煤制油附表2.docx
《煤制油附表2.docx》由会员分享,可在线阅读,更多相关《煤制油附表2.docx(8页珍藏版)》请在冰豆网上搜索。
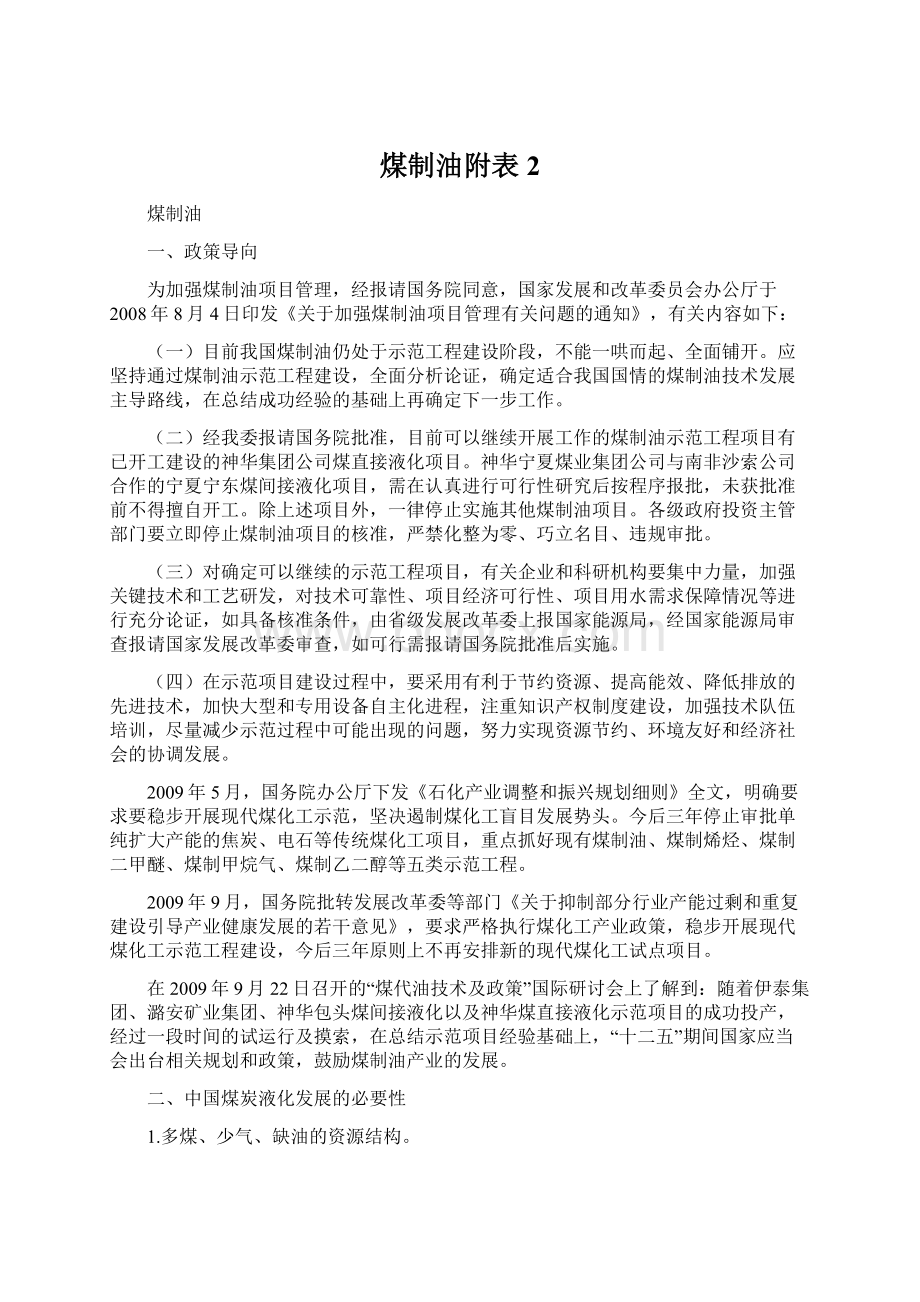
煤制油附表2
煤制油
一、政策导向
为加强煤制油项目管理,经报请国务院同意,国家发展和改革委员会办公厅于2008年8月4日印发《关于加强煤制油项目管理有关问题的通知》,有关内容如下:
(一)目前我国煤制油仍处于示范工程建设阶段,不能一哄而起、全面铺开。
应坚持通过煤制油示范工程建设,全面分析论证,确定适合我国国情的煤制油技术发展主导路线,在总结成功经验的基础上再确定下一步工作。
(二)经我委报请国务院批准,目前可以继续开展工作的煤制油示范工程项目有已开工建设的神华集团公司煤直接液化项目。
神华宁夏煤业集团公司与南非沙索公司合作的宁夏宁东煤间接液化项目,需在认真进行可行性研究后按程序报批,未获批准前不得擅自开工。
除上述项目外,一律停止实施其他煤制油项目。
各级政府投资主管部门要立即停止煤制油项目的核准,严禁化整为零、巧立名目、违规审批。
(三)对确定可以继续的示范工程项目,有关企业和科研机构要集中力量,加强关键技术和工艺研发,对技术可靠性、项目经济可行性、项目用水需求保障情况等进行充分论证,如具备核准条件,由省级发展改革委上报国家能源局,经国家能源局审查报请国家发展改革委审查,如可行需报请国务院批准后实施。
(四)在示范项目建设过程中,要采用有利于节约资源、提高能效、降低排放的先进技术,加快大型和专用设备自主化进程,注重知识产权制度建设,加强技术队伍培训,尽量减少示范过程中可能出现的问题,努力实现资源节约、环境友好和经济社会的协调发展。
2009年5月,国务院办公厅下发《石化产业调整和振兴规划细则》全文,明确要求要稳步开展现代煤化工示范,坚决遏制煤化工盲目发展势头。
今后三年停止审批单纯扩大产能的焦炭、电石等传统煤化工项目,重点抓好现有煤制油、煤制烯烃、煤制二甲醚、煤制甲烷气、煤制乙二醇等五类示范工程。
2009年9月,国务院批转发展改革委等部门《关于抑制部分行业产能过剩和重复建设引导产业健康发展的若干意见》,要求严格执行煤化工产业政策,稳步开展现代煤化工示范工程建设,今后三年原则上不再安排新的现代煤化工试点项目。
在2009年9月22日召开的“煤代油技术及政策”国际研讨会上了解到:
随着伊泰集团、潞安矿业集团、神华包头煤间接液化以及神华煤直接液化示范项目的成功投产,经过一段时间的试运行及摸索,在总结示范项目经验基础上,“十二五”期间国家应当会出台相关规划和政策,鼓励煤制油产业的发展。
二、中国煤炭液化发展的必要性
1.多煤、少气、缺油的资源结构。
在可预见的将来,中国以煤为主的能源结构不会改变。
煤炭是中国未来的主要可依赖能源。
此外,从经济上看,煤炭也是最廉价的能源。
中国是发展中国家,又是能源消费大国,经济实力和能源供应都要求中国的能源消费必须立足于国内的能源供应,这就决定中国的能源结构必须是以煤为主体。
煤炭大量使用,引发了严重的环境污染问题。
2.石油进口迅速上升,已对中国的能源供应安全构成威胁。
石油是保障国家经济命脉和政治安全的重要战略物资。
中国石油资源相对贫乏,由于国产石油无法满足需求,对进口油依存度越来越高。
