第一篇 海上油气田生产系统了解篇讲诉.docx
《第一篇 海上油气田生产系统了解篇讲诉.docx》由会员分享,可在线阅读,更多相关《第一篇 海上油气田生产系统了解篇讲诉.docx(23页珍藏版)》请在冰豆网上搜索。
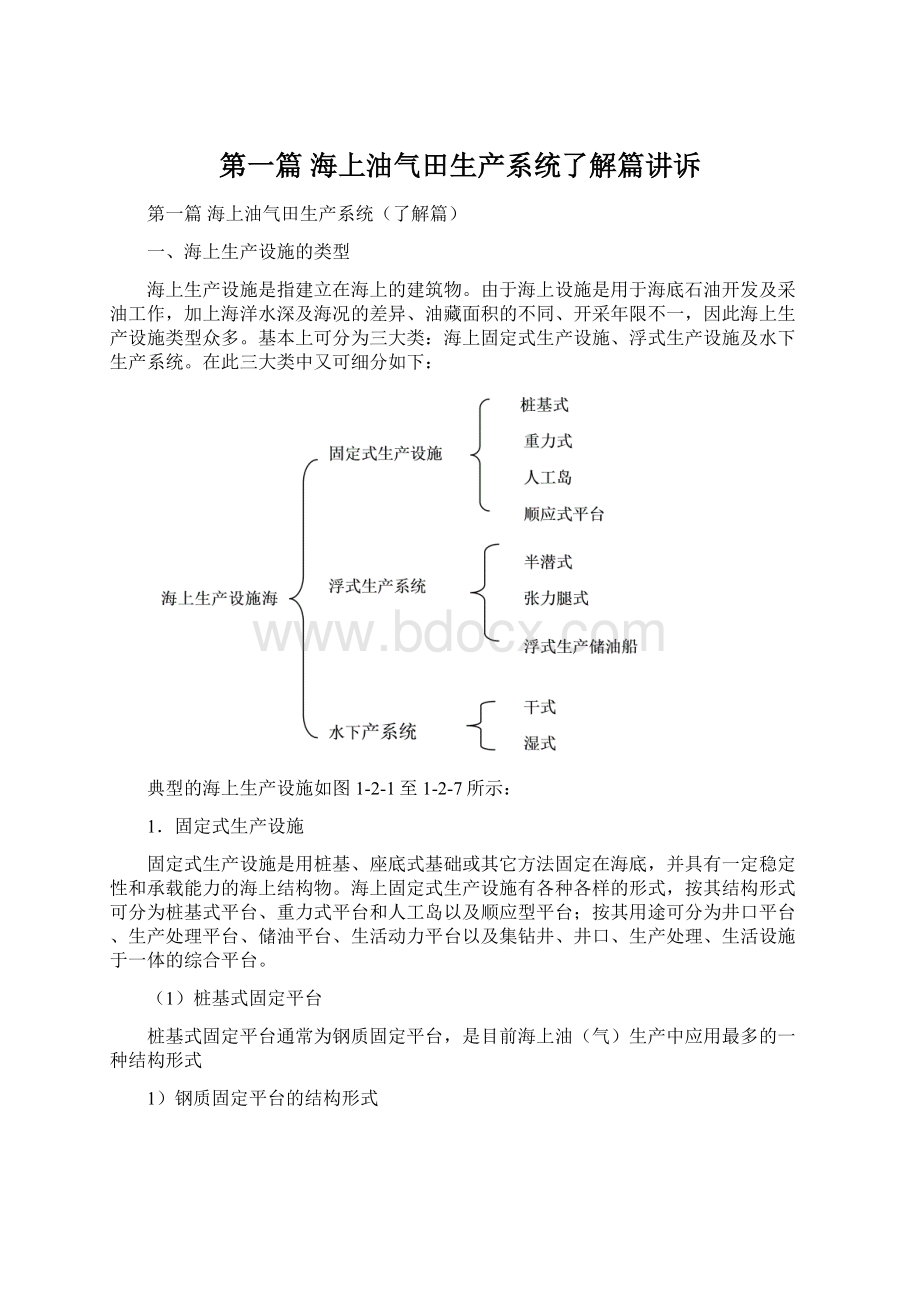
第一篇海上油气田生产系统了解篇讲诉
第一篇海上油气田生产系统(了解篇)
一、海上生产设施的类型
海上生产设施是指建立在海上的建筑物。
由于海上设施是用于海底石油开发及采油工作,加上海洋水深及海况的差异、油藏面积的不同、开采年限不一,因此海上生产设施类型众多。
基本上可分为三大类:
海上固定式生产设施、浮式生产设施及水下生产系统。
在此三大类中又可细分如下:
典型的海上生产设施如图1-2-1至1-2-7所示:
1.固定式生产设施
固定式生产设施是用桩基、座底式基础或其它方法固定在海底,并具有一定稳定性和承载能力的海上结构物。
海上固定式生产设施有各种各样的形式,按其结构形式可分为桩基式平台、重力式平台和人工岛以及顺应型平台;按其用途可分为井口平台、生产处理平台、储油平台、生活动力平台以及集钻井、井口、生产处理、生活设施于一体的综合平台。
(1)桩基式固定平台
桩基式固定平台通常为钢质固定平台,是目前海上油(气)生产中应用最多的一种结构形式
1)钢质固定平台的结构形式
钢质固定平台中最多的是导管架式平台,主要由四大部分组成:
导管架、桩、导管架帽和甲板模块。
但在许多情况下,导管架帽和甲板模块合二为一,所以这时仅为三部分。
如图1-2-8所示。
导管架:
系钢质桁架结构,由大直径、厚壁的低合金钢管焊接而成。
钢桁架的主柱(也称大腿)作为打桩时的导向管,故称导管架。
其主管可以是三根的塔式导管架,也有四柱式、六柱式、八柱式等,视平台上部模块尺寸大小和水深而定。
导管架腿之间由水平横撑与斜撑、立向斜撑作为拉筋,以起传递负荷及加强导管架强度作用。
桩:
导管架依靠桩固定于海底,它有主桩式,即所有的桩均由主腿内打入;也有裙桩式,即在导管架底部四周布置桩,裙桩一般是水下桩。
导管架帽:
导管架帽是指导管架以上,模块以下带有甲板的这部分结构。
它是导管架与模块之间的过渡结构。
模块:
也称组块。
由各种组块组成平台甲板。
平台可以是一个多层甲板组成的结构,也可以是单层甲板组成的结构,视平台规模大小而定。
如钻井区域的模块可称为钻井模块;采油生产处理区称为生产模块;机械动力区可称为动力模块;生活区称为生活模块等。
2)钢质固定平台的施工
