焦炉煤气生产直接还原铁技术分析研究.docx
《焦炉煤气生产直接还原铁技术分析研究.docx》由会员分享,可在线阅读,更多相关《焦炉煤气生产直接还原铁技术分析研究.docx(12页珍藏版)》请在冰豆网上搜索。
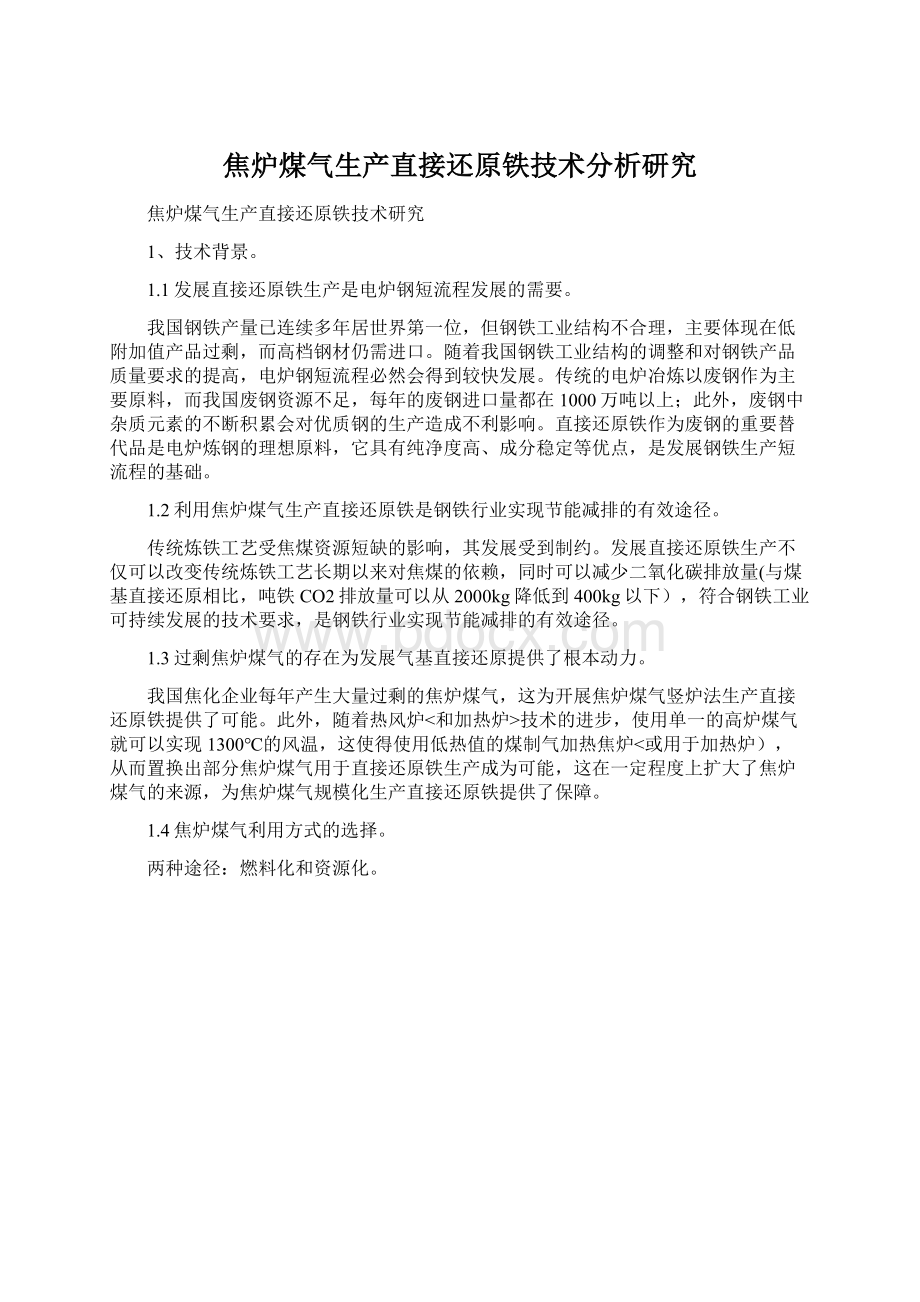
焦炉煤气生产直接还原铁技术分析研究
焦炉煤气生产直接还原铁技术研究
1、技术背景。
1.1发展直接还原铁生产是电炉钢短流程发展的需要。
我国钢铁产量已连续多年居世界第一位,但钢铁工业结构不合理,主要体现在低附加值产品过剩,而高档钢材仍需进口。
随着我国钢铁工业结构的调整和对钢铁产品质量要求的提高,电炉钢短流程必然会得到较快发展。
传统的电炉冶炼以废钢作为主要原料,而我国废钢资源不足,每年的废钢进口量都在1000万吨以上;此外,废钢中杂质元素的不断积累会对优质钢的生产造成不利影响。
直接还原铁作为废钢的重要替代品是电炉炼钢的理想原料,它具有纯净度高、成分稳定等优点,是发展钢铁生产短流程的基础。
1.2利用焦炉煤气生产直接还原铁是钢铁行业实现节能减排的有效途径。
传统炼铁工艺受焦煤资源短缺的影响,其发展受到制约。
发展直接还原铁生产不仅可以改变传统炼铁工艺长期以来对焦煤的依赖,同时可以减少二氧化碳排放量(与煤基直接还原相比,吨铁CO2排放量可以从2000kg降低到400kg以下),符合钢铁工业可持续发展的技术要求,是钢铁行业实现节能减排的有效途径。
1.3过剩焦炉煤气的存在为发展气基直接还原提供了根本动力。
我国焦化企业每年产生大量过剩的焦炉煤气,这为开展焦炉煤气竖炉法生产直接还原铁提供了可能。
此外,随着热风炉<和加热炉>技术的进步,使用单一的高炉煤气就可以实现1300℃的风温,这使得使用低热值的煤制气加热焦炉<或用于加热炉),从而置换出部分焦炉煤气用于直接还原铁生产成为可能,这在一定程度上扩大了焦炉煤气的来源,为焦炉煤气规模化生产直接还原铁提供了保障。
1.4焦炉煤气利用方式的选择。
两种途径:
燃料化和资源化。
焦炉煤气中CH4:
25%〜26%,H2:
56%〜%,H2发热值仅为2580kCal/m3约为曱烷的四分之一,因此,将焦炉煤气作发热剂不尽合理。
由于氢气的还原潜能远远高于CO,因此将焦炉煤气用作还原剂更有利于其化学能的合理利用。
与天然气相比焦炉煤气中的甲烷含量更低,这使得其重整负荷减轻,耗氧量减少,能量消耗也降低。
焦炉煤气的利用应走资源化的道路。
焦炉煤气不同利用方式的投资收益比较。
焦炉煤气用于制氢或直接还原生产海綿铁可以获得最好的经济和环境效益,焦炉煤气生产直接还原铁可以为钢铁企业节能减排、提高产品附加值提供一条有益的途径。
2、焦炉煤气自重整直接还原铁生产工艺。
2.1国内气基直接还原技术的发展方向。
主要包括:
2.1.1煤气化<水煤浆气化、粉煤气化)配竖炉工艺生产还原铁技术方案:
煤制气竖炉方案在技术上是可行的,具有较好的发展前景,但目前主要受到煤制气技术发展的制约,煤制气竖炉流程的发展有赖于低压煤制气技术的突破。
