激光切割质量控制.docx
《激光切割质量控制.docx》由会员分享,可在线阅读,更多相关《激光切割质量控制.docx(17页珍藏版)》请在冰豆网上搜索。
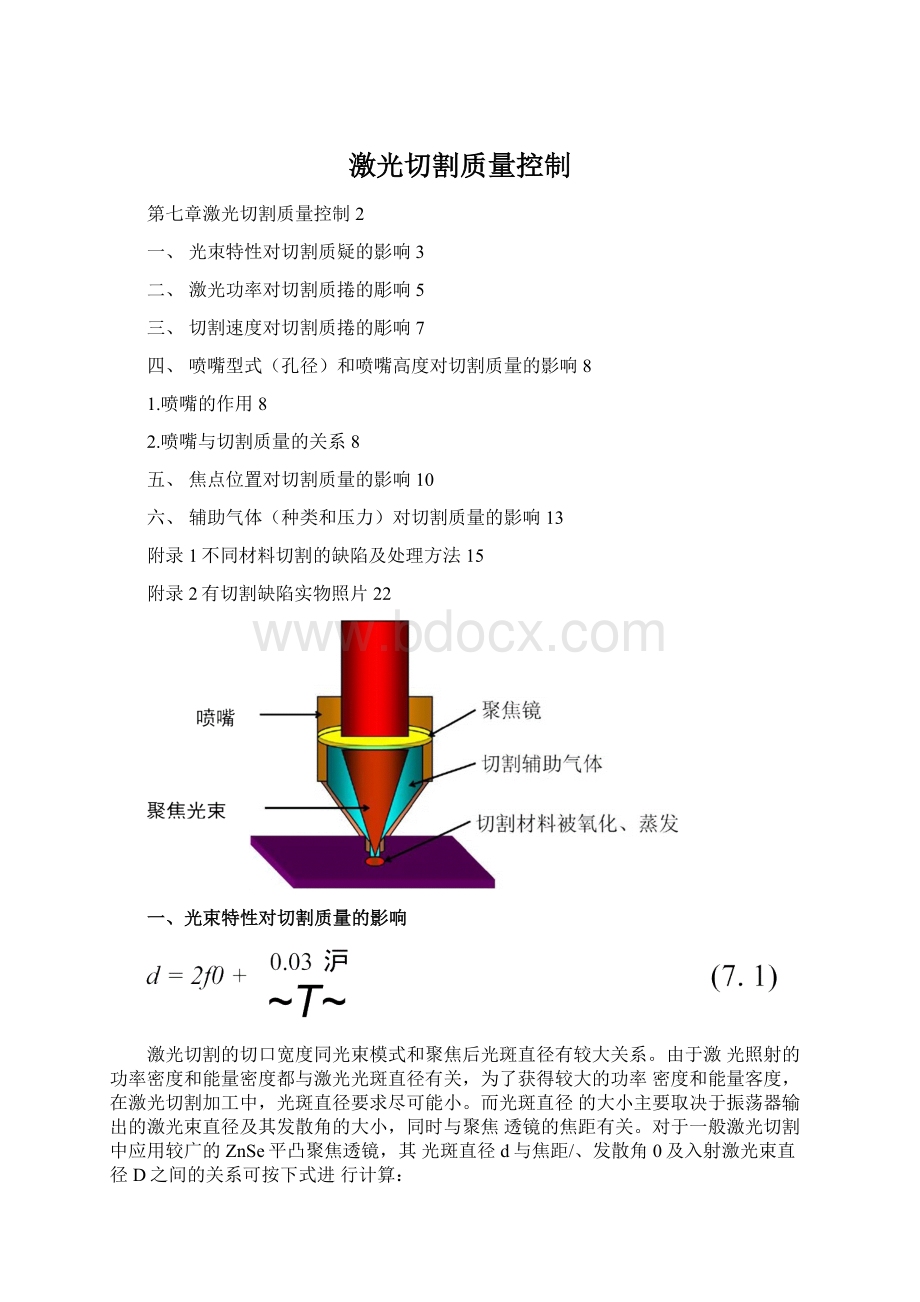
激光切割质量控制
第七章激光切割质量控制2
一、光朿特性对切割质疑的影响3
二、激光功率对切割质捲的彫响5
三、切割速度对切割质捲的彫响7
四、喷嘴型式(孔径)和喷嘴高度对切割质量的影响8
1.喷嘴的作用8
2.喷嘴与切割质量的关系8
五、焦点位置对切割质量的影响10
六、辅助气体(种类和压力)对切割质量的影响13
附录1不同材料切割的缺陷及处理方法15
附录2有切割缺陷实物照片22
一、光束特性对切割质量的影响
激光切割的切口宽度同光束模式和聚焦后光斑直径有较大关系。
由于激光照射的功率密度和能量密度都与激光光斑直径有关,为了获得较大的功率密度和能量客度,在激光切割加工中,光斑直径要求尽可能小。
而光斑直径的大小主要取决于振荡器输出的激光束直径及其发散角的大小,同时与聚焦透镜的焦距有关。
对于一般激光切割中应用较广的ZnSe平凸聚焦透镜,其光斑直径d与焦距/、发散角0及入射激光束直径D之间的关系可按下式进行计算:
由上式,若激光束本身的发散角较小,光斑的直径也会变小,就能获得好的切割效果。
减小透镜焦距/有利于缩小光斑直径,但/减小,焦深缩短,对于切割较厚板材,就不利于获得上部和下部等宽的切口,影响割缝质量;同时,/减小,透镜与工件的间距也缩小,切割时熔渣会飞溅黏附在透镜表面,影响切割的正常进行和透镜的实验寿命。
透镜焦长小,光束聚焦后功率密度高,但焦深受到限制。
它适用于薄板高速切割,只需保证保持透镜和工件间距恒定。
长焦透镜的聚焦光斑功率密较低,但其焦深大,可用来切割厚断面材料。
焦长短,聚焦光斑小;焦长长,聚焦光斑也大,焦深变化也如此。
当透镜焦长增加,使聚焦光斑尺寸增加1倍,即从Y到2Y时,焦深可随之增加到4倍,即从X到4X。
图1聚焦镜的聚焦作用
光束模式与它的聚焦能力有关,与机械刀具的刃口尖锐度有点相似。
最低阶模是TEMOO,光斑内能量呈高斯分布。
它几乎可把光束聚焦到理论上最小的尺寸,如几个微米直径,并形成尖的高能量密度。
激光模式示意如图3-3o而高阶或多模光束的能量分布较扩张,经聚焦的光斑较大而能量密度较低,用它来切割材料如同拿一把钝刀来进行切割。
A
I\.
图2光束能量分布模式
光束的模式越低,聚焦后的光斑尺寸越小,功率密度和能力密度越大,切割性能也就越好。
在低碳钢的切割场合,采用基模TEM00时的切割速度比采用TEM01模式时高出10%,而其产生的粗糙度Rz则要低10Um。
在最佳切割参数时,切割面的粗糙度Rz只有0.8Um。
因此,在金属材料的激光切割中,为了获得较高的切割速度和较好的切割质量,一般使用TEM00模式的激光。
二、激光功率对切割质量的影响
激光功率的大小直接影响所能切割钢板的厚度,能量越高,可切割材料厚度就越厚。
另外,它又影响着工件尺寸精度、切缝宽度、切割面的粗糙度和热影响区的宽度等。
在激光切割加工中,照射到工件上的激光功率密度Po(W/cm2)和能量密度E0(J/cm2)对激光切割过程起着重要的影响。