钢质固定平台的施工是一个复杂的过程,分为陆上预制和海上安装两种作业。
陆上预制是在专门的场地上进行。
导管架、上部模块和导管架帽分别在陆上预制好。
海上安装包括海上运输和海上安装两部分。
导管架和组块用驳船或其它方法运到油田现场,先将导管架沉放到预定位置,然后沿各导管向海底打桩,再将导管架帽安装在导管架上,最后用起重船将上部模块吊装到导管架帽上,这时平台即告建成。
3)海上钢质固定平台用途分类
由于油气处理设施的设置不同,用途各异,钢质固定平台的类型也不同。
一般情况下,钢制固定平台按其用途可分为:
井口平台、生产处理平台、储罐平台等。
①井口平台:
常规井口平台上安装有一定数量的采油树,井液经采油树采出后,通过单井计量系统计量,用海底管线输送到中心处理平台或其它生产处理设施上进行处理。
图1-2-6自升式生产平台
图1-2-7水下生产系统
井口平台上还设有必要的工艺设备及支持系统和公用系统。
一般情况下,其动力和控制由中心平台提供。
某些井口平台由于生产操作的需要还设有生活楼。
生活楼包括住房、办公室、通信室、娱乐室、厨房等。
对于井数较多,且油井为机采井的井口平台,平台上还设有修井机及其配套设施,以满足油井维修的特殊要求。
有些井口平台井数较少,产量规模不大,从减少投资的角度出发,可设置成无人井口平台或简易井口平台。
典型的井口平台见图
图1-2-7水下生产系统
1-2-9
②生产处理平台:
生产平台亦称中心平台,它集原油生产处理系统、工艺辅助系统、公用系统、动力系统及生活楼于一体。
图1-2-10典型的中心平台
图1-2-10典型的中心平台
图1-2-9典型的井口平台
生产平台具有将各井口平台的来液进行加工处理的能力,也要有向各井口平台提供动力以及监控井口平台生产操作的功能。
生产平台按用途可分为:
常规生产平台;生产、生活、动力平台;钻井、生产、生活、动力平台以及生活、动力平台等。
生产平台汇集了各井口平台的来液后,经三相分离器将来液的油、气、水进行分离。
原油在原油处理系统中经脱水达到成品油要求后输送到储油平台或其它储油设施中储存;三相分离器分离出的天然气经气液分离、压缩等一系列处理后供发电机、气举和加热炉等用户使用,多余的天然气进火炬系统烧掉;分离器分离出的含油污水进入含油污水处理系统进行处理,合格的含油污水排海或回注地层。
典型的生产平台见图1-2-10
③储罐平台:
储罐平台是将原油储罐设置在平台上,中心平台处理合格的原油在储罐平台储存。
储罐平台的大小要根据油田规模和穿梭油轮的大小来综合考虑。
