高温合金疲劳.docx
《高温合金疲劳.docx》由会员分享,可在线阅读,更多相关《高温合金疲劳.docx(9页珍藏版)》请在冰豆网上搜索。
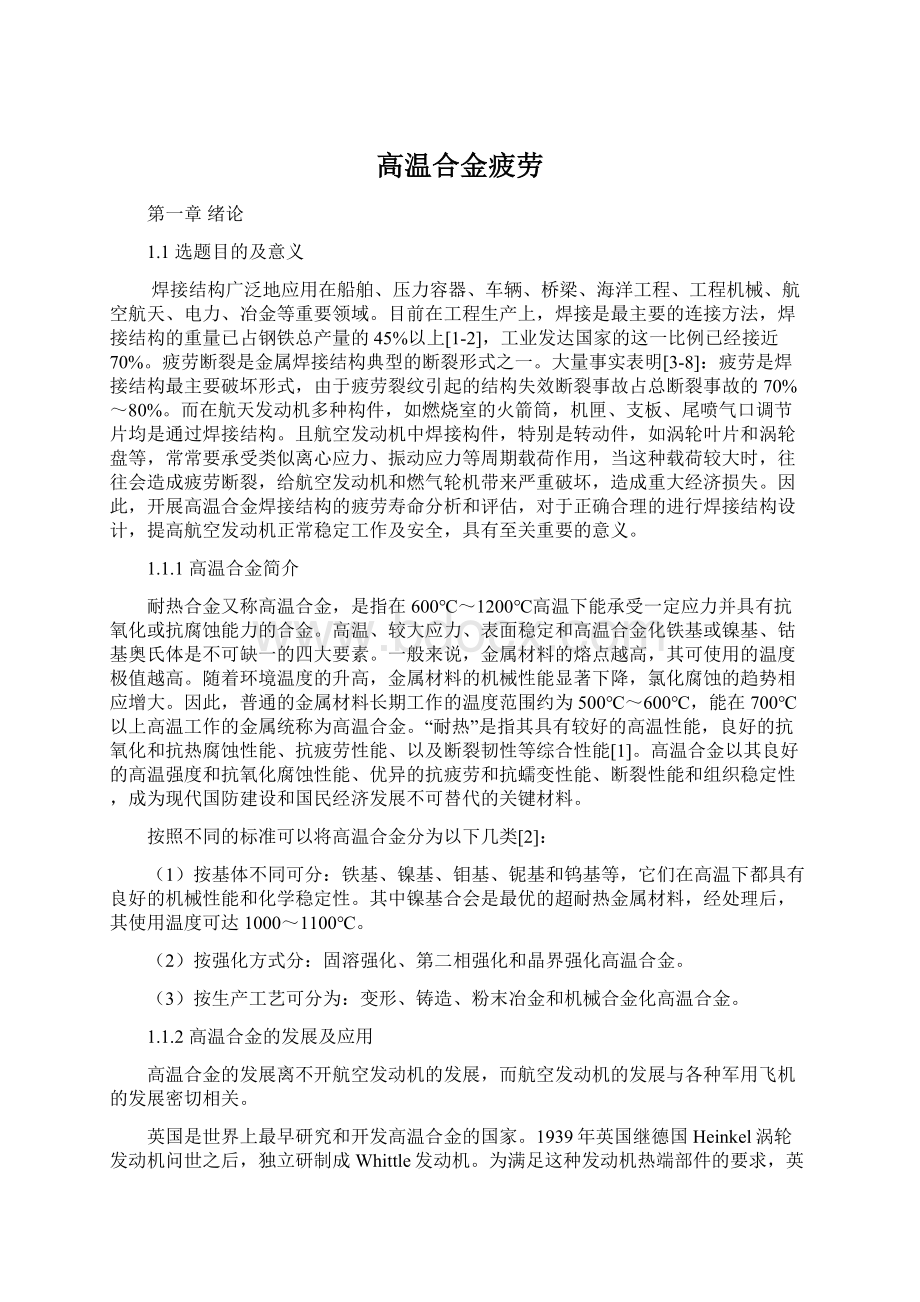
高温合金疲劳
第一章绪论
1.1选题目的及意义
焊接结构广泛地应用在船舶、压力容器、车辆、桥梁、海洋工程、工程机械、航空航天、电力、冶金等重要领域。
目前在工程生产上,焊接是最主要的连接方法,焊接结构的重量已占钢铁总产量的45%以上[1-2],工业发达国家的这一比例已经接近70%。
疲劳断裂是金属焊接结构典型的断裂形式之一。
大量事实表明[3-8]:
疲劳是焊接结构最主要破坏形式,由于疲劳裂纹引起的结构失效断裂事故占总断裂事故的70%~80%。
而在航天发动机多种构件,如燃烧室的火箭筒,机匣、支板、尾喷气口调节片均是通过焊接结构。
且航空发动机中焊接构件,特别是转动件,如涡轮叶片和涡轮盘等,常常要承受类似离心应力、振动应力等周期载荷作用,当这种载荷较大时,往往会造成疲劳断裂,给航空发动机和燃气轮机带来严重破坏,造成重大经济损失。
因此,开展高温合金焊接结构的疲劳寿命分析和评估,对于正确合理的进行焊接结构设计,提高航空发动机正常稳定工作及安全,具有至关重要的意义。
1.1.1高温合金简介
耐热合金又称高温合金,是指在600℃~1200℃高温下能承受一定应力并具有抗氧化或抗腐蚀能力的合金。
高温、较大应力、表面稳定和高温合金化铁基或镍基、钴基奥氏体是不可缺一的四大要素。
一般来说,金属材料的熔点越高,其可使用的温度极值越高。
随着环境温度的升高,金属材料的机械性能显著下降,氯化腐蚀的趋势相应增大。
因此,普通的金属材料长期工作的温度范围约为500℃~600℃,能在700℃以上高温工作的金属统称为高温合金。
“耐热”是指其具有较好的高温性能,良好的抗氧化和抗热腐蚀性能、抗疲劳性能、以及断裂韧性等综合性能[1]。
高温合金以其良好的高温强度和抗氧化腐蚀性能、优异的抗疲劳和抗蠕变性能、断裂性能和组织稳定性,成为现代国防建设和国民经济发展不可替代的关键材料。
按照不同的标准可以将高温合金分为以下几类[2]:
(1)按基体不同可分:
铁基、镍基、钼基、铌基和钨基等,它们在高温下都具有良好的机械性能和化学稳定性。
其中镍基合会是最优的超耐热金属材料,经处理后,其使用温度可达1000~1100℃。
(2)按强化方式分:
固溶强化、第二相强化和晶界强化高温合金。
(3)按生产工艺可分为:
变形、铸造、粉末冶金和机械合金化高温合金。
1.1.2高温合金的发展及应用
高温合金的发展离不开航空发动机的发展,而航空发动机的发展与各种军用飞机的发展密切相关。
英国是世界上最早研究和开发高温合金的国家。
1939年英国继德国Heinkel涡轮发动机问世之后,独立研制成Whittle发动机。
为满足这种发动机热端部件的要求,英国国际镍公司于该年成功研制成Nimonic75合金[3]。
