转炉煤气干法.docx
《转炉煤气干法.docx》由会员分享,可在线阅读,更多相关《转炉煤气干法.docx(12页珍藏版)》请在冰豆网上搜索。
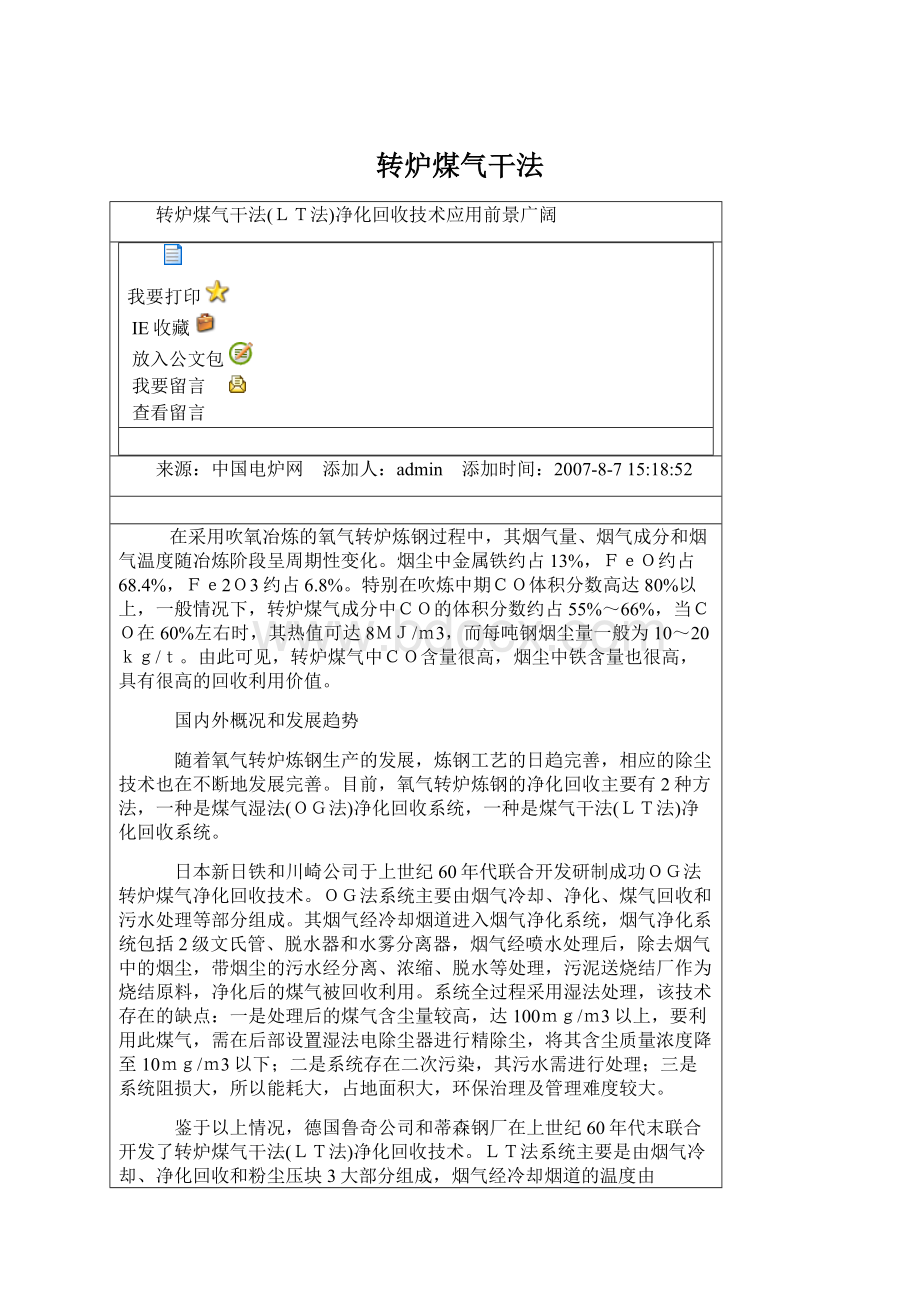
转炉煤气干法
转炉煤气干法(LT法)净化回收技术应用前景广阔
我要打印
IE收藏
放入公文包
我要留言
查看留言
来源:
中国电炉网 添加人:
admin 添加时间:
2007-8-715:
18:
52
在采用吹氧冶炼的氧气转炉炼钢过程中,其烟气量、烟气成分和烟气温度随冶炼阶段呈周期性变化。
烟尘中金属铁约占13%,FeO约占68.4%,Fe2O3约占6.8%。
特别在吹炼中期CO体积分数高达80%以上,一般情况下,转炉煤气成分中CO的体积分数约占55%~66%,当CO在60%左右时,其热值可达8MJ/m3,而每吨钢烟尘量一般为10~20kg/t。
由此可见,转炉煤气中CO含量很高,烟尘中铁含量也很高,具有很高的回收利用价值。
国内外概况和发展趋势
随着氧气转炉炼钢生产的发展,炼钢工艺的日趋完善,相应的除尘技术也在不断地发展完善。
目前,氧气转炉炼钢的净化回收主要有2种方法,一种是煤气湿法(OG法)净化回收系统,一种是煤气干法(LT法)净化回收系统。
日本新日铁和川崎公司于上世纪60年代联合开发研制成功OG法转炉煤气净化回收技术。
OG法系统主要由烟气冷却、净化、煤气回收和污水处理等部分组成。
其烟气经冷却烟道进入烟气净化系统,烟气净化系统包括2级文氏管、脱水器和水雾分离器,烟气经喷水处理后,除去烟气中的烟尘,带烟尘的污水经分离、浓缩、脱水等处理,污泥送烧结厂作为烧结原料,净化后的煤气被回收利用。
系统全过程采用湿法处理,该技术存在的缺点:
一是处理后的煤气含尘量较高,达100mg/m3以上,要利用此煤气,需在后部设置湿法电除尘器进行精除尘,将其含尘质量浓度降至10mg/m3以下;二是系统存在二次污染,其污水需进行处理;三是系统阻损大,所以能耗大,占地面积大,环保治理及管理难度较大。
鉴于以上情况,德国鲁奇公司和蒂森钢厂在上世纪60年代末联合开发了转炉煤气干法(LT法)净化回收技术。
LT法系统主要是由烟气冷却、净化回收和粉尘压块3大部分组成,烟气经冷却烟道的温度由1450℃左右降至800~1000℃,然后进入烟气净化系统。
烟气净化系统由蒸发冷却器和圆筒型电除尘器组成,烟气温度通过蒸发冷却器后降至180~200℃,同时通过调质处理,降低了烟尘的电阻率,收集了粗粉尘。
烟气经过这一初步处理后,进入圆筒型电除尘器,进行进一步净化,使其含尘质量浓度降至10mg/m3以下,从而达到最佳的除尘效率。
蒸发冷却器和圆筒型电除尘器捕集的粉尘,经输送机送到压块站,在回转窑中将粉尘加热到500~600℃,采用热压块的方式将粉尘压制成型,成型的粉块可直接用于转炉炼钢。
LT法与OG法相比的主要优点:
一是除尘净化效率高,粉尘质量浓度降至10mg/m3以下;二是该系统全部采用干法处理,不存在二次污染和污水处理;三是系统阻损小,煤气发热值高,回收粉尘可直接利用,降低了能耗;四是系统简化,占地面积小,便于管理和维护。