储罐平台由于投资较高,储油能力有限,已不常用。
为了外输原油,有时设置海上码头。
典型的储罐平台和海上码头见图1-2-11:
图1-2-11典型的储罐平台和海上码头
4)海上钢质固定平台的优缺点
钢质固定平台的优点是:
①技术成熟、可靠;②在浅海和中深海区使用较为经济;③海上作业平稳和安全。
钢质固定平台的缺点是:
①随着水深的增加费用显著增加;②海上安装工作量大;③制造和安装周期长;④当油田预测产量发生变化时,对油田开发方案进行调整的适应性受到限制。
(2)重力式平台
重力式平台是与桩基平台不同的另一种形式的平台。
它不需要用插入海底的桩去承担垂直荷载和水平荷载,完全依靠本身的重量直接稳定在海底。
根据建造材料的不同,又分为混凝土重力式平台和钢重力式平台两大类。
1)混凝土重力式平台
把混凝土重力式结构物用于岸边和浅水地带已有悠久历史,而用于外海却在70年代以后。
目前,混凝土平台可以适应从浅到深的各种水深。
混凝土重力式平台的结构见图1-2-2。
①组成部分:
混凝土平台由沉垫、甲板和立柱三部分组成。
已建成和正在研究、设计的混凝土平台种类繁多,有把底座做成六角形、正方形、圆形,也有把立柱做成三腿、四腿、独腿的等各种形式。
(a)底座:
底座是整个建筑物的基础。
为了抵抗巨大的风浪推力,要求平台有很大的底座结构,而较大的底座又正好可以用来储存原油,这就使得混凝土平台具备了把钻、采、储三者兼顾起来的优点。
(b)甲板:
甲板为生产提供工作场所,在甲板上可安装各种生产处理设施和生活设施。
(c)立柱:
立柱连接在沉垫和甲板之间,用于支撑甲板。
②建造过程:
混凝土平台的建造相当复杂,采用类似桩基平台的常规建造办法是行不通的。
图1-2-12是这种平台建造的简要过程。
第一步:
在干坞内建造底座的下半部分,如图1-2-12(a)。
因为底座底面积大,重量也大,所以不能在一般的船坞或滑道上建造,只能在地基较好的岸边挖出一块施工预制场地,并用围堰把施工场地和海水隔开,这块预制场地就叫干坞。
第二步:
在干坞内建造至预定高度后,注入海水和海平面一致(向底座内注压载水使其固定),打开船坞闸,排除压载水,使底座上浮,用拖船把底座从干坞内拖出,如图1-2-12(b)。
第三步:
把底座拖至岸边比较深的、隐蔽较好的施工水域,在海面上锚泊,采用滑动施工法建造底座上部,如图1-2-12(c)。
第四步:
用滑动施工法继续浇注立柱,如图1-2-12(d)。
第五步:
用拖轮把结构物拖至深水海域,以便安装甲板,见图1-2-12(e).