2.1.2天然气转化生产还原气配竖炉工艺生产直接还原铁技术方案:
该方案需要有丰富的天然气资源做保障,而我国天然气资源缺乏,而且,天然气裂解工艺复杂、投资较大,因此,采用天然气作为原料气的气基直接还原工艺在我国很难得到发展。
2.1.3焦炉煤气转化生产还原气配HYL工艺生产还原铁技术方案。
焦炉煤气作为一种富氢气源可以用作优质还原气生产直接还原铁,其在冶金工业中的应用前景越来越受到人们的重视,焦炉煤气生产直接还原铁方案是目前国内直接还原技术领域研究的热点,并有望最快实现工业化。
2.2HYL-ZR自重整直接还原铁生产工艺。
传统的气基竖炉直接还原铁生产工艺以Midrex和HYL法为代表,主要以天然气为原料生产直接还原铁。
天然气的主要成分是甲烷,而甲烷无法直接参与还原反应,需要首先将其转化为H2和CO2,因此,在天然气进入竖炉前首先要经过气体重整炉,在金属催化剂的作用下与水蒸气反应发生分解。
HYL法自1997年开始率先完全取消了天然气重整炉,实现了天然气在竖炉内的自重整,在不增设重整炉的前提下提高了竖炉的生产效率,并且开发出可使用焦炉煤气、煤制气等多种气源的气基还原工艺,即HYL-ZR工艺。
两个工艺方案的区别:
是否需要设置冷却段,使用焦炉煤气还原时必须设置冷却回路,使煤气中的杂质分解以满足还原回路对还原气体的要求,因此,使用焦炉煤气的HYL-ZR方案无法得到热态的直和原铁,从而无法实现热态输送。
3、焦炉煤气直接还原铁过程中的关键技术问题及对策。
目前,世界上超过80%的直接还原铁生产是以天然气为原料的,天然气竖炉技术已经非常成熟。
焦炉煤气与天然气相比甲烷含量较低,氢气含量高,更宜作为还原气使用,但由于焦炉煤气中杂质(S、BTX、焦油、萘>较多,因此如何净化焦炉煤气就成为其利用的关键。
3.1甲烷自重整技术。
气基直接还原一般要求还原气氛中CO+H2>90%,CO2+H2O/(C02+H2+C0+H20><5%。
焦炉煤气中含20%以上的CH4,在低温条件下,直接用焦炉煤气还原铁矿石会发生渗碳反应,降低还原速度;在较高温度下,CH4作为惰性气体存在,同样会降低还原速度;此外,从充分利用能源的角度出发也需要将甲烷转化加以利用,因此使用焦炉煤气与天然气一样都需要进行原料气体重整。
甲烷的自重整:
是指无需专设重整炉,原料气体在输送过程中或在竖炉内在高温活性金属铁的催化下进行重整。
提高温度有利于曱烷重整<水蒸气重整)反应的进行,当温度大于1000℃时,曱烷的重整比较彻底,因此要想实现竖炉内的自重整,反应气的温度应大于1000℃。
在气基直接还原工艺中,受加热炉材质的影响,还原气最高只能加热到970℃,从1995年开始HYL工艺引入了O2气喷入技术,吨铁用氧量为12-20m3,该技术使用了特殊设计的燃烧器,借助天然气的部分氧化使还原气的温度达到1085℃,氧气喷入技术的发展最终使得自重整工艺得以实现。