因此,LT法干法除尘技术比OG法湿法除尘技术有更高的经济效益和环境效益,从而获得世界各国的普遍重视和采用。
LT法净化回收技术在国际上已被认定为今后的发展方向,它可以部分或完全补偿转炉炼钢过程的全部能耗,有望实现转炉无能耗炼钢的目标,另外,从更加严格的环保要求和节能要求看,由于OG法净化回收系统存在着较多的缺点,它将逐渐被LT法净化回收系统取代。
我国到目前为止,除宝钢三期工程转炉煤气净化回收系统采用引进的LT法净化回收技术之外,基本上都采用OG法净化回收系统,除尘效果均不够理想,影响用户对煤气的使用,因此许多厂家在系统后部另设置了湿式电除尘器进行精除尘,以保证含尘质量浓度降至10mg/m3以下。
国内许多钢铁公司已经意识到LT法净化回收技术的优越性。
莱芜钢铁公司2003年8月与德国鲁奇公司、西安重型机械研究所合作,建设120t转炉煤气干法净化回收系统,2004年投入使用,经济效益显著。
目前,包头钢铁公司和太原钢铁公司的转炉煤气干法(LT法)净化回收系统正在建设中,宝钢、攀钢、首钢和天铁等企业也准备采用此项技术。
市场需求及推广应用前景
我国自20世纪60年代发展氧气转炉以来,到1989年为止,已先后建设投产的转炉达137余座,转炉钢产量占全国钢产量的60%~70%,其中150t至300t大型转炉8座,产钢量占转炉的20%,50t到120t中型转炉17座,产钢量占转炉的24%,而小于50t的小型转炉达112座,占转炉钢产量的56%(尚未考虑近几年新建转炉项目)。
以上转炉一部分采用湿法净化回收系统,除尘系统大部分能耗高,转炉煤气回收率低,污水处理复杂,污泥均未合理地综合回收利用,而另一部分转炉根本没有转炉煤气净化回收装置。
我国在转炉煤气湿法(OG法)净化回收的技术上,已积累了丰富经验,在此基础上消化移植宝钢三期引进的转炉煤气干法(LT法)净化回收技术,加速我国转炉干法电除尘系统的开发,是当务之急。
随着我国工业的发展,能源的紧缺,钢材需求的矛盾日益突出,如果普遍推行转炉煤气干法(LT法)净化回收技术,全年除尘耗电可减少近3亿kW·h;若将转炉可回收的煤气与蒸汽都综合起来,折合成标准煤,每吨钢可回收35kg左右,可望实现低能或无能炼钢,更值得注意的是干法回收的粉尘,热压块成形后可直接返回转炉代替废钢或矿石作冷却剂,直接回收其金属铁,可增加年钢产量30万t。
因此,在我国转炉上积极推广转炉煤气干法(LT)净化回收技术具有很宽广的应用前景。
经济效益和社会效益分析
根据宝钢转炉煤气湿法净化回收系统及干法净化回收系统运行的经验,采用干法电除尘技术,每吨钢可节约电1.1kW·h,节水3t,并可回收10.5kg含铁75%以上的烟尘和相当于20L左右燃料油的优质煤气。
我国目前广泛采用的转炉湿式除尘系统,除宝钢外,一般大、中型转炉除尘吨钢耗电平均为6kW·h,小型转炉除尘耗电平均10~15kW·h。
转炉煤气的回收率很低,转炉除尘的污水处理复杂,污泥均未合理地综合利用。
如果1个年产300万t钢的大型氧气转炉炼钢车间由OG法改用LT法干式电除尘,假定它们回收的能量和烟尘相等,仅节电、节水和节约生产费用3项合计的年经济效益,按保守的估计也在1700万元以上。