美国高温合金的发展晚于英国。
高温合金在美国的发展起始于上世纪三十年代,主要应用于飞机发动机的涡轮增压器。
1942年美国钴业公司发展了HastelloyB变形镍基合金,用于通用电器公司研制的Bellp—59喷气发动机。
1943年在通用电器公司的J—33发动机使用了钴基合金HS-21制作涡轮工作叶片,代替原来选用的变形合金HastelloyB,开创了使用铸造高温合金制作涡轮叶片的历史[4]。
由于吸收了英国高温合金发展的宝贵经验,很快发展了40多种高温合金。
1944年美国西屋公司的YanKee19A发动机采用了钴基合金HS-23精密铸造叶片[5]。
1950年由于钴资源短缺,镍基高温合金迅速发展,广泛用作涡轮叶片。
这一时期,美国普惠公司、通用电器公司和特殊金属公司分别研制成功Waspalloy、M-252和Udimet500等合金,并在这些合金的基础上,采用了类似于Nimonic合金的不断强化的方法,发展形成了Inconel、Mar-M和Udimet等牌号系统[6]。
直到现在,镍基合金用量愈来愈大,用途愈来愈多。
50年代,由于真空熔炼技术的出现,广泛发展了镍基铸造合金IN-100、Rene100和B1900[7]。
60年代和70年代,高温合金在美国的新工艺蓬勃发展,工艺技术的发展超过了合金成分的研制,成为高温合金向前发展的主要推动力,发展了许多性能更优越的高温合金,如定向凝固(DS)合金,单晶(SC)合金和DS共晶合金。
单晶合金的使用温度达到了合金熔点的90%。
又如粉末合金和弥散强化高温合金,利用高温合金粉末制备高强度涡轮轮盘,利用弥散强化合金制备火箭筒、导向叶片和涡轮叶片。
在高温合金的研究、生产和应用方面,美国在全世界处于领先地位。
中国航空工业自1951年4月开始建立,经历了从维修、仿制、改进、改型到自主研发的道路。
最初仿制前苏联的米格15飞机,国产化发动机叫做WP5,中国高温合金的生产就是从试制WP5发动机所需高温合金开始的。
1956年初由第二机械工业部和重工业部批准WP5发动机火箭筒材料GH3030合金的试制任务[8]。
同年,在前苏联专家指导下,由抚顺钢厂将钢锭锻成板坯,表面质量良好[9]。
1957年,沈阳发动机厂用国产GH3030板材加工成火焰筒,在WP5发动机上通过了长期试车考核[8],我国第一个高温合金正式试制成功。
继GH3030试制成功之后,抚顺钢厂又试制成功WP5用涡轮叶片合金GH4033和涡轮盘合金GH34,航空材料研究所试制成功涡轮导向叶片材料K412铸造镍基合金。
到1957年底,歼5飞机发动机用4种高温合金全部试制成功[4]。
1958年为配合WP6发动机的生产,开始对涡轮叶片合金GH4037、火箭筒材料GH3039和鱼鳞片材料GH3044开展试制工作[8]。
其中,抚顺钢厂把电渣重熔工艺应用于GH4037合金,由于夹杂物含量降低,热加工塑性提高,为GH3047合金的试制成功奠定了基础,也为高温合金生产开辟了型的途径。
