冷挤压模具课程设计.docx
《冷挤压模具课程设计.docx》由会员分享,可在线阅读,更多相关《冷挤压模具课程设计.docx(22页珍藏版)》请在冰豆网上搜索。
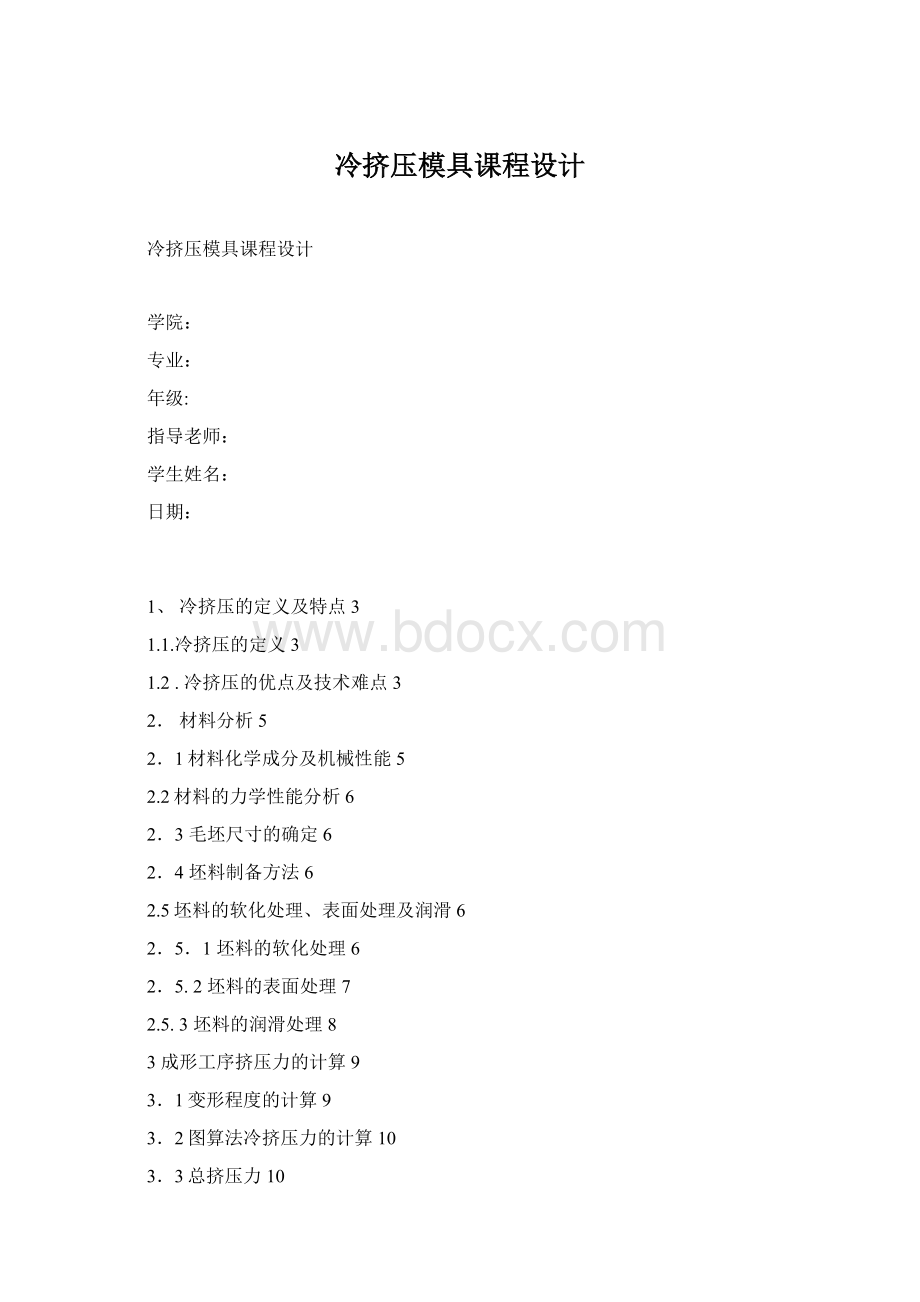
冷挤压模具课程设计
冷挤压模具课程设计
学院:
专业:
年级:
指导老师:
学生姓名:
日期:
1、冷挤压的定义及特点3
1.1.冷挤压的定义3
1.2.冷挤压的优点及技术难点3
2.材料分析5
2.1材料化学成分及机械性能5
2.2材料的力学性能分析6
2.3毛坯尺寸的确定6
2.4坯料制备方法6
2.5坯料的软化处理、表面处理及润滑6
2.5.1坯料的软化处理6
2.5.2坯料的表面处理7
2.5.3坯料的润滑处理8
3成形工序挤压力的计算9
3.1变形程度的计算9
3.2图算法冷挤压力的计算10
3.3总挤压力10
3.4挤压力经验公式的校正10
3.5压力机的选择(挤压设备的选择)10
4.模具设计11
4.1挤压模具设计的基本要求12
4.1.1模具设计时需考虑的安全措施12
4.1.2挤压模具的整体设计12
5.2凸、凹模的设计12
4.2.2凹模的设计和尺寸13
4.3凸、凹模固定圈的设计16
4.3.1凸模固定板16
4.3.2凹模固定板16
4.4压力垫板的设计17
4.5.顶出装置的设计17
4.6卸料板的设置18
4.7导向装置的设计(导柱导套的设计)19
4.8模架的设计20
5.模具材料的选择20
1、冷挤压的定义及特点
1.1.冷挤压的定义
冷挤压是精密塑性体积成形技术中的一个重要组成部分。
冷挤压是指在冷态下将金属毛坯放入模具模腔内,在强大的压力和一定的速度作用下,迫使金属从模腔中挤出,从而获得所需形状、尺寸以及具有一定力学性能的挤压件。
显然,冷挤压加工是靠模具来控制金属流动,靠金属体积的大量转移来成形零件的。
1.2.冷挤压的优点及技术难点
目前,冷挤压技术已在紧固件、机械、仪表、电器、轻工、宇航、船舶、军工等工业部门中得到较为广泛的应用,已成为金属塑性体积成形技术中不可缺少的重要加工手段之一。
二战后,冷挤压技术在国外工业发达国家的汽车、摩托车、家用电器等行业得到了广泛的发展应用,而新型挤压材料、模具新钢种和大吨位压力机的出现便拓展了其发展空间。
日本80年代自称,其轿车生产中以锻造工艺方法生产的零件,有30%~40%是采用冷挤压工艺生产的。
随着科技的进步和汽车、摩托车、家用电器等行业对产品技术要求的不断提高,冷挤压生产工艺技术己逐渐成为中小锻件精化生产的发展方向。
与其他加工工艺相比冷挤压有如下优点:
1)节约原材料。
冷挤压是利用金属的塑性变形来制成所需形状的零件,因而能大量减少切削加工,提高材料利用率。
冷挤压的材料利用率一般可达到80%以上。
2)提高劳动生产率。
用冷挤压工艺代替切削加工制造零件,能使生产率提高几倍、几十倍、甚至上百倍。
3)制件可以获得理想的表面粗糙度和尺寸精度。
零件的精度可达IT7~IT8级,表面粗糙度可达R0.2~R0.6。
因此,用冷挤压加工的零件一般很少再切削加工,只需在要求特别高之处进行精磨。
4)提高零件的力学性能。