其中:
节约工业用电900万元,节约工业用水132万元,节约生产费用750万元。
此外,含铁粉尘压球后代替转炉废钢和矿石也将是一笔可观的附加收入。
技术经济比较
以下引用德国鲁奇公司2座150t转炉为例,提供干法与湿法除尘的技术经济比较,对设计人员、用户选择除尘方法有一定的参考价值。
1 基本参数
氧气量 42000m3/h
转炉容量 150t
年钢产量 1.3×106t
冶炼周期性 40~50min
吹氧时间 16~17min
每天吹炼炉数 30炉
原始炉气量 94000m3/h
燃烧系数 0.1
烟气量 110000m3/h
出汽化冷却器温度 1000℃
2 除尘系统相应设备的主要技术数据对比
OG湿法除尘 LT干法除尘
降温文氏管 t=78℃ 蒸发冷却塔 t=150℃
ΔP=3.0kPa ΔP=100Pa
除尘文氏管 ΔP=12kPa 静电除尘器 ΔP=200Pa
出口烟尘质量浓度≤100mg/m3 出口烟尘质量浓度<10mg/m3
高压离心风机P=21kPa 单机轴流风机P=6.5kPa
N=1865kW N=610kW
------- 饱和冷却器
湿式除尘煤气含尘质量浓度10mg/m3 干式除尘煤气质量浓度10mg/m3
污水沉凝装置 干法输送储存装置
污泥脱水装置 干法成球压块装置
污泥干燥 -------
污泥返回烧结 沉块返回烧结
消耗指标:
每炉耗电1235kW 消耗指标:
每炉耗电335kW
每炉耗水70m3 每炉耗水25m3
经济比较见表1。
转炉除尘大趋势:
湿法转向干法
来源:
中国钢铁新闻网作者:
发布时间:
2008.08.27
改进转炉除尘方法势在必行
我国现有600多座转炉,年产钢超过4亿吨,节能减排潜力巨大。
目前我国绝大多数转炉采用较为落后的湿法除尘,是钢铁工业节能减排的薄弱环节。
湿法除尘的主要缺陷表现在以下6个方面:
一是部分转炉烟尘排放超标,即达不到、或不能稳定达到每立方米控制在100、50、或10毫克这一排放标准;
二是费水,平均吨钢耗新水0.5立方米,全国转炉炼钢年消耗新水近2亿立方米,年循环水量超过8000亿吨;
三是耗电,平均吨钢除尘耗电为15度,全国年耗电60亿度,造成严重浪费;
四是煤气净化和岗位卫生不达标,其回收煤气粉尘浓度标准是每立方米15毫克、岗位粉尘浓度标准是每立方米5毫克,这一标准有的转炉达不到;即使能达到的能源消耗也会很大;
五是煤气回收利用率低,吨钢的转炉煤气回收量平均仅为50立方米,这一回收量只有国外、或国内先进水平的50%,另外50%排放到了大气中,相当于全国每年少回收煤气200亿立方米,折合成动力煤高达4亿吨;
六是蒸汽回收利用率低,转炉吨钢回收蒸汽平均为50千克,这一回收量只有国外、或国内的先进水平的50%,相当于全国每年少回收2000万吨蒸汽;
可见,研究现有的转炉除尘技术,发现存在的问题及存在原因,从而确定正确的改进方法和发展方向是非常有意义的。
除了湿法除尘之外,我国还有少数转炉采用引进的OG湿法;LT干法;第四代OG湿法;以及2006年我国自主研发的高效节水型塔文半干法除尘。