由于中国缺少镍,为了节约镍,利用国产资源,我国开展了以铁代镍的高温合金研究工作。
1958年,师昌绪先生带领中国科学院金属所高温合金研究组,相继成功研制出铁基高温合金808、GH2135、GH1140等。
其中航空材料研究所研制成功的GH1140铁基板材合金,抗冷热疲劳性能好,塑性高,已成为一种优良的、生产量最大的火箭筒材料[10]。
钢铁研究总院研制的铁基合金K213合金是中国目前比较理想的750℃以下工作的增压涡轮材料[10]。
中科院金属所研制的GH2035A铁基变形合金,制成涡轮螺浆发动机一级涡轮内外环零件并已投入民航使用[10]。
同期,我国除了开展以铁代镍的高温合金研制外,还开展了以铸代锻的高温合金工艺研究。
中国科学院金属所成功研制美国最成熟的铸造镍基合金IN100,钢铁研究总院研制成功铸造镍基合金K418[10]等。
进入20世纪90年代,我国自行设计出自己的先进航空发动机,科研部门研制了一批具有先进水平的高温合金,如定向凝固镍基高温合金DZ417G等,单晶合金DD403、DD402等。
进入21世纪,由于能源的需要,我国为满足不同型号中型和重型燃气发动机的需要,正在研制一批抗热腐蚀高温合金,例如铸造涡轮叶片合金K444[11]、K435[12]、K446[13]和变形合金涡轮叶片合金GH4413[14]等。
50多年来,我国高温合金研究已经取得了令人瞩目的成就,几十年来,中国共生产6万多吨高温合金,保证了我国5万多台航空发动机及航天火箭发动机的生产需要,同时也满足了其他民用工业及燃气轮机的要求[8]。
高温合金在航空发动机和各种工业燃气轮机中有广泛的应用。
自四十年代初期,由于迫切要求发展先进燃气涡轮发动机的技术,促使高温合金得到了快速发展。
在现代先进的航空发动机中,高温合金材料在发动机总重量的质量比重达到了40%~60%[5]。
高温合金主要应用于航空发动机的四大热端部件,即:
导向器、涡轮叶片、涡轮盘和燃烧室。
这些热端部件在实际工作状态中承受着非常复杂的载荷状况。
所以要求高温合金必须具有良好的热稳定性、热强性和使用条件下的长期组织的稳定性。
除在航空发动机和各种工业燃气轮机中有广泛的应用外,还可以用于制作火箭发动机的各种高温零部件,如发动机涡轮轴、盘、喷管等,此外,在能源动力、石油化工,交通运输和玻璃建材等工业部门均有应用,甚至可以用作低温钢材和耐蚀材料[4]。
1.1.3GH4169高温合金简介及应用发展
本课题主要是对GH4169高温合金的断裂力学性能和疲劳性能进行研究,所以在本节将对该合金作出概述。
GH4169合金是镍一铬一铁基高温合金。
GH4169合金属于镍基变形高温合金。
镍基合金是一种最复杂的合金。
它被广泛地应用于制造各种高温部件。
同时,也是所有高温合金中最为注目的一种合金。
它的相对使用温度在所有普通合金系中也是最高的。
目前,先进的飞机发动机中这种合金的比重在50%以上[5]。