第六步:
向底座注入压载水,使结构物下沉到海水没至立柱上部左右,再安装甲板,1-2-12(f).
第七步:
在甲板上安装各种模块,见图1-2-12(g)。
第八步:
排出压载水,使结构物上浮,用拖轮拖至预定地点,见图1-2-12(h)。
第九步:
平台位置确定后,注入压载水,边下沉边调节,使之准确安装在海底,见图1-2-12(m).
③重力式平台的优缺点:
(a)优点:
●节省钢材。
如两座挪威人建造的康迪普平台,耗钢量分别为1.2万t及1.5万t,而同样条件的桩基钢平台耗钢达2.0-4.0万t.
●经济效果好。
采用廉价的混凝土材料。
在北海,用混凝土重力式平台比钢导管架平台更为经济。
估计总成本可节省20%。
而且,混凝土重力式平台的底座(沉箱)可以储油,因而经济效益十分显著。
●海上现场安装的工作量小。
这主要是因为全部结构在干坞和岸边隐藏的深水施工水域中已经建造完毕,因而避开了海况恶劣的深水现场安装工作。
●海上安装工艺比钢结构简单些。
不需要在海底打桩。
●甲板负荷大,在立柱中钻井安全可靠。
●防海水腐蚀、防火、防爆性能都好。
●维修工作量小,费用低,使用寿命长。
(b)缺点:
●对地基的要求高。
混凝土平台对地基的要求较高,这是区别于桩基平台的显著特点之一。
一座混凝土平台能否正常工作,除取决于它本身的结构强度外,另一个重要的因素就是看它能否稳坐在海底,由于受巨大风浪力和地震力等的影响,混凝土重力平台对地基的要求远比桩基平台高。
因而,基础设计的好坏,常成为重力式平台成败的关键。
●结构分析比较复杂。
●制造工艺复杂。
●岸边需有较深的、隐蔽条件较好的施工场地和水域。
●拖航时阻力大。
●冰区工作性能差。
2)钢质重力式平台
除混凝土重力式平台外,钢质重力式平台也是重力式平台的一个重要分支。
如图1-2-13所示,整个平台由沉箱、支承框架和甲板三部分组成,沉箱兼作储罐。
建造时,先把各个沉箱、支承框架、甲板分别预制,而后在岸边组装成整体,再拖运到井位下沉安放。
和混凝土平台相比,钢质重力式平台的储油量虽小,但在对储量要求不大的情况下,钢质重力式平台反而有较高的经济效益。
又由于它比混凝土平台轻得多,所以预制过程中不需要较深的施工水域,拖航时要求的拖航马力小,使用中对地基承载力的要求也不高。
钢质重力式平台避免了混凝土平台许多缺点,但在省钢材、耐腐蚀、储油量、隔热等方面,都不如混凝土平台,这又是它的缺点。
3)人工岛
人工岛是在海上建造的人工陆域,人们在人工岛上可以设置钻机、油气处理设备、公用设施、储罐以及卸油码头。
人工岛按岸壁形式可分为护坡式人工岛和沉箱式人工岛。
护坡人工岛如图1-2-14,由砾石筑成,砂袋或砌石护坡。
先由底部开口的驳船向岛的四周抛填砾石,接着码放砂袋,稍高出水面形成水下围堤,然后填充岛体。
沉箱式人工岛又可分为钢沉箱围闭式人工岛,钢筋混凝土沉箱围闭式人工岛和移动式极地沉箱人工岛。
沉箱式人工岛的特点是由一个整体沉箱或多个钢或钢筋混凝土沉箱围成,中间回填砂土。
沉箱可在陆上预制,然后自浮拖至现场安装就位,通过调节水下砂基床的高度以使沉箱适用于不同的水深,人工岛不再使用时,可排除压载,起浮后拖到其它地点再用。
目前钢沉箱围闭式人工岛能成功地用于26m水深。