冷挤压后金属的冷加工硬化,以及在零件内部形成合理的纤维流线分布,使零件的强度远高于原材料的强度。
此外,合理的冷挤压工艺可使零件表面形成压应力而提高疲劳强度。
因此,某些原需热处理强化的零件用冷挤压工艺后可省去热处理工艺,有些零件原需要用强度高的钢材制造,用冷挤压工艺后就可用强度较低的钢材替用。
5)可加工形状复杂的,难以切削加工的零件。
如异形截面、复杂内腔、内齿及表面看不见的内槽等。
6)降低零件成本。
由于冷挤压工艺具有节约原材料、提高生产率、减少零件的切削加工量、可用较差的材料代用优质材料等优点,从而使零件成本大大降低[3]。
冷挤压技术在应用中存在的难点主要有:
1)对模具要求高。
冷挤压时毛坯在模具中受三向压应力而使变形抗力显著增大,这使得模具所受的应力远比一般冲压模大,冷挤压钢材时,模具所受的应力常达2000MPa~2500MPa。
例如制造一个直径38mm,壁厚5.6mm,高100mm的低碳钢杯形件为例,采用拉延方法加工时,最大变形力仅为17t,而采用冷挤压方法加工时,则需变形力132t,这时作用在冷挤压凸模上的单位压力达2300MPa以上。
模具除需要具有高强度外,还需有足够的冲击韧性和耐磨性。
此外,金属毛坯在模具中强烈的塑性变形,会使模具温度升高至250℃~300℃左右,因而,模具材料需要一定的回火稳定性。
由于上述情况,冷挤压模具的寿命远低于冲压模。
2)需要大吨位的压力机。
由于冷挤压时毛坯的变形抗力大,需用数百吨甚至几千吨的压力机。
3)由于冷挤压的模具成本高,一般只适用于大批量生产的零件。
它适宜的最小批量是5~10万件。
4)毛坯在挤压前需进行表面处理。
这不但增加了工序,需占用较大的生产面积,而且难以实现生产自动化。
5)不宜用于高强度材料加工。
6)冷挤压零件的塑性、冲击韧性变差,而且零件的残余应力大,这会引起零件变形和耐腐蚀性的降低(产生应力腐蚀)[4]。
1.3冷挤压的发展趋势
1)随着能源危机的日趋严重,人们对环境质量将更加关注,加之市场竞争日益加剧,促使锻件生产向高效、高质、精化、节能节材方向发展。
因此用挤压成形等工艺手段所生产的精化锻件的产量,在市场竞争中将得到较大的发展。
2)汽车向轻型化、高速度、平稳性方向发展,对锻件的尺寸精度、重量精度及力学性能等都提出了较高的要求。
如轿车发动机用连杆锻件除对大小头之间的误差有要求外,对每件的重量误差也要求不大于八克。
新产品的高要求,将促进精化生产工艺的发展。
3)专业化、规模化的组织生产仍是冷挤压生产的发展方向和趋势。
在法国,以挤压成形工艺生产锻件的专业厂家1991-1994年全员劳动生产率,即每人生产挤压件的产量及产值,均高于一般生产模锻件或者自由锻件的厂家。
以1994年为例,专业厂家挤压件人均产量为51024KG,创产值775688法郎。
而同期一般性生产模锻件的厂家,其人均产量仅为39344KG,产值592384法郎,仅相当于挤压件专业生产厂家的77.1%和76.37%。
自由锻件生产厂与之相比则更低。
4)挤压专机将成为一种发展趋势。
随着中小型锻件的精化生产发展及冷挤压、温挤压工艺的推广应用,多工位冷挤压压力机、精压机及针对某种锻件而设计制造的专机会得到大力发展[7]。
