2500吨提升装置门式液压吊装系统大型设备吊装.docx
《2500吨提升装置门式液压吊装系统大型设备吊装.docx》由会员分享,可在线阅读,更多相关《2500吨提升装置门式液压吊装系统大型设备吊装.docx(27页珍藏版)》请在冰豆网上搜索。
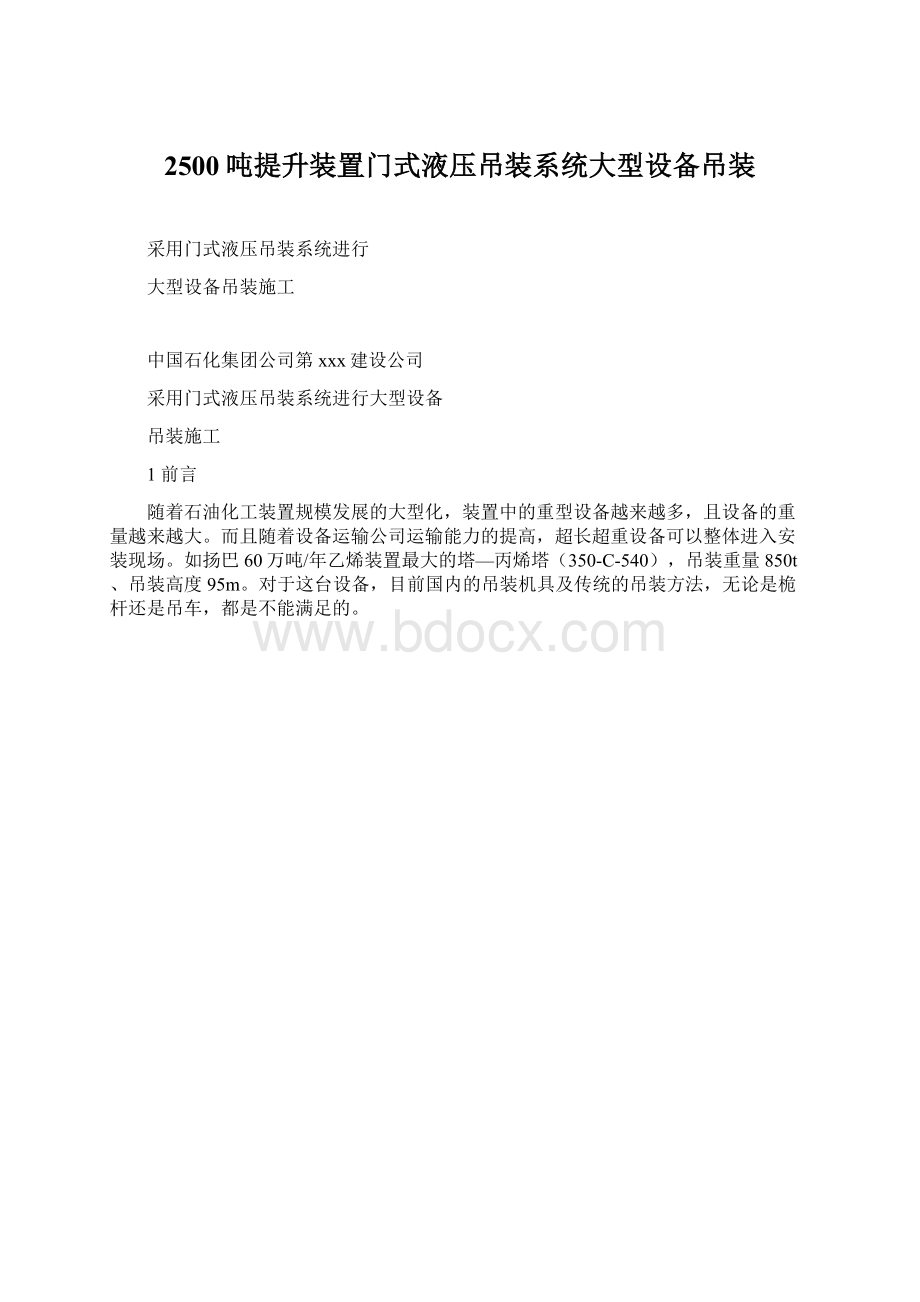
2500吨提升装置门式液压吊装系统大型设备吊装
采用门式液压吊装系统进行
大型设备吊装施工
中国石化集团公司第xxx建设公司
采用门式液压吊装系统进行大型设备
吊装施工
1前言
随着石油化工装置规模发展的大型化,装置中的重型设备越来越多,且设备的重量越来越大。
而且随着设备运输公司运输能力的提高,超长超重设备可以整体进入安装现场。
如扬巴60万吨/年乙烯装置最大的塔—丙烯塔(350-C-540),吊装重量850t、吊装高度95m。
对于这台设备,目前国内的吊装机具及传统的吊装方法,无论是桅杆还是吊车,都是不能满足的。
为适应我国石化装置设备大型化的需要,我公司引进了先进的液压提升技术,开发、制造了“门式液压吊装系统”。
该系统能够满足超重超长设备的吊装。
钢结构设计采用英国BS5400标准。
2特点
本门式液压吊装系统(以下简称吊装系统)主要由桅杆结构、牵索结构、横梁、可旋转组合式平衡梁、滑移系统、自安装系统、主提升液压设备及其控制系统组成(参见图1、图2)。
门式桅杆总高116.3m,最大有效起吊高度达102.1m,最大有效起吊能力达2500t,是目前国内同类施工设备中吊装能力最大、操作最先进的设备。
2.1整个吊装系统为可拆卸结构,包括每一节桅杆均可拆卸成单根杆件,运输时没有超限部件,运输、组装受自然地貌限制小。
2.2吊装系统的安装及拆除在250t履带吊车(横梁的拆、装)配合下,采取自安装的方式进行,减少了大型吊车的使用;同时较以前所使用的普通桅杆吊装系统,减少了大量现场施工用地。
2.3本吊装系统由计算机在地面集中控制,计算机可以显示所吊物体的每一时刻的吊装重量及各个牵索的受力情况,主吊装过程以及牵索的受力状态实现自动化操作,整个吊装过程运行平稳、安全系数高。
2.4本吊装系统的配置,充分考虑了各种吊装工况要求以及施工现场的场地情况,适用范围广,主要体现在以下方面:
a)该吊装系统可根据吊装物体的具体要求来配置桅杆的长度、主提升液压设备的数量,横梁的跨度,来满足对吊装高度、吊装重量、桅杆中心距的要求;
b)利用本吊装系统配备的4套80t能力的推拉千斤顶,吊装系统可以沿直线行走。
若装置中重型设备成一条轴线布置,采用该吊装系统一次竖立,可以进行数台设备的吊装;
c)该吊装系统配备的是可旋转组合式平衡梁,被吊物体吊起后可做360º旋转,保证设备的安装方位。
3适用范围
3.1适用范围
a)本吊装系统可以根据工程的具体情况进行配置,可广泛应用于各行业基本建设中超重超长整体设备的吊装。
桅杆直立状态下,当组装13节桅杆(高76.7m)时,可吊装2600t;当组装18节桅杆(高106.2m)时,可吊装2360t(详见参数表1、图3);
