添加剂对PDMSPS复合膜气体分离影响.docx
《添加剂对PDMSPS复合膜气体分离影响.docx》由会员分享,可在线阅读,更多相关《添加剂对PDMSPS复合膜气体分离影响.docx(31页珍藏版)》请在冰豆网上搜索。
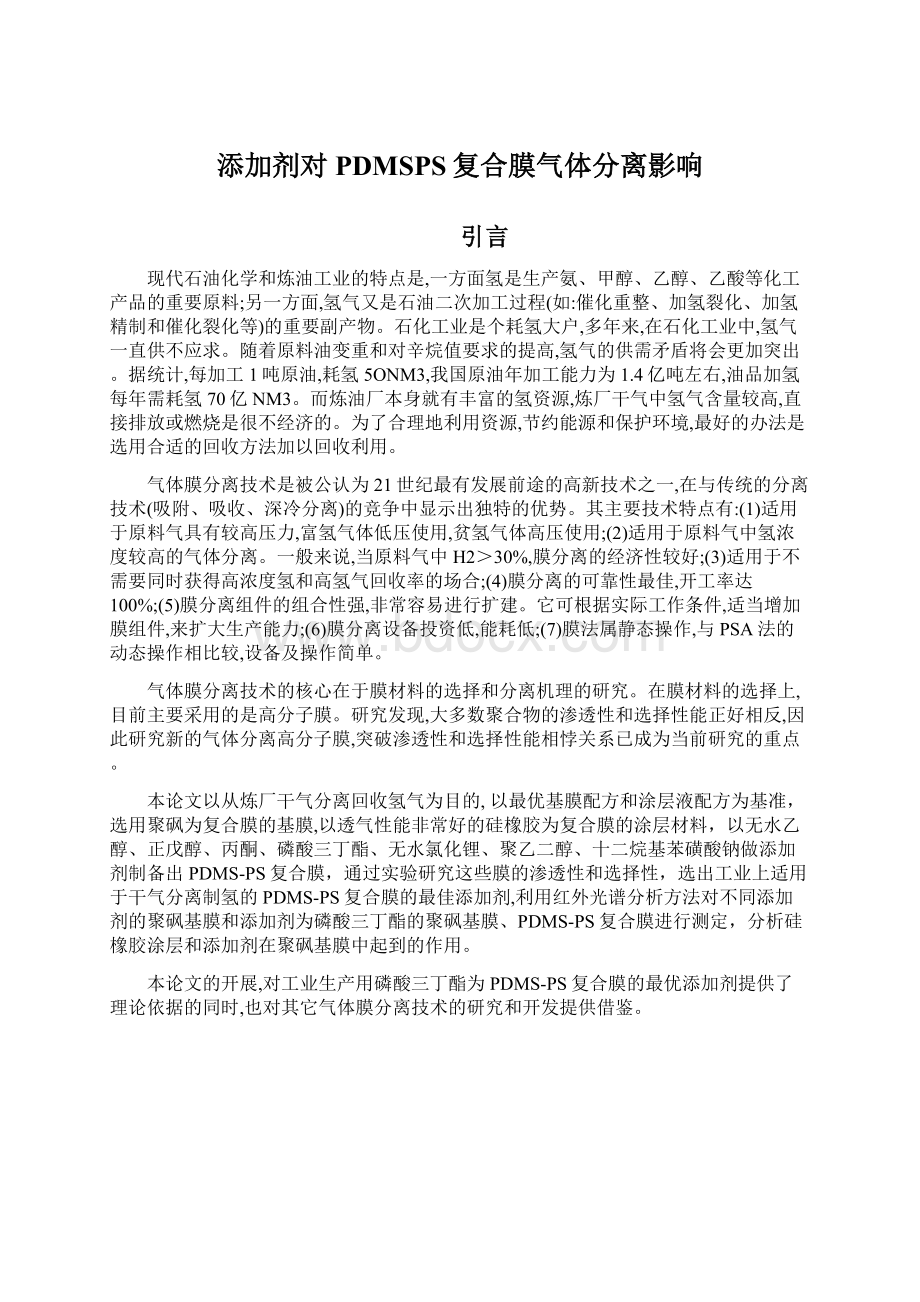
添加剂对PDMSPS复合膜气体分离影响
引言
现代石油化学和炼油工业的特点是,一方面氢是生产氨、甲醇、乙醇、乙酸等化工产品的重要原料;另一方面,氢气又是石油二次加工过程(如:
催化重整、加氢裂化、加氢精制和催化裂化等)的重要副产物。
石化工业是个耗氢大户,多年来,在石化工业中,氢气一直供不应求。
随着原料油变重和对辛烷值要求的提高,氢气的供需矛盾将会更加突出。
据统计,每加工1吨原油,耗氢5ONM3,我国原油年加工能力为1.4亿吨左右,油品加氢每年需耗氢70亿NM3。
而炼油厂本身就有丰富的氢资源,炼厂干气中氢气含量较高,直接排放或燃烧是很不经济的。
为了合理地利用资源,节约能源和保护环境,最好的办法是选用合适的回收方法加以回收利用。
气体膜分离技术是被公认为21世纪最有发展前途的高新技术之一,在与传统的分离技术(吸附、吸收、深冷分离)的竞争中显示出独特的优势。
其主要技术特点有:
(1)适用于原料气具有较高压力,富氢气体低压使用,贫氢气体高压使用;
(2)适用于原料气中氢浓度较高的气体分离。
一般来说,当原料气中H2>30%,膜分离的经济性较好;(3)适用于不需要同时获得高浓度氢和高氢气回收率的场合;(4)膜分离的可靠性最佳,开工率达100%;(5)膜分离组件的组合性强,非常容易进行扩建。
它可根据实际工作条件,适当增加膜组件,来扩大生产能力;(6)膜分离设备投资低,能耗低;(7)膜法属静态操作,与PSA法的动态操作相比较,设备及操作简单。
气体膜分离技术的核心在于膜材料的选择和分离机理的研究。
在膜材料的选择上,目前主要采用的是高分子膜。
研究发现,大多数聚合物的渗透性和选择性能正好相反,因此研究新的气体分离高分子膜,突破渗透性和选择性能相悖关系已成为当前研究的重点。
本论文以从炼厂干气分离回收氢气为目的,以最优基膜配方和涂层液配方为基准,选用聚砜为复合膜的基膜,以透气性能非常好的硅橡胶为复合膜的涂层材料,以无水乙醇、正戊醇、丙酮、磷酸三丁酯、无水氯化锂、聚乙二醇、十二烷基苯磺酸钠做添加剂制备出PDMS-PS复合膜,通过实验研究这些膜的渗透性和选择性,选出工业上适用于干气分离制氢的PDMS-PS复合膜的最佳添加剂,利用红外光谱分析方法对不同添加剂的聚砜基膜和添加剂为磷酸三丁酯的聚砜基膜、PDMS-PS复合膜进行测定,分析硅橡胶涂层和添加剂在聚砜基膜中起到的作用。
本论文的开展,对工业生产用磷酸三丁酯为PDMS-PS复合膜的最优添加剂提供了理论依据的同时,也对其它气体膜分离技术的研究和开发提供借鉴。
第一章文献综述
1.1膜及膜分离技术
