,燃料油流量为副被控对象的串级控制系统。
该控制系统的副回路由燃料油流量控制回路组成,因此,当扰动来自燃料油上游侧的压力波动时,因扰动进入副回路,所以,能迅速克服该扰动的影响。
由于炉内温度的控制不是单一因素所能实现的,所以,还要对空气的流量进行控制。
空气的控制直接影响炉内燃烧的状况,不仅影响炉温,还直接影响了能源的利用率和环境的污染。
所以,对空气的控制很有必要,其原理和燃料控制相同。
图2—1燃料串级控制系统流程
2、燃料、空气流量比例自动控制系统
考虑到空气、燃料的比例合理性,基于各方面因素的考虑,该设计只针对燃料、空气流量比例自动控制系统做以下说明。
其控制系统流程图如下图所示。
图2—2交叉限制式串级燃烧自动系统
交叉限制式串级燃烧自动系统的工作原理,是利用最大、最小值选择器,当炉温低于设定值时,使系统为空气先行方式,而炉温高于设定值则为燃料先行方式,他可有效防止黑烟的产生。
既节约能源减少污染,有保证了生产质量。
2.3控制回路的参数选择
副回路的选择是确定副回路的被控参数,串级系统的特点主要来源于它的副回路,副回路的参数选择一般应遵行下面几个原则:
(1)主、副参数有对应关系。
即通过调整副参数能有效地影响主参数,副参数的变化应反映主参数的变化趋势、并在很大程度上影响主参数;其次,选择的副参数必须是物理上可测的;另外,由副参数所构成的副回路,调节通道尽可能短,调节过程时间常数不能太大,时间滞后小,以便使等效过程时间常数显著减小,提高整个系统的工作频率,加快控制过程反应速度,改善系统控制品质。
(2)副参数的选择必须使副回路包含变化剧烈的主要干扰,并尽可能多包含一些干扰。
在选择副参数时一定要把主要干扰包含在副回路中,并力求把更多的干扰包含在副回路中,但也不是副回路包含的干扰越多越好,因为副回路包含的干扰越多,其控制通道时间常数必然越大,响应速度变慢,副回路快速克服干扰的能力将受到影响。
所以在选择副参数时,应在副回路反应灵敏与包含较多干扰之间进行合理的平衡。
(3)副参数的选择应考虑主、副回路中控制过程的时间常数的匹配,以防“共振”的发生。
在串级控制系统中,主、副回路中控制过程的时间常数不能太接近,一方面是为了保证副回路具有较快的反应能力,另一方面由于在串级控制系统中,主、副会理密切相关,如果主、副回路中的时间常数比较接近,系统一旦受到干扰,就有可能产生“共振”,使控制质量下降,甚至使系统因震荡而无法工作。
在选择副参数时,应注意使主、副回路中控制过程的时间常数之比为3~10,以减少主、副回路的动态联系、避免“共振”。
(4)应注意工艺上的合理性和经济性。
2.4主、副调节器调节规律的选择
2.4.1调节规律分析
(1)比例增益(P)
一方面,我们希望目标信号和反馈信号无限接近,即差值很小,从而满足调节的精度:
另一方面,我们又希望调节信号具有一定的幅度,以保证调节的灵敏度。
解决这一矛盾的方法就是事先将差值信号进行放大。
比例增益P就是用来设置差值信号的放大系数的。
任何一种变频器的参数P都给出一个可设置的数值范围,一般在初次调试时,P可按中间偏大值预置.或者暂时默认出厂值,待设备运转时再按实际情况细调。
(2)积分时间(I)
如上所述.比例增益P越大,调节灵敏度越高,但由于传动系统和控制电路都有惯性,调节结果达到最佳值时不能立即停止,导致“超调”,然后反过来调整,再次超调,形成振荡。
为此引入积分环节I,其效果是,使经过比例增益P放大后的差值信号在积分时间内逐渐增大(或减小),从而减缓其变化速度,防止振荡。
但积分时间I太长,又会当反馈信号急剧变化时,被控物理量难以迅速恢复。
因此,I的取值与拖动系统的时间常数有关:
拖动系统的时间常数较小时,积分时间应短些;拖动系统的时间常数较大时,积分时间应长些。
(3)微分时间(D)
微分时间D是根据差值信号变化的速率,提前给出一个相应的调节动作,从而缩短了调节时间,克服因积分时间过长而使恢复滞后的缺陷。
D的取值也与拖动系统的时间常数有关:
拖动系统的时间常数较小时,微分时间应短些;反之,拖动系统的时间常数较大时,微分时间应长些。
2.4.2调节规律的确定
在串级控制系统中,主,副调节器起的作用不同。
主调节器起定值控制作用,副调节器起随动控制作用,这是选择调节器规律的基本出发点。
主被控参数是工艺操作的主要指标,允许波动范围很小,一般要求无静差。
又由于温度的控制有明显的滞后性,因此,主调节器应选PID调节规律。
副被控参数的设置是为了克服主要干扰对主参数的影响,因而可以允许在一定范围的变化,并允许有静差。
为此,副调节器选择P调节规律。
2.5主、副调节器正、反作用方式的确定
在串级控制系统中,主、副调节器正、反作用方式的选择原则是使整个系统构成负反馈。
串级控制系统中,主、副调节器的正反作用的选择方法是:
首先根据工艺要求决定调节阀的气开、气关形式,并决定副调节器的正反作用;然后再依据主、副过程的正、反形式最终确定主调节器的正、反作用方式。
从生产工艺安全出发,燃料油调节阀选用气开式,即一旦出现故障或气源断气,调节阀应完全关闭,切断燃料油进入加热炉,确保设备安全。
对于副调节器,当炉膛温度升高时,测量信号增大、为保证副回路为负反馈,此时调节阀应关小,要求副调节器输出信号减小。
按照测量信号增大,输出信号减小的原则要求,副调节器应为反作用方式。
对于主调节器,当副参数升高时,主参数也升高,故主调节器应为反作用方式。
2.5主、副调节器选用
DDZ-III型仪表采用了集成电路和安全火花型防爆结构,提高了仪表精度、仪表可靠性和安全性,适应了大型化工厂、炼油厂的防爆要求。
III型仪表具有以下主要特点:
(1)采用国际电工委员会(IEC)推荐的统一信号标准,现场传输信号为DC4~20mA,控制室联络信号为DC1~5V,信号电流与电压的转换电阻为250
。
(2)广泛采用集成电路,仪表的电路简化、精度提高、可靠性提高、维修工作量减少。
(3)整套仪表可构成安全火花型防爆系统。
DDZ-III型仪表室按国家防爆规程进行设计的,而且增加了安全栅,实现了控制室与危险场所之间的能量限制于隔离,使仪表能在危险的场所中使用。
DDZ-III型PID调节器的结构框图如图2-1。
主要由输入电路、给定电路、PID运算电路、手动与自动切换电路、输出电路和指示电路组成。
调节器接收变送器送来的测量信号(DC4~20mA或DC1~5V),在输入电路中与给定信号进行比较,得出偏差信号,然后在PD与PI电路中进行PID运算,最后由输出电路转换为4~20mA直流电流输出。
图2-3给出了温度变送器的原理框图,虽然温度变送器有多个品种、规格,以配合不同的传感元件和不同的量程需要,但他们的结构基本相同。
本设计采用DDZ-III型热电偶温度变送器
图2—3DDZ-III型调节器结构框图
2.6.2温度变送器
检测信号要进入控制系统,必须符合控制系统的信号标准。
变送器的任务就是将检测信号转换成标准信号输出。
因此,热电偶和热电阻的输出信号必须经温度变送器转换成标准信号后,才能进入控制系统,与调节器等其他仪表配合工作。
图2—4温度变送器原理框图
2.7调节阀的确定
由前文得,从生产工艺安全出发,燃料油调节阀选用气开式,即一旦出现故障或气源断气,调节阀应完全关闭,切断燃料油进入加热炉,确保设备安全为了保证。
调节阀按其工作能源形式可分为气动、电动和液动三类。
气动调节阀用压缩空气作为工作能源,主要特点是能在易燃易爆环境中工作,广泛地应用于化工、炼油等生产过程中;电动调节阀用电源工作,其特点是能源取用方便,信号传递迅速,但难以在易燃易爆环境中工作;液动调节阀用液压推动,推力很大,一般生产过程中很少使用。
故本设计采用了气动调节阀,且为气开形式。
2.8联锁保护
联锁保护系统由压力调节器、温度调节器、流量变送器、火焰检测器、低选器等部分组成。
当燃料管道压力高于规定的极限时,压力调节系统通过低选器取代正常工作的温度调节系统,此时出料温度无控制,自行浮动。
压力调节系统投入运行保证燃料管道压力不超过规定上限。
当管道压力恢复正常时,温度调节系统通过低选器投入正常运行,出料温度重新受到控制。
当进料流量和燃料流量低于允许下限或火焰熄灭时,便会发出双位信号,控制电磁阀切断燃料气供给量以防回火。
2.9PID参数整定和仿真
增量式PID控制算法公式如下:
在模拟控制系统中,控制器中最常用的控制规律是PID控制规律。
PID控制器是一种线性控制器,它根据给定值与实际输出值构成控制偏差。
PID控制规律写成传递函数的形式为
式中,
为比例系数;
为积分系数;
为微分系数;
为积分时间常数;
为微分时间常数;简单来说,PID控制各校正环节的作用如下:
(1)比例环节:
成比例地反映控制系统的偏差信号,偏差一旦产生,控制器立即产生控制作用,以减少偏差。
(2)积分环节:
主要用于消除静差,提高系统的无差度。
积分作用的强弱取决于积分时间常数
,
越大,积分作用越弱,反之则越强。
(3)微分环节:
反映偏差信号的变化趋势(变化速率),并能在偏差信号变得太大之前,在系统中引入一个有效的早期修正信号,从而加快系统的动作速度,减少调节时间。
实验过程
1、在MATLAB命令窗口中输入“simulink”进入仿真界面。
2、构建PID控制器:
(1)新建Simulink模型窗口(选择“File/New/Model”),在SimulinkLibraryBrowser中将需要的模块拖动到新建的窗口中,根据PID控制器的传递函数构建出如下模型:
图2.5PID控制器
各模块如下:
MathOperations模块库中的Gain模块,它是增益。
