级 常减压与催化裂化控制任务解析.docx
《级 常减压与催化裂化控制任务解析.docx》由会员分享,可在线阅读,更多相关《级 常减压与催化裂化控制任务解析.docx(19页珍藏版)》请在冰豆网上搜索。
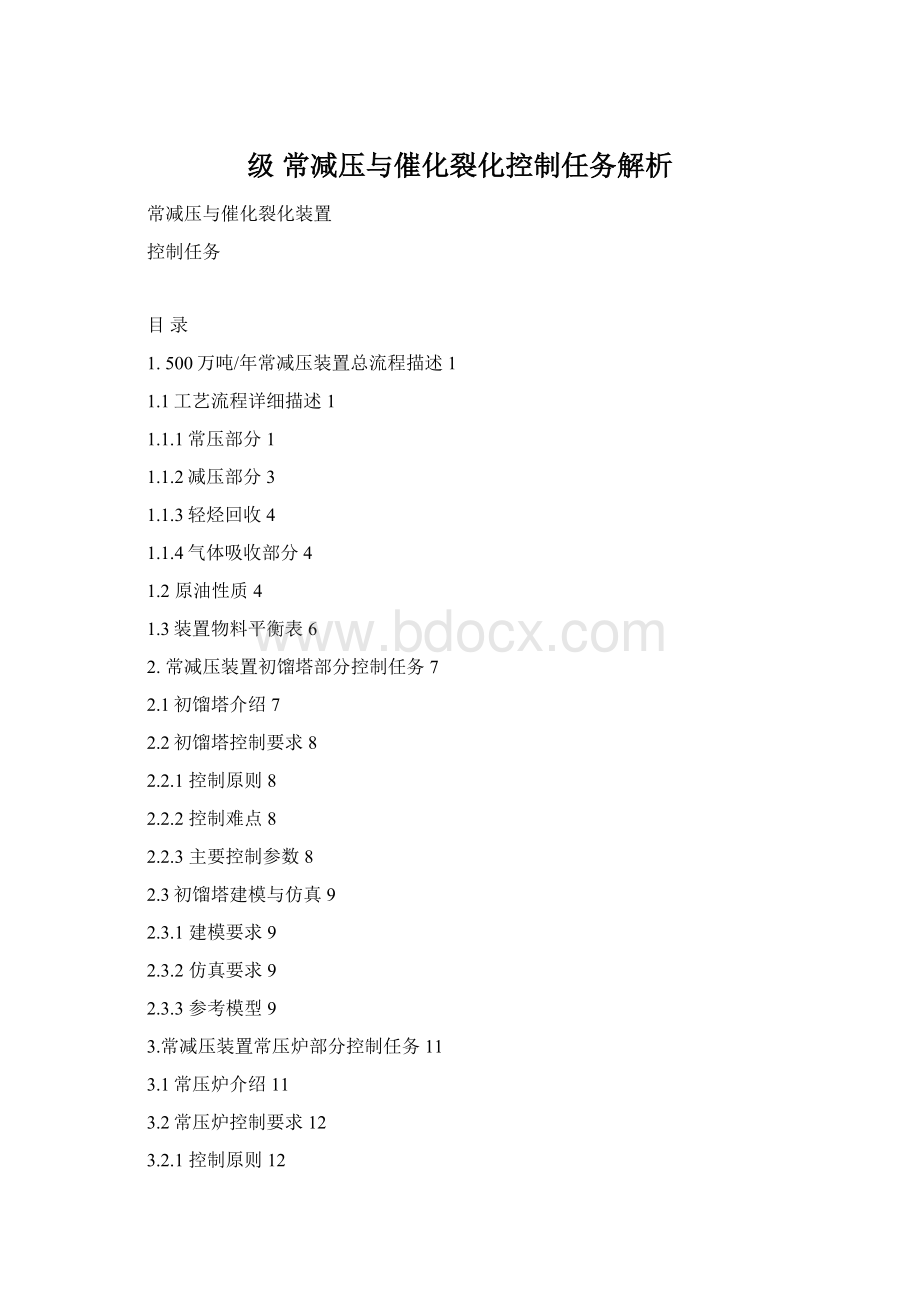
级常减压与催化裂化控制任务解析
常减压与催化裂化装置
控制任务
目录
1.500万吨/年常减压装置总流程描述1
1.1工艺流程详细描述1
1.1.1常压部分1
1.1.2减压部分3
1.1.3轻烃回收4
1.1.4气体吸收部分4
1.2原油性质4
1.3装置物料平衡表6
2.常减压装置初馏塔部分控制任务7
2.1初馏塔介绍7
2.2初馏塔控制要求8
2.2.1控制原则8
2.2.2控制难点8
2.2.3主要控制参数8
2.3初馏塔建模与仿真9
2.3.1建模要求9
2.3.2仿真要求9
2.3.3参考模型9
3.常减压装置常压炉部分控制任务11
3.1常压炉介绍11
3.2常压炉控制要求12
3.2.1控制原则12
3.2.2控制难点12
3.2.3主要控制参数12
3.3常压炉建模与仿真13
3.3.1建模要求13
3.3.2仿真要求13
4.催化裂化反应-再生部分控制任务14
4.1流程描述14
4.2控制要求15
4.3建模与仿真17
3.3.1仿真要求17
3.3.2参考模型17
1.500万吨/年常减压装置总流程描述
1.1工艺流程详细描述
常减压装置在炼油厂中具有非常重要的作用,是企业盈亏的关键。
炼油厂常减压装置是利用石油组分不同的沸点,通过蒸馏,将比重不同的组分进行分离的装置,得到汽油、煤油、柴油等石油产品。
常减压装置油品的轻油收率、总拔出率及能耗指标是装置经济效益的标志性指标。
常减压装置主要由换热、初馏、电脱盐、常压炉、减压炉、抽真空系统、液环增压泵组、空气预热及瓦斯分液系统、轻烃回收系统、轴封、冲洗油系统、火炬分液罐系统等部分组成,如图1-1所示。
主要产品有液化气,乙烯料、重整料、液态烃、航煤(常一线)、轻柴油(常二线)、加氢裂化料(常三线、减顶、减一线、减二线、减三线)、催化裂化料(减三线)、石脑油、氧化沥青溶剂脱沥青料及燃料油组分(减底)。
图1-1常减压装置流程总貌图
1.1.1常压部分
原油自罐区来经原油泵升压后均分2路。
第一路原油依次经E101A-D、E103A,B、E104、E105和E106与热源进行换热到134℃;第二路原油依次经E102A-D、E107A,B、E108A,B、E109A,B与热源进行换热到136℃。
上述两路混合后进电脱盐部分进行脱盐脱水,原油经电脱盐后均分两路,第一路脱后原油依次经E110A-D、E111、E112A-D、E113A-D、E114、E115A,B与热源进行换热到243℃。
第二路脱后原油依次经E116、E117A,B、E118、E119A-C、E120A-D、E121A-B、E122A-B与热源换热到243℃。
上述两路脱后原油合并进T101。
T101(初馏塔)塔顶油气经E101A-D,A101A,B换热及冷凝冷却至61℃进入V102(初顶产品及回流罐)进行油水分离。