2.材料分析
2.1材料化学成分及机械性能
材料牌号:
2A12
2A12,也叫做做LY12,相当于2024,通用的板材标准为AMS-QQ-A-250/4(非包铝);AMS-QQ-A-250/5(包铝),主要用于飞机结构、铆钉、导弹构件、卡车轮毂、螺旋桨元件及其他种种结构件,为Al-Cu-Mg系主要成分为:
各化学成分的含量
元素
百分含量(%)
硅(Si)
0.5
锰(Mn)
0.0~0.9
铁(Fe)
0.5
铜(Cu)
3.80~4.90
镁(Mg)
1.2~1.8
锌(Zn)
0.25
钛(Ti)
0.15
镍(Ni)
0.10
铬
0.10
其他
0.15
铝
其余
2.2材料的力学性能分析
2A12
热处理状态
淬火+自然失效
抗拉强度极限
440-470MPa
延伸率
8-12%
HBW
110-120
2.3毛坯尺寸的确定[11]
坯料的选择,在很大程度上决定着挤压件的质量。
同时,它对金属的冷挤压工艺过程等都有很大的影响。
如果坯料尺寸选择得不合理,不但会造成金属的过分损耗,而且还会严重影响冷挤压工艺过程的顺利进行。
所以说,正确地选择和计算冷挤压坯料的种类、尺寸和公差是十分重要的[9]。
冷挤压坯料的形状应该根据零件相应横截面的形状来确定。
一般旋转体及轴对称多角类零件可以选用圆柱形坯料。
2.4坯料制备方法
坯料制备方法有截切下料、冲裁下料、切削下料、锯切下料等多种方法,可按需选用。
在机械压力机上用专用的截切模对棒料或管料进行截切下料是应用得最为广泛的方法。
本例通过截切下料,与其他方法相比可以节省原料。
2.5坯料的软化处理、表面处理及润滑[11]
2.5.1坯料的软化处理
为了改善冷挤压坯料的挤压性能和提高模具的使用寿命,大部分材料在挤压前和多道挤压工序之间必须进行软化处理,以降低材料的硬度,提高材料的塑性,得到良好的显微组织,消除内应力。
对于硬铝来说,
应该采用高温入炉,这样可以降低硬铝的表面硬度,如在处理前2A12表面硬度为105,软化处理后的硬度在65-73之间。
图一
2.5.2坯料的表面处理
硬铝坯料2A12塑性差,在挤压过程中为避免产生裂纹,应使硬铝坯料表面形成一层氧化膜或者磷化膜。
这是一层多孔、致密的氧化膜或者磷化膜,成灰黑色,可用氧化处理、磷化处理或者氟硅化处理来获得。
由于这层氧化膜中可充填大量的润滑剂,所以在挤压时可取得较好的润滑效果。
两种表面方案:
方案一:
氧化处理其工艺流程如下:
1)汽油清洗以去除油污
2)热水清洗(60~100°C)
3)流动冷水清洗
4)酸洗(工业硝酸400~800g/L,2min)
5)冷水清洗2次
6)氧化处理(工业氢氧化钠NaOH40~60g/L,温读50~70°C,时间1~4min,以表面成均匀细致的多孔灰黑色结晶膜为宜)。
7)流动冷水清洗
硬铝除了采用氧化处理来产生润滑支撑层外,还可以采用磷化处理和氟硅化处理。
实验表明,当采用磷化处理加工业菜油润滑时,挤出的零件的表面粗糙度Ra达0.8um,表面光泽。
当采用氟硅化处理加工业菜油润滑时,挤出的零件的表面质量比磷化处理略有提高,但光泽不好,且氟化处理过程中会产生有毒物质,因此尽量不要采用。
方案二:
磷化处理配方为:
磷酸二氢锌(Zn(H2PO4)2)28g,磷酸(75%)25g,铬酸(CrO3)10g,十二烷基硫酸钠,(润滑剂)0.5g,水1L。
处理温度55~60°C,处理时间2~3min。
纯铜、黄铜在挤压中为获得较高的表面质量,往往进行钝化表面处理,以便在坯料表面形成一层钝化膜作为润滑剂的支撑层。
钝化表面处理工艺流程如下:
1)汽油清洗,以去除油污。
2)热水清洗(60~100°C)
3)冷水清洗(两次)。
4)钝化。
5)冷水洗。
6)干燥。
钝化液配方为:
铬酐200~250g/L,硫酸8~16g/L,硝酸30~50g/L。
处理温度为20°C,时间5~10s。
经过比较,由于方案二污染,并且酸的成分比较多,所以选择方案一的表面处理。
2.5.3坯料的润滑处理
两种润滑方案:
方案一:
工业菜油,应用效果良好,冷挤压件内孔表面粗糙度为Ra0.1um,外表面粗糙度为Ra0.8um。
方案二:
皂化,应用效果尚好,冷挤压件内孔表面粗糙度在Ra0.8um以下。
经比较,方案二皂化处理的效果好于工业菜油处理,耐压能力强。
成形工艺方案的制定
该实例产品成形重点是杯形件内孔,由所给配料及零件图可知是通过反挤压成形实现的
根据零件形状和材料及零件图分析制定工艺方案一如下图1;
图二工步图
1.下料2.反挤压
方案一:
第一步:
下料;第二步:
反挤压;
方案二:
可以用机加工的方法成形,机加工会造成材料的浪费,增加了成本投入。
方案三:
压力铸造。
不过LY12是变形铝合金,并且压铸性能不好。
综合考虑,方案一模具结构简单,无切削加工,大大节约了原料可以作为优先选择的方案。
3成形工序挤压力的计算
3.1变形程度的计算
断面减缩率ε=(F0-F1)/F0*100﹪[9]
FO——毛胚截面积;F1——工件变形后的截面积;
ε=d12/d02=10.12/122
=70.84%
查资料得:
2A12反挤压变形许用变形程度是75%---85%,所以小于该材料的反挤压变形许用变形程度,
另,相对孔深h/d1=18/12.8=1.41<3-6(有色金属一次反挤压相对孔深极限)
底厚S1=2>壁厚S2=1.35
据上计算可以通过一次反挤压成形。
3.2图算法冷挤压力的计算
由断面减缩率ε=70.84%H0/S=10.5/1.35>4以及ly12为AL---CU---Mg系
根据有色金属反挤压时单位挤压力图表查表得:
反挤压杯形件的单位挤压力
Pt=1230MPa
由h0/d0=10.5/12=0.875\
查表图4-24得修正系数Kh=0.99
取凸模底部锥角为180度(零件图要求底部平整)
查图4-23得P=KaKhPt
P=0.99*1.06*1230=1290.8MPa[9]
P——单位挤压力;
——挤压材料变形抗力;
d0——毛胚直径;d1——挤压后的直径;
h0——毛胚高度;h1——凹模工作带的高度;
µ=摩擦系数µ=0.1的时候有润滑
3.3总挤压力
P总=A*P挤=π*10.12*1290.8/4=103KN
3.4挤压力经验公式的校正
反挤压杯形件的单位挤压力
P=
(d02/d12㏑d02/(d02-d12)+(1+3µ)(1+㏑d02/(d02-d12))[9]