b)桅杆双侧变幅状态下,组装18节桅杆,变幅20m时,可吊装1490t;当变幅10m时,可吊装2030t(详见参数表2、图4)。
利用变幅功能,可以实现设备的垂直及水平方向的移动。
在狭窄空间作业时,可以用于框架及厂房内设备的吊装。
如吊装系统站位于框架外,将设备吊起后,通过变幅功能将设备平移就位于框架内部;
c)吊装系统主吊千斤顶(提升能力为650t)、牵索千斤顶(提升能力为180t、105t、15t)可以单独使用,用于框架内或厂房内等狭窄封顶空间、大型吊装机具无法进入的场合的设备吊装;
d)吊装系统配备的4套80t能力的推拉千斤顶可单独使用,用于重型设备的水平移动;
e)集群式千斤顶可以用于机场、车站、影剧院顶部钢结构的吊装。
3.2桅杆直立状态下性能表(如图3所示)。
表1桅杆直立状态下吊装能力表
桅杆节数
n
桅杆高度
h(m)
桅杆顶部
高度
H(m)
有效
吊装高度
(m)
单桅杆极限
压缩能力
(/tower)
单桅杆抗
弯矩能力
(t·m)
桅杆吊装
能力
(t)
吊装系统
吊装能力
(t)
13
76.7
83.8
72.6
2685
4699
2712
2600
14
82.6
89.7
78.5
2685
4699
2689
2600
15
88.5
95.6
84.4
2685
4699
2665
2600
16
94.4
101.5
90.3
2641
4699
2589
2589
17
100.3
107.4
96.2
2567
4699
2475
2475
18
106.2
113.3
102.1
2489
4699
2360
2360
说明:
a)吊装能力为设备、旋转轴、扩展梁、主千斤顶钢缆及吊装绳扣的组合重量;
b)上述性能适用条件:
1)在满负荷吊装情况下,最大工作风速为16m/s;在吊装过程中,最大暴风风速为40m/s,此时设备上附加牵索抵抗水平风载荷;
2)设备高度60m,设备直径20m,横梁跨度25.2m,横梁重量155t;横梁跨度可以在12.2m至25.2m之间变动。
3)吊装系统按照6牵索或4牵索布置,牵索角度45º,牵索预拉力50t。
c)针对具体吊装对象,吊装地点,对吊装系统的吊装能力需要重新核算。
3.3桅杆变幅状态下吊装性能(如图4所示)。
表2桅杆变幅状态性能表
桅杆节数
n
桅杆长度
h(m)
变幅距离
D(m)
桅杆顶部高度
H(m)
变幅角度
A(º)
有效吊装高度
(m)
系统吊装能力
(t)
18
106.2
20
111.488
10.352
100.288
1490
18
106.2
18
111.835
9.307
100.635
1680
18
106.2
16
112.144
8.265
100.944
1840
18
106.2
14
112.416
7.226
101.216
1900
18
106.2
12
112.651
6.189
101.451
1970
18
106.2
10
112.850
5.155
101.65
2030
18
106.2
8
113.012
4.122
101.812
2090
18