如图1-2-3所示。
4)顺应型平台
所谓顺应型平台是指在海洋环境载荷作用下,围绕支点可发生允许范围内某一角度摆动的深水采油平台。
这种平台是一种细长的框架结构,沿高度方向的横截面一般不变。
框架每隔一定的高度有重复的结构形式,井槽在平台的中部。
有的顺应型平台在每个角各有数根桩支持,桩穿过导管打下后,桩顶部约高出泥线某一高度,套管约上至平台高度的一半,桩与导管之间灌注水泥浆,凝固后便组成一套管与桩的组合体,在这个组合体的顶部附接导管架。
这样大的长度提供了足够的轴向弹性来产生柔性复原力,调整组合体的长度可得到系统适应不同环境的结构参数。
有的顺应型平台或/和借助牵索(如绷绳塔平台)用一些浮筒(如浮塔式平台)来产生复原力,浮筒也可给平台提供向上的浮力,从而可减少结构的轴向压力。
见图1-2-15。
顺应型平台的特点如下:
①自振周期大,刚性小,故随着波浪的作用而运动。
而由组合体(由桩和套管组成)和导管架形成的阻尼器却使其运动幅度大大减小,具有很好的抗疲劳特性。
②可用铰接接头或大型浮筒和阻尼器,不需要因限制甲板运动而安装特别装置。
③建造简单。
一般工程与建造时间少于2年。
④重复结构和定型构件很多;
⑤横截面积小,重量轻,起重安装容易;
⑥可按常规方法运输、下水和直立作业。
⑦由于重量轻,结构简单和安装方便,与常规钢导管架相比费用低。
2.浮式生产系统
典型的浮式生产系统是指利用改装(或专建的)半潜式钻井平台、张力腿平台、自升式平台或油轮放置采油设备、生产和处理设备以及储油设施的生产系统。
浮式生产系统最大的特点就是可实现油田的全海式开发。
由于其可重复使用,因此被广泛用于早期生产、延长测试和边际油田的开发过程中。
目前,随着科技的发展,许多大型油田也都采用浮式生产系统。
我国大部分海上油田都采用浮式生产系统。
浮式生产系统分为:
①以油轮为主体的浮式生产系统;②以半潜式钻井船为主体的浮式生产系统;③以自升式钻井船为主体的浮式生产系统;④以张力腿平台为主体的浮式生产系统。
(1)以油轮为主体的浮式生产系统
以油轮为主体的浮式生产系统分为浮式生产储油装置(FPSO)和浮式储油装置(FSO)两种。
FPSO是把生产分离设备、注水(气)设备、公用设备以及生活设施等安装在一艘具有储油和卸油功能的油轮上。
油气通过海底管线输到单点后,经单点上的油气通道通过软管输到油轮(FPSO)上,FPSO上的油气处理设施将油、气、水进行分离处理。
分离出的合格原油储存在FPSO上的油舱内,计量标定后用经穿梭油轮运走。
FSO也是具有储油和卸油功能的油轮,但它没有生产分离设备以及公用设备,通过海管汇集来的合格原油直接储存到FSO的油舱中,由于没有油气生产设备,可直接将旧油轮稍加改装就可以成为FSO,相对于FPSO来说,FSO建造工期短。
FPSO的形式见图1-2-4。
浮式生产储油装置采用新建和旧油轮改造两种方式。
采用哪种方式取决于油田寿命和开发方式。
在油田寿命较长的情况下,新建油轮优于旧油轮改造。
这是因为新建油轮具有较长的使用期限,而改建油轮花费的结构改建费和维修费大大超过了已有船体的经济受益。
然而,对于油田早期开发来说,由于改建油轮费时少,改建油轮更为合适。
