原油储罐的腐蚀机理及防腐措施最新版.docx
《原油储罐的腐蚀机理及防腐措施最新版.docx》由会员分享,可在线阅读,更多相关《原油储罐的腐蚀机理及防腐措施最新版.docx(12页珍藏版)》请在冰豆网上搜索。
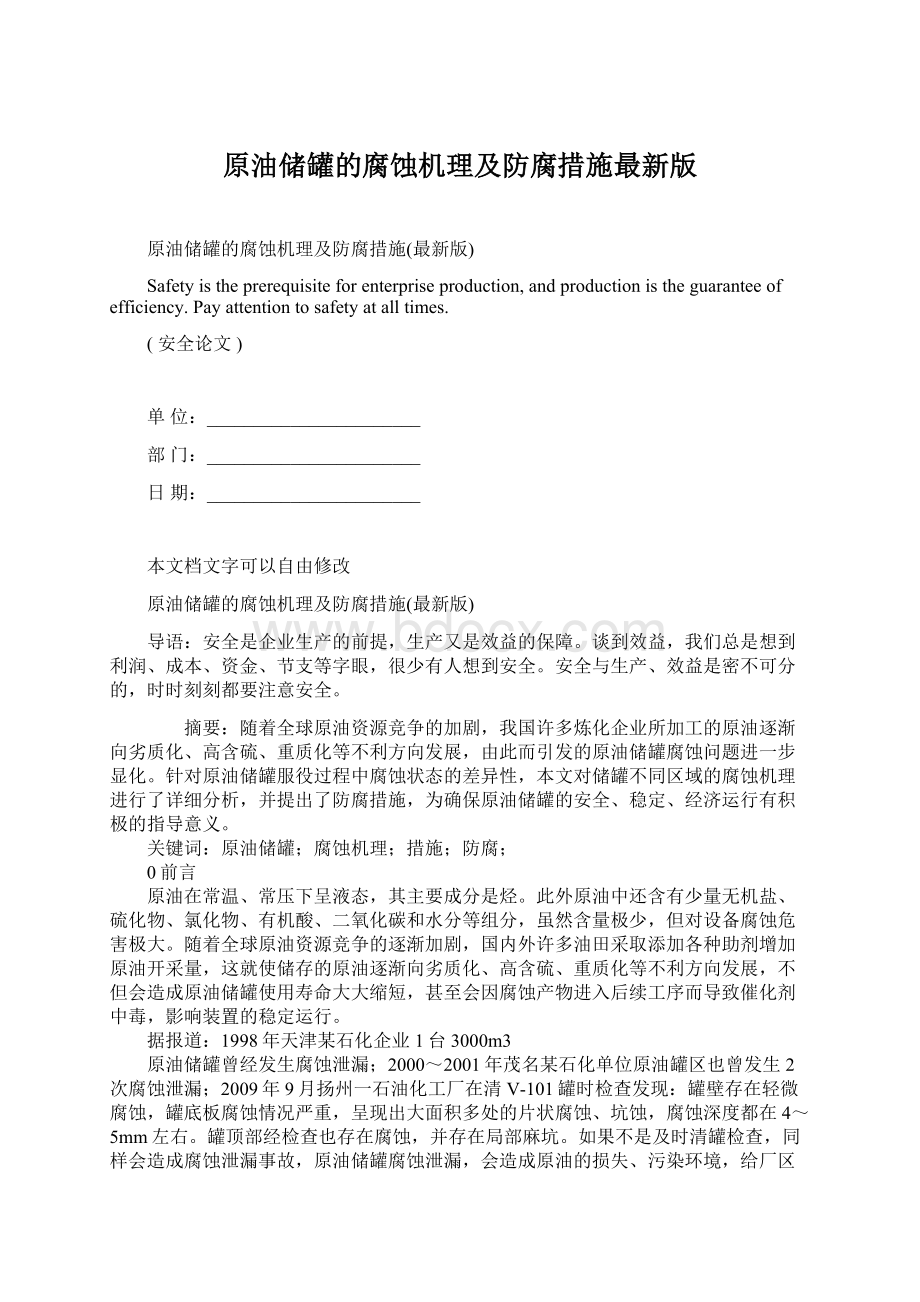
原油储罐的腐蚀机理及防腐措施最新版
原油储罐的腐蚀机理及防腐措施(最新版)
Safetyistheprerequisiteforenterpriseproduction,andproductionistheguaranteeofefficiency.Payattentiontosafetyatalltimes.