膜分离法应用于多个领域,对膜的分类也有很多种,采用适合的膜进行污水处理才能够达到最好的效果。
因此不同的领域对膜的分类有不同的参考标准,如膜的孔径、成膜材料、成膜组件、成膜的组分以及膜形态等。
在炼油污水处理中,常用的分类方法是按照膜孔径和成膜材料分类。
按照膜孔径分为微滤膜、超滤膜、纳滤膜以及反渗透膜等。
若油水体系中的油是以浮油和分散油为主,则一般选择孔径在10~100µm之间的微孔膜;若水体中的油是因有表面活性剂等使油滴乳化成稳定的乳化油和溶解油,油珠之间难以相互黏结,则需采用亲水或亲油的超滤膜分离,一则是因为超滤膜孔径小于10µm,通常为0.2~10µm;二则是超细的膜孔有利于破乳或有利于油滴聚结;纳滤膜的孔径一般为0.5~2nm,主要用于截留透过超滤膜的那部分溶质,同时又可使被反渗透膜所截留的盐通过;反渗透膜的孔径和孔隙率最小,通常小于0.5nm,几乎可以完全将分子量较小的有机组分截留。
按照成膜材料又分为有机膜和无机膜两类。
常用的有机膜有醋酸纤维膜、聚砜膜、聚丙烯膜、聚偏氟乙烯膜等,有机膜制备工艺简单、方便,膜组件的装填密度高,但膜产品易变形,遇热不稳定、不耐高温、在液体中易溶胀、强度低、再生复杂、使用寿命短。
常用的无机膜材料有氧化铝、氧化锆、氧化钛等,无机膜制备工艺较复杂,但膜不易变形、耐高温、耐有机溶剂、抗微生物腐蚀、刚性及机械强度好、不老化,从而表现出更大的潜力[1-2]。
近年来新兴的膜分类方法是按照分离组分的物理-化学性质将膜分为疏水膜和亲水膜两类。
常用的疏水性膜由聚乙烯、聚偏二氟乙烯和聚四氟乙烯等聚烯烃类聚合物组成[3],去除油中少量水杂质的效果良好。
疏水膜机械强度高,膜面积较亲水膜小,受表面活性剂影响小,能耗较亲水膜少,当孔径足够小时能产生良好的破乳作用[4]。
常用的亲水膜材料有聚醚砜,纤维素酯,聚酰亚胺/聚醚酰亚胺,聚脂肪酰胺和聚丙烯腈等具有亲水基团的高分子聚合物,亲水性膜水通量高,抗污染能力强,但是易受表面活性剂影响。
1.膜分离
膜分离是借助于膜在某种推动力的作用下,利用流体中各组分对膜的渗透速率的差别而实现组分分离的过程。
目前常见的膜分离过程可分为以下几种:
微滤、超滤、纳滤、反渗透、电渗析等。
2.膜分离技术的起源
1748年,AbbeNollet观察到水可以通过覆盖在盛有酒精溶液瓶口的猪膀胱进入瓶中,发现了渗透现象。
但是,直到19世纪中叶Graham发现了透析现象,人们才开始对膜分离现象重视起来,并开始研究。
1867年MoritzTaube制成了人类历史上第一张合成膜—亚铁氰化钠膜,并以近代的观点予以论述。
1911年Donnan研究了荷电体传递中的平衡现象。
1920年,Gibbs从热力学角度提供了认识渗透压现象和它与其他热力学性能关系的理论。
1925年世界上第一个滤膜公司(Sartorius)在德国Gottingen公司成立。