自1993年成为石油净进口国后,石油进口量迅速上升,进口量的剧增,依存度的加大,已对中国能源供应安全构成威胁。
3.煤炭液化可增加液体燃料的供应能力,有利于煤炭工业的可持续发展。
煤炭通过液化可将硫等有害元素以灰分脱除,得到洁净的二次能源,对优化终端能源结构、减少环境污染具有重要的战略意义。
煤炭液化可生产优质汽油、柴油和航空燃料,尤其是航空燃料,要求单位体积的发热量高,即要求环烷烃含量高,而煤液化油的特点就是富含环烷烃,通过加氢处理即可得到优质航空燃料。
发展煤炭液化不仅可以解决燃煤引起的环境污染问题,充分利用中国丰富的煤炭资源优势,保证煤炭工业的可持续发展,满足未来不断增长的能源需求,而且更重要的是,煤炭液化还可以生产出经济适用的燃料油,大量替代柴油、汽油等燃料,有效地解决中国石油供应不足和石油供应安全问题。
三、经济性分析
煤制油项目对油价有很强的依赖性,也和项目所在地的煤质情况、市场煤价都有关系。
以目前的工艺可以看出,每产一吨成品油,直接液化消耗原煤是3-4吨,而间接液化则消耗4.5-5.5吨;每吨油品产出中,直接液化耗水量为5-6吨,间接液化项目的耗水量则是8-12吨。
从单位投资金额计算,前者的每万吨成本是0.8亿-1.1亿元,而间接液化则是1.1亿-1.3亿元。
而且直接液化的经济性比间接液化更为明显(见表1)。
表1煤炭价格与成本原油价格对比
煤炭价格(元/吨)
100
500
600
700
800
间接液化(美元/桶)
35~45
60~70
67~77
74~84
80~90
直接液化(美元/桶)
20~30
36~46
40~50
45~55
49~59
首先,煤炭价格的上涨将降低煤制油的经济性。
从表1可见,当煤炭价格为500元/吨,原油价格6O~70美元/桶时,间接液化有经济性。
当煤炭价格为800元/吨,原油价格在8O~9O美元/桶时,间接液化才有经济性。
直接液化对煤炭价格的敏感性也同样明显。
其次,环境成本的提升也将降低煤制油的经济性。
在当前10美元/吨的C02排放交易价下,原油价格在67~77美元/桶以上,间接液化法具有经济性。
但如果CO2排放交易价提高到5O美元/吨,对应的原油价格必须达到96~106美元/桶以上,间接液化法才具有经济性。
据神华煤制油化工有限公司方面透露:
在现在的煤价下,如果国家油价维持在65~70美元一桶,按照既有的设计条件运转下来,直接液化项目能够盈利,至少不会亏损。
但是,国家发改委能源研究所高级顾问周凤起算过一笔账,每生产1吨煤制油,将消耗4吨煤炭,比如生产发热量10000大卡的石油,将消耗4吨5000大卡的煤炭,在转化过程中,能量消耗一半。
当煤炭价格达到1000元/吨时,煤制油成本价将达10000元/吨,折算成原油价格将在120美元/桶左右。
而且新上一个产量为100万吨/年的煤制油项目,还要投资100亿元人民币。
因此,发展煤制油从经济效益上看并不划算。
此外,煤制油项目还受到各种因素制约,特别是能源、市场、投资能力、科研力量和国际合作等因素。
煤制油项目未能解决的设备问题和技术稳定问题也是其商业化运作的制约因素。
因此,除南非曾因禁运而大规模商业性开发煤制油项目外,美国、德国、日本虽纷纷投巨资研究煤制油项目,建设试验工程,但没有真正投入商业运行。
四、工艺技术发展状况
1.间接液化技术