应该承认,上述除尘技术的引进和吸收开发,对我国转炉炼钢节能减排、实现负能炼钢起到了积极的推动作用,但同时也必须清醒地认识到:
这些技术都存在问题、或有值得改进之处,已经不适应我国钢铁工业节能减排新的标准和目标要求。
存在的共性问题主要有以下3点:
1、转炉汽化冷却烟道出口烟气900-1000°C的显热没有得到回收利用;2、平均每吨钢还要消耗0.5吨的新水,全年消耗新水2亿吨;3、吹氧期只有50%的时间回收煤气,前烧、后烧期的可燃气体(CO含量≦35%、相当于高炉煤气热值)没有得到利用,全部放散燃烧。
除了以上共性问题之外,这几种技术还分别存在一些个性问题,现分别列举如下:
一是OG湿法的问题最多。
传统的OG湿法虽然也有多种结构形式,进行了多方面的改进,但始终没有解决两级文氏管的根本问题。
这种技术是日本发明的,但在日本20年前就已经淘汰,而在我国如今仍然是采用最广泛的技术。
这种技术存在太多的先天性问题,主要在以下方面:
1、高排放:
采用传统OG系统有些可以达到我国现在的每立方米100毫克的排放标准,但实际上有很多因素会导致其排放超标;如果把标准提高到每立方米50毫克,或者更高,那么就很少有能达到的企业,如果要达到这一排放标准,则需要更高的能源消耗;
2、高耗能:
这是由于文氏管的先天性能决定的,风机全压在高达25-28千帕的情况下仍然抽不净,还要配备庞大的高耗能进行二次除尘;
3、高耗水:
按照保守的估算,全国转炉炼钢每年使用循环水8000亿吨,这引起多方面的浪费:
首先运行费用平均每年达4000亿元,主要用于水处理药剂、电、设备维修费用;其次是投资浪费,平均每吨水每小时的投资就达25000元;最后是能源浪费;
4、高维修:
因除尘风机等设备频繁结垢,使维修量加大,从而影响生产。
二是饱和塔文(第四代OG湿法)使用的循环水更多。
与传统的OG湿法相比,饱和塔文的进步意义在于其改用饱和冷却塔来替代一文氏管,这样就使系统阻力有所降低,一定程度上缓解了排放,但这种改进并没有解决其它问题,反而要使用更多的循环水。
三是LT干法存在三大问题:
LT干法一直是我国清洁生产推广技术,因为存在多方面的问题一直进展不快;近几年随着国家节能减排、节水力度加大,有加速的趋势,但因为存在较多的问题仍然还限制着其快速推广。
这些问题包括以下几个方面:
1、环保不达标。
最主要的是排放达不到、或不能稳定达到设计的每立方米10毫克这一排放标准,有的甚至比湿法高,导致环保排放和煤气回收利用都有问题;
2、维修工作量大。
因为电除尘器结垢、腐蚀,蒸发冷却器结垢等原因,导致维修设备的工作量特别大,并且降低转炉作业率,有的厂甚至被迫采用备用整套除尘设备;
3、节水还不到位。
LT系统的煤气冷却仍然采用饱和冷却,还是需要大量的循环水。
从这个意义说,LT技术也是半干法,而不是全干法。
比较和采用不同的除尘技术,首先要从各炼钢厂实际情况考虑,更主要的是要从整个相关系统、而不是局部设备进行综合比较,比如采用传统的OG湿法、或新0G法,其单项投资可能少,但加上庞大的水处理系统、比较大的除尘风机、煤气二次净化,总投资就要高得多;而运行费用、高耗能、高维修则是更大的问题;