随着激光功率密度的提高,粗糙度降低。
当功率密度P。
达到某一值(3X106W/cm2左右)后,粗糙度Rz值不再减少。
激光功率越大,所能切割的材料厚度也越厚;但相同功率的激光,因材料不同,所能切割的厚度也不同。
表I给出了各种功率的co:
激光切割某些金属材料的实验最大厚度。
表1激光功率与金属最大切割厚度
co:
激光功率/w
最大切割厚度/mm
碳素钢
不锈钢
tn口乖
铜
黄铜
1500
12
9
3
1
2
1500
12
—
6
3
4
3000
22
12
—
5
5
4
对连续波输出的激光器来说,激光功率大小和模式都会对切割质量发生重要影响。
实际操作时,常常设置最大功率,以获得最快切割速度,提高生产效率,或用以切割较厚的材料。
理论上,我们要求激光器输出功率越大越好,但考虑激光器木身成本问题,激光器输出功率只有尽可能达切割机本身的最大值。
下图示出当激光功率不足时,切割低碳钢板产生的问题(未切透8、下部产生大量沾渣b及粗糙的断面C等)。
(a)(b)
(c)
图3激光功率对低碳钢切割质量影响
三、切割速度对切割质量的影响
切割速度对不锈钢板切割质量有很大影响,最佳的切割速度使切割面呈较平稳线条,光滑且下部无熔渣产生。
若切割速度过快,会导致钢板无法切透,引起火花飞溅,下半部产生熔渣,甚至烧伤透镜,这是因为切割速度过高,单位而积获得的能量减少,金属未能完全熔化;若切割速度过慢,则容易造成材料过熔,切缝变宽,热影响区增大,甚至引起工件过烧,这是因为切割速度过低,能量在切缝处积累,引起切缝变宽,熔化金属不能及时排出,便在钢板下表面形成沾渣。
产生如图3所示的切割缺陷。
切割面光洁下表面沾渣
断面粗糙切不透
图4切割速度对切割质量的影响
切割速度和激光输出功率一起决定被加工件的输入热量。
因此,由于切割速度的增减而引起的输入热量变化和加工质量的关系与输岀功率变化的情况相同。
一般情况下,调整加工条件时,若以改变输入热量为目的,不会同时改变输岀功率和切割速度,只需固定其中一方,变化另一方来调整加工质
量即可。
喷嘴形状(孔径)、喷嘴高度(喷嘴出口与工件表而之间的距离)等,均
会影响切割的效果。
图5气体从喷嘴喷出的情况
2.喷嘴与切割质量的关系
喷嘴出口孔中心与激光束的同轴度是影响切割质量优劣的重要因素之一,匸件越厚,影响越大。
当喷嘴发生变形或有熔渍时,将直接影响同轴度。
喷嘴形状和尺寸精度要求高,故喷嘴应小心保存,避免碰伤以免造成变形。
如果由于喷嘴的状况不良,从而需要要改变切割时的各项条件,那就不如更换新的喷嘴。
如果喷嘴与激光不同轴,将对切割质量产生如下影响。
a.对切割断面的影响
如图所示,当辅助气体从喷嘴吹出时,气量不均匀,出现一边有熔渍,
另一边没有的现象。
对切割3mm以下薄板时,它的影响较小,切割3mm以上时,影响较严重,有时无法切透。
b.对尖角的影响
工件有尖角或角度较小时,容易产生过熔现象,厚板则可能无法切割。
c.对穿孔的影响
穿孔不稳定,时间不易控制,对厚板会造成过熔,且穿透条件不易掌握。
对薄板影响较小。
五、焦点位置对切割质量的影响
焦点位置是指焦点距工件上表面的距离,以被加工材料表面为基准,工件表面以上为正,以下为负。