分离出的含油含硫污水经P123A,B(初顶排水泵)送往酸性水汽提装置;分离出的初顶油经P102A,B(初项产品及回流油泵)抽出后分为两部分,一部分返回塔顶作为回流;另一部分与常顶二级油一起送至轻烃回收系统。
分离出的气体(初顶不凝气),与常顶不凝气及减顶不凝气合并经P-133A/B(液环增压泵)增压后送焦化装置。
初底油由P103A/B(初底油泵)抽出均分两路与热源换热。
第一路初底油依次经E123A,B、E124和E125A-D换热到约296℃。
第二路初底油依次经E126、E127A-D换热到约296℃。
上述两路初底油合并后约296℃进入F101(常压炉),加热到约363℃后进入T102(常压塔)。
T102塔顶油气经E102A-D,A102A-D(常顶一级空冷器)换热及冷凝冷却到100℃后进入V103(常顶回流罐)进行气液分离。
分离出的常顶油经P107A/B(常顶回流泵)抽出,一部分作为常顶回流,另一部分经A-104A,B(石脑油空冷器),E-132(石脑油冷却器)后作为常顶级石脑油再分两路,一路出装置,一路经冷却后进吸收塔。
分离出的含油含硫污水经泵P124A,B(常顶一级排水泵)送往酸性水汽提装置。
分离出的油气,依次经A103A-D(常顶二级空冷器)、E131(常顶油气冷却器)冷凝冷却后,进V-104(常顶产品罐)进行油水分离。
分出的油经P-108A/B(常顶产品泵)抽出后送到轻烃部分的原料缓冲罐。
分离出的含油含硫污水经泵P125A/B(常顶二级排水泵)送往酸性水汽提装置。
分离出的油气,经升压泵P-133A/B送到焦化装置。
常一线油从T102第13层或第15层塔板自流进入T103(常压汽提塔)上段,采用0.3MPa过热蒸汽进行汽提。
常一线油气返回常压塔,常一线油由P109A/B(常一线油泵)抽出,经E208(脱乙烷塔底重沸器)、E108A,B和E206(脱乙烷塔进料加热器)及E147(常一线-热水换热器)换热和冷却至110℃送到加氢装置。
加氢装置暂时不开时,经A105A,B(常一线空冷器)冷至50℃送罐区。
常二线油从T102第25层或第27层塔板自流进入T103中段,采用0.3MPa过热蒸汽进行汽提,常二线油气返回常压塔,汽提后的常二线油由P110A/B(常二线油泵)抽出,经E111、E107A,B、换热和冷却至110℃送到加氢装置。
加氢装置暂时不开时,经A106A,B(常二线空冷器)冷却至50℃送到罐区。
常三线油从T102第37层或39层塔板自流进入T103下段,采用0.3MPa过热蒸汽进行汽提(根据情况决定是否开),常三线油气返回常压塔,汽提后的常三线油由P111A/B(常三线油泵)抽出,经E124、E121A,B、E118和E103A,B换热和冷却至110℃送到加氢装置。
加氢装置暂时不开时,经A107A,B(常三线空冷器)冷却至50℃送到罐区。
常顶循油由泵P104A/B(常顶循泵)自T102第3层塔盘抽出,经E110A-D换热后返回第1层塔盘上。
常一中油由泵P105A/B(常一中油泵)自T102第19层塔盘抽出经E119A-C,E106换热后返回第17层塔盘上。
常二中油由泵P106A/B(常二中油泵)自T102第31层塔盘抽出,经E122、E204、E130换热后返回第29层塔盘上。