(1)Sasol工艺
间接液化已有70多年历史,1943年F-T合成技术实现工业化,1956年在南非形成了规模化工业生产,是成熟可靠的煤液化技术。
至今,在南非已建成了3个大厂,年耗原煤4600万吨,生产液体烃类产品760多万吨,其中油品近500万吨。
Sasol已成为世界煤化工装置的典范。
神华集团、宁夏煤业集团与南非Sasol公司合作,计划投资300亿元在宁夏建设煤间接液化项目。
建成投产后,每年将生产320万吨油品。
神华宁煤与沙索公司合作的间接液化煤制油项目可行性研究报告于2009年11月通过预审,该项目环境影响报告书也已编制完成,并于12月开展了环评公示。
该项目目前正在进行可行性研究,和南非Sasol公司已签署第二阶段合作补充协议和执行计划。
而另一间接液化项目—陕西榆林项目已暂停。
表2主要间接液化工业应用情况
公司机构
工艺名
单体最大规模
应用情况
Sasol
SSPD、SAS
100万吨/年
Sasol工业化、神华筹建
Shell
SMDS
50万吨/年
来西亚Bintulu工业化
Exxon-Mobil
MTG
1.25万桶/d
新西兰工业化
德国伍德
MTG
10万吨/年
晋煤工业化
中国科学院
F-T浆态床
18万吨/年
伊泰、潞安工业化,神华试运行
兖矿
高低温F-T
5000吨/年
山东枣庄的鲁南化肥厂中试
中石化
F-T合成RFI-1催化剂
3000吨/年
镇海炼化建设的中石化第一套GTL中试
(2)荷兰Shell公司的SMDS工艺
SMDS工艺包括造气、F-T合成、中间产品转化和产品分离4部分,主要产品是柴油、航空煤油、石脑油和蜡。
1993年在马来西亚Bintulu建成50万吨/年的工厂。
(3)Exxon-Mobil的MTG工艺
Mobil甲醇-汽油(MTG)间接液化工艺利用两个截然不同的阶段从煤或天然气中生产汽油。
1984年Mobil公司在德国波恩附近的Wesseling建成了一套100桶/d汽油的MTG工艺固定床示范装置,之后又建成一套同样规模的流化床示范装置。
新西兰建造了一座1.25万桶/d的商业化液化厂,处理从Maui矿区生产的气体。
尽管这座液化厂仍进行着生产,但是只生产甲醇,目前这样的经济性最好。
(4)德国伍德公司的MTG生产工艺
晋煤集团与中科院山西煤化所共同组建山西省粉煤气化工程研究中心,联合攻关,在粉煤、特别是劣质粉煤气化的关键技术方面寻求突破。
项目建设过程中,他们与拥有国际先进技术的美国美孚公司和德国伍德公司紧密合作,交流学习,掌握了相关先进技术。
项目的流程工艺是,采用拥有我国自主知识产权的“灰熔聚流化床粉煤气化技术”,将劣质粉煤气化造气,生成甲醇,再通过德国伍德公司的MTG生产工艺,间接生成油品。
晋煤集团10万吨/年甲醇制汽油项目于2009年6月试车成功,该项目配套的30万吨/年煤制甲醇项目所用的“灰熔聚流化床粉煤气化技术”于3季度试车成功。
(5)其它国外以天然气为原料的工艺
除了已经运行的商业化间接液化装置外,埃克森-美孚(Exxon-Mobil),英国石油(BP-Amoco),美国大陆石油公司(ConocoPhillips)和合成油公司(Syntroleum)等也正在开发自己的费托合成工艺,转让许可证技术,并且计划在拥有天然气的边远地域来建造费托合成天然气液化工厂。
