金属硅的氧化精炼.docx
《金属硅的氧化精炼.docx》由会员分享,可在线阅读,更多相关《金属硅的氧化精炼.docx(6页珍藏版)》请在冰豆网上搜索。
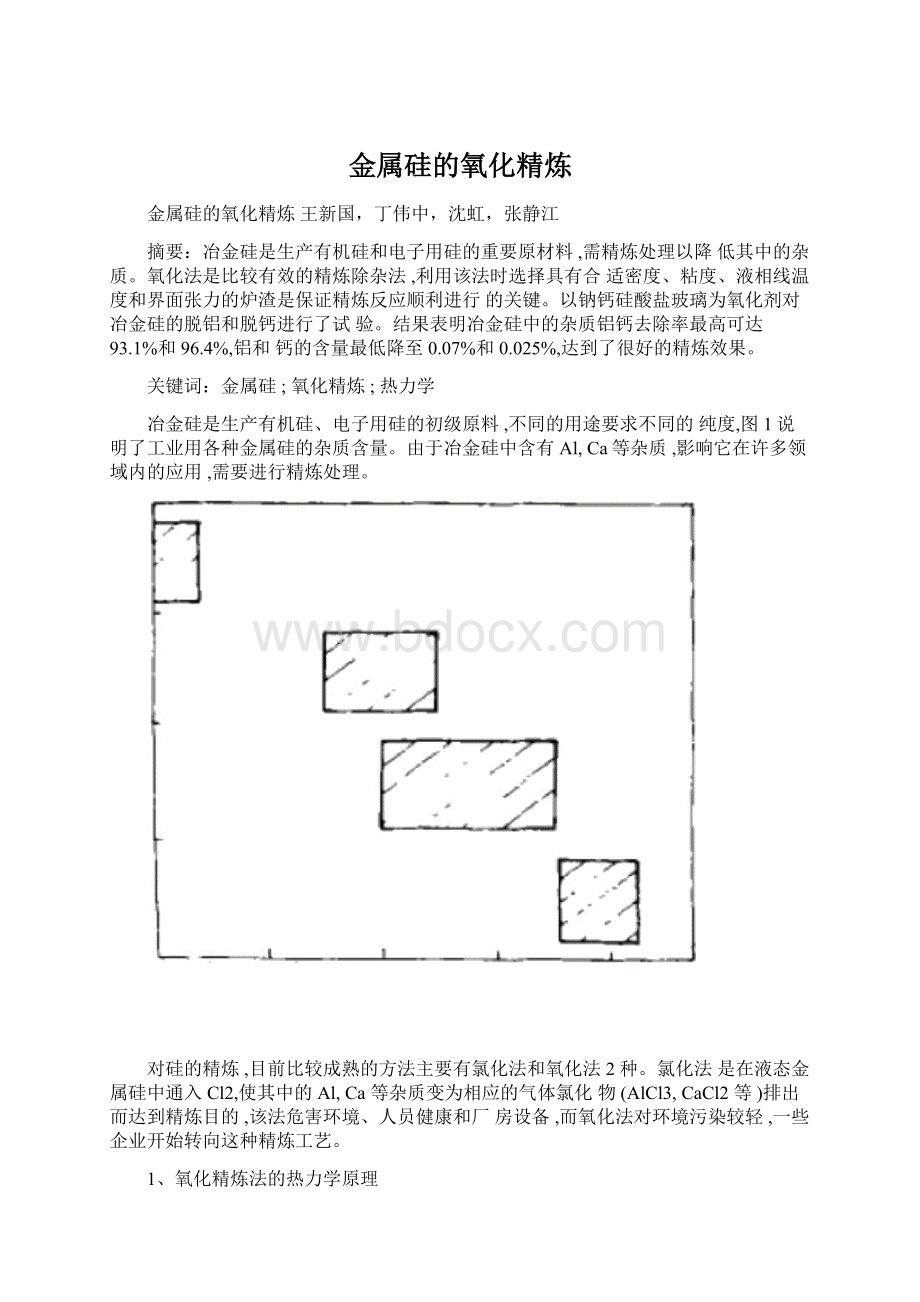
金属硅的氧化精炼
金属硅的氧化精炼王新国,丁伟中,沈虹,张静江
摘要:
冶金硅是生产有机硅和电子用硅的重要原材料,需精炼处理以降低其中的杂质。
氧化法是比较有效的精炼除杂法,利用该法时选择具有合适密度、粘度、液相线温度和界面张力的炉渣是保证精炼反应顺利进行的关键。
以钠钙硅酸盐玻璃为氧化剂对冶金硅的脱铝和脱钙进行了试验。
结果表明冶金硅中的杂质铝钙去除率最高可达93.1%和96.4%,铝和钙的含量最低降至0.07%和0.025%,达到了很好的精炼效果。
关键词:
金属硅;氧化精炼;热力学
冶金硅是生产有机硅、电子用硅的初级原料,不同的用途要求不同的纯度,图1说明了工业用各种金属硅的杂质含量。
由于冶金硅中含有Al,Ca等杂质,影响它在许多领域内的应用,需要进行精炼处理。
对硅的精炼,目前比较成熟的方法主要有氯化法和氧化法2种。
氯化法是在液态金属硅中通入Cl2,使其中的Al,Ca等杂质变为相应的气体氯化物(AlCl3,CaCl2等)排出而达到精炼目的,该法危害环境、人员健康和厂房设备,而氧化法对环境污染较轻,一些企业开始转向这种精炼工艺。
1、氧化精炼法的热力学原理
氧化精炼法的实质,是将液态硅中的杂质元素氧化,使其产物进入渣相,金属与炉渣达到热力学平衡,从而完成脱除杂质的目的。
所用氧化剂主要有气体如O2、固体氧化剂如SiO2及合成炉渣如CaO-Al2O3-SiO2等。
从金属硅中各组元的氧化物生成自由能数据可知,在相同的氧压和温度下,组元与氧的亲和力各不相同,与氧亲和力最大的是Ca,其次是Al,Ti和B,Al-O,Ti-O及B-O之间的亲和力与Si-O之间的亲和力相近,Fe与O之间的亲和力最小。
氧化法精炼就是通过上述选择性氧化原理进行的,尽管氧化剂可采取不同的形式,但杂质得到氧化去除的实质是一样的。
在硅的精炼过程中,主要发生Al,Ca及Si的氧化还原反应,因此将精炼过程热力学研究的对象确定为Si-Al-Ca-O系,即平衡过程是在三元合金Si-Al-Ca和三元炉渣CaO-Al2O3-SiO2之间进行的。
由相律分析知,在温度一定时,只要指定渣系CaO-SiO2-Al2O3中任意两个组元的浓度(或活度),则可确定整个体系。
渣金间的独立反应为:
3/4[Al]+(SiO2)=[Si]+2/3(Al2O3)
ΔGAl/(kJ·-1m)=o-1l05.867-0.0104T
2[Ca]+(SiO2)=[Si]+2(CaO)