常压塔底油由泵P112A/B('常底油泵)抽出送F102(减压炉)升温到约394℃后进入减压塔。
1.1.2减压部分
减顶油气依次经EJ101A,B(增压器),E144A-D(减顶增压冷凝器)增压冷却后进行气液分离,液相(油和水)经大气腿进入V105(减顶一级油分水罐),未凝气体经EJ102A,B(一级抽空器)、E145A,B(减顶一级抽空冷凝器)增压冷却后再进行气液分离,液相(油和水)经大气腿进入V105,未凝气体有两个工艺流程:
一个为“蒸汽抽真空流程”,即未凝油气经EJ103A,B(减顶二级抽空器)、E146A,B(减顶二级抽空冷凝器)进行增压和分离,液相(油和水)经大气腿进入V106(减顶油水二级分离罐),不凝气经V121(减顶气液封罐),V122(减顶气分液罐)与初常顶不凝气一起经V117(增压泵入口分液罐)及增压泵增压后送到焦化装置。
另一个为“机械抽真空流程”,即未凝油气经P127(液环泵)进一步增压,增压后的气、油、水的混合物在V106(减顶油水二级分离罐)中分离,不凝气经V121(减顶气液封罐)、V122(减顶气分液罐)与初常顶不凝气一起经V117(增压泵入口分液罐)及增压泵增压后送到焦化装置。
正常情况下,采用“机械抽真空流程”。
当液环泵不能正常工作时,采用蒸汽抽真空流程。
V105中的油经泵P-113A/B(减顶一级油泵)抽出与常三线合并后送出装置,V105中的水经泵P126A/B(减顶排水泵)抽出与初常顶的排水一起送出装置。
V106中的油经P119A/B(减顶二级油泵)抽出与常三线合并后送出装置,V106中的水由泵P128A/B(液环泵供水泵)抽出经E148(液环泵入口冷却器)冷却后送到循环回液环式真空泵P127。
V106中剩余的水流到V105中。
V105中的减顶污水,经P126A/B(减顶排水泵)抽出分两路,一路与初常顶排水一起送出装置,一路通过V122-V121-V105进行循环,来保持密封液的液位和液体更新,同时防止这些罐结垢。
减一线及一中油由泵P114A/B(减一线及一中油泵)抽出分两路,一路作为塔的内回流返塔,另一路经E134(减一线及一中热水换热器)与热水换热到110℃分两路,一路经A108A-D(减一中及一线空冷器)、E135(减一中冷却器)冷却到50℃后返塔顶,另一路为减一线产品(柴油)与常三线油合并出装置。
到罐区时则经A-109冷却至50℃去灌区。
减二线及二中油经泵P115A/B(减二线及一中油泵)升压后依次经E112A-D和E109A,B与冷源换热到167℃分两路,一路作为回流返回减压塔;另一路经E104换热到135℃与减三线(热蜡油)混合作为热蜡油出装置。
当减二线到罐区时则经E-136A,B(减二线一热水换热器)冷却后与减三线(90℃)一起出装置。
减三线及三中油经泵P116A/B(减三线及三中油泵)升压后分两路,一路作为内回流返回减压塔,另一路依次经E127A-D,E123A/B,E114和E120A-D换热到216℃后分两路,一路作为回流返回减压塔,另一路经E116、E133与冷源换热到135℃作为热蜡油与减二线热蜡油合并一起出装置。
当减三线到罐区时则经E137A,B(减三线一热水换热器)冷却到冷蜡油90℃与减二线冷蜡油合并一起出装置。