106.2
6
113.138
3.090
101.938
2170
18
106.2
4
113.228
2.060
102.028
2230
18
106.2
2
113.282
1.030
102.082
2290
18
106.2
0
113.300
0.000
102.1
2360
说明:
a)吊装能力为设备、旋转轴、扩展梁、主千斤顶钢缆及吊装绳扣的组合重量;
b)上述性能适用条件:
1)在满负荷吊装情况下,最大工作风速为16m/s;在吊装过程中,最大暴风风速为40m/s,此时设备上附加牵索抵抗水平风载荷;
2)设备高度95m,设备直径10.7m,横梁重量120t;
3)吊装系统按照8牵索或10牵索布置,牵索角度45º,侧向牵索预拉力50t。
c)针对具体吊装对象,吊装地点,对吊装系统的吊装能力需要重新核算。
4主要施工程序
5工艺流程及要点
5.1吊装系统的组装
门式液压吊装系统的结构参见图1、图2。
5.1.1基础处理
a)吊装过程中,吊装系统基础承受来自承重底排的均布压力,压力等于吊装系统自重(桅杆全部安装时,整个吊装系统自重900t)与吊装设备的重量及牵索拉力的垂直分力之和,承重底排与地面接触面积为58m2。
所以:
P=(G0+G+N)/58
式中:
P——承重底排对地面压强,t/m2;
G0——吊装系统自重,t;
G——设备的吊装重量,t;
N——牵索拉力的垂直分力,t。
b)吊装系统平移过程中,吊装系统基础承受来自非承重底排的均布压力,压力等于吊装系统自重及牵索拉力的垂直分力之和,承重底排与地面接触面积为58m2。
所以:
P=(900+20×6)/58=17.586(t/m2)
注:
牵索拉力按照20t考虑。
c)根据上述计算结果,对基础进行处理。
对于大型设备,其基础一般采用桩基。
吊装系统基础紧靠设备基础,可以将设备基础与桅杆基础一起设计。
5.1.2底排安装
每根桅杆配有两个承重底排和四个非承重底排。
设备吊装时,吊装系统处于承重底排上;设备吊装就位后,吊装系统滑移到非承重底排上。
a)吊装系统安装前,对基础标高基准线、纵横中心线、沉降观测点的设置情况进行验收;
b)按桅杆中心距要求铺设底排;
c)底排间采用连接螺栓固定(见图5)。
5.1.3滑移系统安装:
滑移系统由滑移轨道、滑移梁、推拉千斤顶、螺纹千斤顶及其支撑梁等组成,在设备吊装就位后,利用滑移系统将整个吊装系统从承重底排推移至非承重底排,拆除该吊装系统。
a)滑移轨道与底排间用螺栓固定;
b)滑移梁就位后用定位销与滑移轨道(含滑移块)及底排固定;
c)安装螺纹千斤顶的支撑梁及螺纹千斤顶,并用螺栓与滑移梁固定(见图6);
d)将滑移梁上的梯子、平台安装就位。
5.1.4安装铰球及桅杆底座
铰球用于将桅杆所受的力垂直向下传至底排。
a)将铰球安装在滑移梁上,用螺栓固定(见图7);
b)底座就位后,用螺纹千斤顶调整预安装底座的水平度(见图8)。
5.1.5安装自安装系统框架
通过自安装系统实现吊装系统的自安装,使桅杆的组装工作在地面进行,减少了高空作业。
自安装系统包括自安装框架(包括自安装加紧千斤顶)及用于桅杆滑移的滑移框架。