ΔGCa/(kJ·-1m)=o-l180.162-0.0364T
2精炼体系的物理化学性质
为了更好地了解精炼过程中渣金间的相互作用,必须对体系的熔点、粘度、密度等基本物性进行分析。
2.1体系液相线温度不同研究者对金属硅的熔点研究结果比较接近,为1414℃,含有杂质后熔点会下降。
精炼过程中炉渣应为熔融态,因此要求炉渣的熔点不能太高。
从SiO2-CaO-Al2O3渣系的相图来看,1550℃时较大成分范围内有一个均匀的液相区。
在实际生产中随着精炼过程的进行,体系不断向环境散热,温度连续降低,较低的温度使炉渣液相区收缩,将影响精炼效果。
所以,一般在精炼时向基渣中加入熔剂物质,使炉渣在不同温度下保持液相状态,从而使合金中的杂质元素有充分的时间去除。
2.2体系密度
精炼过程中,渣系密度应该尽量与合金密度有一定的差别,使精炼产生的炉渣能够上浮。
这样,可以使精炼后的渣金容易分离。
金属硅在1550℃
时的密度为2470kgm·-3。
1550℃时渣系的等密度线测定值见图2
在选择精炼渣系时,对密度的考虑可结合图2进行。
从图2可知,炉渣的密度随SiO2含量的增加而变小,但CaO的含量增加时,炉渣的密度会变大。
在精炼过程中如果选用该炉渣,随着反应的进行,SiO2含量会降低,CaO含量将增加,这将使炉渣的密度随着反应的进行而变大,不利于精炼结束后的渣金分离,易在金属中形成夹杂,故精炼初渣要选择密度小的类
型,比如可以向基炉渣中加入碱金属氧化物等,或者以富含上述氧化物的炉渣代替普通硅酸盐炉渣。
2.3体系粘度
为改善反应的动力学条件,精炼渣系要有好的流动性。
1500℃时渣系的等粘度图如图3,可知渣系的粘度几乎与CaO的等浓度线平行,并且当CaO<17%时渣系粘度出现剧增,说明低浓度范围内CaO含量对渣系粘度的影响很大,从粘度角度考虑,CaO含量不宜过低。
以CaF2形式引入F-会使上述炉渣的粘度降低,流动性改善,加入5%左右的CaF2可使上述渣系粘度降低60%,但随着温度的升高这种作用减弱。
含Na2O13%左右的渣系的粘度在1300℃时为10Pa·s左右,并且随温度的升高而急剧降低。
可见在SiO2-CaO-Al2O3渣系中引入CaF2或Na2O都可不同程度地降低炉渣粘度。
2.4精炼渣系的选择
根据以上分析可知,由于一定温度范围内合金的物化性质基本不变,所以应着重考虑炉渣物化性质对精炼反应的影响。
在选择精炼渣系时要充分考虑其密度、熔点、粘度等,以保证精炼反应的顺利进行。
用普通的钙铝硅酸盐炉渣可能会使渣金分离困难,因此在渣系选择时要注意。
普通钠钙硅酸盐玻璃的密度为约2.50g/cm3,略低于金属硅的密度。
