高科技厂房排气系统节能.docx
《高科技厂房排气系统节能.docx》由会员分享,可在线阅读,更多相关《高科技厂房排气系统节能.docx(13页珍藏版)》请在冰豆网上搜索。
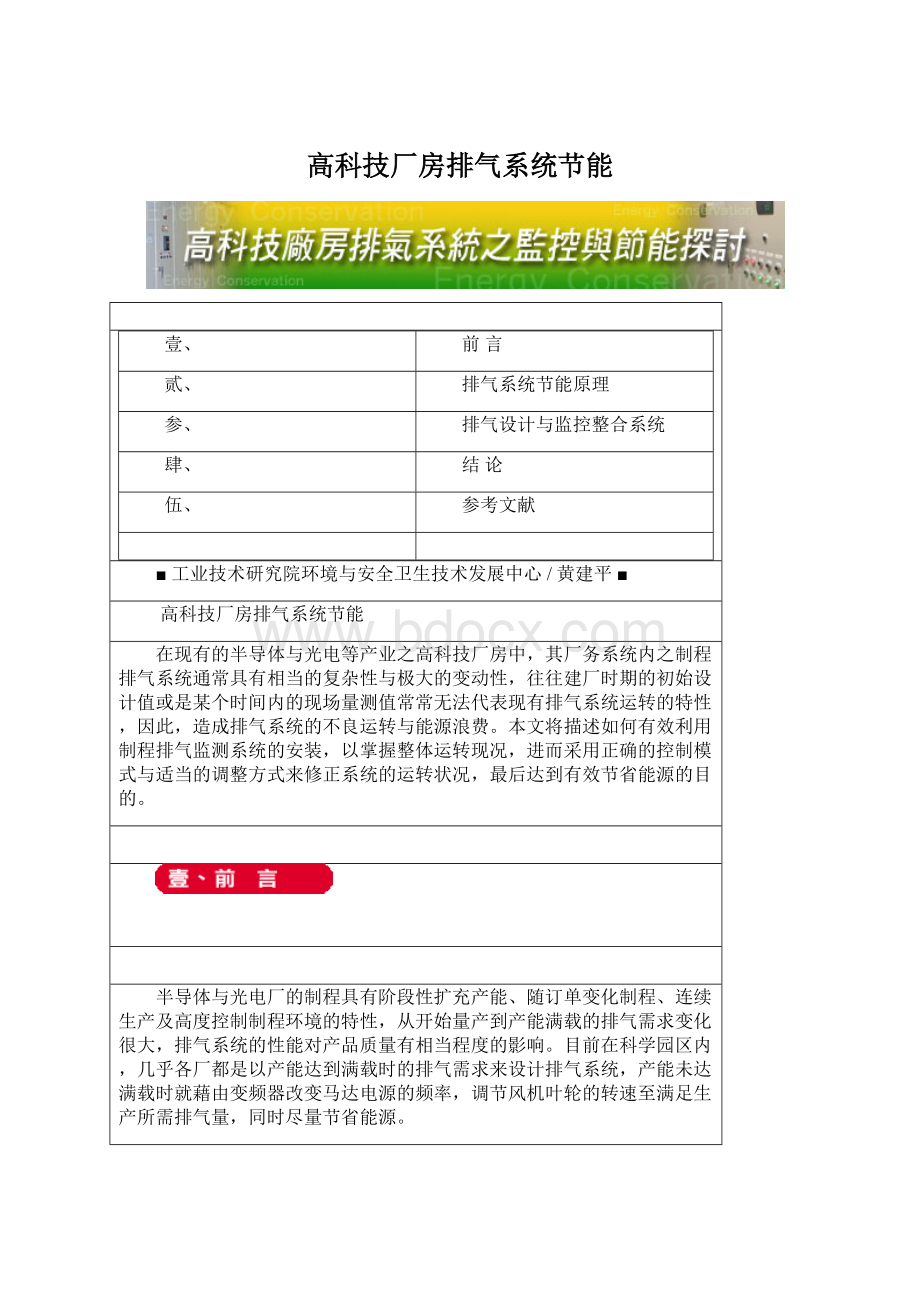
高科技厂房排气系统节能
壹、
前言
贰、
排气系统节能原理
参、
排气设计与监控整合系统
肆、
结论
伍、
参考文献
■工业技术研究院环境与安全卫生技术发展中心/黄建平■
高科技厂房排气系统节能
在现有的半导体与光电等产业之高科技厂房中,其厂务系统内之制程排气系统通常具有相当的复杂性与极大的变动性,往往建厂时期的初始设计值或是某个时间内的现场量测值常常无法代表现有排气系统运转的特性,因此,造成排气系统的不良运转与能源浪费。
本文将描述如何有效利用制程排气监测系统的安装,以掌握整体运转现况,进而采用正确的控制模式与适当的调整方式来修正系统的运转状况,最后达到有效节省能源的目的。
半导体与光电厂的制程具有阶段性扩充产能、随订单变化制程、连续生产及高度控制制程环境的特性,从开始量产到产能满载的排气需求变化很大,排气系统的性能对产品质量有相当程度的影响。
目前在科学园区内,几乎各厂都是以产能达到满载时的排气需求来设计排气系统,产能未达满载时就藉由变频器改变马达电源的频率,调节风机叶轮的转速至满足生产所需排气量,同时尽量节省能源。
然而许多案例显示,排气系统的性能与安全问题一直困扰着厂方,不论是无法达到设计风量,或是因为制程需求不同而排气分布不理想造成排气量过大与不足,亦或是付出庞大的运转维护成本等问题。
另外,在建厂二至三年之后,因管路及设备的老化、长时期的腐蚀与粉尘累积阻塞,以及产能扩充机台增加的情形下,常发生机台或处理设备的风量或静压不足,引起机台或设备当机,产生安全卫生或是产品良率的问题,严重的则会在管内或LocalScrubber内起火引起火灾爆炸危害,使得风险性相对提高。
故整体来说,半导体与光电厂的排气系统最关心的就是安全与效率的问题,如何让排气系统能在安全状态下高效率运作是每个半导体厂殷切盼望的。
基于以上的种种问题,解决之道除了利用量测的方法来加以分析调整外,最有效的方法仍是利用排气监控系统来实时监测与控制,毕竟藉由量测的方法来判定排气系统的运转状态只是一时之间的情形,而且量测的工作不仅费时又费力,高处的量测作业更具有危险性,因此对于变幻莫测的半导体与光电厂之制程排气系统,利用可随时掌握状况的监控系统才是所有问题的解决之道。
要达到排气系统节能可以从降低风机运转压力、降低风机运转风量及提高风机运转效率三个方面着手。
在排气系统运转中,其电能的消耗若排除处理设备的耗能外,真正会导致能源消耗的地方也只有排气系统的风机本身,所以若要达到节能的目的就必须了解风机耗能的原理。
通常风机的效率可以由下列的经验公式一窥端倪:
从以上的说明可知,若要降低风机运转时的消耗电量,则必须有效降低风机的运转马力数,而降低风机的运转马力数则有以下三个方法:
一、降低风机运转压力