P——单位挤压力;
——挤压材料变形抗力;
d0——毛胚直径;d1——挤压后的直径;
代入数值得P=1180N
故校核后采用图算法所算得得力大些,所以结果选用图算法的结果
3.5压力机的选择(挤压设备的选择)
挤压设备选择是挤压成型工艺过程中的重要环节,挤压设备选择是否合适直接影响到设备的安全和合理使用,同时也关系到挤压工艺过程能否顺利完成及模具的使用寿命,产品质量,生产效率,成本高低等一系列问题。
在选择挤压设备时,应该注意到以下几点[8]:
(1)应根据所要完成的挤压工序的性质,生产批量的大小,挤压件的几何尺寸及精度要求来选择挤压设备的类型。
(2)由于在挤压过程中,机械的个部分都会受力变形,因此在选择挤压设备时,应充分注意到其精度和刚度。
(3)挤压全过程的变形力应低于压力机的许用压力。
(4)所选的压力机装模高度应与模具闭合高度相适应。
挤压设备的选择,还需要考虑到压力机台面的尺寸应足以安装模具,以便于安放压板固定,压力机有无气垫等弹顶装置,工作台孔大小是否适于出料等等。
考虑到本零件和模具的具体情况,既尺寸很大,必须选择滑块行程大的压力机,以保证本模具的顺利工作。
根据前面计算,所要求的压力P总=103KN,
本例拟选用JA21—25开式可倾压力机。
标称压力250KN
滑块行程130mm
最大闭合高度250mm
闭合高度调节量70mm
工作台尺寸560×360mm
垫板尺寸50×20
根据经验[7]压力机最低压力不小于标称压力的一半,对此压力机来说最低压力不小于Fg/2=125KN,即可以认为滑块在下行时任一时刻均可承受125KN的力,过标称点之后可承受250KN的力,也就是说任意时刻均能提供大于103KN的力,所以此压力机可以用来本例的反挤压设备,但是安全区的面积并非压力机工作时对工件做的功。
4.模具设计
4.1挤压模具设计的基本要求
挤压模具设计的基本要求,应满足以下条件:
(1)凹模工作部分应有足够高的强度和较长的使用寿命;
(2)凹模工作部分能够简洁可靠的固定在模架上;
(3)极易损坏部分拆卸方便;
(4)毛坯放置容易,定位准确,在大量生产时可能采用半自动或全自动送
(5)挤压的工件可以方便的取出;
(6)制造简单,成本费用低;
(7)保证操作人员的安全。
4.1.1模具设计时需考虑的安全措施
在设计模具时,必须周全的从各个不同角度考虑必要的安全措施,以确保人身安全和设备安全。
模具结构安全措施的一些基本要求如下:
(1)模具的结构不应使操作者有不安全感。
在操作时,严禁向模具内伸手。
模具结构应以操作时不必将操作者身体的一部分进入危险区为原则。
(2)模具要有足够的强度。
整个模具结构的厚度不能过薄,受力部分厚度要大一些。
(3)在设计模座时,应考虑安装螺钉的槽孔尺寸,特大的上模座或具有较大的钢性卸料板的模具,应增加紧固螺钉。
(4)对具有敞开式活动卸料板的模具,应加保护板[10]。
4.1.2挤压模具的整体设计
在高压力作用下,为了保证挤压模具的寿命,对模具结构的强度、刚度等方面的要求应比一般冲压模具高。
该模具采用导柱导套导向,来提高导向的精度。
凸模用凸模固定板固定。