GH4169合金是由国际镍公司亨廷顿分公司的Eiselstein研制成功,于1995年公开介绍的时效硬化镍—铬—铁基变形合金。
合金是以体心立方γ〞和面心立方
γ′相为沉淀强化的一种镍基变形高温合金,在650℃以下具有高的抗拉强度、屈服强度和良好的塑性,具有良好的抗腐蚀、抗辐射能、疲劳、断裂韧性等综合性能,以及满意的焊接和焊后成型性能等[15]。
合金在-253~650℃很宽的温度范围内组织性能稳定,成为在深冷和高温条件下用途极广的高温合金。
由于GH4169良好的综合性能,目前被广泛用于航空发动机的压气机盘、压气机轴、压气机叶片、涡轮盘、涡轮轴、机匣、紧固件和其它结构件和板材焊接件等。
我国于70年代开始研制GH4169合金,主要应用于盘件,使用时间比较短,所以采用真空感应加电渣重熔的双联工艺。
八十年代开始应用于航空领域,提高和改进材料质量、提高合金的综合性能和使用可靠性成为主要的研究方向[16]。
当前GH4169合金的主要研究方向为[17]:
(1)改进冶炼工艺,量化冶炼参数,实现程序稳定操作,使合金显微组织更加均匀,从而得到优良的屈服和疲劳强度以及抗裂纹扩展止裂能力,提高低周疲劳强度等;
(2)改进热处理工艺。
目前的热处理工艺不能很好的消除钢锭中心的偏析,所以对组织的均匀性有不利影响,因此采用合理的均匀化退火工艺,得到细晶坯料成为现在的主要研究方向之一;
(3)改进使用设计。
由于GH4169的工作温度不能高于650℃,所以应当加强零部件的冷却,充分发挥该高温合金的高性能、低成本等优点;
(4)提高组织稳定性能。
由于航空发动机部件的长寿命要求,对于提高GH4169合金长期时效组织稳定性方面也是至关重要的。
本文的研究对象是直接时效GH4169锻件,这种合金材料的化学成分如表1-1所示,其对应的力学性能见表1-2。
直接时效锻造工艺,按照一定的质量要求控制GH4169合会坯料,锻造温度比高强工艺更低,变形量比高强工艺更大,锻后水冷、然后采用时效热处理制度进行热处理。
这种工艺可以保留锻件的形变强化效应,所生产锻件的平均晶粒度大于10级。
直接时效工艺生产的锻件主要用于制造航空发动机的重要转动部件,如压气机盘、封严盘、篦齿盘、涡轮盘和涡轮轴等。
表1-1GH4169合金材料化学成分及参数
元素
Element
C
Cr
Ni
Mo
Al
Fe
Ti
Nb
含量Content(%)
0.02
~
0.08
17.00
~
21.00
50.00~55.00
2.80~3.30
0.20~0.80
15.00~21.00
0.65
~
1.15
4.75
~
5.50
元素
Element
Ca
Mg
Si
Cu
P
S
Bi
Tl
含量Content(%)
≦
0.005
≦
0.005
≦
0.35
≦
0.30
≦
0.015
≦
0.35
≦
0.00003
≦
0.0001
元素
Element
Se
Sn
B
N
Co
Mn
Ag
含量Content(%)
≦