(安全论文)
单位:
_______________________
部门:
_______________________
日期:
_______________________
本文档文字可以自由修改
原油储罐的腐蚀机理及防腐措施(最新版)
导语:
安全是企业生产的前提,生产又是效益的保障。
谈到效益,我们总是想到利润、成本、资金、节支等字眼,很少有人想到安全。
安全与生产、效益是密不可分的,时时刻刻都要注意安全。
摘要:
随着全球原油资源竞争的加剧,我国许多炼化企业所加工的原油逐渐向劣质化、高含硫、重质化等不利方向发展,由此而引发的原油储罐腐蚀问题进一步显化。
针对原油储罐服役过程中腐蚀状态的差异性,本文对储罐不同区域的腐蚀机理进行了详细分析,并提出了防腐措施,为确保原油储罐的安全、稳定、经济运行有积极的指导意义。
关键词:
原油储罐;腐蚀机理;措施;防腐;
0前言
原油在常温、常压下呈液态,其主要成分是烃。
此外原油中还含有少量无机盐、硫化物、氯化物、有机酸、二氧化碳和水分等组分,虽然含量极少,但对设备腐蚀危害极大。
随着全球原油资源竞争的逐渐加剧,国内外许多油田采取添加各种助剂增加原油开采量,这就使储存的原油逐渐向劣质化、高含硫、重质化等不利方向发展,不但会造成原油储罐使用寿命大大缩短,甚至会因腐蚀产物进入后续工序而导致催化剂中毒,影响装置的稳定运行。
据报道:
1998年天津某石化企业1台3000m3
原油储罐曾经发生腐蚀泄漏;2000~2001年茂名某石化单位原油罐区也曾发生2次腐蚀泄漏;2009年9月扬州一石油化工厂在清V-101罐时检查发现:
罐壁存在轻微腐蚀,罐底板腐蚀情况严重,呈现出大面积多处的片状腐蚀、坑蚀,腐蚀深度都在4~5mm左右。
罐顶部经检查也存在腐蚀,并存在局部麻坑。
如果不是及时清罐检查,同样会造成腐蚀泄漏事故,原油储罐腐蚀泄漏,会造成原油的损失、污染环境,给厂区带来安全隐患,同时储罐穿孔被迫停用,直接和间接的经济损失都是惊人的,因此对原油储罐的腐蚀机理进行研究很有必要。
1.原油储罐的腐蚀机理
实践经验表明:
在干燥环境下原油罐外壁发生化学腐蚀,仅与储罐所处区域的环境条件有关,一般腐蚀较轻。
储罐顶部与底部由于所处的环境条件存在着很大差别,决定了腐蚀发生的机理也不尽相同。
1.1罐底板上表面:
原油中含有大量的水分,由于水和油的比重差之故,原油在储罐中经过静置,罐底上表面会形成水层。
沉积的水中含有大量的硫化物、氯化物、氧、酸类物质,形成较强的电解质溶液,产生了电化学腐蚀,腐蚀过程及类型如下:
1.1.1氯化物、硫化物对罐底的电化学腐蚀:
Fe2+
+S2-
→FeS↓(黑色铁锈)
Fe2+
+2Cl-
→FeCl2
Fe2
++SO4
2-
→FeSO4
1.1.2硫酸盐还原菌的腐蚀:
微生物对对油罐的腐蚀国内早已研究,其中以硫酸盐还原菌最具代表性,它的典型特征就是孔蚀。
他的腐蚀机理就是利用细菌生物膜内产生的氢,将硫酸盐还原成硫化氢:
8H+SO4
2-
→S2-
+4H2
O
罐底水溶液中的氢原子不断被硫酸盐还原菌代谢反应消耗,导致有防腐层的罐底部分脱落,从而使电化学反应不断进行下,增强了罐底钢板表面的离子化反应,加快了罐底的腐蚀速度。
国内外使用经验表明,钢制储罐若原油中不含H2