风机运转的目的除了要提供一定的风量外,最重要的就是要克服排气系统中所有组件的压损,包含机台的入口损失、输送管路的摩擦损失、处理设备的压损、风机本身的系统效应以及废气排放烟囱的摩擦与出口损失等。
而要降低风机运转的压力时,就必须藉由正确且精细的设计以及优良的施工质量,才可有效达到低压损的运转目标。
但是该部份的方法应在建厂初始设计时就考虑到,若是到了实际运转阶段才考虑到要降低运转的压损时,则所花费的修改成本通常极为庞大,除非在已影响到制程或安全等情况下且别无他法时,才可采用此法,而且应在修改前作详细的量测、评估与设计,以免花了钱亦得不到预期或明显的效果。
由于此方法属于建厂时的设计或修改管路时的考虑,因此本文中不再多作介绍。
二、降低风机运转风量
排气风机的风量规格通常在建厂初期即根据机台的需求风量加总后决定,为了确保实际运转后不会有风量不足的问题,所以必定会取相当的安全系数,例如1.10、1.15、1.20或更高,然而这也导致厂务人员在实际运转后采用极为保守的控制方式。
但排气风量过高造成的能源浪费不只是排气风机本身的电能消耗过多而已,因为排气的风量过多时,相对地空调侧所需的补充外气亦需大量的加入,以维持无尘室内的正压要求,但因为无尘室温湿度的严格要求,补充外气便需经过相当耗能的处理后才可送至无尘室中,而这些处理、输送等设备所须消耗的能源保守估计约为单纯排气风机耗能的二十倍左右。
因此,如何降低风机运转风量将是排气节能最重要的方法,而其详细的运作模式将在后续的内容中加以叙述。
三、提高风机运转效率
虽然风机的选用在建厂初期的设计阶段即会经过一定的程序来决定,包括风机的设计运转压力与设计运转风量,然而设计的优劣、制程的变动、产量的扩充等因素都会直接或间接影响到风机实际的运转点,即使在变频器的控制下,其与原始的设计运转点或系统特性曲线都可能有大幅度的偏移。
尤其当多台风机并联时,因为风箱(Header)前后之排气管路与风机配置情形的差异,导致每台风机的抽气量与运转压力都不相同,此时若利用相同的频率运转,则各台风机的运转效率必定会有相当的差异性,同时也会导致部分的风机运转效率偏低,造成能源的浪费。
因此,若要避免此种现象产生,则有效的风机运转监测与适当的风机控制模式便成为最重要的议题,相关的理论与详细的实施方法将于后续内容中叙述。
制程排气整合系统的主要目的在使厂内排气系统达到安全、效能提升与扩充容易的目的,进而促使制程良率提高与整体运转成本下降。
工研院现有发展中的制程排气设计与监控整合系统整体架构大致可分为管路监控、风机监控、管路设计及装机查核四个部分,其程序整体架构可参考图1所示,而硬件的架构则可参考图2所示,相关说明如下。
图1.排气设计与监控整合系统架构
图2.排气监测系统硬件架构
一、管路监控系统
含一次配与二次配之管路流量(动压)、静压、温度及浓度等之监测,可有效判断机台或管路异常状况以及提供排气系统分析的重要数据。
另外,针对重要的机台或所有的管路系统,皆可以藉由风门角度的控制来达到流量的调整与能源的节省。
因此,藉由管路监控系统的有效运作将可达到风量降低的目的。
管路监控系统主要包含了机台侧二次配管静压与温度监测、次主管尾端静压监测或上游端静压与流量监测以及主管静压监测等。