LT干法的方向是正确的,如果不超装;供氧严格按照设计执行;喷枪、电除尘设备、蒸发冷却塔能经常、定期清理,应该能达到设计的排放浓度。
LT干法在操作维修和管理方面都存在问题,比如选用、或使用不合格的喷枪等,也不能排除先天设计上的一些缺陷,该技术从1969年发明成功到现在30多年,我国引进也有10多年,其推广速度不快、全球仅不到100套,应该从某种程度上说明其存在的问题。
湿法向干法发展是大势所趋
通过对现有技术存在问题的分析,得出的结论是:
转炉除尘从湿法向干法发展是大势所趋,但这是一个漫长的发展过程,不可能在短期内实现。
在这一发展过程之间应该会有几个过渡阶段,而第一步就是采用高效塔文技术。
因为采用高效塔文设备,可以使循环水量比传统OG法和第四代OG法减少50%。
采用高效塔文设备系统阻力还可以减少4-6千帕。
这一效果可以从两方面加以利用:
其一,可以解决一次烟气、回收煤气粉尘浓度高的问题,使排放量达到≦50mg/Nm3;其二,如果粉尘排放已经达标,则可以调大二文氏管喉口,减少二次除尘风量,辅助采用喷雾等除尘技术,这样就可以减开、停建甚至停开高耗能的二次除尘设备;还可以调低风机转速,降低一次电耗。
在高温区则可以利用外排水,使转炉实现新水零消耗。
这些措施可以延长设备的使用寿命,减少维修量。
这样系统就可以很容易地进一步升级改造为干法。
转炉煤气干法除尘技术在国内钢厂的应用
2009-1-815:
41:
00来源:
作者:
网友评论0条点击查看
中国钢铁新闻网随着氧气转炉炼钢生产的发展及炼钢工艺的日趋完善,相应的除尘技术也在不断地发展完善。
目前,氧气转炉炼钢的净化回收主要有两种方法,一种是煤气湿法(OG法)净化回收系统,一种是煤气干法(LT法)净化回收系统。
日本新日铁和川崎公司于60年代联合开发研制成功OG法转炉煤气净化回收技术。
OG法系统主要由烟气冷却、净化、煤气回收和污水处理等部分组成,烟气经冷却烟道后进入烟气净化系统。
烟气净化系统包括两级文氏管、脱水器和水雾分离器,烟气经喷水处理后,除去烟气中的烟尘,带烟尘的污水经分离、浓缩、脱水等处理,污泥送烧结厂作为烧结原料,净化后的煤气被回收利用。
系统全过程采用湿法处理,该技术的缺点:
一是处理后的煤气含尘量较高,达100mg/Nm3以上,要利用此煤气,需在后部设置湿法电除尘器进行精除尘,将其含尘浓度降至10mg/Nm3以下;二是系统存在二次污染,其污水需进行处理;三是系统阻损大,能耗大,占地面积大,环保治理及管理难度较大。
鉴于以上情况,德国鲁奇公司和蒂森钢厂在60年代末联合开发了转炉煤气干法(LT法)除尘技术。
干法(LT法)除尘系统主要由蒸发冷却器、静电除尘器和煤气冷却器组成。
与OG法相比,LT法的主要优点是:
除尘净化效率高,通过电除尘器可直接将粉尘浓度降至10mg/Nm3以下;该系统全部采用干法处理,不存在二次污染和污水处理;系统阻损小,煤气发热值高,回收粉尘可直接利用,节约了能源;系统简化,占地面积小,便于管理和维护。
因此,干法除尘技术比湿法除尘技术有更高的经济效益和环境效益。
转炉煤气干法除尘技术在国际上已被认定为今后的发展方向,它可以部分或完全补偿转炉炼钢过程的全部能耗,有望实现转炉无能耗炼钢的目标。