S,一般寿命为10~l5年。
含有H2
S时寿命在3~5年,腐蚀破坏首先在罐底发生穿孔,罐底平均腐蚀速度为0.5~1.5mm/a。
[1]
Fe2+
+S2-
→FeS↓
Fe→Fe2+
+2e-
1.1.3溶解氧电化学腐蚀:
原油中的活性硫成分如SO2
、S与O2
能够发生电化学腐蚀,加速铁的腐蚀产物的形成:
2SO2
+O2
+2H2
O=2H2
SO4
Fe+O2
→FeO,Fe3
O4
*nH2
O,Fe2
O3
等
1.2油罐储油部位:
该部位与原油直接接触,罐壁表面粘附一层相当于保护膜的原油,因此该部位腐蚀速率较低,短期内(20~30年)一般不会造成油罐壁腐蚀穿孔的危险。
但由于油品内和油面上部空间含氧量的不同,形成氧浓度差电池而造成腐蚀。
氧浓度差越大,腐蚀速率越大。
在正常情况下,氧浓度差不是太大,但在油罐倒灌、循环搅拌时,氧浓度差将会变大,加快罐壁的腐蚀。
1.3油罐气相部位:
油罐气相部位的腐蚀以化学腐蚀为主,该部位与原油介质不直接接触。
由于原油中挥发出的酸性气体硫化氢,外加通过呼吸阀进入罐内的水分、二氧化碳、二氧化硫等气体,在油罐液面上的罐壁处凝结成酸性溶液,导致化学腐蚀的发生。
1.3.1二氧化碳腐蚀:
二氧化碳溶于水形成弱酸(因原油加热游离水的挥发而形成),基本化学反应式如下:
CO2
+H2
0→H2
CO3
H2
CO3
+Fe→FeCO3
+H2
↑
阳极反应:
Fe→Fe2+
+2e-
阴极反应:
H2
CO3
→H+
+HCO3
-
2H+
+2e-→H2
↑
二氧化碳常常造成坑点腐蚀、片状腐蚀等局部腐蚀。
1.3.2硫腐蚀:
硫腐蚀以原油中的活性成分单质硫和硫化氢为主。
在无水的情况下,油品中的硫化氢对金属无腐蚀作用,湿硫化氢或与酸性介质共同存在时,腐蚀速度会成倍增加。
硫化氢在水中发生的电离式如下:
H2
S→H+
+HS-
HS-
→H+
+S2-
在湿硫化氢的腐蚀环境中的氢离子,硫氢根离子,硫离子和硫化氢对金属腐蚀为氢去极化作用,其反应式如下:
阳极反应:
Fe→Fe2+
+2e-
Fe2+
+S2-
→FeS或Fe2+
+HS-
→FeS+H+
+e-
阴极反应:
2H+
+2e-→H2
1.4储罐外壁:
储罐外壁主要发生大气腐蚀。
油罐所处的大气环境中含有氧、水蒸气、二氧化碳能导致罐体外壁腐蚀。
炼厂周围大气中一般还会含有氮化物、二氧化硫、硫化氢等有害气体,这也使罐体外壁腐蚀加快。
其腐蚀机理如下:
大气中的水汽溶解了有害气体及其他杂质,在罐壁形成电解质溶液,使罐壁发生了电化学腐蚀。
阳极反应:
Fe→Fe2+
+2e-
阴极反应:
O2
+2H2
O+4e-→4OH-
总反应:
2Fe+2H2
O+O2
→2Fe(OH)2
↓
氢氧化亚铁在大气环境转化为三氧化二铁或四氧化三铁,形成疏松的氧化层。
这种氧化层的表面氧和水发生阴极反应,而在锈层与罐比结合处发生则不断进行阳极反应,从而形成氧浓差电池,使腐蚀加剧,严重处导致穿孔。
1.5罐底下表面腐蚀:
罐底外表与土壤接触,其腐蚀速率约为0.8mm/a[2]
。
造成罐底下表面的腐蚀主要有土壤腐蚀、杂散电流腐蚀、氧浓差电池腐蚀、不同金属引起的电偶腐蚀[3]
1.5.1土壤腐蚀:
原油储罐的土壤腐蚀实际是电化学腐蚀,其阴极过程为还原反应:
有氧条件:
O2