在次主管的静压与流量监测主要目的有二:
一为有效获知该次主管之粉尘堵塞情形,另一为建立管路静压背景值以作为日后机台扩充之参考与风门调整之依据;而主管路的静压监测布点则有助于整体系统的情势分析,能更精确的获得系统阻塞位置。
本监控系统的主要画面可参考图3所示。
图3.管路监控系统示意图
排气系统的定期量测与检验有其必要性,尤其是产能与需求风量的关系唯有仰赖定期的量测才有评估的依据,因此如果可以直接利用适当的软硬件相结合之监测设施,不仅可以省却工程师定期量测的工作,亦可以有效的随时纪录管路变化情形,并更加精确的估算出产能与排气量的关系,进一步确保系统备用量能可以满足未来产能扩大时之需要。
由于排气系统的变化性极大,故常需要藉由管路的流量与静压量测来分析系统特性,但是因为所需求的量测数据繁复,若是采用人工的量测方式往往需要消耗相当的时间,而所量测的数据误差亦随着时间的变化而加大,因此采用适当的监测设备即可有效的以低成本、高价值的方式获取所需的信息。
针对次主管的流量监测系统,可将各管路的配置机台需求流量键入事先建立的『管路流量需求数据库』中,并藉由实际的流量监测与数据库数值交叉比对,进而调整管路风门开度以达到节能的目的,其管路调整的方式与流程可参考图4,至于实际的调整控制范围之百分比可依各厂的特性加以修改,最重要的在于数据库的建立与调整流程的确立。
图4.管路调整流程
根据调查,平均每个八吋晶圆厂的排气系统风机运转总风量约为10,000CMM,若采用国内的工业用电收费标准计算(约1.84元/度),则平均每一个CMM的排气风量一年的电费约需1,000元(需要处理设备过滤的排气分类如毒酸管、碱管及有机管较高,一般的排气则较低)。
而在半导体与光电厂的良率需求下,通常排气风量的实际运转值与机台最小需求值相差极大,根据实际测量经验差异值约在30%以上,部分更高达50%以上,因此如果能够有效降低运转风量达10%,则每年的电费将可节省1,000,000元以上,这还不包括排气处理设备、相关空调设备的运转成本及因为排气量减少后可降低的补充外气,预估至少是单纯排气风机节能的20倍左右,亦即藉由管路监控系统将排气风量有效控制后,每年每个厂的电费可节省高达两仟万元以上。
二、风机监控系统
包含风机运转的监测与控制、烟囱流量的监测以及处理设备的压损监测等,藉
由风机的运转监测可得知风机的效率高低与系统的曲线偏移,并利用频率修正的控制方式来达到效率提升与节能的目标。
其中烟囱的流量监测不仅有环保法规的要求,利用监测的数值亦可纳入风机分析的输入参数,以降低其它参数撷取的需求。
另外,有关处理设备CentralScrubber等的压损监测则可判断该设备的状态,提供异常时的警报功能,因此藉由本系统的有效运作即可达成提高风机运转效率的目的。
半导体与光电等高科技厂之制程排气系统会因为产能与制程的变动而产生较大的变化,因此提供排气系统动力的后端风机皆会以一对一的方式来搭配变频器,进而控制运转频率,以改变风机所供应的风量与静压。