减四线油由泵P117A/B抽出,一部分返回减压塔底,另一部分与减压渣油合并后进行换热和冷却,亦可送到减压炉前与常底油一起进减压炉。
减压渣油由P118A/B(减压渣油泵)抽出后与减四线油合并,依次经E-125A-D、E-126、E-115A,B、E-113A-D、E-117A,B和E-105换热到160℃送焦化装置;当焦化装置暂时不要时,则经E138A-D(减压渣油冷却器)冷却到90℃送到罐区。
1.1.3轻烃回收
初顶油、常顶二级油和富吸收油进入V201(脱丁烷塔进料罐)缓冲后由P202A1B(脱丁烷塔进料泵)抽出,经E202A,B(脱丁烷塔进料换热器)与热源进行换热,换热后至T202(脱丁烷塔)。
T202塔顶油气经A201A-D(脱丁烷塔顶空冷器)和E203A,B(脱丁烷塔顶冷凝器)冷凝冷却到42℃后进入V202(脱丁烷塔顶回流罐)进行气液分离,一部分液体经P203A/B(脱丁烷塔顶回流泵)抽出后返回塔顶作为回流。
另一部分液体经P204A/B(脱丁烷塔顶产品泵)抽出后,经E-206A,B(常一线-脱乙烷进料换热器)送到T203(脱乙烷塔)。
T202塔不凝气送T201(吸收塔)。
T202底重石脑油,经E202A,B、A-202A,B(石脑油空冷器)和E-205A,B(石脑油冷却器)换热和冷却后送出装置。
塔底的重沸器用常二中作为热源。
T-203塔顶油气经E-207(脱乙烷塔顶冷凝器)后进V203(脱乙烷塔顶回流罐),罐内的液体经泵P-205A/B(脱乙烷塔顶回流泵)送回塔内。
V-203的气相送吸收塔。
T203塔底产品经E-209(液化气冷却器)冷却后送出装置。
塔底的重沸器用常一线作为热源。
1.1.4气体吸收部分
自加氢装置来的富含液化气的富气和自T202、T203顶来的不凝气混合进入T-201(吸收塔)的下部,由常压塔顶来的一级石脑油进入T201的上部,气液在塔内充分接触后干气自塔顶自流到脱硫装置,塔底富吸收油经P201A/B(富吸收油泵)送至V201。
1.2原油性质
表1原油的一般性质
分析项目
分析结果
密度,kg/m3(20℃)
867.2
APIO
30.89
运动粘度,
mm2/s
40℃
8.748
80℃
3.07
酸值,mgKOH/g
0.40
残炭,%
4.03
凝点,℃
0
闪点(开口),℃
<17
蜡含量,%
7.58
胶质,%
6.28
沥青质,%
1.00
灰分,%
0.036
水含量,%
无
盐含量,mgNaCl/L
8.32
硫含量,%
1.17
氮含量,g/g
1660
金
属
含
量
g/g
Ni
15.0
V
43.3
Fe
5.1
Na
1.4
Cu
0.2
Pb
0.1
Ca
4.1
第一关键馏分
性质
温度范围,℃
250—275
密度(20℃),kg/m3
835.4
基属
中间基
第二关键馏分
性质
温度范围,℃
395—425
密度(20℃),kg/m3
891.6
基属
中间基
原油类别(按关键馏分特性分类法)
含硫中间基
1.3装置物料平衡表
常减压物料平衡表
序
号
物料
名称
收率
流率
备注
wt%
kg/h
t/d
×104t/a
1
2
3
4
5
6
7