另外,从更加严格的环保和节能要求看,由于湿法净化回收系统存在着能耗高、二次污染的缺点,它将随着时代的发展而逐渐被转炉煤气干法除尘系统取代,这是冶金工业可持续发展的要求。
该技术已获得世界各国的普遍重视和采用,到目前为止,转炉煤气干法除尘技术在德国、奥地利、韩国、澳大利亚、法国、卢森堡等国得到了应用,与此同时,美、英、日也开始采用该技术,应用总数已达40套以上。
自1994年上海宝钢第一次全套引进国外转炉煤气干法除尘系统起,我国就开始了对该技术的全面研究工作,并已将其列为“十五”计划中重点开发推广技术项目。
宝钢引进的两套250t转炉煤气干法除尘系统于1997年投运。
西安重型机械研究所在跟踪和研究该技术的基础上,于2001年10月对其进行了改造。
这是国内第一次对该技术的深入研究。
继此之后,山东莱芜钢铁公司2003年8月与德国鲁奇公司及西安重型机械研究所合作,共同建成了三套120t转炉煤气干法除尘系统,其主要设备是由西安重型机械研究所供货和安装的,2004年7月2日第一套干法除尘系统投运,第二、三套干法除尘系统相继于2004年8月29日、2005年1月2日投运。
目前三套干法除尘系统运行良好,而且均已通过验收。
继莱钢之后,包钢炼钢厂于2005年与德国鲁奇公司及西安重型机械研究所合作,为100t转炉移地改造建成了两套100t转炉煤气干法除尘系统,于2005年底两套全部顺利投运。
目前,西安重型机械研究所正在安装太钢新建150t不锈钢两套转炉煤气干法除尘系统。
转炉煤气干法除尘技术
简介转炉煤气干法除尘系统工艺流程为:
约1550℃的转炉烟气在ID风机的抽引作用下,经过烟气冷却系统(活动烟罩、热回收装置及汽化冷却烟道),使温度降至800~1200℃后进入蒸发冷却器。
蒸发冷却器内有若干个双介质雾化冷却喷嘴,对烟气进行降温、调质、粗除尘,烟气温度降低到150~200℃,同时约有40%的粉尘在蒸发冷却器的作用下被捕获,形成的粗颗粒粉尘通过链式输送机输入粗灰料仓。
经冷却、粗除尘和调质后的烟气进入圆筒形静电除尘器,烟气经静电除尘器除尘后含尘量降至10mg/m3以下。
静电除尘器收集的细灰,经过扇形刮板器、底部链式输送机和细灰输送装置排到细烟尘仓。
经过静电除尘器精除尘的合格烟气经过煤气冷却器降温到70~80℃后进入煤气柜,氧含量>2%的煤气通过火炬装置放散。
整套系统采用自动控制,与转炉的控制相结合。
转炉煤气干法除尘系统主要构成及技术特点
1 蒸发冷却器
转炉冶炼时,含有大量CO的高温烟气冷却后才能满足干法除尘系统的运行条件。
蒸发冷却器入口的烟气温度为850~1200℃,出口温度约为200℃才能达到静电除尘器的条件。
为此,采用若干个双流喷嘴调节最佳水量降温。
双流喷嘴的水量可根据进入蒸发冷却器内的干燥气体的热含量随时调整。
通入的蒸汽使水雾化成细小的水滴,水滴受烟气加热被蒸发,在汽化过程中吸收烟气的热量,从而降低烟气温度。
蒸发冷却器除了冷却烟气外,还可依靠气流的减速以及进口处水滴对烟尘的润湿将粗颗粒的烟尘分离出去,达到除尘的目的。
灰尘聚积在蒸发冷却器底部由链式输送机输出。