浮式生产储油装置具有以下优点:
①初始投资低。
因可以低价购置当前过剩油轮,可大大降低投资成本。
②海上安装周期短。
不必动用大型浮吊。
由于油轮可在船厂建造,因而可降低海上安装费和减少海上安装周期。
③储油能力大。
FPSO上船舱的储油能力可根据油田产能和穿梭油轮来船周期进行设计,因此不必建造储罐平台或输送到陆上储存。
另外由于卸油和卖油可直接在海上进行,因此对穿梭油轮吨位选择的范围较大。
④甲板面积大。
有利于油气处理设备的安装,油气水能很好地分离和处理。
⑤可重复使用。
浮式生产储油装置的缺点是:
①受海况的影响较大。
恶劣的海况条件如台风、冰等对FPSO影响较大,因此在设计时要考虑FPSO对单点的解脱,以避开恶劣的海况。
FPSO解脱后,油田要停产,因此要考虑停产的损失,以及恢复生产的困难。
另外穿梭油轮与FPSO的连接受海况的影响也比较大,因此靠船的方式要专门进行研究。
②稳定性差。
由于FPSO漂浮在海上进行生产,受海浪、气候以及卸油的影响,船体的稳定性较固定平台差。
因此甲板上的油气生产设备要考虑防止船体的摇摆。
③设备的布置要考虑周密。
住房应靠近船艏部,以利于船员的安全。
火炬的位置应布置的远离住房和直升机甲板。
生产设施尽可能布置在船的重心附近,以减少船的摆动影响。
(2)以半潜式钻井船为主体的浮式生产系统
该种生产系统的主要特点是把采油设备(采油树等)、注水(气)设备和油气水处理等设备,安装在一艘经改装(或专建的)半潜式钻井船上。
见图1-2-16。
油气从海底井经采油立管(刚性或柔性管)上至半潜式钻井船(常用锚链系泊)的处理设施,分离处理合格后的原油经海底输油管线和单点系泊系统,再经穿梭油轮运走。
这种生产系统的优点是:
①稳定性好,可适用于恶劣的海况条件;
②具有一定的储油能力;
③可利用船上的钻机进行打井、完井和修井作业。
缺点是:
①要另建系泊系统以便穿梭油轮卸油作业;
②改装时间长,成本高;
③如果储油能力不足,油田可能停产。
(3)以自升式钻井船为主体的浮式生产系统
该种生产系统是利用自升式钻井船改装的(图1-2-17)。
其上可放置生产与处理设备,主要用于浅水海域,可以移动。
自海底油井出来的油气上至自升式平台分离处理后,再经海底管线和系泊系统输至油轮运走。
这种系统常用于油田延长测试及边际油田的开发。
(4)以张力腿平台为主体的浮式生产系统
张力腿平台可以看做一个垂直锚系的半潜式平台(图1-2-18)。
虽然张力腿平台不储油,不装油,但这种平台是开发深水油田的一个具有很大竞争力的形式。
这种结构的外形减小了垂向波浪力的影响,因而也就减小了系泊系统的受力变化,上部结构设计成足以承受油田开发各个阶段的载重量,不论在拖航条件,还是在垂直系泊时都能保持稳定。
这种形式的主要优点是:
升沉、纵摇和横摇运动在很大程度上被控制,这就大大地简化了立管与浮动设备之间的输送系统。
3.水下生产系统
随着海洋石油工以及人们对降低成本的不断追求,海洋石油技术从海面发展到了水下,并从单井水下采油树发展到多井水下采油树,直至最近致力于研究的全部油气集输系统都放到水下的种种方案。
典型的水下生产系统由水下设备及水面控制设施组成。
水下设备包括:
水下采油树和水下管汇中心,水上控制系统放置在浮式生产系统上,对水下设备进行控制及维修作业。
水下设备和水上控制设施构成了一套完整的水下生产系统,见图1-2-7。
水下生产系统是将采油树放到海床上,水下采油树采出的井液通过水下管汇中心,水下管汇中心完成对各井井液的单井计量、汇集、增压后通过海底管线输送到浮式生产系统上进行处理和储运。
水上控制系统通过水下管汇中心对水下井口进行控制、关断、注水、注气、注化学药剂以及维护作业。
(1)水下生产系统的主要设备
1)水下采油树(见图1-2-19)
水下采油树分为干式、湿式、干/湿式和沉箱式四种形式。
①干式水下采油树:
干式水下采油树就是把采油树置于一个封闭的常压、常温舱里,通常称之为水下井口舱,维修人员可以像在陆地上一样在舱内进行工作。
水下井口舱通过上部的法兰与运送人员和设备的服务舱连接,然后打开法兰下面起密封作用的舱孔,通过这个舱孔操作人员和井口设备可以进入水下井口舱进行工作。
一般水下井口舱的容积可以容纳二、三个人舒适地工作。
通常水下井口舱内在无人状态下是充满氮气的,需要操作人员进入时,必须排出氮气并充入空气。
对于干式采油树这种操作形式,水下井口舱和服务舱应配有几套生命维护系统,包括供氧系统、连续监测系统、取样系统及独立的安全系统。
由于干式采油树对操作人员存在潜在的危险,而且结构复杂、设备仪器繁多,因此技术难度较大、成本高,逐渐为其它形式的采油树代替。
②干/湿式水下采油树:
干/湿式水下采油树的特点是可以干/湿转换,当正常生产时,采油树呈湿式状态,当进行维修时,由一个服务舱与水下采油树连接,排空海水,使其变成常温常压的干式采油树。
干/湿式采油树主要由低压外壳、水下生产设备、输油管连接器和干/湿式转换接头组成。
低压外壳是一个按照ASME规范设计的外压容器,其上部开孔,当要创造一个干式环境时,其配合环与干/湿式转换接头相接,形成封闭的容器;干/湿树转换接头的外型是一个锥型外壳,操作时,底部与低压外壳的配合环连接,顶部与潜水服务舱连接,以后的工作方式基本和干式采油树相同。
③沉箱式水下采油树:
沉箱式采油树也称插入式水下采油树,是把整个采油树包括主阀、连接器和水下井口全部置于海床以下9.1~15.2m深的导管内,在海床上的部分很矮,一般高于海床2.1~4.6m,而常规水下采油树高于海床10.7m左右,这样采油树受外界冲击造成损坏的机会就大大减少。
沉箱式水下采油树分为上下两部分,上部主要包括采油树下入系统、控制系统、永久导向基础、出油管线及阀门、采油树帽、输油管线连接器和采油树保护罩等。
下部采油树包括主阀、连接器和水下井口等。
但是沉箱式水下采油树的最大缺点是价格高于一般的湿式采油树40%左右,并且不能显示出比常规湿式水下采油树更突出的特点及广泛的适用性,使其应用受到一定的限制。
④湿式水下采油树:
我们现在最常用的水下采油树形式则是湿式采油树,即采油树完全暴露在海水中。
因为金属材料防海水腐蚀的性能、遥控装置的发展以及水下作业的水平越来越先进,而这种形式又是几种不同类型的采油树中相对简单的,因此就逐渐为石油公司所选用,在本文中我们也就主要介绍这种形式的水下采油树。