不锈钢
铝
镰合金
聚焦于表面之下
图7焦点位置
焦点位置直接影响切口宽度、坡度、切断面粗糙度及沾渣附着情况。
焦点位置不同,被加工物表面的光束直径及焦点深度即不同,进而引起加工沟的形状变化,影响加工沟内的加工气体及熔融金属的流动。
由于能量密度与4/兀扌(d为焦点光斑直径)成正比,所以d应尽可能的小,以便产生窄的切缝。
同时d和透镜的焦深成正比,焦深越小,d就越
小。
但切割有飞溅,透镜离工件太近容易被损坏,因此一般高功率激光切割
工业应用中广泛采用5"〜7.5"(127〜190mm)的焦距,实际焦点光斑直
径在0.1〜0.4mm之间。
因此控制焦点位置十分重要。
考虑到切割质量、
切割速度等因素,原则上厚度〈6mm的金属材料,焦点位置在表面;厚度>6mm的碳钢,焦点位置在表面之上;在切割不锈钢板时,焦点位置一般取在
表面以下。
通常切割厚度为4mm以下材料时,选用5〃聚焦镜。
飞行光路切割机切割近端和远端时光程长短不同,聚焦前的光束尺寸有一定差别。
入射光束的直径越大,焦点光斑的直径越小。
为了减少因聚焦前光束尺寸变化带来的焦点光斑尺寸的变化,可安装光路补偿系统,以保持近端和远端的光程不变。
激光束通过聚焦透镜,如图8所示。
图8光束通过透镜后形成的焦点
光斑直径由下式计算:
(2)
其中:
D——聚焦前光束直径;K——光束质量因子
此外,引起焦点位置对切割质量影响的另一个因素是聚焦深度,其计算公式为:
由以上分析知,在不出现沾渣的情况下,焦点位置越靠近钢板中部,切割面越平滑。
焦点位置的选取对不锈钢板切割质量有重要影响。
当焦点位置合适时,
切割下的材料熔化,而切割沿附近的材料并未熔化,渣滓即被吹走,形成无
沾渣的切缝,如下图(a)所示;当焦点位置滞后时,切割材料下端单位而积所吸收的能量减少,切割能量削弱,导致材料不能完全熔化被辅助气体吹走,以致未完全熔化的材料附着在切割板材下表面,呈前端尖锐且短小的沾渣,如下图(b)所示;当焦点位置超前时,切割材料下端单位面积所吸收的平均能量增大,导致所切割下的材料与切割沿附近的材料融化,并呈液体流动状,这时由于辅助气压及切割速度不变,所熔化的材料呈球状沾附在材料下表而,如下图(C)所示。
故在切割过程中可以通过观察沾渣形态来调
/////////,
(a)无沾渣(b)尖锐且短小沾渣(c)球状沾渣
图9焦点位置对沾渣的影响
图10不同焦点位置对切割质量的影响在实际生产中,要求激光切割不锈钢板焦点选取在材料表而或表面以下。
这正是因为扩大切割沟上部宽度,提高气体及熔融物的流动性,并使平滑而范围扩大,提高切割质量。
在切割过程中,对不同厚度的钢板,焦点位置并没有一个确定的值,当焦点位置取在钢板表面或表而以上时,由于钢板下部平均功率密度小,能量不足,易在下表面产生沾渣。
因此,激光切割不锈钢板时,焦点位置应该选取在材料内部。
以提高气体及熔融金属的流动性,保证了下部有足够的能量密度,使平滑面范围扩大。
具体数值通过实验确定。
六、辅助气体(种类和压力)对切割质量的影响
一般情况下,材料切割都需要使用辅助气体,主要涉及气体种类和压力。
气体种类、气压、喷嘴直径和几何结构影响边缘粗糙度和毛刺的生成,气体消耗取决于喷嘴直径和气压,切割气压在0.5MPa以下为低气压,2MPa以上为高压。