(6)中国科学院山西煤炭化学研究所自主研发的催化剂和“煤基液体燃料合成浆态床工业化技术”(中科合成油技术F-T)
中国科学院山西煤炭化学研究所合成油工程研究中心(现中科合成油技术有限公司)完成了2000t/a煤炭间接液化工业试验。
2001年ICC-IA低温催化剂的合成技术完成中试验证。
2007年ICC-II高温催化剂的合成技术进行了中试试验,开发了ICC-I低温(230-270℃)和ICC-II高温(250-290℃)两大系列铁基催化剂技术和相应的浆态床反应器技术,并分别形成了两个系列合成工艺,即针对低温合成催化的重质馏分合成工艺ICC-HFPT和针对高温合成催化剂的轻质馏分合成工艺ICC-LFPT。
工业应用:
伊泰16万吨/年煤制油项目采用的中科院山西煤化所技术于2009年3月试车成功,并于9月正式投产,实现了装置负荷在60%至80%之间的长周期运转。
潞安矿业集团煤制油项目(试车)16万吨/年,主要产品为柴油、液化石油气、石脑油及少量混合醇燃料。
项目是国家“863”高新技术项目和中国科学院知识创新工程重大项目的延续项目,也是通过国家级项目招标确定的国内首个间接液化煤基合成油示范工厂,被国家发改委列入国家煤化工中长期发展规划和“863”高新技术项目。
项目已通过山西省发改委的立项审批,并报国家发改委核准备案。
潞安在山西在建300万吨煤变油项目,预计将于2010年底建成投产,同时在新疆上马300万吨煤变油项目。
并计划到2020年左右,建成年产1500万吨的煤制油基地。
神华18万吨/年油品将与2010年试车。
(7)兖矿技术
2002年12月,兖矿集团在上海组建上海兖矿能源科技研发有限公司,开始开展煤间接液化技术的研究和开发工作。
2004年3月5000吨级低温费托合成、100吨/年催化剂中试装置建成,并实现一次投料试车成功。
2006年4月又开始建设万吨级高温费托合成中试装置和100吨/年高温费托合成催化剂中试装置,2007年初高温费托合成催化剂中试装置生产出高温II型催化剂,2007年6月高温费托合成中试装置一次投料开车成功生产出合格产品。
2010年2月5日,由兖矿集团自主研发完成的“高温流化床费托合成技术”科技成果通过中国石油和化学工业协会组织的技术鉴定。
据兖矿集团介绍,兖矿集团建设了我国唯一的规模为5000吨/年油品的高温流化床费托合成中试装置,位于山东枣庄的鲁南化肥厂,采用两种催化剂连续满负荷运行1580小时,进行了多种工况考核试验。
兖矿集团自主知识产权的陕西榆林100万吨/年间接液化煤制油项目于1月通过了环保部的环评,目前该项目全部二十三份支持文件都已经完备,等待核准。
(8)中石化F-T合成RFI-1催化剂
中石化石科院于2004年开始进行费托合成的相关研究工作,开展了F-T合成的催化剂、反应工程、系统工程等方面的研究工作,开发出了第一代高性能的固定床F-T合成催化剂RFI-1。
2006年初RFT-1催化剂通过中石化集团公司组织的中试评议。
2006年6月在镇海炼化建设的中石化第一套3000t/aGTL中试装置中使用。
2.直接液化
除间接液化工艺外,国外在煤炭的直接液化方面也相当活跃,德国、美国、日本等工业发达国家先后开发了十几种新工艺,其中几种先进技术完成了投煤规模为50-200t/d的大型中试。
