数控机床常用计算项目与计算方法.docx
《数控机床常用计算项目与计算方法.docx》由会员分享,可在线阅读,更多相关《数控机床常用计算项目与计算方法.docx(44页珍藏版)》请在冰豆网上搜索。
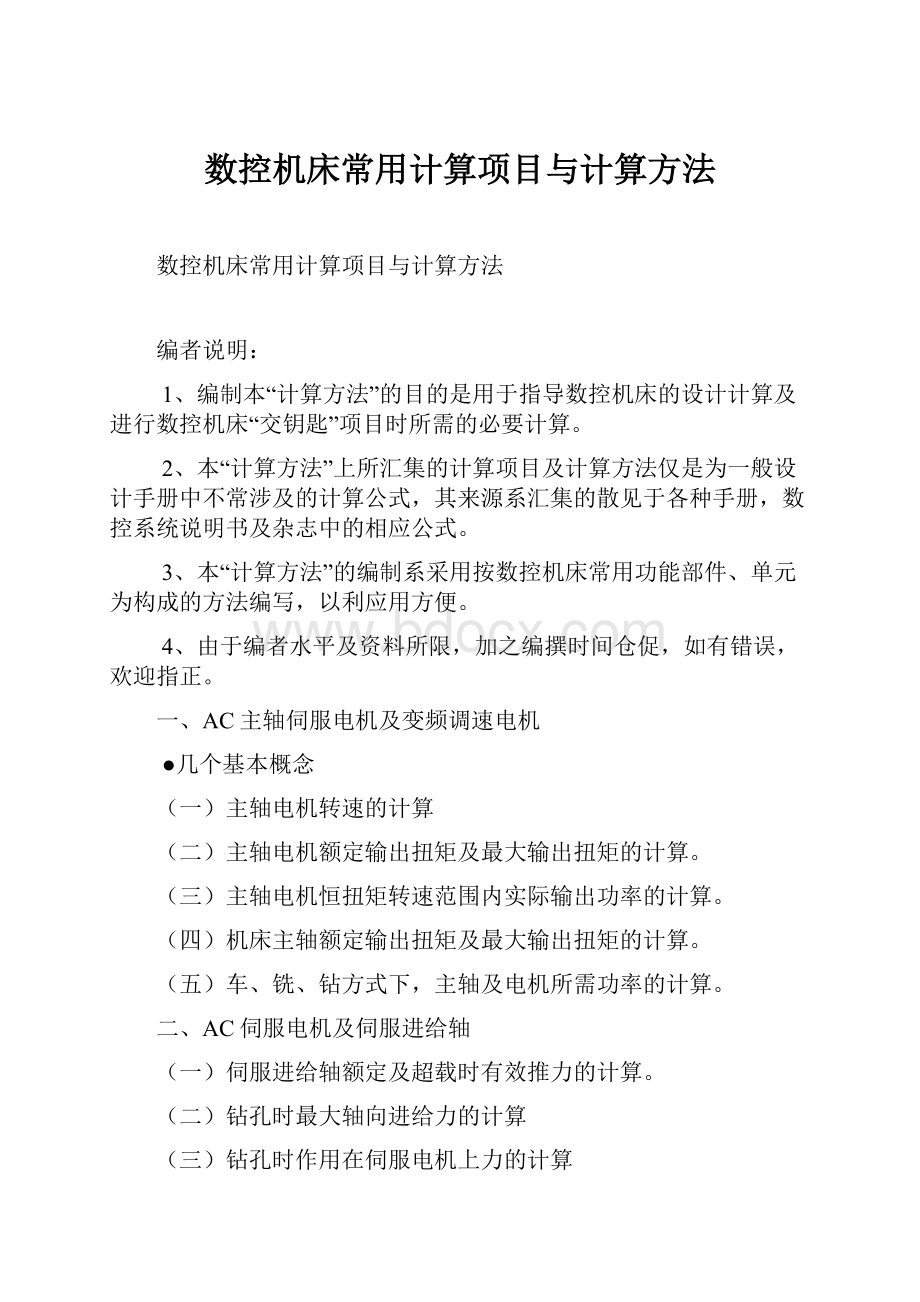
数控机床常用计算项目与计算方法
数控机床常用计算项目与计算方法
编者说明:
1、编制本“计算方法”的目的是用于指导数控机床的设计计算及进行数控机床“交钥匙”项目时所需的必要计算。
2、本“计算方法”上所汇集的计算项目及计算方法仅是为一般设计手册中不常涉及的计算公式,其来源系汇集的散见于各种手册,数控系统说明书及杂志中的相应公式。
3、本“计算方法”的编制系采用按数控机床常用功能部件、单元为构成的方法编写,以利应用方便。
4、由于编者水平及资料所限,加之编撰时间仓促,如有错误,欢迎指正。
一、AC主轴伺服电机及变频调速电机
●几个基本概念
(一)主轴电机转速的计算
(二)主轴电机额定输出扭矩及最大输出扭矩的计算。
(三)主轴电机恒扭矩转速范围内实际输出功率的计算。
(四)机床主轴额定输出扭矩及最大输出扭矩的计算。
(五)车、铣、钻方式下,主轴及电机所需功率的计算。
二、AC伺服电机及伺服进给轴
(一)伺服进给轴额定及超载时有效推力的计算。
(二)钻孔时最大轴向进给力的计算
(三)钻孔时作用在伺服电机上力的计算
(四)进给伺服电机的选择计算
(五)刀架用伺服电机的选用计算
(六)直线伺服进给轴参考点减速档块宽度LDW的计算
(七)倾斜(垂直)进给轴是否增加平衡装置的计算
三、其它计算
(一)切削力、切削功率及切削扭矩的计算
(二)主轴轴承dMN值的计算
(三)主轴轴承润滑脂封入量的计算
(四)螺纹车削走刀次数的计算
(五)根据粗糙度要求,计算合理切削工艺参数的计算
一、AC主轴伺服电机及变频调速电机
●基本概念
1、电机的功率负载特性:
做为一般驱动负载工作的回转电机有以下三种常用的功率负载特性:
(1)连续工作制(S1):
是指该电机在额定工作条件和负载条件下允许长时间、不间断的工作。
(2)短时工作制(S2):
是指该电机在规定的短时间内允许超出额定功率进行运转工作,其超载时间优先采用10、30或60分钟等。