拖到模型窗口中后,双击模块,在弹出的对话框中将‘Gain’分别改为‘Kp’、‘Ki’、‘Kd’,表示这三个增益系数。
Continuous模块库中的Integrator模块,它是积分模块;Derivative模块,它是微分模块。
MathOperations模块库中的Add模块,它是加法模块,默认是两个输入相加,双击该模块,将‘ListofSigns’框中的两个加号(++)后输入一个加号(+),这样就改为了三个加号,用来表示三个信号的叠加。
Ports&Subsystems模块库中的In1模块(输入端口模块)和Out1模块(输出端口模块)。
(2)将上述结构图封装成PID控制器。
①创建子系统。
选中上述结构图后再选择模型窗口菜单“Edit/CreatSubsystem”
②封装。
选中上述子系统模块,再选择模型窗口菜单“Edit/MaskSubsystem”
③根据需要,在封装编辑器对话框中进行一些封装设置,包括设置封装文本、对话框、图标等。
本次试验主要需进行以下几项设置:
Icon(图标)项:
“Drawingcommands”编辑框中输入“disp(‘PID’)”,如下
左图示:
Parameters(参数)项:
创建Kp,Ki,Kd三个参数,如下右图示:
图2.6PID控制器
至此,PID控制器便构建完成,它可以像Simulink自带的那些模块一样,进行拖拉,或用于创建其它系统。
所需模块及设置:
Sources模块库中Step模块;Sinks模块库中的Scope模块;CommonlyUsedBlocks模块库中的Mux模块;Continuous模块库中的Zero-Pole模块。
Step模块和Zero-Pole模块设置如下:
图2.8PID控制器
3、构建好一个系统模型后,就以运行,观察仿真结果。
运行一个仿真的完整过程分成三个步骤:
设置仿真参数、启动仿真和仿真结果分析。
选择菜单“Simulation/ConfiurationParameters”,可设置仿真时间与算法等参数,如下图示:
其中默认算法是ode45(四/五阶龙格-库塔法),适用于大多数连续或离散系统。
4、双击PID模块,在弹出的对话框中可设置PID控制器的参数Kp,Ki,Kd:
5.对PI参数进行整定:
(1)Kp=8.5,Ki=5.3,Kd=3.4
(2)Kp=4.5,Ki=5.3,Kd=3.4
结论:
Ki和Kd保持不变,改变Kp,根据这两个图可以得出P越大调节时间越快,
所以选KP=8.5
(3)Kp=8.5,Ki=2.3,Kd=3.4
结论:
保持Kp和Kd不变,改变Ki,可以得出Ki越小超调量越小,越稳定。
(4)Kp=8.5,Ki=5.3,Kd=2.4
结论:
Kp和Ki保持不变,Kd改变,可以得出,Kd越大调节时间越快。
(5)经过多次仿真比较,可发现当Kp=8.5,Ki=2.3时的参数比较适合,调节时间快且超调量小,更稳定可靠。
故本设计采用Kp=8.5Ki=2.3的PI调节。
第三章结束语
炼钢过程控制系统从最初的建立投入到目前,经过了近7年的发展,从原来的简单数据收集,到现在的模型大量应用于生产;通过各种系统功,能的不断完善促进了钢厂相关部门管理能力的提,升设备控制精度得到稳步提高,炼钢过程控制系统在迅猛的发展,技术创新,是炼钢过程控制系统发展的推动力。
在设计过程中,从方案设计到方案确定,都经过了严谨的思考,回路的设计,调节器的正反作用的确定,被控参数的选择,使系统能够达到设计目的。
在设计中,遇到了许多困难,老师对该论文从开始的题目介绍,构思到最后定稿的各个环节给予细心指引与教导,同时,其他的同学,在设计的过程中曾耐心给与帮助,使我得以最终完成毕业论文设计。
通过这次设计,我对过程控制系统在工业中的运用有了深入的认识,对过程控制系统设计步骤、思路、有一定的了解与认识。
我学到了控制系统的设计方法和步骤,拓展了知识面,了解了工业工程中控制系统起到的重要作用。
参考文献
[1]张根宝.工业自动化仪表与过程控制.西北工业大学出版社.2003.8
[2]潘永湘,杨延西,赵跃.过程控制与自动化仪表[M].机械工业出版社.2008.5
[3]侯志林.[M].过程控制与自动化仪表.机械工业出版社.2000.1
[4]俞金寿,孙自强.过程控制系统.机械工业出版社.2008.8
[5]施仁,刘文江,郑辑光.自动化仪表与过程控制.电子工业出版社.2003.3
[6]中国自动化学会ASEA办公室组编.冶金工业自动化.机械工业出版社,2007.3
[7]周庆海,翁维勤合编.过程控制系统工程设计,化学工业出版社,1992.12第1版
[8]GB2625-81过程检测和控制流程图用图形符号和文字代号
[9]GBJ93-86工业自动化仪表工程施工及验收规范