0.0003
≦
0.0005
≦
0.0006
≦
0.01
≦
1.00
≦
0.35
≦
0.0005
表1-2标准规定的直接时效GH4169锻件性能
材料标准
Q/3B4054直接时效GH4169
品种类别
直接时效锻件
热处理工艺
720℃±10℃,8小时保温,以55℃±15℃/h炉冷至620℃±10℃,保温8小时后空冷
拉伸性能
θ
室温
650℃
σb
1450MPa
1170MPa
σ0.2
1240MPa
1000MPa
δ
10%
12%
Ψ
15%
15%
HB
388kgf/mm2
1.2高温合金焊接简介
航空发动机和燃气轮机的高温结构件,如涡轮盘、导向叶片和涡轮叶片等重要部件,均可以通过前述精密铸造或锻造工艺制作毛胚。
而另一些受热和承载的部件,如燃烧室的火箭筒,机匣、支板、尾喷气口调节片等,若是整体采用较大的实心锻件通过机加工制造,加工费用高,同时材料利用率会非常低,所以一般采用高温合金板材冲压-焊接结构。
即使是涡轮叶片也需要焊接耐磨层,导向叶片也需要焊接成组件等。
高效气冷复杂型腔高温合金铸造对开叶片,也需要焊接工艺将其连接在一起,所以高温合金零件的制造离不开焊接技术[18]。
接下来将对高温合金的焊接性和已经使用的焊接工艺做一下简介。
1.2.1高温合金的焊接性
高温合金的化学成分,随着使用温度的升高,变的愈来愈复杂,因而焊接时越来越困难。
影响焊接性能的四大因素是材料因素、设计因素、工艺因素和服役环境[19]。
高温合金的焊接性是指在某一焊接工艺条件下,对合金产生裂纹的敏感性、焊后接头组织的均匀性、焊接接头力学性能和采取工艺措施的可行性的综合评价[20]。
高温合金的焊接性主要受下面几个因素影响:
(1)高温合金的焊接裂纹敏感性。
在高温合金焊接过程中,出现的焊接裂纹通常有热裂纹和再热裂纹,其中热裂纹分为结晶裂纹和液化裂纹,再热裂纹主要是指应变时效裂纹[21]。
液化裂纹和结晶裂纹形成机理相同,都是由于晶间存在脆弱低熔相或共晶,在焊接产生的高温条件下承受不了力的作用而开裂。
两者的区别在于结晶裂纹是液态焊缝金属在凝固过程中形成,而液化裂纹则是由于固态的母材在热循环的峰值温度作用下使晶间层重新熔化后形成的[22]。
应变时效裂纹一般在沉淀强化高温合金的焊接后进行时效处理时或者焊后在高温使用时产生。
由于沉淀强化高温合金晶体内部由于γ′的大量析出得以强化,而晶界强度在高温环境时一般低于晶内强度,加上杂质元素偏聚的不利影响,晶界进一步弱化,从而在晶界发生塑性变形,增加了应变时效裂纹产生倾向,当晶界的实际变形量超过其塑性变形能力就会产生应变时效裂纹[23]。
(2)焊接接头组织的不均匀性。
高温合金焊接接头组织呈现明显的不均匀性,并且由于化学成分和焊接工艺的不用而明显不同。
固溶强化高温合金的组织比较简单,这类合金焊接后,焊缝金属由变形组织转变为铸造组织。
由于焊接熔池降温速度快,焊缝金属会因晶内偏析形成层状组织,偏析严重会在枝晶间形成共晶组织。