一
原料
1
原油
99.46
595238
14285.71
500.00
轻烃
0.54
3211
77.06
2.70
合计
100
598449
14362.78
502.70
二
产品
1
气体+损失
0.30
1823
43.75
1.53
2
液化气
1.39
8324
199.78
6.99
3
石脑油
16.91
101190
2428.56
85.00
4
常一线油
7.52
45000
1080.00
37.80
5
常二线油
10.03
60000
1440.00
50.40
6
常三线油
10.50
62850
1508.40
52.79
7
减顶油
0.25
1500
36.00
1.26
8
减一线油
3.04
18191
436.58
15.28
9
减二线油
11.78
70500
1692.00
59.22
10
减三线油
14.70
88000
2112.00
73.92
11
减压渣油
23.57
141071
3385.70
118.50
合计
100.00
598449
14362.78
502.70
2.常减压装置初馏塔部分控制任务
2.1初馏塔介绍
初馏塔也叫预分离塔其作用是在较低温度下,把原油中的轻组份汽油和C1—C4及其中含有的酸性物质H2S、Cl+和少量的水除掉,设置初馏塔的目的就是为了提高处理量。
初馏塔一般设置在常压分馏塔前,将原油换热升温过程中已经气化的轻质油及时蒸出,使其不再进入常压加热炉,以降低加热炉的换热负荷和原油换热系统的操作压力降,从而节省装置能耗和操作费用。
初馏塔顶产品轻汽油馏分作催化重整原料。
初馏塔是一个简单塔,对控制方案的设计而言并不复杂。
但是,如果设计不当很可能拿不出油,或者会出现出黑油的现象。
对工程师而言,如果能设计好初馏塔控制系统,对装置的节能、减轻常压炉的负荷和常压塔顶的负荷、提高处理量和搞好优化操作会有很大的好处。
图2-1初馏塔部分管路和仪表流程图
图2-1为某厂500万吨/年常减压装置初馏塔部分管路和仪表流程图。
初馏塔顶油气分成四路进入初顶空冷器后合为一路,分别进入初顶水冷器冷凝冷却,分流进入初顶产品罐。
经脱水及油、气分离后,初顶汽油由初顶油泵抽出后分成二路:
一路打入初馏塔顶作冷回流;另一路作为石脑油与常顶汽油汇合一路去加氢裂化装置或去芳烃罐区。
不凝气送至常压炉烧火。
初侧油自初馏塔第9或第11层塔盘馏出由初侧油泵抽出,与常一中段回流返塔线汇合,进入常压塔第32层塔盘上。
初底油由初底油泵抽出后分成二路,两路换热后合并成一路,在炉前又分成四路进入常压炉。
被加热至365℃出炉后又汇合为一路经转油线进入常压塔的进料段(第4层塔盘上)。
2.2初馏塔控制要求
初馏塔控制参数主要有塔顶压力、塔顶温度、塔顶冷回流量、循环回流量、初侧抽出量、初侧抽出温度、塔进料温度、塔底温度、塔底液面等9个参数,在正常操作中这些参数都是可变的,如果不理顺好这些可变的参数,生产出的产品质量则无法保证,尤其是影响收率问题,而且,因其参数的相互变化影响到其它的正常操作,所以说操作工必须要具备“超前意识,拓展思维”的想象空间,每调节一个参数,不但要顾及前后还要考虑左右的立体思维,这样才能搞好操作平稳。