第一套采用HYL-ZR自重整技术的生产装置,于1998年4月在墨西哥的蒙特雷薄板厂建成投产,该装置的运行实践证明了曱烷自重整技术的可行性。
3.2焦炉煤气中S的影响。
3.2.1S的分配问题.
进入竖炉的硫主要来自于焦炉煤气和铁矿石,其中约40%的硫在CO2吸附环节被去除,60%的硫进入直接还原铁。
3.2.2H2S气体对加热炉管壁的腐蚀问题。
管外:
主要是燃烧产生腐蚀性硫氧化物以后对外管壁形成的硫化和氧化腐蚀。
管内:
主要是H2S分解后,气体中S浓度超过管壁吸附能力从而形成Ni-S溶体和CrS等内硫化物,从而破坏管壁造成腐蚀。
3.2.3直接还原工艺对S含量的要求。
原料中的硫对直接还原工艺本身没有太大影响,直接还原铁中的硫在炼钢铁水脱疏中可以脱除。
考虑到加热炉烟气排放可能对环境造成的影响,同时为降低炼钢工序成本,提高产品质量,要求应对焦化厂送出的焦炉煤气进行脱硫,将煤气中的H2S降至20mg/N.m3以下。
3.3焦炉煤气中焦油、萘的影响。
HYL-ZR工艺中,竖炉内的工作压力为0.6MPa,而焦化厂送出的煤气压力约5kPa,因此需要上煤气增压设施对焦炉煤气进行加压。
由于焦炉煤气中含有焦油≤50mg/N.m3,萘≤500mg/N.m3,因此在增压的过程中会析出大量的焦油和萘,容易堵塞设备和管道。
应设焦炉煤气脱萘、脱焦油设施,将焦炉煤气中的萘降至50mg/N.m3以下,焦油降至10mg/N.m3以下。
3.4焦炉煤气中BTX(苯、甲苯、二甲苯)的影响。
使用焦炉煤气为还原气体的HYL-ZR直接还原工艺与使用天然气相比,由于焦炉煤气中含有BTX(苯、甲苯、二曱苯混合物)<从焦化厂送出的焦炉煤气中BTX<4000mg/N.m3>,而BTX对HYL-ZR工艺本身最大的影响就是当气体通过加热器时会产生析碳,从而造成管道堵塞,因此如何使BTX裂解,就成了以焦炉煤气为原料的HYL-ZR工艺能否打通的技术关键。
HYL-ZR工艺通过将焦炉煤气通入竖炉冷却段的方式,在热金属铁的作用下使BTX分解。
该方法已经得到实验室结果的支持,但通过该方式只能生产冷态直接还原铁,其技术经济性有待提高,而且其工业规模的运行效果也有待于进一步检验。
3.4直接还原铁热态输送技术
HYTEMP是HYL-ZR工艺除O2喷入技术以外的另一项主要技术,该技术通过一个专用的气体加热装置,将运载气体<工艺气或N2>加热到600℃左右,并使用运载气体将约700℃的直接还原铁直接输送至电弧炉内,通过这种方式可以减小直接还原铁的温降。
该装置已于1998年在墨西哥的蒙特雷电炉厂投入工艺生产。
通过直接还原铁热送技术可以有效回收直接还原铁的显热,不仅能够获得显著的经济效益,同时可以减少温室气体排放。
电炉使用热态<〜700°C>高碳DRI可节约电能130kWh/t钢水,电炉的供电冶炼时间可减少30%,电炉的生产能力可提高20%。
HYTEMP工艺产品具有高温和高含碳量的特点,其优势主要体现在炼钢环节。
为了对DRI的显热进行回收利用,有必要开发热态DRI生产工艺。