焊接接头热影响区产生沿晶界的局部熔化和晶粒长大,如固溶强化高温合金GH1015、GH1016和GH1140就具有比较好的焊接性,焊缝组织细小[24]。
相比而言,沉淀强化高温合金和铸造高温合金的组织就比较复杂,焊缝和热影响区的组织成分都比较复杂。
焊缝金属在焊接过程中经历了熔化凝固的过程,原来的γ′相、碳化物相等均溶入基体中,形成单一的γ固溶体。
焊缝金属冷却速度快,容易形成横向枝晶很短主轴很长的枝状晶。
在枝状晶和主轴之间会出现较大的成分偏析,从而在焊缝中出现共晶成分。
在热循环周期性很大的热影响区会引起强化相γ′溶解,碳化物相变,从而使热影响区的组织变的十分复杂,影响高温合金的性能[21]。
如GH4169母材晶粒细小,多为等轴晶,属于变形合金组织。
焊缝组织与母材完全不一样,树枝组织明显,枝晶轴垂直于焊缝。
这种焊接接头组织对拉伸性能影响不大,但是能明显降低持久和疲劳性能[25]。
(3)焊缝接头的等强性。
高温合金的服役环境一般要承受高温和应力的同时作用,因此要求高温合金焊接接头应具有良好的高温强度、塑性、低周疲劳性能以及良好的抗氧化耐腐蚀作用。
同时希望焊接接头的强度与母材一样,即焊接接头的等强性。
通常高温合金在焊接中遇到的主要问题,除了焊接中或焊后出现的裂纹和微裂纹,另一个就是力学性能的降低。
焊接一般会使抗拉强度和屈服强度明显降低,同时使塑性降低。
此外,焊缝熔体凝固会引起元素偏析,降低氧化和抗腐蚀能力,使性能恶化。
所以采用合理的焊接工艺和优良的焊材对提高高温焊缝接头强度至关重要。
如采用摩擦焊焊接高温合金,焊接接头强度系数几乎为100%[26]。
若采用异质焊丝,接头强度降低更大。
焊接接头强度系数是由于焊缝组织的不均匀性造成的,热影响区晶粒组织长大,强化相γ′相的溶解,容易形成弱化区,所以在弱化区会首先出现塑性变形,最终导致断裂失效。
因此高温合金焊接接头的强度和塑性均有明显的降低。
所以应从焊接工艺、焊接材料、焊接方法和热处理等方面着手,优化工艺参数,保证焊接接头系数Kσ接近100%[27]。
高温合金焊接的热裂纹敏感性、接头组织的不均匀性以及焊接接头的等强性都是决定高温合金焊接性的关键因素。
此外,选择合理的焊接工艺也是评价高温合金焊接性的重要依据。
因此,在高温合金使用前,必须分析和研究高温合金的焊接性。
只有掌握了高温合金的焊接性及其影响因素,才能顺利的完成高温合金焊接构件的生产,才能保证高温合金焊接构件的安全使用。
1.2.2高温合金的焊接工艺
由于高温合金构件的制造和焊接密不可分,高温合金的焊接性和焊接工艺的研究随着高温合金的发展而同步发展。
高温合金构件经常采用的焊接方法有氩弧焊、电子束焊、钎焊和摩擦焊等,近年来瞬态液相扩散焊也逐渐发展应用[28-35]。
这些焊接方法均已成功应用于先进的航空发动机上。
(1)氩弧焊焊接高温合金已较为成熟,应用也极为广泛。
如燃烧室火箭筒,加力燃烧室可调喷管、后安装边,涡轮叶片耐磨层等[36]。