通常,辅助气体与激光束同轴喷出,可以保护聚焦透镜不被污染的同时,又可吹走切割区底部熔渣。
在一般切割中使用的气体种类有氧气、氮气和空气,不同切割材料要求不同辅助气体种类。
氧气主要用于开孔、碳钢和不锈钢板的高速切割、高反射材料的氧化切割;氧气作为辅助气体还可以使金属燃烧,利用其氧化反应热进行高效率的切割,但同时会在切割面上产生氧化膜;氮气主要用于不锈钢板的无氧化切割、镀锌板的无沾渣切割;空气主要用于铝和镀锌钢板的无沾渣切割、普通非金属切割。
辅助气体压力随使用气体的种类,切割材料材质,板厚及激光输岀形态(CW/脉冲)而不同。
辅助气体压力大小影响受粘渣附着、切割面质量、热影响区域大小等。
加工时喷嘴岀口气压条件如下表所示:
表2各切割工艺与辅助气体压力之间关系
开孔
(MPa)
薄碳钢02
切割(MPa)
厚碳钢0:
切割(MPa)
不锈钢n2
切割(MPa)
铝材Air
切割(MPa)
丙烯树脂净而切割(MPa)
0.02-0.05
0.l~0.3
0.05-0.1
0.6-1.5
0.6-1.0
<0.01
在确定辅助气体类型的前提下,气体压力大小是一个极为重要的因素,若辅助气体压力过高,会在工件表而形成涡流,削弱气流去除熔融材料的能力,造成切割面较粗糙,切缝较宽;若辅助气体压力过低,则吹不走切口处的熔融材料,在被切割材料背面产生沾渣。
因此,辅助气体压力存在一个最佳值。
当高速切割薄型材料时,需要较高的气体压力,以防切口背而产生沾渣;当材料厚度增加,或切割速度较慢时,则气体压力宜适当降低。
以不锈钢板激光切割为例,在其切割过程中,辅助气体可以冷却切缝邻近区域,减少热影响区,防止燃烧物损坏透镜。
另外,使用氮气作为辅助气体,它可以使熔融金属具有良好的流动性。
在实际加工中,因工艺参数不当而引起加工缺陷,原因复杂。
根据几十年的激光切割工艺经验,总结出切割缺陷的应对之策,以指导实际生产,很有意义。
详见附录。
附录1不同材料切割的缺陷及处理方法
碳钢:
用0:
切割
可能原因进给速率太高激光功率太低气压太低焦点太高
解决办法减小进给速率增加激光功率加大气压降低焦点
进给速率太高气压太低焦点太咼
进给速率太高气压太低气体不纯焦点太咼
减小进给速率加大气压降低焦点
减小进给速率
加大气压
使用更纯的气体
降低焦点
只在一边上有毛刺
喷嘴未对中喷嘴口有缺陷
对中喷嘴换喷嘴
立即停止切割,以免溶渣飞溅到聚焦镜上。
然后增加功率,减小进给速率
极化反射镜不合适,安装不正确或有缺陷极化反射镜安装在了偏转镜的位置
加工气体错误(NJ进给速率太高功率太低
气压太高喷嘴损坏了喷嘴直径太大材料不好立即停止切割,以防止溶渣飞溅到聚焦镜上。
改用0:
作为加工气体减小进给速率
增加功率减小气压
更换喷嘴
安装合适的喷嘴
使用表而平滑均匀的材料
无毛刺,牵引线倾斜切口在底部变得更狭窄
进给速率太高
减小进给速率
产生弹坑
气压太高
进给速雪太低
焦点太咼板材表而有锈加工的工件过热
材料不纯
减小气压
增加进给速率
降低隹占
使用iS召更好的材料
非常粗糙的切割表而
焦点太咼
气压太高进给速率太低
材料太热
不锈钢:
用咼压N?