所有的湿式水下采油树的结构、基本部件及其功能都是相同的,这些部件主要有采油树体、水下井口、采油树与井口连接器、采油树与海底管线连接器、采油树阀件、永久导向基础、采油树内外帽、控制系统等。
20世纪60~80年代期间,水下采油树主要采用立式结构(区别于后来的卧式结构),该名称缘于采油树油管空间的三个主要阀门(生产主阀、生产翼阀及井下安全阀)安置在一条垂直的线上。
而20世纪90年代的最新技术是采用卧式采油树,其树体为整体加工的圆筒,生产主阀和生产翼阀均在树体外面,成水平排列,因而称为卧式。
打开树帽,可以将油管及电潜泵直接提出油井,可以不挪动采油树,大量节省了时间,使修井变得简单易行。
在使用立式采油树的水下生产系统中,如果修井就必须将水下采油树移开,露出井口才可以进行修井,操作比较困难且需较长时间的停产。
两相比较,新的卧式采油树得到了广泛的应用。
2)水下管汇中心(UMC)
水下管汇中心(见图1-2-20)也是水下生产系统的一种主要设备,其功能与一座固定平台相似,可在恶劣海区和深海区安全可靠地进行油气田开发,也可与浮式生产系统配合开发边际油田,及对远离中心平台的卫星油田进行开发。
水下管汇中心主要具有以下功能:
可通过底盘钻海底丛式井和连接卫星井;汇集和控制底盘井和卫星井产出的井液,通过海底管线输往附近的平台进行油气处理;将来自附近平台经过处理的海水注入注水井中,保持地层压力;输送来自水面的气体至各井口,实现气举;从上部设施通过UMC向各井泵送TFL(ThroughFlowLine)工具;向各井注入化学药剂;通过管汇对单井的产液特性进行测试和计量;实现从平台进行的遥控操作等。
水下管汇中心主要由以下部分组成:
①底盘:
底盘一般主要由大管径制成的结构框架组成,一方面为UMC下入海底提供浮力,另一方面也是钻井导向和设备支撑基座及其保护架。
②管汇系统和保护盖:
从底盘井和卫星井产出的井液,在管汇聚集后通过海底管线输往平台,平台上经过处理的海水经管汇分配至各注水井,除此之外,管汇系统还具备油水井测试、压井、化学药剂注入、修井时的通道及管线清洗等功能。
管汇根据油田不同的生产要求配置一定数量的管线,分别负责井液的测试和计量、注水分配、化学药剂注入及修井等。
控制各系统通往各单井的阀门组沿相应的管线布置。
③电液控制与分配系统:
控制系统设备是永久性地安装在水下管汇中心的结构上的,易损坏的控制系统电液元件安装于可取式控制模块中,该控制模块可以是一个阀门组,控制模块的安装位置使ROV(水下机器人)可以很方便的进行维修和操作。
由于电液分配系统的不可替换和不易维修,一般都会留出较大的余量。
④液压储能装置:
液压储能装置与供液设备和回路管线相连接,以提供液压储能防止回压的过分波动,且当平台上的液压泵出现问题时,储能器至少在24小时(或一定时间内)可维持足够的液体压力使管汇正常工作。
⑤化学药剂注入装置。
⑥ROV轨道:
为便于维修,可以用ROV拆卸水下管汇中心和控制系统的所用组件,因此在各阀门组和控制系统模块旁设置了ROV作业轨道(沿轨道两边布置),轨道置于水下管汇中心的中部,ROV将从作业船释放下来并沿此轨道到达工作位置。
⑦连接卫星井输油管线和控制管线用的“侧缘”:
卫星井到管汇中心的输油管线和控制管线用的连接设备,沿着底盘结构的每一侧分布。
在入口