钨极氩弧焊由于惰性气体充分保护,焊缝质量好,表面无熔渣,热量较集中,热影响小;设备投资少,操作简单,成本低,易实现自动焊接[37-38]。
早在1970年,中国科学院金属研究所郭建亭等人曾对GH2135合金板制作火箭筒采用氩弧焊焊接工艺的连接和成型问题做了研究[18]。
报告指出,虽然沉淀强化GH2135合金板材较固溶强化板材的焊接抗裂性能要差,但是采用自动氩弧焊和用GH3039作填充材料的手工氩弧焊均无裂纹和延展裂纹产生,焊接结果比较满意。
且GH2135火箭筒的试制和长期试车情况良好,说明氩弧焊焊接工艺可以满足生产需要。
(2)电子束焊是利用加速和聚焦的电子束轰击置于真空或非真空中的焊件所产生的热能进行焊接的方法,属于熔焊中高能密束焊的一种[39-40]。
电子束焊在焊接厚板时可不开破口,不填充焊丝,单面一次成型;焊接速度快,对材料的热输入较少,热影响区小,焊后几乎不变形;焊接过程中可精确的控制焊接参数,重现性好;可成功的焊接固溶强化型高温合金,同时对氩弧焊难以焊接的沉淀强化型高温合金也可以采用电子束焊焊接。
在先进航空发动机的零组件连接成型工艺中,电子束焊已经在实际生产中成功应用。
如高压涡轮机匣和高压承力环,材料为GH2907和GH4169,火箭筒内环和外壁组合件,材料为GH4141和GH3536;火箭筒外壁材料为GH5188和GH5605;头部转接段为GH5188,外机匣前段和后段为GH4169,内套组件为GH4141等等,这些零组件均采用真空电子束焊接[18],而且焊接接头性能良好。
(3)钎焊是采用比母材熔点低的金属材料作为钎料,将母材与钎料加热到高于钎料熔点,而低于母材熔点的温度,利用液态钎料润湿母材,填充接头间隙,并与母材相互扩散而实现连接焊件的方法[41],属于固相/液相焊接。
与熔焊相比,钎料熔化,而母材不熔化。
优点是可以防止母材组织和性能因受焊接热输入峰值的影响发生变化,焊接时焊件整体加热或钎缝周围大面积均匀加热,焊件的相对变形量及焊接接头残余应力小;可以多条钎缝或大批量的焊件同时或连续进行焊接,焊接效率较氩弧焊和真空电子束焊高。
由于钎焊只在母材数微米至数十微米以下界面反应,通常不影响母材深层的结构,特别适用于异种金属的连接[21]。
钎焊的缺点在于,高温合金中由于含有较多的Al、Ti等活性元素,在焊接时易在合金表面形成稳定的氧化膜,从而影响钎料的润湿和填缝能力。
因此,为了防止液态钎料高温氧化,高温合金通常采用真空钎焊或保护气体钎焊。
并且高温合金钎焊温度一般要求和固溶处理温度一致,如果钎焊温度过高,会造成晶粒长大,钎焊温度过低,达不到固溶处理效果,都会影响钎焊接头性能[42]。
由于高温合金焊件的使用温度处于高温条件下,有时会承受较大的应力,为了满足这种使用条件,往往会在钎焊后进行扩散处理,以此来提高焊缝组织的稳定性和重熔温度、增强接头强度。
钎焊在航空发动机和燃气轮机的应用很广泛,如压气机静子叶片组件,涡轮导向叶片组件,涡轮叶片堵头以及导管组件等。