至于变频器的控制模式不外乎利用管路内某一点或少数几点的静压设定值来连动风机的运转频率,会有不同的地方最多仅止于静压设定点的位置。
静压设定点主要有两种位置:
一为接近风机侧的Header或MainDuct,另一为接近机台侧的Sub-mainDuct或其End-Cap。
兹就其优、缺点与适用情形分析如表1。
表1.风机控制方式比较表
根据表1的分析结果可知,在半导体与光电等厂房之排气系统大多属于复杂性较高的多主管型式,因此其静压设定点的位置应以风机侧的Header或MainDuct为佳,这也是大多数厂选择此种模式的原因。
但是无论设定的位置为何,现有的风机监控方式都会遇到下列的问题:
1.
当产能或制程改变而导致排气需求量降低或增加时,无法有效藉由风机监控系统的控制模式来调整运转频率以达到或接近实际的需求值,也因此常常造成设备负责人员与厂务运转人员间的争执与摩擦。
2.
不同种类的排气系统需求风量皆不相同,通常以一般排气系统及毒酸排气系统的用量最大,其次为有机排气系统,而碱排气系统的用量最小,所以各系统的风机设置数目可从一、两台并联到五、六台并联,甚至有的厂区单一种类的排气系统可高达十台风机并联的情形,在这种并联的方式下,主管与风机汇入口的分布无法完全平均,因此若将风机的频率都调整在相同的数值时,各风机的抽气量会相当的不平均,其效率的差别亦相当大,浪费的能源亦极高。
3.
无论采用的静压设定点有几个,因为半导体与光电厂所使用的机台数量与排气管路相当多,所以无法兼顾到每个机台的排气需求,但是当排气无法达到基本需求时,必定会造成制程的影响,所以备的管理者必定会将排气的使用量尽可能提高,亦即厂内的排气总量一定比实际的最低需求量大很多,造成能源的浪费。
针对现有排气风机运转控制方式不足之处,工研院环安中心研发出一套利用风机性能曲线搭配运转中排气系统特性曲线的监测系统,可有效监测风机的运转操作点与实际效率值,藉由并联风机间的效率差异性来调整个别风机之运转频率,进而提高平均效率值,以节省运转的能源及增进排气系统的稳定度。
另外,若能利用「平均动压量测管」来监测各个次主管甚至二次配的管路流量,并建立机台流量需求数据库,如此一来可藉由两者之间的比对调整风门角度,达到降低排气量以节省运转能源的目的。
一般而言,现有的半导体与光电等高科技厂房之厂务制程排气系统风机皆采用变频器加以控制,另外亦会针对风机的功率与轴承温度加以监测,排放的烟囱也因为环保法规的要求而设置了流量的监控系统,因此,只要将现有的烟囱流量、风机频率、风机功率(或电流,因电压为固定值)等监测数值搭配风机出厂的测试风机曲线数据,则可绘制排气系统的特性曲线以及计算出风机的实际效率值,监测的画面如图5所示。
此外,利用风机运转曲线与系统的特性曲线则可进一步分析排气系统的运转情形,并藉以分析系统的备用量及风机增设的需求性等。
图5.风机监测系统
所谓的风机运转分析法亦即利用现有风机性能曲线与系统特性曲线来预估风机满载时的最大风量Qmax,又因为风机现有的运转风量Qoperate已知,即可获得该风机系统的剩余可供风量Qback(Qback=Qmax-Qoperate)。
其分析法的详细步骤如下:
1.