2.2.1控制原则
原油产量要稳定,保证塔底液面30~70%,不能忽高忽低,造成进料温度、塔底液面波动,以致造成常压塔、减压塔操作条件发生变化,使全装置操作受到影响。
掌握原油性质变化,根据原油性质的变化调整好塔底液面、塔顶温度、塔顶压力。
稳定原油换热后的温度,波动要小,原油入塔温度要求平稳。
平稳控制初顶油水分离罐液面及油水界面在30~60%,液面过高会使瓦斯带油;液面过低,油水界面过高会使油水分离不好,回流油带水,油水界面过低会造成脱水带油。
初侧线抽出量要稳定,其变化量要小,保证常压塔操作稳定。
2.2.2控制难点
由于初馏塔的流量调节阀在泵的出口,原油进料要经过换热、电脱盐部分,使调节进料流量的变化要经过较长的时间才会反映出塔底液位的变化,响应缓慢。
当原油性质变化时,初馏塔的操作波动较大;当装置在提、降量过程中,系统跟踪缓慢,塔底液位波动较大;当对电脱盐进行操作时,如注水、脱水、电脱盐压力调整以及热温度变化(干扰信号),对初馏塔都产生较大影响,影响调节质量。
如果初馏塔操作不稳,将影响初馏塔顶馏出油的质量,改变初底油原有的性质,对换热、电脱盐、原油脱水、常压炉、常压塔的操作均带来不利影响。
2.2.3主要控制参数
1、初馏塔顶温度:
TIC-1307
控制目标:
110±10℃
相关参数:
初馏塔回流量FIC-1301
控制方式:
通过初馏塔顶温与回流流量串级调节控制初馏塔顶温。
初顶温度在压力不变的情况下,直接影响塔顶产品的组成和产量,同时还影响初顶汽油的干点及数量。
温度高,干点高,馏出物增加,温度低,干点低,馏出物减少,汽油尾部变轻,而初馏塔顶温度是受初顶回流控制的。
初顶温度一般维持在使初顶回流罐液面正常的温度,温度控制在110℃左右。
2、初馏塔塔顶压力:
PI-1301
控制目标:
0.05±0.03MPa
相关参数:
原油入塔温度TI1301、汽油冷后温度TI1310
控制方式:
通过开空冷风机和调节水冷器水量来控制初馏塔塔顶压力。
3、初顶回流罐液位、界位:
LIC-1302、LIC1303
控制目标:
45±15%
控制方式:
通过初顶汽油流量调节初顶回流罐液面,通过调节初顶回流罐脱水阀LIC1303来控制初顶回流罐界位。
液位过低,初顶回流罐底泵易抽空;液位过高,气相分离空间减少,易引起雾沫夹带,使得液体中的轻组分被初顶瓦斯带入到低压瓦斯系统中,造成瓦斯带油,影响加热炉操作。
4、初馏塔顶汽油干点
控制范围:
≤180℃
控制目标:
±5℃
相关参数:
塔顶温度TIC-1307、塔顶压力PI-1301、原油入塔温度TI1301
控制方式:
塔顶温度与初顶回流量(TIC-1307与FIC-1301)。
5、初馏塔塔底液位LIC1301
控制目标:
50±20%
控制方式:
通过FIC1001、FIC1004控制原油一、二路流量,调节FIC1001、FIC1004阀位来控制初馏塔底液位。
2.3初馏塔建模与仿真
2.3.1建模要求
查阅文献,根据初馏塔工作机理以及上述控制要求,建立塔顶温度、塔顶压力、出顶回流罐液位和界位、塔顶汽油干点、塔底液位的数学模型。
可以是多变量的联立方程组,也可以是单变量的传递函数。
2.3.2仿真要求