吨钢耗电量和吨钢成本与金属化率和碳含量等因素的关系。
3.5热态DRI生产工艺及BTX裂解技术路线探讨。
新的有前途的焦炉煤气处理工艺应该能够合理有效的利用二次热源,同时具有最低的动力费用消耗。
考虑到焦炉煤气中的BTX对还原工艺的危害,主要体现在加热和加压过程中的析碳和焦油析出,因此,应在焦炉煤气进入直接还原系统之前进行煤气精制。
方案一:
目前焦化厂对此处焦炉煤气的物理热<650°C>并未进行利用,如果可以对来自焦炉的热的焦炉煤气直接进行净化处理,则既可以使煤气的余热得到回收又可以避免由于煤气升温带来的问题。
在焦炉旁设置高温裂解炉<1200-1250°C>,使焦油、BTX等杂质分解。
方案二:
除高温裂解法以外,以金属铁为催化剂,以焦炉煤气为冷却介质,在熄焦炉内对焦炉煤气进行处理也是一种煤气净化的思路。
与传统的干熄焦工艺相比,由于焦炉煤气中的杂质和甲烷裂解吸热,使得其具有更高的传热效率,此外,煤气中的氢气还可以与焦炭中的硫化物和有机硫反应生成硫化氢,从而显著降低焦炭内的硫含量,达到脱硫效果。
方案三:
由于BTX杂质与甲烷相比,热稳定性差,更容易发生重整反应,因此可以考虑采用重整法对焦炉煤气进行净化处理。
与方案一相似,该方案直接利用来自焦炉的热焦炉煤气,采用管道喷氧或裂解炉加热的方式将焦炉煤气由650℃左右升高至800-1000℃,在催化剂的作用下发生重整反应。
此处的焦炉煤气重整是半重整,通过配入过量的水蒸气使焦炉煤气中的焦油等大分子化合物优先裂解而大部分甲烷并未分解。
3.6使用100%DRI电炉炼钢。
目前在国外有很多采用100%DRI为原料进行炼钢生产实例,位于阿联酋阿布扎比的ESI钢铁公司和M塔尔公司在墨西哥也有6个全部使用直接还原铁的钢厂,实践证明100%DRI电炉炼钢不存在技术问题。
但国外一般要求SiO2+Al2O3≤3%,国内矿粉SiO2基本在4%以上,而每增加1%的脉石含量,约增加约40公斤的石灰用量,渣量增加64公斤,铁损失约升高11.5公斤,因此电炉是否采用100%DRI需要统筹考虑成本问题。
3.7对球团原料的要求。
由于HYL竖炉对球团矿的还原是在铁矿石软化温度以下进行的,因此球团矿的化学性能、物理和机械性能,以及冶金性能均与高炉使用的球团矿有一定的差别。
HYL-ZR工艺生产对球团矿中脉石、S、P、碱度等性能指标没有特殊要求。
化学性能:
物理和机械性能:
冶金性能:
4、焦炉煤气重整热力学分析。
4.1焦炉煤气重整的方法。
4.1.1曱烷水蒸气重整。
CH4+H2O=3H2+CO(1>
H2O+CO=H2+CO2(2>
由反应1得到H2/CO约为3,反应2继续生产氢气,焦炉水蒸气重整后的H2/CO为5-7。
目前,天然气气基直接还原工艺多采用水蒸气重整法。
4.1.2曱烷部分氧化重整。
CH4+1/2O2=2H2+CO(3>
反应为微放热反应,可在较低的温度下达到90%以上的热力学平衡转化率,反应的H2/CO为1.9-2.1。
4.1.3甲烷CO2重整.