(3)断续工作制(S3):
是指该电机应按一定的通、断周期进行工作,以保证电机在大电流、超载情况下不致因电机温度过高,击穿绝源而烧坏。
在S3工作制下工作的电机允许的每一通、断工作周期为10分钟,例FANUCAC主轴电机规定在50%ED率下(S3工作制),其循环时间周期为10分钟(即ON:
5min,OFF:
5min)。
目前的AC主轴电机有一个重要特性就是允许在S2或S3工作制下运转,其实际就是一种短的工作制电机。
如FANUC的α11型主轴电机的额定连续输出功率为11kw。
S2工作制下的30分钟时间内允许的超载功率为15kw。
因数控机床在实际超载切削时每一次走刀时间很难超出30分钟,故许多机床制造厂在标定其生产的某型机床动力参数时,常用主轴电机的30分钟超载功率做为其样本上标示的主轴电机的主参数。
同样,进行数控机床设计时,设计者亦充分利用好主轴电机的这种特性。
特别需要指出的是,目前多采用的标准型普通变频电机,其仅能在S1工作制下工作,不允许超载使用,因此设计者选用时必须注意。
但随着技术的发展,最近市场上出现了一种称为“变频主轴电机”的新型变频电机,其恒功率的拐点转速控制频率(周波)为33.3Hz,不但大幅降低了电机的拐点转速,提高了电机低速时的特性能力,且允许在S2工作制下进行30分钟超载运行,是一种具有良好价格性能比的新型电机。
2、电机的负载特性及主轴电机的拐点转速nj:
无论AC主轴电机还是变频调速电机,其在nj拐点转速以上进行无级调速时,均基本为恒功率调速。
即随着电机转速的提高,其输出功率保持基本不变,而电机的输出扭矩则随转速的升高而下降;其在nj拐点转速以下进行无级调速时,均为恒扭矩调速,即随着电机转速的下降,其输出扭矩恒定不变,而电机的输出功率则随转速的降低而下降。
因此机床主轴在低速段进行粗加工而转速又落入电机的恒扭矩段转速时,设计者必须认真校核此时电机的实际输出功率能否满足切削所实际需要的功率,否则会出现“闷车”现象。
在我国,因发电厂采用50Hz频率(周波)数发电,故对标准AC主轴电机(如FANUC的α系列)和标准普通变频电机而言,因多采用4极(4P)绕组电机,则nj拐点转速值应为1500r/min。