由于挤压时的挤压力很大,为了防止由凸模和凹模传来的高压直接作用在上、下模座上,一般是在凸模和模座之间,以及凹模和模座之间设置垫板,来分散压力,起缓和作用。
根据理论分析可知,压力在板内传播是向外扩大的,即垫板厚度增加,压力面的传递直径增大,传递的压力减少。
垫板是承受高压的零件,要求有较高的强度和刚度。
凹模通过预应力圈固定在下模座上。
为了防止挤压件卡在凹模内,采用顶杆顶出零件,应尽量减少顶杆的长度[10]。
5.2凸、凹模的设计
5.2.1凸模的设计,如图2;
根据零件需要反挤压的内径来确定凸模工作带的尺寸,另杯形件底部要求是平底,故要求工作带底部也是平底,参考书表6-2反击压模尺寸参数设计计算表有色金属部分
根据经验公式:
工作带d1=10.1mm
工作带高度h=0.5-1.5这里取h=1mm
非工作部分直径d=(0.85-0.95)d1=9.5取0.90
定位直径d2=(1.1-1.3)d1=12.4取1.2
定位高度h2=(0.55-0.65)d1=6.1取0.6
支撑部分直径d3=(1.2-1.5)d1=14.1取1.4
支撑部分高度h3=(0.5-1.0)d3=10取0.71
支撑部分锥角B=5-15取10度
支撑锥面与d2交接处R11.0d2R1=12.1
d与d2交接处R22.0dR2=20.2
d与d1交接处R31.5d1R3=15.2
图三凸模
4.2.2凹模的设计和尺寸
凹模的设计主要包括凹模型腔的设计和预应力圈的设计。
挤压凹模大体上可分整体凹模和组合凹模两种形式,但整体凹模无论从模具强度,还是挤压件的顶出都不利,使用极少,反而组合凹模用的比较普遍。
组合凹模的优点是同样外形尺寸(包括外套在内的整个组合凹模外形尺寸)和相同内腔尺寸的条件下,其强度要比单层(即整体式)凹模的强度大得多;结构合理、模具寿命长、挤压件底部圆角连接处的毛刺大为减少,适用于大批量生产而且它不但节省了材料,而且大大减少了模具加工的难度。
但它增加了凹模加工的工作量,主要表现在压合面的加工和装配上,而且它要求精度高,以保证同轴度,并且拼合面宽度应小于3mm,上下两面应留出0.2mm空隙,结合面的表面粗糙度取Ra0.2[9]。
在具体冷挤压工艺设计的条件下,根据冷挤压单位挤压力的大小决定采用整体式、二层式或三层式凹模。
根据下表来确定预应力圈的层数:
表1 一般工具钢制成的组合凹模的选择[11]
单位挤压力
/MPa
凹模型式
简 图
≤1100
整体凹模
1100<p≤1600
二层组合凹模
1600<p≤2500
三层组合凹模
根据前面计算的P=1290.8MPa>1100MPa
可知应该用两层组合凹模
1)两层组合凹模两层组合凹模结构见资料【4】,参数见表1。
[9]
d1—凹模内径(按挤压件最大外径)(mm);
d3=(4~6)d1;γ=1°30′(锥度可向上,亦可向下);
C2=δ2d2—d2处轴向压合量;
u2=β2d2—d2处径向过盈量;
3)两层组合凹模各圈直径的确定
根据冷挤压件图外径12.8mm决定了凹模型腔d1即d1=12.8mm
d3=(4-6)d1=(4-6)12.8mm=51.2-76.8mm
取d3=64mm
故总直径比a3=d3/d1=64/12.8=5