CH4+CO2=2H2+2CO(4>
CO2+H2=H2O+CO(5>
该法可以充分利用CO2,减少碳排放,反应的H2/CO约为2。
4.2反应产物的H2/CO对还原反应的影响。
1/4Fe3O4(s>+H2=3/4Fe(s>+H2O(g>AGº=35550-30.40T<6)
1/4Fe3O4(s>+CO=3/4Fe(s>+CO2AGº=-9832+8.58T<7)
焦炉煤气重整生产直接还原铁,属于富氢气体还原,而氢气还原氧化铁的反应是强吸热反应,如何持续向反应区供给热量是富氢直接还原技术的难点,还原气体中H2/CO越高则还原系统的热负荷也越高。
反应温度为900℃,含铁原料预热,还原气体物理热供热时H2/CO对还原气用量的影响。
富氢气体的热力学利用率随氢含量的增加而提高,因此提高H2/CO有利于提高还原气的综合利用率。
但由于氢气还原反应为吸热反应,提高煤气的H2/CO吨铁还原需要的热量增加,同时由于炉内热收入主要靠还原气物理热来提供,因此,要增加炉内的供热量就必须加大还原气量,而加大气量又会造成气体利用率的进一步降低,这使得反应炉内的气体成分和气体利用率很难得到最优化的协调统一,即反应炉内热平衡和化学平衡之间的矛盾决定了富氢气体一次利用率极限的存在。
自重整工艺入炉气体温度约1085℃,为了维持一定的反应温度,还原气的温降就具有的一定的局限性。
取气体温降为250℃,当H2/CO=1.67时,还原气利用率接近热力学利用率,约为34.5%。
当H2/CO>1.67时,还原气的利用率迅速降低,适宜的H2/CO应为1-2。
目前,水蒸汽重整的气体产物的H2/CO=4.6,过高的H2/CO较难满足富氢煤气还原的经济性要求。
若对焦炉煤气进行CO2重整,可以在不引入H2的前提下,增加CO的量,有利于重整产物H2/CO的降低。
为此对焦炉煤气CO2重整过程进行了热力学模拟计算。
4.3焦炉煤气CO2重整热力学计算。
典型焦炉煤气成分:
联立:
分压总和方程,
独立反应的平衡常数方程
元素原子摩尔量恒定方程
对平衡态气体组分含量进行计算。
CH4含量随着CO2配入量的增加逐渐减少;CO2配入量>20%时,H2/CO<2,CO2配入量>30%时,开始出现H2O和CO2,甲烷的转化率在95%以上。
不同CO2配加量对H2/CO的影响
温度对气体产物的H2/CO影响显著,温度升高H2/CO迅速降低。
当反应温度大于900℃时达到一个稳定值约为1.7,可见CO2重整反应温度应大于1000℃。
反应温度对H2/CO的影响
压力对CO2重整反应的影响不大,低压下更有利于CH4的转化,但系统压力对还原气体总量影响显著。
反应压力对H2/CO的影响
4.4焦炉煤气CO2重整与水蒸气重整效果的比较。
焦炉煤气重整过程中,水蒸气配入量对其重整产物H2/CO的影响较小,H2/CO的大小主要决定于CO2的配入量,通过改变水蒸气和CO2配入量的方法可以实现对其重整效果
的有效调节,从而对还原气体成分进行合理控制。
5、总结。
合理利用焦炉煤气资源,开展直接还原铁生产,可以缓解国内废钢需求,是钢铁企业优化产品结构,实现节能减排的一条有益途径,是高炉炼铁流程的有益补充。
焦炉煤气精制是其利用过程中的关键。
HYL-ZR工艺焦炉煤气净化的技术方案不能用于生产热态直接还原铁,而且其工业规模的运行效果有待实践检验。
焦炉煤气热态直接还原铁生产技术有待开发。
与甲烷水蒸气重整法相比,CO2重整法的H2/CO值更低,从热平衡的角度更有利于降低还原气消耗量,应该给以重视。