1930年的时候TreorellMeyer,Sievers等对膜电动势的研究,为电渗析和膜电极的明打下了一定的基础。
1950年W.Juda等试制成功第一张具有实用价值的离子交换膜,电渗析过程得到迅速发展。
3.膜分离技术的发展状况
目前,膜分离技术的发展是从5O年代离子交换膜的开发和60年代反渗透膜的出现开始的。
1950年WJuda试制出选择透过性能的离子交换膜,奠定了电渗析的实用化基础。
l960年洛布和索里拉简首次研制成世界上具有历史意义的非对称反渗透膜,这在膜分离技术发展中是一个重要的突破,使膜分离技术进入了大规模工业化应用的时代。
其发展的历史大致为:
30年代微孔过滤,40年代透析;50年代电渗析;60年代反渗透;70年代超滤和液膜;80年代气体膜分离;90年代渗透汽化。
此外以膜为基础的其它新型分离过程,以及膜分离与其它分离过程结合的集成过程也日益得到重视和发展。
膜分离技术在近20年发展迅速。
其应用已从早期的脱盐发展到化工、轻工、石油、冶金、电子、纺织、食品、医药等工业。
废水、废气的处理,原材料即产品的回收与分离和生产高纯水等是适应当代新产业发展的重要高新技术[5]。
尤其是在水处理领域具有相当的技术优势,是现代分离技术中一种效率较高的分离手段。
在环境过程中膜分离技术以其独特的作用而被广泛用于水的净化与纯化过程中[6]。
膜分离技术不但在工业领域得到广泛应用同时正在成为解决能源资源和环境污染问题的重要技术和可持续发展的技术基础[7]。
分离过程往往是一个十分耗能的过程,在生产的投资和操作费用中所占比例极高。
因此选择高效、低耗的分离技术与降低成本、减少能耗以及提高产品质量密切相关。
膜分离过程作为一门新兴的分离、浓缩、及净化技术与传统的分离方法如蒸馏、吸收、解吸、萃取、蒸发、结晶、深冷分离等过程相比较,在越来越多的分离领域显现出强劲的竞争势头。
膜分离过程具有如下特点[8,9,10]。
1.膜分离过程能耗比较低
大多数膜分离过程都不发生相态变化。
由于避免了潜热很大的相变化,膜分离过程的能耗比较低。
另外,膜分离过程通常在室温附近的温度下进行,被分离物料加热或冷却的能耗小。
2.适合热敏性物质的分离
膜分离过程通常在常温下进行,因而特别适合于热敏性物质和生物制品(如果汁、蛋白质、酶、药品等)的分离.分级.浓缩和富集.例如在抗生素生产中,采用膜分离过程脱水浓缩,可以避免减压蒸馏时因局部过热,而使抗生素受热破坏产生有毒物质。
在食品工业中,采用膜分离过程替代传统的蒸馏除水,可使产品在加工后仍保持原有的营养和风味。
3.分离装置简单,操作方便
膜分离过程的推动力以压力差为多,因此分离装置简单,占地面积小,操作方便,有利于连续化生产和自动化控制。
4.分离系数大,应用范围广
膜分离不仅可以应用于从病毒、细菌到微粒的有机物和无机物的广泛分离范围,而且还适用于许多特殊溶液体系的分离,如溶液中大分子与无机盐的分离,共沸点物或近沸点体系的分离等.