无论何种调速电机,根据机床的负载特点,其nj拐点转速值越低,其与电机最高转速间的比值越大(恒功率调速比),则该电机的力能特性越好。
(一)主轴电机转速的计算:
2×F
公式:
n=———×60
P
式中:
n:
电机转速
F:
控制赫兹(周波)数
P:
电机的极数
注:
日本FANUCα系列主轴电机参数如下:
1、调频范围:
α0.5~α6型:
0~266.6Hz
α8~α22型:
0~200Hz
α30~α40型:
0~150Hz
2、极数(P):
FANUC标准系列主轴电机多为4
以FANUCα12型主轴电机为例计算(0-200Hz):
电机最高输出转速:
2×200
n=———×60=6000r/min
4
电机恒功率输出转速(电机拐点转速)
2×50
n=———×60=1500r/min
4
(注:
电机50Hz以下为恒扭矩特性输出)
(二)主轴电机额定输出扭矩及最大输出扭矩的计算:
式中:
N:
主轴电机额定/30分超载的功率(KW)
nj:
主轴电机恒功率拐点转速(r/min)
以FANUCα12型主轴电机为例计算(11/15kw)
则:
电机额定输出扭矩(连续输出扭矩):
电机最大输出扭矩(30分钟超载):
注:
(1)根据数控机床切削作业时的特点,计算主轴电机输出扭矩时一般均将30分钟超载扭矩做为标准扭矩数值。
(2)扭矩值为kg.m时除于0.102即可换算成Nm。
(三)主轴电机恒扭矩转速范围内输出功率的计算
计算的目的:
当主轴电机在恒功率转速范围下进行运转时,随着转速的下降,主轴电机的输出功率亦随之下降,此时在切削参数选择不当时,极易出现闷车现象,计算出主轴电机特定转速下的输出功率,是为校核切削时所消耗的功率是否符合为目的。
公式:
P(kw)=1.0269×n(r/min)×T(kg.m)/1000
式中:
P(kw):
所要求得的电机功率
n(r/min):
电机的实际转速(恒扭矩段内)
T(kg.m):
电机的恒扭矩值
举例:
仍以FANUCα12型主轴电机为例(11/15kw)
(1)电机30分钟超载时的输出扭矩:
(2)求电机在1000转时电机的输出功率(30分超载)?