蒸发冷却器还有对烟气进行调节改善的功能,即在降低气体温度的同时提高其露点,改变粉尘比电阻,有利于在静电除尘器中将粉尘分离出来。
除了烟气冷却和调节以外,占烟气中总灰尘含量约40%的粗灰也在蒸发冷却器中进行收集。
2 静电除尘器
静电除尘器为圆筒形静电除尘器,它是转炉煤气干法除尘系统中的关键除尘设备,其主要技术特点为:
①优异的极配形式。
由于转炉煤气的含尘量较高,在进入电除尘器时,一般为40~55g/Nm3,而除尘器出口的排放浓度要求小于10mg/Nm3。
这就要求电除尘器具有非常高的除尘效率,而除尘效率高低的主要因素就取决于其极配设计的合理性。
该除尘器分为4个独立的电场,平行布置。
每个电场均采用了ZT24型阳极板,由于烟气温度较高,所以阳极板采用了一种耐温材料。
针对4个电场的先后顺序,阴极采用了不同的形式和材质。
通过对投运设备的检测,证明了该极配形式能够保证除尘效率。
②良好的安全防爆性能。
由于转炉煤气属于易燃易爆介质,对设备的强度、密封性及安全泄爆性提出了很高的要求。
该除尘设备采用了抗压的圆筒外形,而且在锥形进出口各装有可靠的泄爆装置,从而保证了除尘器长期运行的安全可靠性。
③除尘器内部的扇形刮灰装置。
电除尘器内部刮灰装置是电除尘器中非常重要的一部分,电除尘器排灰是否顺利,会影响到整个系统的正常运转。
该除尘器的刮灰装置采用齿轮带动弧形齿条传动,并采用干油集中润滑,保证了刮灰装置的顺利运行。
④耐高温链式输送机。
由于该除尘设备除尘效率高,所以有大量的灰需要即时输送出去。
设备采用了可靠的耐高温链式输送机进行输灰,确保输灰顺畅。
3 煤气冷却器
煤气冷却器在静电除尘器后主要起洗涤降温作用,把经过静电除尘器除尘的合格烟气(150~200℃)降温到70~80℃后排入煤气柜。
煤气冷却器内上部装有两层喷水系统,合格烟气从煤气冷却器下部进入顶部排出,从而达到降温作用。
4 控制系统
LT控制系统共分三个控制回路:
蒸发冷却器的温度控制、风机流量控制、切换站气体成分控制。
整个控制系统的关键是静电除尘器的控制,其性能特点是根据吹炼、停吹、振打等三种工作状态,进行火花跟踪控制、间歇供电、反电晕检测、峰值跟踪控制并提供各种保护功能。
按设定好的程序对电压和电流进行调节,以发挥最大的电流效率,确保安全生产。
蒸发冷却器的温度控制根据出入口烟气温度、流量调节喷水量,确保烟气出口温度在控制范围内。
烟气在汽化冷却和除尘装置中的流量由流量控制系统确定。
烟气流量可通过烟气流量调节器的输出信号控制,这种控制可通过改变风机的转速来实现,使炉口保持微正压。
汽化冷却烟道中的静压力是决定烟气流量调节的主要参数,另外对烟气流量调节起作用的影响参数是吹氧量和烟气量,在转炉正常作业中,1台计算机负责处理这三个参量并将此作为修正参量输给风机速度调节控制机构。
对于在炼钢过程中进行的加料作业,如矿石或石灰石,或者辅助作业,LT系统的烟气流量调节系统将根据给定的程序做出反应。
切换站气体成分控制是在规定的时间内根据烟气成分分析确定切换站的动作。
当烟气中CO含量大于规定值30%、氧气含量小于规定值2%时,回收烟气阀打开。
烟道转换所用阀门配有调节