两层组合凹模各圈直径,查资料得:
d2大于等于2d2=2*12.8=25.6mm
取d2=30mm
a2=d2/d1=2.34
4)径向过盈量与轴向压合量的确定
在确定了各圈直径后,便可确定d2处的径向过盈量(双面)△d2与轴向压合量c2
查表教材6-31得:
径向过盈系数β2=0.0068
查表教材6-32得:
轴向压合系数δ2=0.17
则△d2=β2d2=0.0086*30mm=0.258mm
C2=δ2d2=0.17*30mm=5.1mm
式中d2-------内层凹模外径
4)凹模的尺寸计算方法:
型腔的尺寸根据零件的尺寸来确定,还要考虑零件材料的尺寸收缩变形等因素对外形的影响。
预应力圈的尺寸是根据公式计算得到的。
根据教材图6-17例以及以及表6—3所示经验公式可计算出各部分尺寸
凹模型腔高度H2=h0+h+r+(2-4)=10.5+1+2.5+3=17mm
凹模入口圆角半径r=2-3取2.5
凹模型腔内径D=12.8D=2D2凹模总高度H=17+12.8=29.8
过度外圆角半径R=0.5-2取1mm
图四内凹模
凹模采用两层预应力圈的设计,可以提高凹模承担强度的能力,
凹模横截面积的尺寸,若是杯形的,凹模的内腔尺寸越摩越大,故可以按零件的最小外径设计,而应取正公差。
凹模的内部形状根据预成形后挤压件的期望形状而定,过渡部分用圆角。
4.3凸、凹模固定圈的设计
4.3.1凸模固定板
凸模固定圈的设计如图五
图五凸模固定板
4.3.2凹模固定板
凹模固定板设计如图六
图六凹模固定板
4.4压力垫板的设计
挤压时,模具型腔中单位冷寂压力很高,如凸模或凹模所传递的轴向压力直接作用在上下模板上有可能造成模板压塌,因此必须在模板与凸凹模之间设置淬硬的压力垫板,有时简称垫板,以起减缓轴向压力的作用,降低应力密度,根据经验垫板厚度至少等于杆直径,由于d2=15.4,则取垫板厚度t=16mm为防止垫块弹性变形和塑性变形,必须选用优质碳素工具钢T8A、T10A,热处理到高硬度56-60hrc
挤压时凸模或凹模作用于垫板表面积上的单位挤压力应均匀分布在凸模或凹模支撑面的直径范围内,压力大致扩展成圆锥状传到垫板底面,压力分部以加压中心最小,其周边最小,垫板厚度增加时,受压面的传递直径增加,传递压力随之减小。
因此应尽量加大垫板厚度,如果垫板的厚度相同,则多层垫板力的传递范围比使用单层垫板大。
因此,同样厚度时应尽量采用多层垫板。
垫板必须采用T10A工具钢制造。
4.5.顶出装置的设计
顶出装置设计原则如下;
(1)顶杆的工作部分略带五度的锥度,可延长使用寿命;
(2)顶端直径的
按
计算,下端为了能承受较大的单位挤压力,采用锥形结构,增大支撑面的面积,取
=(2~3)d,含炭量小于0.15﹪或尺寸较小的挤压件取较小值,含碳量大于0.2﹪或尺寸较大的挤压件取较大值。
(3)顶杆的长度L越短越好,能将挤压件顶出凹模的上平面即可;装配后,顶杆的工作端面应比凹模底面高出0.1mm左右。
(4)兼作挤压凹模的顶杆,设计时必须与凹模一样考虑;不作挤压凹模用的顶杆,应根据载荷的具体情况,以保证纵向稳定的要求进行设计。
顶杆须用工具刚制造。
图七顶料杆
4.6卸