在地面将自安装框架组装成整体后吊装就位(见图9)。
5.1.6顶部第一节桅杆安装
a)桅杆组装
桅杆各构件间均采用螺栓连接,先成两片,再组装成框;
b)第一节桅杆安装
将第一节桅杆吊于自安装系统框架上,四个夹紧千斤顶定位于自安装系统的顶部框架(见图10);
c)连接夹紧千斤顶的电气及液压部分;
d)对夹紧千斤顶进行动作调试;
e)夹紧千斤顶的动作调试完成后,将第一节桅杆下降至桅杆头部露出夹紧千斤顶。
5.1.7顶座及上部铰球安装
顶座包括牵索系挂的结构;当载荷作用时,由于桅杆和横梁的安装偏差,两铰球之间的距离会发生变化。
为适应这种变化,上部铰球为两种,一种为固定式,一种为滑移式。
滑移铰球上有滑移板,允许横梁与铰球水平滑移,最大滑移量100mm。
a)顶座为组合件,采用吊车吊装就位;
b)铰球采用吊车吊装就位(见图11);
c)顶座就位后,连接顶座与第一节桅杆之间的连接螺栓,安装侧向牵索框架以及塔顶连接的支撑管。
5.1.8桅杆连接管及牵索的连接
a)布置牵索千斤顶及动力箱,连接好液压及电气系统,将辅助牵索连接到顶座上;
b)将主牵索连接到顶座上,并使主牵索保持松弛状态;
c)连接两个顶座之间的连接管;
d)安装辅助牵索,并使每个辅助牵索受力5t;保持受力状态(见图12)。
e)放松底部的螺纹千斤顶;
※:
在上文的叙述中,主辅牵索同时使用是考虑到几台设备吊装时牵索的倒换。
若针对一台设备的吊装,则可以直接使用主牵索,不再使用辅助牵索。
5.1.9横梁的安装
横梁用于提供千斤顶的主吊吊挂点及其动力箱。
a)横梁由左段、右段和中间段组成,各段之间采用高强螺栓连接。
在地面将横梁组装为一体,要求各段间连接螺栓达到规定的扭矩值;
b)横梁组装为整体后,采用250t履带吊(M250型)单车吊装的方法完成横梁的安装;
c)安装主吊千斤顶托架;
d)安装千斤顶托架的梯子、平台、缆绳导向器、主吊千斤顶动力箱及缆绳器(见图13);
e)连接主吊千斤顶与动力箱的电气及液压部分;
f)用顶部的螺纹千斤顶找平横梁。
5.1.10第2~11节桅杆安装
a)提升第一节桅杆
用8个夹紧千斤顶夹住第一节桅杆主肢的方钢,提升至下部净空超过5.9m。
在此过程中,辅助牵索千斤顶保持一定的内力(最小为5t~6t,最大为10t~12t),不回放。
监视桅杆的垂直度,如果内力变化超过允许范围,则停止起升,调整牵索,当内力在允许范围内,停止调整牵索,继续提升桅杆。
b)滑移第二节桅杆
将预组装成整体的第二节桅杆,吊放在自安装系统的运输小车上,滑移至第一节桅杆的下部(见图14);
c)连接前两节桅杆
第二节桅杆滑移到位后,用夹紧千斤顶将第一节桅杆降至第二节桅杆上。
对正后,将第一节桅杆与第二节桅杆连接在一起;
d)重复上面的步骤,安装其他节桅杆。
e)主牵索受力
当桅杆安装至第11节后,启动主牵索千斤顶,使主牵索受力10t~12t;辅助牵索不再受力,随着桅杆的继续升高,保持松弛状态(见图15)。
5.1.11安装上下扩展梁及旋转轴