P(kw)=1.0269×1000r/min×9.74(kg.m)/1000=10.002kw
(四)机床主轴额定输出扭矩及最大输出扭矩的计算:
●计算的目的:
电机上所输出的扭矩不等于是主轴上所输出的扭矩,因为在机床主传动链上常采用皮带轮或变档齿轮等进行降、升速,如采用的是降速传动时,则有一个降速比i对电机输出扭矩的放大作用,这就是机械设计上常采用一个小功率电机,通过大的降速比来拖动大的运动负载的原因。
公式:
式中:
M:
主轴的输出扭矩(kg.m)
N:
主电机额定功率或30分超载功率(KW)
Nj:
主电机恒功率时的拐点转速(r/min)
i:
传动链降速比
η:
机械传动效率(皮带轮直接传动时取0.96)
注:
根据数控机床切削作业的特点,计算主轴的输出扭矩时,一般均按主轴30分钟超载时的最大输出扭矩来计算。
(五)车、铣、钻方式下主轴及电机所需功率的计算
注:
在欧、美、日等国家的切削手册、资料中,在进行切削力及切削功率计算时,常采用单位切削力和单位切削功率的概念。
所谓单位切削力是指“单位切削面积上的主切削力”,用P表示,单位为N/mm2;所谓单位切削功率是指“在单位时间内切除单位体积的金属所消耗的切削功率”,用Ps表示,单位为KW/(mm3/S)。
下面所述的“车、铣、钻方式下主轴及电机所需功率的计算”是日本FANUC公司手册上所推荐的,计算车、铣、钻不同切削方式时公式中的每kw金属去除率MRt,MRm,MRd值,应从相应的切削手册或资料中查出。
a.车削时
切削条件
(1)主轴转速:
Ns(r/min)
(2)工件直径:
Dt(mm)
(3)进给速度:
fr(mm/r)
(4)切削深度:
t(mm)
(切削公式)
(1)切削速度:
Ⅴc=π×Dt×Ns(mm/min)
(2)进给率:
fm=fr×Ns(mm/min)
(3)金属去除率:
Q=t×fr×Vc/1000(cm3/min)
=t×fr×π×Dt×Ns/1000(cc/min)
Q=π×Dt×t×fm/1000(cc/min)
(4)机床主轴所需功率:
Ps=Q/MRt(KW)
式中:
MRt=每kw的金属去除率(cc/min/kw)
(5)主轴驱动电机所需的功率:
PM=1/η×Q/MRt
式中:
η=主轴驱动的效率(%)
b.铣削时
(切削条件)
(1)主轴转速:
Ns(r/min);
(2)铣刀直径:
Dm(mm)
(3)铣削宽度:
W(mm);(4)铣削深度:
t(mm)
(5)铣刀齿数:
n(齿数);(6)进给:
ft(mm/每齿)
(切削公式)
(1)切削速度:
Ⅴc=π×Dm×Ns(mm/min)
(2)进给率:
fm=ft×n×Ns(mm/min)
(3)金属去除率:
Q=W×t×ft×n×Ns/1000(cm3/min)
Q=W×t×fm/1000(cc/min)
(4)机床主轴所需功率:
Ps=Q/MRm(KW)
式中:
MRm=每kw的金属去除率(cc/min/kw)
(5)主轴驱动电机所需的功率:
PM=1/η×Q/MRm(kw)
式中:
η=主轴驱动的效率(%)
c.钻削时
(切削条件)
(1)主轴转速:
Ns(r/min)
(2)钻头直径:
Dd(mm)
(3)进给:
fr(mm/r)
(切削公式)
(1)切削速度:
Ⅴc=π×Dd×Ns(mm/min)
(2)进给率:
fm=fr×Ns(mm/min)
(3)金属去除率:
Q=π/4×Dd2×fr×Ns/1000(cm3/min)
Q=π/4×Dd2×fm/1000(cc/min)
(4)机床主轴所需功率:
Ps=Q/MRd(KW)
式中:
MRd=每kw的金属去除率
(5)主轴驱动电机所需的功率:
PM=1/η×Q/MRd(kw)
式中:
η=主轴驱动的效率(%)
二、AC伺服电机及伺服进给轴
(一)伺服进给轴额定及超载时有效推力的计算