切割
缺陷
可能原因
解决办法
产生点滴状的细小规则毛刺
焦点太低进给速率太高
抬咼焦点减小进给速率
两边都产生长的不规则的细丝状毛刺,大板材的表面变色
进给速雪太低
焦点太高
气压太低
材料太热
增加进给速率降低焦点加大气压冷却材料
只在切割边缘的一边产生长的不规则的毛刺
喷嘴未睾中
焦点太咼气压太低速度太低
对中喷嘴降低焦点加大气压提高速度
切割边缘发黄
氮气里含有氧气杂质
使用质量好的氮气
在直线截面上产生等离子体
光束分散
进给速率太高功率太低焦点太低
立即停止切割,以免溶渣飞溅到聚焦镜上减小进给速率
增加功率
抬NJ焦点
拐角处产生等离子体
进给速率太高功率太低焦点太低
角度公差太高调制太咼加速度太高
减小进给速率
增加功率
抬高焦点
减小角度公差减小调制或加速度
光束在开始处发散
加速度太高
焦点太低
熔化的材料未能排出
减小加速度抬高焦点穿圆孔
切口粗糙
喷嘴损坏了透镜脏了
更换喷嘴
清洗透镜,如果需要就更换
材料从上面排出
垄
功率太低进给速率过大气压太高
立即停止切割,以免溶渣飞溅到聚焦镜上增加功率
减小进给速率
减小气压
合金:
用高压N2切割
缺陷
可能原因
解决办法
两边都产生长的不月状毛刺,很难除去1111
U则的细丝
M
焦点太高气压太低进给速率太低
降低焦点加大气压增加进给速率
两边都产生长的不为朿1],可手工除去
U则的毛
■
进给速率太低
增加进给速率
切口粗糙
喷嘴直径太大喷嘴损坏了气压太髙
安装合适的喷嘴更换喷嘴
减小气压
细小规则的毛刺,的
1难除去
焦点太低进给速率太高
抬高焦点减小进给速率
在直线截而上产生等离子体
进给速率太高
减小进给速率
焦点太低
抬咼焦点
光束分散
进给速率太高
减小进给速率
拐角处产生等离子体
角度公差太高调制太咼加速度太高
减小角度公差减小调制或加速度
光束在开始处发散
进场速度太高焦点太低
减小进场速度抬高焦点
切口粗糙
喷嘴损坏了
更换喷嘴
材料从上而排出
功率太低进给速率过大
立即停止切割,以免溶渣飞溅到聚焦镜上
增加功率
减小进给速率
附录2有切割缺陷实物照片
1.不锈钢切割缺陷
切割速度太快
切割速度每次减少50-
200mm/min
•
焦点太低
焦点每次提高0.1-
0.2mm
氮气不纯
气管中存在氧气或空气
检查氮气的纯度.增加延时以清洁气管检查气路(不漏)
2.碳钢
缺陷
八、
可能的原因
排除
透镜中心不正喷嘴孔堵或不圆光路不正
检查透镜中心检查喷嘴状态检查光路,重新打靶
引入线长或引入方式不对线型不对
穿孔时间太长
切割时的热量太多
改正引入方式和引入长度
检查线型
穿孔时间W2秒减少占空比,每次2-3%
压力太高焦点太高功率太高材料不好
减小压力,每次0.1
bar
减小功率
检查透镜的焦点
功率低速度高压力低
增加功率降低速度增加压力
J
速度太高功率低
压力太低
减少速度增加占空比,每次5-10%
增加功率,每次
100W
逐步增加压力,每次
0.l~0.2bar
局部热量太多材料问题
改变切割顺序更换材料
压力太高速度太高
减少压力,每次
0.l~0.2bar
降低速度
焦点太低压力太低
提高焦点,每步
0.1-0.2mm增加压力,每步
0.1~0.2bar