其液相线温度最高为1100℃,在精炼温度(至少在金属硅的熔点1414℃以上)下,其粘度较低(粘度20~30Pa·s)。
此外,由于这种硅酸盐制品中富含SiO2,因此反应性好,其主要成分范围见表1。
Weiss等用Na2O(20%)-CaO(20%)-SiO2(60%)的炉渣与金属硅进行平衡实验时,金属硅中平衡Na含量仅为0.012%,说明该类型的炉渣可以作为金属硅的精炼剂。
本研究采用普通钠钙硅酸盐玻璃作为精炼渣系,对金属硅进行氧化精炼的试验研究。
同时观察底吹Ar气和压缩空气的不同试验条件对精炼结果的影响。
3实验
3.1实验原料
试验用原料粗硅由某厂提供,为了调整其中所含的[Al],[Ca]含量,采用分析纯级铝块(99.99%)和SiCa合金作为合金剂。
其成分见表2。
试验用Ar气纯度为99.994%。
所用钠钙硅酸盐玻璃的成分范围见表1,精确的成分在试验结果的化学分析过程给出。
3.2实验设备及过程
试验在100kVA的感应炉内进行。
实验过程采用“钠钙硅酸盐玻璃+金属硅+底吹气体”方式进行。
渣金比0.24,底吹气体为Ar气和压缩空气2种,流量分别为2.5L/min和1.5L/min。
温度为1550±30℃。
在不同时刻取渣金样品以备化学分析,并且在精炼反应进行一段时间后扒渣,重新加入新玻璃渣进行操作。
渣系和合金体系中的(Na2O)和[Na]含量采用PyeUnicomLtd.-SP9-800型原子吸收光谱仪进行分析。
渣系组元和合金中的[Al],[Ca]含量用PerkinElmer-Plasma400ICPSpectrometer等离子发射光谱仪进行分析。
4结果及讨论
底吹氩气和空气进行精炼时渣金成分随时间的变化关系曲线见图4和图
∣[A1]0.158%
<[Cβ]0.0339%
I[Na]0.0395%
■—[Al]•—[Ca]♦-[Na]
NeWSlag
OIO20304050607080
Refiningtime/min
∏—AljQjO—CaO
图4金属硅粘炼过程体系成分随时间的
钠钙硅酸盐玻璃渣对金属硅中[Al],[Ca]杂质元素的去除非常有效(图4)。
在精炼反应进行到35min时,71.8%的[Al]和92.4%的[Ca]已经得到去除。
将初始炉渣扒掉,加入相同量的新渣,30min后[Al],[Ca]含量分别达到0.16%和0.034%,杂质最终去除率分别为83.5%和96.4%。
可见Ar气搅拌改善了反应的动力学条件,可以在短时间内达到比较好的精炼效
同时由于玻璃中含有氧化钠,使金属硅中的[Na]含量也经历了一个先增加再降低的变化过程。
[Na]非常活泼且易挥发,当有[Si]存在时,其氧化物(Na2O)含量将变得不稳定,发生如下反应:
2(Na2O)+[Si]=4Na(g)+SiO2反应前期,金属硅中[Na]含量逐渐升高,渣中(Na2O)含量在逐渐降低。
Haaland等指出,与2Na2O·SiO2形式的渣进行平衡时,上述反应的pNa(g)最大,除此之外,随着(SiO2)含量的增加或降低,上述蒸气压都将降低。
因此随着反应的进行,金属硅中的[Na]含量又会逐渐下降。
Haaland等实验中的钠含量变化趋势与本研究相同。
以压缩空气代替Ar气进行底吹搅拌的实验结果见图5。
从实验结果看,底吹压缩空气对[Al],[Ca]的去除都非常有效。
精炼的最终结果,[Al],[Ca]杂质含量分别达到0.0701%和0.0248%,去除率为93.1%和88.7%。
初始[Al]含量几乎相同的金属硅用压缩空气精炼的结果比Ar气搅拌的结果提高了一倍,这是因为底吹压缩空气一方面可以加强精炼体系的搅拌,另一方面为精炼过程引入了更多的氧化剂。
Haaland等在1500℃时,利用钠钙废玻璃渣(渣/金比为0.3)与底吹空气(流量1.5L/min)对初始铝、钙含量为0.6%和0.3%左右的金属硅进行了精炼处理,其试验结果也在图5中列出,尽管杂质铝、钙和钠的变化趋势相同,
但在处理时间相同时,他们的铝、钙脱除率比本研究低。
Weiss等在1500℃时,利用Na2O(15%)-
SiO2(85%)的炉渣对初始杂质含量为Al0.44%和Ca0.09%的金属硅进行精炼处理(渣金比2.5∶1),处理时间60min时铝钙含量分别为0.244%和0.002%,其杂质去除率分别为45%和97%,可见Weiss等的铝去除率比本研究的结果要低,钙的去除率基本相同。
从本研究结果和相关文献结果的比较看出,钠硅酸盐玻璃是一种有效的精炼渣系。
尽管在精炼过程中,可能使金属硅中的钠含量有所增加,但其作为普通高纯硅(杂质总量要求<0.5%),在应用过程中不构成大的危害。
5结论
氧化精炼法可以有效去除金属硅中的铝和钙等杂质,但由于普通钙铝硅酸盐炉渣的密度与金属硅的密度相近或略大,在精炼时可能发生渣金分离困难的现象,利用同样具有精炼作用且密度较低、粘度较小的钠钙硅酸盐玻璃作为精炼渣系可克服渣金分离困难。
在温度为1550℃、渣金比为0.24的试验条件下,底吹氩气对初始铝钙含量分别为0.953%和0.902%的金属硅精炼65min后,杂质的去除率分别为83.5%和96.4%,达到了很好的精炼效果。
在相同的条件下,底吹压缩空气的操作结果表明杂质铝钙的去除率也达到了93.1%和88.7%。
由于试
验过程使用了含钠氧化物炉渣,使精炼结束后的合金中钠含量有所增加但其作为普通高纯硅(杂质总量要求<0.5%),应用过程中增加的钠不构成大的危害。
说明普通钠钙硅酸盐玻璃是冶金级金属硅精炼的一种良好氧化剂。