注:
本计算是数控机床设计时一项较重要的计算,其进给轴所实际达到的进给推力是机床能力的反映,也是做工件切削工艺方案时对切削参数进行效核的重要依据。
1、与计算有关的符号的含义(准备知识)
(1)Fi:
进给轴的有效推力(kg)
(2)TMi:
伺服电机的输出扭矩(kg.Cm)
注:
a.伺服电机TMi值在不同的过载扭矩状态下允许有不同的最大输出扭矩值及对应的允许的不同通、断时间,该允许的通、断时间应根据具体选用型号的伺服电机的“负载、扭矩、时间特性曲线图”(伺服电机手册上有)或用公式进行计算。
方法如下:
根据已知或需要的电机ON(通)时间及负载扭矩百分比值(负载、扭矩百分比=所需超载扭矩/电机连续额定扭矩×100%),利用特性曲线图得出负载、扭矩百分比值后,用下式计算电机的OFF(断)时间:
例:
选用FANUCα6伺服电机
根据FANUCα系列电机手册上该电机的“扭矩特性表”查得,α6电机在ON时间为8min,扭矩超载值为150%时,负载的百分比为40%,则该电机在ON8min时的OFF时间可用公式求出:
=12(min)
注:
此时α6电机的OFF时间亦可用下式求得:
已知α6电机额定扭矩为61kg.cm,其超载150%时,扭矩为:
61×150%=91.5kg.cm
超载扭矩
则:
OFF(min)=ON(min)—————
额定扭矩
91.5
=8(min)———
61
=12(min)
b.TMi值在不同的负载过载扭矩下有不同的输出扭矩值及相对应的不同的ON(通)、OFF(断)时间,通常数据如下:
负载
状态
通、断
100%
150%
180%
ON
连续
8min
3min
OFF
0
12min
7min
(3)i:
进给传动链的降速比(其值与有效进给推力有关)。
(4)T:
滚珠丝杠螺距(导程),(其值与有效进给推力有关)。
(5)η:
进给轴的传动效率,电机与丝杠直连时取0.95,电机与丝杠降速间连时取0.9。
(6)TL:
被移动部件无负载时所需消耗的静扭矩(kg.cm)
Fa2×T×i
TL=————
20×π×η
式中:
TL:
无负载时的移动部件的静扭矩(摩擦扭矩)
Fa2:
部件移动时的磨摩阻力
i:
进给传动链降速比
T:
滚珠丝杠螺距(导程)(mm)
注:
关于Fa2摩擦阻力的计算:
Fa2=(μ+fg)W
式中:
μ=摩擦系数(滑动导轨取0.15,滚动导轨取0.08)
fg=镶条(斜铁)的紧固力系数,有时取0.01,滚动导轨取0.08。
例,已知条件如下:
●移动部件总重量:
W=157kg
20(主动)
●传动链降速比:
i=——————(同步带降速)
24(从动)
●滚珠丝杠螺距;T=6mm
●铸铁滑动导轨:
μ=0.15
●有镶条(斜铁):
fg=1.0
则:
a:
Fa2=(μ+fg)W=(0.15+1)×157=180.55
Fa2×T×i180.55×6×20/24
b:
TL=—————=—————————
20×π×η20×3.14×0.9
=15.97≈16kg.cm
2、Fi进给轴有效推力的计算
公式:
Fi=20×π×η(TMi-TL)/T×i
(式中符号含义详见前面解释)
例:
根据公式和已知条件计算某型数控机床X轴在各种负载状态下的有效推力及该轴电机的通、断时间。
已知条件:
a.电机型号:
FANUCα6(额定输出扭矩:
61kg.cm(6N.m)
b.其余:
与前面TL值计算时举例条件相同。
(1)计算电机不同负载条件下的输出扭矩及电机通、断时间:
●61kg.cm×100%=61kg.cm(ON:
连续,OFF:
0)
●61kg.cm×150%=91.5kg.cm(ON:
8min,OFF:
12min)
●61kg.cm×180%=109.8kg.cm(ON:
3min,OFF:
7min)