比较著名的有溶剂精炼煤法(SRC-l,SRC-2)、供氢溶剂法(EDS)、氢煤法(H-COAL)等。
表3主要直接液化发展情况
公司
工艺
发展情况
德国鲁尔
IGOR
中试
日本NEDO
NEDOL法烟煤液化工艺
中试
美国
HTI
中试
神华
自主液化工艺
108万吨/年工业化
(1)德国IGOR工艺
20世纪70年代,德国鲁尔煤炭公司与Veba石油公司和DMT矿冶及检测技术公司合作开发出了IGOR工艺,其主要特点是反应条件较苛刻(温度470℃,压力30MPa),催化剂采用炼铝工业的废渣,液化反应和液化油加氢在一个高压系统内进行,可一次得到杂原子含量极低的液化精制油。
循环溶剂是加氢油,供氢性能好,煤液化转化率高。
(2)日本NEDOL法烟煤液化工艺
日本于20世纪80年代初专门成立了日本新能源产业技术综合开发机构(NEDO),负责组织十几家大公司合作开发出了NEDOL法烟煤液化工艺。
该工艺的特点是反应压力低(17-19MPa),反应温度为455-465℃;催化剂采用合成硫化铁或天然硫铁矿;固液分离采用减压蒸馏的方法;配煤浆用的循环溶剂单独加氢;液化油含有较多的杂原子还需加氢提质才能获得合格产品。
(3)美国HTI工艺
美国HTI工艺是在H-COAL工艺基础上发展起来的。
该工艺采用两段催化液化,悬浮床反应器和铁基催化剂。
其主要特点是反应条件较温和(440-450℃,反应压力17MPa);催化剂用量少;在高温分离器后面串联有在线固定床反应器,对液化油进行加氢精制;固液分离采用临界溶剂萃取的方法,从液化残渣中最大限度地回收重质油,从而大幅度提高了液化油收率。
(4)神化煤直接液化技术
我国从20世纪70年代开始开展煤炭直接液化技术研究。
1997-2000年煤炭科学研究总院分别与美国、德国、日本等有关机构合作,完成了神华煤、云南先锋煤和黑龙江依兰煤直接液化示范工厂的初步可行性研究。
神华集团在对国内外煤直接液化技术进行了认真比选的基础上,采用众家之长和成熟的单元工艺技术,开发出神华自己的煤直接液化工艺路线和催化剂合成技术。
以无水无灰基煤计,C4以上油收率为57%-58%,油品重馏分增多,更有利于柴油产品的生产。
催化剂表现出非常高的活性具有生产流程简单、操作平稳方便、投资小、运行成本低等优点。
神华集团煤直接液化项目在内蒙古鄂尔多斯市伊金霍洛旗乌兰木伦镇建的一期工程首条生产线投资达123亿元,每年可转化350万吨煤,生产108万吨柴油、液化石油气、石脑油等产品。
首条生产线2008年12月30日开始投煤,12月31日顺利实现油渣成型,打通全流程,产出合格油品和化工品。
并于2009年三季度进行第二次试车,截至12月,已经总计出产了10万吨左右汽油、柴油等油品,首列石脑油专列于10月18日载着2300吨石脑油出厂运往天津港外销。
神华煤制油化工公司18万吨/年的铁剂浆态床间接液化装置也成功试运行。
并于2009年三季度进行第二次试车,截至12月,已经总计出产了10万吨左右汽油、柴油等油品,首列石脑油专列于10月18日载着2300吨石脑油出厂运往天津港外销。
神华煤制油化工公司18万吨/年的铁剂浆态床间接液化装置也成功试运行。
神华集团也已经正式拿到成品油批发执照。
据了解,神华集团将在第一条直接液化生产线工业化运行后,再建一期工程的另外两条生产线,最终达到年产320吨各种产品的能力。