上扩展梁用于固定主吊千斤顶的固定锚块;下扩展梁用于系挂主吊绳扣;旋转轴连接上、下扩展梁,并保证设备吊起后,在360º范围内旋转。
a)吊装上扩展梁;
b)连接固定锚块与上扩展梁
操作主吊千斤顶,使主吊千斤顶的固定锚块降至上扩展梁的正下方,然后用螺栓将固定锚块与上扩展梁连接在一起(见图16/图17);
c)连接上扩展梁与旋转轴之间的销轴;
d)连接下扩展梁(见图18)及吊装绳扣。
5.1.12继续用自安装方法安装桅杆
a)用自安装系统将桅杆安装至所需的最终高度
在此过程中,通过调整主牵索千斤顶的内力保证桅杆的垂直度,使其控制在H/1000以内。
牵索千斤顶在此过程中的最小受力为10t,最大受力为45t(见图19);
b)移走移动小车;
c)连接底节桅杆与底座
用自安装系统的夹紧千斤顶,将桅杆降低,直至底节桅杆降低至自安装系统的底座上,用螺栓将两者连接在一起;
d)预拉地锚
将牵索的张力逐渐增至吊装过程的最大受力(根据吊装方案确定)。
保持30min,检查牵索及地锚有无异常情况。
当结构没有破坏及地锚未移动时,才能继续工作;
e)调节主牵索,使其预张力达到规定植(根据吊装方案确定)。
5.1.13整个吊装系统调试
进行千斤顶、动力箱、控制系统计算机之间的调试。
吊装系统调试后,利用平衡梁(带无接头钢丝绳)做升降运动的试验,并检验计算机测出力和实际载荷是否相符。
在整个过程中(吊装系统安装前、吊装过程中、吊装完成及系统拆除后)应按照预先标定的测点作基础沉降观测,详细记录基础下降和回升情况,并应填写“沉降观测记录”。
5.1.14连接绳扣
将吊装绳扣连接到待吊设备上。
5.2设备吊装(以扬巴丙烯塔吊装为例)
5.2.1吊装前的准备
a)确定吊装方案,用门式液压吊装系统做为吊装设备,设备抬尾需要一台具有足够吊装能力的吊车。
该吊车能够满足整个吊装过程中溜尾吊点的受力;
表3起重机参数表
一.主吊机具(门式液压吊装系统)
起吊能力
1250t/100m
提升速度
≤16m/h
构造
有牵索门式桅杆
主提升千斤顶间距
4.2m
主桅杆高度
5.9×18=106.2m
旋转平衡梁
1250t
牵索数量
6条
安全工作载荷
1250t
主提升千斤顶
650t×2=1300t
二.抬尾吊车(CC8800)
起重能力
1250t
标准配重/超起配重
280+100t/0
构造
主杆SSL工况
半径
18m
表3起重机参数表(续)
起重臂长度
54m
SWL
427t
三.索具部分
主吊耳
管轴式吊耳
抬尾吊耳
板式
起重架
抬尾吊索
2×200t×18m
吊索
2×400t×36.5m
吊钩
500t
卡扣
150Tx2
表4设备参数
尺寸
Φ8446/Φ5800×92100
配管
36.1t
重量
685.88t
索具
22t
绝热
10.46t
平衡梁自重
68.23t
平台
23.129t
系统承受载荷
845.8t
表5吊装过程中门式液压吊装系统及抬尾吊车受力情况
设备角度(度)
溜尾力臂(米)
主吊力臂(米)
门式吊装系统受力
(吨)
抬尾吊车受力
(吨)
0
45.26
20.45
525.75
237.55
5
45.47
20.37