利用监测系统读取需求数据,包含风机运转频率、风机功率以及烟囱流量Qoperate。
2.
绘制风机性能曲线与系统特性曲线,其中风机性能曲线需包含满载时的运转曲线(50Hz或60Hz,一般国内为60Hz)。
3.
由系统特性曲线与风机满载时之运转曲线交会点订出满载时可提供的风量值Qmax。
4.
将满载风量值减去现有风量值即为风机系统的剩余可供风量值Qback。
实际的分析范例可参考图6,根据此种分析法即可获得各个风机系统剩余风量值。
图6.风机监测与备用量评估分析
综合上述,利用风机监测系统有以下的优点:
1.
了解风机的实际运转点与排气系统的特性曲线,藉以比对风机的运转现况是否落在稳定运转与高效率的区域,若否,则可提供其如何调离不稳定与低效率运转区的参考。
2.
利用风机性能曲线与系统特性曲线的关系可有效预估各风机的备用风量值,并藉以判断是否有增设风机的需求,避免不必要的风机增设浪费亦或风机增设不及而影响制程扩充。
若能有效搭配机台端的次主管或二次配管的流量监测,则将可大量降低运转所需电源,达到节能环保的最大目标。
三、管路设计系统
与排气管路设计相关的应用软件极多,但截至目前为止,依旧尚未发展出一套可以结合建厂设计阶段使用之设计程序以及生产运转阶段使用之监控程序,因此,为了排气监控系统发展的完整性,工研院亦针对现有软件的缺点将其改进后再纳入整体的程序系统中,而该部分的主要功能与其它的设计程序大致相同,其功用则与本文所探讨的主题关联不大,因此本文中不再详加描述。
但是如能透过节能方法,藉由良好的应用程序来协助排气系统的初始设计,即可有效降低排气系统的主管压损,降低生产时风机的运转压力,达到排气节能的最终目的。
四、装机查核系统
本系统的主要目的在协助机台装设时的安全查核与排气功能查核,藉由内建的安全数据库来协助相关工程人员判别排气的分类、管材的选用、管路的设计,并可藉由管路的监测数值与管段压损计算的结果,以查核机台安装后的静压与流量是否正确。
本系统的有效运作将可降低危害发生的机率,并避免管路配置后无法达到机台设备需求的现象发生,同样地,藉由二次配管的有效设计亦可降低二次配管的压损并达到节能的目的。
为实现二十一世纪产业永续发展的前景,实施节约能源与环境保护等重要议题已是众所皆知的事情。
然而如何有效的做到排气系统的节能工作仍旧有很大的发展空间,因此藉由充足且正确的硬件设施安置后,再搭配适当的应用程序与合宜的控制手段,针对排气系统管路的流量监测及排气风机的运转曲线与效率监测等,即可达成真正有效的排气系统节能,并创造企业永续发展与国家环保要求的双赢局面。
‧
1.ACGIH,“IndustrialVentilation-AManualofRecommendedPractice”,AmericanConferenceofGovernmentalIndustrialHygienists,22ndEdition,1995。
2.AMCAPublication201-90,“FansandSystems”,AirMovementandControlAssociation,Inc.,1990。
3.ANSI/AMCAStandard210-85,“LaboratoryMethodsofTestingFansforRating”,AirMovementandControlAssociation,Inc.,1986。
4.黄建平,「排气系统设计与分析技术手册」,工研院环安中心,2003。