+2H2
O+4e-→OH-
缺氧条件:
SO4
2-
+4H2
O→S2
-
+8OH-
阳极过程为氧化反应:
Fe→Fe2+
+2e-
Fe2+
+2OH-→Fe(OH)2
(绿色腐蚀产物)
2Fe(OH)2
H2
O+1/2O2→Fe(OH)3
Fe(OH)3
→FeOOH+H2
O(赤色腐蚀产物)
Fe(OH)3
→Fe2
O3
·H2
O(黑色腐蚀产物)
Fe2+
+CO3
2-
→FeCO3
Fe2+
+S2-
→FeS↓
1.5.2杂散电流腐蚀:
杂散电流是一种漏电现象[4]
。
罐区是大地中电流较为复杂的区域。
当站内管网有阴极保护而罐未受保护和电焊机装置绝缘不好时,则可能产生杂散电流引起宏观电池的腐蚀。
位于电气化铁路、大型电气设备附近的原油罐,其底板会因杂散电流的影响而腐蚀。
1.5.3氧浓差电池腐蚀:
在罐底板下面,氧浓差主要表现在罐底板与砂基础接触不良,如满载和空载比较,空载时接触不良;再有罐周和罐中心部位的透气性差别,也会引起氧浓差电池,该中心部位成为阳极而被腐蚀。
1.5.4不同金属引起的电偶腐蚀:
为避雷和消除静电,油罐须接地。
当接地材料和罐底板的材料不同时,就会形成电偶腐蚀。
2.防腐措施
原油储罐在服役过程中的防腐工作主要有:
2.1应用新型热喷技术:
针对罐内壁腐蚀较严重的情况,可采用金属火焰喷镀的方法对罐内壁进行喷涂,热喷铝技术在碳钢罐的应用上较为成熟。
喷铝涂层在大气中极易产生致密的氧化膜,提高了稳定性。
此项技术可以避免罐体与氧气和H2S发生反应,阻止油罐的腐蚀。
2.2采用新型的防腐涂料——乙烯基酯树脂
乙烯基酯树脂是一种改性的环氧树脂,在具备环氧树脂几乎所有特性的同时,大大提高了环氧树脂的
耐热性、耐腐蚀性、耐溶剂性、施工性,尤其是介质条件下的耐热性。
乙烯基酯树脂优良的耐化学品性、
耐热性可以解决目前我国石油储罐防腐领域遇到的问题,提高储罐的防腐蚀水平[5]
。
2.3采用涂料与阴极保护结合技术:
单一的涂层可以对大面积基体金属起到保护作用,但对涂层缺陷处不但不能起到保护作用,还会形成大阴极小阳极而加速涂层破损处的腐蚀;涂层与牺牲阳极联合保护可以对涂层破损处达到有效保护,并且联合保护比单纯的阴极保护节省牺牲阳极用量,电流分散效率好,是行之有效的保护办法。
同时还可利用外加电流阴极保护使被保护部位的电极电位通过阴极极化达到规定的保护电位范围,从而抑制腐蚀发生。
“实践表明,阴极保护加涂敷层技术是油品储罐防腐蚀最经济合理的方法”[6]
。
表1反应了某原油罐区采取阴极保护技术后,恒电位仪所测电位情况。
2#罐参比电压
3#罐参比电压
参比电压01
参比电压02
参比电压03
参比电压04
参比电压05
参比电压06
参比电压07
参比电压08
参比电压09
参比电压10
参比电压11
参比电压12
参比电压13
参比电压14
参比电压15
参比电压16
v
v
v
v
v
v
v
v
v
v
v
v
v
v
v
v
1.28
1.23
1.26
1.22
1.23
1.25
0.00
0.00
1.12
1.17
1.21
1.34
1.27
1.21
0.00
0.00
1.24
1.23
1.25
1.26
1.23
1.25
0.00
0.00
1.12
1.17
1.21
1.34