将所建模型用欧拉法离散化(或者其他离散化方法),利用VB语言编程,实现各控制回路的动态仿真。
2.3.3参考模型
经过严格的机理分析,可以建立初馏塔连续模型为:
其中:
时间单位为分钟
X为状态变量SV,维数为8;U为操纵变量MV,维数为3;
V为可测干扰变量FV,维数为2;Y为被控变量CV,维数为5。
Y:
塔顶干点、塔顶温度、塔顶压力、塔底液位、塔底液位变化速率
U:
顶循流量、顶冷温度、定冷流量
操纵变量MV和可测干扰变量FV对状态变量SV存在多重纯滞后的影响,而且状态变量SV之间存在状态纯滞后的影响。
3.常减压装置常压炉部分控制任务
3.1常压炉介绍
加热炉是石油、化工、冶金、建材、电子、材料、日化以及制药等行业必不可缺的一部分,主要作用是用来加热物料或者工件,使其温度达到指定值。
在工业生产中加热炉是非常重要的换热设备,在其炉膛内将燃料燃烧或者通过电加热释放的热量通过热辐射的方式传递给被加热的工艺介质。
加热炉控制主要的任务是保证工艺介质最终达到需要温度并且维持在工艺要求的范围内,然而由于加热炉有强耦合、大滞后等特点,控制起来非常复杂。
同时,近几年来能源的合理利用、节约以及回收日益受到关注。
加热炉是炼油、化工等生产部门典型的换热设备,能耗很大。
所以在设计加热炉控制系统的同时,在满足工艺要求的前提下,也应注重考虑节能问题,把节能看做一个重要的控制指标,从而保证加热炉的最高热效率,最大经济效益。
另外,在设计加热炉控制系统的同时,还应保证燃料的充分燃烧,使产生的有害气体最少,达到减排的目的以更好的保护环境。
为了保证工艺介质最终的温度稳定以及达到节能减排的目的,一般的加热炉控制系统包括如下控制回路:
空气量和燃料量的交叉限制式串级燃烧自动系统、炉膛压力的自动控制,热风温度的自动控制系统以及燃料、空气流量比自动控制。
此外,为了更大程度地节约能源,工业生产中在具有下游换热器的加热炉装置中,在平稳生产时下游换热器不起作用只在工艺介质最终温度异常升高时才工作。
图3-1常压炉监控界面
常热炉的主要作用就是把工艺介质加工到后续工序所需要的温度,一般是把初馏塔底出来的油加热到360~370摄氏度。
图3-1为某厂500万吨/年常减压装置常压炉部分的监控界面图。
加热炉的热量来源主要是燃料气或燃料油的燃烧。
燃料在炉膛内燃烧产生高温烟气以辐射的方式将大量的热量传递给炉管并传给工艺介质。
3.2常压炉控制要求
因处理量大,常压炉进料分为四个支路进行加热,主要控制参数有分支出口温度、分支入口流量、炉膛压力、燃料流量等4个参数。
加热炉出口的温度将直接影响后续工序的操作状况,并且还会影响到产品分布和质量。
炉膛的压力是实现加热炉的安全燃烧的一个重要指标。
烟气的氧含量是降低消耗、提高热效率的重要指标。
常规的PID控制不能解决多变量耦合系统,也很难有效的克服扰动,不能达到满意的控制效果。
3.2.1控制原则
四个支路的出口温度要恒定,支路入口流量要均衡,尽量保持总入口流量不变。
3.2.2控制难点
由于常压炉燃烧不均匀,造成各支路出口温度不同;由于炉膛容积大,温度反应滞后;燃料气压力、组分等波动大;还有燃料油主要来自于减压塔底,受液面指示滞后和渣油出装置的影响,燃料油系统压力一直不够稳定。
因此,常压炉的