(4)瞬态液相扩散焊
瞬态液相扩散焊(TLP)是在待焊接件之间放置熔点较低的薄层中间层合金,然后,对连接平面施加法相载荷或不施加载荷,用夹具或点焊定位,在真空条件下加热至中间层合金熔化,,润湿母材,并在焊接面形成均匀的液态薄膜,经过一度保温时间,中间层中降低熔点元素B等向母材扩散,使连接界面处母材熔点降低并发生少量溶解。
由于中间层降低熔点元素B等元素的减少,中间层组织熔点随之提高,中间层液相组织逐渐凝固;延长保温时间,等温凝固继续进行,固/液界面不断向焊缝中心推进,多余的溶质元素在界面前沿富集,当富集达到一定程度时,便形成化合物相。
等温凝固结束后继续延长保温时间,焊缝中心溶质元素扩散更加充分,合金元素趋于平衡,焊缝熔点升高达到扩散焊加热温度而进一步扩散,最终形成牢固的连接,实现了TLP焊接[42]。
TLP焊接综合了高温钎焊和固态扩散焊的特点,它既可以得到高强度的接头,在连接处基本看不出焊缝的痕迹,综合了高温钎焊和固态扩散焊的优点。
对于对开单晶叶片,连接后连接层与基体取向匹配良好,实现了整个叶片单晶化要求。
TLP适合焊接焊接性较差的铸造高温合金,包括定向凝固和单晶高温合金,也包括铸造Ni-Al系金属间化合物,如单晶和定向凝固的涡轮叶片、涡轮导向叶片等。
美国P&W公司为PWA1480单晶合金配制的中间层合金是与PWA1480单晶成分接近但加入了一定量B元素的韧性箔带,为TLPR-613。
采用该中间层合金连接PWA1480合金,接头在982℃的持久强度和等温低周疲劳性能与PWA1480合金相当[43]。
焊接的叶片已试用于F100发动机及其他新型发动机。
Ni3Al和NiAl金属间化合物的连接主要采用瞬态液相扩散焊。
Ni3Al合金IC6采用17P作为中间层合金。
采用17P中间层合金焊接IC6合金接头的持久性能已达到母材横向性能水平[44]。
(5)摩擦焊
摩擦焊是利用焊件接触面相对运动中相互摩擦所产生的热,使端部达到热塑性状态,然后迅速顶锻,完成焊接的一种方法。
摩擦焊有许多地方与闪光焊和电阻焊相似,如焊接接头多为圆形截面对接,焊接循环时间也大致相似,先接合面加热再顶锻。
其最大的不同在于,闪光焊和电阻焊利用电阻热源,而摩擦焊则是利用摩擦生热[21]。
与闪光焊、电阻焊相比较而言,摩擦焊有以下优点:
接合表面的清洁度,因为摩擦焊过程中能破坏和清除表面层;受热更集中于接合面处,因为全部能量的转换仅发生在接合面,所以焊接接头热影响区很窄;局部受热与不发生熔化使得其比其他焊接方法更适合于异种金属的连接;大多数情况,接头强度与母材一样高,并且接头性能稳定等等。
摩擦焊是一种广泛应用的高效、可靠、节能及环保的固态焊接方法。
我国目前生产的先进航空发动机的压气机鼓筒组件就是采用惯性摩擦焊将5个DAGH4169压气机盘焊在一起的。
1.3本文研究内容及主要工作
焊接结构中存在的缺陷在较大的外界负载作用下,高温合金焊接接头将可能失稳扩展