5.工艺适应性比较强
膜分离的处理规模根据用户要求可大可小,工艺适应性强。
6.便于回收
在膜分离的过程中,分离与浓缩同时进行,以便于回收有利用价值的东西
7.无二次污染
膜分离过程中不需要从外界加入其它物质,既节省了原材料,又避免了二次污染。
1.电渗析法(ED)
电渗析(简称ED)是以直流电为推动力,用阴阳离子交换水溶液中阴阳离子选择透过性,水体中的离子通过膜迁移到另一水体中的物质分离过程。
利用单阳膜的选择透过性使有机废液阳离子作定向迁徙,使有机物在阳极析出。
2.反渗透(RO)技术
反渗透装置就是利用高压泵将待处理水经过增压以后,借助半透膜的选择截留作用来除去水中的无机离子的,由于反渗透膜在高压情况下只允许水分子的通过,而不允许钾、钠、钙、锌等离子及病菌、细菌通过,从而获得高质量的纯水。
其主要应用领域有海水和苦成水的淡化,纯水和超纯水制备,工业用水处理,饮用水净化,医药、化工和食品等工业料液处理和浓缩以及废水处理等。
3.正渗透技术
尽管目前依靠渗透压驱动的正渗透膜分离技术的应用范围,还未达到各种依靠外加压力驱动的膜分离技术那么广泛,但是它已在许多领域得到了应用。
(1)水纯化的应用在水纯化中,正渗透滤水器是目前正渗透膜分离技术少有的几种商业化应用之一。
正渗透滤水器的基本原理是,在其膜组件里面填装可食用的驱动液(如糖或饮料粉),当把滤水器浸没到任何水体(如清洁水、泥浆、盐水、污水等)中时,由于这些水体中的渗透压低于驱动液中的渗透压,这些水体中的水将透过正渗透膜进入驱动液中,而水体中的污染物(如悬浮固体、有机物、病毒、细菌等)将被截留下来,水体进入驱动液后,驱动液渐渐被稀释,被稀释的驱动液可被人体直接安全饮用,并且里面富含营养物质与矿物元素,它将能长时间维持人类生存。
(2)海水淡化在海水淡化方面,正渗透的方法一直不够成熟。
不过近几年来,耶鲁大学MenachemElimelech教授课题组发明了一种新型的利用正渗透膜分离方法进行海水脱盐的技术,并且进行了中试研究。
这种正渗透脱盐过程的关键在于其选择的驱动液,它的驱动液是将碳酸氢铵与氨水按照一定比例混合,然后溶解于水中配置成一定浓度的铵盐作为驱动液,这种驱动液既具有较高的渗透压,又能方便的将溶质和水分离。
驱动液吸收海水中的水分后得到稀释,对于稀释后的驱动液,只需将其加热到60℃,驱动液中的铵盐就被分解为氨气和二氧化碳,采用合适的方法(如蒸馏)就能将其与水分离,得到纯净的产品水,分离出的氨气和二氧化碳再次浓缩溶解于水中,便能得到铵盐驱动液,使得驱动液能够得以循环使用。
4.超滤(UF)与微滤(MF)技术
超滤主要适用于大分子溶液的分离与浓缩,广泛应用在食品、医药、工业废水处理、超纯水制备及生物技术工业,包括牛奶的浓缩、果汁的澄清、医药产品的除菌、电泳涂漆废水的处理、各种酶的提取等。