(2)计算三种不同负载扭矩下的对应有效推力:
●100%Fi=20×π×η(TMi-TL)/T×i
=20×3.14×0.9(61-16)/6×20/24
=508.6kg
●150%Fi=853.45kg
●180%Fi=1060kg
(3)将上面计算结果列表如下
轴
降速比
螺距
TMi(kg.cm)
Fi(kg)
无负载扭矩
i
T
100%
150%
180%
100%
150%
180%
TL
X
20/24
6mm
61
91.5
109.8
508.6
853.4
1060
16kg.cm
ON
连续
8min
3min
OFF
0
12min
7min
特别提示:
计算Fi(进给轴有效推力)时,移动部件的重量W值的准确是十分重要的。
(二)钻孔时最大轴向进给力的计算:
注:
在钻头进行作业时,在机床的Z轴方向会产生最大轴向进给力,因此根据机床已得知的Z轴有效进给力来校核钻头钻孔作业时所产生的轴向力对选定钻头的切削参数是有意义的。
1、用高速钢金头钻铸铁工件的计算
公式:
M=D1.9·S0.8·HB0.6
P=2.6·D·S0.8·HB0.6
式中:
V=切削速度(m/min)
M=扭矩(kg.mm)
T=刀具耐用度(min)
S=进给量(mm/r)
π=圆周率
N=切削功率(kw)
P=轴向力(kg)
HB=布氏硬度(本公式系按HB=220时得出)
D=钻头直径(mm)
2、用高速钢钻头钻钢时最大轴向力的计算:
340·D0.4
公式:
T=(——————)5
V·S0.5·δb0.9
M=1.65·D2·S0.8·δb0.7
P=3.3·D·S0.7·δb0.75
式中:
V=切削速度(m/min)
P=轴向力(kg)
S=每转进给量(mm/r)
N=切削功率(kw)
T=刀具耐用度(min)
D=钻头直径(mm)
M=扭矩(kg.cm)
π=圆周率
δb=材料的抗拉强度(kg/mm2)
注:
材料为45#钢,热处理T235时,δb≥75kg/mm2,不热处理时,δb=55kg/mm2。
(三)钻孔作业时,作用在伺服电机上力的计算:
1、计算目的:
因数控车床是在刀架上安装钻头,又因在数车上推力主要是由作用在钻头上的切削力所产生。
(钻头的切削刃能产生非常大的推力,这是因钻头钻削刃上的前角越接近钻头中心越小,而钻头的横刃部位带有很大的负前角的缘故)。
所以由此而产生的推力负载是由下图所示的伺服电机一侧所承受的,钻削时如负载超出该轴伺服电机的能力,则电机会产生过载报警,机床停止。
因此,在数控车床上必须准确确定,计算出伺服进给轴的有效推力值。
2、作用在伺服电机上的力:
(1)可以从上图求出用钻头加工所产生的推力Ps。
(2)床鞍的重量(Ws)对推力的影响(Pws)可用公式:
Pws=μ·Ws来表示。
μ是磨擦系数。
(3)床鞍的扭曲对推力也有影响(Pαs)。
从图所求出的由Ps所决定的扭曲可用公式:
Ps·H
Fs1=————来表示
Ls
由于床鞍重量所产生的扭曲用公式:
Ws·Lc
Fs2=————来表示
Ls
因此由床鞍整体所决定的扭曲用公式:
Fs=FS1-Fs2来表示
由扭曲所影响的推力Pαs可用公式:
Pαs=2μ·Fs来表示
由此可知钻孔加工所产生的全部推力(PAS)可用公式:
PAS=PS+PWS+Pas来表示。
另外,把在钻头作业中伺服电机上所产生的临界扭矩用Tp表示,那么滚珠丝杠上所产生的扭矩TB可表示为TB=Tp/i,(i是齿轮箱或同步带轮的减速比)。
滚珠丝杠上产生的切向力FB可表示为:
FB=TB/r,r是滚珠丝杠的半径。
从些关系中可进一步推导出在滑鞍上所产生的允许推力为:
FB·π·2r·Y2Tp·π·Y
PBS=———————=——————
PP·i
Y是机械效率,P是滚珠丝杠的螺距(mm)
在钻孔加工中条件必须是:
PBS>PAS
(五)刀架用伺服电机的选用计算
刀架用伺服电机的负载情况有别于直线伺服运动轴,其主要区别在于刀架在进行分度时的受力是主要承受不平衡扭矩时的启动加速扭矩。
本节选用的计算方法仅是提供了一种选用计算实例,设计者遇到同类计算问题时可直接套用。
(以MJ-520伺服刀架设计计算为例)
一、计算目的:
校核所采用的伺服电机在最大不平衡扭矩下,进行加速时,电机输出的最大扭矩是其额定扭矩的3倍以内为目标。
二、伺服电机参数:
型号:
三菱HC-SF102功率:
1.0kw额定扭矩:
48.7kg.cm
最大输出扭矩:
146kg.cm转速:
标准2000r,最高:
3000r/min
转动惯量:
J=13.6kg.cm2,GD2=54.4kgf.cm2
48.7×3=146kg.cm(14.4N.m)
(48.7kg.cm=4.78N.m,146kg.cm=14.4N.m)
三、刀架参数:
1、刀位数:
10
2、减速齿轮比i=12=3×4
(Z1=18×2.5,Z2=54×2.5i=3A=90mmZ3=18×2.5,
Z4=72×2.5i=4A=112.5mm)
3、最大镗刀杆重量(Φ40×300):
2.9kg
4、镗孔刀座重量:
3.4kg
5、刀盘尺寸(直径×宽):
Φ420×90
πD2/4×H3.14×422/4×9.0
6、刀盘重量:
——————×7.8=————————×7.8
10001000
12462.66
=——————×7.8=97kg(式中7.8为钢的比重)
1000
注:
因伺服电机可实现无级调速,另外充分考虑到MJ-520的规格,综合考虑,确定以下刀架转位参数:
(1)转一刀位时间:
0.2sec,锁紧时间:
0.2秒
(2)转一刀位并锁紧时间:
0.4sec(锁紧:
0.2sec)
(3)转最远刀具时间:
0.2×5=1.0秒
(4)伺服电机分度转速:
60/0.2×10×i=360r/min
(5)刀盘转速:
30r/min
0.2sec
(6)转位加速时间:
△t1=————=0.1(秒/单步)
2
三、计算并校核伺服电机的扭矩:
1、T:
伺服电机必须的扭矩
T=T1+T2+T3(kgf.m)
式中:
T1:
传动链摩擦扭矩(kgf.m)
T2:
不平衡扭矩(必要的扭矩)(kgf.m)
T3:
起动扭矩(加速扭矩)(kgf.m)
●计算T1:
T1=W.R.μ.i(传动链中的摩擦扭矩)
式中:
W:
工件重量(kgf),R:
工件回转半径(m)
μ:
所有轴承的摩擦系数(本刀架取0.15)
i:
减速比
则:
T1=97kg×0.21m×0.15×12=36.7kg.cm=0.367kg.m
●计算T2(不平衡扭矩):
T2=(r1W1+RW2+r3W3+......)i
11
(注:
i=———=——)
3×412
注:
上图是镗孔刀座在刀盘上分布的一种极端情况,一般情况下不可能出现,故W的重量可略为减少进行计算。
取W=5.5kg
1
则:
T2=[(0.15×W1)×2+(0.21×W2)×2+(0.26×W3)]×——
12
1
=(1.65+2.31+1.43)×12=5.39×——=0.5(kgf.m)
12
●计算T3(加速扭矩)
GD2×NGD2×i2×N
公式:
T3=————-×i=——————
375×△t375×△t
式中:
GD2飞轮距=重量×回转直径(kgf.m2)
△t:
刀架加速时间(sec)
N:
刀盘转速(r/min)
1、设刀盘上装5个刀座并均装镗刀杆时的GD2:
公式:
GD2=4WK2(kgf.m2)
式中:
W=回转体的重量
r12+r22
K2=————+R2
2
因MJ-520刀盘可简化为实心圆盘,则上式可为:
r12+0r12
K2=————+02=——
22
简图如下:
r12
则:
GD