527.11
236.19
10
45.33
20.14
528.48
234.82
15
44.84
19.75
529.88
233.42
20
44.02
19.22
531.33
231.97
25
42.85
18.53
532.85
230.45
30
41.37
17.71
534.48
228.82
35
39.57
16.75
536.25
227.05
40
37.46
15.67
538.23
225.07
45
35.07
14.46
540.47
222.83
50
32.42
13.15
543.09
220.21
55
29.52
11.73
546.23
217.07
60
26.39
10.23
550.14
213.16
65
23.06
8.643
555.23
208.07
70
19.56
6.994
562.25
201.05
75
15.91
5.293
572.74
190.56
80
12.14
3.551
590.50
172.80
82
10.6
2.846
601.72
161.58
84
9.049
2.138
617.45
145.85
86
7.489
1.427
641.16
122.14
88
5.919
0.714
681.17
82.13
89
5.131
0.357
713.66
49.64
90
4.342
0
763.30
0.00
吊装过程中门式液压吊装系统及抬尾吊车受力示意图:
吨
门式液压吊装系统受力
抬尾吊车受力
b)检查吊装系统是否符合吊装方案的要求,包括桅杆垂直度(小于100mm)、设备运输位置(保证主吊点位于桅杆平面内)、设备进向正确(符合吊装方案要求)、抬尾吊车位置(符合方案要求)、吊车前进的轨迹线标识、主吊绳扣、抬尾绳扣是否处于垂直状态。
牵索预拉力符合吊装方案要求,该预拉力保证在横向力作用下,所有牵索保持在拉紧状态,并且使桅杆顶部的挠度最小;
c)吊装系统和抬尾吊车受力至应受载荷的10%,再次检查桅杆的垂直度,如超出允许范围进行调整;
d)气象预报至少3天内的风速在允许的工作范围内。
本吊装系统设计风速为:
最大工作风速为16m/s。
5.2.2地锚设置
a)根据地锚受力计算书,采用3800mm×1800mm×900mm的钢筋混凝土锚块,每块重29.5t;两块一组;
b)锚块埋设深度4100mm,分层回填夯实,回填土并高出原地面600mm;
c)锚块上捆绑φ43-6×37+1-1700的钢丝绳,2圈4股;单股破断力118.5t×0.82=97.2t,安全系数n=97.2×4×0.75/50.391=5.78倍,大于3.5倍安全要求。
5.2.3设备吊装(见图20)
a)门式桅杆系统的主吊千斤顶和抬尾吊车逐步增加载荷,随着每次载荷的增加,应检查桅杆的垂直度是否在100mm以内,如果超过100mm,通过计算机调整偏移方向的牵索受力进行调整;抬尾绳扣的垂直度也进行类似的检查调整;
b)抬尾吊车与吊装系统同步起吊,设备支撑移走;
c)设备尾部降低至底部离地面高度小于500mm。