微滤是所有膜过程中应用最普遍的一项技术,主要用于细菌、微粒的去除,广泛应用在食品和制药行业中饮料和制药产品的除菌和净化,半导体工业超纯水制备过程中颗粒的去除,生物技术领域发酵液中生物制品的浓缩与分离等。
5.气体膜分离(GS)
气体膜分离的主要应用有:
1)H2的分离回收:
膜分离H2主要应用于从合成氨排放气中回收H2;从甲醇驰放气中回收H2;从炼厂气中回收H2;合成气生产中H2/CO比例调节等,是当前气体分离应用最广的领域;2)空气分离利用膜分离技术可以得到富氧空气和富氮空气,富氧空气可用于高温燃烧节能、家用医疗保健等方面;富氮空气可用于食品保鲜、惰性气氛保护等方面;3)气体脱湿:
如天然气脱湿、工业气体脱湿等,这样可防止气体在天冷时结冰。
6.渗透汽化(PV)技术
渗透汽化(PV)技术是近年来发展起来的一种新型膜分离技术,特别适合于分离蒸馏法难以分离或不能分离的近沸点、恒沸点有机混合物,对有机溶剂及混合溶剂中微量水的脱除、废水中少量有机物的脱除及水溶液中高价值有机组分的回收具有明显的技术和经济优势。
目前,生产生活的各个方面都已经离不开膜分离技术,随着新材料、新技术的不断出现,膜技术在化学和生物工程中的应用愈加显示出令人瞩目的前景。
1.2气体膜分离技术
气体膜分离技术是以膜两侧的气体压差为推动力,利用不同气体在膜中渗透速率的差异,使不同气体在膜两侧富集实现分离的过程。
它是本世纪开发的一类较为成熟的膜分离技术,由于它具有分离效率高、能耗低、设备简单、操作方便、占地面积小、不产生二次污染等特点,使得气体膜分离技术成为深冷分离、吸收和变压吸附等传统气体分离方法的强有力的竞争者。
早在1831年Mtichell用膜进行氢气和二氧化碳混合气渗透实验,发现了不同种类气体分子透过膜的速率不同的现象,首先揭示了用膜实现气体分离的可能性。
1866年,Grhaam研究橡胶膜对气体的渗透性能,用膜可以将空气中氧气由21%富集至41%,并提出了溶解一扩散机理,使人们对气体在膜中的渗透过程有了进一步的认识。
气体膜分离应用研究始于20世纪50年代初。
60年代,Loeb和Msuriarjna研制出了第一张醋酸纤维素非对称膜,为制备高渗透通量分离膜奠定了基础"70年代,HneiS在非对称膜基础上研发了阻力复合膜,将硅橡胶涂在非对称高分子基膜上,弥补了膜表面缺陷,得到了渗透通量和选择性都很好的气体分离膜,实现了气体膜分离的飞跃。
1979年,美国Monsanto公司研制出“prism”膜分离装置,成功应用在合成氨弛放气中回收氢气。
这是气体膜分离技术发展过程中的一个重大的突破,标志着气体膜技术走向了工业应用阶段。
自1980年以来,已有上百套装置在运行,用于合成氨驰放气中氢气的回收和石油炼厂气中氢气的回收。
除氢氮分离膜外,近年来富氧、富氮膜也在工业应用中取得了长足的进展。
气体膜分离技术已在许多方面得到了广泛的应用.随着气体膜分离技术开发的不断深入,市场的不断扩大,气体膜分离技术也已从分离常量的永久性气体向分离含有微量组分和可凝性气体的过程发展。
渗透汽化是在液体混合物中组分的蒸气压差推动下,利用组分通过膜的溶解与扩散速率的差异来实现分离的过程,它是近三十年来研究开发出来的一个新型膜分离过程。
早在1906年Khaelnbegr报道了醇与烃的混合物通过橡胶膜的选择渗透作用。
191年,Kboer发表的论文中介绍了蛋白质一甲苯溶液中的水分透过火棉胶的选择渗透作用,从而第一个提出渗透汽化(Pevrpaoratoin,简称PV)概念。
1935年Fabrezrlo采用渗透汽化法浓缩蛋白质溶液,使人们认识到渗透汽化在分离与浓缩方面的应用价值。
在50年代以后,对渗透汽化的研究才较广泛Binning等人认识到了该过程的潜在开发价值,对此作了较广泛、深入的研究,并试图开发到工业应用阶段,但未取得大的突破。
此后,这个领域沉寂了十多年,随着新型高分子物质的合成和制膜技术的发展,再加上能源危机的冲击,渗透汽化在70年代中期再度被引起重视。
直至1982年,德国GFT公司取得重要突破,率先推出商品化聚乙烯醇复合膜,在巴西建立第一座乙醇/水分离小型示范厂,其生产能力430kg/h,标志着渗透汽化开始进入工业化阶段。
至今在世界上已经建立了100多套PV的工业装置,90%是GFT公司提供的膜和技术(现属SulzerChemtech公司),多数用于有机溶剂的脱水,其中24套用于乙醇脱水,16套用于异丙醇脱水,其余的用于进行酷类、醚类及其它有机溶剂脱水,装置的产量大多在1500吨/年一10000吨/年,也有几套年产4万吨的装置。
在我国渗透汽化的研究处于基础研究阶段,只有燕化和清华大学合作研制苯脱水装置用于工业化生产[11]。
目前正在发展和具有发展潜力的气体膜分离过程主要有:
空气中有机蒸气脱除、工业气体脱湿及净化、低质量天然气富集、从生物气中富集甲烷、空气富氧、烷烃\烯烃分离、烟道气脱硫、二氧化碳脱除与富集\高温分离等。
近年来,国内外学者对气体膜分离技术在膜材料、制膜、渗透机理模型、分离过程等方面开展了大量研究,取得了一些新进展。
气体膜分离是一种“绿色技术”,并且由于它具有分离效率高、能耗低、设备及操作简单等优点,在与传统的分离技术,如吸附、吸收、深冷等的竞争中显示出独特的优势,其研究和应用发展十分迅速。
高分子膜分离氢气技术的原理是气体组分在压力差的推动下,氢气和其它气体通过高分子膜时具有不同的渗透速率,从而使氢气和其它的气体分离开来。
由于原料气为高压,渗透气为低压,因此在高分子膜两侧形成了一个压力差,HZ在压力差的推动下就可以透过膜。
气体渗透包括两个连续的步骤:
首先气相组分溶解于膜中,然后在膜中扩散到低压侧。
不同的组分具有不同的溶解度和扩散速率,也就是有不同的渗透速率。
渗透速率较高的气体如氢气在膜的低压侧浓缩,而渗透速率较低的气体如氮气、甲烷等烃类物质由于氢气的优先渗透而在膜的高压侧富集,从而达到分离目的。
氢气膜分离技术的特点主要有:
(1)适用于原料气具有较高压力,富氢气体低压使用,贫氢气体高压使用工况;
(2)适用于原料气中氢气浓度较高的气体分离。
一般来说,当原料气中H2>30%,膜分离的经济性较好;(3)膜分离的可靠性最佳。
氢气分离的可靠性十分重要,尤其是当这一工艺是作为补充氢气的主要来源时更显得重要。
可靠性通常以开工率和非计划停工率来衡量。
由于膜分离装置工艺流程简单,无运动部件,控制部分少,适于连续生产,所以开工率达100%;(4)膜分离器件的组合性强,非常容易进行扩建。
它可根据实际工况条件,适当增加膜组件,来扩大生产能力;(5)膜分离设备投资最低;(6)膜法属静态操作,与PSA法的动态操作相比较,设备及操作简单[12]。
膜分离回收氢气的装置,可在炼油厂的每一套有氢源的装置上使用,如临氢降凝,柴油、汽油、煤油加氢精制,加氢裂化等单元操作过程都可以通过膜分离直接回收氢气,然后再进入循环压缩机入口使用,而渗余气可作为制氢原料或作其它用途。
此外还有一些含氮气和二氧化碳较多的炼厂气如催化干气也可以利用膜分离方法回收氢气[13,14]。
膜分离技术的核心是分离膜,膜的优劣决定了气体分离膜的分离性能、应用范围、使用寿命等等,膜材料及分离膜的发展将推动气体膜分离技术的进一步发展。
按材料类型和性质,气体分离膜材料可以分为:
高分子材料,无机材料和有机一无机杂化材料[15]。
下面将分别加以论述:
1.高分子材料
已经应用于气体膜分离领域的高分子膜材料有聚酞亚胺(PI),醋酸纤维素(EA),聚二甲基硅氧烷(PDMS),聚矾(PS),聚碳酸酷(PE)等现已工业化生产的多种高分子膜,对氢气不但具有较大的渗透速率,而且选择性也较高,因此非常适合从含氢混合气中分离和回收氢气。
一些高分子膜对氢气、氮气和甲烷的渗透分离性能示于表1.1[16]。
但是,大多数高分子膜存在透气性和选择性互为制约的相反关系,因此研究开发出兼顾高透气性和高选择性的新型高分子膜材料已成为目前的研究热点。
表1.1氢气、氮气、甲烷在高分子膜中的渗透分离性能
Tablel.1PermeationofH2、N2、andCH4throughPolymericmembranes
膜材质
H2
N2
CH4
αH2/CH4
αH2/N2
聚二甲基硅氧烷
390
181
-
-
2.15
聚苯醚
113
3.8
-
-
29.6
天然橡胶
49
9.5
-
-
5.2
聚碳酸酯
12
0.3
-
-
40.0
聚砜
13(44)
0.088
0.22
60
50
醋酸纤维
12(3.8)
0.14
0.20
60
27.1
聚酰亚胺
9(2.6)
0.028
0.048
200
200
聚乙烯三甲基硅烷
0.13
-
0.011
12
-
注:
括号中指的是与N2相配套的值
(1)聚酰亚胺许多研究结果表明,聚酰亚胺等含氮芳杂环聚合物同时具有高透气性和高选择性,是气体膜分离的理想材料。