确认桅杆和千斤顶钢缆处于垂直状态,设备吊装可以继续进行;
d)随着吊装的进行,抬尾吊车前行或通过吊车扒杆的动作,保持主吊钢缆的垂直。
在吊装过程中,抬尾吊车向前移动的速度越来越快,直到设备处于垂直状态。
设备降低至设备刚好位于地脚螺栓的正上方,用倒链等将设备转至正确的方位;
e)设备降低,穿入地脚螺栓落至基础上,直至主吊千斤顶载荷降低25%;当设备垂直度调整合格后,放松主吊千斤顶载荷,把紧地脚螺栓;
f)拆除主吊绳扣并各自与桅杆固定在一起,准备将吊装系统移至桅杆拆除位置。
5.3吊装系统拆除
5.3.1桅杆平移
a)连接推拉千斤顶
在滑移轨道、底排与滑移梁之间连接推拉千斤顶(见图21)。
b)桅杆垂直度控制
放松前进反方向的牵索,同时收紧前进方向的牵索,侧面的牵索也随着调整。
在此操作过程中,桅杆垂直度保持在H/250以内。
c)桅杆前移
推拉千斤顶回收,使桅杆系统前移,在此过程中,桅杆保持前倾。
然后松开推拉千斤顶与滑移轨道之间的连接,推拉千斤顶伸缸后再次与滑移轨道连接。
d)桅杆前移到位
重复2)、3)的动作,直到吊装系统移动到预定位置。
5.3.2拆除桅杆系统
按5.1.1~5.1.14相反的程序进行拆除。
5.3.3装箱运输
采用专用包装架进行吊装系统的包装与运输。
6施工机具及措施用料(按照吊装系统主吊,吊车抬尾的吊装方法):
序号
名称
规格、型号
数量
备注
1
汽车吊
50t(TG-500)
2台
100t(LTM1100)
1台
160t(KMK5160)
1台
2
砼块
1200mm×1200mm×4000mm
8块
3
卡兰
5t(L5型)
4个
4
无接头钢丝绳扣
Ф200mm×73m
1对
5
钢丝绳扣
Ф24mm×16m
Ф26mm×8m
6根
Ф43mm×20m
1对
Ф47.5mm×12m
施工机具及措施用料(续)
序号
名称
规格、型号
数量
备注
6
卡扣
60t
6个
40t
4个
16t
4个
5t
4个
7
运输车
半挂拖板车30t
1台
卡车15t
1台
8
尼龙吊装带
3t×6m
2根
9
地锚连接用钢丝绳
Ф43mm×30m
6根
Ф15.5mm×30m
6根
10
绳卡
Y5-15
30个
Y12-45
36个
11
手拉葫芦
HS2
12台
HS5
2台
12
钢板
2000mm×6000mm×40mm
4块
δ=30mm或δ=60mm
0.4m2
13
道木
200mm×160mm×2500mm
60根
注:
施工机具中未包括抬尾吊车,抬尾吊车根据设备的实际情况确定。
7劳动力安排
以单台大型立式设备的吊装为例,劳动力安排如下:
序号
工种
人数
备注
1
控制吊装系统操作人员
2
具备较高素质
2
起重工
20
吊装阶段需要10人
3
钳工
10
吊装阶段需要6人
4
架子工
10
在吊装系统组立阶段
5
工程师
2
其中液压技术1人,吊装技术1人
6
吊车司机
5
包括组装阶段及吊装阶段
7
测量工
2
从两个方向同时监测
8
电工
2
8效益分析:
8.1吊装系统具有自安装功能,所以吊装系统组装在自安装平台上完成,减少了高空作业,确