由芳香二酐和二胺单体缩聚而成的芳香聚酰亚胺(PI),因分子主链上有芳环结构,具有很好的耐热性和机械强度,并且化学稳定性很好,耐溶剂性能优异,可以制成具有高渗透系数的自支撑型不对称中空纤维膜。
随着高分子科学的不断发展以及各种应用对膜性能要求的提高,聚酰亚胺作为性能优异的膜材料越来越受到重视[17]。
与其它高分子材料相比,聚酰亚胺的选择性高得多,并能用于高温条件,特别是聚酰亚胺在可凝性烃类中不溶胀,所以从含可凝性烃类气体(如石油气、炼厂气等)中回收氢气具有无可比拟的优点。
目前,高分子科学已经进入了分子工程时代,对于聚酰亚胺气体分离膜,可以在分子水平上设计出符合分离体系的要求的分子结构,通过对单体和反应条件的控制,制备出透气性和选择性均佳的新型膜[18]。
(2)聚砜聚砜(PS)是一种机械性能优良,耐热性好,耐微生物降解,并且价廉易得的膜材料,由聚砜制成的膜具有膜薄、内层孔隙率高且微孔规则等特点,因而常用作气体分离膜的基本材料。
例如,美国Mnosnaot公司开发的Prism分离器采用的就是聚砜非对称中空纤维膜,并采用硅橡胶涂敷,以消除聚砜中空纤维皮层的微孔,将其用于合成氨厂弛放气以及炼厂气中回收氢气,HZ和NZ的分离系数可达到30一60。
一些研究者通过调整聚砜制膜液配方,降低了制膜液的湿度敏感性,用相转化法制备聚砜支撑膜,并消除针孔和其它缺陷,显著地提高聚砜支撑膜的性能稳定性和完整性。
为了进一步改善聚砜中空纤维的皮层结构,Kesting等将聚砜溶于LewiS酸和LewiS碱的络合溶剂中纺丝,得到梯度皮层结构,提高了气体渗透速率。
sImali等[19]制得高选择性聚砜中空纤维膜,以硅橡胶堵孔,用于分离CO2/CH4和02/N2物系,分离系数分别可以达到83.1和7.32。
chung等[20]制成了多层中空纤维复合膜,其底膜为聚砜,选择性活性层为聚乙烯基毗咤(PVP),用聚二甲基硅氧烷(PDMS)堵孔密封,许多气体在这种多层中空纤维复合膜的渗透速率都较好,如HZ可以达到9.90×10﹣8cm2/(cm·S·Pa)并且用于分离H2/N2的分离系数为104。
研究表明,在聚砜的分子结构上引入其它基团,可以制成性能更好,应用范围更广的膜材料[21]。
总之,聚砜在今后一段时间内还将是重要的气体分离膜材料。
(3)聚二甲基硅氧烷许多独特性能,是目前发现的气体渗透性能最好的高分子膜材料之一。
美国、日本已聚二甲基硅氧烷(PDMS)从结构上看属半无机、半有机结构的高分子,已经成功的用它及其改性材料制成富氧膜。
王学松等采用活化涂敷技术制成的PDMS/PS复合膜,可使H2/N2的分离系数达到60。
chung等[22,23]研制了用聚二甲基硅氧烷堵孔的多层复合膜,这是利用聚二甲基硅氧烷(硅橡胶)优良的气体渗透性能来促进气体的渗透,硅橡胶起到弥补聚砜或聚丙烯睛基膜表皮缺陷孔的作用,真正起分离作用的还是基膜。
Lundy,Kimmerle,Ashworth和Fouda等分别制备了涂层为硅橡